计算机辅助机械产品设计090156.docx
《计算机辅助机械产品设计090156.docx》由会员分享,可在线阅读,更多相关《计算机辅助机械产品设计090156.docx(30页珍藏版)》请在冰豆网上搜索。
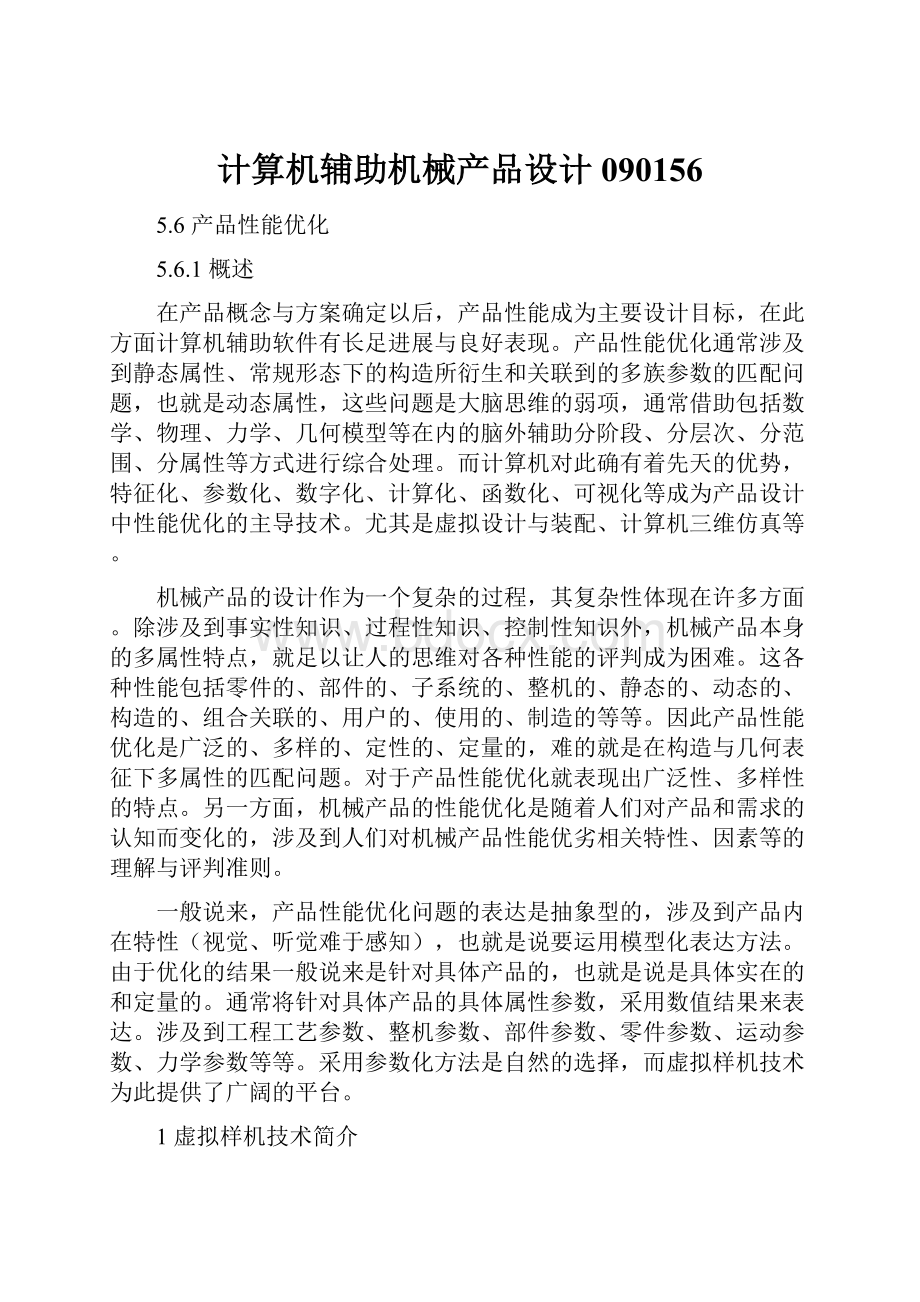
计算机辅助机械产品设计090156
5.6产品性能优化
5.6.1概述
在产品概念与方案确定以后,产品性能成为主要设计目标,在此方面计算机辅助软件有长足进展与良好表现。
产品性能优化通常涉及到静态属性、常规形态下的构造所衍生和关联到的多族参数的匹配问题,也就是动态属性,这些问题是大脑思维的弱项,通常借助包括数学、物理、力学、几何模型等在内的脑外辅助分阶段、分层次、分范围、分属性等方式进行综合处理。
而计算机对此确有着先天的优势,特征化、参数化、数字化、计算化、函数化、可视化等成为产品设计中性能优化的主导技术。
尤其是虚拟设计与装配、计算机三维仿真等。
机械产品的设计作为一个复杂的过程,其复杂性体现在许多方面。
除涉及到事实性知识、过程性知识、控制性知识外,机械产品本身的多属性特点,就足以让人的思维对各种性能的评判成为困难。
这各种性能包括零件的、部件的、子系统的、整机的、静态的、动态的、构造的、组合关联的、用户的、使用的、制造的等等。
因此产品性能优化是广泛的、多样的、定性的、定量的,难的就是在构造与几何表征下多属性的匹配问题。
对于产品性能优化就表现出广泛性、多样性的特点。
另一方面,机械产品的性能优化是随着人们对产品和需求的认知而变化的,涉及到人们对机械产品性能优劣相关特性、因素等的理解与评判准则。
一般说来,产品性能优化问题的表达是抽象型的,涉及到产品内在特性(视觉、听觉难于感知),也就是说要运用模型化表达方法。
由于优化的结果一般说来是针对具体产品的,也就是说是具体实在的和定量的。
通常将针对具体产品的具体属性参数,采用数值结果来表达。
涉及到工程工艺参数、整机参数、部件参数、零件参数、运动参数、力学参数等等。
采用参数化方法是自然的选择,而虚拟样机技术为此提供了广阔的平台。
1虚拟样机技术简介
人们在产品开发与应用过程中,逐渐认识到这样一个事实:
即使机械系统中的每个零部件都是经过优化的,也不能保证整个系统的性能是良好的,即系统级的优化绝不是系统中各部件优化的叠加,而是由各部件组成的整机系统性能优化。
机械系统虚拟样机技术作为一种应用于机械系统设计过程中的高新技术手段,是现阶段解决这类问题较为有效的技术方案之一。
虚拟样机技术(VirtualPrototypeTechnology)是当前设计制造领域的一门新技术,涉及多体系统动力学、计算方法与软件工程等学科。
它通过计算机软件建立机械系统的三维实体模型与力学模型,利用参数化方法分析和评估系统的性能,从而为物理样机的设计和制造提供合理的参数匹配依据。
虚拟样机技术的主体是被称为机械系统动态仿真的技术,是国际上二十世纪八十年代随着计算机技术的发展而迅速发展起来的一项计算机辅助工程(CAE)技术。
它是一种崭新的产品开发方法,是一种基于产品的计算机仿真模型的数字化设计方法,它从构造、功能和行为上模拟真实产品,支持并行工程方法学。
目前对于虚拟样机的概念还没有一种通用精确的定义,针对不同的研究领域,有不同的定义方法。
