培养基模拟灌装试验方案.docx
《培养基模拟灌装试验方案.docx》由会员分享,可在线阅读,更多相关《培养基模拟灌装试验方案.docx(22页珍藏版)》请在冰豆网上搜索。
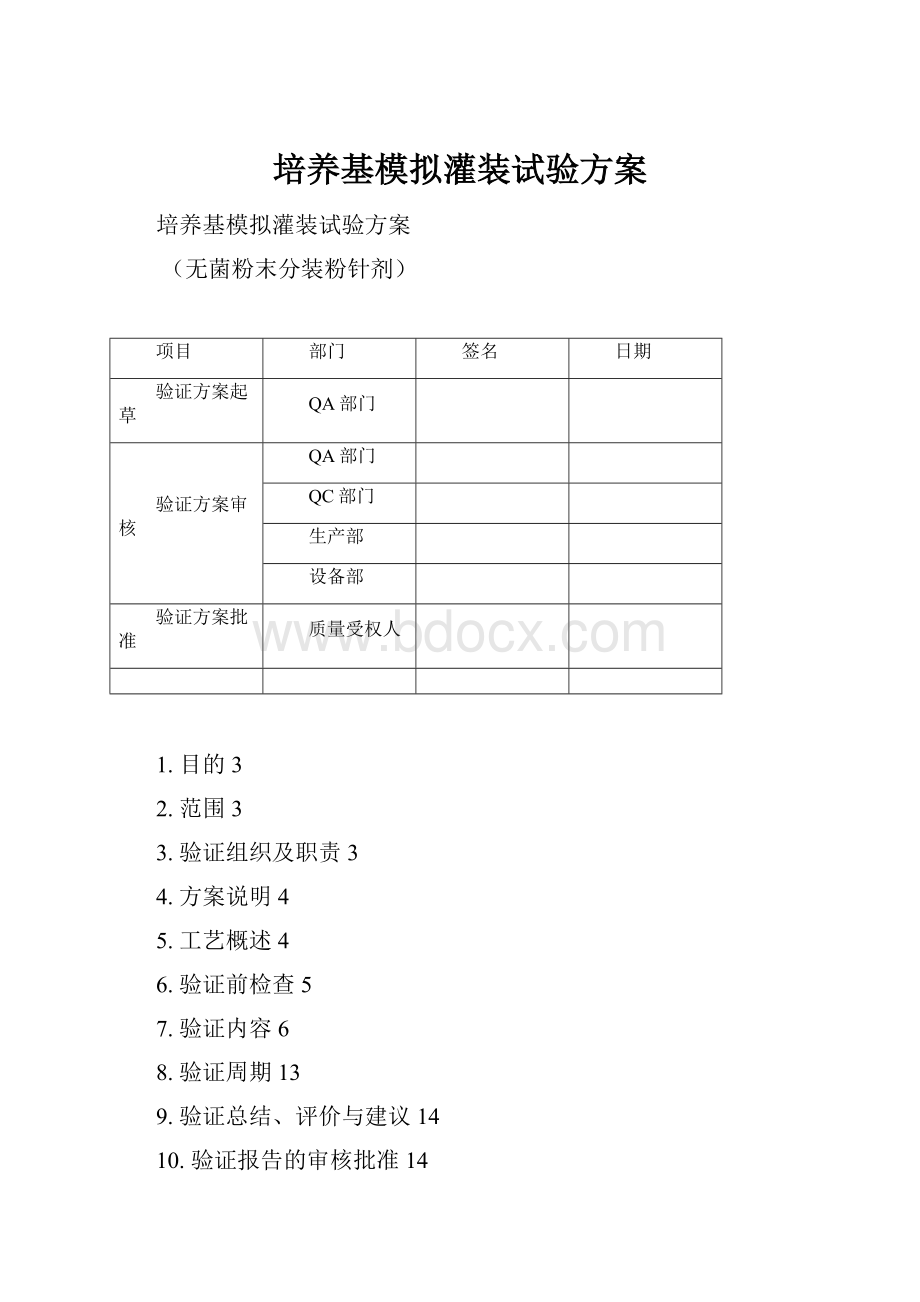
培养基模拟灌装试验方案
培养基模拟灌装试验方案
(无菌粉末分装粉针剂)
项目
部门
签名
日期
验证方案起草
QA部门
验证方案审核
QA部门
QC部门
生产部
设备部
验证方案批准
质量受权人
1.目的3
2.范围3
3.验证组织及职责3
4.方案说明4
5.工艺概述4
6.验证前检查5
7.验证内容6
8.验证周期13
9.验证总结、评价与建议14
10.验证报告的审核批准14
11.验证合格证14
1.目的
对于无菌生产来说,即使所有与产品无菌性有关的设备部件、容器以及原料都经过有效地灭菌处理,但当这些生产要素在实际工艺条件下组合在一起时,仍有可能因各种原因导致产品被污染。
对于非最终灭菌的无菌生产工艺必须进行培养基灌装来验证。
培养基灌装是用于评估整个无菌工艺过程,用于表明如果严格按照工艺要求生产,产品的无菌性有可靠保证。
2.范围
本验证方案适用于无菌粉末分装粉针剂生产线的培养基模拟灌装试验。
3.验证组织及职责
3.1验证职责
项目
部门
QA部门
1.起草验证方案和验证报告,监控验证过程并做出评价
2.审核验证方案和验证报告,协调培养基模拟灌装试验的实施
3.正常工艺条件监控
4.培训培养基模拟灌装试验方案
QC部门
1.培养基无菌性试验
2.培养基灵敏度试验
3.乳糖无菌检查
4.模拟分装后培养基的观察
设备部
1.保证公用系统的正常运行
2.配备液体灌装机
3.检查确认验证相关设备的校验情况
生产部
1.制定验证进度计划表
2.采购验证所需物料
3.组织车间员工按正常生产条件进行培养基模拟灌装试验
培训中心
1.确认人员体检情况
2.确认人员培训情况
3.2验证方案的培训
验证实施前,QA部门对验证相关人员培训,填写《员工培训记录表》。
4.方案说明
4.1验证过程中偏差处理的要求
执行《偏差管理规程》
4.2验证过程中变更的要求
执行《变更管理规程》
4.3验证过程中记录填写的要求
执行《记录管理规程》
4.4其他要求
5.工艺概述
5.1产品:
5.1.1性状:
白色结晶或结晶性粉末。
5.1.2规格:
0.25g/瓶。
5.1.3包装:
10ml西林瓶。
5.1.4批量:
24000瓶。
5.2胶塞处理:
纯化水清洗、硅化、注射用水清洗、灭菌。
(121℃,20分钟)
5.3西林瓶处理:
纯化水清洗、注射用水清洗、压缩空气吹干、隧道烘箱灭菌。
(灭菌段温度320℃≥5分钟,冷却温度﹤40℃)
5.4铝盖干热灭菌。
(180℃,120分钟)
5.5无菌药粉通过分装机充填到西林瓶中,盖胶塞、轧铝盖、灯检、贴签、包装。
5.6工艺流程图如下:
6.验证前检查
6.1人员的确认
确认参与验证人员均接受过微生物知识、更无菌衣、无菌操作、培养基模拟灌装试验方案的培训,同时确认参与验证人员的健康体检情况,详见附件1《员工体检和培训确认表》。
