罩式炉电气说明书概要.docx
《罩式炉电气说明书概要.docx》由会员分享,可在线阅读,更多相关《罩式炉电气说明书概要.docx(22页珍藏版)》请在冰豆网上搜索。
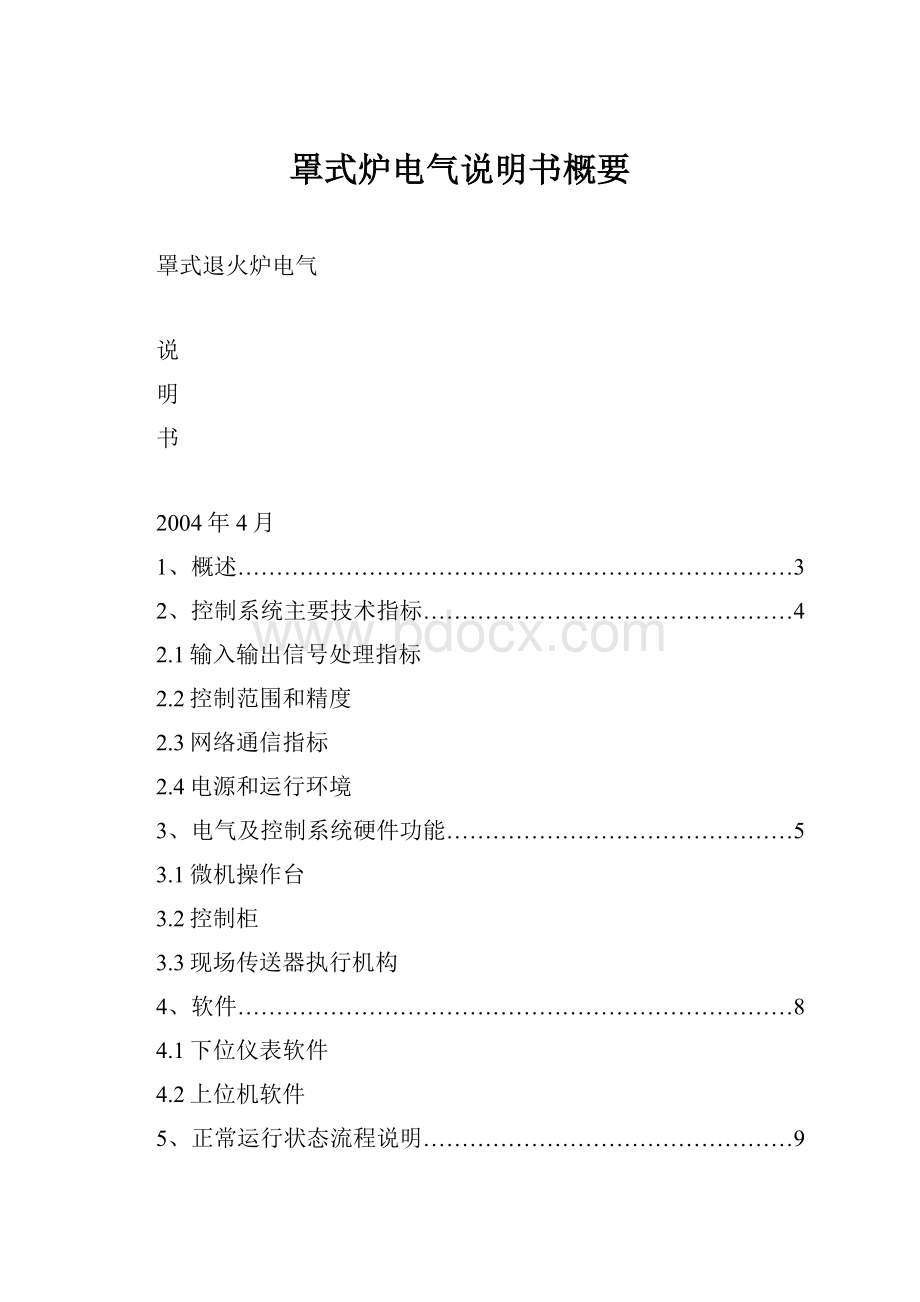
罩式炉电气说明书概要
罩式退火炉电气
说
明
书
2004年4月
1、概述………………………………………………………………3
2、控制系统主要技术指标…………………………………………4
2.1输入输出信号处理指标
2.2控制范围和精度
2.3网络通信指标
2.4电源和运行环境
3、电气及控制系统硬件功能………………………………………5
3.1微机操作台
3.2控制柜
3.3现场传送器执行机构
4、软件………………………………………………………………8
4.1下位仪表软件
4.2上位机软件
5、正常运行状态流程说明…………………………………………9
5.1工艺流程顺序控制
5.2运行中的联锁
5.3正常工作流程光信息
5.4操作提示报警信号
6、控制柜运行前检查及开机………………………………………11
6.1电源柜
6.2补偿柜
6.3风机柜
6.4公用柜
6.5PLC柜
6.6现场操作箱
6.7运行前控制柜仪表工作方式和初始参数设定
6.8常规退火操作
7、非常运行状态及处理………………………………………………20
7.1手动运行
7.2纯手动运行
7.3故障报警及处理
7.4断电事故处理
1、概述
本套冷煤气加热强对流罩式光亮退火炉控制系统,是基于现代计算机技术,把数据通讯、显示装置,过程控制和智能化数字仪表有机的结合起来,组成的高性能控制系统,具有分散控制、集中管理的优点。
系统控制对象为七套罩式光亮退火炉,每套退火炉由2个炉台、2个内罩、1个加热罩、1个冷却罩组成。
本系统由控制室中的微机操作台、主控制柜以及公用泵控制柜、现场操作箱、传感器、执行机构等组成。
系统采用计算机作为上位监控仪,图形界面丰富,具有流程显示、趋势显示、历史记录等多项功能。
在控制室中,操作人员可通过微机键盘输入和修改工艺参数,进行数据处理;也可以通过彩色显示器上提供的控制结构图、参数图、工况图等了解炉群及其周边设备的各过程参数以及控制设备本身状态。
配备打印机,还可把当前或历史的数据打印下来永久保存。
系统选用智能数字仪表作为主控单元。
在控制柜、操作箱面板上设有各种仪表、开关、按钮、指示灯、闪光报警器等,操作人员亦可设定工艺曲线修改各种工艺参数、启动或中止工艺运行,并了解各种过程控制参数及控制设备本身的状态。
由于系统采用了工业级微机、智能仪表,系统的抗干扰能力强,在显示器及控制柜面板上及时显示各种故障信息,设备的正常维护及故障处理十分方便。
2、控制系统主要技术指标
2.1输入、输出信号处理指标
2.1.1智能化控制仪表对输入、输出信号的处理指标由仪表选型确定,主要参数列表(表1)
2.1.2PLC(SIEMENSS7-300)
CPU314,32KB语句,40KBRAM,指令执行速度约0.3ms/每1000条二进制指令,数字量输入配置128点,数字量输出配置80点,模拟带输入配置2点。
2.2控制范围和精度
