70t级铁路货车段修技术条件暂行运装货车427号.docx
《70t级铁路货车段修技术条件暂行运装货车427号.docx》由会员分享,可在线阅读,更多相关《70t级铁路货车段修技术条件暂行运装货车427号.docx(53页珍藏版)》请在冰豆网上搜索。
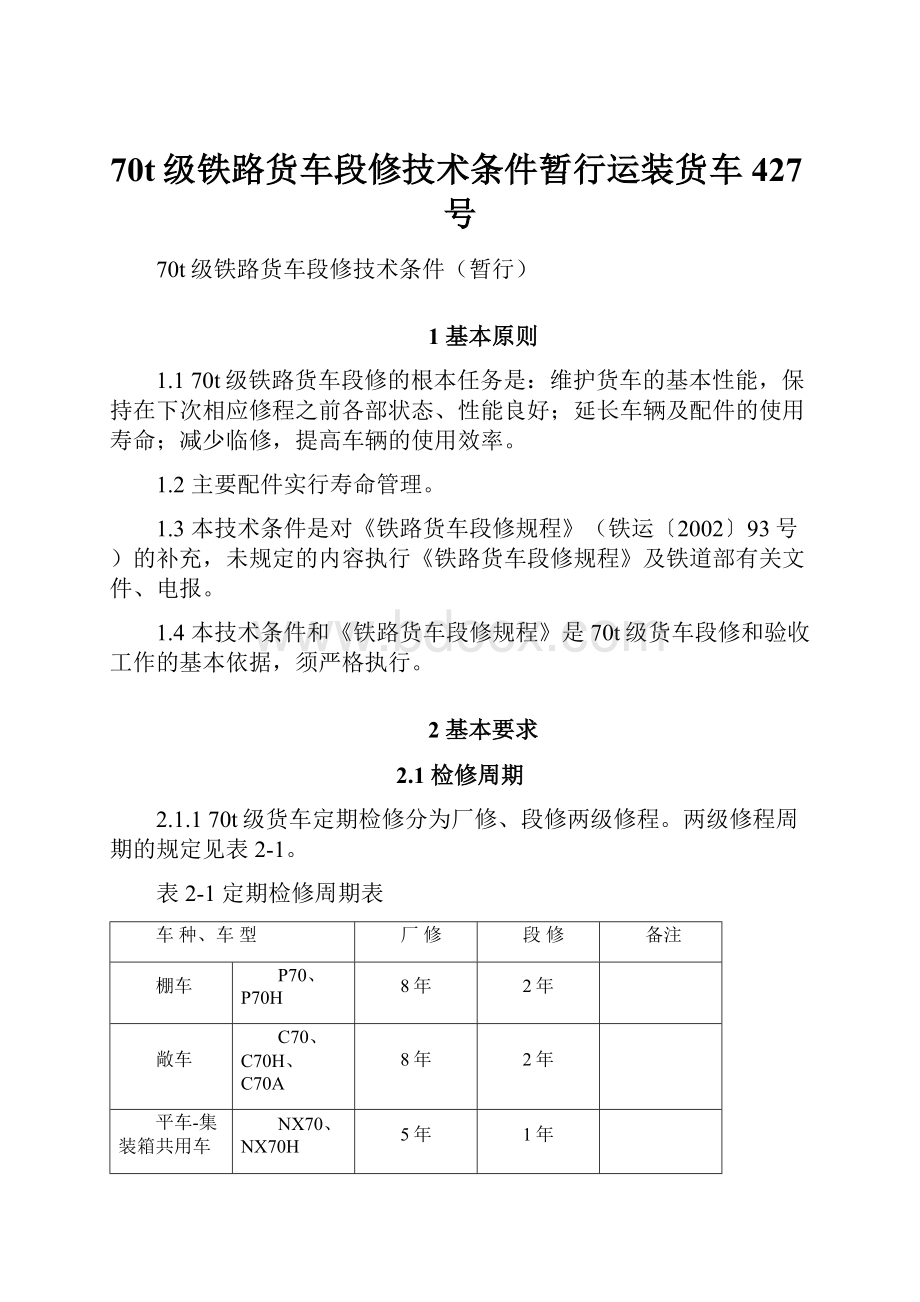
70t级铁路货车段修技术条件暂行运装货车427号
70t级铁路货车段修技术条件(暂行)
1基本原则
1.170t级铁路货车段修的根本任务是:
维护货车的基本性能,保持在下次相应修程之前各部状态、性能良好;延长车辆及配件的使用寿命;减少临修,提高车辆的使用效率。
1.2主要配件实行寿命管理。
1.3本技术条件是对《铁路货车段修规程》(铁运〔2002〕93号)的补充,未规定的内容执行《铁路货车段修规程》及铁道部有关文件、电报。
1.4本技术条件和《铁路货车段修规程》是70t级货车段修和验收工作的基本依据,须严格执行。
2基本要求
2.1检修周期
2.1.170t级货车定期检修分为厂修、段修两级修程。
两级修程周期的规定见表2-1。
表2-1定期检修周期表
车种、车型
厂修
段修
备注
棚车
P70、P70H
8年
2年
敞车
C70、C70H、C70A
8年
2年
平车-集装箱共用车
NX70、NX70H
5年
1年
集装箱平车
X4K
8年
2年
罐车
GQ70、GQ70H
5年
1年
GN70、GN70H
5年
1年
GF70、GF70H
8年
2年
矿石车
KZ70、KZ70H
8年
2年
KM70、KM70H
8年
2年
2.1.2须按现车检修周期标记扣修段修车,以月为准,不得提前。
当厂修、段修同时到期时须做厂修,如确因事故等特殊情况需提前扣修时,须经铁道部批准。
2.2主要配件的寿命管理
2.2.1寿命期限以制造时间为准,时间统计精确到月,车轴使用时间以轮对第一次组装时间为准,当轮对第一次组装时间不明时,以车轴制造时间为准。
实行寿命管理的配件有下列情况之一时报废:
2.2.1.1无制造单位、时间标记。
2.2.1.2摇枕、侧架、车轴、钩体、钩尾框及牵引杆使用时间满25年,钩舌使用时间满20年。
2.2.1.3摇枕、侧架、车轴、钩体、钩尾框及牵引杆使用时间满20年而未满25年,有下列情况之一时:
2.2.1.3.1摇枕、侧架A、B部位裂纹。
2.2.1.3.2车轴横裂纹。
2.2.1.3.3钩体的钩身、冲击台、牵引台横裂纹。
2.2.1.3.4钩尾框、牵引杆横裂纹,纵裂纹长度大于30㎜。
2.2.1.4MT-2型缓冲器使用时间满18年(以箱体标记为准)。
2.2.1.5交叉杆轴向橡胶垫使用时间满6年。
2.2.1.6轴箱橡胶垫使用时间满6年。
2.2.1.7弹性旁承体使用时间满6年。
2.2.1.8心盘磨耗盘使用时间满6年。
2.2.1.9弹簧托板组成使用时间满8年。
2.2.1.10摇动座使用时间满8年。
2.2.1.11滚动轴承经大修后,有下列情况之一时报废:
2.2.1.12.1353130A、353130C紧凑型轴承使用时间满7年(或70万km)。