6.2验证所需文件的确认
确认验证所需文件已经批准,文件编号正确,文件是现行版本。
详见附件2《验证所需文件确认记录》
6.3仪器仪表校验的确认
确认验证过程中使用的仪器仪表在校验效期内。
详见附件3《仪器仪表校验确认记录》
6.4模拟灌装试验前需要完成验证的确认
确认已经完成设施、设备的确认和验证工作,详见附件4《试验前需要完成验证的确认记录》
7.验证内容
7.1验证项目
7.1.1验证项目名称:
培养基模拟灌装
7.1.2法规要求:
《药品生产质量管理规范(2010年修订)》附录1无菌药品
第四十七条无菌生产工艺的验证应当包括培养基模拟灌装试验。
应当根据产品的剂型、培养基的选择性、澄清度、浓度和灭菌的适用性选择培养基。
应当尽可能模拟常规的无菌生产工艺,包括所有对无菌结果有影响的关键操作,及生产中可能出现的各种干预和最差条件。
培养基模拟灌装试验的首次验证,每班次应当连续进行3次合格试验。
空气净化系统、设备、生产工艺及人员重大变更后,应当重复进行培养基模拟灌装试验。
培养基模拟灌装试验通常应当按照生产工艺每班次半年进行1次,每次至少一批。
培养基灌装容器的数量应当足以保证评价的有效性。
批量较小的产品,培养基灌装的数量应当至少等于产品的批量。
培养基模拟灌装试验的目标是零污染,应当遵循以下要求:
(一)灌装数量少于5000支时,不得检出污染品。
(二)灌装数量在5000至10000支时:
1.有1支污染,需调查,可考虑重复试验;
2.有2支污染,需调查后,进行再验证。
(三)灌装数量超过10000支时:
1.有1支污染,需调查;
2.有2支污染,需调查后,进行再验证。
(四)发生任何微生物污染时,均应当进行调查。
7.1.3模拟灌装试验的准备
7.1.3.1生产部编制《培养基模拟灌装试验进度计划表》,详见附件5。
(如果验证主计划中规定了详细的进度计划,那么可以不编制该表)
7.1.3.2模拟灌装试验批量和时间的确定
(1)理论批量为10,000瓶,灌装批量为11,000瓶,剔除轧盖缺陷瓶后能确保培养量大于10,000瓶。
(2)批量确定的依据:
理论生产批量为24,000瓶,模拟灌装10,000瓶,具有足够的代表性。
(3)模拟灌装时间设计为为6小时。
(4)时间设计的依据:
生产中无菌原料药3kg/桶,每批分装两桶,即6kg。
产品规格0.25g/瓶,故理论产量是6000g/0.25g=24000(瓶)。
分装速度是100瓶/分钟,约4小时分装完毕。
模拟6小时,能够达到最差的时间条件。
7.1.3.3模拟灌装用培养基和空白物料的选择与处理
(1)培养基选择:
所用培养基能够支持微生物生长的菌谱范围要宽,应能促进革兰氏阳性菌、革兰氏阴性菌、酵母菌、霉菌的生长。
(2)本实验选择大豆胰蛋白胨液体培养基,将培养基进行配制和灭菌,用于无菌灌装。
取大豆胰蛋白胨g,加入ml大烧杯内,加入xxxml,使溶解,搅拌均匀后,分装于x个ml三角瓶中,加塞盖严后121℃,15min灭菌即得。
(3)培养基无菌性检查和灵敏度检查与培养基模拟灌装试验同步进行,具体操作依据《中国药典附录XIH无菌检查法》和相关SOP执行,做好记录,以附件形式附在验证报告中。
