半导体蚀刻技术.docx
《半导体蚀刻技术.docx》由会员分享,可在线阅读,更多相关《半导体蚀刻技术.docx(43页珍藏版)》请在冰豆网上搜索。
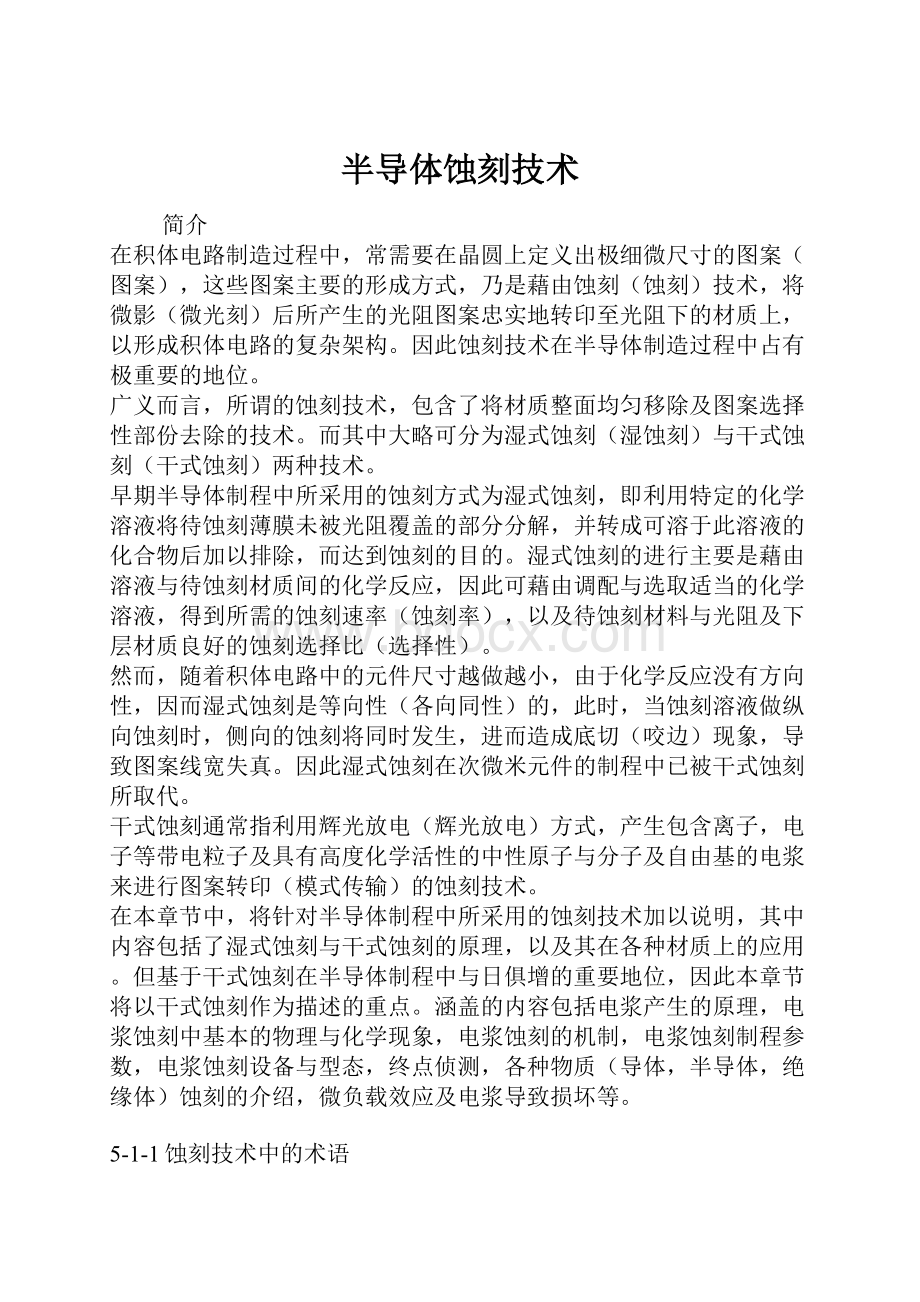
半导体蚀刻技术
简介
在积体电路制造过程中,常需要在晶圆上定义出极细微尺寸的图案(图案),这些图案主要的形成方式,乃是藉由蚀刻(蚀刻)技术,将微影(微光刻)后所产生的光阻图案忠实地转印至光阻下的材质上,以形成积体电路的复杂架构。
因此蚀刻技术在半导体制造过程中占有极重要的地位。
广义而言,所谓的蚀刻技术,包含了将材质整面均匀移除及图案选择性部份去除的技术。
而其中大略可分为湿式蚀刻(湿蚀刻)与干式蚀刻(干式蚀刻)两种技术。
早期半导体制程中所采用的蚀刻方式为湿式蚀刻,即利用特定的化学溶液将待蚀刻薄膜未被光阻覆盖的部分分解,并转成可溶于此溶液的化合物后加以排除,而达到蚀刻的目的。
湿式蚀刻的进行主要是藉由溶液与待蚀刻材质间的化学反应,因此可藉由调配与选取适当的化学溶液,得到所需的蚀刻速率(蚀刻率),以及待蚀刻材料与光阻及下层材质良好的蚀刻选择比(选择性)。
然而,随着积体电路中的元件尺寸越做越小,由于化学反应没有方向性,因而湿式蚀刻是等向性(各向同性)的,此时,当蚀刻溶液做纵向蚀刻时,侧向的蚀刻将同时发生,进而造成底切(咬边)现象,导致图案线宽失真。
因此湿式蚀刻在次微米元件的制程中已被干式蚀刻所取代。
干式蚀刻通常指利用辉光放电(辉光放电)方式,产生包含离子,电子等带电粒子及具有高度化学活性的中性原子与分子及自由基的电浆来进行图案转印(模式传输)的蚀刻技术。
在本章节中,将针对半导体制程中所采用的蚀刻技术加以说明,其中内容包括了湿式蚀刻与干式蚀刻的原理,以及其在各种材质上的应用。
但基于干式蚀刻在半导体制程中与日俱增的重要地位,因此本章节将以干式蚀刻作为描述的重点。
涵盖的内容包括电浆产生的原理,电浆蚀刻中基本的物理与化学现象,电浆蚀刻的机制,电浆蚀刻制程参数,电浆蚀刻设备与型态,终点侦测,各种物质(导体,半导体,绝缘体)蚀刻的介绍,微负载效应及电浆导致损坏等。
5-1-1蚀刻技术中的术语
5-1-1A型等向性与非等向性蚀刻(各向同性和各向异性蚀刻)
不同的蚀刻机制将对于蚀刻后的轮廓(资料)产生直接的影响。
纯粹的化学蚀刻通常没有方向选择性,蚀刻后将形成圆弧的轮廓,并在遮罩(面膜)下形成底切(咬边),如图5-1所示,此谓之等向性蚀刻。
等向性蚀刻通常对下层物质具有很好的选择比,但线宽定义不易控制。
而非等向性蚀刻则是借助具有方向性离子撞击,造成特定方向的蚀刻,而蚀刻后形成垂直的轮廓,如图5-1所示。
采用非等向性蚀刻,可定义较细微的线宽。
5-1-1B的选择比(性)(选择性)
选择比即为不同物质间蚀刻速率的差异值。
