数控机床三维建模与设计.docx
《数控机床三维建模与设计.docx》由会员分享,可在线阅读,更多相关《数控机床三维建模与设计.docx(36页珍藏版)》请在冰豆网上搜索。
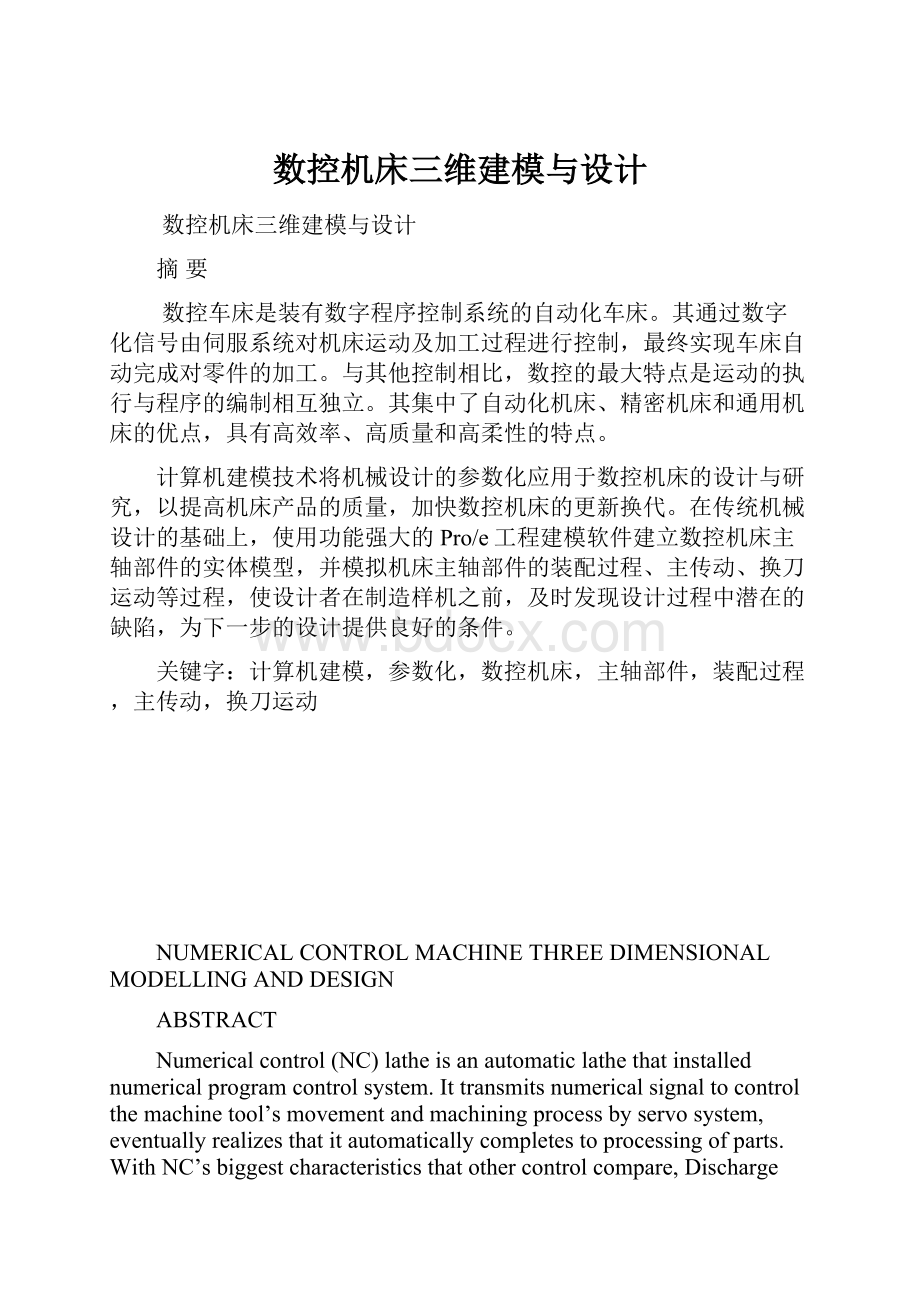
数控机床三维建模与设计
数控机床三维建模与设计
摘要
数控车床是装有数字程序控制系统的自动化车床。
其通过数字化信号由伺服系统对机床运动及加工过程进行控制,最终实现车床自动完成对零件的加工。
与其他控制相比,数控的最大特点是运动的执行与程序的编制相互独立。
其集中了自动化机床、精密机床和通用机床的优点,具有高效率、高质量和高柔性的特点。
计算机建模技术将机械设计的参数化应用于数控机床的设计与研究,以提高机床产品的质量,加快数控机床的更新换代。
在传统机械设计的基础上,使用功能强大的Pro/e工程建模软件建立数控机床主轴部件的实体模型,并模拟机床主轴部件的装配过程、主传动、换刀运动等过程,使设计者在制造样机之前,及时发现设计过程中潜在的缺陷,为下一步的设计提供良好的条件。
关键字:
计算机建模,参数化,数控机床,主轴部件,装配过程,主传动,换刀运动
NUMERICALCONTROLMACHINETHREEDIMENSIONALMODELLINGANDDESIGN
ABSTRACT
Numericalcontrol(NC)latheisanautomaticlathethatinstallednumericalprogramcontrolsystem.Ittransmitsnumericalsignaltocontrolthemachinetool’smovementandmachiningprocessbyservosystem,eventuallyrealizesthatitautomaticallycompletestoprocessingofparts.WithNC’sbiggestcharacteristicsthatothercontrolcompare,Dischargemovementandprogrammutuallyindependent.Itcollectstheadvantagesofautomaticmachinetools,precisemachinetoolsandgeneralpurposemachinetools,havingthecharactersofhigh-efficiency,high-qualityandhigh-flexibility.
Thecalculatorissetupthemoldtechniquetoturntheparameterthatthemachinedesigntoapplyinthedesignandresearchesthatthenumbercontrolthetoolmachine,withthequantityoftheexaltationtoolmachineproduct,therenewalthatspeedsnumbertocontrolthetoolmachinechangesthegeneration.Onthefoundationthatthetraditionalmachinedesign,thestrongengineeringofPro/eoftheusagefunctionsetsuptheentitymodelthatthemoldsoftwarebuildsupnumbertocontrolthetoolmachineprincipalaxisparts,andimitatetheassembleprocess,lordofthetoolmachineprincipalaxispartstospreadtomove,changetheknifethesportetc.process,makedesignisbeforemakethekindmachine,discoveringtodesigntheprocessintimeinthelatentblemish,providethegoodconditionforthedesignofthenextmove.
KEYWORDS:
Computermodelling,Parametrization,Numericalcontrolmachine,Mainaxlepart,Assemblyprocess,Masterdrive,Theknifemovementtrading
1绪论
1.1数控机床的产生与发展
1.1.1数控机床的产生与发展
微电子技术,自动信息处理,数据处理以及电子计算机的发展,给自动化带来了新的概念,推动了机械制造自动化的发展。
采用数字控制技术进行机械加工的思想,最早在20世纪40年代提出的,当时美国的一个小型飞机工业承包商帕森公司在麻省理工学院伺服机构试验室的协助下,经过三年时间的研究,于1952年试制成功世界第一台数控机床试验性样机。
这是一台采用脉冲乘法器原理的直线插补三坐标连续控制铣床,这便是数控机床的第一代。
在早先的数控机床都采用专用控制计算机的硬逻辑数控系统,装有这类数控系统的机床为普通数控机床(简称NC机床)。
随着计算机技术的发展,小型计算机的价格急剧下降。
小型计算机开始取代专用数控计算机,数控的许多功能由软件程序实现。
这样的数控系统称为计算机数控系统(简称CNC)。
近20年来,微处理机数控系统的数控机床得到了飞速发展和广泛应用。
1.1.2数控机床的技术发展趋势
数控技术的应用不但给传统制造夜带来了革命性的变化,使制造也成为工业化的象征。
当前世界上数控技术及其装备的发展呈现出高速、高精密化发展趋势。
1).高速
新一代数控机床(含加工中心)只有通过高速化大幅度缩短切削工时才能进一步提高其生产率。
超高速加工,特别是超高速铣削与新一代数控机床特别是高速加工中心的开发与应用紧密相关。
依靠快速、准确的数字量传递技术对高性能的机床执行部件进行高精密度、高响应速度的实时处理,由于采用了新型刀具,车削和铣削的速度已达5000m/min-8000m/min以上,主轴转速在10000r/min以上;工作台移动速度:
分辨率为1μm时在100m/min以上,分辨率为0.1μm时在24m/min以上;自动换刀速度在1s以内;小线段插补速度达12m/min。
根据高效率、大批量生产需求和电子驱动技术的飞速发展,高速直线电机的推广应用,已开发出一批高速、高效的高速响应的数控机床。
2).高精密度