从机械工程研究领域的角度出发,EdP.Andert等人认为虚拟样机是一种针对测试的对象和物理原型进行的一个虚拟制造和仿真过程,基于虚拟样机技术建立的工程化制造开发模型可以使设计人员访问一个实际物理模型的所有关于机械、物理、外观和功能特性的有关信息。
虚拟样机技术研究的优势主要是机械系统运动学和动力学分析,核心是利用计算机辅助分析技术进行机械系统的运动学和动力学分析,以确定系统及其各构件在任意时刻的位置、速度和加速度,同时,通过求解代数方程组,确定引起系统其各构件运动所需的作用力和反作用力。
2虚拟样机技术的相关技术
机械系统的种类繁多,虚拟样机分析软件在进行机械系统运动学和动力学分析时,需要融合其他相关技术。
为了能充分发挥不同分析软件的特长,有时可能希望虚拟样机软件可以支持其他机械系统计算机辅助工程(MCSE)软件,或者反过来,虚拟样机的输入数据可以由其他的专用软件产生。
图5-21给出了虚拟样机技术的相关技术。
虚拟样机的开发和实施涉及以下技术:
(1)几何形体的计算机辅助设计(CAD)技术。
用于机械系统的几何建模与构造实现,或者用来展现机械系统优化构造的仿真分析结果。
在几何建模中,模型主要是二维图形、三维线框和三维实体造型。
几何建模技术还包括不同格式的几何模型间的无损变换;几何模型的渲染技术,主要有表面纹理修饰和光照技术;几何模型的操纵技术,涉及模型的坐标变换、立体显示、消隐、透明等
(2)有限元分析(FEA)技术。
可以利用机械系统的运动学和动力学分析结果,确定进行机械系统有限元分析所需要的外力和边界条件。
或者利用有限元分析对构件应力、应变和强度进行进一步的分析。
(3)模拟各种各样的软件编程技术。
虚拟样机软件运用开放式的软件编程技术来模拟各种力和动力,例如:
电动力、液压力动力、风力等等,以适应各种机械系统的要求。
(4)利用实验装置的实验结果进行某些构件的建模。
实验结果经过线性化处理输入机械系统,成为机械系统模型的一个组成部分。
(5)控制系统设计与分析技术。
虚拟样机可以运用传统的和现代的控制理论,进行机械系统的运动仿真分析。
或者可以应用其他专用的控制系统分析软件,进行机械系统和控制系统的联合分析。
(6)优化分析技术。
运用虚拟样机分析技术进行机械系统的优化设计和分析,是一个重要的应用领域,通过优化设计,确定最佳设计机构和参数值,使机械系统获得最佳的综合性能。
3虚拟样机设计方法的特点
同传统的基于物理样机的设计研发方法相比,虚拟样机设计方法具有以下特点:
参数化方法使得虚拟样机具有全新的研发模式。
传统的研发方法从设计到生产是一个串行过程,这种方法存在很多弊端。
而虚拟样机技术真正地实现了系统多角度的产品优化,它基于并行工程,使产品在概念设计阶段就可以迅速地分析、比较多种设计方案,确定影响性能的敏感参数,并通过可视化技术设计产品、预测产品在真实工况下的特征以及所具有的响应,直至获得最优工作性能。
虚拟样机使产品的开发设计具有更低的研发成本、更短的研发周期、更高的产品质量。
采用虚拟样机设计方法有助于摆脱对物理样机的依赖。
通过计算机技术建立产品的数字化模型(即虚拟样机),可以完成无数次物理样机无法进行的虚拟试验(成本和时间条件允许),从而无需制造及试验物理样机就可获得最优方案,因此不但减少了物理样机的数量,而且缩短了研发周期、提高了产品质量。
降低了开发成本与风险。
虚拟样机技术是实现动态联盟的重要手段。
目前世界范围内广泛地接受了动态联盟的概念,即为了适应快速变化的全球市场,克服单个企业资源的局限性,出现了在一定时间内,通过Internet临时缔结成的一种虚拟企业。