其中又可分为对遮罩物质的选择比及对待蚀刻物质下层物质的选择比。
5-1-1C的负载效应(负载效应)
负载效应就是当被蚀刻材质裸露在反应气体电浆或溶液时,面积较大者蚀刻速率较面积较小者为慢的情形。
此乃由于反应物质在面积较大的区域中被消耗掉的程度较为严重,导致反应物质浓度变低,而蚀刻速率却又与反应物质浓度成正比关系,大部份的等向性蚀刻都有这种现象。
湿式蚀刻技术
最早的蚀刻技术是利用特定的溶液与薄膜间所进行的化学反应来去除薄膜未被光阻覆盖的部分,而达到蚀刻的目的,这种蚀刻方式也就是所谓的湿式蚀刻。
因为湿式蚀刻是利用化学反应来进行薄膜的去除,而化学反应本身不具方向性,因此湿式蚀刻过程为等向性,一般而言此方式不足以定义3微米以下的线宽,但对于3微米以上的线宽定义湿式蚀刻仍然为一可选择采用的技术。
湿式蚀刻之所以在微电子制作过程中被广泛的采用乃由于其具有低成本,高可靠性,高产能及优越的蚀刻选择比等优点。
但相对于干式蚀刻,除了无法定义较细的线宽外,湿式蚀刻仍有以下的缺点:
1)需花费较高成本的反应溶液及去离子水,2)化学药品处理时人员所遭遇的安全问题,3)光阻附着性问题;4)气泡形成及化学蚀刻液无法完全与晶圆表面接触所造成的不完全及不均匀的蚀刻;5)废气及潜在的爆炸性。
湿式蚀刻过程可分为三个步骤:
1)化学蚀刻液扩散至待蚀刻材料之表面,2)蚀刻液与待蚀刻材料发生化学反应,3)反应后之产物从蚀刻材料之表面扩散至溶液中,并随溶液排出(3)。
三个步骤中进行最慢者为速率控制步骤,也就是说该步骤的反应速率即为整个反应之速率。
大部份的蚀刻过程包含了一个或多个化学反应步骤,各种形态的反应都有可能发生,但常遇到的反应是将待蚀刻层表面先予以氧化,再将此氧化层溶解,并随溶液排出,如此反覆进行以达到蚀刻的效果。
如蚀刻矽,铝时即是利用此种化学反应方式。
湿式蚀刻的速率通常可藉由改变溶液浓度及温度予以控制。
溶液浓度可改变反应物质到达及离开待蚀刻物表面的速率,一般而言,当溶液浓度增加时,蚀刻速率将会提高。
而提高溶液温度可加速化学反应速率,进而加速蚀刻速率。
除了溶液的选用外,选择适用的遮罩物质亦是十分重要的,它必须与待蚀刻材料表面有很好的附着性,并能承受蚀刻溶液的侵蚀且稳定而不变质。
而光阻通常是一个很好的遮罩材料,且由于其图案转印步骤简单,因此常被使用。
但使用光阻作为遮罩材料时也会发生边缘剥离或龟裂的情形。
边缘剥离乃由于蚀刻溶液的侵蚀,造成光阻与基材间的黏着性变差所致。
解决的方法则可使用黏着促进剂来增加光阻与基材间的黏着性,如六甲基-二硅氮烷(HMDS的)。
龟裂则是因为光阻与基材间的应力差异太大,减缓龟裂的方法可利用较具弹性的遮罩材质来吸收两者间的应力差。
蚀刻化学反应过程中所产生的气泡常会造成蚀刻的不均匀性,气泡留滞于基材上阻止了蚀刻溶液与待蚀刻物表面的接触,将使得蚀刻速率变慢或停滞,直到气泡离开基材表面。
