制动钳设计资料全.docx
《制动钳设计资料全.docx》由会员分享,可在线阅读,更多相关《制动钳设计资料全.docx(147页珍藏版)》请在冰豆网上搜索。
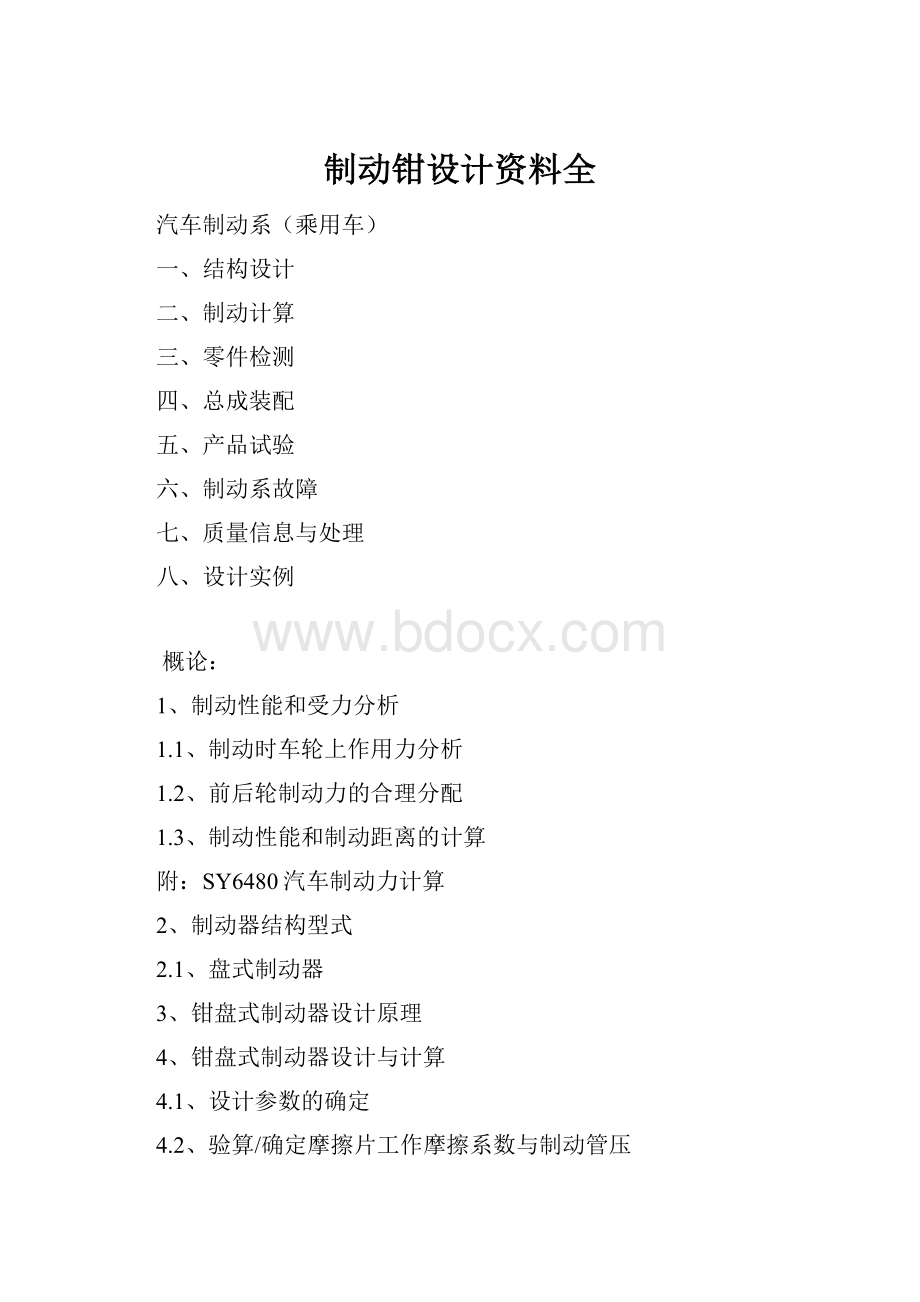
制动钳设计资料全
汽车制动系(乘用车)
一、结构设计
二、制动计算
三、零件检测
四、总成装配
五、产品试验
六、制动系故障
七、质量信息与处理
八、设计实例
概论:
1、制动性能和受力分析
1.1、制动时车轮上作用力分析
1.2、前后轮制动力的合理分配
1.3、制动性能和制动距离的计算
附:
SY6480汽车制动力计算
2、制动器结构型式
2.1、盘式制动器
3、钳盘式制动器设计原理
4、钳盘式制动器设计与计算
4.1、设计参数的确定
4.2、验算/确定摩擦片工作摩擦系数与制动管压
4.3、主要配合部位尺寸与形状公差原则
4.4、活塞密封部位的核算(压缩率)
4.5、密封槽部位的设计(形状)
4.6、钳体导向滑动部位设计
4.7、导向部位密封核算(压缩率)
4.8、设计基准的确定(钳体,支架)
4.9、摩擦片与制动盘的设定间隙(自由状态时)
4.10、制动钳总成与周围零部件关系
4.11、主要零件设计
4.12、设计校核
6、制动器零部件的检测与总成装配
6.1、盘式制动器
6.1.1、零部件检验
6.1.2、制动钳装配
6.2、鼓式制动器
6.2.1、零部件检验
6.2.2、鼓式制动钳装配
7、制动系和制动器的试验与检测
7.1、制动系试验
7.1.1、滚筒式测力器
7.1.2、汽车制动系道路试验
7.1.3、制动系试验标准
7.1.4、车辆路试概况
7.2、制动器试验
7.2.1、制动钳盘式制动器
7.2.1.1、性能项目:
密封性能-真空密封,高压密封,低压密封
所需液量,拖滞扭矩,钳体刚性,活塞滑动阻力,钳体滑动阻力
7.2.1.2、强度项目:
耐压破坏强度,扭转强度
7.2.1.3、可靠性项目:
高压耐久,扭转耐久,常温工作耐久,高温工作耐久,低温工作耐久,
振动耐久,防水性能,耐腐蚀性,低温泄漏,放气螺钉强度,
放气螺钉性能,螺纹破坏强度,长期存放橡胶件耐候性,耐泥水振动耐久
7.2.2.2、液压制动轮缸技术条件
7.2.3、制动器制动性能试验
7.2.3.1、制动性能的试验项目
7.2.3.2、制动性能的试验标准
7.2.3.2.1、中国汽车行业标准
7.2.3.2.2、日本汽车行业标准
7.2.3.2.3、美国汽车行业标准
7.2.3.2.4、德国汽车行业标准
附录4:
中,日,德等制动器台架性能试验
7.3、部件试验
7.3.1、中国GB5763—汽车用制动器衬片
7.3.2、美国SAEJ661a—制动衬片质量控制试验程序
7.3.3、德国大众公司PV3212—制动衬片摩擦系数试验台上进行摩擦系数与磨损试验-盘式制动器
PVW3211—制动衬片摩擦系数试验台上动摩擦力矩与磨损试验-鼓式制动器
