数控加工对刀编程实例.docx
《数控加工对刀编程实例.docx》由会员分享,可在线阅读,更多相关《数控加工对刀编程实例.docx(10页珍藏版)》请在冰豆网上搜索。
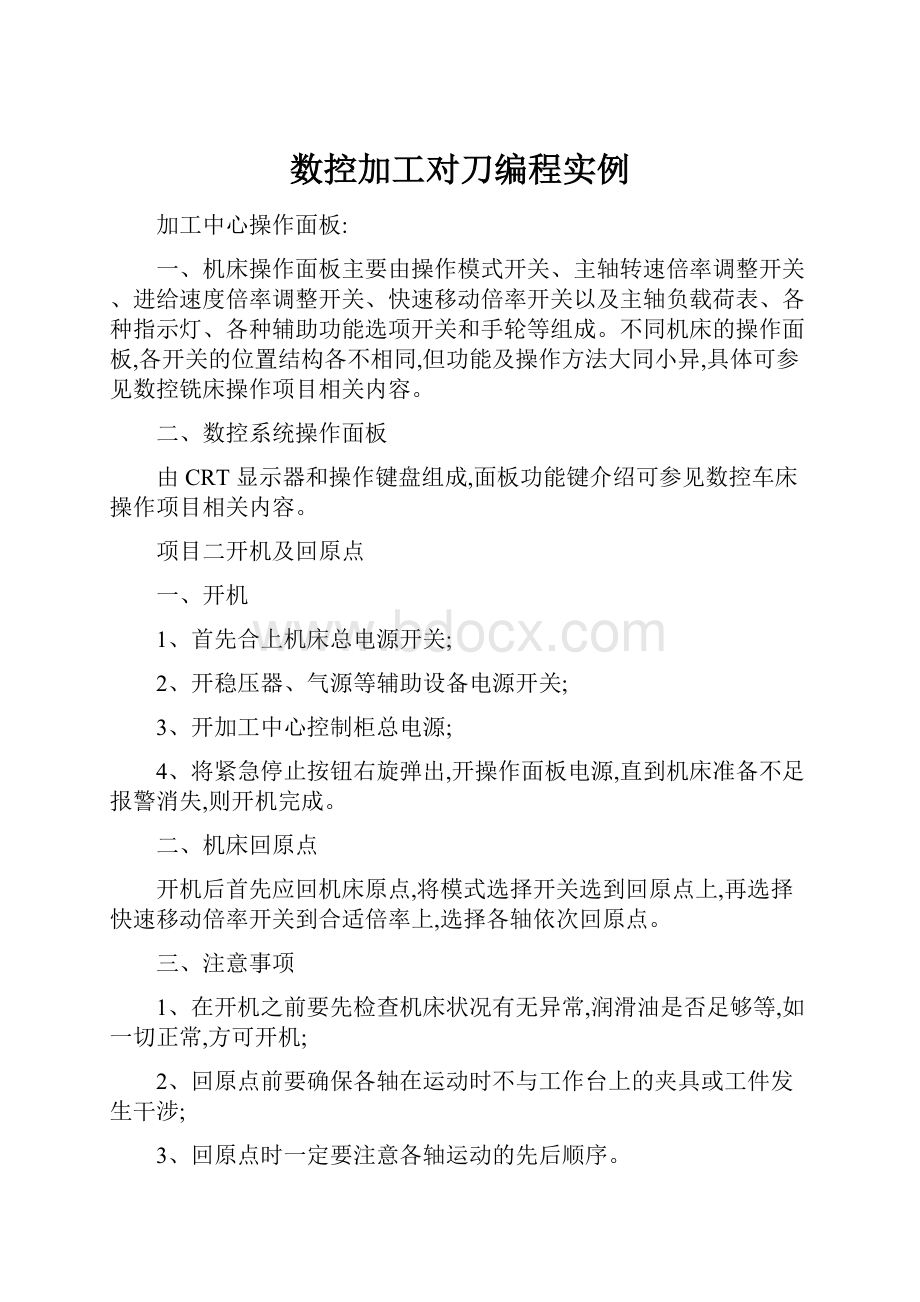
数控加工对刀编程实例
加工中心操作面板:
一、机床操作面板主要由操作模式开关、主轴转速倍率调整开关、进给速度倍率调整开关、快速移动倍率开关以及主轴负载荷表、各种指示灯、各种辅助功能选项开关和手轮等组成。
不同机床的操作面板,各开关的位置结构各不相同,但功能及操作方法大同小异,具体可参见数控铣床操作项目相关内容。
二、数控系统操作面板
由CRT显示器和操作键盘组成,面板功能键介绍可参见数控车床操作项目相关内容。
项目二开机及回原点
一、开机
1、首先合上机床总电源开关;
2、开稳压器、气源等辅助设备电源开关;
3、开加工中心控制柜总电源;
4、将紧急停止按钮右旋弹出,开操作面板电源,直到机床准备不足报警消失,则开机完成。
二、机床回原点
开机后首先应回机床原点,将模式选择开关选到回原点上,再选择快速移动倍率开关到合适倍率上,选择各轴依次回原点。
三、注意事项
1、在开机之前要先检查机床状况有无异常,润滑油是否足够等,如一切正常,方可开机;
2、回原点前要确保各轴在运动时不与工作台上的夹具或工件发生干涉;
3、回原点时一定要注意各轴运动的先后顺序。
项目三工件安装
根据不同的工件要选用不同的夹具,选用夹具的原则:
1、定位可靠;
2、夹紧力要足够。
安装夹具前,一定要先将工作台和夹具清理干净。
夹具装在工作台上,要先将夹具通过量表找正找平后,再用螺钉或压板将夹具压紧在工作台上。
安装工件时,也要通过量表找正找平工件。
项目四刀具装入刀库
一、刀具选用
加工中心的刀具选用与数控铣床基本类似,在此不再赘述。
二、刀具装入刀库的方法及操作
当加工所需要的刀具比较多时,要将全部刀具在加工之前根据工艺设计放置到刀库中,并给每一把刀具设定刀具号码,然后由程序调用。
具体步骤如下:
1、将需用的刀具在刀柄上装夹好,并调整到准确尺寸;
2、根据工艺和程序的设计将刀具和刀具号一一对应;
3、主轴回Z轴零点;
4、手动输入并执行“T01M06”;
5、手动将1号刀具装入主轴,此时主轴上刀具即为1号刀具;
6、手动输入并执行“T02M06”;
7、手动将2号刀具装入主轴,此时主轴上刀具即为2号刀具;
8、其它刀具按照以上步骤依次放入刀库。
三、注意事项
将刀具装入刀库中应注意以下问题:
1、装入刀库的刀具必须与程序中的刀具号一一对应,否则会损伤机床和加工零件;
2、只有主轴回到机床零点,才能将主轴上的刀具装入刀库,或者将刀库中的刀具调在主轴上;
3、交换刀具时,主轴上的刀具不能与刀库中的刀具号重号。
比如主轴上已是“1”号刀具,则不能再从刀库中调“1”号刀具。
项目五对刀及刀具补偿
一、对刀
对刀方法与具体操作同数控铣床。
