小容量注射剂工艺规程.docx
《小容量注射剂工艺规程.docx》由会员分享,可在线阅读,更多相关《小容量注射剂工艺规程.docx(71页珍藏版)》请在冰豆网上搜索。
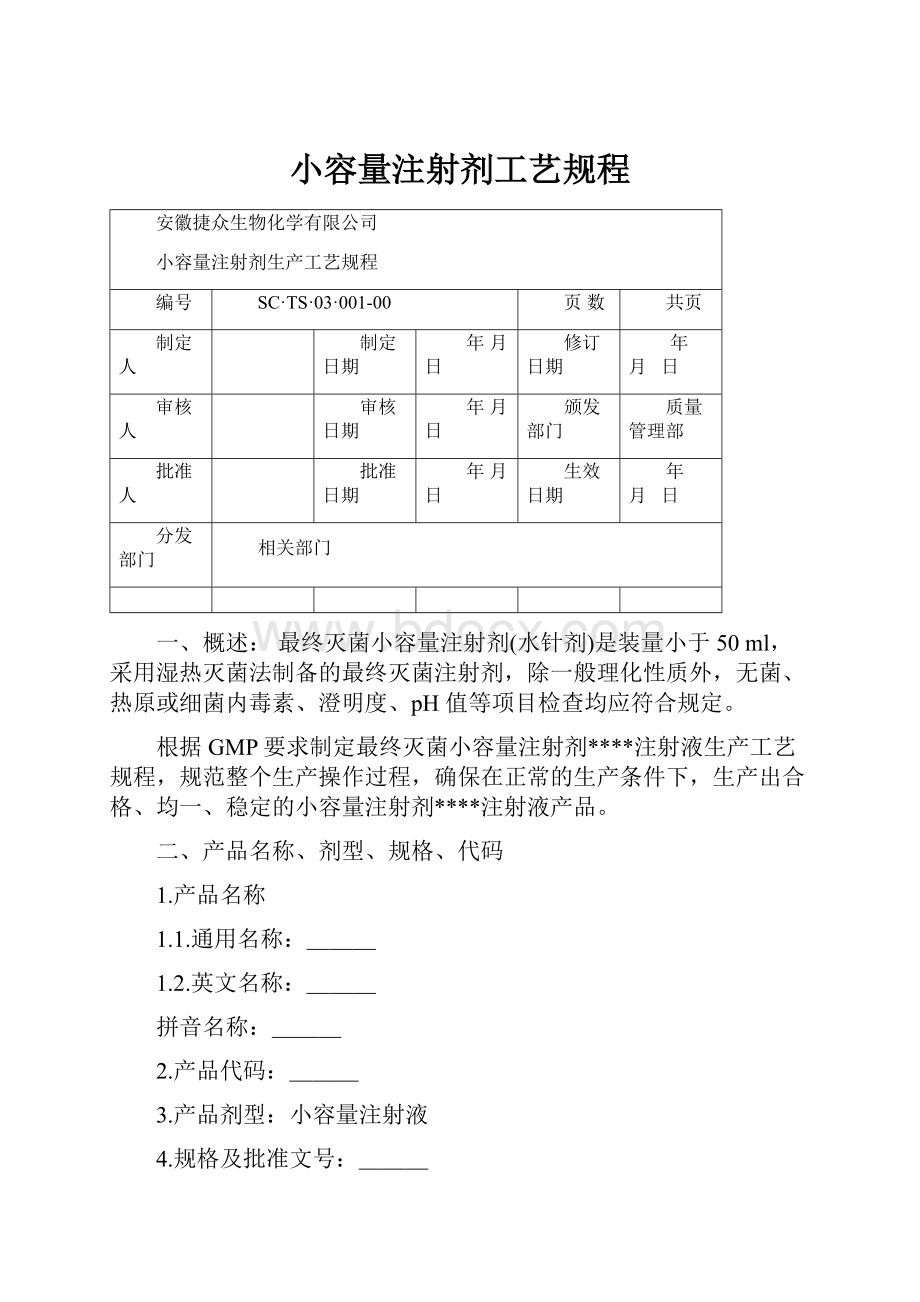
小容量注射剂工艺规程
安徽捷众生物化学有限公司
小容量注射剂生产工艺规程
编号
SC·TS·03·001-00
页数
共页
制定人
制定日期
年月日
修订日期
年月日
审核人
审核日期
年月日
颁发部门
质量管理部
批准人
批准日期
年月日
生效日期
年月日
分发部门
相关部门
一、概述:
最终灭菌小容量注射剂(水针剂)是装量小于50ml,采用湿热灭菌法制备的最终灭菌注射剂,除一般理化性质外,无菌、热原或细菌内毒素、澄明度、pH值等项目检查均应符合规定。
根据GMP要求制定最终灭菌小容量注射剂****注射液生产工艺规程,规范整个生产操作过程,确保在正常的生产条件下,生产出合格、均一、稳定的小容量注射剂****注射液产品。
二、产品名称、剂型、规格、代码
1.产品名称
1.1.通用名称:
___
1.2.英文名称:
___
拼音名称:
___
2.产品代码:
___
3.产品剂型:
小容量注射液
4.规格及批准文号:
___
4.1.产品规格:
___
4.2.包装规格:
纸箱___
4.3.批准文号:
___国药准字H
三、生产处方及依据
1.处方
处方量(_)万支(_)万支
原料_________
辅料_________
注射用水加至__ml__ml
2.批量:
最大量:
_ml支最小量_ml支
最大量:
_ml支最小量_ml支
3.依据:
《中国药典》2010年版二部
《产品注册要求文件》
四、生产工艺流程及环境区域划分
五、操作过程及工艺条件
1、纯化水制备
将饮用水经石英砂过滤和活性碳过滤去除水中有机质及微粒,再经过阳离子交换柱(软化器)制的软化水,精密过滤器过滤后经二级反渗透制得纯化水。
1.1.纯化水制备操作过程:
饮用水→机械过滤→活性炭过滤→精密过滤→阳离子交换柱→一级反渗透→二级反渗透→贮罐→至各用水点。
1.2.纯化水制备工艺条件
1.2.1、纯水制备以合格饮用水为水源,纯化水水质≤2.0us/cm或≥0.5Ω/cm。
1.2.2、纯化水贮存在密闭不锈钢(316L)罐。
1.2.3纯化水制备存放时间不超过72小时。
1.2.4纯化水经紫外灯灭菌用泵输送至各使用点,各使用点使用前须安装0.45um和0.22um滤芯(膜)过滤后使用。
