模具毕业设计149止动杠杆冲压模设计.docx
《模具毕业设计149止动杠杆冲压模设计.docx》由会员分享,可在线阅读,更多相关《模具毕业设计149止动杠杆冲压模设计.docx(23页珍藏版)》请在冰豆网上搜索。
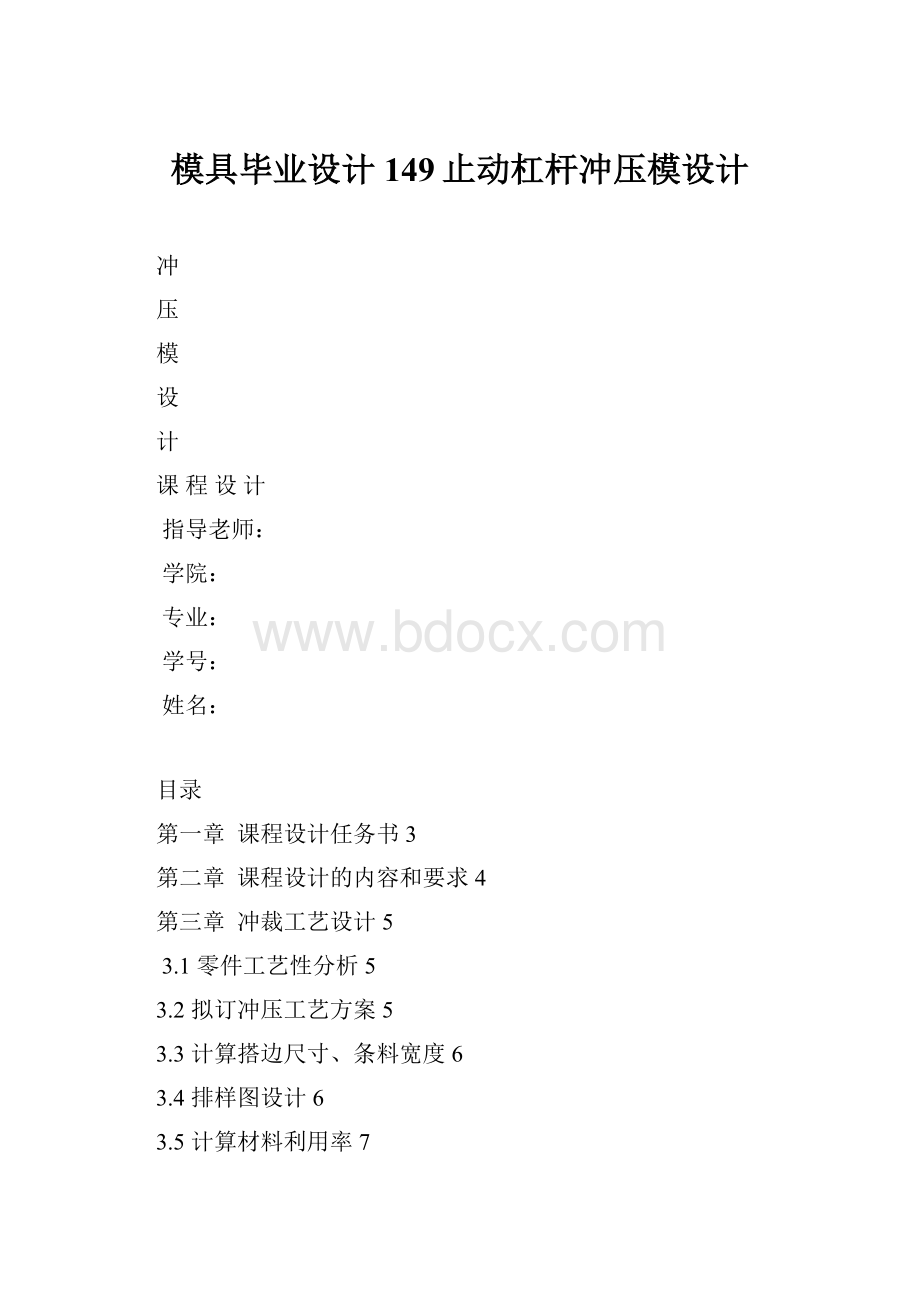
模具毕业设计149止动杠杆冲压模设计
冲
压
模
设
计
课程设计
指导老师:
学院:
专业:
学号:
姓名:
目录
第一章课程设计任务书3
第二章课程设计的内容和要求4
第三章冲裁工艺设计5
3.1零件工艺性分析5
3.2拟订冲压工艺方案5
3.3计算搭边尺寸、条料宽度6
3.4排样图设计6
3.5计算材料利用率7
第四章工艺尺寸计算9
4.1凸、凹模工作部分尺寸9
4.2冲压工艺力及机床吨位选择11
4.3确定压力中心13
第五章模具整体结构设计15
5.1模架的选择15
5.2定位零件的选择与设计16
5.3卸料与出件装置16
5.4联接与固定零件17
5.5模具零件的材料及热处理19
第六章模具工作零件结构设计20
6.1落料凹模的结构设计20
6.2凸凹模的结构设计21
6.3冲孔凸模的结构设计22
第七章课设心得与体会24
参考文献25
第一章“模具设计”课程设计任务书
姓名
邓家磊
专业班级
理工材料04-01
教研室主任
李树桢
题目
止动杠杆冲压模设计
指导教师
赵明娟
设计时间
2007年12月3日~12月21日(共3周)
设计地点
6-609
制品:
止动杠杆
材料:
铝L2
料厚:
3mm
数量:
100万件
课程设计提交的档案材料
1.设计计算说明书10000字
(A4幅面)1份
2.模具装配图
(1#图纸)1张
3.模具工作零件图
(2#或3#图纸)3张
4.上述材料电子文档
基本要求及设计步骤建议:
1、冲裁工艺设计:
对制件的结构、尺寸、精度、数量、材质等要素进行分析,初步确定制件的冲裁工艺,计算搭边尺寸、毛坯尺寸,确定排样图(绘在总装图上);
2、模具结构方案设计;根据冲裁工艺方案,初步确定模具结构方案和坯料导向、定位方式;
3、计算冲裁力,初步选择冲压设备;了解其行程、吨位、容模尺寸等有关技术参数;
4、计算卸料力,确定卸料方案及卸料元件的规格、尺寸;
5、计算并确定冲裁间隙继而确定凸模、凹模等主要工作零件的尺寸、结构形式;选择凸模、凹模或凸凹模进行强度、刚度的计算并校核;
6、协调模具各零件的结构、尺寸,完善导料、定位等辅助功能件结构及尺寸设计;
7、绘制模具总装配图:
1)、考虑采用“半剖法”表示上模使用中的两个极限位置;
2)、按装配图要求标注尺寸及配合性质、技术要求等;
3)、零件标号无遗漏;明细表内容详实、规范;
4)、制图遵照国家标准;排样图按习惯绘在总装图的右上角或适当位置。