2.2.1控温范围0~1000℃
2.2.2仪表控温精度±5℃(保温阶段)
表1.智能化控制仪表参数
序号
分项仪表
AI-808P
AI-708
AI-708H
1
输入信号
热电偶K分度
热电偶K分度
电流4~20mADC
电流4~20mA
2
响应时间
≤0.5S
≤0.5S
≤0.5S
3
控制输出电流
4~20mADC
4
控制输出继电触点
250VAC/1A
5
报警输出(状态)
250VAC/1A
250VAC/1A
6
斜率控制
1~9999分
7
设定
30组SV、PID上/下限
两组上/下限
8
指示
双四位LED显示
双四位LED显示
双四位LED显示
9
测量精度
0.2%FS±2.0℃
0.2%FS±2.0℃0.2级
0.5级
2.3网络通信指标
2.3.1AI808P;AI-708仪表,网络通迅采用RS-485接口,网络系统的通讯媒介采用双绞线或屏蔽线。
2.3.2SEMENSS7-300(PLC)网络通讯采用5611卡对MPI接口,传输速率187.5KB/S,传输最大距离50M,网络系统的通讯媒介采用屏蔽线。
2.4电源和运行环境
电源电压:
上位机单相180~240VAC
仪表单相100~240VAC
电源频率上位机及仪表50~60Hz
工作温度0~50℃
工作湿度40~85%(无凝露)
3、电气及控制系统硬件功能
电气及仪表控制系统由微机操作台(上位机)、控制柜(下位机),及现场传感器、执行机构组成。
下位仪表采用带微处理器的智能化仪表和PLC,控制精度高,并且各个控制仪表相互独立,可靠性好。
系统工作时,由上位机设定各控制对象的工艺曲线和需要控制的工艺参数,通过网络传送给各下位仪表;下位仪表根据上位机传送来的设定值与控制对象的实测值比较,构成闭环控制回路,控制算法在下位机中完成;工艺流程顺序、联锁等开关量控制也在下位机(PLC)中完成。
上位机同时通过网络采集各控制对象及下位仪表的各项参数,经过数据处理,以图、表、声等形式在显示器及音响系统显现出来,使操作简单、直观。
下位机也能脱离上位机单独运行。
3.1微机操作台(上位机)
3.1.1硬件配置
3.1.1.1主机研华IPC610,PⅢ1.0,128M内存,40G硬盘,1.44软驱,52X光驱,键盘、光电鼠标。
3.1.1.2显示器PHILIPS17″纯平显示器
3.1.1.3通讯适配器RS232/485,6ES75611
3.1.1.4打印机惠普喷墨A4幅面
3.1.1.5UPS山特500VA
3.1.2上位机功能
对整个生产运行过程进行集中监视、管理
3.2控制柜(下位机)
3.2.1主控柜
共17面,从右至左分别为总电源控制柜,补偿柜,1~4组炉风机柜,公用柜,5~7组炉风机柜,1~7组炉PLC柜。
3.2.1.1总电源柜包括电源的控制,供电指示、操作开关。
3.2.1.2补偿柜包括无功补偿的手、自动控制,功率因数显示。
3.2.1.3风机柜包括对1#、2#循环风机2台,冷却风机2台,助燃风机1台,喷淋冷却水阀2个,排气阀2个,进气阀2个的纯手动启动、停止控制。
循环风机的高/低速纯手动转换控制和指示。
(纯手动指信号不经过上位机及PLC,直接由按纽或开关控制)。