1.2.5反渗透装置在进口处须安装保安过滤器。
1.2.6机械过滤器和活性炭过滤器正常工作时每班生产前进行反冲一次。
1.2.7纯化水制备操作过程在线监测,应每2小时检查一次电导率、总有机碳、铵盐、酸碱度均应符合规定。
2.注射用水的制备
纯化水经多效蒸馏水机蒸馏制得注射用水,经80℃以上保温或70℃以上保温循环,用泵输送至各使用点,各使用点使用前须安装0.45um和0.22um滤芯(膜)过滤后使用。
2.1.注射用水制备操作过程:
2.2.纯化水→多效蒸馏水机蒸馏→注射用水→贮存→至各用水点。
2.2.1.注射用水制备工艺条件
2.2.2.注射用水的制备必须以合格的纯化水为制备水源。
2.2.3.注射用水贮存在密闭不锈钢(316L)罐。
2.2.4注射用水制备操作过程,应每2小时检查电导率、总有机碳、铵盐、pH值均应合格。
2.1.5贮水罐夹套保温良好,注射用水应在80℃以上保温贮存,70℃以上保温循环。
2.1.6注射用水贮存、输送系统应做到每星期工作结束后进行在线清洗(CIP)、灭菌(SIP);生产前用注射用水清洗后使用。
3.备料
备料程序:
批生产指令→确认所需物料→计算→复核→领料单→仓库备料→检查、复核领取所需物料→脱去外包装→清洁→物料暂存间备用。
3.1根据生产指令确认所需物料名称、规格、生产厂家及批号,并按产量及消耗定额(原辅料需折干折纯)计算各自用量,复核无误后填写领料单,通知仓库备料。
3.2车间领料员、备料人员凭车间领料单到仓库领取所需物料,检查外包装是否完好,核对品名规格、生产厂家、批号、检查产品合格证及有效期。
3.3检查因取样或重复领取后重新封好的包装应有取样标记或领用标记,并复核取样或领用记录无误后方可领料。
3.4对于需拆包称取的物料应用清洁容器盛放,称后密封。
3.5复核领取的物料数量无误后,发料人、领料人、复核人签名由车间物流入口按《物品进出洁净区操作规程》(文件编号:
SC·SOP·00·006-00)脱去外包装,清洁后(必要时用75%乙醇擦拭消毒)经气闸室传递进入物料暂存间。
3.6由车间使用人核对物料,核对品名、批号、数量无误后接收。
4.称量
称量程序:
分别核对物料→校准衡器→称量→复核→QA独立复核→送至配制间(调配间)备用。
4.1.称量操作前准备
4.1.1.操作人员按照《人员进出C级洁净区清洁操作规程》(文件编号:
SC·SOP·00·031-00)进行清洁、消毒、更衣后进入称量间,房间编号XR-***.
