操纵杆支架及铣36槽内侧面夹具说明书.docx
《操纵杆支架及铣36槽内侧面夹具说明书.docx》由会员分享,可在线阅读,更多相关《操纵杆支架及铣36槽内侧面夹具说明书.docx(19页珍藏版)》请在冰豆网上搜索。
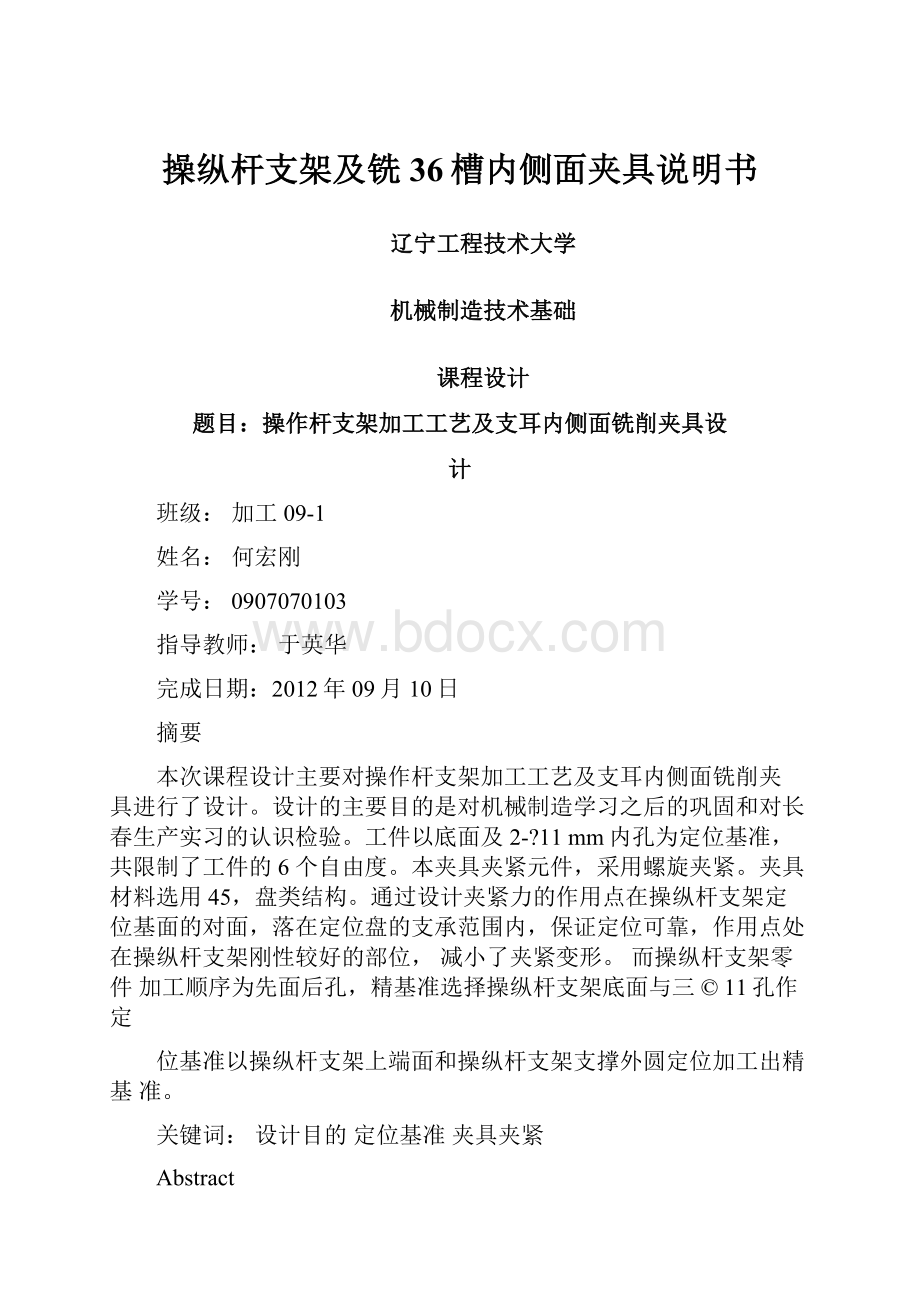
操纵杆支架及铣36槽内侧面夹具说明书
辽宁工程技术大学
机械制造技术基础
课程设计
题目:
操作杆支架加工工艺及支耳内侧面铣削夹具设
计
班级:
加工09-1
姓名:
何宏刚
学号:
0907070103
指导教师:
于英华
完成日期:
2012年09月10日
摘要
本次课程设计主要对操作杆支架加工工艺及支耳内侧面铣削夹具进行了设计。
设计的主要目的是对机械制造学习之后的巩固和对长春生产实习的认识检验。
工件以底面及2-?