3.2.1.4公用柜为7组炉公用,包括4台真空泵,4台抽水泵的手动启动,停止控制和指示,故障报警指示。
煤气流量积算仪表(8BT1)也在公用柜上。
3.2.1.5PLC柜包括PLC模块、仪表、二次控制回路,完成对1#、2#炉台的温度控制、炉压控制、工艺顺序和联锁控制、声光报警和指示等。
BT1、BT2、BT3、BT4、BT5智能控制仪完成对1#、2#炉台及加热罩温度的程序设定、闭环控制、报警等功能。
本控制系统主控部分可看作由BT1、BT3、BT5温度控制仪对1#、2#两个炉台内罩温度及加热罩温度主参数闭环控制。
BT6、BT7对1#、2#两个炉台的炉气压力进行三位调节控制、报警显示。
逻辑控制包括工艺流程顺序控制、联锁控制、声光报警显示,由PLC完成。
可实现自动/手动运行切换,手动操作时,由PLC柜和现场操作箱上各开关、按钮直接控制相应电动机、阀门的启动、停止(此手动信号经过PLC)。
3.2.2现场操作箱
共14台,每组炉1#、2#炉台对应有1#、2#两个操作箱,包括状态显示,阀门控制,急停按钮等。
3.3现场传感器及执行机构
3.3.1每个炉台现场传感器包括内罩K型热电偶2只,炉压变送器1台,加热罩K型热电偶1支为2炉台公用,它们分别检测炉温、炉内压力,输出模拟量作为仪表控制信号。
3.3.27组炉共用压力控制器2个,分别检测炉台冷却水及喷淋冷却水的水压过低及水压下限信号。
3.3.3每套炉一个加热罩,加热罩上带有烧嘴控制器箱,箱内装有10个烧嘴控制器,分别控制10个烧嘴的点火、熄火及火焰监测,并将信号传回PLC。
每套烧嘴控制包括烧嘴控制器、点火变压器、燃气电磁阀、点火电极,监测电极。
每个加热罩上设有电动执行器1台,由温控仪表的PID调节输出4~20mA信号控制,它通过双连杆带动煤气及空气管道上的两个蝶阀比例调节,控制火焰大小。
加热罩上还设有两个煤气压力开关,分别检测煤气压力上、下限。
3.3.4每个炉台配有现场执行器电磁阀3台(供气阀1,排气阀1,冷却阀1)手阀限位开关2台(供气手阀限位1,抽真空手阀限位1),循环风机1台,加热罩助燃风机1台及冷却罩冷却风机2台为2炉台共用。
真空泵4台(1、2组炉1台,3、4组炉1台,5、6组炉1台,7组炉1台),每个真空泵带有电磁阀1个,抽水泵4台为7组炉公用。
3.3.5煤气主管道设有孔板1台,配套三阀组及压力变送器一套,检测煤气流量。
4、软件
4.1下位仪表软件
4.1.1AI-808P和AI-708仪表
仪表软件完成该仪表上各工业过程点的实时采样,模数转换处理,并进行系列报警检测。
仪表固化有一套标准算法,可由用户自行选择。
软件还支持实时网络传送功能。
4.1.2SIMATICS7-300(PLC)
根据工艺流程顺序控制要求进行梯形图编程
4.2上位机软件
上位机软件,采用通用工控组态软件MCGS。
它运行于中文Windows视窗,通过图形用户界面,将各种煤体一体化,使访问大量信息更容易,包括图形、动画、文本和声音信息。
用户通过屏幕上表示的实时过程图形,可以对整个生产过程进行集中监视、管理。
4.2.1软件组成
4.2.1.1画面制作系统——应用开发环境
