第八章孔加工Drill课件资料.docx
《第八章孔加工Drill课件资料.docx》由会员分享,可在线阅读,更多相关《第八章孔加工Drill课件资料.docx(20页珍藏版)》请在冰豆网上搜索。
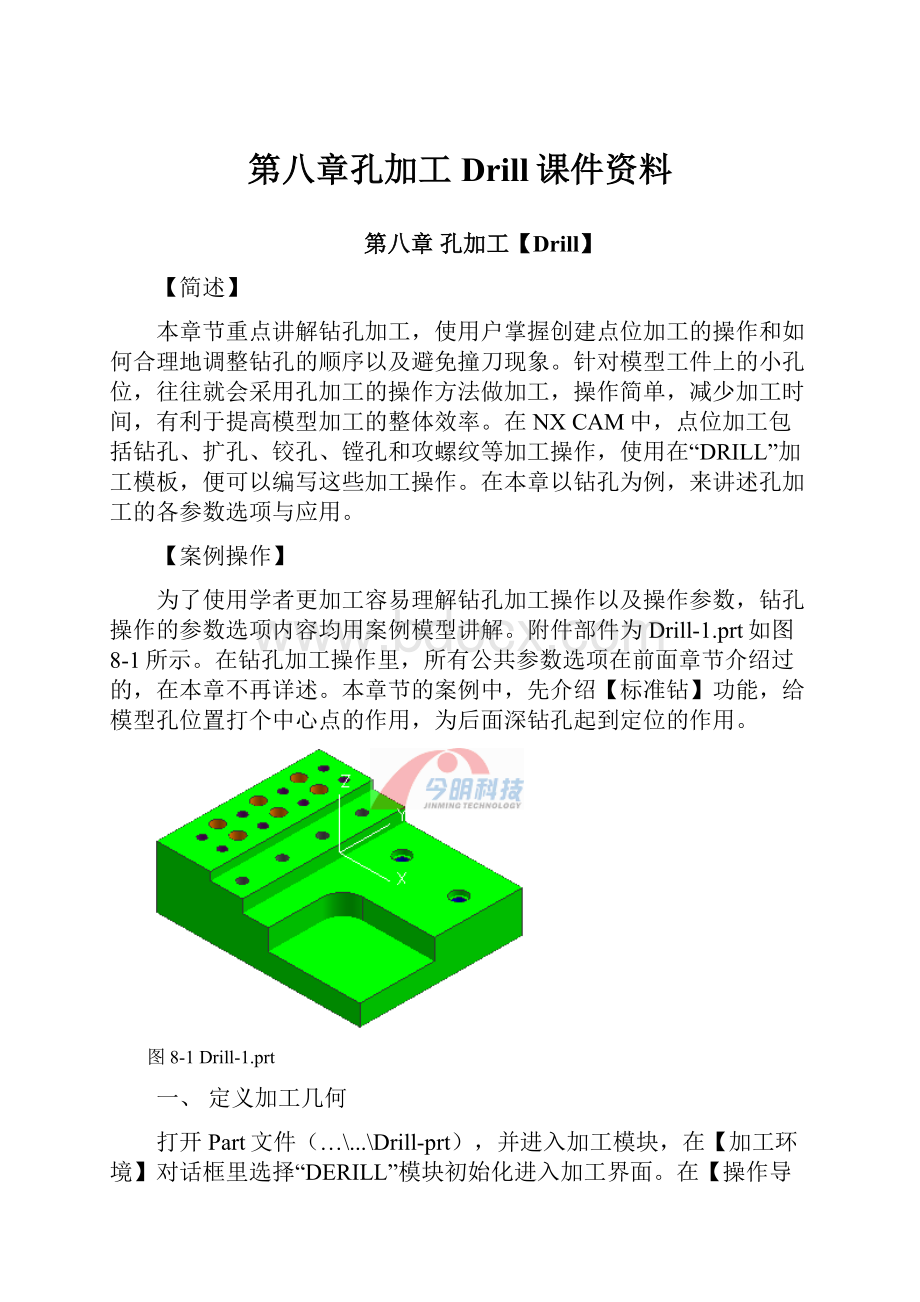
第八章孔加工Drill课件资料
第八章孔加工【Drill】
【简述】
本章节重点讲解钻孔加工,使用户掌握创建点位加工的操作和如何合理地调整钻孔的顺序以及避免撞刀现象。
针对模型工件上的小孔位,往往就会采用孔加工的操作方法做加工,操作简单,减少加工时间,有利于提高模型加工的整体效率。
在NXCAM中,点位加工包括钻孔、扩孔、铰孔、镗孔和攻螺纹等加工操作,使用在“DRILL”加工模板,便可以编写这些加工操作。
在本章以钻孔为例,来讲述孔加工的各参数选项与应用。
【案例操作】
为了使用学者更加工容易理解钻孔加工操作以及操作参数,钻孔操作的参数选项内容均用案例模型讲解。
附件部件为Drill-1.prt如图8-1所示。
在钻孔加工操作里,所有公共参数选项在前面章节介绍过的,在本章不再详述。
本章节的案例中,先介绍【标准钻】功能,给模型孔位置打个中心点的作用,为后面深钻孔起到定位的作用。
图8-1Drill-1.prt
一、定义加工几何
打开Part文件(…\...\Drill-prt),并进入加工模块,在【加工环境】对话框里选择“DERILL”模块初始化进入加工界面。
在【操作导航器】切换为“几何视图”,编辑节点(MCS_MILL)设定机床坐标与安全平面,如图8-2所示。
加工几何节点(WORKPIECE),此模型为“指定部件”;毛坯几何体不需要设定。
图8-2加工坐标与安全平面
二、创建刀具
在操作导航器切换到“机床”视图里,选择节点“GENERIC_MACHINE”并点击右键(MB3)→【插入】→【刀具】,然后弹出【创建刀具】对话框,如图8-3所示。
按指定要求创建钻头刀具,刀具类型为“DEILL”,刀具子类型为【SPOTDRILLING_TOOL】图标
、刀具名称为“JMSK_ZD_5”,在【钻刀】对话框中,设置“直径”为5,其他参数选项均为默认值。
单击【确定】完成刀具的创建。
图8-3创建钻头刀具
三、创建标准钻孔操作
在操作导航器“程序视图”里,选择节点“PROGRAM”并单击〖MB3〗→〖插入〗→〖操作〗,将弹出【创建操作】对话框。
设置〖类型〗为“Drill”、操作子类型为标准钻(DRILLING)图标
、刀具为“JMSK_ZD_5”、几何体为“WORKPIECE”、方法为“DRILL_METHOD”、操作名称为“POINT_DRILL”,点击【确定】按钮并弹出【钻】对话框。
创建操作如图8-4所示,【钻】操作对话框如图8-5所示。
图8-4创建钻孔操作
图8-5钻孔操作对话框
1.标准钻操作参数选项的设置