二、刀具长度补偿设置
加工中心上使用的刀具很多,每把刀具的长度和到Z坐标零点的距离都不相同,这些距离的差值就是刀具的长度补偿值,在加工时要分别进行设置,并记录在刀具明细表中,以供机床操作人员使用。
一般有两种方法:
1、机内设置
这种方法不用事先测量每把刀具的长度,而是将所有刀具放入刀库中后,采用Z向设定器依次确定每把刀具在机床坐标系中的位置,具体设定方法又分两种。
(1)第一种方法将其中的一把刀具作为标准刀具,找出其它刀具与标准刀具的差值,作为长度补偿值。
具体操作步骤如下:
①将所有刀具放入刀库,利用Z向设定器确定每把刀具到工件坐标系Z向零点的距离,如图5-2所示的A、B、C,并记录下来;
②选择其中一把最长(或最短)、与工件距离最小(或最大)的刀具作为基准刀,如图5-2中的T03(或T01),将其对刀值C(或A)作为工件坐标系的Z值,此时H03=0;
③确定其它刀具相对基准刀的长度补偿值,即H01=±│C-A│,H02=±│C-B│,正负号由程序中的G43或G44来确定。
④将获得的刀具长度补偿值对应刀具和刀具号输入到机床中。
screen.width-500)this.width=screen.width-500">
(2)第二种方法将工件坐标系的Z值输为0,调出刀库中的每把刀具,通过Z向设定器确定每把刀具到工件坐标系Z向零点的距离,直接将每把刀具到工件零点的距离值输到对应的长度补偿值代码中。
正负号由程序中的G43或
G44来确定。
2、机外刀具预调结合机上对刀
这种方法是先在机床外利用刀具预调仪精确测量每把在刀柄上装夹好的刀具的
轴向和径向尺寸,确定每把刀具的长度补偿值,然后在机床上用其中最长或最短的一把刀具进行Z向对刀,确定工件坐标系。
这种方法对刀精度和效率高,便于工艺文件的编写及生产组织。
三、刀具半径补偿设置
进入刀具补偿值的设定页面,移动光标至输入值的位置,根据编程指定的刀具,键入刀具半径补偿值,按INPUT键完成刀具半径补偿值的设定。
项目六程序输入及调试
一、程序输入
程序的输入有多种形式,可通过手动数据输入方式(MDI)或通信接口将加工程序输入机床,也可实行在线加工。
二、程序调试
由于加工中心的加工部位比较多,使用的刀具也比较多。
为方便加工程序的调试,一般根据加工工艺的安排,针对每把刀具将各个加工部位的加工内容编制为子程序,而主程序主要包含换刀命令和子程序调用命令。
程序的调试可利用机床的程序预演功能或以抬刀运行程序方式进行,依次对每个子程序进行单独调试。
在程序调试过程中,可根据实际情况修调进给倍率开关。
项目七程序运行
在程序正式运行之前,要先检查加工前的准备工作是否完全就绪。
确认无误后,选择自动加工模式,按下数控启动键运行程序,对工件进行自动加工。
在自动运行程序加工过程中,如果出现危险情况时,应迅速按下紧急停止开关或复位键,终止运行程序。
项目八零件检测