4.1.2.检查生产现场有上批清场合格证副本,地面、墙面、容器具、工具、计量器具等清洁合格。
4.1.3检查温度、湿度符合工艺要求,并做好记录。
4.2.称量操作过程:
4.2.1.按电子秤标准操作规程校准电子称。
4.2.2.按生产指令复核领取物料,核对品名、批号、数量、产品代码、生产厂家、有效期是否一致。
4.2.3.按《称量操作规程》(文件编号:
SC·SOP·00·020-00)对原辅料进行称量,复核操作;按《药用炭称量操作规程》(文件编号:
SC·SOP·00·019-00)对药用炭进行称量。
4.2.4.送至浓配间备用。
4.3.工艺条件
4.3.1.称量前二人认真分别核对欲配药物应与生产指令相符和检查现场无上批遗留物料。
4.3.2配制人员在称量配制投料时,将对每一原辅料的物料名称、规格、数量、生产日期等进行核对,确认该投放原辅料是否是该批投料的物料。
4.3.3.配制人员在称量配制投料时,将对每一原辅料包装内物料按同一物品的感官检验方法或者其他的检验确认方法确认每一包装内的原辅料为同一物料。
4.3.4确认方法:
配制人员在称量配制投料时,按《原辅料确认操作规程》(文件编号:
WC·SOP·00·001-00)对每一原辅料包装内物料进行确认
4.3.5.称量前认真校准衡器后方可称量。
4.3.6.称量前检查盛装药物容器应清洁干燥,否则应重新处理后方可称量。
4.3.7.称量前应开启直排风装置,检查相对压差成负压;在排风罩下进行称量操作(未开排风不得进行称量操作),避免与其他房间送风形成交叉污染。
4.3.8.称量后按内外包装顺序紧扎(或密闭容器),袋(容器)上标识填写药物名称、批号、称量数量、剩余数量、称量人、存放人、存放时间等内容,退回到原辅料暂存间该品种存放位置,然后再进行下个原辅料的称量工作。
4.3.9.称量时认真做好称量记录,并核对无误方可进行下道工序。
称量时必须做到一人称量一人复核,QA独立复核,确保称量原辅料符合生产指令要求。
4.4.活性炭调配
4.4.1.操作前准备
4.4.1.1.检查调炭间仪清洁并有清场合格证副本,工具有清洗合格证
4.4.1.2.接收针用活性炭,并核对品名、规格、数量。
4.4.1.3检查注射用水供给情况应符合规定;量具清洁备用。
4.4.2.调配操作过程
4.4.2.1.将活性炭在脱外包间除去外包装放,清洁后(必要时用75%乙醇表面檫拭消毒)置传递窗,关闭传递窗门开紫外灯照射灭菌15分钟。
4.4.2.2.小心打开活性炭包装,根据处方称量所需活性炭,称好后放入容器内。
4.4.2.3.用洁净量筒量取注射用水__ml,将称量好的活性炭调成炭糊,备用。
4.4.2.4.将处理好的活性炭(贴上标签,注明品名、数量、规格、配制人)传至浓配间,备用。
4.4.2.5.将剩余活性炭封好置洁净容器内加盖,贴上标签注明品名、数量、规格、批号、称量数、剩余量、称量人、复核人等,退回原辅料暂存间置活性炭存放区存放。
4.4.2.6.称量结束按《清场操作规程》(文件编号:
SC·SOP·02·012-00)、《洁净区容器具清洗消毒规程》(文件编号:
SC·SOP·01·007-00)清场、清洗消毒;清场、清洗消毒结束自检合格后通知QA检查,填写生产、清场记录。
4.4.2.7.由QA检查合格后颁发清场合格证。
5.配制
配制程序:
加热煮沸
物料(已称量物料)→浓配脱碳→稀配→粗滤→
调PH、加活性炭
