工业制氮.docx
《工业制氮.docx》由会员分享,可在线阅读,更多相关《工业制氮.docx(15页珍藏版)》请在冰豆网上搜索。
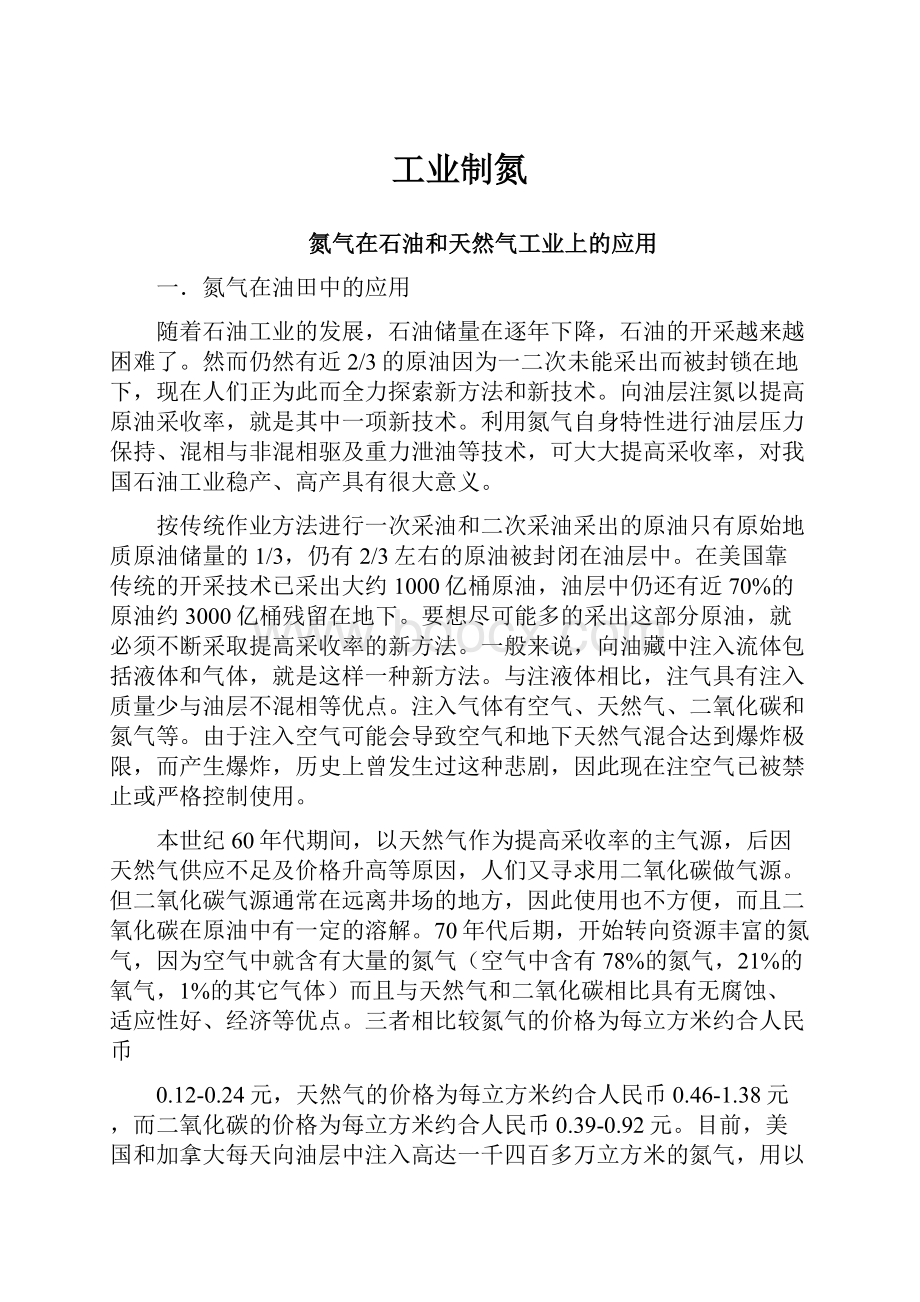
工业制氮
氮气在石油和天然气工业上的应用
一.氮气在油田中的应用
随着石油工业的发展,石油储量在逐年下降,石油的开采越来越困难了。
然而仍然有近2/3的原油因为一二次未能采出而被封锁在地下,现在人们正为此而全力探索新方法和新技术。
向油层注氮以提高原油采收率,就是其中一项新技术。
利用氮气自身特性进行油层压力保持、混相与非混相驱及重力泄油等技术,可大大提高采收率,对我国石油工业稳产、高产具有很大意义。
按传统作业方法进行一次采油和二次采油采出的原油只有原始地质原油储量的1/3,仍有2/3左右的原油被封闭在油层中。
在美国靠传统的开采技术已采出大约1000亿桶原油,油层中仍还有近70%的原油约3000亿桶残留在地下。
要想尽可能多的采出这部分原油,就必须不断采取提高采收率的新方法。
一般来说,向油藏中注入流体包括液体和气体,就是这样一种新方法。
与注液体相比,注气具有注入质量少与油层不混相等优点。
注入气体有空气、天然气、二氧化碳和氮气等。
由于注入空气可能会导致空气和地下天然气混合达到爆炸极限,而产生爆炸,历史上曾发生过这种悲剧,因此现在注空气已被禁止或严格控制使用。
本世纪60年代期间,以天然气作为提高采收率的主气源,后因天然气供应不足及价格升高等原因,人们又寻求用二氧化碳做气源。
但二氧化碳气源通常在远离井场的地方,因此使用也不方便,而且二氧化碳在原油中有一定的溶解。
70年代后期,开始转向资源丰富的氮气,因为空气中就含有大量的氮气(空气中含有78%的氮气,21%的氧气,1%的其它气体)而且与天然气和二氧化碳相比具有无腐蚀、适应性好、经济等优点。
三者相比较氮气的价格为每立方米约合人民币
0.12-0.24元,天然气的价格为每立方米约合人民币0.46-1.38元,而二氧化碳的价格为每立方米约合人民币0.39-0.92元。
目前,美国和加拿大每天向油层中注入高达一千四百多万立方米的氮气,用以提高原油的采收率。
在美国实施注气的30个油田中,注氮气的就有25个。
从多油藏的角度看,油层注氮主要有如下几方面作用
1.保持油层压力
将油气层的压力保持或高于其露点压力或泡点压力,或保持在目前压力水平上,以使油气层流体能顺利流出。
2.重力泄油和非混相驱
根据氮气密度小的特点,将其注入构造顶部或允许其运移至构造顶部,增强向下驱替油层流体或重力和稳定混相段塞的作用,提高油气层流体的产量。
3.混相驱
利用氮气的多次接触混相作用驱替油气层中的油气。
4.驱动二氧化碳段塞
利用氮气作为驱替流体扒动二氧化碳等溶剂在油气层中所形成的混相段塞。
5.阁楼油开采
高压氮气可将构造顶部的阁楼层中被圈闭的原油驱替到生产井中。
6.气顶驱替
在油藏最佳部位注入氮气,可保持或提高油藏压力并同时驱替和采出气顶气。