11mm内孔为定位基准,共限制了工件的6个自由度。
本夹具夹紧元件,采用螺旋夹紧。
夹具材料选用45,盘类结构。
通过设计夹紧力的作用点在操纵杆支架定位基面的对面,落在定位盘的支承范围内,保证定位可靠,作用点处在操纵杆支架刚性较好的部位,减小了夹紧变形。
而操纵杆支架零件加工顺序为先面后孔,精基准选择操纵杆支架底面与三©11孔作定
位基准以操纵杆支架上端面和操纵杆支架支撑外圆定位加工出精基准。
关键词:
设计目的定位基准夹具夹紧
Abstract
Thecurriculumdesignoftheoperatingrodmachiningtechnologyandsupportingtheearsidemillingfixturedesign.DesignofthemainpurposeistoconsolidateandmachinerymanufacturingafterlearningofChangchunproductionpracticeknowledgetest.Theworkpiecetothebottomandthe2-Diameter11mmholeforpositioningdatum,atotallimitof6degreesoffreedomofworkpiece.Theclampingcomponent,theclampingscrew.Clampmaterialselection45,discstructure.Throughthedesignoftheclampingforceeffectpointontheleverbracketpositioningsurfaceopposite,fallsonthepositioningplatebearingrange,guaranteereliablepositioning,functionpointintheleverbracketthepositionwithhigherrigidity,reducestheclampingdeformation.Whiletheleverbracketpartsprocessingsequenceofthesurfaceafterthefirsthole,precisiondatumselectionleverbracketandthebottomsurfaceofthethree©11holes
forlocatingdatumtothejoystickonthetopsurfaceofthesupportandjoysticksupportexternalpositioningprocessingprecisionreference.
Keywords:
designobjectivepositioningdatumclamp
第一部分:
工艺设计说明书
一、零件的工艺性分析5
二、毛坯选择6
三、机械工艺路线确定7
四、主要工序尺寸及其公差确定9
五、设备及其工艺装备确定9
六、切削用量及工时定额确定10
第二部分:
专用夹具设计说明书
一铣床夹具设计12
二问题的提出16
三定位基准的选择16
四夹具的结构设计18
五定位元件的选择及要求18
六夹紧元件的选择19
七夹具体的设计19
八夹紧方案的设计19
九夹具设计及操作的简要说明20
第三部分设计体会22
第一部分工艺设计说明书
1.零件工艺性分析
1.1零件结构功用分析:
操纵杆支架零件是机械中常见的一种零件,操纵杆支架的具体作
用起到支撑零件作用,因为操纵杆支架上面可以按装其它零件,因此
要的加工表面。
用锻造毛坯。
由于该零件的两个©20孔要求较高,它的表面质量直
接影响工作状态,通常对其尺寸要求较高。
一般为IT5-IT7。
加工时两0©20孔的同轴度应该控制在0.01mm3-©11孔的尺寸它直接影响孔在空间的位置,加工时可以将其加工精度降低,通过装配来提高精度。
1.3主要技术条件:
1.孔径精度:
两©20孔的孔径的尺寸误差和形状误差会造的配合不
良,因此对孔的要求较高,其孔的尺寸公差为IT7
2.主要平面的精度:
由于©11孔接影响联接时的接触刚度,并且加工过程中常作为定位基面,则会影响孔的加工精度,因此须规定其加工要求。
2.毛坯选择
2.1毛坯类型
选择毛坯及毛坯制造方法
根据零件材料确定毛坯为铸件,根据其结构形状、尺寸大小和材料性能毛坯的铸造方法选用----低压铸造毛坯公差等级---IT8级
球墨铸铁:
在铁水(球墨生铁)浇注前加一定量的球化剂(硅,镁)使铸铁中石墨球化,由于碳以球状存在于铸件基体中,改善其对基体的割裂作用,球墨铸铁的抗拉强度,屈服强度,塑性,冲击韧性大大提高,并且有耐磨,减震。
工艺性能好,成本低等优点因为零件要求无砂眼,所以在毛坯铸造时要注意气孔的产生气孔原因:
1.空气夾杂在熔汤中
2.气体的来源:
熔解时、在料管中、在模具中、离型剂
改善方法:
1.适当的慢速
2.检查流道转弯是否圆滑,截面积是否渐減
3.检查逃气道面积是否够大,是否有被阻塞,位置是否位於最后充
填的地方
4.检查离型剂是否噴太多,模温是否太低
5.使用真空.
