接岸上部结构施工方案.docx
《接岸上部结构施工方案.docx》由会员分享,可在线阅读,更多相关《接岸上部结构施工方案.docx(39页珍藏版)》请在冰豆网上搜索。
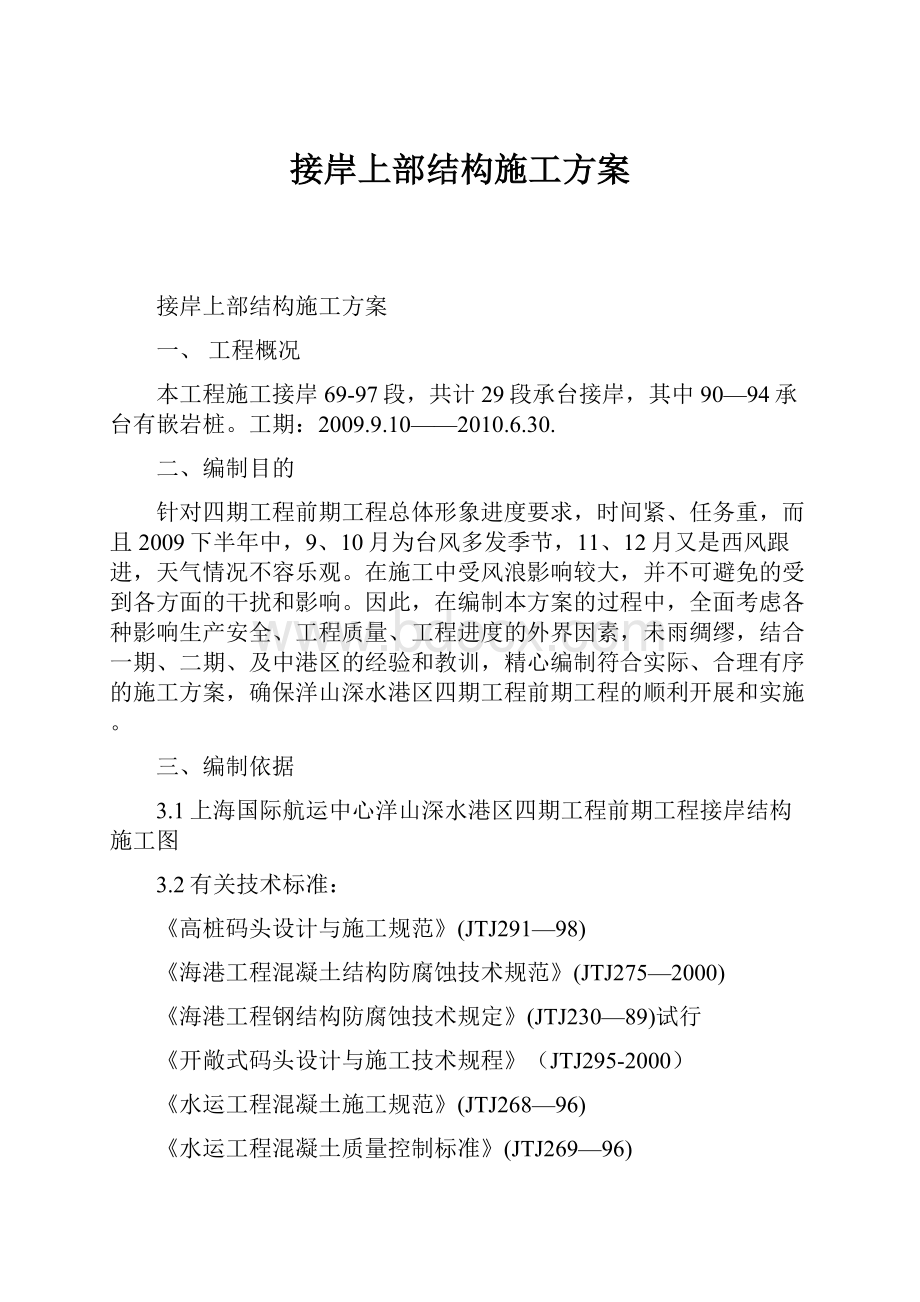
接岸上部结构施工方案
接岸上部结构施工方案
一、工程概况
本工程施工接岸69-97段,共计29段承台接岸,其中90—94承台有嵌岩桩。
工期:
2009.9.10——2010.6.30.
