操纵杆支架加工工艺及底面铣削夹具设计.docx
《操纵杆支架加工工艺及底面铣削夹具设计.docx》由会员分享,可在线阅读,更多相关《操纵杆支架加工工艺及底面铣削夹具设计.docx(14页珍藏版)》请在冰豆网上搜索。
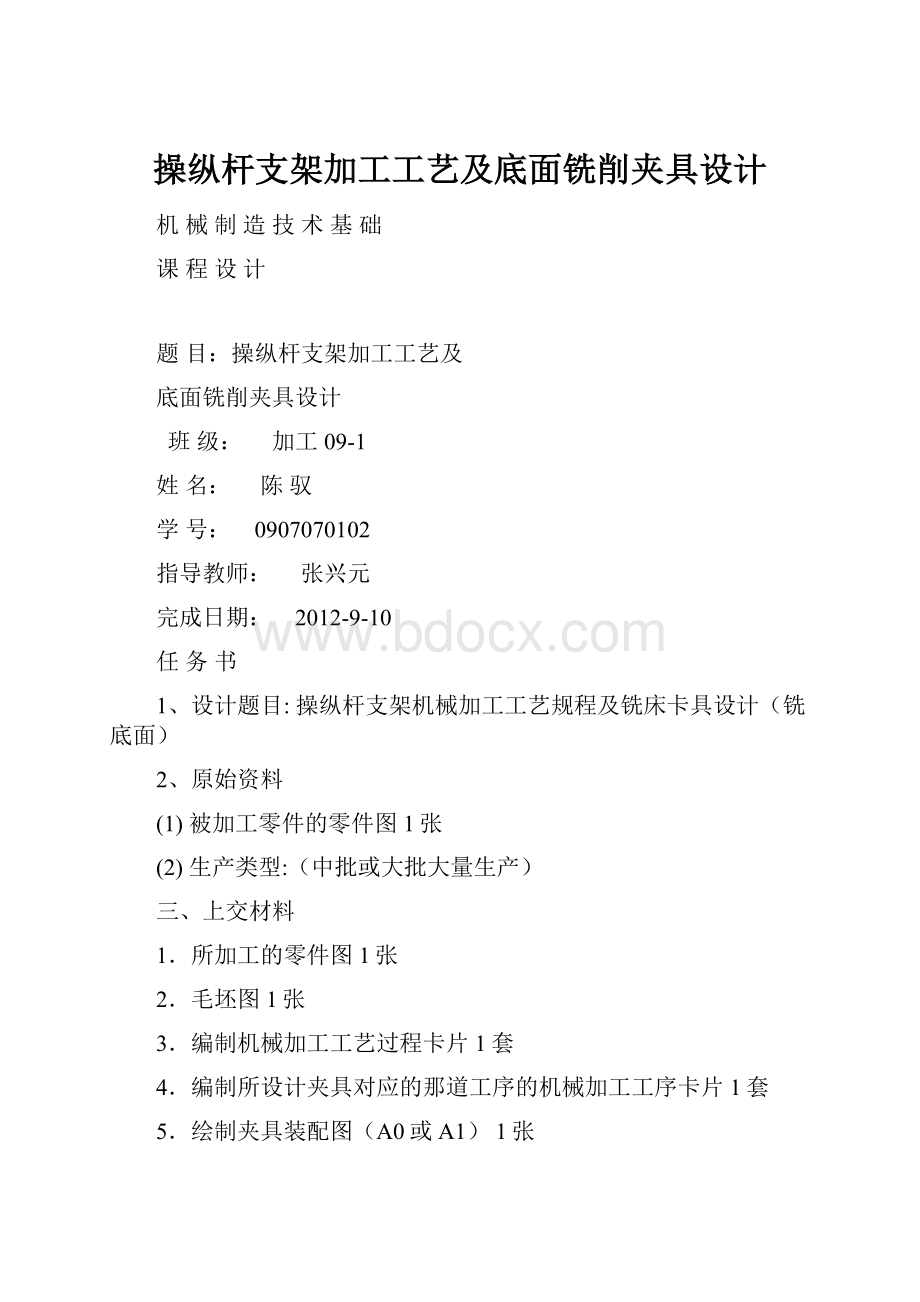
操纵杆支架加工工艺及底面铣削夹具设计
机械制造技术基础
课程设计
题目:
操纵杆支架加工工艺及
底面铣削夹具设计
班级:
加工09-1
姓名:
陈驭
学号:
0907070102
指导教师:
张兴元
完成日期:
2012-9-10
任务书
1、设计题目:
操纵杆支架机械加工工艺规程及铣床卡具设计(铣底面)
2、原始资料
(1)被加工零件的零件图1张
(2)生产类型:
(中批或大批大量生产)
三、上交材料
1.所加工的零件图1张
2.毛坯图1张
3.编制机械加工工艺过程卡片1套
4.编制所设计夹具对应的那道工序的机械加工工序卡片1套
5.绘制夹具装配图(A0或A1)1张
6.绘制夹具中1个零件图(A1或A2。
装配图出来后,由指导教师为学生指定需绘制的零件图,一般为夹具体)。
1张
7.课程设计说明书,包括机械加工工艺规程的编制和机床夹具设计全部内容。
(约5000-8000字)1份
四、进度安排
本课程设计要求在3周内完成。
1.第l~2天查资料,绘制零件图。
2.第3~7天,完成零件的工艺性分析,确定毛坯的类型、制造方法,编制机械加工工艺规程和所加工工序的机械加工工序卡片。
3.第8~10天,完成夹具总体方案设计(画出草图,与指导教师沟通,在其同意的前提下,进行课程设计的下一步)。
4.第11~13天,完成夹具装配图的绘制。
5.第14~15天,零件图的绘制。
6.第16~18天,整理并完成设计说明书的编写。
7.第19天~21天,完成图纸和说明书的输出打印。
答辩
五、指导教师评语
该生设计的过程中表现,设计内容反映的基本概念及计算,设计方案,图纸表达,说明书撰写,答辩表现。
综合评定成绩:
指导教师 日 期
摘 要
机械制造工艺课程设计是在我们完成了全部基础课、技术基础课、大部分专业课以及参加了生产实习之后进行的。
这是我们在进行毕业设计之前对所学各课程的一次深入的综合性的复习,也是一次理论联系实际的训练,因此,它在我们四年的大学生活中占有重要的地位。