检查可见异物
精滤符合规定→灌封
调PH、测含量
摩尔浓度渗透压
5.1.浓配
5.1.1.操作前准备
5.1.1.1.操作人员按《人员进出C级洁净区清洁操作规程》(文件编号:
SC·SOP·00·031-00)进行清洁、消毒、更衣后进入浓配间。
5.1.1.2.确认生产现场有上批清场合格证副本。
5.1.1.3.确认地面、墙面、设备、管道、器具已清洁。
5.1.1.4.确认水、电、气供应充足,质量符合规定,设备计量器具完好。
5.1.1.5.确认生产文件、状态标志齐备,核对生产状态标志,包括品名、规格、数量。
5.1.1.6.领取并核对原辅料,名称、规格、批号、数量与批生产指令一致。
5.1.1.7.确认过滤系统安装完毕符合要求。
5.1.2浓配操作过程
5.1.2.1.根据批生产指令及工艺参数要求,按《投料前检查复核操作规程》(文件编号:
SC·SOP·04·008-00)、《PLG300浓配(罐)设备系统操作规程》(文件编号:
SB·SOP·07·005-00)、《小容量注射剂浓配岗位操作规程》(文件编号:
SC·SOP·04·013-00)等SOP要求进行浓配操作。
5.1.2.2.打开注射用水阀向浓配罐注入注射用水,加注射用水至配制全量的1/3;取称量好的原料辅料按工艺要求投料顺序从投料口加入浓配罐加热、搅拌使其溶解;测量PH值,按工艺要求用PH调节剂(10%氢氧化钠溶液或10%盐酸溶液)调节酸碱度;加入已调好的炭,开启搅拌器,搅拌15分钟,使原辅料完全溶解。
(煮沸100℃、30分钟、设备夹层压力≤0.3MPa)
5.1.2.3.打开循环系统阀门(配液罐出料阀、循环阀)经钛棒过滤器循环过滤药液25分钟,除去药液活性炭;使药液澄明无明显可见异物。
5.1.2.4.开启至稀配阀门关闭循环阀门,将药液泵入稀配罐。
5.1.2.5.药液泵完后打开注射用水阀、万向清洗球阀冲洗浓配罐内壁,重复冲洗2遍,冲洗用水量≤配制全量的1/3,淋洗液泵入稀配罐。
5.1.2.6.认真填写生产记录,生产后清场。
5.1.2.7.QA检测合格后颁发清场合格证
表1浓配设备、容器具清洗方法、时间及合格标准
清洗方法
名称
超声波清洗(次/min)
纯化水冲洗(次/min)
注射用水冲洗(次/min)
合格标准
备注
不锈钢桶
——
3次/每次
2min
2次/每次
2min
洁净
无明显污渍
不锈钢勺
——
3次/每次
2min
2次/每次
2min
洁净
无明显污渍
配液罐
——
3次/每次
5min
2次/每次
5min
洁净
无明显污渍
钛棒过滤器
15min
——
2次/每次
3min
洁净
无明显污渍
呼吸器
15min
——
2次/每次
3min
完整性测试
符合规定
表2浓配设备、容器具消毒(灭菌)方法、时间及合格标准
消毒方法
名称
消毒液浸泡消毒(min)
或湿热灭菌
(121℃/min)
或纯蒸汽灭菌
(121℃/min)
注射用水冲
洗(次/min)
合格标准
备注
不锈钢桶
30min
121℃/30min
121℃/30min
2次/每次
3min
微生物、细菌内毒素测试应符核规定
不锈钢勺
30min
121℃/30min
121℃/30min
2次/每次
3min
配液罐
——
——
121℃/30min
2次/每次
3min
钛棒过滤器
——
121℃/30min
——
2次/每次
3min
呼吸器
——
121℃/30min