从精密加工到超精密加工,是世界个工业强国致力发展的方向。
其精度从微米级到亚微米级,乃至纳米级,其应用范围日益广泛。
随着科学技术的发展,对超精密加工技术不断提出了新的要求。
新材料及新零件的出现,更高精密要求的提出等都需要超精密加工工艺,发展新型超精密加工机床,完善现代超精密加工技术,以适应现代科技的发展。
1.2设计的主要任务
数控机床主轴部件是机床的核心部件。
目前,高速主轴单元在国外有很大的发展,其数控机床的转速已经达到10000-20000r/min,主轴功率可达22KW;较先进的数控机床主轴转速可达20000-60000r/min,主轴功率达20-60KW。
而我国对高速高精度机床虽然也取得了一定的成果,但无论在转速还是精度方面与国外先进水平还有很大的差距,其已成为我国发展超高速加工技术的“瓶颈”。
本设计主要通过对现有数控机床主轴部件现状的分析,探讨合理的结构形状,优化其参数,提高机床主轴部件的工作性能;采用计算机建模技术,设计数控机床主轴部件的数控样机。
因此,将数字化技术应用于数控机床的主轴部件的设计与研究,对于稳定机床产品的质量,提高生产率,推动机床功能部件的发展,加快产品的更新换代具有重要意义。
2主传动设计
2.1驱动源的选择
机床上常用的无级变速机构是直流或交流调速电动机,直流电动机从额定转速nd向上至最高转速nmax是调节磁场电流的方法来调速的,属于恒功率,从额定转速nd向下至最低转速nmin是调节电枢电压的方法来调速的,属于恒转矩;交流调速电动机是靠调节供电频率的方法调速。
由于交流调速电动机的体积小,转动惯量小,动态响应快,没有电刷,能达到的最高转速比同功率的直流调速电动机高,磨损和故障也少,所以在中小功率领域,交流调速电动机占有较大的优势,鉴于此,本设计选用交流调速电动机。
根据主轴要求的最高转速4000r/min,最大切削功率5.5KW,选择北京数控设备厂的BESK-8型交流主轴电动机,其基本转速是300r/min,最高转速是4500r/min。
2.2转速图的拟定
根据交流主轴电动机的最高转速和基本转速可以求得交流主轴电动机的恒功率转速范围
Rdp=nmax/nd=3(2-1)
而主轴要求的恒功率转速范围Rnp=26.7,远大于交流主轴电动机所能提供的恒功率转速范围,所以必须串联变速机构的方法来扩大其恒功率转速范围。
设计变速箱时,考虑到机床结构的复杂程度,运转的平稳性等因素,取变速箱的公比Фf等于交流主轴电动机的恒功率调速范围Rdp,即Фf=Rdp=3,功率特性图是连续的,无缺口和无重合的。
变速箱的变速级数
Z=lgRnp/lgRdp=lg26.7/lg3=2.99(2-2)
取Z=3
确定各齿轮副的齿数:
取S=116
由u=1.955得Z1=39Z1′=77
由u=1.54得Z2=46Z2′=70
由u=4.6得Z3=20Z3′=96
由此拟定主传动系统图、转速图以及主轴功率特性图分别如图2-1、图2-2、图2-3。
图2-1主传动系统图
图2-2转速图图2-3主轴功率特性
2.3传动轴的估算
传动轴除应满足强度要求外,还应满足刚度要求。
强度要求保证轴在反复载荷和扭转载荷作用下不发生疲劳破坏。
机床主传动系统精度要求较高,不允许有较大的变形。
因此疲劳强度一般不是主要矛盾。
