汽车制造工艺学课程设计讲解.docx
《汽车制造工艺学课程设计讲解.docx》由会员分享,可在线阅读,更多相关《汽车制造工艺学课程设计讲解.docx(30页珍藏版)》请在冰豆网上搜索。
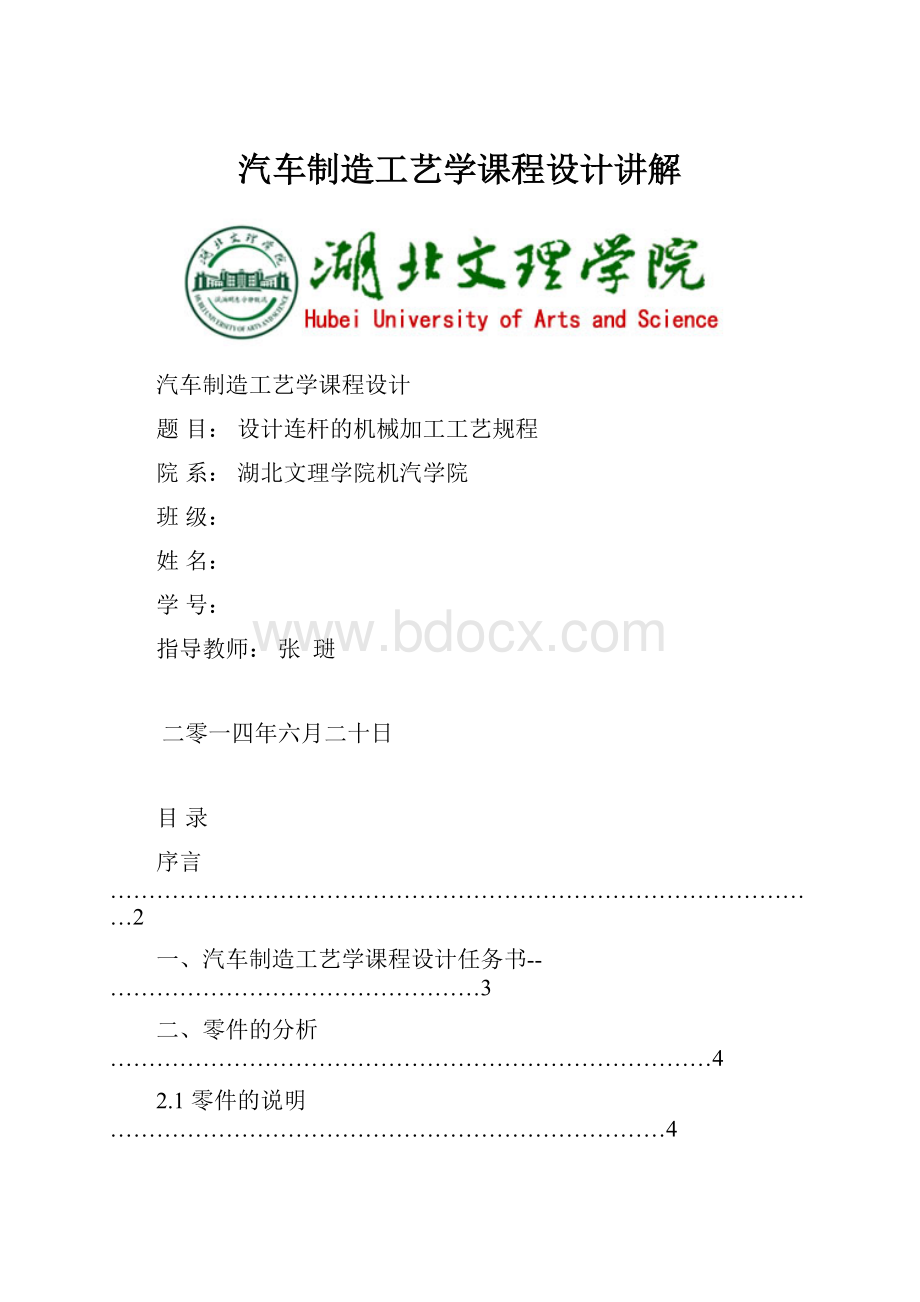
汽车制造工艺学课程设计讲解
汽车制造工艺学课程设计
题目:
设计连杆的机械加工工艺规程
院系:
湖北文理学院机汽学院
班级:
姓名:
学号:
指导教师:
张琎
二零一四年六月二十日
目录
序言…………………………………………………………………………………2
一、汽车制造工艺学课程设计任务书--…………………………………………3
二、零件的分析……………………………………………………………………4
2.1零件的说明………………………………………………………………4
2.2零件的工艺分析…………………………………………………………4
三、工艺规程设计…………………………………………………………………5
3.1连杆的材料和毛坯………………………………………………………5
3.2连杆的技术要求…………………………………………………………5
3.3确定毛坯的制造形式……………………………………………………7
3.4基准面的选择……………………………………………………………8
3.5制定工艺路线……………………………………………………………8
四、切削用量的选择原则………………………………………………………9
五、确定各工序的加工余量、计算工序尺寸及公差…………………………11
六、工时定额的计算……………………………………………………………12
七、课程设计总结………………………………………………………………21
八、参考文献……………………………………………………………………22
附件一机械加工工艺过程卡片
附件二连杆零件图
附件三连杆毛坯图
序言
《汽车制造工艺学课程设计》是我们学习完大学阶段的汽车类基础和技术基础课以及专业课程之后的一个综合的课程设计,它是将设计和制造知识有机的结合,并融合现阶段汽车制造业的实际生产情况和较先进成熟的制造技术的应用,而进行的一次理论联系实际的训练,通过本课程的训练,将有助于我们对所学知识的理解,并为后续的课程学习以及今后的工作打下一定的基础。
对于本人来说,希望能通过本次课程设计的学习,学会将所学理论知识和工艺课程实习所得的实践知识结合起来,并应用于解决实际问题之中,从而锻炼自己分析问题和解决问题的能力;同时,又希望能超越目前工厂的实际生产工艺,而将有利于加工质量和劳动生产率提高的新技术和新工艺应用到机器零件的制造中,为改善我国的汽车制造业相对落后的局面探索可能的途径。
但由于所学知识和实践的时间以及深度有限,本设计中会有许多不足,希望各位老师能给予指正。
一、汽车制造工艺学课程设计任务书
一、设计目的
汽车制造工艺学课程设计是综合运用《汽车制造工艺学》及有关课程内容,分析和解决实际工程问题的一个重要教学环节。
通过课程设计培养学生制定零件机械加工工艺规程和分析工艺问题的能力。