从其具体使用情况看主要有以下几方面的用途
氮气泡沫液由含表面活性剂的水溶液和氮气组成,其中气体是分散相,液体是连续相。
气体在液体中呈小气泡分散状态。
气体的直径越小,泡沫流体的性能越好。
同时泡沫流体具有密度小、粘度大、携砂能力强,遇水敏性地层不会产生粘土膨胀问题,同时具有良好的封堵能力等特性,被广泛的应用于钻井、压洗井、压裂、酸化、堵水、调剖,氮气泡沫驱等方面。
1.高压应用
1.1压裂酸化
压裂酸化作业是目前油田稳产、增产的有效措施之一。
压裂酸化后,油层裂缝通道加长、渗透性改善、油气采收率提高。
根据有关统计资料,油气井进行得当的酸化作业后,产量可增加几倍至几十倍。
1.2气举排液
压裂酸化完成后,要进行必要的排液和诱喷作业。
近年来油田采用气举诱喷新工艺,效果良好。
气举排液、气举诱喷是指向井筒内注入一定量的高压气体,高压气体将油管内的液体扒到油管最下部,高压气体从油管下部进入套管空间成正举法,使环形空间内的液体和气体充分混合,并一同从井口喷出。
此时井底压力急剧减小,油气喷向低压区的井底口,渗透并引起自喷。
因井底积水停喷的油井使用氮气排液后,可将井抽活成为自喷井。
向油井内注入的高压气体必须具有阻燃抗爆的特性,而空气中的氧分在高压高温下容易引起燃烧爆炸不宜使用,目前油田普遍使用液氮和液态二氧化碳。
液氮和液态二氧化碳价格昂贵,需要专用设备长途运输,不适合油田的过程,从热能方面来讲,也是一种极大的浪费。
而现场制取氮气系统可从空气中直接分离氮气,不需要外加电源及其他外围设备,消耗能源少,移动方便。
1.3蒸汽、泡沫、氮气注井
实践证明,蒸汽、加泡沫剂、加氮气注井是稠油开采及油气井二次开采的最有效手段。
在重质稠油地层,稠油粘度高、渗透性及流动性极差,用传统采收技术无法奏效。
单独注入蒸汽会发生汽串而减低蒸汽的驱油效力。
使用蒸汽泡沫注入工艺,向井内注入高温蒸汽泡沫,蒸汽泡沫阻尼大,地层中原有裂缝通道对蒸汽阻力增大,从而减低汽串的负面作用,使含油地层温度升高,在高压氮气的作用下,稠油井可以成为自流井。
1.4管道、容器试压
在管道或容器内残存易燃、易爆气体或液体时,氮气系统可同时做吹扫及试压工作。
2.中压应用
2.1管道吹扫
易燃易爆气,液输送管线维修前,须对管道中残留气、液进行吹扫。
根据管道的实际情况,用一定压力和流量的氮气对管路进行吹扫作业。
2.2燃油储罐气封
燃油储罐顶部残存空气是造成油罐起火爆炸的主要原因之一。
在油罐顶部充氮,是解决这一隐患的根本途径,这一方法同样用于其它液体储罐
从资料上看,美国参与注氮项目的30个油田中的5个油田因注氮气而产出原油累计11.4亿地面桶,占其原始地质储量的68%。
在洛杉矶地区的4个油田,为了油层非混相驱、混相驱和凝析油藏保持压力而向油层注入了452.8万立方米的氮气,由此增产的原油达2亿桶。
相比之下中国的注氮技术刚刚起步。
目前在中国辽河、胜利、华北等油田己开始进行注氮项目的试验研究,并已经取得了一些可喜成果。
二、制氮原理及各种制氮方法的比较