除了载荷比较大的情况外,可以不必验算轴的强度。
刚度要求轴在载荷下(弯曲,轴向,扭转)不致产生过大的变形(弯曲,失稳,转角)。
如果刚度不够,轴上的零件如齿轮,轴承等由于轴的变形过大而不能正常工作,或者产生振动和噪音,发热,过早磨损而失效。
因此,必须保证传动轴有足够的刚度。
通常,先按扭转刚度轴的直径,画出草图后,再根据受力情况,结构布置和有关尺寸,验算弯曲刚度。
计算转速nj是传动件传递全部功率时的最低转速,各个传动轴上的计算转速可以从转速图上直接得出如表2-1所示。
表2-1各轴的计算转速
轴
Ⅰ
Ⅱ
计算转速(r/min)
682
150
各轴功率和扭矩计算:
已知一级齿轮传动效率为0.97(包括轴承),同步带传动效率为0.98,则:
Ⅰ轴:
P1=Pd×0.98=7.5×0.98=7.35KW
Ⅱ轴:
P2=P1×0.97=7.35×0.97=7.13KW
Ⅰ轴扭矩:
T1=9550P1/n1=9550×7.35/682=1.029×105N.mm
Ⅱ轴扭矩:
T2=9550P2/n2=4.539×105N.mm
[φ]是每米长度上允许的扭转角(deg/m),可根据传动轴的要求选取,其选取的原则如表2-2所示。
表2-2许用扭转角选取原则
轴
主轴
一般传动轴
较低的轴
[φ](deg/m)
0.5-1
1-1.5
1.5-2
根据表3-2确定各轴所允许的扭转角如表3-3所示。
表2-3许用扭转角的确定
轴
Ⅰ
Ⅱ
[φ](deg/m)
1
1
把以上确定的各轴的输入功率N=7.5KW、计算转速nj(如表2-1)、允许扭转角[φ](如表2-3)代入扭转刚度的估算公式
d=91
(2-3)
可得传动轴的估算直径:
d=40mm;
主轴轴径尺寸的确定:
已知车床最大加工直径为Dmax=400mm,则:
主轴前轴颈直径D1=0.25Dmax±15=85~115mm取D1=95mm
后轴颈直径D2=(0.7~0.85)D1=67~81mm取D2=75mm
内孔直径d=0.1Dmax±10=35~55mm取d=40mm
2.4齿轮模数的估算
按接触疲劳强度和弯曲疲劳强度计算齿轮模数比较复杂,而且有些系数只有在齿轮的各参数都已知方可确定,故只有在装配草图画完后校验用。
在画草图时用经验公式估算,根据估算的结果然后选用标准齿轮的模数。
齿轮模数的估算有两种方法,第一种是按齿轮的弯曲疲劳进行估算,第二种是按齿轮的齿面点蚀进行估算,而这两种方法的前提条件是各个齿轮的齿数必须已知,所以必须先给出各个齿轮的齿数。
根据齿轮不产生根切的基本条件:
齿轮的齿数不小于17,在该设计中,即最小齿轮的齿数不小于17。
而由于Z3,Z3’这对齿轮有最大的传动比,各个传动齿轮中最小齿数的齿轮必然是Z3。
取Z3=20,S=116,则Z3’=96。
从转速图上直接看出直接可以看出Z3的计算转速是682r/min。
根据齿轮弯曲疲劳估算公式
mω
=2.4(2-4)
根据齿轮接触疲劳强度估算公式计算得:
m=2.84
由于受传动轴轴径尺寸大小限制,选取齿轮模数为m=3mm,对比上述结果,可知这样设计出的齿轮传动,既满足了齿面接触疲劳强度,又满足了齿根弯曲疲劳强度,故取同一变速组中的所有齿轮的模数都为m=3mm。
可得两轴中心距为a=175mm.