2.2.1.13.2353130B、C353130、SKFOR-7030AITALY紧凑型轴承使用时间满8年(或80万km)。
2.2.2实行寿命管理的配件,当剩余寿命不足一个段修期时,经检查确认质量状态良好,可继续装车使用,并由装车单位负一个段修期的质量保证责任。
2.2.3实行寿命管理和有制造质量保证期的新制配件必须有制造时间和制造厂代号标记。
标记应清晰,标记位置须在非磨耗部位。
2.3质量保证期
2.3.1检修单位须对整车质量负责。
经过段修的车辆在正常运用、维修的情况下,在质量保证期内由于段修质量不良,不能满足表2-2质量保证要求时,应返段修理;经当地车辆段同意代为修理时,须由责任车辆段承担修理费用。
表2-2段修质量保证期
顺号
部位
保证内容
保证期限
1
车体
1.棚车不漏雨,罐车罐体新焊缝不漏泄、罐体不裂
2.中梁(牵引梁)、侧梁、枕梁、大横梁及枕梁中央下盖板不裂
3.防火板不脱落
1个段修期
2
车钩缓冲装置
1.钩体、钩尾框无旧痕裂损
2.钩舌无旧痕裂损
3.车钩闭锁位不超过运用限度,防跳作用不失效
1个段修期
3
转向架
1.摇枕、侧架无旧痕裂损
2.交叉支撑装置各零部件、弹簧托板组成、摇动座无旧痕裂损
3.重新组装的交叉支撑装置无组装质量问题
4.新焊支撑座不裂
1个段修期
1个段修期
剩余厂修期
剩余厂修期
4
轮对与滚动轴承
1.轮对
①车轴经超声波探伤的部位不裂
②车轴外露部位不裂
③车轮无旧痕裂损
2.滚动轴承
①一般检修者无一般检修范围内的质量问题
②轴颈与滚动轴承组装(压装)不松动、无组装质量问题
③未退卸经外观检查者无外观质量问题
1个段修期
1个段修期
1个段修期
1个段修期
1个段修期
3个月
5
制动
装置
1.制动梁梁体及支柱、闸瓦托、滑块、各拉杆及链无旧痕裂损,闸瓦托不松动
2.编织制动软管总成、控制阀、限压阀、传感阀不发生故障
3.球芯折角塞门、组合式集尘器、密封式制动缸、法兰接头、主管、支管无旧痕裂损
4.闸瓦间隙自动调整装置和人力制动机不发生故障
1个段修期
6
底开门机构
1.操纵阀、给风调整阀、旋压双向风缸、风动管路无旧痕裂损
2.底开门机构不发生故障,各传动部件无旧痕裂损
1个段修期
注:
1.质量保证是指在保证期限内,车辆在正常运用中不应发生的质量故障。
但不包括在定期检修时发现的问题。
2.凡由于运用中不正常冲撞、脱轨、超载、偏载、集重、装卸碰撞、错装(车型不符),或由于操作不良、擅自拆卸等情况而导致的损坏,均不属质量保证范围。
3.事故责任的确定按铁道部《铁路行车事故处理规则》办理。
2.3.2配件制造质量保证内容和保证期限
2.3.2.1在正常使用条件下,凡在制造质量保证期限内配件发生质量问题时,须由配件制造单位承担质量保证责任,装用单位承担装用责任。
2.3.2.2车辆在检修中因设计、制造原因,需改造的项目或配件在质量保证期内超过段修限度或产生裂损等影响使用的缺陷,需更换的配件由车辆制造或检修单位无偿以旧换新,车辆制造或检修单位继续向配件生产单位进行质量追溯。
2.3.2.3在使用寿命期内,因配件内部缺陷造成事故时由制造单位负责。
2.3.2.4质量保证期限以制造时间为准,时间统计精确到月。