因此在这种情况下会在溶液中加入一些催化剂增进蚀刻溶液与待蚀刻物表面的接触,并在蚀刻过程中予于搅动以加速气泡的脱离。
以下将介绍半导体制程中常见几种物质的湿式蚀刻:
矽,二氧化矽,氮化矽及铝。
5-2-1矽的湿式蚀刻
在半导体制程中,单晶矽与复晶矽的蚀刻通常利用硝酸与氢氟酸的混合液来进行。
此反应是利用硝酸将矽表面氧化成二氧化矽,再利用氢氟酸将形成的二氧化矽溶解去除,反应式如下:
泗+硝酸+6HFàH2SiF6++H2+的水亚硝酸
上述的反应中可添加醋酸作为缓冲剂(缓冲剂),以抑制硝酸的解离。
而蚀刻速率的调整可藉由改变硝酸与氢氟酸的比例,并配合醋酸添加与水的稀释加以控制。
在某些应用中,常利用蚀刻溶液对于不同矽晶面的不同蚀刻速率加以进行(4)。
例如使用氢氧化钾与异丙醇的混合溶液进行矽的蚀刻。
这种溶液对矽的(100 )面的蚀刻速率远较(111)面快了许多,因此在(100)平面方向的晶圆上,蚀刻后的轮廓将形成V型的沟渠,如图5-2所示。
而此种蚀刻方式常见于微机械元件的制作上。
5-2-2二氧化矽的湿式蚀刻
在微电子元件制作应用中,二氧化矽的湿式蚀刻通常采用氢氟酸溶液加以进行(5)。
而二氧化矽可与室温的氢氟酸溶液进行反应,但却不会蚀刻矽基材及复晶矽反应式如下。
:
二氧化硅+6HFà+2H2O的H2+的SiF6
由于氢氟酸对二氧化矽的蚀刻速率相当高,在制程上很难控制,因此在实际应用上都是使用稀释后的氢氟酸溶液,或是添加氟化铵作为缓冲剂的混合液,来进行二氧化矽的蚀刻。
氟化铵的加入可避免氟化物离子的消耗,以保持稳定的蚀刻速率。
而无添加缓冲剂氢氟酸蚀刻溶液常造成光阻的剥离。
典型的缓冲氧化矽蚀刻液(教委:
缓冲区氧化物刻蚀机)(体积比6:
1之氟化铵(40%)与氢氟酸(49%))对于高温成长氧化层的蚀刻速率约为1000Å/min。
在半导体制程中,二氧化矽的形成方式可分为热氧化及化学气相沉积等方式,而所采用的二氧化矽除了纯二氧化矽外,尚有含有杂质的二氧化矽如BPSG等然而。
由于这些以不同方式成长或不同成份的二氧化矽,其组成或是结构并不完全相同,因此氢氟酸溶液对于这些二氧化矽的蚀刻速率也会不同。
但一般而言,高温热成长的氧化层较以化学气相沉积方式之氧化层蚀刻速率为慢,因其组成结构较为致密。
5-2-3氮化矽的湿式蚀刻
氮化矽可利用加热至180℃的磷酸溶液(85%)来进行蚀刻(5)。
其蚀刻速率与氮化矽的成长方式有关,以电浆辅助化学气相沉积方式形成之氮化矽,由于组成结构(SixNyHz相较于氮化硅)较以高温低压化学气相沉积方式形成之氮化矽为松散,因此蚀刻速率较快许多。
但在高温热磷酸溶液中光阻易剥落,因此在作氮化矽图案蚀刻时,通常利用二氧化矽作为遮罩。
一般来说,氮化矽的湿式蚀刻大多应用于整面氮化矽的剥除。