(4)空白粉末选择的原则:
空白粉末应可以在干粉状态下灭菌,灭菌后其无菌性可以达到药典标准,无抑菌性,可以溶解于液体培养基并不会对目视检查产生影响,适用于分装工艺,选择物理性质与产品相似的空白粉末。
一般可以选择乳糖、甘露醇、聚乙二醇6000或氯化钠。
(5)由于本公司产品密度在0.4至0.6g/cm3,而乳糖的密度最接近产品(详见下表),故选择乳糖作为空白粉末。
名称
松密度(g/cm3)
乳糖
0.53
甘露醇
0.43
聚乙二醇6000
1.08
氯化钠
2.16
备注:
松密度数据来源《HandbookofPharmaceuticalExcipients(Sixthedition)》
(6)乳糖灭菌和检验:
依据无菌检查取样的3倍量取g乳糖装入样品袋,再将剩余乳糖kg分装到两个塑料袋中,均塑封严密。
其中一袋与样品袋共装一个铝桶,另一袋装入一个铝桶中,再用钴60辐射灭菌这两桶物料,辐射剂量25kGy。
对样品袋中乳糖做无菌检查,检查合格后乳糖放行使用。
(装塑料袋再装铝桶或直接装铝桶都可以,但要与实际购买物料的包装形式一致。
)
7.1.4培养基模拟灌装试验步骤和操作
7.1.4.1依据《粉针车间洁净室清洁消毒管理规程》对生产环境进行清洁和消毒。
7.1.4.2正式生产人员控制为5人,本次模拟灌装试验人员控制为8人,以模拟最差条件。
7.1.4.3依据《XX产品工艺规程》对胶塞、西林瓶、铝盖处理;对无菌乳糖进行模拟取样。
分别做好相应的批生产记录和取样记录。
7.1.4.4依据《无菌分装岗位SOP》的要求,将干热灭菌后分装机的可拆卸部件组装。
7.1.4.5操作步骤
(1)粉末分装设备前加一个灭菌合格的液体灌装器(详见7.1.8.4),调整速度使其与分装机速度协调一致。
(2)将灭菌后的培养基在A级条件下加入到液体灌装器。
(3)开启液体灌装器和螺杆分装机,每一西林瓶先灌4ml的液体培养基,再分装乳糖0.25g。
(4)低速分装运行30分钟(90瓶/分钟),停止灌装130分钟;正常速度运行50分钟(100瓶/分钟),停止灌装130分钟;再高速运行30分钟(110瓶/分钟)。
(5)停止灌装期间只传输西林瓶,不灌装液体培养基、不分装乳糖、也不盖胶塞,旨在模拟西林瓶传输中可能出现的倒瓶、挤瓶现象和需要人员干预的状况。
(6)运行时间加上停止灌装时间,总的培养基模拟灌装试验时间是370分钟,约6小时,共灌装11,000瓶,足以保证10,000瓶的要求。
7.1.4.6环境检测:
试验期间依据《粉针车间空气净化系统日常监测管理规程》对生产环境的尘埃粒子进行在线监测,对浮游菌和沉降菌进行动态检测,监测记录以附件形式附在验证报告后面。
7.1.4.7视频录像:
试验期间全程拍摄监控录像,以帮助判断整个人员操作和无菌工艺的风险,有利于事后调查和原因查找,有利于下一次做培养基模拟灌装试验前对员工进行培训。
7.1.4.8模拟灌装过程中的干扰设计
(1)倒瓶、扶瓶:
由于西林瓶总运行时间是6小时,大于正式生产时的4小时,所以倒瓶、扶瓶的概率大于正常生产情况,不增加干扰设计。