通过本次课程设计,应该得到下述各方面的锻炼:
1.能熟练运用机械制造工艺设计中的基本理论以及在生产实习中学到的实践知识,正确地解决一个零件在加工中的定位、夹紧以及工艺路线安排、工艺尺寸确定等问题,保证零件的加工质量。
2.提高结构设计的能力。
通过设计夹具的训练,应当获得根据被加工零件的加工要求,设计出高效、省力、经济合理而且能保证加工质量的夹具的能力。
3.学会使用手册及图表资料。
掌握与本设计有关的各种资料的名称、出处、能够做到熟练运用。
Abstract
Mechanicalmanufacturingtechnologycoursedesignisinourcompletedallbasiccourse,technologybasiccourse,mostprofessionalcourseandtookpartintheproductionpracticeofafter.Thisisourgraduationdesigninthecoursetolearnbeforeafurthercomprehensivereview,isalsoatheorywithpracticetraining,therefore,itinourfouryearuniversitylifeoccupiesanimportantposition.
Throughthiscurriculumdesign,shouldhavethefollowingvariousaspectsofexercise:
1.Abletoskillfullyusemechanicalmanufacturingprocessdesignofthebasictheoryandproductionpracticeinmiddleschooltopracticeknowledge,properlysolveapartintheprocessingofpositioning,clampingandprocessroutearrangement,processtodeterminesizeandsoon,andensurethequalityofpartsprocessing.