8、绘制凸模、凹模零件图,尺寸、粗糙度标注齐全;
9、编写设计说明书一份,要求内容详实,措词准确,具有较好的可读性;
10、其它详见《“模具设计”课程设计指导书》。
机电工程学院材料成型及控制工程教研室2007.12
第二章课程设计的内容和要求
一、课程设计教学目的及基本要求
1.了解并掌握模具设计的一般方法,具备初步的独立设计能力;
2.初步掌握冲裁模的具体设计思想及设计过程;
3.提高综合运用所学的理论知识独立分析和解决问题的能力;
4.为工程实际的模具设计打下良好基础。
二、课程设计内容及安排
1.设计内容:
止动杠杆零件的冲压模
2.具体任务:
根据经教研室审批的设计任务书所制定的制件,设计一套止动杠杆零件的冲压模。
具体要求如下:
1)制件冲压工艺设计
2)模具结构方案设计
3)模具工作零件设计计算(含:
误差分析,强度、刚度计算并校核)
4)模具整体结构设计
5)成型设备选择
6)模具总装图绘制(1#)。
须符合下述要求
A.考虑采用“半剖法”表示上模使用中的两个极限位置;
B.按装配图要求标注尺寸及配合性质、技术要求等;
C.零件标号无遗漏;明细表内容详实、规范;
D.制图遵照国家标准;排样图按习惯绘在总装图的右上角或适当位置。
7)绘制凸模、凹模零件图(2#或3#),尺寸、粗糙度标注齐全;
8)编写设计说明书一份,要求内容详实,措词准确,具有较好的可读性;说明书按目录、设计任务书及产品图、零件工艺性分析、冲压零件工艺方案的拟订、模具类型及结构形式的选择、排样方式,材料利用率的计算、冲裁力的计算、压力中心的确定、模具主要零部件的确定(选择、设计和必要的计算)、压力机的选择、参考资料等。
3.计划进度:
第1周:
接受并消化设计任务,搜集资料,冲压工艺及模具结构方案设计;
第2周:
模具工作零件设计,绘制装配图、凸模、凹模或凸凹零件图;
第3周:
编写计算说明书;答辩。
第三章冲裁工艺设计
3.1零件工艺性分析
这次冲压模设计课程设计的制品是止动杠杆零件,该零件的材料为铝L2,厚度为3mm,产量为100万件。
该零件形状较简单,且在一个方向上对称。
除孔φ200-0.2mm有公差要求(IT12)外,其余尺寸均为自由公差,按IT14计算。
通过一般冲压均能满足其尺寸精度要求。
3.2拟订冲压工艺方案
查文献一P42.表2-10凸、凹模最小壁厚a:
φ9mm和φ4mm孔边距外轮廓的距离远大于凸、凹模允许的最小壁厚,故可以考虑采用复合冲压工艺,无凸、凹模强度之忧。
下面讨论几种可供选择的冲压工艺方案。
该零件包括落料、冲孔两个基本工序,可用以下3种工艺方案:
方案一:
先落料,后冲孔,采用单工序模生产;
方案二:
落料—冲孔复合冲压,采用复合模生产;
方案三:
冲孔—落料连续冲压,采用级进模生产。