7.3.4、日本JASOC418—制动器摩擦片摩擦性能试验方法
7.3.5、日本JASOC427—制动器摩擦片磨损在测功机上试验方法
7.3.6、摩擦片,衬块的物理试验(中,日,美)
7.3.7、制动钳的制动噪音试验(日,美资料)
7.3.8、制动系其他主要部件的试验有关标准(中)
7.3.9、汽车防抱死装置(中,美,德)
7.3.10、制动器橡胶密封件(中,日)
附录:
1\典型国家和地区摩擦材料试验资料(定速机)
2\日-丰田公司TSD7325G制动尖叫,异响,振动评价方法
3\日-丰田公司TSD7301G
4\德-SABS制动防抱死功能评价,路试规
ATE产品技术条件
ATE集成电子控制产品技术条件
5\日-丰田公司盘式制动器防尘罩用橡胶材料
8、制动系统故障
8.1、制动系统故障概述
8.2、制动系故障的形成和原因
8.3、制动鼓和制动盘故障的形成
8.4、制动系故障的分析
9、用户的质量反馈与技术分析
9.1、制动器安装的设计位置与外形干涉(新设计产品)
9.2、制动器在悬架总成上工作状况不良
9.3、汽车调试线上制动力问题(单轮不足,两轮不均)
9.4、试车中制动跑偏
9.5、试车中制动侧滑
9.6、试车中制动时车身抖动
9.7、试车与使用中制动器发啃
9.8、试车与使用中轮毂轴头发热
9.9、使用中摩擦片过度磨损
9.10、使用中制动盘的过度磨损
9.11、使用中制动噪音
9.12、生产者的质量责任
10、设计实例(夏利汽车(TJ7100)制动计算
10.1、理想制动力与实际制动力分配
10.2、附着系数与制动效率
10.3、踏板力—制动管压,制动力,制动距离
10.4、摩擦副能量设计评价
SY6480制动钳总成装配
一、装配前的准备工作:
1、装配前各组装零部件应除尘、除油、清洁干燥
1.1\清洗液温度:
50—70℃
1.2\干燥条件:
60--80℃x60s以上
2、活塞矩形密封圈的预处理:
2.1\润滑脂:
橡胶润滑脂(TSK2511-2)/JISK2228-2种或硅脂7502
2.2\温度:
70±2℃处理时间:
10—12小时
3、装配前在钳体活塞孔底部喷涂防锈油(TSK7503-2)/JISK2228-1种0.1—0.5g,说明:
防锈油为非矿物质油
4、装配活塞矩形密封圈时,应在钳体密封槽和矩形密封圈四周涂橡胶润滑脂0.2—0.5g
5、装配活塞防尘罩时,应在钳体活塞防尘罩涂橡胶润滑脂0.4g,装入卡簧(定位环)时,注意不能刺伤活塞防尘罩,并保证活塞防尘罩装配正确,不能有折边现象,卡簧装入到位.
6、装配导向销部分时;
6.1\钳体导向孔\防尘槽应涂一定量的润滑脂;
6.2\导向防尘罩壁与外圈应涂一定量的润滑脂
6.3\衬套孔外圆周涂一定量的润滑脂
6.4\注意所有橡胶件装配后不能有损伤.折边现象,注意排除气阻.
二、装配过程:
2.1、工序名称:
零件准备
容:
矩形密封圈应用放大镜(5—10倍)全检,无毛刺、飞边、缺料、破损、划伤等缺陷