二、编制目的
针对四期工程前期工程总体形象进度要求,时间紧、任务重,而且2009下半年中,9、10月为台风多发季节,11、12月又是西风跟进,天气情况不容乐观。
在施工中受风浪影响较大,并不可避免的受到各方面的干扰和影响。
因此,在编制本方案的过程中,全面考虑各种影响生产安全、工程质量、工程进度的外界因素,未雨绸缪,结合一期、二期、及中港区的经验和教训,精心编制符合实际、合理有序的施工方案,确保洋山深水港区四期工程前期工程的顺利开展和实施。
三、编制依据
3.1上海国际航运中心洋山深水港区四期工程前期工程接岸结构施工图
3.2有关技术标准:
《高桩码头设计与施工规范》(JTJ291—98)
《海港工程混凝土结构防腐蚀技术规范》(JTJ275—2000)
《海港工程钢结构防腐蚀技术规定》(JTJ230—89)试行
《开敞式码头设计与施工技术规程》(JTJ295-2000)
《水运工程混凝土施工规范》(JTJ268—96)
《水运工程混凝土质量控制标准》(JTJ269—96)
《港口工程质量检验评定标准》(JTJ221—98)
《港口工程质量检验评定标准》(JTJ221—98局部修订)
《混凝土和钢筋混凝土施工规范》(GB50204一2002)
《钢筋焊接及验收规程》(JGJl8—2003)
《钢结构工程施工质量验收规范》(JGJl07—2003)
《钢结构工程施工及验收规范》(GB50205-2001)
《水运工程测量规范》(JTJ203-2001)
《海港水文规范》(JTJ213-98)
《水运工程混凝土试验规程》(JTJ270-98)
《港口设备安装工程质量检验评定标准》(JTJ244-95)
《镦粗直螺纹钢筋接头》(JG/T3057-99)
《建筑施工安全检查评分标准》(JGJ59-99)
《施工现场临时用电安全技术规范》(JGJ18-96)
3.3施工图设计交底及相关会议纪要
3.4国家或上海市颁布的其他法规、规范和标准
《建筑施工安全检查标准》(JGJ59—99)
《施工现场临时用电安全技术规范》(JGJl8—96)
四、接岸上部结构施工工艺流程及主要施工机械
4.1、主要施工流程
4.2拟投入的主要机械设备、测量设备计划
拟投入的主要施工机械表
序号
设备名称
型号规格
数量
国别场地
用途
备注
1
经纬仪
J2
2台
苏州一光
测量
2
自动安平水准仪
DSZ2
3台
苏州一光
测量
3
交流电焊机
200A
20台
中国
电焊
4
钢筋切断机
3台
中国
钢筋制作
5
钢筋弯曲机
3台
中国
钢筋制作
6
钢筋套丝机
1台
钢筋制作
7
木工电刨
4台
8
木工电钻
3台
中国
木工打眼
9
绞丝机
1台
中国
绞丝
10
电钻
2
中国
植筋
4.3、主要施工船舶机械
承台施工使用船舶机械
序号
船舶车辆
数量
用途
1
50T轮胎吊
1辆
装卸材料(钢材)及桩笼
2
10~20T超长车
1辆
路上运输(加工区至码头)
3
自航舶
2条
码头施工区域运输成型钢筋500T左右、承台钢筋绑札
4
1000T自航驳上配50T履带吊
1条
1条承重体系安装及前期密排桩桩笼,另条后期上承台钢筋及承重体系拆除(1000T浮吊)