配件制造质量保证内容和保证期限见表2-3。
表2-3配件制造质量保证内容和保证期限
顺号
配件名称
保证内容
保证期限
备注
1
底架、端墙、侧墙、车顶、罐体等车体承载结构
无裂损
1个厂修期
2
摇枕、侧架、钩体、铸造钩尾框、牵引杆
无裂损、铸造缺陷不超限
8年
3
锻造钩尾框
无裂断
25年
4
钩舌
无裂损、铸造缺陷不超限
6年
6
控制阀、传感阀、限压阀
阀体无裂损、不漏泄
铸造缺陷不超限
9年
7
组合式集尘器、球芯折角塞门、球芯直端塞门
器体无裂损、不漏泄
铸造缺陷不超限
8年
8
制动缸体及前盖
无裂损
8年
9
脱轨自动制动阀
阀体、阀盖、拉环
无裂损
8年
10
制动阀杆、作用杆
无裂损,阀杆端头与作用杆孔上、下间隙不超限
2年
11
顶梁组成、弹片
无裂损、变形和磨耗不超限
2年
12
摇动座
无裂损、磨耗不超限、铸造缺陷不超限
8年
13
弹簧托板
无裂损
8年
14
上、下心盘
无裂损、磨耗不超限
8年
15
MT-2型缓冲器
无裂损、铸造缺陷不超限
6年
16
闸瓦间隙自动调整器
不失效
6年
17
组合式制动梁(不含滑块磨耗套)
无裂损
8年
18
转向架交叉杆、支撑座
无裂损
8年
19
含油尼龙钩尾框托板磨耗板
无裂损、磨耗不超限
8年
20
轴箱橡胶垫、弹性旁承橡胶体、轴向橡胶垫
不失效
6年
21
摇枕弹簧、减振弹簧
无裂损、不失效
9年
22
侧架立柱磨耗板
无裂损、磨耗不超限
8年
23
组合式斜楔体
无裂损、磨耗不超限
8年
24
斜楔主摩擦板
裂损、磨耗不超限
1个厂修期
25
心盘磨耗盘
裂损、磨耗不超限
6年
26
奥-贝球铁衬套
无裂损、磨耗不超限
8年
27
侧架滑槽磨耗板
无裂损、磨耗不超限
8年
28
摇枕斜楔摩擦面磨耗板
无裂损、磨耗不超限
3年
29
旁承磨耗板、制动梁滑块磨耗套
无裂损、磨耗不超限
2年
30
编织制动软管总成
不脱层、无裂损、漏泄不超过规定
6年
31
人力制动机
无裂损、磨耗不超限、作用不失效
6年
32
双向风缸体及前盖、减速箱体、传动轴轴承
无裂损
8年
33
操纵阀、给风调整阀、减压阀
阀体无裂损,铸造缺陷不超限
8年
34
底门开闭机构
作用正常,各传动部件无裂损
8年
2.3.3向车辆上安装的轮对按月计算其超探的剩余保证期,须达到下次段修到期月份。
轮座镶入部位发生断轴事故时,在组装保证期内的,由轮对组装单位负责;超过组装保证期的,由向车辆上安装的单位负责。
轴颈根部、防尘板座及轮座外侧的外露部位发生断轴时,轮对第一次组装不超过5年时,由轮对组装单位负责;但轴承如经退卸,由重新压装轴承的单位负责。
2.4其他
2.4.1架车前须分解脱轨自动装置拉环。
2.4.2制动衬套材质须为奥-贝球铁,硬度为38~48HRC;制动圆销材质须为45号钢,热处理后表面硬度为50~55HRC。
3车体
3.1综合要求
3.1.1车体挖补、截换时须符合原设计的材质要求,70t级货车车体主要部件材质见表3-1。
表3-1车体主要部件材质
车型
型钢
板材
端、侧墙
罐体
冲击座
前、后从板座
P70、P70H
Q450NQR1
Q450NQR1