在设计过程中,学生应熟悉有关标准和设计资料,学会使用有关手册和数据库。
汽车制造工艺学课程设计是作为未来从事机械制造技术工作的一次基本训练。
二、设计的题目和内容
1、课程设计的题目:
设计连杆的机械加工工艺规程
条件:
年产5000件。
零件图根据自己选择的零件进行绘制。
2、设计应完成的内容:
1)制定指定零件(或零件组)的机械加工工艺规程,编制机械加工工艺卡片,选择所用机床、夹具、刀具、量具、辅具;(一套)
2)对所制定的工艺进行必要的分析论证和计算;
3)确定毛坯制造方法及主要表面的总余量;
4)确定主要工序的工序尺寸、公差和技术要求;
5)对主要工序进行工序设计,编制机械加工工序卡片,画出的工序简图,选择切削用量;(一份)
6)设计加工该零件的毛坯图或者零件与毛坯合图;(一张)
7)编写设计说明书。
(封面、目录参考附后、不少于1万字)(一份)
二、零件的分析
2.1、零件说明
连杆是汽车发动机中的主要传动部件之一,它把作用于活塞顶面的膨胀的压力传递给曲轴,又受曲轴的驱动而带动活塞压缩气缸中的气体。
连杆在工作中承受着急剧变化的动载荷。
连杆由连杆体及连杆盖两部分组成。
连杆体及连杆盖上的大头孔用螺栓和螺母与曲轴装在一起。
为了减少磨损和便于维修,连杆的大头孔内装有薄壁金属轴瓦。
轴瓦有钢质的底,底的内表面浇有一层耐磨巴氏合金。
在连杆体大头和连杆盖之间有一组垫片,可以用来补偿轴瓦的磨损。
连杆小头用活塞销与活塞连接。
小头孔内压入青铜衬套,以减少小头孔与活塞销的磨损,同时便于在磨损后进行修理和更换。
在发动机工作过程中,连杆受膨胀气体交变压力的作用和惯性力的作用,连杆除应具有足够的强度和刚度外,还应尽量减小连杆自身的质量,以减小惯性力的作用。
为了保证发动机运转平衡,同一发动机中各连杆的质量不能相差太大。
考虑到装夹、安放、搬运等要求,连杆大、小头的厚度相等(基本尺寸相同)。
在连杆小头的顶端设有油孔,发动机工作时,依靠曲轴的高速转动,把气缸体下部的润滑油飞溅到小头顶端的油孔内,以润滑连杆小头衬套与活塞销之间的摩擦运动副。
2.2、零件的工艺分析
连杆体要求加工的平面有结合面、轴瓦锁止口、螺栓孔、大头中心孔、凹槽以及端面。
其中,零件的大头中心孔和凹槽面粗糙度较低且精度要求较高,为主加工面,需要进行较精密的加工过程,其余为次加工面,没有必要进行精密加工。
根据各面的粗糙度和公差等级确定不同的加工方式。
(1)连杆体和盖厚度不一样,改善了加工工艺性。
连杆盖厚度为31mm,比连杆杆厚度单边小3.8mm,盖两端面精度产品要求不高,可一次加工而成。
由于加工面小,冷却条件好,使加工振动和磨削烧伤不易产生。
连杆杆和盖装配后不存在端面不一致的问题,故连杆两端面的精磨不需要在装配后进行,可在螺栓孔加工之前。
螺栓孔、轴瓦对端面的位置精度可由加工精度直接保证,而不会受精磨加工精度的影响。
(2)连杆小头两端面由斜面和一段窄平面组成。
这种楔形结构的设计可增大其承压面积,以提高活塞的强度和刚性。
在加工方面,与一般连杆相比,增加了斜面加工和小头孔两斜面上倒角工序;用提高零件定位及压头导向精度来避免衬套压偏现象的发生,但却增加了压衬套工序加工的难度。