为实现并行设计和制造,加盟企业之间产品信息的敏捷交流尤显重要,而虚拟样机是一种数字化模型,通过网络输送产品信息,具有传递快速、反馈及时的特点,进而使动态联盟的活动具有高度的并行性。
4虚拟样机技术的实现
虚拟样机技术在工程中的应用是通过界面友好、功能强大、性能稳定的商品化虚拟样机软件实现的。
目前比较有影响的产品包括美国机械动力学公司MDI的ADAMS,比利时LMS公司的DADS,德国航天局的SIMPACH,俄罗斯航天工业尖端技术EULER以及韩国FunctionBay公司开发出的新一代动力学仿真软件RecurDyn等。
在虚拟样机领域最具领先地位的软件是MDI的ADAMS,它是建立在多体动力学基础上大型机械系统自动动力学分析软件。
因此,熟悉多体动力学理论对于软件使用是相当重要的。
多体系统动力学是通过将机械系统划分为若干个自由刚体或弹性体,采用广义坐标,应用拉氏方程确立其力学行为的。
这种处理方法极大地方便了软件使用者的各种要求。
5虚拟样机技术的工程应用
传统的机械设计与制造,从概念设计开始经过方案论证、产品设计,直到制造物理样机来验证设计。
如果通过物理样机实验发现缺陷,便进行修改设计,并重复以上步骤,直至获得满意的产品为止。
通过周而复始的设计-实验-设计的过程,产品才能达到要求。
这一过程是漫长的。
虚拟样机技术可以使产品设计人员在各种虚拟环境重复地模拟产品的运动及受力情况,对于设计中的缺陷和不足,利用软件可以很方便地做出修改,快速分析多种设计方案,进行对物理样机而言难以进行或根本无法进行的实验,直到获得系统及的优化设计方案。
虚拟样机技术在国外已得到广泛应用,涉及汽车制造业、工程机械、航天航空业、造船业、国防工业、通用机械制造业、人机工程、生物力学以及工程咨询等领域。
1)汽车制造方面,一家卡车制造公司在研制新型柴油机时,发现点火控制系统的链条在转速达到每分钟6000转时运动失稳并法生振动。
常规的测量技术在这样的高温下的环境失灵,工程师们不得不借助于虚拟样机技术。
根据对虚拟模型的动力学及控制系统的分析结果,发现了不稳定因素,改进了控制系统,使系统的稳定范围达到每分钟10,000转以上。
2)工程机械在高速行驶时的蛇行现象及在重载下的自激振动一直困扰着设计师及其用户。
由于工程机械系统非常复杂,传统的分析方法无能为力,找不出原因。
约翰.迪尔(JohnDeere)公司的工程师利用虚拟样机技术对其工程机械产品进行分析,不仅找到了原因,而且提出了改进方案,并且在虚拟模型上验证了方案的有效性。
通过实际改进,该公司产品的高速行驶性能与重载作业性能大为提高。
3)航天航空方面,美国航空航天局(NASA)的喷气推进实验室(JPL)利用的虚拟样机技术研究飞船在进入火星大气层、减速、着陆不同阶段的工作过程,成功的预测到由于制动火箭和火星风的作用,探测器有可能在着陆时翻滚,于是工程师们针对这个问题进行了修改,成功地实现了探测器的软着陆。
4)造船界的美国AME的工程师利用虚拟样机技术研究轮船装料台的工作过程,快速分析了几百种装料台在不同工作情况下的性能。
与传统的设计方法相比较,虚拟样机技术在制造物理样机之前就能够进行样机的各种测试与实验,从而发现潜在的设计缺陷和问题,减低产品开发成本、缩短产品开发周期、提高产品设计质量。