对于有图案的氮化矽蚀刻,最好还是采用干式蚀刻为宜。
5-2-4铝的湿式蚀刻
铝或铝合金的湿式蚀刻主要是利用加热的磷酸,硝酸,醋酸及水的混合溶液加以进行
(1)。
典型的比例为80%的磷酸,5%的硝酸,5%的醋酸及10%的水。
而一般加热的温度约在35℃至45℃左右,温度越高蚀刻速率越快,一般而言蚀刻速率约为1000-3000Å/分钟,而溶液的组成比例,不同的温度及蚀刻过程中搅拌与否都会影响到蚀刻的速率。
蚀刻反应的机制是藉由硝酸将铝氧化成为氧化铝,接着再利用磷酸将氧化铝予以溶解去除,如此反覆进行以达蚀刻的效果。
在湿式蚀刻铝的同时会有氢气泡的产生,这些气泡会附着在铝的表面,而局部地抑制蚀刻的进行,造成蚀刻的不均匀性,可在蚀刻过程中予于搅动或添加催化剂降低介面张力以避免这种问题发生。
干式蚀刻技术(电浆蚀刻技术)
5-3-1电浆蚀刻简介
自1970年代以来元件制造首先开始采用电浆蚀刻技术,对于电浆化学新的了解与认知也就蕴育而生。
在现今的积体电路制造过程中,必须精确的控制各种材料尺寸至次微米大小且具有极高的再制性,而由于电浆蚀刻是现今技术中唯一能极有效率地将此工作在高良率下完成,因此电浆蚀刻便成为积体电路制造过程中的主要技术之一。
电浆蚀刻主要应用于积体电路制程中线路图案的定义,通常需搭配光阻的使用及微影技术,其中包括了1)氮化矽(氮化物)蚀刻:
应用于定义主动区,2)复晶矽化物/复晶矽(多晶硅化物/聚)蚀刻:
应用于定义闸极宽度/长度;3)复晶矽(聚)蚀刻:
应用于定义复晶矽电容及负载用之复晶矽4)间隙壁(间隔)蚀刻:
应用于定义LDD的宽度;5)接触窗(联系)及引洞(VIA)的蚀刻:
应用于定义接触窗及引洞之尺寸大小;6)钨回蚀刻(蚀刻):
应用于钨栓塞(W型插入)之形成;7)涂布玻璃(特别一次过拨款)回蚀刻:
应用于平坦化制程,8)金属蚀刻:
应用于定义金属线宽及线长,9)接脚(邦定垫)蚀刻等。
影响电浆蚀刻特性好坏的因素包括了:
1)电浆蚀刻系统的型态,2)电浆蚀刻的参数;3)前制程相关参数,如光阻,待蚀刻薄膜之沉积参数条件,待蚀刻薄膜下层薄膜的型态及表面的平整度等。
5-3-2何谓电浆?
基本上电浆是由部份解离的气体及等量的带正,负电荷粒子所组成,其中所含的气体具高度的活性,它是利用外加电场的驱动而形成,并且会产生辉光放电(辉光放电)现象。
蚀刻用的电浆中,气体的解离程度很低,通常在10-5-10-1之间,在一般的电浆或活性离子反应器中气体的解离程度约为10-5-10-4 ,若解离程度到达10-3-10-1则属于高密度电浆。
5-3-3电浆形成之原理
电浆的产生可藉由直流(DC)的偏压或交流射频(RF)的偏压下的电场形成,如图5-3所示,而在电浆中的电子来源通常有二:
一为分子或原子解离后所产生的电子,另一则为离子撞击电极所产生的二次电子(二次电子),在直流(DC)的电场下产生的电浆其电子源主要以二次电子为主,而交流射频(RF)的电场下产生的电浆其电子源则以分子或原子解离后所产生的电子为主。
在电浆蚀刻中以直流方式产生辉光放电的缺点包含了:
1)需要较高的功率消耗,也就是说产生的离子密度低;2)须要以离子撞击电极以产生二次电子,如此将会造成电极材料的损耗。
三)所需之电极材料必须为导体如此一来将不适用于晶圆制程中。
在射频放电(RF放电)状况下,由于高频操作,使得大部份的电子在半个周期内没有足够的时间移动至正电极,因此这些电子将会在电极间作振荡,并与气体分子产生碰撞。
而射频放电所需的振荡频率下限将视电极间的间距,压力,射频电场振幅的大小及气体分子的解离位能等因素而定,而通常振荡频率下限为50kHz的。
一般的射频系统所采用的操作频率大都为13.56。
相较于直流放电,射频放电具有下列优点:
1)放电的情况可一直持续下去而无需二次电子的发射,当晶圆本身即为电极的一部份时,这点对半导体材料制程就显得十分重要了;2)由于电子来回的振荡,因此离子化的机率大为提升,蚀刻速率可因而提升;3)可在较低的电极电压下操作,以减低电浆对元件所导致之损坏; 4)对于介电质材料同样可以运作。
现今所有的电浆系统皆为射频系统。
另外值得一提的是在射频系统中一个重要的参数是供给动力的电极面积与接地电极面积之比。
5-3-4等效电子及离子温度
存在于电浆中的电场分别施力于带正电荷之离子与代负电荷之电子,女=é*q时,而加速度为a=男/女,由于离子质量远大于电子,因此电子所获得的加速度与速度将远大于离子,以致电子的动能远大于离子,电子与离子间处于一非平衡状态。
从气体动力论中,得知Ekinetic=(3/2)KT公司,由此可知,等效电子温度远大于等效离子温度,如此可视为“热”电子处于“冷”电浆之中。
因此电子能够在低温的状态下提供一般在高温下才能使分子解离所需要的能量。
在一般蚀刻用的电浆中,等效的电子温度约为10000-100000°K的。
5-3-5电浆蚀刻中的基本物理及化学现象
在干式蚀刻中,随着制程参数及电浆状态的改变,可以区分为两种极端的性质的蚀刻方式,即纯物理性蚀刻与纯化学反应性蚀刻。
纯物理性蚀刻可视为一种物理溅镀(溅射)方式,它是利用辉光放电,将气体如氩气,解离成带正电的离子,再利用偏压将离子加速,溅击在被蚀刻物的表面,而将被蚀刻物质原子击出。
此过程乃完全利用物理上能量的转移,故谓之物理性蚀刻。
其特色为离子撞击拥有很好的方向性,可获得接近垂直的蚀刻轮廓。
但缺点是由于离子是以撞击的方式达到蚀刻的目的,因此光阻与待蚀刻材料两者将同时遭受蚀刻,造成对遮罩物质的蚀刻选择比变差,同时蚀刻终点必须精确掌控,因为以离子撞击方式蚀刻对于底层物质的选择比很低。
且被击出的物质往往非挥发性物质,而这些物质容易再度沉积至被蚀刻物薄膜的表面或侧壁。