方案一模具结构简单,但需要两道工序两套模具,生产效率较低,难以满足该零件的产量。
方案二只需要一套模具,冲压件的形位精度和尺寸精度易于保证,且生产效率也高。
尽管模具结构较方案一复杂一点,但由于零件的几何形状较简单且对称,模具制造并不困难。
方案三也只需要一套模具,生产效率也很高,但零件的冲压精度较复合模的低,欲保证冲压件的形位精度,需要在模具上设置导正销导正,故其模具结构较复合模相应复杂些。
通过以上3种方案的分析比较,对该件冲压生产以采用方案2为佳。
3.3计算搭边尺寸、条料宽度
查文献一P26.表2-7搭边a和a1的数值(低碳钢)对于材料厚度t=3mm,条料边长L>50mm,查得工件间a1=2.5mm,沿边a=2.8mm。
对于材料为铝的制件,需要将查得的数值乘以1.3—1.4,所以取该零件的搭边a=3.7mm,a1=3.3mm。
在确定了搭边值之后就可以确定条料的宽度,为了保证送料顺利,可以考虑条料的单向(负向)公差,其计算公式为B=D+2a+Δ
式中B为条料宽度的基本尺寸(mm);D为工件在宽度方向的尺寸(mm),在这里D=92mm;a为侧搭边的最小值(mm),由刚刚的取值可知a=3.7;Δ为条料宽度的单向(负向)公差(mm),考虑到计算的方便在此取Δ=0。
所以本课设的零件的条料宽度为:
B=D+2a+Δ=92+2×3.7+0=99.4mm。
3.4排样图设计
考虑到该零件的形状结构特征,宜选择有废料排样方法。
沿工件全部外形冲裁,工件四周都留有搭边。
也正因为有搭边,所以可以由搭边来补偿误差,因而可以保证冲裁件的精度和质量,冲模的寿命也较高。
但这样致使材料的利用率比较低。
另外由于工件的特殊形状,导致材料利用率低是必然的。
在这次课设中对排样的型式进行了几种比较(统一取条料的长度为1000mm)。
一种是直排,材料的利用率为35.6%(关于材料利用率计算的问题请见3-5节)。
而采用对头直排的材料利用率也仅为38.45%,而且这种排样型式使得模具尺寸增大,需要隔一个冲裁一个,一条料冲完还要调回头再冲一次,降低生产率,且对操作者来说也不方便。
还有使得挡料销过远。
综合考虑采用对头直排对模具设计并没有起到什么明显的作用,且材料利用率也没有提高多少。
所以这里依然选择直排。
具体排样图如图3-1所示:
图3-1排样图
3.5计算材料利用率
由于该工件的尺寸比较多且是由几个规则的几何图形构成,所以在计算材料的时候需要调入零件图(如图3-2所示),对零件图进行详细的尺寸计算。
该零件的材料利用率通过冲裁件实际面积与板料面积之比来表示。
其计算公式为η=(nA)/(LB)×100%.其中n为一张板料上的冲裁件的总数目(n=1000/39.3=25.45取25);A为一个冲裁件的实际面积;L为板料总长(L=1000mm);B为板料宽(B=99.4mm)。