通常是直接从空气中获得氮气,空气中含有大量的氮气。
工业制氮主要是通过空气分离来实现的。
目前的制氮方法主要有三种,即深冷空分法、分子筛空分法及薄膜空分法。
深冷空分法是将先空气液化然后对液化空气的精馏进行制氮,它适用于大规模生产。
它的特点是产气量大、设备庞大复杂、产品纯度高成本也高。
分子筛和薄膜空分法是本世纪70一80年代发展起来的新型空分技术。
与深冷空分法相比具有结构简单、工艺流程简单、出气时间短、运转部件少、运转稳定性好、价格低廉等优点。
三种制氮方法原理如下:
1.深冷空分法
l)原理及工艺过程深冷空分法在制氮领域内是最传统,技术也是最成熟的一种方法。
它将压缩后的空气送入冷却装置内,使之液化,再进入精馏塔精馏,把低纯度的氧气冷凝下来,而产出高纯度的氮气,最后进入换热装置使之接近环境温度。
2)特点
产气量大,日产气量最大可达140万立方米以上,氮气的纯度高,可达99.999%,并可连续工作。
但不利因素也很突出,深冷设备庞大复杂。
占地面积大、不易操作管理、启动时间长、工程建设造价高。
由于其设备庞大不可能放在油井现场,液氮要运至现场需要使用液氮车。
2.分子筛空分法(PSA)
l)基本原理由于氧气和氮气在分子筛吸附剂微孔内扩散速度不同,当空气经过分子筛时,直径较小的氧气分离以较快的速度向微孔内扩散,并优先被分子筛所吸附,剩下直径较大的氮分子供用户使用,而后再采用解吸方法释放分子筛中的富氧成分。
因此分子筛空分法要连续生产需使用二个吸附罐,切换使用。
2)工艺流程分子筛空分制氮的主要设备如图一所示。
该系统的核心分子筛(如碳分子筛),装在吸附塔A和B之内,工作时压缩空气过滤后分别进入A塔和B塔,A与B两塔交替轮换进行加压吸附产氮和减压解吸再生的变压吸附操作。
实现氧氮分离,从而连续制氮。
流程示意
3)特点:
与传统的深冷法相比它具有如下优点:
A.起动速度较快:
通常在开机后30分钟左右便可获得合格的产品氮气。
而深冷法则需6小时以上的启动时间。
B.随时停机:
可根据需要随时开车和停机,即使停机数小时甚至几天,都不会影响运行工况,而深冷则做不到。
C.实现自动化操作:
设备少,运行正常后就可进行自动化及无人操作。
而深冷装置机组多。
故障因素多,即使自动化程度很高也得有人看管。
D.装置紧凑,占地面积小:
因设备少无需建专用厂房,工程建筑投资省,而深冷机组复杂,占地面积大,故工程建设造价高。
3.中空纤维膜空分制氮法
l)原理压缩空气由中空纤维膜分离器的纤维管程进料,其分离推动力就是气体各组分的分压在中空纤维内腔原料侧与外腔(渗透侧)所形成的分压差,当气流沿中空纤维内腔表面流动时,各组分在其分压差的推动下,渗透到丝外。
“快气”如氧气H2O迅速渗透。
所以丝外(渗透)气流量为富集氧气,压力为一大气压,被排放至大气中。
而那些氮气、氢气的溶解扩散速度较低,决定了它们通过膜的渗透速度较慢,因此管程(非渗透侧)气流为富集氮气,氮气压力损失很小,产品氮的压力只略低原料气的压力。