矩形密封圈应提前做好预处理(恒温箱70℃x(10—12小时)加一定量的橡胶润滑脂浸润
钢质零件清洗干净、干燥
衬套外部涂脂
导套防尘罩涂脂
2.2、工序名称:
钳体、活塞矩形密封圈组装
容:
钳体活塞孔涂定量橡胶润滑脂(矩形密封槽与防尘罩槽)
矩形密封圈手工装入,周向抹平
批量生产时,涂脂前钳体活塞孔底部应喷非矿物质防锈油
2.3、工序名称:
钳体、活塞装入
容:
活塞防尘罩套在活塞上(过渡段以上)
手工压入活塞至矩形密封圈处
如采用机械或气动装置装入活塞至钳体活塞孔底部,压入力应≤500N,当压入力>500N时,产品应隔离,检查,查明原因。
2.4、工序名称:
钳体、定位环装入防尘罩
容:
定位环一端先装入活塞防尘罩,小心装入,抹平定位环,装配后,定位环两端应有1—3mm间隙
用定扭矩扳手将放气螺钉拧入,力矩要求8—13N.m
2.5、工序名称:
密封性检测
容:
按要求作真空,高低压密封性检测,
低压密封性检查:
气试:
P=0.1MpaX5s,无泄漏
高压密封性检查;气试P=3MpaX5s,无泄漏
2.6、工序名称:
支架与摩擦片装配
容:
按要求装入锁片,装配到位,
报警片装入摩擦片凹坑
将摩擦片分别装入支架槽
2.7、工序名称:
钳体衬套/导套/防尘罩安装
容:
将长短衬套装入钳体
先将一个防尘罩装入钳体,一导套端部套装一个防尘罩,导套上的防尘罩配合部位装钳体,导套均匀穿过2个防尘罩
2.8、工序名称:
钳体与支架组装
容:
长短螺栓联接(扭力M=35—45N.m)
两摩擦片距离>27mm
2.9、工序名称:
拖滞扭矩检测
容:
检测产品外形轮廓,
拖滞扭矩小于3.5N.m
按要求包装
汽车制动系
一、概论:
1、基本功能:
1.1、以适当的减速度降低车速到所需要值(包括零值)-----减速、停车
1.2、原地停车或驻车
2、组成部分:
2.1、制动器-----对车轮产生摩擦阻力
2.2、驱动机构----对制动器进行驱动
3、设计要求
3.1、可靠的制动能力
3.2、保证汽车在各车速和减速度工况情况下的制动力
3.3、制动能力的热稳定性
保证车辆在持续制动,重复制动的高温情况下,制动能力衰退率小,并且衰退后能较好地恢复。
3.4、制动能力的水稳定性
保证车辆在行驶中,制动器有水侵入时制动能力下降,出水后能较快地恢复到一定能力。
3.5、车辆制动的方向稳定性
设计和制造应保证前后轴间的制动力合理分配和左右两轮制动力差异大小,避免和减小车辆制动侧滑与跑偏。
3.6、车辆的驻坡能力
保证汽车在规定路面上(坡度\附着系数),有效地停驻而不下滑。
3.7、部分失效可靠性
保证系统中,部分失效后,剩余制动能力的安全程度。
3.8、操纵轻便性
规定车辆一定的踏板行程与操作力,不能过大,也不宜过小。
3.9、作用滞后性
尽量减少制动作用开始滞后时间和解除制动恢复的滞后时间。
3.10、公害程度
减少粉尘污染和制动噪声。
3.11、调整和维修方便