在创建【标准钻】操作对话框里,用户需要指定孔加工的位置,有时还需要指定部件的表面和孔的底面;在【标准钻】对话框的“几何体”选项卡中,可以允许用户作此相应的操作选项。
如图8-6所示。
图8-6标准钻的几何体选项
(1).指定孔:
允许用户指定要加工的孔位置。
在“几何体”选项卡中,点击“指定孔”图标
,并进入到【点到点几何体】对话框,如图8-7所示。
在【点到点几何体】对话框里,几何参数选项的含意,如表8-1所示。
图8-7点到点几何体对话框
表8-1【点到点几何体】对话框各选项的说明
选项
说明
【选择】
允许选择待加工孔的位置,可以选择圆弧、二次曲线的圆心和一般点定义孔的位置。
【附加】
允许在原来已指定点的基础上增加新的点位置。
【省略】
允许移除已经指定的但不需要加工的点位。
【优化】
允许依据规则对点位的钻削顺序进行重新排序。
【显示点】
将在图形屏幕中显示已指定的点位。
【避让】
控制刀具在点位与点位之间非切削移动抬刀的距离,避免发生干涉。
【反向】
颠倒先前选定的转至点的顺序。
【圆弧轴控制】
显示和/或反向先前选定的圆弧和片体孔的轴。
【Rapto偏置】
相对指定点的位置作偏置的距离,在默认的情况下,以指定的点位置作为偏置的距离。
【规划完成】
此选项与【确定】含义相似,它表示完成当前点位的设置。
【显示/校核循环参数组】
允许用户在图形屏幕中显示指定参数组的点位,检查是否有错误。
在【点到点几何体】对话框里点击“选择”选项,并弹出选择点位过滤器对话框,并在模型里随意选择点的位置,如图8-8所示。
图8-8选择点位示意图
孔的位置选择完成后,由于前面是随意选择的,接下来要对点位进行【优化】顺序。
点击【优化】选项,步骤:
【ShortestPath】→【优化】→【接受】,确定完成【优化】顺序,如流程图8-9所示。
图8-9点位顺序的优化流程图
(2).指定部件表面:
是刀具进入材料的位置。
如果没有指定部件表面,则默认是点或圆弧加以的所在位置,钻孔移动将从该点上位(沿刀轴方向盘)距离为【最小安全距离】的高度开始以速度切入工件。
当需要“指定部件表面”时,则单击【选择或编辑部件表面几何体】图标
,将会弹出如图8-10所示的【部件表面】对话框。
注:
指定表面的时候,点的位置一定要在指定表面的范围之内,否则计算刀轨时会出现【警告】对话框。
图8-10部件表面对话框
(3).指定底面:
允许用户定义刀轨的切削下限。
“底面”可以是一个已有的面,也可以是一个一般平面。
仅适用于那些在【Cycle深度】对话框中将深度参数设置为“到底面”和“穿过底面”的孔。
当需要“指定底面”时,则单击【选择或编辑底面几何体】图标
,将会弹出挖如图8-10所示的【底面】对话框。
然后选择合适的类型确定孔的底面深度,再单击【确定】按钮即可。
如果需要取消之前所指定的底面,则单击【无】图标
,再单击【确定】即可。
2.循环类型