据统计,应用虚拟样机技术的设计方法比传统的设计方法在开发周期上缩短了40%~70%、在研发经费上投入传统设计方法的10%,就可以达到传统设计方法90%的目标。
5.6.2振动磨虚拟样机分析应用实例
1.振动磨虚拟样机设计过程
1)建立虚拟样机动力学模型
依靠ADAMS/View模块中的交互建模环境建立磨机的虚拟样机。
包括零件的几何模型的建立、约束副的处理与添加、驱动力与运动特性的处理与添加等。
2)验证模型
通过虚拟仿真结果和物理样机的测试结果,验证模型。
3)振动体与介质的运动学与动力学仿真分析
分别对振动体与介质进行了运动学与动力学分析,明确了振动磨稳定工作时整机的运动特性与动力特性,介质的运动特性与受力特点等。
4)对振动特性的仿真分析包括
a)介质碰撞力的影响因素及对磨矿性能的影响
b)介质输送速度的影响因素及对磨矿粒度与产量的影响
c)筒体摆角的影响因素及对介质动力特性的影响
d)激振频率对介质碰撞力与介质输送速度的影响等
5)虚拟样机技术所作的数字仿真研究与高速摄影、物理样机实验比较,确定磨机系列化设计参数的规律。
2.振动磨机的模型化原则与方法
虚拟样机技术的首要事情是产品原型的模型化,其目的在于应用适当的几何与动力特性参数,获得最佳的物理样机实验效率和效益。
这个过程的核心是对所设计产品的动力学本质的认识,包括运动质量参数、质量关联参数、质量与力的关联参数、力与力的关联方式与参数、运动参数、运动关联参数、力与运动的关联参数等。
由于模型化问题是软件应用的前处理,因此要仔细了解软件的内部工作机制,尽量将实际产品的本质与软件本质融合在一起。
这种融合的关键就是模型化方法,为此,在一次的重述该方法的要点与原则。
一般说来,对于现实世界中的一个特定对象,为了某个特定目的,根据特有的内在规律,做出一些必要的简化假设,用贴切的符号描述出来,称之为模型。
模型的类型通常有:
物质模型(形象模型)和理想模型(抽象模型)。
前者包括直观模型、物理模型、试验模型等,后者包括思维模型、符号模型、逻辑模型、理论模型、数学模型、计算模型、软件模型、预测模型、解释模型等等。
将实际问题模型化,可以抓住主要矛盾和矛盾的主要方面,解决最本质的问题,解释问题的内部核心实质。
按照特有的内在规律建立模型,可以将问题从一个领域转换(变换、映射)到另一个领域。
模型化的方法主要是,确定现实世界中的研究对象、研究目的,根据问题的特有的内在规律,进行必要的简化假设,用该问题特有的符号(代号)描述出来。
这些符号是在特定学科领域中的抽象表述,而这些抽象表述体现了人们研究问题的方法,更体现了人们对现实问题的本质上的理解。
例如:
物理学中的质点、加速度、惯性、弹性、约束、力、点电荷、电阻、电流、电路、光波等。
数学上的自然数字、字母、运算符号(±、≥、∮、∞、∑、∈、⊥、⊙等)、函数关系、运算法则等。
简约抽象的几何图形往往是研究问题本质的好工具。
软件学科的数据及其结构、对象、类、属性、数据流、消息、数据关联等抽象问题的直观表述。
对研究对象的特有的内在规律,从理论上、实践上、经验上有深刻的了解与理解。
这是建模的基石。
这个基石又是建立在丰富的实践经验与渊博的理论知识之上的。
应该理解到,对现实问题的抽象是模型化的基础,理解与熟悉各种已有模型是建模的基础。
熟悉大量的实例是抽象的基石,而由抽象得来的概念是建模的工具。
建模方法的基础是对符号表达的熟练掌握与正确运用。