(3)带止口斜结合面。
连杆结合面结构种类较多,有平切口和斜切口,还有键槽形、锯齿形和带止口的。
该连杆为带止口斜结合面.精加工基准采用了无间隙定位方法,在产品设计出定位基准面。
在连杆杆和总成的加工中,采用杆端面、小头顶面和侧面、大头侧面的加工定位方式;在螺栓孔至止口斜结合面加工工序的连杆盖加工中,采用了以其端面、螺栓两座面、一螺栓座面的侧面的加工定位方法。
这种重复定位精度高且稳定可靠的定位、夹紧方法,可使零件变形小,操作方便,能通用于从粗加工到精加工中的各道工序。
由于定位基准统一,使各工序中定位点的大小及位置也保持相同。
这些都为稳定工艺、保证加工精度提供了良好的条件。
(4)大小头孔加工既要保证孔本身的精度、表面粗糙度要求,还要保证相互位置和孔孔与端面垂直度要求。
小头底孔径由钻孔、扩、铰孔及倒角等工序完成。
青铜衬套,再以衬套内孔定位,在金刚镗床上精镗内孔。
大头孔的半精镗、精镗、珩磨工序都是在合装后进行。
三、工艺规程设计
3.1、连杆的材料和毛坯
选取连杆标准件。
连杆材料选用42CrMo钢,毛坯生产使用整体模锻成形。
模锻是利用模具使毛坯变形以获得锻件的锻造方法。
模锻主要用来减小或增大管材(或棒料)的直径,尤其是生产具有复合形状的零件。
模锻时,把管材或棒料放置在模锻模腔内,然后连续的施加径向的压力以实现金属的变形。
通过放置芯轴在宫腔内并连续的施加径向的压力可以增大管材的直径。
通过对内径进行锻造和对外径进行锻造,可获得不同的零件形状。
42CrMo钢,属于超高强度钢,具有高强度和韧性,淬透性也较好,无明显的回火脆性,调质处理后有较高的疲劳极限和抗多次冲击能力,低温冲击韧性良好。
该钢适宜制造要求一定强度和韧性的大、中型塑料模具。
化学成份:
碳C:
0.38~0.45%,硅Si:
0.17~0.37%,锰Mn:
0.50~0.80%,硫S:
允许残余含量≤0.035%,磷P:
允许残余含量≤0.035%,铬Cr:
0.90~1.20%,镍Ni:
允许残余含量≤0.030%,铜Cu:
允许残余含量≤0.030%,钼Mo:
0.15~0.25%。
42CrMo强度、淬透性高,韧性好,高温时有高的蠕变强度和持久强度。
3.2、连杆的技术要求
连杆的作用是把活塞和曲轴联接起来,使活塞的往复直线运动变为曲柄的回转运动,以输出动力,同时又压缩汽缸内气体。
因此,连杆的加工精度将直接影响发动机的性能,而工艺的选择又是直接影响精度的主要因素。
反映连杆精度的参数主要有5个:
(1)连杆大端中心面和小端中心面相对连杆杆身中心面的对称度。
(2)连杆大、小头孔中心距尺寸精度。
(3)连杆大、小头孔平行度。
(4)连杆大、小头孔尺寸精度、形状精度。
(5)连杆大头螺栓孔与接合面的垂直度。
1)大、小头孔的尺寸精度、形状精度
为了使大头孔与轴瓦及曲轴、小头孔与活塞销能密切配合,减少冲击的不良影响和便于传热。
大头孔公差等级为IT6,表面粗糙度Ra应不大于0.8μm;大头孔的圆柱度公差为0.012mm,小头孔公差等级为IT8,表面粗糙度Ra应不大于3.2μm。