2)工艺流程
如上所述,薄膜空分制氮是利用空气中的氧和氮通过中空纤维膜时的不同渗透率,把压缩空气分离为富氧和富氮的两股气流。
薄膜空分制氮装置由膜分离器,空压机,加热器等部分组成。
具体示意见(氮/氧膜分离器示意图)。
在空分制氮流程中,中空纤维膜分离器是核心部分,过滤及加热部分是为保证原料气能清洁恒温地进入膜分离器延长膜的使用寿命。
由图二可以看出,分离器的左端是空气入口.气体进入空纤维膜后氧气迅速渗透过去,从侧口出去,氮气继续前进从分离器的右端出去。
在系统中,分离器是并联安装的,并联多少分离器可根据产气量和空压机排量等诸多因素而定。
3)特点:
由于膜分离器原理及结构简单合理,所以比深冷法和分子筛法具有更多的优越性,除分子筛空分法所具有的优点外,膜法还具有如下几个特点:
A.启动迅速:
从开机到产出氮气只需5分钟左右,而深冷法需6个小时以上,分子筛需要30分钟左右。
B.无运动部件:
深冷及分子筛系统中均有运动部件,而膜法没有,不需维修,可靠性高。
C.可移动性强:
全部设备、仪表可以集中安装在一个可移动的框架上,灵活性高,可在多种场合就地现场制氮。
三种空分制氮法的综合比较
分离方法深冷分子筛膜分离
原理分离机理低温精馏高压吸附/低压解吸溶解扩散
相变化有无无
设备情况安装方式
运动部件
工艺流程
生产能力
占地面积固定式
有
复杂
大
大固定,移动式
有
简单
中等
小移动式
无
简单
较大
小
操作维修情况气源要求
氮气纯度%
启动时间
随时开,停车
运转稳定性
无人操作
再生工艺
维修情况
产量扩大可能性脱水,脱油
〉99.9
〉6h
不可
较难
不可
不需
需要
不能脱水,脱油
97-99.9
《30min
可以
好
可以
需要
需要
不需脱油
95-99.9
〈5min
很好
很好
可以
不需
不需
可以
从对三种空分法的技术分析来看,深冷法除在产气量大时(12.5万立方米/小时)有优势外,其系统占地面积、生产情况、运转状况、操作及装置保养等诸多方面均不如分子筛和薄膜空分法,尤其是油田开采地点不固定这种条件下,需使用罐装车运送至现场,一则使用量受液氮车容量的限制,一车液氮需一次使用完毕;二则运输等条件多有不便;三则氮气由气态变液态再变为气态本身就是一个能量损耗过程,而且液态车的价格很昂贵。
因此深冷法液态氮气使用受到各方面的限制。
现代薄膜气体分离技术支柱的中空纤维膜分离器是美国盂山都公司的子公司Permea(帕米亚)于1979年首先研制出的第一个工业用薄膜空分装置。
其原理是利用薄膜对氧和氮的不同选择性,使氧和氮透过薄膜的渗透率不同而达到分离氮的目的。
中空纤维膜在正常情况下使用寿命可达十年以上。
三、大连力德气体分离技术有限公司氮气作业系统
大连力德科技开发有限公司油田高压氮气作业系统为高压大容量氮气系统,可以从空气中直接分离氮气、运行成本低、可靠性高。
整套系统由制氮撬及增压撬组成,可由两部国产卡车载运,移动便捷。
该系统可用于气举排液、稠油开发、二次采油、管道容器试压。