5
运输船
2条
6
小吊机
1条
稳桩等(80T左右)
7
工作船
6条
上部结构施工及运输施工人员(20T左右)
五、主要分部分项主要施工方法
1、基桩加固
1.1、由于沉桩速度及上部结构与沉桩需要一段距离,确保桩基稳定性,沉桩后应及时进行基桩加固,使形成所沉桩的整体性。
1.2、基桩加固采用H型钢,先在承台板桩内壁上焊接一根4米长的H型钢,每处焊接,必须按规范、设计要求施工而且要垂直,焊接后承台板桩钢凳上及相应的斜顶桩、支撑桩上用水准仪测量加固H型钢的标高。
1.3、板桩与斜顶桩及支撑桩之间的加固型钢长度实测后在浮吊上先进行气割,后用浮吊吊至相应位置进行焊接,焊缝应饱满,保证焊缝长度,确保焊接质量,并须采用加劲板加固。
1.4、每个承台有4套H型钢加固体系,各板桩之间的加固视打桩情况在有缝的地方进行帮焊接,使整个稳桩系统有足够刚度、强度、稳定性,确保桩基稳定。
1.5、在整个稳桩过程中,使用气割电焊时,严禁烧坏+3.5m以下涂层。
2、桩顶处理
2.1、基桩加固后,用水准仪测设桩顶标高。
由于沉桩原因和人为因素,造成桩顶标高与实际标高有一定差距,高于设计标高需割除,低于设计标高太多需接桩。
2.2、割除时应注意对钢管桩涂层的保护,不能用氧气乙炔伤害设计标高以下的钢管桩涂层。
3、钢筋笼加工、运输、安装
3.1、板桩桩芯长度为4.9m,规格为Φ32,共42根;支撑桩桩芯长度为4.6m,规格为Φ28,共26根;斜顶桩桩芯长度为4.6m,规格为Φ25,共32根。
3.2、桩芯笼加工先在附近的钢码头进行焊接加工,加工时应钢筋笼重量较大,为防止钢筋笼吊装时扭曲变形,在桩笼内制3道Φ25衬箍,衬箍第一道距离底口700mm,其余@2000mm左右,桩笼主筋直接焊在定位衬箍上。
再进行箍筋绑扎。
焊接时确保主筋一条线,焊接牢固。
3.3、制作好的桩笼,在上口用4根Φ22焊接好吊点及搁置点,便于起吊安装、搁置。
桩芯底模直接焊在笼上,为确保安装顺利,底模根据桩口直径,每边缩小15mm。
3.4、利用制作桩笼主筋,作为底模吊筋。
桩芯砼8.12-13.88m3,约20.3-34.7T,底模采用三拼100×150mm搁栅,底板采用σ=30mm落叶松板。
吊筋拟定φ22,6点吊。
底板中间预留一个300×300mm孔洞(见附图),砼浇筑前用400×400mm板封牢。
这样便于桩芯水抽干净及底模检修。
3.5、桩芯反吊内力验算
N1、N2为吊筋螺杆的反力,按均布受力计算
N1=95×0.95×3.14×2.7×2.5=19.13T(Φ1900板桩)
N2=0.75×0.75×3.14×4×2.5=17.66T(Φ1900支撑桩)
若取Φ22螺杆
在N1处n=19.13÷11.3=1.69根
在N2处n=17.66÷11.3=1.56根
综上计算,并考虑受力对称及保险系数,桩芯反吊螺杆均采用6根Φ22螺杆均布,能满足要求。
3.6、桩芯笼制作好后,利用浮吊及运输船将钢筋笼运至现场进行安放,吊运过程应有专职指挥员在现场,防止钢筋笼脱落,如发现钢筋笼有变形等现象,应及时进行加固返修,等返修合格后方可进行安装。
钢筋加工区平面布置图见附图.