09CuPCrNi-A
C级铸钢
C级铸钢
C70、C70H、C70A
Q450NQR1
Q450NQR1
Q450NQR1
C级铸钢
C级铸钢
NX70、NX70H
09CuPTiRE-B或09CuPCrNi-A
Q450NQR1
C级铸钢
C级铸钢
X4K
Q450NQR1(槽钢)
09CuPCrNi-A(方管)
Q450NQR1
C级铸钢
C级铸钢
GQ70、GQ70H
GN70、GN70H
Q450NQR1
Q345A
Q345-A、Q295-A
B级铸钢
C级铸钢
GF70、GF70H
Q450NQR1
Q450NQR1
Q450NQR1
C级铸钢
C级铸钢
KZ70、KZ70H
KM70、KM70H
Q450NQR1
Q450NQR1
Q450NQR1
C级铸钢
C级铸钢
3.1.2Q450NQR1高强度耐候钢、09CuPCrNi-A、09CuPTiRE-B、Q345-A高耐候结构钢及C级铸钢的焊接须执行相应焊接工艺。
Q450NQR1高强度耐候钢的化学成分及机械性能、焊接工艺及技术要求见附件A和附件B。
3.1.3采用专用拉铆钉连接的部件重新铆接时,须采用专用拉铆钉及专用设备。
铆接工艺见附件C。
3.1.4专用拉铆钉铆接后,零部件的接触面间须严密,在距铆钉中心50㎜范围内用厚0.5㎜的塞尺测量,不得触及铆钉杆,触及时须重新铆接。
3.2底架附属件
3.2.1牵引梁内侧磨耗板焊缝开裂时焊修,上部磨耗板磨耗大于2㎜时更换,两侧磨耗板磨耗大于3㎜时更换。
上部磨耗板材质为27SiMn,规格为204㎜×204㎜×12㎜,两侧满焊;两侧磨耗板材质为Q235-A,规格为250㎜×140㎜×10㎜,两侧段焊。
3.2.2上旁承磨耗板原型厚度为14㎜,磨耗大于2㎜或裂纹时更换,上旁承磨耗板下表面须抛光处理,平面度为1㎜;上旁承调整垫板总厚度为2~25㎜,数量为1~2块;组装螺栓与螺母须点焊固。
3.3车体
3.3.1P70、P70H型车车门的门挡组成连接螺栓作用不良或丢失时须更换,材质为橡胶的顶板破损时更换,门挡座与侧板和侧柱的焊缝开裂时焊修。
3.3.2P70、P70H型车通风器作用良好时可不分解检修。
3.3.3C70、C70H型车侧开门的上门锁杆、下门锁铁、手把支座等装置须齐全,作用良好,防盗焊接牢固。
3.3.4NX70、NX70H型车集装箱锁闭装置须符合图样ECH58-09-00-000,X4K型集装箱车门挡与锁闭装置须符合图样QCH246B-50-00-000,配件齐全,作用良好。
3.3.5GN70、GN70H型车内加热装置须进行压力为200kPa的气密性试验,保压10min,不得漏泄。
3.3.6GF70、GF70H型车
3.3.6.1压铁变形、裂损时调修或更换。
3.3.6.2尼龙帆布因物料板结导致透气性能失效时清理,清理后失效面积之和大于总面积的50%时更换。
3.3.6.3水平流化床区域内的罐体、补板及吊托与罐体的结合部进行火焰调修、补焊及截换时,须掀开水平流化床,采取防护措施。
3.3.6.4安全阀组装后进行气密性试验:
压力达到440kPa时须开始排风,压力降至380kPa时须停止排风。