将加工好的零件从机床上卸下,根据零件不同尺寸精度、粗糙度、位置度的要求选用不同的检测工具进行检测。
项目九关机
零件加工完成后,清理现场,再按与开机相反的顺序依次关闭电源。
零件加工实例
一、加工要求
加工如图5-3所示零件。
零件材料为LY12,单件生产。
零件毛坯已加工到尺寸。
选用设备:
V-80加工中心
screen.width-500)this.width=screen.width-500">
二、准备工作
加工以前完成相关准备工作,包括工艺分析及工艺路线设计、刀具及夹具的选择、程序编制等。
三、操作步骤及内容
1、开机,各坐标轴手动回机床原点
2、刀具准备
根据加工要求选择Φ20立铣刀、Φ5中心钻、Φ8麻花钻各一把,然后用弹簧夹头刀柄装夹Φ20立铣刀,刀具号设为T01,用钻夹头刀柄装夹Φ5中心钻、Φ8麻花钻,刀具号设为T02、T03,将对刀工具寻边器装在弹簧夹头刀柄上,刀具号设为T04。
3、将已装夹好刀具的刀柄采用手动方式放入刀库,即
1)输入“T01M06”,执行
2)手动将T01刀具装上主轴
3)按照以上步骤依次将T02、T03、T0
4放入刀库
4、清洁工作台,安装夹具和工件
将平口虎钳清理干净装在干净的工作台上,通过百分表找正、找平虎钳,再将工件装正在虎钳上。
5、对刀,确定并输入工件坐标系参数
1)用寻边器对刀,确定X、Y向的零偏值,将X、Y向的零偏值
输入到工件坐标系G54中,G54中的Z向零偏值输为0;
2)将Z轴设定器安放在工件的上表面上,从刀库中调出1号刀具装上主轴,用这把刀具确定工件坐标系Z向零偏值,将Z向零偏值输入到机床对应的长度补偿代码中,“”、“-”号由程序中的G4
3、G4
4来确定,如程序中长度补偿指令为G43,则输入“-”的Z向零偏值到机床对应的长度补偿代码中;
3)以同样的步骤将2号、3号刀具的Z向零偏值输入到机床对应的长度补偿代码中。
6、输入加工程序
将计算机生成好的加工程序通过数据线传输到机床数控系统的内存中。
7、调试加工程序
采用将工件坐标系沿Z向平移即抬刀运行的方法进行调试。
1)调试主程序,检查3把刀具是否按照工艺设计完成换刀动作;
2)分别调试与
3把刀具对应的3个子程序,检查刀具动作和加工路径是否正确。
8、自动加工
确认程序无误后,把工件坐标系的Z值恢复原值,将快速移动倍率开关、切削进给倍率开关打到低档,按下数控启动键运行程序,开始加工。
加工过程中注意观察刀具轨迹和剩余移动距离。
9、取下工件,进行检测
选择游标卡尺进行尺寸检测,检测完后进行质量分析。
10、清理加工现场
11、关机
R参数与子程序的妙用
一提到R参数编程(或宏程序),大多数都是用在一些曲面或复杂的轮廓中,本人结合自己工作实际,在一些大小不一,外形相似一些槽系中将子程序与R参数结合,缩短了编程的时间,增加了程序的灵活性和通用性,提高了加工效率。
一、零件图见10.26
注:
板厚为15mm,未注圆角R3
二、工艺分析