对于机械产品的计算机化设计来说,就是要把机械设计中的各种工作转化成计算机可以识别的指令。
为了这个目的必须将产品的某一部分信息简缩、提炼而构造出产品的替代物。
这个过程也称之为抽象。
这项工作通常有以下几个方面:
a.确定计算机化工作的对象和目标。
如:
机械产品的方案论证、产品的整机动力学、产品的零件设计、产品的图形绘制等。
b.确定模型类型:
物理模型、数学模型、计算模型、软件模型等。
如:
减振部件的物理模型、整机性能参数的数量关系模型、零部件强度分析的计算模型、零件或整机设计的软件模型等。
c.确定模型的基本元素及其表达形式。
如:
机械零件中的轴、齿轮、轴承、皮带、键、连杆、链条、位移、速度、约束、转动惯量、扭矩等。
模型的元器件、零部件(系统元素、系统要素)—基本概念(质点、刚体、质量、位移、速度、加速度、齿轮、轴承、连杆、螺栓、压力、温度等)。
d.确定特定对象中各个基本元素之间的关联及其规律,将问题从一个领域转换(变换、映射)到另一个领域的方法和工具。
例如:
力与加速度的关联—牛顿定律(F=ma)、齿轮与轴的关联—键、连杆与连杆的关联—连接销、转动惯量与功率的关联—动能定理等。
模型的结构与构造(系统组成、关联与装配、拼装与组合)与基本原理、基本定理、基本定律、基本法则等紧密相连。
现实世界的抽象、理想化、科学合理的简化依赖于这些基本原理。
通常将现实世界中的物体称作原型,而将简约化后得到的研究对象称作模型。
原型和模型是一对对偶体。
原型是人们在现实世界里关心、研究或者从事生产、管理的实际对象。
在科技领域通常使用系统、过程等词汇,如机械系统、电力系统、生态系统、生命系统、社会经济系统,又如钢铁冶炼过程、产品开发过程、化学反应过过程、污染扩散过程、生产销售过程、计划决策过程等,本书所述的现实现象、研究对象、实际问题等均指原型。
模型是为某个特定的目的将原型的某一部分信息简缩、提炼而构造的原型替代物。
是经过剔除不必要的细节,而对核心的本质问题所作的简化描述,也就是抽象或称理想化。
这里特别强调构造模型的目的性。
模型不是原型原封不动的复制品,原型有各个方面和各种层次的特征,而模型只要求反应与某种目的有关的那些方面和层次。
一个原型,为了不同的目的可以有许多不同的模型。
如放在展厅里的塔式起重机模型,在外形上非常逼真,但是不能起吊重物,而参加机械博览会的塔式吊车,则应该具有良好的起吊性能。
所以模型的基本特征是由构造模型的目的决定的。
那些供展览用的实物模型(直观模型),以及玩具、照片等,通常把原形尺寸按比例缩小或放大,主要追求外观上的逼真。
这类模型的效果是一目了然的。
通过人们对原型的反复认识,将获得的知识以经验形式直接存贮在人脑中,从而可以根据思维或直觉做出相应的决策,得到相应的思维模型。
如汽车司机对方向盘的操纵,一些工艺性较强的工种(如钳工)的操作,大体上是靠这类模型进行的。
通常说的某些领导者凭经验作决策也是如此,思维模型便于接受,也可以在一定条件下获得满意的结果,但是它往往带有模糊性、片面性、主观性、偶然性等缺点,难以对他的假设条件按进行验证,并且不便于人们的相互沟通。
如果采用符号模型,在一些约定或假设下借助于专门的符号、线条等,按一定形式组合起来描述原型,如机械原理图、电路图、受力分析图等,具有简明、方便、目的性强等非量化的特点。
根据机械产品的计算机辅助设计目标,研究将其中的非思维工作转化为计算机工作的问题。
