工厂珍典精益生产实施方案.pptx
《工厂珍典精益生产实施方案.pptx》由会员分享,可在线阅读,更多相关《工厂珍典精益生产实施方案.pptx(62页珍藏版)》请在冰豆网上搜索。
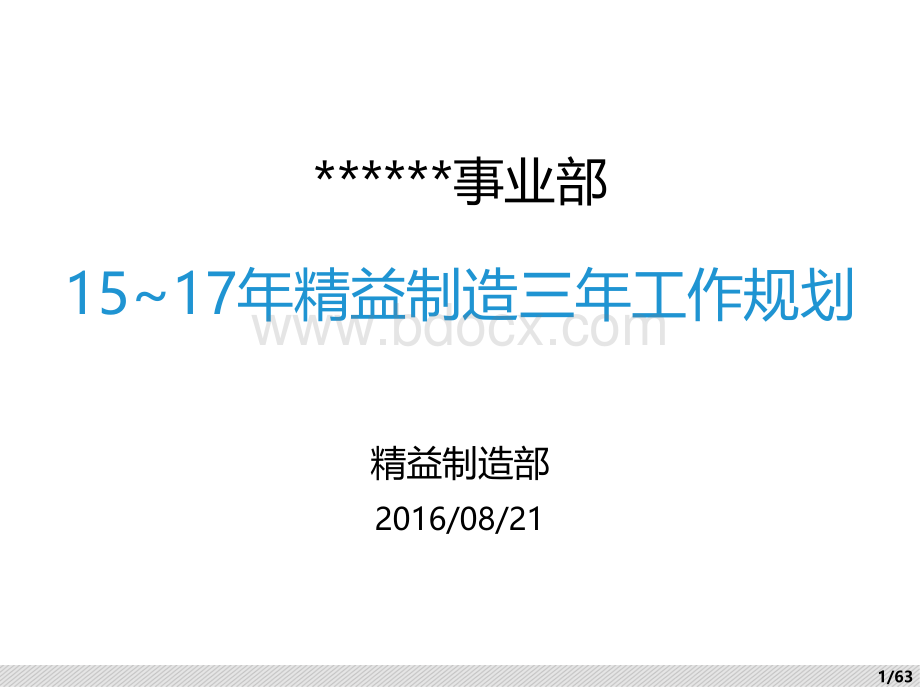
1/63*事业部1517年精益制造三年工作规划精益制造部2016/08/212/63目录三年规划与思路二制造现状一重点推进工作三15年具体工作计划四3/63制造现状第一部分第一部分4/63一、制造现状1、制造过程浪费多,现场作业、在制品、仓储库存、不良品以及管理方式等均存在过多浪费,有巨大的改善空间。
在制品库存过多不必要拆包不合理作业过长的移动距离大段空线等待物料重复拿取5/63一、制造现状2、人员不稳定,对效率及品质冲击明显。
上半年人员累计流失率超过43%,固定工流失率占比20%30%。
6/63一、制造现状3、生产计划不稳定,计划变动多:
订单取消、生产插单、调产现象普遍,总装需求、生产采购、自制件计划手工操作多,信息传递效率低。
总装当天作业完成率平均83%。
自制件(注塑)第一次需求时间与第二次需求时间吻合率约30%。
2014年月份当天计划完成率(量)当天作业完成率(单)2天作业完成率3天作业完成率1月95.9%83.5%96.4%99.5%2月93.6%76.6%94.5%98.7%3月97.9%85.0%96.9%99.8%4月98.6%87.6%97.8%99.9%5月95.6%86.3%96.3%99.8%6月93.0%83.1%95.0%98.9%总装7-14天周计划注塑计划进行分解分解到二级供方分解车间自制二级供方根据总量生产采购通知回货计划员定义系统作业采购根据作业日期指导厂家生产回货计划员根据总装上线时间进行排产车间生产配套出货7/63一、制造现状4、TPM、设备保全工作薄弱,现场设备缺乏管控,重大设备异常分析不足,人员技能提升缓慢,基本仍处于救火的状态,未能做到事前保全.顺德工厂1-6月份设备异常影响月份设备损失(分钟)设备损失(小时)产能损失(台)1月188231.484783月131021.858864月121920.354815月80913.536456月201533.690728/63一、制造现状品质手工报表5、信息化使用程度低,已有各系统集成不足,制造信息、品质信息等多采用手工记录,异常响应速度慢且数据易失真、难以追溯。
品质数据无记录关键物料无扫码效率手工报表专职报表统计人员9/63一、制造现状6、产品可制造性不足,基于可制造性的产品设计,还有很大改善空间。
现有产品系列较多,零部件通用性差,结构设计复杂,制造装配效率低下。
未来产品设计要同步考虑制造自动化的适用性。
W190外机螺钉海绵纯装配人数种类数量种类数量1162131376.GCLBICQAHBFDL电器盖板10/63二、问题总结问题一:
信息化应用水平偏低,信息传递人为影响多,响应速度慢问题二:
问题三:
问题四:
问题五:
观念意识转变不彻底,各工厂精益意识、观念转变深入程度参差不齐,执行力不足,各项工作落地效果差精细化管理不足,人员定编定岗、直间比管理缺失、制造过程异常管控薄弱制造基础工作没有做到坚持和规范,不能形成稳定、良性提升制造效率系统规划不足,缺乏有效项目支撑,目标达成存在风险11/63三年规划思路第二部分第二部分12/63一、总体战略精益设计通过彻底消除浪费,追求最高效率18年20000人,效率逐年提升25%精益供应链精益制造信息化l平台化设计l标准化设计l可制造性设计l面向自动化设计l来料恰时保障l来料合格保障l供方现场扶持l供方管理输出l全员改善l工艺技术提升l生产模式革新l精益物流l自动化改造l系统串接兼容l从端到端的全流程信息化lMES制造程管理及可追溯愿景策略目标以人为本、全员持续改善基础突破方向成为全球家电精益生产企业标杆13/63二、推进路径以效率提升、精品制造为牵引,以精益设计、精益供应链、精益制造、信息化为突破方向,达成效率逐年提升25%目标,初步实现工厂少人化、信息化,逐步向智能化工厂过渡。