3.3.6.5各管路变形时调修或更换,腐蚀大于30%时截换或更换,截换时风管及卸料管每节长度不小于500㎜。
3.3.6.6组装时喇叭口至流化床盲板上平面的距离为50+20㎜,超限时可安装钢垫圈调整。
3.3.7KZ70、KZ70H、KM70、KM70H型车
3.3.7.1侧板、端板、门板、窗板及地板腐蚀深度大于30%时挖补或补强,挖补时须对接,外露部分须两面焊;窗板腐蚀面积大于50%时更换。
3.3.7.2侧墙板内凹、外胀大于30㎜,端墙板内凹、外胀大于50㎜时调修。
3.3.7.3侧柱、端柱、角柱裂纹时焊修后补强,腐蚀深度大于30%时截换或补强;侧柱、端柱外胀大于30㎜时调修。
3.3.7.4顶板或檐板下垂大于30㎜时调修;顶板或檐板支承腐蚀深度大于30%时截换或更换;支承和边梁弯曲时调修,裂纹时焊修。
3.3.7.5分碴板、流碴板、底门包板、导流板及筋板腐蚀、磨耗严重时挖补、截换、补强或更换。
3.3.7.6漏斗板、漏斗脊背、调整板及导流板腐蚀、磨耗严重时挖补、补强或更换。
挖补时须对接两面焊。
3.3.7.7观察孔盖开关须作用良好,变形时调修。
3.3.7.8底门风控管路按制动管系标准检修。
3.3.7.9风控管路检修后须试验并符合下列要求:
3.3.7.9.1漏泄试验:
储风缸压力为420kPa时,关闭制动主管与风控装置储风缸之间的截断塞门,保压1min,风控装置漏泄量不大于10kPa。
3.3.7.9.2保压试验:
储风缸压力为420kPa时,关闭制动主管与风控装置储风缸之间的截断塞门,制动管压力降为零后保压,1min内制动管压力不得上升。
3.3.7.9.3试验完毕关闭制动主管与风控装置储风缸之间的截断塞门。
3.3.7.10底门机械开闭系统须分别进行手动及风动开闭性能试验,开关底门时,机构应传动平稳、轻便、灵活,且须符合下列要求:
3.3.7.10.1KZ70、KZ70H型车底门开度不小于190㎜,KM70、KM70H型车底门开度为460±20㎜;各曲拐和传动轴连接不松动。
3.3.7.10.2使用手动传动机构应能灵活开关底门,手动关门力矩不大于80N·m。
3.3.7.10.3底门关闭后,KM70、KM70H型车左、右锁体滑槽端面应与底门销密贴,间隙不大于2㎜;上曲拐转至极限位置时,连杆应通过死点,形成自锁状态。
3.3.7.10.4风动开关底门的灵敏度:
空车开门压力不大于150kPa,关门压力不大于260kPa。
4车钩缓冲装置
70t级货车装用17型车钩(16型钩舌),17型铸造或锻造钩尾框,MT-2型缓冲器;C70A装用16、17型车钩及牵引杆。
4.117型钩体
4.1.1钩身下平面须焊装磨耗板,磨耗板磨耗超限时更换,丢失时补装。
磨耗板应焊装在钩身下平面距钩肩51㎜处,规格为250㎜×150㎜×6㎜,两侧段焊,如图4-1所示。
磨耗板材质为27SiMn,硬度为314~415HBW,须使用经烘干处理的J606焊条焊接。
图4-1钩体磨耗板焊装示意图
4.217型钩尾框及钩尾框托板磨耗板
4.2.117型锻造钩尾框磨耗超限时堆焊后磨平。
4.2.2不得焊装钩尾框框身磨耗板,须配套装用图号为QCH194A-84-00-002含油尼龙钩尾框托板磨耗板,如图4-2所示。