(2)人工压塞、人工加塞:
实际盖塞分装时间是110分钟,小于正常生产时的240分钟,模拟灌装时人工压塞、人工加塞的频率小于实际生产,故需要增加人工压塞、人工加塞的干扰设计,从盖塞时间上换算,应增加两倍次数的模拟操作,第一批试验时统计人工压塞和人工加塞的数量A,第二批和第三批试验时模拟人工压塞和人工加塞的动作(A+2*A)次。
(3)过程控制取样:
正常生产情况下是每隔20分钟取样两支样品抽检装量,试验期间模拟取样动作后将样品放回传送带。
(4)物料换桶:
正常生产情况下是分装两桶原料药,所以将乳糖分成两份,分别装在两个铝桶中,模拟一次换桶操作。
(5)人员进出:
正常生产情况下,分装间内有一个辅助人员,做换桶、补塞操作。
其他主操作人员如果有事离开分装间,这个辅助人员临时替岗,故要在试验期间模拟人员进出,试验期间有8个人在洁净区,要求这8个人轮换操作,每人做一次人员进出模拟。
7.1.4.9轧盖间也可适当增加1-2名操作人员或辅助人员。
7.1.4.10装托盘人员将准备好的标签贴在西林瓶上,将每个西林瓶上下翻转后装入托盘,保证培养基可以完全接触到胶塞和西林瓶内壁。
标签编号原则详见7.2验证样品编号原则。
7.1.4.11容器密封完整性测试:
QA人员每个托盘取一瓶样品做容器密封完整性测试,具体操作详见7.1.9。
7.1.4.12培养基灌装后应立即对生产设施和设备清洗、消毒和灭菌,避免残留培养基造成污染,执行《粉针车间洁净室清洁消毒管理规程》。
7.1.4.13每批灌装结束,清洁前应对人员进行五指手套和无菌服的取样检测,清场结束,人员退出后,应进行悬浮粒子监测,最后一个离开分装间的人员打开尘埃粒子计数器,设定每五分钟自动测试和打印一次(5分钟、10分钟、15分钟、20分钟、25分钟),30分钟以后再次进入分装间并关闭尘埃粒子计数器,查看打印数据,以确认净化系统的自净时间。
检测记录作为报告附件。
7.1.5培养及观察:
所有分装后的样品在20℃至25℃培养7天,再在30℃至35℃继续培养7天。
QC专人每天每支观察一次,做好记录,附在验证报告中。
7.1.6培养基模拟灌装流程图:
7.1.7设计思路:
7.1.7.1尽可能的模拟实际生产工艺,并能充分代表实际生产操作的环境条件。
7.1.7.2包含实际生产中可能出现的污染风险因素,如停机、换班、设备维修等。
7.1.7.3工艺条件的选择应选取合理的最差条件,用最差条件对工艺流程、设备和整个体系进行挑战,如物料在无菌条件下保存到被允许的最长时间,生产现场人员最多,生产活动频率最高,生产线最长允许运行时间。
7.1.8试验说明及特殊要求
7.1.8.1容器规格选择:
有些情况下同一生产线可能用于不同大小容器的灌装。
一般来说培养基灌装可以针对规格最大和最小的容器进行,首次验证时可以进行两次最大规格容器和一次最小规格容器的灌装挑战,在以后的周期性半年度培养基灌装试验时可以轮换,每次挑战一个规格。
本条生产线只分装一个规格的西林瓶,即10ml西林瓶。
7.1.8.2抑菌影响因素分析:
7.1.8.2.1抑菌因素应当在培养基灌装时予以考虑,从而避免污染微生物在模拟过程中被杀死造成假阴性的结果。
7.1.8.2.2消毒剂会杀灭微生物,对设备的清洗、消毒、和灭菌在灌装前后进行,喷洒消毒酒精的操作不能超出正常生产时的使用频率,不能将消毒剂直接接触到培养基上。
7.1.8.3培养基加入方式讨论:
7.1.8.3.1方式一:
使用无菌粉末分装设备来灌装液体培养基,有些粉末分装设备有液体灌装功能,当使用这一功能灌装时,液体培养基可以和空白粉末一起注入加料斗。
7.1.8.3.2方式二:
在粉末分装设备前加一个液体灌装器,将灭菌后的培养基加入到液体灌装器,先灌4ml的液体培养基到西林瓶中,再分装乳糖。
7.1.8.3.3方式三:
在粉末分装设备后加一个液体灌装器,这种方式是在粉末分装设备前没有足够空间增加液体灌装器时采用。
7.1.8.3.4三种培养基加入方式优缺点比较见下表:
培养基加入方式
优点
缺点
方式一:
使用无菌粉末分装设备来灌装液体培养基
一步灌装、简化操作、减少污染、不需要额外设备
加料方式与正常工艺有差别
方式二:
在粉末分装设备前加一个液体灌装器
培养基灌装时不需要离线操作,对容器无需更多处理
需要增加液体灌装器
方式三:
在粉末分装设备后加一个液体灌装器
培养基灌装时不需要离线操作,对容器无需更多处理
需要增加液体灌装器,在灌液体时粉末可能被溅出
综上,因为该条生产线的分装机是螺杆分装机,不适用于液体分装,且方式三可能引起粉末溅出,所以选择方式二的培养基加入方式,即在粉末分装设备前加一个液体灌装机。
7.1.8.4液体灌装器:
将双头自吸液体灌装机放在隧道烘箱出瓶与分装之间传送轨道旁的合适位置,调整两个灌装头的位置在西林瓶传送带正上方与西林瓶口垂直,两个灌装头分别对准两个相邻西林瓶的瓶口,调整液体培养基的灌装速度,使其与螺杆分装机分装速度协调一致。
不同的液体灌装器有不同的安装方式,选择液体灌装器时应考虑灌装速度、操作空间等因素。
7.1.8.5惰性气体保护:
由于粉针生产中不适用惰性气体保护,所以模拟分装时也不使用惰性气体保护。
7.1.8.6灌装批量:
无菌原料药3kg/桶,每批分装两桶,即6kg。
产品规格0.25g/瓶,6000g/0.25g=24000(瓶),故理论产量是24000瓶。
分装速度的范围是90-110瓶/分钟,正常分装速度是100瓶/分钟,4小时分装完毕。
由于低速运行可以评估无菌产品、容器、胶塞在无菌区暴露导致污染的风险,高速运行可以用来评估手工操作的干扰,所以设置低速、正常速度、高速三个试验条件,低速运行30分钟,90*30=2700(瓶),正常速度运行50分钟,100*40=4000(瓶),高速运行30分钟,110*30=3300(瓶),合计11,000瓶,11,000瓶的模拟批量包含常规操作和干扰操作,人员配备、灌装时间均满足要求,所以11,000瓶的模拟批量足以保证评价的有效性。
7.1.8.7灌装时间:
尽管最准确的方法是模拟全批量的操作时间,也有其他合理并适当的模式,应综合考虑生产操作、各种干扰、生产速度后,决定培养基灌装的时间,当无菌工艺采用人工灌装(或密封)或人工操作的工作量很大时,模拟试验的时间一般不应少于实际生产操作时间,以更好地反映人员所致污染的风险。