重重点点突突破破基基础础深深化化稳定提升峰值人数控制26000人效率提升45%夯实基础峰值人数控制22000人效率提升25%深化突破峰值人数控制24000人效率提升25%第二阶段(16年)第一阶段(15年)第三阶段(17年)在前期精益推进的基础上,建立健全标准业务体系,适应自动化大规模导入的人才梯队培养、管理能力提升:
u精益设计:
基于老产品的可制造性整改u精益制造:
基础工艺研究、单工序自动化突破,开展对外合作,导入业内成熟技术u信息化推进:
以广州为试点,深入推广应用MES,同时为导入WMS做好前期准备基于计划、生产、设备、人员等持续稳定的管理变革、技术突破:
u开展精益设计体系搭建u关键工艺技术突破,多工序实现自动化连续流,检测、搬运、组装等岗位少人化uISE、MES、ERP系统融合,六地工厂同步推进基于价值流改善的拉动式生产及信息化改造全流程信息管理串接研究,初步集成制造品质、生产、设备等系统:
u推动产品模组化、标准化、装配简单化设计落地u工厂整体实现少人化,工艺技术处于业内领先水平u开放ERP供方送货看板,指导供方物料实现JIT送货u针对基层开展精益知识培训,全员普及精益理念u成熟供方管理制度,战略供应商改善起到明显成效u总装、自制件区域物流实现无人化配送、WMS系统导入u精益文化革新:
精益改善氛围营造、精益基础普及,探索基于价值流改善的拉动式生产u供方管理输出:
针对战略供应商,开展淡季改善,旺季帮扶工作u精益物流:
推进内/外机大件物料无人化配送、物流器具标准化u精益理念深入人心,自主改善氛围浓厚u供方管理常态化,供应商扶持占比80%以上u基于信息化、单点智能化的物流配送模式及器具引入14/63重点推进工作第三部分第三部分15/63一、开展策略精益意识转变基础深化重点突破价值流改善供方扶持夯实上年度已开展工作,作为下一年基础工作深化推进,追求稳定、规范、持续运作;结合三年规划,围绕年度目标,聚焦四项重点工作,实现实质性突破提升。
精益物流自动化工艺技术提升产品可制造性产出提升16/63二、基础深化
(一)精益意识转变思考:
如何设定精益的目标和愿景,让它成为大家共同的行动方向?
战略引导“精益”成为全员共同的事业,通过高层倡导、中层带动、全员参与,逐步形成制造体系持续改善的文化,转变思想意识,实现由传统制造向精益制造的蜕变。
高层倡导全局统筹、战略引导中层带动系统思维、先锋队伍全员参与问题精神、持续改善以精益六西格玛、价值流为工具,深化精益理念,推动重大革新活动开展:
制造体系高层黑带普及;制造高层年度重大经营改善策划及项目推动;工厂价值流推动责任主体。
掌握精益核心思想、理论知识,精益体系搭建,引导基层转变观念,改善落地责任主体:
制造体系区域对标,营造比学赶帮超的氛围;精益专员培训体系完善,人才梯队建设;中层绿带普及,制造中层成长为精益专家改善实施责任主体,改善技能提升,全员参与:
员工自主改善体系搭建,工厂两级改善发布活动开展,激发员工参与热情;分厂内部标杆班组评比,以点带面,营造全员参与氛围。
核心是真正做到以人为本,激发基层员工的活力17/63二、基础深化l组织优化后,各精益专员直接对接六地工厂项目执行人员,资源整合、协同更快捷,充分调动执行人员主观能动性,实现对精益推进的保障。
l按照中长期各重点项目调整岗位设置,即精益专员队伍,所有精益专员70%时间聚焦各自负责的项目上,推动公司自上而下的精益落地。
措施2:
工作方式改进,直接对接各项目执行人,对精益推进项目负责措施1:
按精益制造中长期规划优化设置,打造敏捷型组织l现有工作方式:
由各工程部策划、组织、实施,其他相关部门参与,但是存在执行人主动性不足,协同人员旁观、不作为现象,且没有系统的评价体系,导致项目质量、进度难以保证。
l现有四个模块:
自动化、工艺、效率、电子,除自动化外,其他岗位未紧密契合精益制造各项目进行设置,工作聚焦性、连续性不足,部分工作存在遗失。
问题2:
精益推进的承接、评价没有调动所有部门参与,整体的行动力不足问题1:
精益制造部组织架构无法满足企业精益转型需求思考:
选择什么样的组织和推进方式以及配套机制,使精益工具和方法落地?
