火车车轮锻造工艺分析详细版.docx
《火车车轮锻造工艺分析详细版.docx》由会员分享,可在线阅读,更多相关《火车车轮锻造工艺分析详细版.docx(5页珍藏版)》请在冰豆网上搜索。
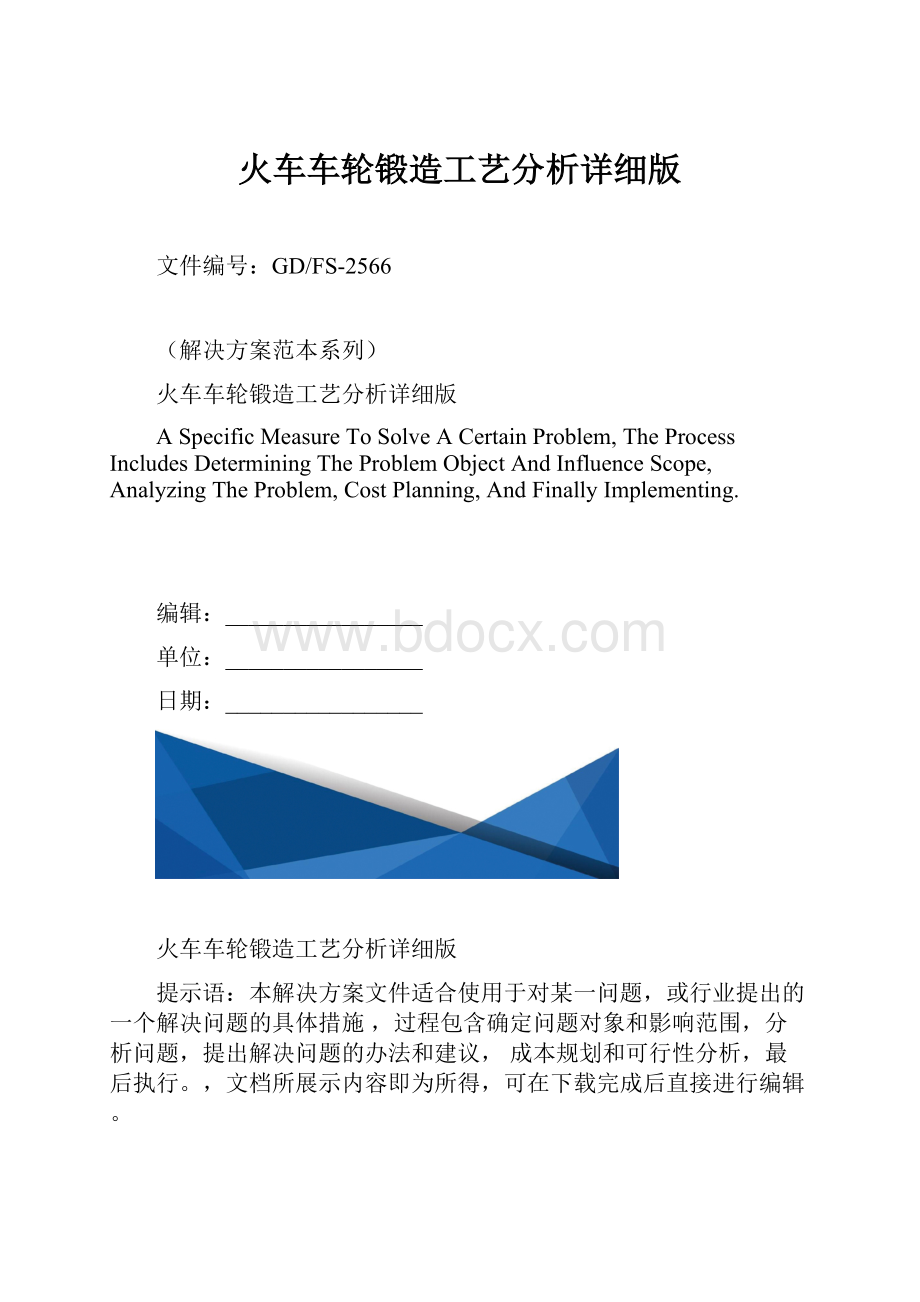
火车车轮锻造工艺分析详细版
文件编号:
GD/FS-2566
(解决方案范本系列)
火车车轮锻造工艺分析详细版
ASpecificMeasureToSolveACertainProblem,TheProcessIncludesDeterminingTheProblemObjectAndInfluenceScope,AnalyzingTheProblem,CostPlanning,AndFinallyImplementing.