本次试验结合
7.1.8.7确定灌装时间是30+30+50=110(分钟),低速、正常速度、高速三个步骤之间分别间隔130分钟,间隔期间只传输西林瓶,不灌装液体培养基、不分装乳糖、也不盖胶塞。
运行时间加上间隔时间,总的培养基模拟灌装试验时间是370分钟,约6小时。
7.1.8.8整个培养基灌装过程中要严格控制丢弃已灌装的培养基,避免将一些潜在污染的可能性也同时丢弃,任何丢弃都要有充分的理由,并做好相应的记录并合理解释。
只有确定因操作不当而导致培养基密封性缺陷的,且有明确的书面规程可以进行剔除缺陷的产品才可以丢弃。
7.1.9容器密封完整性测试:
无菌容器的完整性测试可以在培养基灌装时进行,可以采用微生物侵入试验来评价系统的密封完整性。
每个托盘取一瓶样品做容器密封完整性测试,每个托盘大约200瓶,11000/200=55(瓶),取其中4瓶接种10-100CFU的运动性菌悬液,如大肠埃希菌、铜绿假单胞菌或黏质沙雷菌,两瓶正置两瓶倒置培养做阳性对照,将其余挑战瓶倒置于菌悬液(浓度不低于106CFU)中,浸没时间不小于4小时,结束后将外表面擦拭干净,将每瓶容器来回翻转,确保容器内表面和胶塞内表面跟培养基完全接触,然后在阳性对照相同条件下培养7天目视检查,如果阳性对照生长良好而挑战瓶无生长,表明容器的完整性测试通过。
7.1.10接受标准
项目
接受标准
培养基无菌性检查
每批培养基随机取不少于5支(瓶),培养14天,应无菌生长。
培养基灵敏度检查
空白对照管应无菌生长,加菌的培养基管均生长良好。
灌装样品无菌检查
1.阴性对照,在14天内,无任何微生物生长,显示阴性。
2.阳性对照,在7天内,所有接种瓶的培养基里都出现繁殖现象,显示阳性。
3.灌装的样品,有1支污染,需调查,可考虑重复试验;有2支污染,需调查后,进行再验证。
7.1.11检查结果
7.1.11.1发现污染后的处理:
发现任何污染样品均应进行调查。
调查从人、机、料、法环各个方面进行调查。
分离到的污染微生物至少要鉴定到属,有条件的话可以鉴定到种以帮助确定来源,查明原因后制定纠偏措施。
7.2验证样品编号原则
样品编号采用“批号+托盘序列号+瓶号”的形式,例如20121220-1-00009。
7.3记录索引(请企业自行整理齐全)
8.验证周期
8.1培养基模拟灌装试验的首次验证,每班次应当连续进行3次合格试验。
8.2培养基模拟灌装试验通常应当按照生产工艺每班次半年进行1次,每次至少一批。
8.3空气净化系统、设备、生产工艺及人员重大变更后,应当重复进行培养基模拟灌装试验。
8.4当发生偏差时,可以用培养基灌装来评估已生产批次的风险。
但需要注意,即使为了评估偏差情况而设计的培养基灌装结果符合要求,也不能因此将偏差或引起偏差的行为看作正常操作,即如果操作会带来风险,培养基灌装的结果并不能用来证明这些操作可以作为常规操作规程来实施。
9.验证总结、评价与建议
10.验证报告的审核批准
11.验证合格证
附件1