4、桩芯砼浇注
4.1、在H型钢加固好后,先安装板桩钢筋笼。
斜顶桩及支撑桩待第一次砼浇注完毕后再进行浇注。
4.2、浇注前,先将桩芯中的水抽除,抽除干净后人工将桩芯底板预留孔封闭。
4.3、因桩顶高度在潮水变动区域或,所以桩芯砼在高潮时要赶潮水施工,确保桩芯质量
4.4、浇注过程中,应避免砼产生离析现象。
砼泵管应深入钢管桩中,倾落高度小于2M。
在施工时宜乘低潮位浇筑砼。
因浇筑后潮位上涨,砼顶在海水面下,应及时用塑料薄膜封顶。
4.5、砼浇注后,应将桩顶的浮浆凿除,并用水清除干净。
5、承重体系安装
5.1承重扁担安装
5.1.1、由于斜顶桩上口不平整,先用水准仪抄平,用氧气乙炔将高处开口与低处相平。
5.1.2、在斜顶桩上焊接一四拼[40b槽钢扁担,扁担应与钢管桩焊接牢固,且扁担应水平。
5.1.3、反吊槽钢采用双拼[40b槽钢,共38对,分别在板桩两侧布置,
反吊螺丝选用φ25精轧螺纹钢,共76根,上、下各4个螺帽拧紧,螺栓与槽钢结合处用配套垫片
5.1.4、承重体系安装完,根据标高用2T左右手拉葫芦水平调平,抬高20mm预留量,确保承台高度达设计标高,在槽钢两侧用Φ32钢筋牵联所有承重槽钢,保其整个承重体系整体性和稳定性。
5.1.5、所有承重槽钢与桩壁接触都有固定橡皮或防撞板,确保涂层不受损伤。
5.1.6、承重体系布置图详见附图
5.1.7、承重体系主要材料表
主要承重体系材料/段
序号
名称
型号
数量
备注
合计
1
【40b四拼槽钢
4米长
4根
4.173T
58.403T
2
【40b双拼双排槽钢
12米长
8根
25.038T
3
【36b双拼槽钢
6米长
21根
13.473T
4
【36b双拼槽钢
7米长
21根
15.719T
5
Φ25精致螺纹钢
4米长
21根
精致螺纹钢下口开眼
4米长
21根
4.5米长
42根
6
配套垫片
84块
7
配套螺母
210个
8
100*150围囹料
4米长
245根
9
18厚多层板
1.83m*0.915m
186块
5.2、底板、搁栅
拟定搁栅采用100×150×4000mm落叶松,间距不大于300mm,用14#钢丝与承重槽钢绑牢。
在桩处加密搁栅,增加承载力,减少底模挠度。
底板拟定σ=18mm厚多层板,增加底板平整度,光洁度及减少底模拼缝,增其美观。
应底板标高为+3.50,受潮水影响时间较长,风浪冲击对底板破坏大,在底板铺设的同时加固底板及围囹料.
在底板铺设完后进行底模标高复核,轴线施放。
5.3、承台承重结构体系结构计算
1荷载计算
2围檩、搁栅自重:
q1=1.5KN/m2
2混凝土自重(以1m厚底板计算):
q2=25×1.0=25KN/m2
3施工荷载:
q3=2.5KN/m2
4振捣荷载:
q4=2.0KN/m2
施工总荷载:
q=q1+q2+q3+q4=31KN/m2
2搁栅计算
1计算简图:
采用落叶松木方,@400布置:
计算荷载:
q=31×0.4=12.4KN/m
2内力计算:
按照四等跨连续梁计算,l0=2000
查静力计算手册:
Mmax=-0.107×ql0=-0.107×12.4×22=-5.31KN·m
3、截面计算:
木材:
[δ]=17×0.9=15.3N/mm2
落叶松:
E=1000×0.85=8500N/mm2
W=Mmax/[δ]=5.31×106/15.3=347.1cm3
选用100×150木方:
W木=1/6(10×152)=375cm3>W=347.1cm3
可以满足
4、挠度验算:
查静力计算手册:
I=10×153/12=2812.5cm4
ymax=0.632ql04/(100EI)
=0.632×12.4×20004/(100×8500×2812.5×104)=8.3mm
允许挠度:
[y]=2000/200=10mm>ymax=8.3mm
3承重围檩计算