在点位加工操作的对话框中,如图8-11所示,系统提供了14种循环类型,允许用户选择合适的循环类型应用于各种类型的孔加工。
在章节里,主要介绍【标准钻】与【标准钻,深度】两种类型,其他都是相似的,在此章中就不再详细。
图8-11点位加工的循环类型
1.标准钻(G81):
此循环类型将在每个点位激活一个标准钻循环,产生的刀轨将一次性将孔加工到指定的深度位置,故该循环类型不适宜于深孔加工。
当指定【标准钻】循环类型,需要定义点位的深度、循环进给率和停留时间等参数时。
点击【编辑参数】图标
,将会弹出【指定参数组】对话框,如图8-12所示。
图8-12指定参数组对话框
指定参数组允许用户设置1~5个参数组(最多可以定义5组,至少定义需要定义1组),每个参数组具有相同类型的循环参数,包括深度、进给率和步进量等参数,每一组的循环参数组可以定义不同的参数。
当指定循环参数组为1时,点击【确定】按钮,将弹出【Cycle参数】对话框,如图8-13所示。
在【Cycle参数】对话框是,包括有Depth(深度)、进给率、Dwell(停留时间)、Option(选项)、Cam和Rtrcto(退刀到)等几个参数选项。
图8-13【Cycle参数】对话框
在【Cycle参数】对话框中,选择【Depth-模型深度】将弹出如图8-14所示的【Cycle深度】对话框,它允许用户确定钻孔尝试的方法,表8-2是各选项的说明。
图8-14Cycle深度对话框及各项的说明图
表8-2Cycle深度的各选项说明
深度选项
说明
模型深度
该选项使得系统自动计算实体模型中孔的深度作为钻削深度。
此时,如果刀具超过孔的直径,则系统将拒绝刀具进入孔。
刀尖深度
该选项将计算刀尖与点位之间的距离作为钻削深度,如果指定了部件表面,则钻削深度为刀尖与部件表面之间的距离。
刀肩深度
该选项将计算刀肩与点位之间的距离作为钻削深度,如果指定了部件表面,则钻削深度为刀肩与部件表面之间的距离,如图8-14所示。
至底面
该选项将计算刀尖到达孔底时刀尖与点位之间的距离作为钻削深度,如果指定了部件表面,则钻削深度为刀尖与部件表面之间的距离,如图8-14所示。
穿过底面
该选项将计算刀尖到达孔底时刀肩与点位之间的距离作为钻削深度,如果指定了部件表面,则钻削深度为刀肩与部件表面之间的距离,如图8-14所示。
至选定点
该选项将计算刀尖到达指定点时刀尖与点位之间的距离作为钻削深度,如果指定了部件表面,则钻削深度为刀尖与部件表面之间的距离,如图8-14所示。
本章节案例操作中,设定【Cycle深度】为“刀尖深度”并设置【深度】值为2,点击【确定】并完成深度参数的设置。
2.进给率
在【Cycle参数】对话框中,选择【进给率(MMPM)-250.000】参数选项将弹出如图8-15所示的【Cycle进给率】对话框,它允许用户设置循环钻削时的进给率和单位。
若用户同时在【进给和速度】对话框中设置了〖剪切〗进给时,则系统将优先使用循环参数组中设置的进给率。