小头压衬套的底孔的圆柱度公差为0.0025mm,素线平行度公差为0.04/100mm。
2)大、小头孔轴心线在两个互相垂直方向的平行度
两孔轴心线在连杆轴线方向的平行度误差会使活塞在汽缸中倾斜,从而造成汽缸壁磨损不均匀,同时使曲轴的连杆轴颈产生边缘磨损,所以两孔轴心线在连杆轴线方向的平行度公差较小;而两孔轴心线在垂直于连杆轴线方向的平行度误差对不均匀磨损影响较小,因而其公差值较大。
两孔轴心线在连杆的轴线方向的平行度在100mm长度上公差为0.04mm;在垂直与连杆轴心线方向的平行度在100mm长度上公差为0.06mm。
3)大、小头孔中心距
大小头孔的中心距影响到汽缸的压缩比,即影响到发动机的效率,所以规定了比较高的要求:
217±0.05mm。
4)连杆大头孔两端面对大头孔中心线的垂直度
连杆大头孔两端面对大头孔中心线的垂直度,影响到轴瓦的安装和磨损,甚至引起烧伤;所以对它也提出了一定的要求:
规定其垂直度公差等级应不低于IT9(大头孔两端面对大头孔的轴心线的垂直度在100mm长度上公差为0.08mm)。
5)大、小头孔两端面的技术要求
连杆大、小头孔两端面间距离的基本尺寸相同,但从技术要求是不同的,大头两端面的尺寸公差等级为IT9,表面粗糙度Ra不大于0.8μm,小头两端面的尺寸公差等级为IT12,表面粗糙度Ra不大于6.3μm。
这是因为连杆大头两端面与曲轴连杆轴颈两轴肩端面间有配合要求,而连杆小头两端面与活塞销孔座内档之间没有配合要求。
连杆大头端面间距离尺寸的公差带正好落在连杆小头端面间距离尺寸的公差带中,这给连杆的加工带来许多方便。
6)螺栓孔的技术要求
在前面已经说过,连杆在工作过程中受到急剧的动载荷的作用。
这一动载荷又传递到连杆体和连杆盖的两个螺栓及螺母上。
因此除了对螺栓及螺母要提出高的技术要求外,对于安装这两个动力螺栓孔及端面也提出了一定的要求。
规定:
螺栓孔按IT8级公差等级和表面粗糙度Ra应不大于6.3μm加工;两螺栓孔在大头孔剖分面的对称度公差为0.25mm。
7)对口面的技术要求
在连杆受动载荷时,对口面的歪斜使连杆盖及连杆体沿着剖分面产生相对错位,影响到曲轴的连杆轴颈和轴瓦结合不良,从而产生不均匀磨损。
结合面的平行度将影响到连杆体、连杆盖和垫片贴合的紧密程度,因而也影响到螺栓的受力情况和曲轴、轴瓦的磨损。
对于本连杆,要求结合面的平面度的公差为0.025mm。
3.3、确定毛坯的制造形式
连杆材料一般采用45钢或40Cr钢,近年来也有采用球墨铸铁。
钢制连杆都用模锻制造毛坯,连杆毛坯的锻造工艺有两种方案:
将连杆体和盖分开锻造或整体锻造。
因为连杆盖中间有凹坑,这样就不能采用整体锻造工艺。
因为整体锻造是总以杆身对称面为分模面,此时连杆盖两端的筋就无法锻出,所以必须分开锻造。
从锻造后材料的组织来看,分开锻造的连杆盖金属纤维是连续的,因此具有较高的强度,而整体锻造的连杆,经切开后,连杆盖的金属纤维是断裂的,因而削弱了强度。
当然整体锻造要增加切开连杆的工序。
但是,整体锻造可以提高材料利用率,减少结合面的加工余量。
机械加工的装夹比较方便,而且只需要一套模锻,一次便可锻成,毛坯也只有一只,便于组织和管理生产。