——
2次/每次
3min
5.1.3.浓配工艺条件
5.1.3.1.投料前认真核对原辅料与生产指令相符,确认无上批遗留物、清场符合要求。
5.3.2.操作前应检查浓配罐及过滤系统应清洁,符合工艺要求,用注射用水淋洗__遍方可投料。
5.1.3.3.浓配注射用水量应控制全量的__%左右。
5.1.3.4.注射用水__℃左右投料,边投料边搅拌。
5.1.3.5.浓配(煮沸)经1.0um钛棒过滤器回流__min,取样,药液澄清后泵入稀配罐
5.1.3.6.泵完药液后浓配罐用注射用水淋洗__遍后药液经1.0um钛棒过滤器泵入稀配罐。
5.1.3.7.使用完毕后,按《小容量注射剂浓配系统清洗消毒操作规程》(文件编号:
SC·SOP·05·001-00)、《清场操作规程》(文件编号:
SC·SOP·02·012-00)进行清洗、灭菌。
清洗罐体、管道、容器具至无产品残留药液,更换相关生产文件及生产状态标志,将废弃物清理干净,清洁地面、平台。
5.1.3.8.QA检查合格后悬挂“已清洁”标志和清场合格证。
5.1.3.9按《记录填写操作规程》(文件编号:
SC·SOP·04·002-00)填写生产清洁、清场记录,
55.2稀配
5.2.1操作前准备
5.2.1.1.操作人员按照《人员进出C级洁净区更衣操作规程》(文件编号:
SC·SOP·00·031-00)进行清洁、消毒、更衣后进入稀配间.
5.2.1.2.确认现场无上批生产遗留物、有上批清场合格证副本。
5.2.1.3.确认地面、门窗、墙面清洁,设备、管道、器具已清洁。
5.2.1.4.确认水、电、气供应符合,设备完好、过滤系统完好。
5.2.1.5.确认生产文件、状态标志齐备
5.2.1.6.核对生产状态标志包括品名、批号、数量等。
5.2.1.7.确认配料间与相邻房间压差≥5Pa,温度18℃~26℃,湿度45%~65%。
5.2.2稀配操作过程
5.2.2.1.待浓配罐药液泵入稀配罐,按《PLG600稀配(罐)设备系统操作规程》(文件编号:
SB·SOP·07·005-00)、《小容量注射剂稀配岗位操作规程》(文件编号:
SC·SOP·04·014-00)等SOP要求进行浓配操作。
加入注射用水至生产工艺规定量的4/5。
5.2.2.2.开启搅拌器搅拌15分钟,开启过滤循环系统各阀门,使药液在管道系统内经过滤系统循环15分钟。
5.2.2.3.取样检测PH值,确认使用PH调节剂的名称、浓度、数量,调节PH开启搅拌器搅拌均匀;调节药液PH值应符合工艺规定。
5.2.2.4.药液经过循环过滤装置回流15分钟后,定容至工艺要求的全量。
5.2.2.5.按产品中间体质量标准取样检测含量、PH、可见异物,含量、PH、可见异物检测合格。
备用。
5.2.2.6.取样检验合格后打开回流阀、至灌装间泵入灌装间备用。
5.2.2.7.生产结束后按《小容量注射剂稀配系统清洗消操作规程》(文件编号:
SC·SOP·05·002-00)、《C洁净区清场操作规程》(文件编号:
SC·SOP·02·012-00)进行清洗、消毒(灭菌)操作。
清洗罐体、管道、容器具至无产品残留液;更换相关生产文件及生产状态标志;将废弃物清理干净;清洁地面、平台。
5.2.2.8.按《记录填写操作规程》(文件编号:
SC·SOP·04·002-00)填写生产清洁、清场记录,
5.2.2.9.经QA检查合格后悬挂“已清洁”标志和清场合格证。