制氮撬可作为低压及中压氮气气源单独运行,无需联结增压撬,可应用于管道吹及储油罐充氮防火,水果保鲜等多种用途,系统配制灵活操作灵活简便。
大连力德科技开发有限公司氮气作业系统的组成:
A.主动力系统
B.空气压缩机系统
C.氮气发生器系统
D.氮气增压机系统
E.蒸汽泡沫注入系统(本项用于蒸汽、氮气、泡沫注入)
大连力德科技开发有限公司氮气作业参数可根据用户要求设计1.氮气排量
氮气排量:
在氮气纯度为95%时,氮气排量为10一20Nm3/min出口压力:
<5000Pis(35Mpa)
运行方式:
连续
2.氮气纯度
氮气纯度:
95%至99.9%连续可调
用户可随时通过氮气纯度仪设定氮气纯度,氮气纯度高定后,即自动保持恒定
3、温度
环境温度:
-40至45摄氏度
氮气出口温度:
可根据具体情况设置压缩机级间冷器来保证。
4、装载方式:
根据系统参数和用户要求可提供撬装、车载或拖挂式。
5、动力系统:
标准设置为柴油机,也可根据用户要求改用电动机。
四.大连力德气体分离技术有限公司氮气作业系统配置
1.空压机
空压机为螺杆式压缩机。
螺杆式压缩机的气缸内室为蝶形,气缸内的两个转子分别为阳螺杆(主动转子)及阴螺杆(被动转子)。
气缸内充满压缩机油,阳螺杆带动阴螺杆旋转时,空气由螺杆一端吸入然后由另一端挤出与传统的活塞式压缩机相比,螺杆式压缩机有以下突出优点:
(l)能耗低
由于吸气,压缩为连续过程中,阳螺杆与阴螺杆之间并无直接机械摩擦,螺杆式压缩机比活塞式能耗要低40%左右。
(2)体积小
螺杆式压缩机的体积只有相同容量活塞式压缩机的四分之一到六分之一。
因为能耗小,所需原动机的马力及体积也相应减少。
因此,螺杆式压缩机最适用于车载系统。
(3)震动小
活塞式压缩机由于活塞的往复运动现时产生固有震动:
而螺杆式压缩机的两根螺杆各自围绕其轴心旋转,根本上消除了震源。
(4)出气量大
螺杆式压缩机不存在不作功冲程,压缩效率高、出气量大。
(5)寿命长
螺杆式压缩机的两根螺杆之间并无直接机械磨擦,系统中运动部件少,运行寿命远较活塞式压缩机长。
2.膜氮气分离系统
氮气分离器的心脏部分为氮气分离薄膜纤维管,薄膜管的外径很小,薄膜管壁对空气中的氧气、氮气、二氧化碳、水蒸汽及氢的渗透能力不同,水蒸汽由管壁渗出的速度最快,其余依次为而二氮化碳、氮气;氮气渗透速度最慢。
压缩空气由薄膜管一端注入,其中水蒸汽、氧、二氧化碳由管壁渗出,氮气由管另一端排出。
由管壁排出的气体收集后放空。
分离器中装有数万根薄膜管,以增加总渗透面积。
与其它制氮方法相比,薄膜分离器具有下列优越性:
(l)无需能源
除仪表电源外,氮气分离过程不需任何能源。
因此,运行成本极低。
(2)高可靠性
氮气分离器系统中没有转动件,可靠性极高。
(3)连续运行
氮气分离器可长期连续运行,无需维护。
(4)纯度稳定
氮气纯度连续可调。
用户可由控制盘改变氮气纯度设定,氧气纯度一经设定后即保持稳定。
3.氮气增压机