下面计算一个冲裁件的面积。
图3-2零件图
由零件凸可得:
Saj=0.5πR2=0.5×3.14×52=39.27mm2;
Sabij=Lab*Laj=30.033×10=300.33mm2;
Sbchi=5×20-0.5×3.14×52=60.73mm2;
Scdgh=2[0.5×10×14.967+0.5×12×13.416+(104.441°×3.14×182/360°)]=901.262mm2;
Sdefg=Lde*Ldg=11.584×24=278.016mm2;
Sef=0.5πR2=0.5×3.14×122=226.1946mm2;
所以工件实际面积为
S工件=(39.27+300.33+60.73+901.262+278.016+226.1946)-π(22+102+4.52)=1415.4597mm2.
S原材料=1000×99.4=99400mm2.
因此材料的利用率为:
η=(nA)/(LB)×100%=(25×1415.4597/99400)×100%=35.6%
第四章工艺尺寸计算
4.1凸、凹模工作部分尺寸
一、确定凸、凹模间隙及制造公差
查文献一P17.表2-2得凸、凹模间隙Zmin=0.14mm,Zmax=0.20mm.若凸、凹模制造公差按IT8级精度选取。
对于冲φ4mm的孔,δ凸=δ凹=0.020mm(查文献一P20.表2-4);
对于冲φ9mm的孔,δ凸=δ凹=0.020mm;
对于冲φ20mm的孔,δ凸=0.020mm,δ凹=0.025mm;
对于落料φ10mm以及10mm,δ凸=δ凹=0.020mm;
对于落料φ24mm以及24mm,δ凸=0.020mm,δ凹=0.025mm;
对于落料φ36mm,δ凸=0.020mm,δ凹=0.030mm;
对于落料92mm,δ凸=0.025mm,δ凹=0.035mm.
由于凸、凹模均满足|δ凸|+|δ凹|≤Zmax-Zmin条件,故可采用凸、凹模分开加工法。
二、凸、凹模工作部分尺寸
⑴落料端部直径φ10mm:
D凹=(D-xΔ)0+δ凹=(10-0.5×0.36)0+0.020=9.820+0.020mm;
D凸=(D-xΔ-Zmin)0-δ凸=(9.82-0.14)0-0.020=9.680-0.020mm;
式中,根据课设题目给出的条件,制件精度为IT14级,取x=0.5,Δ=0.36mm.
⑵落料端部直径φ24mm:
D凹=(D-xΔ)0+δ凹=(24-0.5×0.52)0+0.025=23.740+0.025mm;
D凸=(D-xΔ-Zmin)0-δ凸=(23.74-0.14)0-0.020=23.600-0.020mm;
式中,根据课设题目给出的条件,制件精度为IT14级,取x=0.5,Δ=0.52mm.