所以一般只要不受连杆盖形状和锻造设备的限制,尽可能采用连杆的整体锻造工艺。
3.4、基准面的选择
连杆机械加工工艺过程的大部分工序都采用统一的定位基准-——一个指定的端面,小头孔及工艺凸台。
这样不久有利于保证连杆的加工精度。
特别是作为技术要求的关键项目——连杆大;小头孔的尺寸精度。
几何形状精度和相互位置精度,而且端面的面积大,定位比较稳定。
由于连杆的外行不规则,为了定位需要,在连杆大头处作出工艺凸台(俗称工艺搭子而)作为辅助基面。
连杆大,小头端面对称分布在杆身的两侧,由于大,小头孔厚度不等,所以大头端与同侧小头端面不在一个平面上,这样的端面作为定位基准显然是不利的。
为了避免用阶梯面定位产生的定位误差,一定工艺规程时,先把大,小头作成一样的厚度,这样不仅避免了上述缺点,而且加大了定位面积,增加了定位稳定性。
在加工的最后阶段才铣出这个阶梯面。
用端面定位安装工件时,注意将厂标号及件号标记的一面不与夹的定位元件接触。
在精镗小头孔及小头活塞销轴轴承孔时,也用小头孔(轴承孔)作为定位基准,这是精加工中自身定位的典型例子。
将定位销做成活动的,当连杆定位夹紧后,定位销从小头孔中抽出。
精镗大,小头孔时,用大头端面起主要定位作用,有利于保证大头孔与端面的垂直度要求,而精镗小头轴承孔时,大头孔用可心轴起主要定位作用,有利于保证大,小头孔轴线的平行度。
粗基准的选择:
1.选择两端为粗基准其理由如下:
A该加工表面为连杆的重要表面,为保证其余量均匀。
B毛坯该两端面较光洁。
2.工艺凸台由于其加工余量较小,且与加工面的位置精度要求高,故也可以做粗基准。
精基准的选择:
因尽量遵守基准重合原则,以减少因基准不重合而引起的定位误差。
应尽量选择工序基准。
因此,两端面和半精加工后的大小头孔。
工艺凸台以作为精基准。
3.5、制定工艺路线
制定工艺路线的出发点,应当是使零件的几何形状,尺寸精度几位置精度等技术要求能得到合理的保证。
在生产纲领已确定为大批生产的条件下,可以考虑采用万能性机床配以专用夹具,并尽量使工序集中来提高生产率。
除此以外,还应当考虑经济效果,以便使生产成本尽量下降。
四、切削用量的选择原则
正确地选择切削用量,对提高切削效率,保证必要的刀具耐用度和经济性,保证加工质量,具有重要的作用。
1.粗加工时切削用量的选择原则
粗加工时加工精度与表面粗糙度要求不高,毛坯余量较大。
因此,选择粗加工的切削用量时,要尽可能保证较高的单位时间金属切削量(金属切除率)和必要的刀具耐用度,以提高生产效率和降低加工成本。
金属切除率可以用下式计算:
Zw≈V.f.ap.1000
式中:
Zw单位时间内的金属切除量(mm3/s);V切削速度(m/s);
f进给量(mm/r);ap切削深度(mm)。
提高切削速度、增大进给量和切削深度,都能提高金属切除率。
但是,在这三个因素中,影响刀具耐用度最大的是切削速度,其次是进给量,影响最小的是切削深度。
所以粗加工切削用量的选择原则是:
首先考虑选择一个尽可能大的吃刀深度ap,其次选择一个较大的进给量度f,最后确定一个合适的切削速度V.