编辑:
_________________
单位:
_________________
日期:
_________________
火车车轮锻造工艺分析详细版
提示语:
本解决方案文件适合使用于对某一问题,或行业提出的一个解决问题的具体措施,过程包含确定问题对象和影响范围,分析问题,提出解决问题的办法和建议,成本规划和可行性分析,最后执行。
,文档所展示内容即为所得,可在下载完成后直接进行编辑。
铁路交通是我国运输系统的重要组成部分,在国民经济和社会发展过程中,铁路运输扮演着不可替代的重要角色。
我国一直以来都十分重视铁路运输的发展。
最近几年以来,随着以高铁为代表的新型铁路运输技术的应用,我国铁路运输朝着高速、重载方向发展,车轮在复杂的运行工况和恶劣的工作条件下,受到来自于速度效应和制动方式的双重影响,对其耐磨性、强韧性以及抗疲劳性提出了更高的要求。
但是我国现有的车轮锻压生产技术,还不能完全满足铁路运输发展对火车车轮质量的要求。
尤其是我国高速列车的车轮,在车轮的制造中,还存在废品率较高的现象。
因此,笔者认为,研究火车车轮锻压生产工艺,提高我国火车车轮锻压生产技术水平,制造优质火车车轮,对于降低我国火车整车生产成本,促进铁路运输的发展,有十分重要的现实意义。
1.火车车轮概述。
1.1.我国火车车轮形制特征简析
火车车轮是火车整车零件中的一个关键组成部分,是火车机车生产中技术较高的环节之一。
由于火车的种类繁多,工作环境和机车构造也不尽相同,所以火车车轮的结构形式和形制特征也多种多样。
一般由轮毂、轮辋、辐板三个部分组成。
火车车轮属于典型的金属塑性成形产品,常常会出现多种内部和外部缺陷。
比较常见的有偏心缺陷、组织和填充不完全等缺陷。
所以车轮生产中对锻压技术要求较高。
1.2.我国现行车轮生产工艺。
当前包括我国在内的世界各国普遍采用模锻——轧制法(又称整体辗钢车轮生产法)进行火车车轮锻造生产,这一方法主要采用模锻和轧制扩径两个主要步骤来完成车轮主体的成形。
和铸造法相比较,该法所生产的车轮内在质量要好很多,与全模锻制造法相比,该法的优点在于对模锻设备的要求较低。
全世界有20多个生产厂家,虽然各自的生产工艺有其独有特点,但是总体来说从流程来讲可以分为三个主要步骤:
预成型及成型、轧制扩径和压弯冲孔。
通过初步总结,笔者认为,各厂家在工艺上的差别,主要体现在预成型及成型的差异上,压弯压力机的配置方面则基本相同,冲孔设备的配置也只是稍有差别。
2.火车车轮锻造工艺分析。
2.1.车轮预成型工艺。
车轮坯料采用圆柱形钢坯下注,坯料直径介于380mm——406mm之间。
使用高速锯床对钢坯进行锯切成段,成段坯料经加热后,有机械手夹持上料到压力机进行预成型工序。
在预成型工序中,上磨具采用成型模,下模具则选用中央突起的压痕模,以此实现对轮辋、轮毂的金属体积分配。
在压力机模锻工序采用的是静压力锻造,整个锻造过程在一次行程中完成。
优异的车轮预成型工艺,不但能够保证车轮初步形状的成形,同时还可以起到改善车轮内部组织结构和金属流线的双重作用。
但是如果此阶段的工艺不合理,则会直接导致车轮偏心、填充不完全等缺陷。
给后续加工阶段操作带来困难,严重的还会直接导致车轮报废。
2.2.车轮成型工艺。
在车轮的成型阶段,主要得到的是轮毂和压制辐板的形状,同时完成轮辋主要部位的成形。
其过程属于典型的开式无飞边模锻。
模具压下后,首先受压的是车轮的辐板处,车轮内层金属受到来自中央冲头的作用力,带动外侧金属沿水平方向流动。
随着下压量的急剧增大,轮坯的最外侧金属和成形模的内壁接触。
在中央冲头和成形模内壁的共同作用下,轮坯内的金属形成一个分流面,分别流向轮毂和轮辋下侧以及轮辋上侧。
在该流程中,轮辋下侧的填充情况最佳。
此外,由于该工序中模具模膛的高度有所不同,所以直接导致轮坯中不同部分的金属变形量不一样,其中辐板处变形量最为突出,而轮辋部分的变形量则最小。
车轮成形工艺是热成形机组轧压能力匹配的关键工艺。
合理科学的成形工艺,不仅要保证压力机的压力极限数值满足事先设定的工艺数值,同时还要满足下道工序中轧机的轧制能力需求。
2.3.车轮压弯工艺。
车轮压弯工序一般情况下是和冲孔工序一起在同一台压力机上进行,是火车车轮热成形中的最后一道工序。
其主要目的是对辐板进行压弯成形、对轮辋表面进行平整以及确定车轮两侧和车轮内径等的成形。
2.4.轮坯各个部位加工余量的确定。
车轮加工中的锻造余量,是整个车轮锻造工艺设计中非常重要的环节。