考虑到操纵杆支架工作时的作用,要求材料要有很高的强度,
并且该零件结构较为复杂,故选用铸造毛坯材料为HT2O0
2.2毛坯余量确定
由书机械加工工艺设计资料表1.2-10查得毛坯加工余量为2,毛坯
尺寸偏差由表1.2-2查得为士1.4.
2.3毛坯一零件合图草图
1
?
・*tir.*if
3.机械工艺路线确定
3.1定位基准的选择:
3.1.1精基准的选择:
选择操纵杆支架底面与三©11孔作定位基准,因为©11孔面,及底面是装配结合面,且操纵杆支架底面又是空间位置的设计基准,故选择操纵杆支架底面与外圆作定位基准,符合基
准重合原则且装夹误差小。
3.1.2粗基准的选择:
以操纵杆支架上端面和操纵杆支架支撑外圆定位加工出精基准。
3.2加工顺序的安排:
操纵杆支架零件加工顺序为先面后孔,这样可以用加工好的平面定位再来加工孔,因为操纵杆支架孔的精度要求较高,加工难度大,先加工好平面,再以平面为精基准加工孔,这样即能为孔的加工提供稳定可靠的精基准,同时可以使孔的加工余量较为均匀
3.3加工阶段的划分说明
加工阶段分为:
粗加工阶段、半精加工阶段、精加工阶段。
3.4加工工序
工
序
号
工名
序称
工序
内
容
1
锻造
锻造,清理
2
热处理
时效
4
铣
铣底平面
5
钻
钻铰3-©11孔
6
铣
铣支耳内侧面
7
钻
钻铰2-©20孔
8
钳工
倒角
9
钳工
去各部分锐边毛刺
10
终检
终检
4.主要工序尺寸及其公差确定
铣下平面
工艺路线
基本尺寸
工序余量
经济精度
工序尺寸
锻
14
2.5
14士0.1
粗铣
11.5
2
12.5(IT11)
11.5
半精铣
10.5
0.5
6.3(IT9)
©10.5
©20孔
工艺路线
基本尺寸
工序余量
经济精度
工序尺寸
铸
10
钻
©18
9
12.5(IT12)
虫13
©180
扩
©19.8
0.9
6.3(IT10)
4IUM3
©19.80
铰
©20
0.5
3.2(IT8)
©20士0.01
5.设备及其工艺装备确定
所用的设备有:
X62WZ4012、检验台、钳工台。
夹具有:
钻2-©20孔专用夹具、钻3-©11底孔专用夹具、铣底平面
夹具。
刀具有:
硬质合金铣刀、平板锂、©18钻头、©11钻头、©20铰刀、圆锉刀
量具有:
游标卡尺、专用塞规。
6.切削用量及工时定额确定
铣底平面时:
切削用量:
ap=1.5
由表6.3-2得:
f=0.2m/r
由表6.3-21得:
v=120m/r
则n=318V/D=318x120/85=449m/r
工时定额:
由表6.4-1得:
T2=lw+lf/fxn=1.45min
由表3.3-7得:
操作机床时间为:
0.83min
由表3.3-8得:
测量工件时间为:
0.14min
T1=2.27minT3=51minT4=15min
T基=lz/nfap=0.5min
则T总二T1+T2+T基=68.7min
:
钻3-©11孔时;
切削用量:
ap=3.5
由表7.3-1得:
f=0.36m/r
由表7.3-11得:
v=13m/r
则n=318V/D=318x13/5=826m/r
工时定额:
T2=lw+lf/fxn=0.1min
由表3.3-9得:
装夹工件时间为0.17min由表3.3-10得:
松开卸下工件时间为0.15min由表3.3-12得:
测量工件时间为:
0.04minT1=0.76minT3=47minT4=15min
则T总二T1+T2+T基=62.9min
粗铣、半精铣支耳内侧面时;
粗铣时:
切削用量:
ap=1.5
由表6.3-2得:
f=0.2m/r
由表6.3-21硬质合金铣刀铣削灰锻铁时v=120m/r
则n=318V/D=763.2m/r
工时定额:
由表6.4-1得:
T2=lw+lf/vf=2.63min精铣时:
切削用量:
ap=1
由表6.3-2得:
f=0.12m/r
由表6.3-21硬质合金铣刀铣削灰锻铁时v=150m/r
则n=318V/D=561m/r
工时定额:
由表6.4-1得:
T2=lw+lf/vf=3.5min由表3.3-7得:
操作时间为0.83min由表3.3-8得:
测量工件时间为:
0.14minT1=2.27minT3=51minT4=15min则T总二T1+T2+T基=80.53min
:
钻铰©20内孔时;
钻孔时:
切削用量:
ap=9
由表8.2-1得:
f=0.5m/rv=80m/r
则n=318V/D=1496.5m/r工时定额:
T2=lw+lf/vf=0.03min扩孔时:
切削用量:
ap=0.9由表6.3-2得:
f=0.2m/rv=100m/r则n=318V/D=1630.7m/r工时定额:
T2=lw+lf/vf=0.04min铰孔时:
切削用量:
ap=0.5由表6.3-2得:
f=0.15m/rv=80m/r则n=318V/D=1590m/r工时定额:
T2=lw+lf/vf=0.07min由表3.3-1得:
装夹工件时间为0.42min由表3.3-2得:
松开卸下工件时间为0.12min由表3.3-3得:
操作机床时间为:
0.02+0.04+0.03+0.07+0.06+0.02+0.01+0.02+0.03+0.04=0.64min由表3.3-4得:
测量工件时间为:
0.16min
T1=1.34minT3=56minT4=15min
则T总二T1+T2+T基=72.62min
第二部分支耳内侧面铣削夹具设计
铣床夹具的设计
(一)、机床夹具在机械加工中的作用
对工件进行加工时,为了保证加工要求,首先要使工件相对于刀具及机床有正确的位置,并使这个位置在加工过程中不因外力的影响而变动。
为此,在进行机械加工前,首先要将工件装夹好。
工件的装夹方法有两种:
一种是工件直接装夹在机床的工作台或花盘上;另一种是工件装夹在夹具上。
采用第一种方法夹工件时,一般要先按图样要求在工件表面划线,划出加工表面的尺寸和位置,装夹时用划针或百分表找正后再夹紧。
这种方法无需专用装备,但效率低,一般用于小批生产。
批量较大时,大都用夹具装夹工件。
用夹具装夹工件有下列优点:
(1)能稳定地保证工件的加工精度用夹具装夹工件时,工件相
对于刀具及机床的位置精度由夹具保证,不受工人技术水平的影响,使一批工件的加工精度趋于一致。
(2)能提高劳动生产率使用夹具装夹工件方便、快速,工件不
需要划线找正,可显著地减少辅助工时,提高劳动生产率;工
件在夹具中装夹后提高了工件的刚性,因此可加大切削用量,
提高劳动生产率;可使用多件、多工位装夹工件的夹具,并可采用高效夹紧机构,进一步提高生产率。
(3)能扩大机床的使用范围
4)能降低成本在批量生产中使用夹具后,由于劳动生产率的提高、使用技术等级较低的工人以及废品率下降等原因,明显地降低了生产成本。
夹具制造成本分摊在一批工件上,每个工件增加的成本是极少的,远远小于由于提高劳动生产率而降低的成本。
工件批量愈大,使用夹具所取得的经济效益就愈显著。
二、机床夹具的分类机床夹具的种类繁多,可以从不同的角度对机床夹具进行分类。
常用的分类方法有以下几种。
1.按夹具的使用特点分类
(1)通用夹具已经标准化的,可加工一定范围内不同工件的夹具,称为通用夹具,如三爪定心卡盘、机床用平口虎钳、万能分度头、磁力工作台等。
这些夹具已作为机床附件的专门工厂制造供应,只需选购即可。
2)专用夹具专门为某一工件的某道工序设计制造的夹具,称为专用夹具。
专用夹具一般在批量生产中使用。