制动衬片与制动鼓、制动盘间隙由于磨损而加大,需要调整方便而出现多种调整方法。
2.3.5.1、盘式制动器
Mf=Af.Pf.2μ.Rf(N.m)
式中:
Af—活塞作用面积(mm2)
Pf—前轮制动管压(Mpa)
μ—前摩擦片摩擦系数
Rf—活塞作用半径(mm)
例:
SY6480
A=66.7^2x0.7854=3494(mm2)
Pf=7μ=0.35Rf=103
M单轮=3494x7x2x0.35x0.103=1864N.m
FBF=M/r=1864/0.313=5956(N)=608(kgf)FBF:
地面制动力r-轮胎半径0.313m
附:
SY6480汽车制动计算
1\计算参数:
空载Go1675Kgf
Go1899Kgf
Go2776Kgf
Ho617mm
满载Ga2692Kgf
Ga11255Kgf
Ga21437Kgf
Hg699mm
轴距L2590mm
Lo1=1200Lo2=1390La1=1383La2=1207
滚动半径rk=314mm
(比例阀调节曲线)
图示4:
2\汽车静轴荷分配
参数
空戟
满载
整车载荷G(kgf)
1675
2692
前轴载荷G1(kgf)
899
1255
前轴负荷分配%
53.67
46.62
后轴载荷G2(kgf)
776
1437
后轴负荷分配%
46.33
53.38
3\汽车动轴荷分配
减速度变化时轴荷值(Gd)(kgf)
j/g
0.1
0.2
0.3
0.4
0.5
0.6
0.7
0.8
0.9
1.0
空
载
前轴
938.9
978.8
1018.7
1058.6
1098.5
1138.4
1178.3
1218.2
1258.1
1298
后轴
736.1
696.2
656.3
616.4
576.5
536.6
496.7
456.8
416.9
377
满
载
前轴
1327.6
1400.3
1473
1546
1618
1691
1764
1836
1909
1982
后轴
1364.4
1291.7
1219
1146
1074
1001
928
856
783
710
减速度变化时轴荷分配比(%)
j/g
0.1
0.2
0.3
0.4
0.5
0.6
0.7
0.8
0.9
1.0
空
载
前轴
56.0
58.4
60.8
63.2
65.6
68.0
70.3
72.7
75.1
77.5
后轴
44
41.6
39.2
36.8
34.6
32.0
29.7
27.3
24.9
22.5
满
载
前轴
49.3
52.0
54.7
57.4
60.1
62.8
65.5
68.2
70.9
73.6
后轴
50.7
48.0
45.3
42.6
39.9
37.2
34.5
31.8
29.1
26.4
4\理想制动力计算
汽车以不同减速度(j/g)制动时,前\后轮(轴)各需制动力
前轮:
FF=GDF.j/g
后轮:
FR=GDR.j/g
(kgf)