用于建立图形显示、动画连接、定义数据库及建立与下位工业控制器、I/O服务程序的连接。
4.1.1.2画面运行系统——实时运行系统
用于显示由画面制作系统建立的图形画面。
4.2.2软件功能
4.2.2.1监视功能
动态显示工况图
动态显示工艺曲线图
仪表参数显示
故障报警显示和音响
实时趋势和历史趋势
操作提示
4.2.2.2管理功能
历史曲线显示和打印
随机打印数据、曲线、图形等。
5、正常运行状态流程说明
5.1工艺流程顺序控制
5.1.1工艺流程(操作顺序)(带罩冷却)
1.(手动)装料2.(手动)扣内罩(开关信号)3.(手动)工艺方式选择,保温时间设定4.(手动)PLC程序复位,自动启动5.(手
动)内罩锁紧6.(手动)锁紧信号7.(手动)抽真空手阀打开(开关信号)8.一次抽真空(压力信号)9.(手动)抽真空手阀关闭(开关信号)10.炉台密封合格11.(手动)充保护气手阀开(开关信号)12.(手动)罩加热罩(开关信号)13.(手动)连接插头14.(手动)插头接好确认(开关信号)15.助燃风机启动16.吹扫外罩(5分钟)17.循环风机低速启动18.保护气压力合格19.点火、加热20.温度300℃,循环风机高速启动21.继续加热(内罩温度到)22.保温开始23.保温结束24.停止烧嘴燃烧25.助燃风机继续运转,当温度(内罩)降至500℃26.停助燃风机27.(手动)去加热罩28.(手动)吊扣冷却罩29.关废气阀30.(手动)连接插头31.(手动)插头接好确认32.风冷开始33.关冷却风机、循环风机低速运转(300℃)34.喷水冷却35.冷却温度到(冷却结束)36.停喷冷却水37.(手动)关保护气手阀38.(手动)开抽真空手阀39.二次抽真空40.充空气41.停循环风机42.(手动)去冷却罩43.(手动)松内罩44.(手动)吊内罩45.(手动)卸料46.(手动)清理炉座47.(手动)装料
5.1.2不带罩冷却:
去掉25步,其余与带罩冷却操作顺序相同。
5.1.3PLC自动控制
系统的正常运行由PLC接5.1.1工艺流程自动执行。
5.2运行中的联锁
5.2.1送气操作中的联锁
5.2.1.1不合内罩,送气操作不能进行。
5.2.1.2手动阀位组合错误或不符合流程要求,电磁阀及真空泵都不能动作。
5.2.2退火过程中的联锁
5.2.2.1未正常供气,退火过程不能进行。
5.2.2.2加热罩未合,加热过程不能进行。
5.2.2.3未进行吹扫,加热过程不能进行。
5.2.2.4冷却罩未合,水冷却过程不能进行。
5.2.2.5风冷与水冷互锁,不能同时进行。
5.2.2.6抽水泵有高低水位控制,高液位开示,低液位停泵。
5.2.2.7发生以下情况之一,发出声光报警,严重时停止加热。
炉压低;加热罩超温;内罩超温;冷却水压力低;助燃风机故障;循环风机故障。
5.3正常工作流程光信息
正常工作流程由PLC柜中部绿色LED信号灯指示,其左部分2、3、4排及右部分2、3、4排分别表示1#、2#炉台。
包括抽真空过程、抽真空达标、充保护气、排废气、加热过程、加热结束、冷却过程、冷却结束、吹扫指示共9个。
5.4操作提示报警信号,每套炉有10个:
1#、2#真空达标;1#、2#充气达标;1#、2#锁紧、1#、2#保温结束;1#、2#冷却结束。
6、控制柜运行前检查及开机
首先检查各柜外部电气接线有无异常,接头是否松脱,所有柜面板上转换开关全部置“停”位。
6.1电源柜
6.1.1如电源柜上口有电,并且电压转换开关SA1不在停位,则电压表指示电源电压。
6.1.2在确认断路器断开情况下,合上刀开关DK1。
6.1.3按下储能按钮SB1,储能指示灯HG1亮,按下合闸按钮,断路器OQSO合上后,合闸指示灯HR1亮,按下分闸按钮,断路器OQSO断开。
6.2补偿柜
6.2.1接通刀开关
6.2.2旋转开关置自动,仪表根据互器LH4信号,自动控制投入电容器组数。
6.2.3旋转开关置手动,手动控制投入电容器组数。
6.2.4投入后,电容器对应指示灯亮。
6.3风机控制柜(以第一组风机柜为例)(需与公用柜及PLC柜配合)
6.3.1接通柜内1#、2#循环风机、助燃内机及冷却风机的电源空气开关1QS1、1QS2、1QS3、1QS4,对应电源指示灯1RD1、1RD4、1RD7、1RD9亮。
6.3.2接通柜内控制电源空气开关1QS5、1QS6,如已选择纯手动工作(在PLC柜选择),则纯手动指示灯亮。
6.3.3在纯手动工作时,1#循环风机手动高/低速转换开关1LA1置低速,循环风机低速运转,低速指示灯1RD2亮;1LA1置高速,循环风机先低速启动,然后自动转高速,高速指示灯亮1RD3亮。
6.3.4纯手动工作时,2#循环风机手动高/低速转换开关1LA2置低速,循环风机低速运转,低速指示灯1RD5亮,1LA2置高速,循环风机先低速启动,然后自动转高速,高速指示灯亮1RD6亮。
6.3.5纯手动工作,冷却风机转换开关1LA3置启动,冷却风机运行,冷却风机运行指示灯1RD8亮。
6.3.6纯手动工作,助燃风机转换开关1LA4置启动,助燃风机运行,助燃风机运行指示灯1RD10亮。
6.3.7纯手动工作,1#真空泵转换开关8LA1置启动,真空泵运行。
6.3.8纯手动工作,喷淋水选择开关1LA5置1#或2#,1#水冷电磁阀或2#水冷电磁阀打开;1#充保护气选择开关1LA6置打开,1#充保护气电磁阀打开;2#充保护气选择开关1LA8置开,2#充保护气电磁阀打开;1#排气选择开关1LA7置开,1#排气电磁阀打开;2#排气选择开关1LA9置开,2#排气电磁阀打开。
6.4公用柜
6.4.1接通柜内总空开8QSO。
6.4.2接通柜内真空泵、抽水泵电源开关8QS1、8QS2、8QS3、8QS5、8QS6。
6.4.3接通控制电源空开8QS7,仪表8BT1有指示。
6.4.4在1#风机柜上1#真空泵转换开关8LA1置启动,真空泵运转,运行指示灯8RD2亮。
说明工作正常,然后置停止。
(本试验条件为:
工作在纯手动状态下)。
6.4.5抽水泵选择开关8LA7选1#或2#,抽水泵控制开关8LA5置手动,抽水泵运行,运行指示灯8RD10或8RD11亮,说明正常。
然后置停止位。
6.4.6抽水泵选择开关8LA8选3#或4#,抽水泵控制开关8LA6置手动,抽水泵运行,运行指示灯8RD16或8RD17亮,说明正常,然后置停止位。