图4-2含油尼龙钩尾框托板磨耗板装用示意图
4.2.3含油尼龙钩尾框托板磨耗板原型厚度为8㎜,剩余厚度小于4㎜或裂损时更换。
4.3车钩组装
4.3.1车钩组装后处于闭锁位置时,车钩闭锁显示孔须全部露出,如图4-3所示。
图4-3闭锁显示孔示意图
4.3.2钩舌处于牵引位置时,用检查样板与钩头正面贴靠,闭锁位置钩舌内侧面与钩体正面沿垂直方向距离须不大于97㎜,如图4-4所示。
图4-4闭锁位置内侧面与钩体正面距离检查示意图
4.4牵引杆
4.4.1杆身、杆颈横裂纹在同一断面之和小于50㎜时焊修,大于时更换。
4.4.2钩尾销孔周围25㎜范围内裂纹时焊修;超过范围的裂纹深度小于3㎜时可铲磨清除,大于3㎜时更换。
4.4.3钩尾销孔后壁与钩尾端部距离小于83㎜时堆焊后磨平,小于77㎜时更换。
4.4.4长度小于1741㎜时在两端堆焊后磨平,小于1734㎜时更换。
4.4.5尾端高度磨耗超限时堆焊后磨平。
4.4.6焊修后须经热处理,材质保持为E级钢;材质无法保持为E级钢时更换。
4.5车钩缓冲装置检修限度表(表4-1)
表4-1车钩缓冲装置检修限度表单位㎜
序号
名称
原型
段修
备注
1
钩尾端部与钩尾销孔后边缘的距离不小于
89
83
钩尾端部与钩尾销孔边缘的距离小于77㎜时更换
2
闭锁位置时钩舌内侧面与钩体正面距离不大于
82~89
97
3
全开位置时钩舌内侧面与钩腕内侧面距离不小于
219
4
钩舌销孔径向磨耗不大于
42
2
5
17型锻造钩尾框磨耗不大于
(1)框身厚度
(2)其他部位
28
3
4
5转向架
C70、C70A、P70、NX70、X4K、GQ70、GN70、GF70、KZ70、KM70等型车须装用转K6型转向架,C70H、P70H、NX70H、GQ70H、GN70H、GF70H、KZ70H、KM70H等型车须装用转K5型转向架。
5.1转K6型转向架
5.1.1侧架
5.1.1.1导框两侧摩擦面单侧磨耗(含局部磨耗)大于2㎜、两侧磨耗之和大于3㎜,内侧面磨耗(含局部磨耗)深度大于3㎜或组装间隙超限时,堆焊后加工。
5.1.1.2承载鞍支承面检修须符合下列要求:
5.1.1.2.1偏磨大于1㎜时加工,磨耗大于3㎜时堆焊后加工,恢复原型。
5.1.1.2.2加工后承载鞍支承面与导框两侧摩擦面未磨耗部位的垂直度为1㎜,承载鞍支承面至支撑座安装孔中心距离为412±2㎜。
5.1.1.3卡入式滑槽磨耗板裂损或磨耗大于3㎜时更换。
磨耗板材质为47Mn2Si2TiB或T10,材质为47Mn2Si2TiB时硬度须为43~58HRC,材质为T10时硬度须为36~42HRC或332~392HBW。
5.1.1.4侧架立柱磨耗板丢失时补装,磨耗大于3㎜、裂损时更换,松动时更换折头螺栓。
组装时,须采用ZT型平头折头螺栓,螺栓紧固力矩为500~550N·m,折头端须低于侧架立柱磨耗板平面,新组装磨耗板与侧架立柱的间隙,用厚度为0.8㎜(顶部用1㎜)塞尺检查,插入深度不得大于13㎜。
侧架立柱磨耗板材质为45号钢,热处理后硬度为38~50HRC。