j/g
0.1
0.2
0.3
0.4
0.5
0.6
0.7
0.8
0.9
1.0
空
载
前轴
93.9
195.8
305.6
423.4
549
683.0
824.8
974.6
1132.3
1298
后轴
73.6
139.2
196.9
246.6
288.2
322
347.7
365.4
375
377
满
载
前轴
133
280.1
442
618
809
1015
1235
1469
1718
1982
后轴
136
258
366
458
537
601
650
685
705
710
5\制动器实际产生制动力(地面制动力)
前轮
FB1=MF/rk=608(kgf)
后轮
FR1=MR/rR=298.2(kgf)
前后轮制动力比例:
FB1/FR1=2.039(线性比例)
6\前后轮同步抱死时的减速度
前后轮理想需要的制动力曲线与制动器实际产生的制动力直线相交,即为前后轮同时抱死点.解下列联立方程,可得出同时抱死点减速度值.
(1)FB/FR=(GDF/GDR).(α/g)
(2)FB/FR=2.039
由
(1)
(2)解方程得:
空载时;(GoF+Go.Ho/L.j/g)/(GoR-Go.Ho/L.j/g)
=(899+1675x617/2590Xj/g)/(776-1675x617/2590xj/g)=2.039
j=0.56g
满载时:
(GaF+Ga.Hg/L.j/g)/(GaR-Ga.Hg/L.j/g)
=(1255+2692x699/2590Xj/g)/(1437-2692x699/2590xj/g)=2.039
j=0.76g
二、制动器结构型式
1、盘式制动器
2.1\按结构型式
固定钳式—刚性好,较复杂,要求高
浮动钳式—较普通,较简单,成本低,刚性差
2.2\按活塞作用方式
对置式—如固定钳
双缸/多缸式---减少径向布置尺寸,增大活塞作用半径,压力分布均匀
三、钳盘式制动器设计原理
1、作用特点
制动力矩平稳—效能BEF=2μ=K线性关系特别是乘用车采用
热稳定性好---摩擦件暴露,易散热,热衰退率低
水恢复性好—浸水后易除水,又平面接触,第1次即很高恢复力矩,鼓式需几次以后
间隙自调,易维护—自动调整摩擦片间隙,维护方便,换件简易.
效能因数低(增益小)—要求增大驱动力(增加液压)密封性和液体气化,要求高.
2、活塞回位原理与自动补偿功能
图示5
3、盘式制动器制动力矩计算与参数设计
3.1\制动力矩的计算:
图示6:
R1,R2摩擦片、外半径
δ摩擦片夹角
Mr=∫R∫δμPr^2drdδ式中μ为摩擦系数P为摩擦片上的单位压力
求解后:
Mr=2μPKRm
其中:
K=2δ/3sinδ/2.(1-R1R2/(R1+R2)^2)
Rm=(R1+R2)/2
δ摩擦片夹角增大,Mr制动力矩增大,故δ角度应适量.
δ从40°~80°Mr将增大6.6%
3.2\参数设计
主要考虑尺寸布置和材料情况.