现将各齿轮齿数和模数列表如下:
表2-4齿轮的估算齿数和模数列表
齿轮
Z1
Z1′
Z2
Z2’
Z3
Z3’
齿数
46
70
77
39
20
96
模数(mm)
3
3
3
3
3
3
3主轴箱展开图的设计
主轴箱展开图是反映各个零件的相互关系,结构形状以及尺寸的图纸。
因此设计从画展开图开始,确定所有零件的位置,结构和尺寸,并以此为依据绘制零件工作图。
3.1各零件结构和尺寸设计
3.1.1设计的内容和步骤
这一阶段的设计内容是通过绘图设计轴的结构尺寸及选出轴承的型号,确定轴的支点距离和轴上零件力的作用点,计算轴的强度和轴承的寿命。
3.1.2有关零部件结构和尺寸的确定
传动零件,轴,轴承是主轴部件的主要零件,其它零件的结构和尺寸是根据主要零件的位置和结构而定。
所以设计时先画主要零件,后画其它零件,先画传动零件的中心线和轮廓线,后画结构细节。
1)传动轴的估算
这一步在前面已经做了计算。
2)齿轮相关尺寸的计算
为了确定轴的轴向距离,齿轮齿宽的确定是必须的。
齿宽影响齿的强度。
但如果太宽,由于齿轮的制造误差和轴的变形,可能接触不均,反而容易引起振动和噪声,一般取齿宽系数Φm=(6-10)m。
这里取齿宽系数Φm=10,则齿宽B=Φm×m=10×3=30mm.现将各个齿轮的齿厚确定如表3-1所示。
表3-1各齿轮的齿厚
齿轮
Z1
Z1′
Z2
Z2′
Z3
Z3′
齿厚(mm)
30
30
30
30
30
30
齿轮的直径决定了各个轴之间的尺寸,所以在画展开图草图前,各个齿轮的尺寸必须算出。
现将主轴部件中各个齿轮的尺寸计算如表3-2所示。
表3-2各齿轮的直径
齿轮
Z1
Z1′
Z2
Z2′
Z3
Z3′
分度圆直径(mm)
138
210
231
117
60
288
齿顶圆直径(mm)
144
216
237
123
66
294
齿根圆直径(mm)
130.5
202.5
223.5
109.5
52.5
280.5
由表3-2可以计算出各轴之间的距离,现将它们列出如表3-3所示。
表3-3各轴的中心距
轴
ⅠⅡ
ⅡⅢ
距离(mm)
175
175
3)确定齿轮的轴向布置
为避免同一滑移齿轮变速组内的两对齿轮同时啮合,两个固定齿轮的间距,应大于滑移齿轮的宽度,一般留有间隙1-2mm,所以首先设计滑移齿轮。
Ⅱ轴上的滑移齿轮的两个齿轮轮之间必须留有用于齿轮加工的间隙,插齿时,当模数在1-2mm范围内时,间隙必须不小于5mm,当模数在2.5-4mm范围内时,间隙必须不小于6mm,且应留有足够空间滑移,据此选取该滑移齿轮三片齿轮之间的间隙分别为d1=17.5mm,d2=15mm。
由滑移齿轮的厚度以及滑移齿轮上的间隙可以得出主轴上的两个齿轮的间距至少是60mm,现取齿轮之间的间距为64mm和70mm。
4)轴承的选择及其配置
主轴组件的滚动轴承既要有承受径向载荷的径向轴承,又要有承受两个方向轴向载荷的推力轴承。
轴承类型及型号选用主要应根据主轴的刚度,承载能力,转速,抗振性及结构要求合理的进行选定。
同样尺寸的轴承,线接触的滚子轴承比电接触的球轴承的刚度要高,但极限转速要低;多个轴承的承载能力比单个轴承的承载能力要大;不同轴承承受载荷类型及大小不同;还应考虑结构要求,如中心距特别小的组合机床主轴,可采用滚针轴承。
为了提高主轴组件的刚度,通常采用轻型或特轻型系列轴承,因为当轴承外径一定时,其孔径(即主轴轴颈)较大。
通常情况下,中速重载采用双列圆柱滚子轴承配双向推力角接触球轴承(如配推力轴承,则极限转速低),或者成对圆锥滚子轴承,其结构简单,但是极限转速较低,如配空心圆锥滚子轴承,其极限转速显著提高,但成本也相应的提高了。
高速轻载采用成组角接触球轴承,根据轴向载荷的大小分别选用25°或15°的接触角。
轴向载荷为主且精度要求不高时,选用推力轴承配深沟球轴承,精度要求较高时,选用向心推力轴承。
该设计的主轴不仅有刚度高的要求,而且有转速高的要求,所以在选择主轴轴承时,刚度和速度这两方面都要考虑。
主轴前轴承采用3182119型轴承一个,后支承采用30215型和8215型轴承各一个
3.1.3各轴结构的设计
Ⅰ轴的一端与带轮相连,将Ⅰ轴的结构草图绘制如图3-2所示。
Ⅱ轴其结构完全按标准确定,根据其轴向的尺寸可将结构简图绘制如图3-1所示。
图3-1Ⅱ轴的结构简图
图3-2Ⅰ轴的结构简图
3.1.4主轴组件的刚度和刚度损失的计算:
最佳跨距的确定:
取弹性模量E=2.1×105N/mm2,D=(95+75)/2=85;
主轴截面惯距:
I=
=2.48×106mm4;
截面面积:
A=4415.63mm2
主轴最大输出转矩:
Mn=9550000
=4.775×105N.mm
Fz
=2122.2N
Fy=0.5Fz=1061.1N
故总切削力为:
F=
=2372.69N
估算时,暂取L0/a=3,即取285mm.