承重围檩分2部分计算:
海侧斜顶桩至板桩、岸侧支撑桩至板桩。
采用槽钢作为承重围檩:
[δ]=215N/mm2。
海侧斜顶桩至板桩部分:
1计算简图:
计算荷载:
q=31×1.75=54.3KN/m
2内力计算:
支座反力:
R1×2.5-54.3×4.92/2+54.3×1.12/2=0
R1=247.6KN
R2=78.2KN
支座弯矩M1=-156.4KN·m
M2=-32.9KN·m
跨中弯矩M中=54.3×(2.4+1.25)2/2-247.6×1.25=52.2KN·m
支座弯矩M1=-156.4KN·m最大
3截面计算:
W=156.4×106/215=727.4cm3
选用2[36b槽钢:
Wx=2×702.9=1405.8cm3>W=727.4cm3
可以满足
4挠度验算:
悬臂段挠度:
查表:
Ix=12654cm4
E=2.1×105N/mm2
ymax=ql04/(8EI)
=54.3×24004/[8×2.1×105×(12654×2)×104]=4.2mm
允许挠度:
[y]=2400/250=10mm>ymax=4.2mm
岸侧支撑桩至板桩
1计算简图:
最大间距布置在承台两端悬臂
计算荷载:
q=31×1.70=52.7KN/m
2内力计算:
支座反力:
R1×3.7-52.7×52/2+52.7×22/2=0
R1=149.6KN
R2=219.3KN
支座弯矩M1=-44.5KN·m
M2=-105.4KN·m
跨中弯矩M中=52.7×3.152/2-149.6×1.85=-15.3KN·m
支座弯矩M2最大
3截面计算:
W=105.4×106/215=490.2cm3
选用2[36b槽钢:
Wx=2×702.9=1405.8cm3>W=768.2cm3
可以满足
4挠度验算:
查表:
Ix=12654cm4
E=2.1×105N/mm2
跨中ymax=5ql04/(384EI)
=5×52.7×37004/[384×2.1×105×(12654×2)×104]=2.4mm
允许挠度:
[y]=3700/500=7mm>ymax=2.4mm
可以满足
5反吊钢筋计算
最大受力点R1=247.6KN
选用精轧螺纹钢:
fy=700N/mm2(抗拉强度为885N/mm2)
As=247.6×103/700=353.7mm2
选用Φ25精轧螺纹钢:
As=490.1mm2>353.7mm2
4主围檩计算
以岸侧主围檩进行计算,分有悬臂段和无悬臂段计算
有悬臂部分:
1计算简图:
F1=158.1KN
F2=199.9KN
F3=F7=167.1KN
F4=F5=F6=131.3KN
2内力计算
支座反力:
R1×6-F1×8.5-F2×6.85-F3×5.15-F4×4.05-F5×2.95-F6×1.85
-F7×0.85=0
R1=815.1KN
R2=271.0KN
悬臂弯矩M=-F1×2.5-F2×0.85=-565.2KN·m
跨中弯矩M中=F1×5.5+F2×3.85+F3×2.15+F4×1.05+F5×0.5-R1×3
=-243.4KN·m
悬臂弯矩最大
3截面计算
W=565.2×106/215=2629cm3
选用4[40b槽钢:
Wx=4×932.2=3729cm3>W=2629cm3
可以满足
4挠度验算
[40b槽钢I=18644.5cm4,A=83.05cm2
IX=18644.5+83.05×(40/2)2=51864.5cm4
悬臂段:
在F1=158.1KN作用下:
y1=F1l3/3EI=158.1×103×30003/3×2.1×105×(4×51864.5)×104
=3.3mm
在F2=199.9KN作用下
y2=F2b2l/6EI(3-b/l)
=199.9×103×8502×3000/[6×2.1×105×(4×51864.5)×104]×(3-850/3000)