氮气增压机为多级活塞式压缩机,与传统活塞压缩机相比,大连力德科技开发有限公司高压氮气业系统采用了下列新结构:
(l)增压机采用无水夹套缸体,体积小、密封件少、冬季升温快、不易拉缸。
(2)级间冷却器采用风冷器/水冷却器,散热效率高。
多级冷却器垂直叠放,共用一主风扇,占用空间小。
(3)专用注油泵对多级活塞分别加注润滑油,计量准确、润滑可靠。
活塞润滑油经专用滤油器过滤。
(4)曲轴精密配重,整机震动小。
(5)控制盘采用中心电子数字显示、操作简便。
(6)仪表及润滑管线全部为不锈钢,经久耐用。
4.柴油机配备
空压机及氮气增压机设计由相同型号两台柴油机分别带动。
即便于维护保养,又减低了备件储备量要求。
五.大连力德气体分离技术有限公司氮气作业系统特点
本系统采用世界制氮领域的最新技术中空纤维膜分离空分制氮,配合高效氮气自动化装置。
我公司生产的中空纤维膜分离空分制氮机是通过引进、消化、吸收国外先进技术,开发而成,其主体部分采用了美国AIRPRODUCTS氮膜分离器,该膜特性是抗污染能力强,性能稳定,其控制部分的主要部件采用原装进口仪表。
该设备达到了国内先进水平,得到了用户的好评。
中空纤维分离制氮系统特性:
能耗少:
中空纤维膜由于比表面积大,具有很高的分离系数,比其它空分设备能耗至少15一25%,大大降低了生产成本。
可靠性高:
中空纤维膜分离制氮系统不象其它空分设备,它没有移动的部件,静态运行,只需甚少保养,连续运行可靠性高。
寿命长:
使用寿命在十年以上。
增容简单:
若需增加产氮气量,只需增加膜组件即可。
易于安装:
体积小,重量轻,占地少。
瞬间安装:
开机停机既方便又迅速,操作简单,氮气纯度稳定性好。
特点1一配备油田专用空压机:
本系统空压机选用油田制氮专用移动式螺杆空气压缩机,该种压缩机专门为野外作业、移动使用而设计的,它充分考虑到各种恶劣环境及移动中的要求。
它的技术处于全球压缩机待业的领导地位,设备的最大特点是寿命长,故障率极低,节省能耗,操作方便,适合在非常恶劣的环境下工作。
特点2一使用安全性高:
本系统中的空气预处理系统是保证膜的性能及寿命的重要部分。
对压缩空气中的有害成份除的干净,膜的性能就能得到充分的发挥,并不会被空气污染中毒,则使用寿命就长,因此本系统选用旋风冷却器,加大了除水及油的力度,并选用了美国原装汉克森的空气过滤器粗、细及超细过滤器三支,达到了膜的使用要求,并为防止过滤器滤芯的失效影响对压缩空气的净化处理,所以在每支过滤器上设有压差计,及时显示出滤芯的工作状态并在每支过滤器下面的出口处设一微机控制点。
当最后出来的气体不合格时,微机及时报警,同时关机,决不让不合作气体进入膜组件,这双重保险保证了膜不会受空气的污染,使膜能始终处于最佳高纯净的压缩空气中工作。
同时在旋风冷却器、空气罐及三支过滤器下面都设有排污阀,保证了污物能及时排出,并设有过滤器的压差报警,来提醒操作者对失效过滤器滤芯的更换使过滤器始终处于正常状态,防止污物对滤芯的侵害。