图8-15【Cycle进给率】对话框
3.停留时间(Dwell)
在【Cycle参数】对话框中,选择【Dwell-关】参数选项将弹出如图8-16所示的【CycleDwell】对话框,它允许用户设置当到达指定深度时刀具的停留时间,使得刀具空转,保证孔表面质量,表8-3是各选项的说明。
图8-16【CycleDwell】对话框
表8-3停留时间的选项说明
选项
说明
关
该选项将使得刀具在到达指定深度时不做停留。
开
该选项将使得刀具在到达指定深度时稍做停留。
秒
该选项将允许用户设置秒数来确定刀具在到达指定深度时的停留时间。
旋转
该选项将允许用户设置转数来确定刀具在到达指定深度时的停留时间。
4.选项(Option)
【Option】选项将用于激活机床的专有特性,它的功能将依赖于后处理器,单击该选项时将在“关”与“开”之间切换。
如果该选项为“开”,系统将在循环语句中输出“Option”单词。
一般地,编写刀轨时无须设置该项参数。
5.CAM
【CAM】选项允许用户为那些没有可编程Z轴的机床预先设置一个刀具停止的位置,不能输入负值,否则系统将会发出警告。
一般无须设置该项参数。
6.退刀到(Rtrcto)
在【Cycle参数】对话框中,选项【Rtrcto-无】参数选项将弹出如图8-17所示的退刀选项对话框,它允许用户设置一个退刀距离,表8-4是各选项的说明。
这个距离是从点位置或部件表面(如果指定了部件表面)沿刀轴方向起始计算的,通常设置一个大于0的值。
在默认情况下,刀具将退刀到【最小安全距离】高度处,由于最小安全距离太低,一般情况下都需要设置该项参数。
图8-17退刀选项对话框
表8-4退刀选项的说明
选项
说明
距离
该选项将允许直接设置一个退刀距离确定退刀位置
自动
该选项将使得刀具沿刀轴方向退回到安全平面的位置(需要该操作继承安全平面)
设置为空
该选项表示取消退刀距离
3.深度偏置
在钻孔加工的操作界面中,【深度偏置】选项卡里提供了“通孔安全距离”和“肓孔余量”两个参数选项,“通孔安全距离”选项是指刀具肩部穿过底面的距离,仅当尝试循环参数设置为“模型深度”或“穿过底面”时才有效;而“肓孔余量”选项是指肓孔底部的剩余材料量,即孔底面与刀尖的距离,仅当深度循环参数指定为“模型深度”或“至底面”时才有效。
如图8-18所示。
图8-18深度偏置参数
注:
∙如果将“循环参数”中的“深度”选项设为“模型深度”,“深度偏置”将只适用于实体孔。
它不适用于点、圆弧或片体中的孔。
∙如果将“循环参数”中的“深度”选项设为“到底面”,“盲孔”余量将应用于所有选定的对象。
必须有一个“底面”处于活动状态。
∙如果将“循环参数”中的“深度”选项设为“穿过底面”,通孔安全距离将应用于所有选定的对象。
必须有一个“底面”处于活动状态。
4.操作
在【标准钻】操作中,针对指定的几何参数与循环参数设置完成后,其他没设置的参数选项均为默认值。