选用较大的ap和f以后,刀具耐用度t显然也会下降,但要比V对t的影响小得多,只要稍微降低一下V便可以使t回升到规定的合理数值,因此,能使V、f、ap的乘积较大,从而保证较高的金属切除率。
此外,增大ap可使走刀次数减少,增大f又有利于断屑。
因此,根据以上原则选择粗加工切削用量对提高生产效率,减少刀具消耗,降低加工成本是比较有利的。
(1)切削深度的选择:
粗加工时切削深度应根据工件的加工余量和由机床、夹具、刀具和工件组成的工艺系统的刚性来确定。
在保留半精加工、精加工必要余量的前提下,应当尽量将粗加工余量一次切除。
只有当总加工余量太大,一次切不完时,才考虑分几次走刀。
(2)进给量的选择:
粗加工时限制进给量提高的因素主要是切削力。
因此,进给量应根据工艺系统的刚性和强度来确定。
选择进给量时应考虑到机床进给机构的强度、刀杆尺寸、刀片厚度、工件的直径和长度等。
在工艺系统的刚性和强度好的情况下,可选用大一些的进给量;在刚性和强度较差的情况下,应适当减小进给量。
(3)切削速度的选择:
粗加工时,切削速度主要受刀具耐用度和机床功率的限制。
切削深度、进给量和切削速度三者决定了切削功率,在确定切削速度时必须考虑到机床的许用功率。
如超过了机床的许用功率,则应适当降低切削速度。
2.精加工时切削用量的选择原则
精加工时加工精度和表面质量要求较高,加工余量要小且均匀。
因此选择精加工的切削用量时应先考虑如何保证加工质量,并在此基础上提高生产效率。
(1)切削深度的选择:
精加工时的切削深度应根据粗加工留下的余量确定。
通常希望精加工余量不要留得太大,否则,当吃刀深度较大时,切削力增加较显著,影响加工质量。
(2)进给量的选择:
精加工时限制进给量提高的主要因素是表面粗糙度。
进给量增大时,虽有利于断屑,但残留面积高度增大,切削力上升,表面质量下降。
(3)切削速度的选择:
切削速度提高时,切削变形减小,切削力有所下降,而且不会产生积屑瘤和鳞刺。
一般选用切削性能高的刀具材料和合理的几何参数,尽可能提高切削速度。
只有当切削速度受到工艺条件限制而不能提高时,才选用低速,以避开积屑瘤产生的范围。
由此可见,精加工时选用较小的吃刀深度ap和进给量f,并在保证合理刀具耐用度的前提下,选取尽可能高的切削速度V,以保证加工精度和表面质量,同时满足生产率的要求。
五、确定各工序的加工余量、计算工序尺寸及公差
1.确定加工余量
用查表法确定机械加工余量:
(根据《机械制造技术基础课程设计》表3-4表5-49表5-50)
表1平面加工的工序余量(mm)
工艺名称
工序基本余量
工序经
济精度
工序尺寸
粗铣
2
IT9
38.0
精铣
0.5
IT8
39.0
(1)则连杆两端面总的加工余量为:
A总=
=(A粗铣+A精铣)
2
=(2+0.5)
2
=5mm
(2)连杆锻造出来的总的厚度为H=38.0+5=43.0mm
2.确定工序尺寸及其公差
(根据《机械制造技术基础课程设计》表3-4表5-39表5-44)
表2大头孔各工序尺寸及其公差(锻造出来的大头孔为
60mm)
工序名称
工序基本余量
工序经
济精度
工序尺寸
尺寸公差
表面粗糙度
珩磨
0.1
IT6
0.5
精镗
0.2
IT8
1.2
半精镗
1.2
IT10
1.5
粗镗
4.0
IT11
12.5
六、工时定额的计算
1)铣连杆两侧面
选用X51铣床
根据《新编实用切削加工速查手册》选取数据
铣刀直径D=100mm由于采用标准高速钢圆柱铣刀所以齿数Z=6