⑶落料中部直径φ36mm:
D凹=(D-xΔ)0+δ凹=(36-0.5×0.62)0+0.030=35.690+0.030mm;
D凸=(D-xΔ-Zmin)0-δ凸=(35.69-0.14)0-0.020=35.550-0.020mm;
式中,根据课设题目给出的条件,制件精度为IT14级,取x=0.5,Δ=0.62mm.
⑷落料宽度92mm:
D凹=(D-xΔ)0+δ凹=(92-0.5×0.87)0+0.035=91.5650+0.035mm;
D凸=(D-xΔ-Zmin)0-δ凸=(91.565-0.14)0-0.025=91.4150-0.025mm;
式中,根据课设题目给出的条件,制件精度为IT14级,取x=0.5,Δ=0.87mm.
⑸落料中部宽度10mm:
A凹=9.820+0.020mm,A凸=9.680-0.020mm;
⑹落料中部宽度24mm:
A凹=23.740+0.025mm,A凸=23.600-0.020mm;
⑺冲孔φ4mm:
d凸=(d+xΔ)0-δ凸=(4+0.5×0.30)0-0.020=4.150-0.020mm,
d凹=(d+xΔ+Zmin)0+δ凹=(4.15+0.14)0+0.020=4.290+0.020mm;
式中,根据课设题目给出的条件,制件精度为IT14级,取x=0.5,Δ=0.30mm.
⑻冲孔φ20mm:
d凸=(d+xΔ)0-δ凸=(20+0.75×0.20)0-0.020=20.150-0.020mm,
d凹=(d+xΔ+Zmin)0+δ凹=(20.15+0.14)0+0.025=20.190+0.025mm;
式中,根据课设题目给出的条件,制件精度为IT12级,取x=0.75,Δ=0.20mm.
⑼冲孔φ9mm:
d凸=(d+xΔ)0-δ凸=(9+0.5×0.36)0-0.020=9.180-0.020mm,
d凹=(d+xΔ+Zmin)0+δ凹=(9.18+0.14)0+0.020=9.320+0.020mm;
式中,根据课设题目给出的条件,制件精度为IT14级,取x=0.5,Δ=0.36mm.
⑽孔间距50mm:
Ld=(Lmin+0.5Δ)±0.125Δ=(50+0.5×0.62)±0.125×0.62
=50.31±0.0775mm
式中,根据课设题目给出的条件,制件精度为IT14级,Δ=0.62mm.
⑾孔间距25mm:
Ld=(Lmin+0.5Δ)±0.125Δ=(25+0.5×0.52)±0.125×0.52
=25.26±0.065mm
式中,根据课设题目给出的条件,制件精度为IT14级,Δ=0.52mm.
4.2冲压工艺力及机床吨位选择
一、落料冲裁力的计算:
落料周长的计算:
Laj=πR=3.14×5=15.7mm,
Lab+Lde=Lji+Lgf=50+25-5-14.967-13.416=41.617mm,
Lcd=Lgh=32.81mm,Lbc+Lhi=15.7mm,
Lef=πR=3.14×12=37.68mm,
所以工件总周长为:
L落料=217.97mm
下面计算落料冲裁力F落料:
由公式F=KLtτ(K为修正系数,一般取K=1.3;t为板料厚度;τ为材料的抗剪强度)可得:
F落料=1.3×217.97×3×78=66.31KN
式中,查文献二P503.表8-9得铝L2的抗剪强度为78MPa。
二、冲孔冲裁力的计算
冲孔周长为L=2π(2+10+4.5)=33π=103.67mm
所以冲孔冲裁力F冲孔=KLtτ=1.3×103.67×3×78=31.54KN
三、计算卸料力
由公式得卸料力F3=K1F落料=0.05×66.31=3.32KN
式中卸料系数K1值可由文献一P24.表2-5查得这里的K1=0.05.