在考虑计算机辅助设计因素在内时,机械产品的设计问题、设计问题的模型化(物理、力学、数学、几何等)、基本的机械零件、运动机构、机械产品转化为计算机设计的公式化、程序化方法均应在模型化时统一考虑。
机械产品的计算机辅助设计,可以是部分的、局部的、整体的、系统的软件化,可以是小型的、大型的,可以是单机的、多机的局域网、多机的internet等。
必须特别强调,在机械产品常规设计和软件化设计的时候,应该同时考虑两方面的问题,一是机械设计的思路与顺序,二是软件设计的思路与顺序。
二者结合获得的解决方案将最终反映在软件的交互界面和计算机的内部工作方式上。
必须特别强调,建立机械产品设计模型时,对产品设计主导者:
人的大脑思维过程的模型化表述。
从下图可以看到这种表述的作用,以及对机械产品设计软件化的贡献。
人获得机械产品设计参数的信息,通过分析、判断、选择等过程对信息进行处理,然后搜索大脑中存储的相关信息(设计理论、设计工具、机械零部件特性等),在通过书本、国家标准、参考资料、调研访问等搜索密切关联的信息,在经过处理加工,变换成与机械产品所使用的参数传回受信体。
3.振动磨虚拟设计方法与过程
虚拟设计在很大程度上与上述的计算机辅助设计(CAD)相一致。
在进行产品的可行性论证之后,首先要做的是将产品的虚拟模型呈现给大家,也就是常说的建模,即把所开发产品的零件、部件、产品整体用计算机建模软件建立虚拟模型,其目的主要是给人们以产品外观的印象,并为后续的虚拟分析做准备。
计算机建模工作流程一般为:
(1)在某一预先设置的平面内绘制零件大致外型(草图绘制),通过拉伸、旋转、切割、挖孔等方法生成零件的三维模型。
(2)将不同的零件在装配状态下,通过平移、旋转、固定等三维实体定位方法组装成不同功能的部件。
不同的零件、部件在装配程序中,再通过平移、旋转、固定等三维实体定位方法组装成不同功能的产品整体。
(3)将零部件及整机在实体投影模块中生成二维的工程图,或将部件、产品整体投影成二维的工程装配图、剖视图等。
建立实体模型是ADAMS设计流程的第一步。
首先要将整机分解并创建组成实体的各个几何零部件,然后在零部件(包括大地)之间添加约束,以获得和实际物理设备尽量吻合的有机关系,最后在部件上施加初始运动与初始载荷,完成动力学模型的建立。
因此说虚拟样机的建模是一个从整体到部分,又从部分到整体的过程。
模型与约束是关键,这是由拉格朗日方程的参数决定的。
4.1几何建模
在几何实体建模过程中,不需要将物理样机的每一个零部件都都模型化,而是使用合并、简化等方法根据研究的目的将物理样机理想化为少数个虚拟样机的零部件。
总的简化原则:
在不影响研究结果的前提下,零部件数目越少越好,越简单越好。
零件的几何模型可以通过两种途径来完成:
一是利用ADAMS/View本身提供的几何体建模工具,完成对其零件及整机的建模。
二是通过ADAMS/View的图形接口模块(ADAMS/Exchang)完成ADAMS与其他CAD/CAM/CAE软机之间数据的双向传输,从而可以在ADAMS中使用由其他专业的几何建模软件建立的几何模型,当然约束还是需要在ADAMS中添加。
通常对于结构较复杂的机械建模使用第二种方法,而机构相对简单的机械建模使用第一种方法。
ADAMS/View提供了三种几何体:
刚体、柔体和质点。
通常刚体具有质量和转动惯量,柔体具有节点和单元等信息,质点只具有质量。
刚体有6格自由度,质点只有3个方向的移动自由度。