空气加热器是保证把经过净化的压缩空气,加热到一定的温度,以保证空气在最佳的温度进入膜,提高膜的工作效率。
空气温度低降低了膜的分离效果,温度过高则会降低膜的寿命或被损坏。
因此空气加热的温度是非常重要的,本系统采用了微机对净化后的压缩空气进入加热器前的进口温度,加热器的自身温度及加热器出口温度三个温度的严格控制,当加热温度没有达到要求前,气体从自动排放阀排出,当温度达到要求时排放阀自动关闭,进入膜组件的空气自动阀打开则压缩空气进入膜组件进行气体分离,这样能使膜组件始终处于最佳温度工作状态,保证了膜的工作效率及寿命。
特点3—系统自动化程度高:
本系统只要将空气压缩机开启后,将一截止阀打开,开启微机后一切都在自动运行,过滤出来的污物可自动排放,压缩空气温度不到时,自动打开放空阀,自动放空,当温度达到要求时,放空阀自动关闭,通向膜组件的自动阀打开,空气通过膜组件,当氮气纯度达不到设定要求时,自动排放阀打开,自动排空,当氧气线性度达到设定值时,自动排放阀关闭,通向氮气贮罐的自动阀打开,产品气进入氮气贮罐,控制及报警系统可以在系统上,也可搬工作人员的操作室内,使操作人员不必守在设备旁,面貌一新操作室控制即可。
特点4—环境适用性高:
系统充分考虑到工作环境恶劣性,因此对膜组件及仪器、仪表等均组装在密闭的保温箱内。
(l)膜组件的保温加热密封箱考虑木系统工作条件差,环境温度在-30℃—50℃,又是野外使用。
因此为适用各种复杂的工作环境,所以本系统将膜组件安装在一个能加温的保温密封箱中,该箱能做到保温、加温、防尘、防雨功能,保证膜能在最佳的环境中工作。
(2)仪器、仪表安装在控制箱内
测氧仪、微机、电器元件及温度表、压力表等均安装在控制箱中,防止泥沙雨水的侵害及高、低温度的影响。
高温量箱内设有风扇,温度低时,可以加热,使各仪器、仪表在要求的范围内工作,以保证其工作性能
特点5一设备可靠性高:
1.本系统中的连接管路及阀门均采用不锈钢材质,保证在风吹雨打中不会受损。
2.本系统考虑设备安装在两个大集装箱内,可由用户直接安装在拖车上。
3.本系统的增压系统,从增压泵、冷却器到柴油发动机及管路均为原装机进口,所以整套设备性能稳定可靠。
氮气增压机为多级活塞式压缩机,其结构特点如下:
1)增压机采用无水夹套缸体,体积小、密封件少、冬季升温快,不易拉缸。
2)级间冷却器采用风冷却器/水冷却器、散热效率高。
多组冷却器垂直叠放,共用一主风扇占用空间少。
3)专用注油泵对多级活塞分别加注润滑油计量准确,润滑可靠。
4)曲轴精密配重,整机震动少。
5)控制盘采用中心电子数字显示操作简便。
6)仪表及润滑管线全部用不锈钢,经久耐用。
特点6-整个系统灵活性好:
氮气橇主要由螺杆空气压缩机和膜分离器组成。
这两部分都有各自的控制系统,考虑一整个系统在现场工作,环境条件比较苛刻,因此要求控制系统必须可靠,所以选用结构简单可靠,维护方便的仪表和控制部分,以降低可能的故障率和对售货员的要求。
另外,氮气橇有可单独运行,因此两橇控制相独立。
两橇设有联动系统,保证能同时停机。