2.Improvetheabilitytostructuredesign.Throughthefixturedesigntraining,shouldbegivenaccordingtobeprocessingpartsprocessingrequirements,designthehighefficiency,energysaving,economicreasonableandcanguaranteethemachiningqualityoftheabilityoffixture.
3.Learnhowtousemanualandchartmaterial.Masterandthisdesignrelatedmaterialname,origin,canskillfullyuse.
目录
1、零件分析…………………………………………
(1)
1.1零件的作用……………………………………
(1)
1.2零件的工艺分析………………………………
(1)
2、工艺规程的设计…………………………………
(1)
2.1选择毛坯种类并确定制造方法………………
(1)
2.2基面的选择……………………………………
(1)
2.3制订定工艺路线………………………………
(2)
2.4工艺路线的比较与分…………………………(3)
2.5机械加工余量、工序尺寸及毛坯尺寸的确…(4)
2.6确定切削用量及基本工时…………………(4)
3、夹具的设计………………………………………(7)
3.1问题的提出……………………………………(7)
3.2夹具设计的有关设计…………………………(7)
4、设计感言…………………………………………(9)
5、参考文献…………………………………………(10)
1.零件的分析
1.1支架的的作用
题目所给定的零件是汽车换挡部分的操纵杆支架,它的主要作用是固定操纵杆,使其在行驶过程中牢固可靠。
零件上的3-Φ11孔用螺栓固定在底座上,操纵杆用Φ20的定位销固定在支架上,并且在换挡时依靠利用36槽轨迹不会引起偏差。
1.2支架的技术要求
操纵杆支架共有4组加工表面,分析如下:
(1)支架底面
(2)2-Φ20孔
(3)36槽
(4)3-Φ11孔
该零件外形较小、形状特殊、结构简单,属典型的支座类零件。
为实现换挡的功能,其2-Φ20孔,公差要求较严格,但其它加工面公差要求较低,并且无位置度要求,但是为了满足装配性能,根据现场实际,在加工过程中要制定工艺基准,并制定出工艺公差,利用工艺基准来加工后续工序。
1.3支架的工艺性
分析零件图可知,支架的底面、内壁均要求切削加工。
底座铸造时中心较低,可减少切削加工面积,且底座无位置精度要求,做粗基准。
2-Φ20孔外壁有角度,钻削时需防止钻偏。
3-Φ11孔仅作为螺栓的通过孔,精度要求不高。
故整个零件可用普通加工设备加工,最后精镗2-Φ20孔
1.4支架的生产类型
依设计题目知:
Q=800台/年,m=1件/台;结合生产实际,备品率α%和废品率β%分别取3%和0.5%。
代入公式(1-1)得
N=800台/年×1件/台×(1+3%)×(1+0.5%)=8281.2/年
由表1-4知,该支架的生产类型为大批生产;该支架重为3.5kg,由表1-3知,该支架属轻型零件。
2.工艺规程设计
2.1选择毛坯种类并确定制造方法
操纵杆支架材料为灰铁件,牌号HT150,零件年产量为8000件,已达大批生产的水平,而且零件的轮廓尺寸不大,故可采用精铸件,这从提高生产率、保证加工精度上考虑也是应该的。
2.2基面的选择
基面选择是工艺规程设计中的重要工作之一。
基面选择得正确与合理,可以使加工质量得到保证,生产率得以提高。
否则,加工工艺过程中会问题百出,更有甚者,还会造成零件大批报废,使生产无法正常进行。