它与车轮材料的利用率、成品率以及生产率密切相关,直接决定着车轮生产的成本。
因此,要合理确定轮坯合理的锻造余量。
踏面余量的确定。
在确定轮坯踏面余量时,轮坯的椭圆度和热处理过程中直径0.1—0.2%的变化量应该予以充分考虑。
但是,主要还是要注意踏面上表面氧化皮压入、裂纹以及结疤等的消除。
经过实践中的反复摸索,笔者认为,踏面锻造余量的确定取8mm较为合适。
轮毂外径余量确定。
轮毂外径余量的确定,主要取决于设备对轮毂、轮辋偏心的精度控制。
目前,山西某重型机械集团公司在这一精度控制上可以达到6mm以内。
为了确保最大偏心后,轮毂能有3mm的加工余量,初期生产中,应该把轮毂余量确定为9mm。
实践证明,在设备正常情况下的批量生产中,轮毂外径余量取7mm比较适宜。
轮毂、轮辋端面的余量确定。
这两项余量的确定主要取决于端面氧化皮压入、端面的不平整状况以及预成形时轮毂端面尖角部位填充不完全所造成的轮毂端部圆角三个因素。
在模具首次设计中,这一余量一般取7mm和6mm。
为了降低成本,曾经试图降低这两种余量,结果造成轮毂端面尖角部位加工不起来。
所以,最终仍然将轮毂、轮辋的单边余量设定至7mm和6mm的初期水平。
辐板和轮辋内径加工余量的确定。
由于在淬火和冷却处理过程中辐板会出现变形,因此辐板加工余量的确定,不仅要考虑氧化皮压入、表面裂纹等缺陷的去除,还要格外重视辐板变形的影响。
经生产企业长期批量生产经验的积累,辐板单边余量确定为6mm最为适合。
轮辋内径也取相同尺寸为宜。
淬火下沉量的确定。
车轮淬火后,轮辋的增大量叫做淬火下沉量。
压弯模设计时,应该确保车轮压弯成形以后,毂辋距减小一个淬火下沉量,以确保淬火后的毂辋距符合要求尺寸。
淬火下沉量的确定,和火车轮的型号有关。
据苏联资料介绍,915车轮淬火下沉量为3—5mm。
安徽某钢厂在915车轮模具设计时,淬火下沉量取6mm。
2.5.车轮锻造过程中的数值模拟分析。
由于火车车轮的锻造工序繁多,各环节中对轮坯不同部分的数据误差要求较高,且由于涉及到材料金属物理化学性质的变更,因此对锻造过程中的数据控制和数值模拟要求较高,所以对于锻造工作的每个环节而言,建立数值模拟分析是十分必要的。
目前在数值分析方面,主要采取的是有限元数值分析法,这是一种将连续体根据实际需要,分化为若干个大小有限的单元个体集合,以方便分析连续体力学问题相关数据的方法。
这一方法应用在车轮锻造生产过程中,可以精确求解轮坯变形时内部速度场、应力场以及应变场等的变量,从而为车轮锻造各道工序,提供了科学的理论依据。
在目前我国火车车轮生产中,基于有限元理论和相关软件支持,已经普遍建立起了火车轮预成形和成形工步数值模拟分析模型、压弯过程数值模拟分析模型、冲孔过程数值模拟分析模型等一系列环节的模拟分析模型。
使得工作人员能够及时掌握各阶段数值的变化,以及由此带来的对成品质量的影响,实时调整参数设置,确保车轮最终质量得以实现。
2.6.当前火车车轮锻造工艺存在的问题。
随着对火车车轮数量要求的增加和质量要求的提高,我国火车车轮锻造工艺的缺陷也显露出来。
目前主要问题在于各工步,尤其是在车轮预成形和压弯工步,对金属变形量的分配以及模具结构和尺寸的设计等诸多问题,有待进一步研究和改进。
这些问题的存在不仅使得车轮锻造工序和模具设计的周期更长、对模具和车轮的调试以及模具维修的过程趋于复杂,而且还会导致车轮辐板出现裂纹、车轮成形形状和尺寸满足不了设计要求等一系列质量问题,使得当前的火车车轮生产,从数量到质量都与实际需要存在相当差距。
火车车轮的锻造,是一个从材料选择、模具设计制造、到前期预成形、成形、再到后期压弯和冲孔的连续性工序系统。
由于金属在各工艺阶段会发生相应的物理和化学变化,因此常常会出现诸如填充不充分和偏心等缺陷,导致产品质量不能达到预期要求,严重者产生废品。
从加工流程优化、数值模拟分析等方面加以完善,是弥补当前车轮锻造工艺相关环节缺陷,保证车轮最终质量的有效途径。
以有限元理论为基础的数值模拟分析模型,是目前实现锻造过程数值模拟分析的可靠途径,是实现对锻造过程中相关数值精确控制的有效手段。
笔者认为,我国火车车轮锻造工艺的改进,除了要注重生产设备和新型工艺的开发外,对以有限元理论为依托的计算机软件辅助分析系统的开发运用也应该予以重视,将其纳入工艺改进的重要组成部分。
可在这里输入个人/品牌名/地点
Personal/BrandName/LocationCanBeEnteredHere