切削速度V=3.93m/s铣削宽度ae=60mm
进给量fm=1.2mm/r
则主轴转速n=1000×60v/
D=750.96r/min
根据《机械制造技术基础课程设计指南》表5-27按机床选取n=750r/min
则实际切削速度V=
Dn/(1000×60)=3.93m/s
铣削工时为:
根据《机械加工工艺手册》表2.1-99
L=278mmL1=
+2=48.9mmL2=4mm
基本时间tj=L/fm×2=(278+48.9+4)/(fm×n)×2=0.74min
辅助时间ta=0.4×0.4=0.16min
2)加工小头孔
(1)钻小头孔选用钻床Z3025
根据《机械切削工艺参数速查手册》表9-14选取数据
扩刀直径D=27mm切削速度V=0.71m/s
切削深度ap=5mm进给量fm=0.45mm/r
则主轴转速n=1000×60v/
D=502.5r/min
根据表3.1—30按机床选取n=500r/min
则实际切削速度V=
Dn/(1000x60)=0.71m/s
钻孔工时为:
按表2.5—7
L=38mmL1=(D-d)/2xcotkr+2=9.22mmL2=4mm
基本时间tj=L/fm×2=(38+9.22+4)/(0.45×500)=0.23min
辅助时间ta=0.4min
其他时间tq=0.2min
(2)扩小头孔选用钻床Z3025
根据《机械制造工艺设计手册》表2.4—47选取数据
扩刀直径D=29mm切削速度V=1.21m/s
切削深度ap=2mm进给量fm=0.8mm/r
则主轴转速n=1000×60v/
D=797.3r/min
根据表3.1—74按机床选取n=800r/min
则实际切削速度V=
Dn/(1000×60)=1.21m/s
扩削工时为:
按表2.5—10
L=38mmL1=(D-d)/2×cotkr+2=2.6mmL2=2mm
基本时间tj=L/fm×2=(38+2.6+2)/(0.8×800)×2=0.13min
辅助时间ta=0.2min
(3)半精镗小头孔选用镗床T2115
根据《简明金属切削手册》表5-55选取数据
铰刀直径D=30mm切削速度V=1.1m/s
切削深度ap=0.8mm进给量fm=0.2mm/r
则主轴转速n=1000×60v/
D=700.6r/min
根据表3.1—99按机床选取n=800r/min
则实际切削速度V=
Dn/(1000×60)=1.3m/s
镗削工时为:
按表2.5—3
L=38mmL1=(D-d)/2×cotkr+2=2.45mmL2=2mm
基本时间tj=L/fm=(38+2.45+2)/(0.2×800)=0.26min
辅助时间ta=0.2min
3)铣大头两侧面
选用X51铣床
根据《实用机械制造工艺设计手册》表10-18选取数据
铣刀直径D=20mm切削速度V=0.63m/s
铣刀齿数Z=8切削深度ap=15mm
切削宽度ae=6mmaf=0.10mm/r
则主轴转速n=1000×60v/
D=601.9r/min
按机床选取n=750r/min
则实际切削速度V=
Dn/(1000×60)=0.78m/s
铣削工时为:
L=53mmL1=
+2=9.2mmL2=2mm
基本时间tj=L/fmz=(53+9.2+2)/(750×0.10)×2=1.71min
辅助时间ta=0.4×0.4=0.16min
4)铣开连杆体和盖
选用X51铣床
根据