该零件上的九个槽尺寸长度和宽度方向尺寸不完全一致,直接调用子程序加工很难做到。
经过分析,本人将R参数引入子程序中,在加工每个槽之前,只需将槽长度和宽度赋予相应R参数中,再调用子程序,就可用一个子程序将横纵槽系都加工出来,编程效率极高。
三、程序如下:
(所用系统为SIEMENS840C)
1、主程序MPF100(所用刀具为¢6的高速钢立铣刀)
G54G90G18G64
S1200M3D1
(R10为槽在X方向的宽度)
(R11为槽在Y方向的宽度)
G0Z100(刀具提到安全高度)
G58X50Y50(将零点偏到左下角槽中心,加槽长为20mm,槽宽为8mm的纵向槽)
R10=20(槽长)
R11=8(槽宽)
R20=3.1(在横向槽时,其值为刀具半径单边留量,纵向槽时为R10/2)
R21=R11/2(在纵向槽时,其值为刀半径单边留量,纵向槽时为R11/2)
L30(调用子程序)
G58X100Y50(将零点偏到左下角槽2中心,加槽长为20mm,槽宽为8mm的横向槽)
R10=8(槽宽)
R11=20(槽长)
R20=R10/2(在横向槽时,其值为刀半径单边留量,纵向槽时为R10/2)
R21=3.1(在纵向槽时,其值为刀半径单边留量,纵向槽时为R11/2)
L30(调用子程序)
G58X150Y50(将零点偏到左下角槽3中心,加槽长为25mm,槽宽为8mm的横向槽)
R10=25(槽长)
R11=8(槽宽)
R20=3.1(在横向槽时,其值为刀半径单边留量,纵向槽时为R10/2)
R21=R11/2(在纵向槽时,其值为刀半径单边留量,纵向槽时为R11/2)L30(调用子程序)
……(依次输入参数,加工出其他槽)
……
G58X0Y0(取消坐标系的偏移)
G0Z200
M30
2、子程序L30
G90G18G64
G0Z100
G0X=-R30Y=R31
Z10
G1Z0F1000
L31P=30
G1X0Y0
Z-8
L32
G1X0Y0
Y-16
L32
G1X0Y0
G1Z10
G0Z100
M17
3、子程序L31
R12=R10/2
R13=R11/2
G91
R14=R12-R20
R15=R13-R21
R30=2*R14
R31=2*R15
G1X=R30Y=-R31Z=-0.5F300(每次下刀0.5mm)G1X=-R30Y=R31
G90
M17
4、子程序L32
G1G41X=R12F300
Y=R13
X=-R12
Y=-R13
X=R12
Y0.4
G40X0
M17
四、结语
在手工编程中,充分运用R参数,不仅能使程序简单方便,提高加工效率,而且便于修改,占用空间也较少。
通过R20和R21赋不同的值,使子程序中G1X=R30Y=-R31Z=-0.5F300;G1X=-R30Y=R31的轨迹实际是平行于槽长度方向的往复直线,采用斜线下刀。
通过上述例子不难看出,参数编程有其具大的优势,在生产中充分发挥参数编程的优势,对提高数控机床加工效率有重要的意义。