加上蚀刻效率偏低,因此,以纯物理性蚀刻方式在积体电路制造过程中很少被用到。
纯化学反应性蚀刻,则是利用电浆产生化学活性极强的原(分)子团,此原(分)子团扩散至待蚀刻物质的表面,并与待蚀刻物质反应产生挥发性之反应生成物,并被真空设备抽离反应腔。
因此种反应完全利用化学反应来达成,故谓之化学反应性蚀刻。
此种蚀刻方式相近于湿式蚀刻,只是反应物及产物的状态由液态改变为气态,并利用电浆来促进蚀刻的速率。
因此纯化学反应性蚀刻拥有类似于湿式蚀刻的优点及缺点,即高选择比及等向性蚀刻。
在半导体制程中纯化学反应性蚀刻应用的情况通常为不需做图形转换的步骤,如光阻的去除等。
一个仅基于化学反应机制的理想干蚀刻过程可分为以下几个步骤:
1)反应气体进入腔体,2)产生电浆形态之蚀刻物种,如离子及自由基(自由基),3)蚀刻物种藉由扩散,碰撞或场力移至待蚀刻物表面并吸附于表面;4)蚀刻物种停滞在待蚀刻物表面一段时间;5)进行化学反应并产生挥发性之生成物;6)生成物脱离表面;7)脱离表面之生成物扩散至气体中并排出
(1)。
上述步骤中若其中一个停止发生,则整个反应将不再进行。
而其中生成物脱离表面的过程最为重要,大部份的反应物种皆能与待蚀刻物表面产生快速的反应,但除非生成物有合理的蒸气压以致让其脱离表面,否则反应将不会发生。
综观而论,纯物理性蚀刻,如离子束蚀刻(离子束蚀刻)有两大缺点:
一为低选择比,一为低蚀刻效率而纯化学反应蚀刻也有两个缺点:
。
一为等向性蚀刻,另一为无法应用至次微米的元件制程上,包含了线宽控制与均匀性等问题。
最具广泛使用的方法便是结合物理性蚀刻与化学反应性蚀刻,即所谓的活性离子蚀刻(RIE刻蚀,反应离子蚀刻),此种蚀刻方式兼具非等向性及高选择比等双重优点,蚀刻的进行主要靠化学反应来达成,以获得高选择比加入离子撞击的作用有二:
一是将待蚀刻物质表面的原子键结破坏,以加速蚀刻速率;二是将再沉积于待蚀刻。
物质表面的产物或聚合物(聚合物)打掉,以便待蚀刻物质表面能再与反应蚀刻气体接触。
非等向性蚀刻的达成,则是靠再沉积的产物或聚合物,沉积于待蚀刻图形上,在表面的沉积物可被离子打掉,蚀刻可继续进行,而在侧壁上的沉积物,因未受离子的撞击而保留下来,阻隔了表面与反应蚀刻气体的接触,使得侧壁不受侵蚀,而获得非等向性蚀刻。
综合以上所言,电浆(干式)蚀刻的完成包含了以下几种过程:
1)化学反应,属等向性,2)离子辅助蚀刻,具方向性,3)保护层的形成,可避免侧壁遭受蚀刻4)生成物残留的排除。
垂直的蚀刻轮廓(非等向性蚀刻),主要源自于两大原因:
一为垂直方向的离子撞击,加速垂直方向的蚀刻;一为侧壁保护层的形成而侧壁保护层的形成种类有下列。
几种方式:
1)非挥发性的副产物,例如:
SiBr4,二氧化硅,BrxOy2)光阻蚀刻时所产生之聚合物;3)聚合物气体,例如:
CFX的CClx中,x<34 )侧壁表面氧化或氮化,例如:
AlxNy,SixOy。
5-3-6电浆蚀刻机制
以矽蚀刻为例,图5-4所示为含氟原子的电浆蚀刻矽薄膜的机制,反应后的产物为挥发性之SiF4及SiF2
(2)。
若以纯四氟化碳电浆气体蚀刻矽或氧化矽薄膜,则蚀刻速率相对很慢。
但若将少量的氧气(氧气)加入的CF4气体中,则矽或氧化矽薄膜的蚀刻速率将大幅度增加,如图5-5所示(6)氧气的加入通常伴随着电浆中氟原子密度的增加,此乃由于氧与CF4的反应而释出氟原子所致,可能的反应为:
。
四氟化碳+氧气àCOF2 +2楼。
氧气的加入并且消耗掉部份的碳,使得电浆中的氟碳比增加,进而增进了矽或氧化矽薄膜的蚀刻速率。
从图5-5亦可看出,在氧的添加后,对矽的蚀刻速率提升要比氧化矽来得快,由此可知,氧的加入将使得氧化矽对矽的蚀刻速率选择比降低。
但若将氧的含量持续增加,则额外的氧将会把氟原子的浓度稀释,因而造成蚀刻速率的降低。
如果我们在四氟化碳中加入氢气,则氢气分解成氢原子后与氟原子反应形成氟化氢(HF)的。
对矽的蚀刻而言,氟原子浓度减少,使得蚀刻速率直线下降。
对氧化矽的蚀刻而言,虽然高频可蚀刻氧化矽,但蚀刻速率仍比原来慢了点。
因此,适量氢气的加入可提升氧化矽对矽的蚀刻选择比。
图5-6为加入氢气后,矽,氧化矽及光阻蚀刻速率的变化情形(7)。
5-3-7氟碳比模型(氟对碳比模型)
在氟碳化物的电浆中,氟的作用是与基材表面反应,产生挥发性的产物,并藉由真空设备带出腔体外,因此当氟的成份增加时,蚀刻速率增加。
碳在电浆中的作用为提供聚合物的来源,因此碳会抑制蚀刻的进行,当碳的成份增加时,将使得蚀刻速率减缓。
基于上述之原理,我们可以藉由电浆中的氟/碳(女/C)的比的变化来推测反应进行的方向。
在添加其它气体的状况下,亦会改变氟/碳比,因此反应的趋势可借此来预知,此即称之为氟碳比模型。
氟碳比模型适用于以氟碳化物电浆作为主要蚀刻机构的材料,除矽,氧化矽之外,在氮化钛,氮化硅,钨等均可适用。
以矽,氧化矽为例,在矽表面上的反应只会消耗氟,而碳并不会损失。
因此在蚀刻的过程中氟碳比(F值/C)下降,当晶片上矽表面积曝露于电浆增加时,蚀刻速率将变慢。
而当加入氧气时会消耗许多碳原子而形成一氧化碳或二氧化碳,且氟原子的解离也因而增加,因此氟碳比(F值/C)上升,蚀刻速率也跟着上升。
加入氢气则会消耗氟原子形成高频,氟碳比(F值/C)因而下降,对矽的蚀刻速率也就下降;但对氧化矽而言,因其含有氧的成份,可局部性地消耗碳的成份,因此氟碳比(男/三)在局部区域呈现不变的情形,使得氧化矽的蚀刻速率变化较小。
除了加入氧气及氢气外,加入CHF3,或以CHF3,C2F4等氟碳比小于4的气体来取代CF4的,亦可达到降低氟碳比(F值/C),提高蚀刻选择比的效果。