四、计算推料力
由公式得推料力F4=nK2F冲孔=4×0.05×31.54=6.31KN
式中卸料系数K1值可由文献一P24.表2-5查得这里的K1=0.05,n为卡在凹模内的冲孔废料数目,这里取n=4.
考虑到该零件较厚,其平直度要求不严,从操作方便出发,采用落料冲孔复合模正装结构及弹性卸料和下出料(冲孔废料)方式,则冲压总工艺力F为:
F=F落料+F冲孔+F3+F4=66.31+31.54+3.32+6.31=107.48KN
从满足冲压工艺的角度看,查文献二P543.表9-3开式压力机规格
可选用160KN开式压力机。
工作台尺寸为450*300mm,模柄孔尺寸φ30*50mm。
4.3确定压力中心
工件的压力重心计算如下所示:
(由于该零件在此坐标里关于y=18对称,所以在计算工件重心坐标时可不用计算y方向的重心坐标)
将工件轮廓分为13段,各段的长度为:
L1=15.71mm,L2=30.033mm,L3=7.854mm,L4=32.81mm,
L5=11.584mm,L6=37.70mm,L7=11.584mm,L8=32.81mm,
L9=7.854mm,L10=30.033mm,L11=12.566mm,L12=62.83mm,
L13=28.27mm.
则L总=L1+L2+L3+L4+L5+L6+L7+L8+L9+L10+L11+L12+L13=321.64mm.
各段的重心:
直线段的重心在线段的中心点,圆弧L1,L3,L6,L9的重心按下式决定,Z=Rsinα/(πα/180°)=57.29Rsinα/α=Rb/s.式中b为弦长,s为弧长,R为圆弧半径,Z为这段圆弧的重心到圆心的距离。
对于圆弧L1:
b=10mm,s=πR=15.71mm,
所以Z1=5×10/15.71=3.18mm,转化为x坐标轴方向时:
x1=1.19.
同理可得其它圆弧的重心坐标值为:
X3=39.533,X6=87.64X9=39.533
三个圆孔的重心即为圆心坐标,所以X11=5,X12=55X13=80
四条直线段的重心即为线段中点,所以X2=20.03X5=74.21
X7=74.21X10=20.03。
综合以上分析计算代入文献二P48.式2-1可得压力重心的坐标为:
X0=(15.71×1.19+30.033×20.03+7.854×39.533+32.81×53.9+11.584×74.21+37.7×87.64+11.584×74.21+32.81×53.9+7.854×39.533+30.033×20.03+12.566×5+62.83×55+28.27×80)/321.64=50.3144
考虑计算的误差等影响因素,认为该工件的压力重心为X=50,Y=18。
第五章模具整体结构设计
5.1模架的选择
根据零件结构以及操作的方便等因素考虑可以选择后侧滑动导柱导套标准模架。
在实际生产中,凹模的轮廓尺寸通常根据冲裁件尺寸和板料厚度,凭经验概略地加以计算。
由工件最大外形尺寸(92mm)及一定的凹模壁厚。
按文献一P41.经验公式得到:
凹模厚度H=Kb(≥15mm);凹模壁厚C=(1.5—2.0)H(≥30—40mm);式中,b表示冲裁件最大外形尺寸,K为一系数,考虑坯料厚度的影响,其值查阅文献一P41.表2-9系数K值。
在这里b=92mm,查表可得这里系数K取0.35。
所以H=0.35×92=32.2mm取H=35mm.因此凹模壁厚C=(1.5—2.0)H,取C=60mm.所以现在可以确定凹模周界了。
L=b+2C=92+2×60=212mm取标准L=250mm;B=36+2C=36+2*60=156mm取标准B=160mm。
据此按标准确定选择标准模架为:
上模座:
250×160×45HT200
下模座:
250×160×50HT200
导柱:
32×16020钢渗碳58—62HRC
导套:
32×105×4320钢渗碳HRC58—62
闭合高度:
最小200mm,最大240mm.