6.4.7检查声光报警系统工作是否正常,按下“试验”按钮(8SB2)报警指示灯8RD19亮,电笛DD发声,旋转“消音”(8LA9)旋钮,电笛停止发声,报警灯依旧亮,按下“复位”(8SB1)按钮,报警灯灭,再将消音旋转钮旋回原位。
说明工作正常。
6.5PLC柜
6.5.1接通柜内总电源空开QF1,接通电源QF2,PLC上“RUN”指示灯亮。
6.5.2接通电源开关QF3、QF5,将手控/PLC控转换置手控,则风机柜上纯手动指示灯亮,将转换开关置PLC控。
6.5.3接通电源开关QF4,BT1~BT7共7台仪表均有指示。
6.5.4检查声光报警系统工作是否正常,正常时,无声光报警,按下“试行”按钮SB307,所有指示灯亮,同时发出声光报警(1HZ)。
放开“试灯“按钮”SB307,声光报警停止,指示灯灭,说明工作正常。
6.6现场操作箱(以1#炉台为例)
6.6.1面板所有手动转换开关置“停”位;
6.6.2接通电源开关SB401,电源指示灯H100亮;
6.6.3压下试灯按钮SB307,所有指示灯亮。
6.6.41#保护气阀选择开关SB109置“开启”,保护气电磁阀接通,1#送保护气灯H104亮,SB109置“关闭”,保护气电磁阀关闭。
6.6.51#排气阀选择开关SB110置“开启”,排气电磁阀接通,1#排气指示灯H105亮,SB110置“关闭”,排气电磁阀关闭。
6.6.6加热过程中“1#加热指示灯”H106亮,可按下手动加热急停按钮SB302停止加热。
其余操作箱运行前检查及开机同1#炉台操作箱类似,不另述;
控制柜与现场执行机构的分部联动调试,必须考虑内罩、加热罩、冷却罩限位联锁要求;
抽真空和送保护气、排气试验,必须正确协同操作真空手阀和保护气手阀。
6.7运行前控制柜仪表工作方式和初始参数设定:
仪表BT1~BT7处于停止状态
PLC柜上“1#手动—停—自动”及“2#手动—停—自动”开关置手动。
仪表BT1—BT7按参数表设定工艺要求的限幅值和报警值,参见表2。
表中除工艺设定的参数外,其它参数均不必再作修改,全部参数在运行中修改亦有效,设定方法请参考有关仪表说明书。
表2.仪表参数设定
设定对象
参数
参数取值
备注
BT1/BT3
HIAL
按工艺(保温温度+8)
内罩超温报警
LoAL
按工艺(保温温度-2)
内罩保温温度(保温开始)
dF
2.0
Ctrl
1
M5.P.t.ctl
整定确定,可按参数修改
Sn
0
oP1
4
ALP
2
CF
2
Addr
bAud
BT1/BT3
dl
run
10
C01
按工艺(保温温度)
t01
保温时间或9999
C02
按工艺(保温温度)
t02
-121
BT2/BT4
HIAL
9999
LoAL
300
dLAL
(SV-出炉温度)-dF-dF
dF
2
Ctrl
0
Sn
0
oP1
0
ALP
45
Addr
bAud
dl
SV
500+2
面板设定
BT5
HIAL
850-dF
加热罩高限850℃报警
LoAL
820-dF
加热罩超温820℃报警
dF
10
Ctrl
1
BT5
M5.P.t.ctl
整定确定,可按参数修改
Sn
0
oP1
4
ALP
1