=0.5mm
允许挠度[y]=3000/500=6mm>y1+y2=3.8mm
无悬臂部分:
1计算简图
F1=F5=167.1KN
F2=F3=F4=131.3KN
2内力计算
支座反力:
R1=R2=364.1KN
跨中弯矩M中=F1×2.15+F2×1.05+F2×0.5-R1×3=-529.5KN·m
3截面计算
W=-529.5×106/215=2463cm3
选用4[40b槽钢:
Wx=4×932.2=3729cm3>W=2463cm3
可以满足
4挠度验算
查表:
在F1、F4作用下(a1=850)
y1=F1a1(3l2-4a12)/24EI
=167.1×103×850×(3×60002-4×8502)/[24×2.1×105×(4×51864.5)×104]
=1.4mm
在F2、F3作用下(a2=1950)
y2=F2a2(3l2-4a22)/24EI
=131.3×103×1950×(3×60002-4×19502)/[24×2.1×105×(4×51864.5)×104]
=2.3mm
在F5作用下
y3=F5l3×48EI
=131.3×103×60003/48×2.1×105×(4×51864.5)×104
=1.4mm
允许挠度[y]=6000/500=12mm>y1+y2+y3=5.1mm
5板桩内H型钢立柱焊缝计算
HM型钢500×300(截面482×300)材质Q235
采用20mm角焊缝,荷载垂直焊缝长度方向
查表焊缝应力ffw=160N/mm2
焊缝有效厚度he=0.7×20=14mm
焊缝计算长度lw=(200-10)380mm
正面角焊缝强度设计增大系数βf=1.22
焊缝最大承载力N=βf×ffw×he×lw
=1.22×160×14×380=1038.5KN
根据承重围檩计算可知,单根HM型钢立柱焊缝承受荷载:
Nmax=31×6×[(1.1+1.25)+(1.3+1.85)]=1023KN<N=1038.5KN
可以满足,但考虑电焊质量的不稳定,在板桩靠海侧增加一个支点与HM型钢形成支撑。
5.4、考虑到施工进度,本工程共配备6套沉重槽钢,便于施工流水作业面形成,利于船舶排开。
6、第一次浇注钢筋绑扎、侧模支立
6.1、钢筋工程
6.1.1、钢筋采购
由于本工程的钢筋用量巨大,规格、品种繁多,力学指标不同,应根据设计要求和施工进度安排,应提前将钢筋计划上报总包单位,同时明确到货日期,以满足工程各不同施工阶段的需要,防止钢筋供应短缺,影响工程进度,做到有备无患。
6.1.2、钢筋加工
钢筋进入施工现场首先查验出厂质保单,并按规范要求的比例,进行有关力学和施工性能的测试,禁止不合格材料在工程中使用。
钢筋进场后,按不同钢种等级及规格分别堆放,并且按贯标要求悬挂标识牌。
钢筋在堆放过程中注意避免锈蚀和污染。
在使用前如有油渍和局部锈蚀应予清除,锈蚀严重严禁使用。
认真分析图纸,严格按图落料及配制钢筋,注意钢筋在弯曲时的伸量,防止断料过长造成不必要的浪费。
拼装时按设计图纸放大样,并考虑焊接变形和预留拱度。
拼装前,检查每根有焊接接头的钢筋,发现有焊接变形的及时调整。
拼装时,防止电焊引起的局部变形,在需要焊接的位置用锲型卡卡住,待所有焊接点卡好后,先在焊接两端电焊固定,然后进行焊缝施焊。
在钢筋进行弯钩、折曲、对焊或其他加工施工中应符合规范规定。
6.1.3、钢筋绑扎
钢筋加工基本在码头附近的钢码头进行加工后经运输船运输至施工现场,由于桩体偏位,主筋遇到桩体后要断开并弯曲64cm,需要根据实测进行加工,考虑到施工进度,另租用一1000T自航驳,在自航驳上进行现场加工。
钢筋绑扎首先将钢筋构成骨架,然后逐点进行绑扎。
扎钢筋时,扎丝应满足规范规定,并向内弯,确定无一扎丝头留在钢筋保护层中。