3)可调夹具夹具的某些元件可调整或可更换,以适应多种工件加工的夹具,称为可调夹具。
它还分为通用可调夹具和成组夹具两类。
4)组合夹具采用标准的组合夹具元件、部件,专为某一工件的某道工序组装的夹具,称为组合夹具。
5)拼装夹具用专门的标准化、系列化的拼装夹具而成的夹具,称为拼装夹具。
它具有组合夹具的优点,但比组合夹具精度高、效能高、结构紧凑。
它的基础板和夹紧部件中常带有小型液压缸。
。
此类夹具更适合在数控机床上使用。
2.按使用机床分类
夹具按使用机床可分为车床夹具、铣床夹具、钻床夹具、镗床夹
具、齿轮机床夹具、数控机床夹具、自动机床夹具、自动线随行夹具以及其它机床夹具等。
3.按夹紧的动力源分类
夹具按夹紧的动力源可分为手动夹具、气动夹具、液压夹具、气液增力夹具、电磁夹具以及真空夹具等。
三、机床夹具的组成
机床夹具的种类和结构虽然繁多,但它们的组成均可概括为下面几个部分。
1.定位装置定位装置的作用是使工件在夹具中占据正确的位置。
2.夹紧装置
夹紧装置的作用是将工件压紧夹牢,保证工件在加工过程中受到外力作用是不离开已经占据的正确位置。
3.对刀或导向装置对刀或导向装置用于确定刀具相对于定位元件的正确位置。
4.连接元件连接元件是确定夹具在机床上正确位置的元件。
5.夹具体夹具体是机床夹具的基础件。
6.其它装置或元件
它们是指夹具中因特殊需要而设置的装置或元件。
如需加工按一定规律分布的多个表面时,常设置分度装置;为能方便、准确地定位,常设置预定位装置;对于大型夹具,常设置吊装元件等。
二.问题的提出
本夹具主要用来铣操纵杆支架的侧面,有一定的技术要求,要求相对于36的轴线的对称度为0.2,表面粗糙度为12.5。
主要应考虑机械加工的精度,而提高劳动生产率,降低劳动强度为次要因素。
三.定位基准的选择
精基准的选择主要应考虑基准重合问题。
当设计基准与工序基准重合时,应该进行尺寸换算。
现设计计算如下:
工件以底面及2-?
11mm内孔为定位基准,共限制了工件的6个自由度。
a)定位误差的分析
如图所示,工件以?
11mm内孔柱面在定位元件的?
11mm定位,加工内侧面,
(a)零件定位误差
操纵杆支架工序图及定位元件简解工件定位基准与止口定位基准(?
361mm重合,△丫工0。
定位基准可以任意方向移动。
(b)计算:
△B=0.02mm(同轴度误差)。
△Y=TD+Td+Xmin
=0.03+0.10+0.02
=0.15mm
△D=△Y+△B
=0.15+0.02=0.17mm
这种定位方式的定位误差不大,保证侧面的对称度要求。
其原因:
一方面是定位基准与工序基准重合,另一方面是定位基面的公差不大。
II
J
£
33
■■
四夹具的结构设计
夹具的总体结构为盘类形状
五定位元件的选择及要求
本夹具选用的定位元件是两个定位心轴,因为这种类型的心轴适
用于直径在50mm以下的孔定位。
限制了操纵杆支架6个自由度。
用两个垫板限制操纵杆支架底面一个自由度。
垫板的定位基面必须有足够的精度,因为工件的定位是通过定位副的接触实现的,垫板的精度直接影响工件的定位精度,因此,该定位盘基面应有足够的精度,以适应操纵杆支架的加工要求。
该垫板应有足够刚度和强度,垫板不仅限制工件的自由度,还有支撑工件,承受夹紧力和切削力的作用,所以应该有足够刚度和强度,以免使用中变形或破坏。
定位盘的耐磨性好,操纵杆支架的装卸会磨损定位元件的定位基面,导致定位精度下降。
定位盘的工艺性要好,定位盘的的结构应力求简单,合理,便于加工,装配和更换。
定位盘的材料:
HT45,
6夹紧元件的选择
本夹具夹紧元件,采用螺旋夹紧。
7夹具体的设计
夹具材料选用45,盘类结构。
夹具体采用铸件。
8夹紧方案的设计
夹紧力的作用点在操纵杆支架定位基面的对面,落在定位盘的支承范围内,保证定位可靠,作用点处在操纵杆支架刚性较好的部位,减小了夹紧变形。