5-3-8电浆蚀刻制程参数
电浆蚀刻制程参数一般包括了射频(RF)的功率,压力,气体种类及流量,蚀刻温度及腔体的设计等因素,而这些因素的综合结果将直接影响蚀刻的结果,图5-7中所示为其相互间关系的示意图。
射频(RF)的功率是用来产生电浆及提供离子能量的来源,因此功率的改变将影响电浆中离子的密度及撞击能量而改变蚀刻的结果。
压力也会影响离子的密度及撞击能量,另外也会改变化学聚合的能力。
蚀刻反应物滞留在腔体内的时间正比于压力的大小,一般说来,延长反应物滞留的时间将会提高化学蚀刻的机率并且提高聚合速率气体流量的大小会影响反应物滞留在腔体内的时间;增加气体流量将加速气体的分布并可提供更多未反应的蚀刻反应物,因此可降低负载效应(负载效应);改变气体流量也会影响蚀刻速率。
原则上温度会影响化学反速率及反应物的吸附系数(吸附系数),提高晶片温度将使得聚合物的沉积速率降低,导致侧壁的保护减低,但表面在蚀刻后会较为干净;增加腔体的温度可减少聚合物沉积于管壁的机率,以提升蚀刻制程的再现性。
晶圆背部氦气循环流动可控制蚀刻时晶圆的温度与温度的均匀性,以避免光阻烧焦或蚀刻轮廓变形。
其他尚须考量的因素还有腔体的材质,一般常见的材质包含铝,陶瓷,石英,矽及石墨等,不同的腔体材质会产生不同的反应产物并会改变蚀刻的直流偏压。
应用干式蚀刻时主要须注意蚀刻速率,均匀度,选择比及蚀刻轮廓等。
蚀刻速率越快,则产能越快,有助于降低成本提升竞争力。
蚀刻速率通常可由气体种类,流量,电浆源及功率等所控制,一般而言,在其他因素尚可接受的范围内,蚀刻速率越快越好。
均匀度是晶圆上不同位置蚀刻差异的一个指标,均匀度越好意谓着有较佳的良率,当晶圆尺寸越来越大,均匀度的控制就显得更加重要。
控制选择比通常与气体种类与比例,电浆源及功率,乃至于反应温度均有关系。
蚀刻轮廓一般而言以接近90度为佳,除了少数特例,如接触窗(联系窗口)或引洞(通孔),为了使后续金属溅镀能有较佳的覆盖能力(步骤覆盖范围),因而故意将其轮廓蚀刻成小于90度的型态。
而通常蚀刻轮廓的控制可藉由调变气体种类与比例,电浆源及功率等来进行。
5-3-9蚀刻设备
电浆蚀刻系统通常包含下列几个主要组件:
1)蚀刻用腔体,2)真空系统(如帮浦等),3)压力计;4)射频电源供应器,5)气体流量控制器; 6)电极等,详细的组成将视系统的型态而定。
这小节中,将介绍常见的几种电浆蚀刻机台设备。
5-3-9A条桶式蚀刻机(桶式蚀刻)
最早期所发展出,也是最简单型态的的蚀刻机即为桶式蚀刻机,它的基本型态如图5-8所示
(2)。
其中,由于带有能量的离子或电子不会进入蚀刻区域中,因此蚀刻时不会产生离子轰击,故蚀刻属完全之化学反应。
也由于如此,蚀刻趋于等向性,因此有很好的蚀刻选择性,并且不会造成幅射损伤。
此种型态的蚀刻机一般