在创建零部件模型时,先创建简单的几何实体,然后通过充分利用布尔运算,可以在简单几何实体的基础上生成复杂的几何实体。
1)整机几何模型总成
将各零部件装配连接为一个‘整体’,完成磨机的几何实体建模过程,如图5-23所示。
此时各部件之间并无任何约束关系,只是按照空间的装配关系将他们‘放’在各自的位置上,只有在各个部件之间添加了约束,才算是一个真正意义上的整体。
到此为止所建模型只涉及到机体,没有考虑机体的动力源,电机以及电机与轴之间的联轴器。
这是由于电机在物理样机中相对地面静止,不参与筒体的振动。
电机通过柔性联轴器将电机轴的旋转运动传于磨机的偏心块,由于联轴器除了传递扭矩外,几乎没有对磨机施加任何约束。
故为了简化建模的程序,将不在虚拟样机中表达电机及其与主轴的联轴器,这种简化不影响仿真结果。
4.2约束处理
前面所建模型还不能进行仿真运动,模型需要用约束将各个相互关联的部件联系起来的,也就是说需要添加约束。
而约束的添加与刚体动力学理论密切相关,主要有力约束、位移约束、运动约束等。
实际上就是对每一个零件对象施加该对象承受的所有形式的力、所有相互作用的位移与运动约束。
ADAMS建立动力学方程组时,需要有约束方程。
在实际的软件应用中,用户不需要自定义约束方程,ADAMS会根据用户添加的每一个约束,自动建立约束方程,完成方程组的建立。
ADAMS/View提供了3种类型的约束:
运动副约束;基本约束;运动约束。
在运动副约束中,ADAMS/View提供了多种基本运动副,用来表示具有相互作用的物理运动副,例如转动副和移动副等。
基本运动副经组合后可形成复杂运动副,例如齿轮副和关联副等。
ADAMS/View提供的基本约束包含:
平行约束;垂直约束;方向约束;点面约束;点线约束等。
运动约束定义零件运动随时间变化的函数。
ADAMS/View提供了两种类型的运动:
运动副运动:
定义运动副的移动或转动。
每一个运动副运动限制一个自由度。
只能对移动副、转动副或圆柱副添加运动副运动。
点运动:
定义两个零件的相对运动。
创建点运动时,需指定运动的方向。
点运动也可以添加到运动副上。
此外。
可以应用点运动在模型中创建复杂的运动。
本模型将主要应用运动副约束,集中列于表5.1中。
表5.1磨机运动副约束表
约束名
解释
约束名
解释
JOINT_1
左筒与前机架(固定副)
JOINT_10
左筒与后机架(固定副)
JOINT_4
右筒与前机架(固定副)
JOINT_12
偏心块与中轴(转动副)
JOINT_5
右筒与前机架(固定副)
JOINT_9
左筒与前机架(固定副)
JOINT_6
中轴与前机架(固定副)
JOINT_11
右筒与后机架(固定副)
JOINT_7
右筒与后机架(固定副)
JOINT_8
中轴与后机架(固定副)
模型将四组偏心块通过刚性连接(rigidjoint)连接成为一个整体,故只要用一个转动副就可以表达偏心块对整机的激励作用。
这不仅可以解决多组偏心块同步运转的问题,也便于仿真分析时对偏心块运动参数的参数化调整。
为了简化模型,凡是物理样机中由螺栓联机、焊接等固定连接的地方,均使用固定副。
对于固定副,它的定位参数(location)非常重要,合理选择固定副的位置,可以得到固定副位置处的受力特性,从而能够校核连接件或零部件的安全性。
本模型将固定副设置在物理样机的螺栓连接处,从此固定副的受力图可以校和