CF
2
Addr
bAud
dl
run
10
C01
室温
t01
10
C02
800
加热罩加热温度
t02
9999
C03
800
t03
-121
BT6/BT7
HIAL
5(Kpa)
炉压上限
LoAL
1.0(Kpa)
炉压低报警
dLAL
98.5(Kpa)
真空
dF
0.5(Kpa)
Ctrl
0
Sn
33
oP1
0
BT6/BT7
ALP
45
Addr
bAud
dl
SV
3(Kpa)
炉压下限
6.8常规退火操作
正常退火运行由PLC自动执行。
人工干预仅仅是:
吊内罩、加热罩、冷却罩,对于抽真空、送气过程,操作相应的手阀,加热罩、冷却罩上插头的连接,内罩压紧。
6.8.1内罩锁紧,送气操作
6.8.1.1装料,扣内罩
6.8.1.2根据工艺要求在现场操作箱上设定工艺选择开关SB107(左边为带罩冷却,右边为不带罩冷却),电源开关置“开”,其它开关全部置“停止”。
6.8.1.3PLC柜上,“手动—停—自动”开关置“自动”,按复位按钮SB106,复位指示灯亮,PLC程序复位。
人工设定保温时间。
PLC柜上,按“自动启动”按钮SB104,复位指示灯灭,“自动”灯亮,自动流程执行。
6.8.1.4人工锁紧内罩。
锁紧后,按操作箱上“内罩夹紧”按钮确认。
6.8.1.51次抽真空:
人工打开对应炉台真空手阀,抽真空指示灯亮,真空达标后,真空达标指示灯亮,人工关断真空手阀;保压10分钟后,合格进入下一步;若不合格,密封不严灯亮,重新检查完毕后,重新按“内罩夹紧“按钮,又开始抽真空。
6.8.1.6送保护气:
打开充保护气手阀,充保护气电磁阀打开,充保护气指示灯亮,炉压达到3.5Kpa以上时,排气电磁阀找开,排气指示灯亮,炉压自动调整在2.5Kpa~5.5Kpa。
6.8.2加热过程操作
6.8.2.1扣加热罩,循环风机低速运转。
6.8.2.2人工连接助燃风机插头、加热罩热电偶插头,信号插头连接好后,打开煤气阀门,然后按操作箱上“助燃风机接好确认”按钮,助燃风机开始运行。
6.8.2.3吹扫过程:
PLC控制电动调节阀开到最大,吹扫5分钟,再使调节阀开至低火位置,等待点火,此过程“吹扫指示灯”亮。
6.8.2.4PLC控制烧嘴控制器点火,10个烧嘴顺序点火,1分钟点1个,点燃后,经过10分钟,电动调节阀改由加热罩仪表控制,按设定曲线升温、保温。
此过程“加热指示灯”亮。
6.8.2.5当内罩温度达到300℃时,循环风机由低速转为高速。
6.8.2.6保温结束,PLC控制烧嘴熄灭,“加热指示灯”灭,“加热结束”指示灯亮。
①带罩冷却:
烧嘴熄灭后,加热结束灯亮5秒后熄灭,冷却过程指示灯亮。
②不带罩冷却:
烧嘴熄灭后,加热结束灯亮,冷却罩罩上后(冷却罩限位信号),加热结束灯灭,冷却过程指示灯亮。
6.8.2.7内罩升温过程中,调节阀由加热罩温控仪表控制,当内罩升到设定保温温度时,调节阀改由内罩温控仪表控制。
6.8.3冷却过程操作
6.8.3.1助燃风机继续运转,调节阀由PLC控制开至最大,内罩温度降至500℃时,停助燃风机。
6.8.3.2人工取下加热罩各插头,去加热罩。
6.8.3.3扣冷却罩,人工连接冷却风