5.2定位零件的选择与设计
冲模的定位装置及零件的作用是保证材料的正确送进及在冲模中的正确位置,以保证冲压件的质量及冲压生产的顺利进行。
由于这里使用的是条料,所以在模具中的定位有两个内容,一是在送料方向上的定位,用来控制送料的进距,也就是挡料销。
二是在与送料方向垂直的方向上的定位。
挡料销分为固定挡料销和活动挡料销,因为定位销距离凹模孔比较远,且凹模具有足够的强度,所以这里选择固定挡料销,装在落料凹模上。
采用闭式刚性卸料装置起到在送料方向垂直的方向上的定位,这样做可以使模具结构简单,且可以保证前后工序相对位置的精度和对工件内孔与外缘的位置精度。
5.3卸料与出件装置
一、卸料装置
卸料装置分为刚性卸料装置和弹性卸料装置两种形式,这里考虑到冲裁件的材料厚度,制件要求平整的复合模等因素选择刚性卸料装置。
因为用的是正装复合模,所以刚性卸料装置的固定卸料板装在下模上。
这种装置的推件力大而可靠。
这样使得操作方便,工件质量较好。
二、出件装置
考虑出件的方便与操作安全,可选择弹性出件装置,装于下模,顶件力由装在下模板底部的弹性缓冲器提供,由弹性元件(橡皮)推动推板,再推动顶块而出件。
这种装置除有顶出工件的作用外,还可压平工件。
此装置亦可用于卸料。
5.4联接与固定零件
一、模柄
模具的上部分通过模柄联接固定在冲床滑块上。
这里选用凸缘模柄B型。
通过4颗紧固螺钉与上模板联接固定。
祥见文献二P623.
表10-49(GB2862.3-81)
二、凸模固定板与垫板
用凸模固定板将凸模联接固定在模板的正确位置上。
凸模固定板有圆形和矩形两种,这里考虑整体结构选用矩形,其平面尺寸除保证能安装凸模外,还能够正确的安装定位销钉和紧固螺钉,其厚度一般取等于凹模厚度的60%—80%。
这里取25mm。
固定板与凸模之间采用过渡配合,压装后将凸模尾部与固定板一起磨平。
垫板的作用是分散凸模传来的力,防止模板被挤压损伤。
垫板厚度一般为6—12mm,这里取10mm。
垫板的材料选为45钢。
最终,得到止动杠杆冲裁件模具的总装配图如图5-4示:
图5-4止动杠杆正装复合模总装配图
5.5模具零件的材料及热处理
根据前面的分析与标准的选择,现将止动杠杆正装复合模具中用的一些零件的名称、国家标准、材料以及热处理方式列表如表5-1所示:
止动杠杆正装复合模零件的材料及热处理
名称
标准
材料
热处理
垫板
Q235
固定板
Q235
垫块
Q235
落料凹模
Cr12
HRC58-62
销钉
GB119-76
35
HRC28-38
冲孔凸模
GB2863.2-81
T10A
HRC56-60,尾部回火HRC40-50
导柱
GB2861.2-81
20
淬火HRC58-62
上模座
GB2855.5-81
HT200
下模座
GB2855.6-81
HT200
导套
GB2861.6-81
20
淬火HRC58-62
刚性卸料板
Q235
推杆
45
HRC43-48
模柄
GB2862.1-81
A3
打杆
45
HRC43-48
打板
45
凸凹模
Cr12
HRC58-62
顶板
GB2867.4-81
45
HRC43-48
螺钉
GB5782-66
Q235
表面氧化或镀锌钝化
挡料销
GB2866.11-81
45
HRC43-48
表5-1零件材料及其热处理
第六章模具工作零件结构设计
6.1落料凹模的结构设计
凹模的推荐材料为9Mn2V、T10A、Cr6WV、Cr12,热处理硬度为HRC58-62。
这里选择Cr12。
凹模的轮廓尺寸,因结构型式不一,受力状态各不相同,目前还不能用理论计算方法确定,在生产中,通常根据冲裁件尺寸和板料厚度,凭经验概略地加以计算。