μ:
0.30~0.45,承压面积(温升,磨损)
P:
一般10Mpa以下
R1,R2应考虑安装间隙
四、钳盘式制动器设计与计算
1、设计参数的确定:
1.1\整车质量:
空载时:
Kg前轴Kg后轴Kg
满载时:
Kg前轴Kg后轴Kg
1.2\车辆重心高度:
空载时:
Homm满载时:
Hgmm
1.3\轴距LmmL1mmL2mm
1.4\轮胎滚动半径rmm
1.5\车轮轮网与辐条型式(或制动钳安装尺寸)
1.6\制动盘外缘直径与宽度,制动盘轮毂外缘直径
1.7\摩擦片材料设计要求(材料类型,指定性能,测试标准)
1.8\制动器总成性能设计要求(制动性能,基础性能,可靠性能)与试验标准和试验惯量
1.9\车辆规定最高速度Km/h
1.10\车辆规定制动液种类
1.11\制动钳支架安装平面至制动盘两平面中心距离
2、验证计算确定
摩擦片工作摩擦系数与制动管压
根据测绘,求出活塞作用半径R
根据设计文件提供的摩擦系数μ或制动管压,求得制动管路压力,一般P=7~8MPa
3、主要配合部位尺寸与形状公差原则
3.1\活塞,钳体活塞孔配合
间隙配合:
0.06~0.10(主要考虑密封,兼考虑密封槽同轴度等)
钳体活塞孔基孔制H8φ30~500-+0.039φ50~800-+0.046
活塞松动配合f7φ30~50-0.025-0.05φ50~80-0.03-0.06
表面粗糙度3.2(活塞孔)活塞表面1.6
3.2\导销与销孔
一般分为上(主)下(副)销不同配合型式
主孔
(1)ΦD(0+0.04)H9导销Φd(-0.15-0.19)b9
副孔
(2)ΦD(0+0.04)H9导销Φd(-0.29-0.33)a9
3.3\形状公差
设计基准:
钳体:
两爪表面A支架:
安装孔端平面
设计要求:
活塞孔相对于A面有垂直度要求:
0.08~0.10
销孔
(1)
(2)相对于安装面有垂直度要求:
0.06~0.08
两销孔间有平行度要求:
0.08~0.10
5.1\设计原则:
与矩形密封圈配合,形成压力密封带,保证密封能力.
活塞受力外移时,密封圈能产生一定的变形,此变形的弹性力能使活塞在解除压力时回复至原始状态.
密封槽的轴向宽度应留有余量(比密封圈宽度宽约1mm)以保证密封圈膨胀的需要.
密封槽侧倒角,选择合适型式.
5.2\钳体密封槽槽底形状:
A\槽底斜度:
活塞外移,密封圈随之移动变形,为保证密封圈侧的密封,除了密封圈设计一定的压缩率,槽底应有一定的斜度.此数值视结构而不同,如浮动钳多为5°少的为7°,固定钳因对置活塞,每个活塞移动行程少.为3.5°.
B\外侧倒角:
是影响活塞回位量的重要因素,一般倒角增大,回位量增大,角度30°~45°底边0.45~0.9,例:
Φ48(0.45X45°)Φ51.1(0.45X41°)Φ66.7(0.7X30°)
30°倒角,活塞回位较稳定,采用比较多.
固定钳,倒角小,多为0.3~0.4x45°
C\轴向宽度:
由于密封圈压入后,产生轴方向变形,制动液浸渍后膨胀,设计时应留有30%密封圈宽度的余量,例:
密封圈宽3.2槽宽4.2
D\侧倒角:
考虑槽侧间隙液体的充溢,设计有不同侧倒角(15°30°45°60°斜度等)
E\槽底V形槽
加工槽形时,为减少切削振动和铁屑在槽卡滞,增加了此小槽,如果切削时振动不大和能保证铁屑的排除,可以不设此槽,注意加工时槽底锥形圆周面不能有振动波纹.
F\槽底两侧角度
考虑刀具磨损和对密封圈的挤压,此角度不大,一般0.2~0.5x45°或R0.2~0.5.