(1)粗基准的选择:
对于零件而言,尽可能选择不加工表面为粗基准。
而对于有若干个不加工表面的工件,则应以与加工表面要求相对位置精度较高的不加工表面做粗基准。
因为铣底面时要保证12-1.10,所以以底座上表面为粗基准。
(2)精基准的选择:
精基准的选择有利于保证加工精度,并使工件装夹方便。
在选择时,主要应该考虑基准重合、基准统一等问题。
当设计基准与工序基准不重合时,应该进行尺寸换算。
精基准选择为底面A及3-Φ11孔。
2.3制订工艺路线
制订工艺路线的出发点,应当是使零件的几何形状、尺寸精度及位置精度等技术要求能得到合理的保证。
在生产纲领已确定为大批生产的条件下,可以考虑采用万能性机床配以专用工夹具,并尽量使工序集中来提高生产率。
除此之外,还应当考虑经济效果,以便使生产成本尽量下降。
(1)工艺路线方案一
工序Ⅰ钻铣2-Φ20孔。
工序Ⅱ粗精铣底面A。
工序Ⅲ钻底面3-Φ11孔。
工序Ⅳ铣36槽。
工序Ⅴ检查
(2)工艺路线方案二
工序Ⅰ粗精铣底面A。
工序Ⅱ钻底面3-Φ11孔。
工序Ⅲ铣36槽。
工序Ⅳ钻铣2-Φ20孔。
工序Ⅴ检查
(3)工艺路线方案三
工序Ⅰ粗精铣底面A。
工序Ⅱ铣36槽。
工序Ⅲ钻铣2-Φ20孔。
工序Ⅳ钻底面3-Φ11孔。
工序Ⅴ检查
2.4工艺路线的比较与分析
上述三个工艺方案的特点在于:
方案一是先加工出2-Φ20孔,再以其为基准,加工出底面,而后以底面为基准,加工底面3-Φ11孔及36槽。
方案二是先加工出底面,再以底面为基准,加工出底面3-Φ11孔,36槽,及2-Φ20孔,这种方案基准统一。
方案三是先加工出底面,再以底面为基准,加工出36槽及2-Φ20孔,最后以36槽与Φ20做定位基准加工3-Φ11孔。
三种方案相比较,可以看出,方案一中,先以毛坯底面为粗基准,加工出2-Φ20孔,再以2-Φ20孔为基准加工底面,而后又以底面为基准,加工另外两组尺寸,由于中间变换了定位基准,不利于基准统一原则。
方案二,先加工出底面,后续加工都已底面定位,可以使加工质量得到保证,生产率得以提高。
而方案三也存在与方案一同样的弊端。
因此,我们选用方案二做为操纵杆支架的加工路线:
工序Ⅰ以底座上表面做为粗基准,粗精铣底面A。
选用X53立式铣床及专用夹具加工。
工序Ⅱ以底面A为基准,侧边采用辅助支撑,加工底面上3-Φ11孔,其中2个孔做为后续工艺定位孔,按工艺尺寸加工。
选用Z3040钻床及专用钻模。
工序Ⅲ以底面A及2-Φ11孔,一面两销定位,加工36槽。
选用X63卧式铣床及专用夹具加工。
工序Ⅳ以一面两销定位,钻铣2-Φ20孔。
选用X53立式铣床及专用夹具加工
工序Ⅴ终检。
2.5机械加工余量、工序尺寸及毛坯尺寸的确定
“操纵杆支架”零件材料为HT150,硬度HB163-229,生产类型为大批生产,采用精铸件毛坯。
根据上述资料及加工工艺,分别确定各加工表面的机械加工余量、工序尺寸及毛坯尺寸如下:
(1)底面(A面)
根据《金属机械加工工艺人员手册》表5-5,铸件最大尺寸≦120,确定底面毛坯机械加工余量为RAM=3mm。
又根据《机械制造技术基础课程设计指导书》的公式(2-1),最终机械加工的尺寸F=12,铸件公差CT=1.10,得:
铸件毛胚的基本尺寸
R=12+3+1.10=16.10mm
粗精铣一次加工完成到尺寸。
(2)3-Φ11
为工艺孔,加工时按工艺尺寸加工,直接在零件上钻铰完成。
(3)36槽
又根根据《金属机械加工工艺人员手册》表5-5,确定槽的机械加工余量为RAM=3mm。
再根据《机械制造技术基础课程设计指导书》的公式R=F-2RAM-CT/2,最终机械加工的尺寸F=36,公差等级CT=0.25,得:
铸件毛胚的基本尺寸