表3稀配设备、容器具清洗方法、时间及合格标准
清洗方法
名称
超声波清洗(次/min)
纯化水冲洗(次/min)
注射用水冲洗(次/min)
合格标准
备注
不锈钢桶
——
3次/每次
2min
2次/每次
2min
洁净
无明显污渍
不锈钢勺
——
3次/每次
2min
2次/每次
2min
洁净
无明显污渍
稀配罐、输送系统设备
——
3次/每次
5min
2次/每次
5min
洁净
无明显污渍
钛棒过滤器
15min
——
2次/每次
3min
洁净
无明显污渍
折叠式滤芯
15min
——
2次/每次
3min
完整性测试
符合规定
呼吸器
15min
——
2次/每次
3min
完整性测试
符合规定
表4稀配设备、容器具消毒(灭菌)方法、时间及合格标准
消毒方法
名称
消毒液浸泡消毒(min)
或湿热灭菌
(121℃/min)
或纯蒸汽灭菌
(121℃/min)
注射用水冲
洗(次/min)
合格标准
备注
不锈钢桶
30min
121℃/30min
121℃/30min
2次/每次
3min
1、微生物、细菌内毒素测试应符核规定
2、完整性测试符合规定
不锈钢勺
30min
121℃/30min
121℃/30min
2次/每次
3min
稀配罐、输送系统设备
30min
——
121℃/30min
2次/每次
3min
钛棒过滤器
30min
121℃/30min
——
2次/每次
3min
折叠式滤芯
30min
121℃/30min
——
2次/每次
3min
呼吸器
30min
121℃/30min
——
2次/每次
3min
5.2.3稀配工艺条件
5.2.3.1.操作前应检查罐及管道过滤系统应清洁,符合工艺要求方可投料;挂有“清场合格证”标志。
5.2.3.2.水、电、汽(气)供应满足生产需要;设备运行应正常;配制罐液位计显示度灵敏。
5.2.3.3.应将处方量的注射用水注入配制罐,定容时应缓慢地补加注射用水至全量,冷却降温至50-60℃左右,取样检测含量、渗透压摩尔浓度、PH值合格后,经1.0um钛棒过滤器粗滤、0.45um折叠式滤器(膜)精滤,取样检查可见异物,合格后方可送入灌装室经0.22um折叠式滤器过滤后灌封。
5.2.3.4.药液在精滤前折叠式滤芯需做完整性测试,合格后方可使用;生产结束折叠式滤芯仍需做完整性测试确认生产过程过滤精度的可靠性。
5.2.3.5生产过程应密切观察折叠式滤芯(膜)精滤时过滤前和过滤后压力。
若压力出现异常应即时查找原因并排除。
5.2.3.6.药液配制结束应在12小时内灌封。
5.2.3.7.药液灌封完毕后应及时按《小容量注射剂稀配系统清洗消操作规程》做好稀配罐及输送系统设备的清洁和灭菌(消毒),备用。
5.2.3.8.配制工作结束后及时做好本工序的清洁和清场工作,应符合清洁及清场要求。
5.2.3.9.按《记录填写操作规程》(文件编号:
SC·SOP·04·002-00)填写生产清洁、清场记录,并复核。
6.洗瓶
洗瓶程序:
三水、三气
按批生产指令
领取空安瓿瓶理瓶超声波洗瓶精洗干燥灭
水压≥0.2MPa
压缩空气≥0.3MPa
菌冷却灌封
6.1.理瓶操作前准备
6.1.1.理瓶岗位操作人员按《一般区更衣更衣操作规程》(编码__)清洁更衣后进入理瓶间。
6.1.2.确认操作间已清洁、清场,无上批生产遗留物,有清场合格证副本。
6.1.3.确认地面、门窗、墙面清洁;安瓿周转盘清洁并有“已清洁”标志。