1、精益制造部率先转型为精益专员队伍,以先锋力量带动制造体系转型,实现精益推进和落地的保障;2、改变工作推进方式,保证各部门工作聚焦。
(一)精益意识转变18/63二、基础深化20152015201420142013201320122012精益物流品质管理20162016现场管理工人管理价值流提案改善标准作业TPM安全管理班组管理20172017成本管理
(一)精益意识转变在精益制造战略规划中明确模块组成、先后顺序、实践路线。
各模块理念集成1成立精益协同组织;各模块在2个试点工厂同步开展。
推进组织系统设计2全方位系统设计生产计划2011201119/63二、基础深化标准课件操作手册精益先锋试点工厂非试点工厂事业部层面评审编制提供开展方法等级评价标准
(一)精益意识转变思考:
影响精益持续性的根源问题是什么?
如何解决?
以试点工厂带动非试点工厂,通过标准优化、人才育成、方法和工具导入等,实现一种相互交流的语言-改善成果分享模式。
各工厂排名评价和激励20/63二、基础深化
(二)价值流改善价值价值流拉动1畅流拉动2完善6.标准作业固化.拉动节拍、工序排布、WIP数量5S固化,线体5S看板,包括岗位排布、人员排布、操作区域、物料摆放等目视化管理(品质效率看板、关键岗位(CCPKGR图)KPI管控5.确认基准节拍点(N点)排产模式调整,总装与部装、各工序间看板设计;工序产能平衡改善断点工序单元设计,作业要素分解和优化重点突破断流工序,并完善已畅流工序,降低WIP数量4.畅流爆炸点选定课题在基准节拍点基础上,确定库存降低的目标,按此在价值流中实施拉动,调整我们的作业排产方式及现场使用看板进行拉动,确保有序流动1.选择改善流程,确定价值从VOC角度出发,确定浪费和价值,选择改善流程,确定项目组织分工2.绘制现状、未来价值流图根据现有水平确定库存水平,进行内部断点间形成拉动,目的是真正的管控库存,及知道库存产生的原因3.现状整理,初步改善根据分析的库存的原因用畅流的工具去改善CTQ/KPI订单交付周期生产阻碍损失率OPE(线体)OEE(设备)人均产出效率在制品库存现状12.67天6.88%65%105套/人.月1天3天目标9天3%75%130套/人.月4H1天(库存下降30%)以价值流(VSM)为抓手,按“价值、价值流、拉动1、畅流、拉动2、完善”六大环节依次开展,结合SMED、TPM、QI、物流容器、S-OJT等工具改善,实现生产流程的顺畅与效率提升。
(以广州工厂为试点工厂,成熟后复制推广)21/63二、基础深化精益物流建立:
场地布局调整;配送节拍制定;物流器具统一;物流人员培训。
开展管理人员精益培训。
建立TPM三级保养制度。
持续提升战略供应商的精益改善意识,建立健全供应商精益改善架构及平台,持续提升自身能力,保障供应商内部成本、品质、交期问题,以进一步解决美的空调旺季物料供应不畅问题。
生产效率低下计划排产无序物流配送混乱精益理念不足过程品质失控设备保养缺失制造现场改善:
时间观测;线平衡改善;技能培训。
计划排产规范:
排产流程建立;排产优化机制;先进系统导入。
直通率提升专项:
建立过程监控;关键岗位划线防呆检测改善。
聚焦供方六大问题(三)供方扶持22/63二、基础深化强化供方品质管控,将供应商供货情况进行系统管理(包括下单、供货及时性及品质等)。
通过“打”(处罚、淘汰)“拉”(扶持奖励)的方式培养优秀供应商供应商技能提升活动:
-供应商中高层领导培训活动,精益革新意识改变-干部责任制,对口供应商扶持:
周别、月别现场诊断活动,挖掘现场问题点并协助改善供应商评比交流活动:
-月别季度别供应商大会,供应商指标及改善活动分享;促进供应商竞争,打造优秀供应商-内部优秀改善事例分享,供应商学习提升,并对积极配合改善的优秀供应商进行奖励No.培训内容课时组织单位培训对象1精益管理6天事业部高层管理者2经营决策沙盘2天3企业战略规划制定与分解2天4标杆企业的参观学习7天5QCC项目开展每期3天六地工厂中层管理6标准作业、现场改善7现场管理5S、TPM实践活动8物流与看板、生产线布