R=36+2×3+0.25/2=42.125mm
粗精铣一次加工完成到尺寸。
(4)2-Φ20孔
根据手册表5-58,先用钻头钻孔至Φ19,再用Φ20镗刀加工。
2.6确定切削用量及基本工时
工序Ⅰ铣底面A
(1)加工条件
工件材料:
HT150,铸件
加工要求:
粗精铣底面A。
机床:
XK7150数控铣床。
刀具:
采用成都成量工具有限公司的面铣刀刀柄及立装式立铣刀,刀具直径φ160。
刀片材料P/K,型号LZ1282,适用加工材料为铸铁等。
(2)计算切削用量
毛坯加工余量为3mm左右,根据《组合机床切削用量计算》表9,Vc选60m/min,f=0.3mm/r。
(3)确定机床主轴转速
n=VcX1000πXDc=60×10003.14×160=119r/min
按机床说明书,与119r/min相近的机床转速为95r/min
所以实际切削速度v=47.728r/min
(4)计算切削工时
t=4.2min
工序Ⅱ以底面为基准,侧边采用辅助支撑,加工底面上3-Φ11工艺孔。
(1)加工条件
工件材料:
HT150,铸件。
加工要求:
钻铰3-Φ11孔。
机床:
Z3040钻床。
刀具:
钻头选取高速钢钻头,直径Φ10.5,铰刀选取高速钢机用铰刀Φ11H9
(2)计算切削用量
①先用Φ10.5钻头钻底孔。
根据《组合机床切削用量计算》表1选取f=0.20mm/r,v=20m/min
所以n=1000vπD=1000x203.14x10.5=606r/min
按机床选取n=630r/min
实际切削速度v=20.77m/min
②用Φ11H9铰刀进行铰孔
根据《组合机床切削用量计算》表6,选取f=0.5mm/r,v=6m/min
所以n=1000vπD=1000×63.14×11.=173.7r/min
按机床选取n=200r/min
实际切削速度v=6.9m/min
(3)计算切削工时
钻削一孔:
t=0.72min
铰削一孔:
t=1.8min
总切削时间:
0.72×3+1.8×3=7.5min
工序Ⅲ以底面及Φ11孔,一面两销定位,加工36槽。
(1)加工条件
工件材料:
HT150,铸件。
加工要求:
铣36槽。
机床:
X63卧式铣床。
刀具:
选用可调式三面刃铣刀,直径Φ120,刀片767,加工铸铁件。
(2)计算切削用量
根据《组合机床切削用量计算》表9,选取Vc=60m/min,f=0.2mm/r
确定机床转速
n=Vc×1000π×Dc=60×10003.14×120=159.2r/min
按机床说明书,与212.3r/min相近的机床转速为150r/min
所以实际切削速度v=56.52m/min
(3)计算切削工时,
t=4min
工序Ⅳ以一面两销定位,钻镗2-Φ20孔
(1)加工条件
工件材料:
HT150,铸件。
加工要求:
钻铣2-Φ20孔。
机床:
X53立式铣床。
刀具:
采用钻镗的形式,先用Φ19高速钢钻头钻出底孔,再用Φ20镗刀精加工。
①先用Φ19钻头钻底孔
根据《组合机床切削用量计算》表9,选取f=0.2mm/r,v=40m/min
所以n=1000vπD=1000×403.14×19.=670r/min
按机床选取n=600r/min
实际切削速度v=35.796m/min
②用Φ20成型镗刀进行镗孔
根据《组合机床切削用量计算》选取f=0.15mm/r,v=70m/min
所以n=1000vπD=1000×703.14×20.=581r/min
按机床选取n=600r/min
实际切削速度v=37.68m/min
(3)计算切削工时
钻削时间:
t=2.3min
铰削时间:
t=1.2min
总切削时间:
t=3.5min
工序Ⅴ检查
3、夹具的设计