6.1.4.确认生产文件、状态标志齐备,核对生产状态标志;确认安瓿瓶型号、规格、数量、批号、代码等。
6.1.2.理瓶操作过程
6.1.2.1.按需料领料单领取安瓿瓶核对规格、批号、生产厂家、数量、报告书号等,与生产指令一致后除去外包装,清洁后搬入理瓶间;按《理瓶岗位操作规程》进行正确操作。
6.1.2.2.除去外包装检查安瓿破损情况,如破损重新更换。
6.1.2.3.将安瓿瓶整齐摆放在空安瓿周转盘内排满,放标示卡标明品名、规格、数量;剔除破损、受污染等不合格的安瓿瓶。
6.1.2.4.将装好安瓿的安瓿周转盘按规定放在安瓿缓冲间货架上,备用。
6.1.2.5.通知洗瓶工序进行接瓶。
6.1.2.6.理瓶结束按《一般生产区清场操作规程》清场,更换相关生产文件及生产状态标志,整理、清除内、外包装物及其他废弃物;清洁工作台及地面按《记录填写操作规程》(文件编号:
SC·SOP·04·002-00)认真填写生产清洁、清场记录,并复核。
6.1.3.理瓶工艺条件
6.1.3.1.理瓶前应核对安瓿规格、批号、数量等与生产指令一致。
6.1.3.2.理瓶时应随时注意剔除瓶口不圆整、瓶身不规格、麻点、砂眼、破瓶、歪底、掉底等不合格瓶。
6.1.3.3.将安瓿瓶整齐摆放在安瓿周转盘中,瓶口一律朝上。
6.1.3.4.理瓶过程中应轻拿轻放,尤其注意保护安瓿瓶口。
6.1.3.5.安瓿瓶要排列紧密,以手轻按安瓿瓶,左右摆动无缝隙。
6.1.3.6.摆放好的安瓿瓶必须经过气闸间(缓冲间)进入洗瓶间。
6.2.洗烘瓶
6.2.1.操作前准备
6.2.1.1洗烘瓶岗位操作人员按《C级洁净区更衣操作规程》清洁、更衣、消毒后进入洗烘瓶间。
6.2.1.2.检查清场情况是否符合规定,确认生产现场无上批遗留物,地面、门、窗、墙面清洁,有清场合格证副本。
6.2.1.3.确认生产文件、状态标志正确、齐备。
6.2.1.4.核对安瓿瓶规格、数量、代码。
6.2.1.5.确认设备完好,计量器具(压力表、温度计)完好,气水管路、电路连接符合要求,水、电、气供应符合生产需求。
6.2.1.6.确认洗烘瓶间温湿度在规定范围内(温度18℃~26℃,湿度45%~65%),与相邻房间相对压差≥5Pa。
6.2.2.洗烘瓶操作步骤
6.2.2.1.在气闸间接收从理瓶间移交过来的安瓿瓶核对品名、规格、数量,并填写记录,将安瓿瓶送至洗瓶间。
6.2.2.2.接通电源打开超声波洗瓶机,检查设备空运是否正常;按《小容量注射剂洗烘瓶岗位操作规程》、《QLC120型立式超声波清洗机操作规程》、《KSZ620/43型隧道式干燥灭菌机操作规程》进行正确操作。
6.2.2.3.在操作画面上轻触“加热Ⅰ启动”、“加热Ⅱ启动”,信号灯由红色变为绿色,水箱自动加热,并将水温恒定在,40℃~60℃。
6.2.2.4.打开新鲜水控制阀门,将压力调到≥0.2MPa,打开压缩空气阀门,将压力调到≥0.3MPa。
6.2.2.5.在操作画面上轻触“水泵启动”按键,水泵状态指示灯由红色变成绿色,同时将循环水过滤罩内空气排尽,水泵启动是储水槽内水位会下降,这时应打开新鲜水阀门,将水槽注满水。
6.2.2.6.打开循环水控制阀,将压力调到≥0.2MPa,打开喷淋水控制阀,将压力调到≤0.05MPa。
6.2.2.7.在操作画面上轻触“超声波”按钮,启动超声波,频率控制在20~50Hz。
6.2.2.8.将空安瓿放在