夹紧力的方向:
夹紧力的方向朝向操纵杆支架定位底面以保证操纵杆
支架的定位精度。
该夹紧力的方向有利于减小夹紧力,在工件上铣床上铣销,夹紧力因于铣销轴向力工件的重力同向,切削力、重力由夹具的固定支承承受。
切削扭矩由夹紧力所产生的摩擦力矩平衡,轴向力和重力所产生的摩擦力矩有利于减小所需夹紧力。
故所需夹紧力可最小。
夹紧力对工件定位的可靠性、工件和夹具的变形、夹紧机构的复杂程度和传动装置的选择有很大的影响。
夹紧力的大小计算涉及到复杂的动力平衡问题,这里只作粗略的估算。
Fj二KFo=1.5X600=900N
1.夹紧元件的结构:
在夹紧机构中多数是以斜锲夹紧机构、螺旋夹紧机构以及偏心夹紧机构为基础构成的,这三种夹紧机构合称为基本夹紧机构。
本夹紧机构采用螺旋夹紧机构,它的结构形式变化最多,选用典型的移动压板,它的结构紧凑,使用方便。
2.夹具与工作台安装联结方式:
本铣夹具通过定位键与铣床工作台
T形槽的配合来确定夹具在机床上的位置。
定位键采用沉头螺钉固定在夹具体底面的纵向槽中,使用两个,两定位键的距离较远,定位精度较好。
定位键与夹具体的配合为H7/h6。
为提高夹具安装精度,定位键的下部(与工作台T形槽配合部分)可留有余量进行修配,或者在安装夹具时使定位键一侧与工作台T形槽靠紧,以小轴间隙的影响。
铣床夹具的夹具体设计有耳座,并通过M16的螺栓将夹具紧固
在机床的工作台T形中,耳座的间距与T形槽的间距一致。
9夹具设计及操作的简要说明
本夹具用在立式铣床上加工操纵杆支架的上表面.
工件以底面,侧面,后面定位,在孔11的地方用快速螺旋夹紧机构夹紧,旋转手柄,当加工完毕后,扳手顺时针转动,使工件与夹具体之间松开。
及可换另一零件加工
铣床夹具的装配图及夹具主要零件图分别见图纸
-t-
作新{會〒
iifcjvgg
FT
JI
n
-!
■.BTfl
31_
■I
■k
w1-L-^PII
T*
■rR.
ir
II"Bl,,-.SW
II2■■«**!
JJT"
*
■P
I4
I
|F1
—
■
IISB
f;
1
1
jle
ri'
>
n
1
ST
-
iTfa
S
i"
J'
Tf
P
■!
•
■*
r
!
1
■1
E5E^SSISii
■
■
■
I
典
吃穿二召以电比專RM45
**5ji_f5<1士注**W
i
114-"1]
//«014\11
ggiizi
I,,wL
iI
11
n
f打亠
□Z迸
」
「1十丁歹
+I
o
4
第三部分设计体会
课程设计是对我们所学课程知识的总结。
通过课程设计可以体现
出我们在校期间的学习程度。
从而对我们所学专业知识做出有力判
断。
从我们拿到零件图纸的第一天开始,我们的老师就详细给我们讲了设计的步骤,还安排了辅导时间。
为我们圆满的完成任务奠定了良好的基础。
我们以前所接触的只是课本上的知识,对机械加工工艺只有侧面的了解。
但是同过这次设计,我们才全方位的懂得了什么是机械设计,从而更加了解了我们的专业。
刚开始设计的时候,总觉的难度很大,不知道从什么地方下手,对一些设计的步骤根本不知道怎么安排,怎么设计。
老师给我们详细讲解了机械设计应注意的条件,让我们先从分析零件图开始,然后在得出零件技术要求,在根据零件的技术要求画出毛坯和零件合图。
在设计期间,我们第一次接触了机械加工工艺的设计,对我有了很大提高。
遇到不懂的问题时,指导老师们都能细心的帮助我。
同学之间虽然每个人的设计课题不一样,但我们之间还是会经常讨论,互相帮助,不紧学会了知识,而且还锻炼了我们的团队精神。
在这次设计中,要感谢我们的指导老师,他们在设计期间为我们的解决了很多难题。
相信我们通过这次设计,一定会在以后的工作岗位中更好的发挥。