前后支承支反力Ra=3163.59N
Rb=790.897N
取Ka=13.976×105N/mm
Kb=2.67×105N/mm
η=
=0.435
则L0/a=2.96.
则L0=281mm
因在上式计算中,忽略了ys的影响,故L0应稍大一点,取L0=300mm
计算刚度损失:
取L=385mm,χ=4.61
由
公
式
弹性主轴y1
弹性支承k
总
柔
度
总
刚度
弯曲变形yb
剪切变形ys
前支承
后支承
悬伸段
跨距段
悬伸段
跨距段
L=385
5.488×10-7
2.224×10-6
2.361×10-7
1.165×10-7
11.12×10-7
2.28×10-7
44.65×10-7
2.24×105
12.29%
49.8%
5.29%
2.61%
24.9%
5.1%
100%
L0=300
5.488×10-7
1.732×10-6
2.361×10-7
1.4915×10-7
12.4×10-7
3.756×10-7
42.83×10-7
2.33×105
12.81%
40.46%
5.51%
3.48%
28.9%
8.77%
100%
由L≠L0引起的刚度损失约为3.68%,可知,主轴刚度损失较小,选用的轴承型号及支承形式都能满足刚度要求。
主轴端部挠度的验算:
传动力的计算:
已知齿轮最少齿数为39,模数为3,则分度圆直径为78mm,
则齿轮的圆周力:
P=2T2/dmin=11638.46N
径向力:
Pr=0.5Pt=5819.23N
则传动力在水平面和垂直面内有分力为:
水平面:
QH=PtH+PrH=4365.717N
垂直面:
Qv=Ptv+Prv=11547.18N
取计算齿轮与前支承的距离为185mm,其与后支承的距离为200mm.
切削力的计算:
已知车床拖板最大回转直径Dmax=200mm,
则主切削力:
Pv=Pc=4539.004N
径向切削力:
PH=0.5Pc=2269.5N
轴向切削力:
Pr=0.35Pc=1588.65N
当量切削力的计算:
P=(a+B)p′/a对于车床B=0.4Dmax=160mm
则水平面内:
PH=6091.8N
垂直面内:
Pv=4264.27N
主轴端部挠度的计算:
Yp=P〔
(1+
)+χ
〕(mm)
YPH=2.47×10-2mm,yPv=1.73×10-2mm
传动力作用下,主轴端位移的计算公式见5-17:
YQ=Q〔-
〕(mm)
式中:
“-”号表示位移方向与力反向,b表示齿轮与前支承的距离,c表示齿轮与后支承的距离,将各值代入,得yQ=-16.896×10-7Q
YQH=-7.376×10-3mmyQV=-1.951×10-2mm
则水平面内:
yH=yPH+yQH=1.7324×10-2mm
垂直面内:
yv=yPV+yQV=-0.221×10-2mm
则主轴最大端位移为:
ymax=0.0174mm
又已知主轴端部位移的许用值「y」=0.0002L,L=385mm
则「y」=0.0002×385=0.077mm.
ymax﹤「y」,符合要求。
主轴倾角的验算:
如果轴承处的倾角过大,会破坏轴承的的正常工作,缩短轴承的寿命,因此需要加以限制。
而前轴承所受的载荷较大,故只需校核前轴承。
通常在计算主轴倾角时,不考虑支承弹性的影响。
在切削力P作用下主轴前轴承处的倾角为:
水平面内:
=
×10-4rad
垂直面内:
=
=9.982×10-5rad
在传动力Q作用下主轴前轴承处的倾角为:
水平面内:
=
=-7.8547×10-5rad
垂直面内:
=
=-2.0775×10-4rad
则主轴前轴承处的倾角为:
水平面内:
=
=6.4053×10-5rad
垂直面内:
=
=-10.793×10-5rad
则
=
=1.255×10-4rad
又已知主轴倾角的许用值为「
」=0.001rad
所以
﹤「
」,符合要求。
3.2装配图的图纸设计
根据主轴展开图第一阶段的设计,已将主轴部件的各个部分的零件确定下来,但作为完整的展开图,必须包含主轴部件的各个视图,尺寸,