骨架需要焊接时,不同直径钢筋的中心线应在同一水平面上,为此较小直径的钢筋在焊接时,下面垫以厚度适当的钢板。
钢筋需要搭接时,无论是绑扎搭接,还是电焊搭接均应做到搭接形成的面与结构面平行,以确保钢筋保护层的实际厚度,满足设计和规范规定,搭接位置不宜处于结构受拉区。
施焊顺序为由中间向两端对称地进行,先焊骨架下部,后焊骨架侧面及上部,相邻的焊缝采用分区对称跳焊,以防止顺同一方向一次焊成,药皮做到随焊随敲,焊缝饱满,焊缝高度满足规范要求。
钢筋焊接点的位置严格按规范规定错开,同时按要求保证必要的搭接长度。
由于钢筋笼面积较大,在施工中可能有人员踩压,同时浇筑混凝土时的冲击力也可能造成钢筋混凝土骨架的变形,将视具体情况,合理设置架立钢筋。
保证钢筋保护层厚度的主要技术措施在于垫块的设置,在钢筋骨架绑扎完成,安装模板前,视构件尺寸、形状,合理设置垫块。
垫块的构造形式采用“倒锥形”:
厚度根据保护层厚度确定,以增加垫块与现浇混凝土的结合面的渗径长度,并在垫块背面予埋四组铅丝。
垫块混凝土为高性能混凝土,其设计强度在主体结构混凝土设计强度基础上增加一级。
垫块绑扎要求牢固,贴靠模板,可用手检查有无松动,并确保垫块表面洁净。
嵌岩桩区域桩顶以上部分钢筋在预留孔洞区域预留套丝接头,等嵌岩桩结束后再进行绑扎浇注。
承台钢筋翻样单及总吨位详见附图。
6.2模板工程
6.2.1模板拟定钢框胶合模板,委托专业厂家加工,钢框采用3mm厚,间距为250mm扁钢拼合形成,其优点是:
自重中等,拆装方便,防水性好,光滑无收缩,刚度好,不易产生弯曲变形,拆模后,砼观感较好。
6.2.2侧模设计参数:
底标高+3.50m,第一次浇注高度为1.0m。
6.2.3侧模的制作加固是承台成型及砼外观质量的关键环节。
侧模为底包墙形式,帽梁模板加固先竖夹料后横夹料,竖夹料用10×15㎝木方@600,横夹料采用5×10㎝方钢三道,模板下口用3cm×3cm三角条钉在底板上,防止模板进出,无法固定。
而且具有止浆作用,以防漏浆烂根。
为了更好地确保几何尺寸和模板顺直,侧模每2~3m处加对称斜撑,增加侧模稳定性。
(模板图详见附图)
6.2.4模板表面应整洁,脱模剂应涂刷均匀,且不得污染钢筋,模板上脱模剂采用机油加柴油(4:
1),其特点是光滑,遇水不化,不锈蚀不污染钢筋。
模板拆除后操作方便。
6.2.5砼浇筑过程中,加强对模板的沉降和变形观测,专人看模,一旦出现异常情况,应及时采取加固补救措施,以确保帽梁成型质量。
砼浇筑达48小时后进行模板拆除清理,派专人维护保养,如有损坏及时调换整修,便于下次周转使用。
6.2.6、嵌岩区域预留孔洞,具体详见附图。
7、第一次砼浇注(4.50m)
7.1、浇注前先将整个承台垃圾进行清理及板底冲洗干净。
由于承台面积较大,浇注前先用水准仪抄平并用红油漆做好标志,使浇注后比较平整。
7.2该混凝土为C45高性能砼,第一次浇注达到了312m³,在施工大体积时,为了减少砼在凝结过程中水泥散发出大量的水化热而形成内外温度差所产生砼裂缝,砼下料要分层下料,分层振捣,每层布料厚度不超过500mm,为确保砼质量及接缝质量,上、下层震动要仲入下层50mm~100mm为界,以防产生接缝线,确保砼一次性成型。
砼浇筑,振捣严格按照规范要求。
7.3砼浇筑时,保持四周模板顺直。
7.4砼浇筑完,待砼初凝前,对表面进行拉毛处理,增加同上二层砼接触面,四周保护层处压光拉毛处理。
防砼干缩裂缝。
7.5砼养护专人专职,养护时间视情况而定,一般不少于14天。
7.6拆模时间控制在砼浇筑完24小时以外,防止粘模。
8、拆除承重体系
8.1待砼达70%强度方能拆底模及承重体系。
8.2拆除承重体系时,安排专职安全员及吊机指挥员在现场,确保安全。
9、浇注支撑桩及斜顶桩桩芯笼安装及砼浇注
9.1、支撑桩桩芯参考板桩桩芯施工
9.2、斜顶桩桩芯施工
9.2.1、由于斜顶桩桩芯砼要浇注至-