员工体检和培训确认表
人员
体检情况
培训情况
确认标准:
1.接受过微生物知识、更无菌衣、无菌操作、培养基模拟灌装试验方案的培训。
2.本年度接受过员工健康体检。
(符合标准在空格内划“√”)
备注:
签名
日期
QA复核
日期
附件2
验证所需文件确认记录
文件编号
文件名称
存放地点
确认
ZX-SMPXX-XXX-XX
洁净区管理规程
粉针车间
ZX-SMPXX-XXX-XX
XX产品工艺规程
粉针车间
ZX-SMPXX-XXX-XX
紫外灯、紫外传递橱和紫外灯封锁区管理规程
粉针车间
ZX-SMPXX-XXX-XX
洁净服清洗、灭菌、使用管理规程
粉针车间
ZX-SMPXX-XXX-XX
洁净室清洁消毒管理规程
粉针车间
ZX-SMPXX-XXX-XX
生产过程质量控制管理规程
粉针车间
ZX-SMPXX-XXX-XX
空气净化系统日常监测管理规程
粉针车间
ZX-SOPXX-XXX-XX
洗烘瓶岗位标准操作规程
粉针车间
ZX-SOPXX-XXX-XX
胶塞清洗灭菌岗位标准操作规程
粉针车间
ZX-SOPXX-XXX-XX
分装岗位标准操作规程
粉针车间
ZX-SOPXX-XXX-XX
轧盖岗位标准操作规程
粉针车间
ZX-SOPXX-XXX-XX
洁净室(区)沉降菌测定标准操作规程
QC微生物岗
ZX-SOPXX-XXX-XX
洁净室(区)浮游菌测定标准操作规程
QC微生物岗
ZX-SOPXX-XXX-XX
生化培养箱使用标准操作规程
QC微生物岗
ZX-SOPXX-XXX-XX
湿热灭菌标准操作规程
粉针车间
ZX-SOPXX-XXX-XX
消毒剂的配制使用标准操作规程
粉针车间
ZX-SOPXX-XXX-XX
螺杆分装机清洁标准操作规程
粉针车间
ZX-SOPXX-XXX-XX
培养基、缓冲液、稀释液、配制操作规程
QC微生物岗
ZX-SOPXX-XXX-XX
菌种制备、保藏操作规程
QC微生物岗
ZX-SOPXX-XXX-XX
无菌检查法操作规程
QC微生物岗
ZX-SOPXX-XXX-XX
无菌隔离系统使用操作规程
QC微生物岗
确认标准:
1.文件已经批准。
2.文件编号正确。
3文件是现行版本。
(符合标准在空格内划“√”)
备注:
签名
日期
QA复核
日期
附件3
仪器仪表校验确认记录
名称
编号
上次校验时间
是否在有效期内
备注
签名
日期
QA复核
日期
附件4
试验前需要完成验证的确认记录
名称
验证报告编号
确认
空调系统确认报告
纯化水系统确认报告
注射用水系统确认报告
压缩空气系统确认报告
洗瓶机确认报告
隧道烘箱确认报告
多功能胶塞清洗机确认报告
螺杆分装机确认报告
湿热灭菌柜确认报告
干热灭菌柜确认报告
轧盖机确认报告
培养箱(培养室)确认或校验报告
确认标准:
1确认报告已经批准。
2确认报告在验证效期内。
(符合标准在空格内划“√”)
备注
签名
日期
QA复核
日期
附件5
培养基模拟灌装试验进度计划表
物料
采购时间
检验时间
放行时间
乳糖
培养基
西林瓶
胶塞
铝盖
生产部签字
日期
质量部签字
日期
批次
批号
生产日期
备注