5.1.1.5侧架立柱与摇枕挡内表面配合处磨耗大于3㎜时,堆焊后磨修恢复原型。
5.1.1.6侧架制动梁滑槽无防止制动梁脱出挡块时,须按图样QCZ133JX-20-01焊装挡块。
5.1.2摇枕
5.1.2.1摇枕斜楔摩擦面磨耗板检修须符合下列要求:
5.1.2.1.1焊缝开裂时焊修,裂损、磨耗大于3㎜时更换。
5.1.2.1.2焊装磨耗板前摇枕斜楔摩擦面(基准面)须平整,不平整时须堆焊后磨平,磨耗板的焊装如图5-1所示。
图5-1摇枕斜楔摩擦面磨耗板焊装示意图
5.1.2.1.3斜楔摩擦面磨耗板材质为0Cr18Ni9,硬度不大于187HBW。
5.1.2.2摇枕挡内、外表面距离大于283㎜时,须堆焊后磨修,恢复原型;摇枕斜楔槽内、外表面磨耗超限时,须对中焊修后磨平,恢复原型。
5.1.2.3摇枕弹簧定位圆脐为结构Ⅰ的,磨耗部位小于最小磨耗尺寸时焊修后磨修,磨修部位应符合结构Ⅱ圆脐相应部位尺寸,未焊修部位不用磨修;摇枕弹簧定位圆脐为结构Ⅱ的,磨耗部位小于最小磨耗尺寸时焊修后磨修,磨修部位应符合结构Ⅱ圆脐相应部位尺寸。
弹簧定位圆脐如图5-2所示。
图5-2摇枕定位圆脐示意图
5.1.2.4摇枕上拉杆托架组成的含油尼龙滚套外表面磨耗深度大于3㎜时更换。
5.1.3轴箱橡胶垫
5.1.3.1中间橡胶挤出变形或中间橡胶层与上、下钢衬板脱开时更换。
5.1.3.2轴箱橡胶垫允许有龟裂;表面裂纹深度大于10㎜且水平投影长度超过该边长度的50%时更换。
5.1.3.3铜铰线及配套紧固螺母丢失时须补装。
5.1.4承载鞍
5.1.4.1顶面偏磨大于1.5㎜时加工,磨耗超过5㎜时更换。
5.1.4.2导框挡边内侧磨耗一侧大于2㎜或两侧之和大于3㎜时更换。
5.1.4.3导框底面磨耗一侧大于2㎜或两侧之和大于3㎜时更换。
5.1.4.4鞍面径向(半径)磨耗大于0.5㎜时更换。
5.1.4.5推力挡肩两端磨耗后不大于165.8㎜时须消除棱角,大于时更换。
5.1.5组合式斜楔
5.1.5.1须装用组合式斜楔,斜楔体材质为贝氏体球墨铸铁(ADI),主摩擦板材质为高分子复合材料,配套装用45号钢侧架立柱磨耗板。
5.1.5.2组合式斜楔主摩擦板原型厚度10㎜,磨耗大于4㎜时更换;斜楔体副摩擦面磨耗大于3㎜时更换。
主摩擦板四角断裂区域限度如图5-3(a)所示;两角断裂区域限度如图5-3(b)所示;断裂区域超限或缺损面积之和大于总面积的15%时更换。
(a)(b)
图5-3斜楔主摩擦板断裂区域限度示意图
5.1.6JC型双作用弹性旁承
5.1.6.1尼龙磨耗板裂损或磨耗超限时更换。
5.1.6.2弹性旁承橡胶体表面裂纹深度大于5㎜且水平投影长度大于该边长度的30%时更换。
5.1.6.3弹性旁承纵向定位橡胶块与两侧金属板中的一侧全部脱开时更换。
5.1.6.4旁承座与滚子轴接触凹槽磨耗大于3㎜时,焊修后加工,恢复原型;旁承滚子外径径向磨耗、腐蚀深度大于2㎜或严重变形影响作用时更换。
旁承滚子与滚子轴的间隙大于2㎜时更换;旁承座底面、侧面磨耗大于2㎜时,更换或与弹性旁承体分离后堆焊加工、恢复原型。
5.1.7弹簧
5.1.7.1弹簧规格见表5-1。
表5-1转K6型转向架圆弹簧规格表