然后在【操作】选项卡中点击“生成”图标
,计算出钻孔的刀轨,如图8-19所示,点击【确定】并完成此操作。
图8-19标准钻的刀轨图
四、创建深孔钻操作
由于模型有几种不同大小的孔,要想把模型的孔加工出来,还需要创建不同的刀具。
接下来针对此模型直径为16MM的孔,创建深孔钻操作,其他的大小的孔在本章节将不再加工。
1.创建深孔钻刀具
在操作导航器切换到“机床”视图里,选择节点“GENERIC_MACHINE”并点击右键(MB3)→【插入】→【刀具】,然后弹出【创建刀具】对话框,如图8-3所示。
按指定要求创建钻头刀具,刀具类型为“DEILL”,刀具子类型为【DRILLING_TOOL】图标
、刀具名称为“JMSK_ZD_15.8”,在【钻刀】对话框中,设置“直径”为15.8,其他参数选项均为默认值。
单击【确定】完成刀具的创建。
2.创建操作
在加工创建工具条点击【创建操作】,弹出【创建操作】对话框,选项组的〖类型〗默认选择drill,在选项组〖操作子类型〗中,选择“PECK_DRILLING”图标
,各个选项设置如下:
1.“程序”选择父级组“PROGRAM”。
2.“刀具”选择前面已创建好的刀具名称,即“JMSK_ZD_15.8”。
3.“几何体”选择前面已创建好的几何体节点名称,即“WORKPIECE”。
4.“方法”选择前面已创建好的方法名称,即“DRILL_METHOD”。
5.“名称”将原来系统的名称改为“PECK_DRILL”。
按上面所设,所有选项设置完毕,点击【确定】,即可进入【啄钻】操作对话框,如图8-20所示。
在啄钻加工操作里,每一步骤的参数设置,将在下面详细解说。
图8-20创建深孔钻操作
第一步:
定义【几何体】选项卡里的“指定孔”参数。
点击【选择或编辑孔几何体】图标
,操作流程图如8-21所示。
图8-21指定孔位置流程图
第二步:
设置循环类型。
要定义钻孔深度、循环进给率和步进距离等参数,如流程图8-22所示.。
图8-22设置循环参数类型
在【标准钻,深度…】循环类型里跟前面所介绍的【标准钻】循环类型有些不同,在【标准钻,深度…】循环类型,需要设置“步进量”(Step值)。
在【Cycle参数】对话框里,选择【Step值-未定义】参数选项将弹出如图8-23所示的步进量对话框,它允许用户设置啄式循环钻孔时每次钻孔的深度值,可输入1~7个非零的步进量。
若后续的步进量设置为0,则系统默认为前一个步进量的值。
图8-23步进量对话框
第三步:
进给率和速度。
主要是用来定义刀具切削时,主轴的转速设置为1000;切削速度设置为200。
第四步:
生成刀轨。
在〖操作〗选项卡里,点击生成图标
,待系统计算完成,点击【确定】按钮将完成此操作。
最终生成的刀轨如图8-24所示。
图8-24【啄钻】操作的刀轨图
〖小结〗:
本节重点介绍钻孔加工的操作方法。
〖附练习文件〗drill-1.prt