4、钳体导向滑动部位设计
6.1\导向滑销类(SY6500)
此类配合型式为钳体上两长销与支架上两深孔配合,配合间隙两孔不同,配合间隙也较大,主要考虑到钳体\支架孔的间距误差和销与孔的形位公差.此种情况分为两种型式:
A\等径销孔:
即两销孔孔径一样,两销子直径不同
例:
有产品两销孔φ11(0+0.04)销1φ11(-0.07-0.12)销2φ11(-0.30-0.34)
B\等径销子:
即两销孔孔径不同,两销子直径一样
例:
有产品销孔1φ9.1(0+0.04)销孔2φ9.4(0+0.04)两销子φ9(0-0.04)
意见:
考虑到导销防尘罩与销子的配合,一般多采用B\等径销子型式.
考虑到销的安装和销孔制造的形位公差,一般主销的配合间隙为0.1~0.2(多为上方安装),副销配合间隙0.3~0.4(多为下方安装).
另,主销应在制动盘旋转的切入方向一侧.
6.2\导向滑套类(SY6480)
此类配合型式为钳体两侧耳部是销孔结构,沿固定于支架或转向节上的销套滑动.
5、导向部位密封核算(压缩率)
7.1\密封的重要性
制动钳钳体滑动导向是影响制动器拖滞阻力的主要因素,处理好密封槽的设计,防尘罩的材料与性能,导向销(套)公差等是设计中重要注意问题,否则以下问题会导致阻力的加大甚至卡死.防尘罩压缩率过大(阻力增大);压缩率过小(阻力小,但密封易产生不良,易渗水,和湿气,导销/套易生锈卡滞);防尘罩本身压缩部分的厚度,材料老化性能(增大阻力或长期可靠性降低),导向销与滑动部位的润滑(润滑脂的定点,定量,润滑脂的性能影响了阻力和防尘罩的老化).
7.2\压缩率计算
A\导向销类
例:
一产品(φ54丰田科罗拉)
导向销(d)φ11(0-0.04)
防尘罩径向厚度(t)3.6(+0.2-0.1)其中橡胶厚度2.7(+0.2-0.1)铁件厚0.9
支架防尘罩槽孔径(D)φ17.15±0.05
压缩率βmax={tmax-(Dmin/2-dmax/2)}/tmax={(3.8-0.9)-(17.1/2-11/2-0.9)}/2.9=25.86%
βmin={tmin-(Dmax/2-dmix/2)}/tmin={(3.5-0.9)-(17.2/2-10.96/2-0.9)}/2.6=14.61%
B\导向套类
导套直径φ15.9±0.08(短)φ16.1±0.08(长)(d)
防尘罩径向厚度4.15±0.10(t)
密封槽底直径φ23±0.1(D)
短导套:
压缩率βmax={tmax-(Dmin/2-dmax/2)}/tmax={4.25-(22.9/2-15.98/2)}/4.25=18.58%
压缩率βmin={tmin-(Dmax/2-dmin/2)}/tmin={4.05-(23.1/2-15.82/2)}/4.05=10.1%
长导套:
压缩率βmax={tmax-(Dmin/2-dmax/2)}/tmax={4.25-(22.9/2-16.18/2)}/4.25=20.9%
压缩率βmin={tmin-(Dmax/2-dmin/2)}/tmin={4.05-(23.1/2-16.02/2)}/4.05=12.59%
建议:
钳体滑动基本属于静密封,根据一般O型圈的静密封压缩率要求,滑动阻力的计算与滑动阻力试验,推荐压缩率为15%~18%左右.
6、设计基准的确定(钳体,支架)
盘式制动器影响制动效能,拖滞扭矩,摩擦片非常磨损,偏磨,发热等现象,除了其他因素外,钳体和联连支架的设计基准选定产品设计的关键问题之一.
8.1\钳体设计基准:
分析:
活塞孔—输出作用力,与活塞有较大间隙配合,其孔的公差/形状精度,影响制动钳性能的程度不是最重要的.