为了提高劳动生产率,保证加工质量,降低劳动强度,需要设专
用夹具。
经过与指导老师协商,决定设计第一道工序——铣底面A的铣床夹具。
本夹具将用于X52立式铣床。
刀具采用成都成量工具有限公司的面铣刀刀柄及立装式立铣刀,刀具直径φ160。
刀片材料P/K,型号LZ1282,适用加工材料为铸铁等。
3.1问题的提出
本夹具主要用来铣工件底面A,粗精铣一次完成。
在本道工序加工时,主要应考虑如何提高劳动生产率,降低劳动强度,而精度则不是主要问题。
3.2夹具设计
(1)定位基准的选择
前期方案分析过程中,是将2-Φ20孔圆弧面为粗基准,因此本工序可以2-Φ20孔圆弧面以及辅助支撑定位进行加工,主要的是设计出的夹具需要定位迅速可靠。
(2)切削力及夹紧力计算
(3)定位误差分析
(A)定位元件尺寸及公差的确定:
夹具的主要定位元件为一面及两销。
圆柱销产生的X(Y)方向定位误差△=0.043+0.043+0.046=0.132mm,能满足加工要求。
由于是通孔(槽),Y(X)向可不考虑。
底面定位基准重合,不存在基准不重合误差和位移误差。
两孔中心连线对两销中心连线的最大转角误差为:
△=2α=2cot((0.092+0.092)/2l)=0.063。
即α=0.031。
满足加工要求。
(4)夹具设计及操作的简要说明
如前所述,在设计夹具时,应该注意提高劳动生产率。
为此,夹具的实用性及劳动强度也要考虑在内。
本零件是精铸件,余量较小,切削力不是太大,需要的压紧力也不大,所以没有必要使用气动或液压夹紧,手动压紧就可以满足需要。
夹具上装有对刀块,可使夹具在一批零件的加工之前很好地对刀(与塞尺配合使用);同时,夹具体底面上的一对定位键可使整个夹具在机床工作台上有一正确的安装位置,以利于铣削加工。
铣床夹具的装配图及夹具体零件图见附图。
4、设计感言:
这次的课程设计,我们算是真正的做了一次工艺人员,由方案的出台、查表、计算到夹具的设计,都由我们自己独立思考亲自操作完成的。
在这次课程设计当中,我们重温了《机械制造技术基础》、制图的课本知识,第一次感受到了运用所学的知识来指导实践所带来的快乐,同时也提高了我们查图、查表的能力,也算是为以后的工作提前进行了适应。
更重要的是,在此过程当中,我们明确了做为一个工程技术人员应该具有的认真、仔细的素养,也是机械人员最基本的素养,在以后的学习、工作当中,必须重视这种这素养的培养;同时,我们也认识到团队合作的可贵,1加1大于2,我们一次次的对方案进行讨论、修改,使我们的方案逐渐走上成熟,各种疑团都得到了解决,团结合作是我们完成工作的保证。
三周的课程设计是如此短暂,但在此过程中所学到的东西将指引我们以后的学习工作。
感谢老师的指导。
参考文献:
[1]、黄健求主编,机械制造基础[M],北京:
机械工业出版社,2011范
大学出版社,2007
[2]、李益明主编,机械制造工艺设计简明手册[M],北京:
机械工业出
版社,2007
[3]、艾兴等编,切削用量简明手册[M],北京:
机械工业出版社,2002
[4]、东北重型机械学院等编,机床夹具设计手册[M],上海:
上海科技出版社,1990
[5]、邹青主编,机械制造技术基础课程设计指导教程[M],北京:
机械工业出版社,2004
[6]、段明扬主编,现代制造工艺设计方法[M],桂林:
广西师范大学出
版社,2007
[7]、崇凯主编,机械制造技术基础课程设计指南[M],北京:
化学工业出版社,2007
[8]、华楚生主编,机械制造技术基础[M],重庆:
重庆大学出版社,2000
[9]、段明扬主编,现代机械制造工艺设计实训教程[M],桂林:
广西师
[10]、吴拓主编,简明机床卡具设计手册[M],北京:
化学工艺出版社2010.2