整体装配式框架结构施工工法.doc
《整体装配式框架结构施工工法.doc》由会员分享,可在线阅读,更多相关《整体装配式框架结构施工工法.doc(21页珍藏版)》请在冰豆网上搜索。
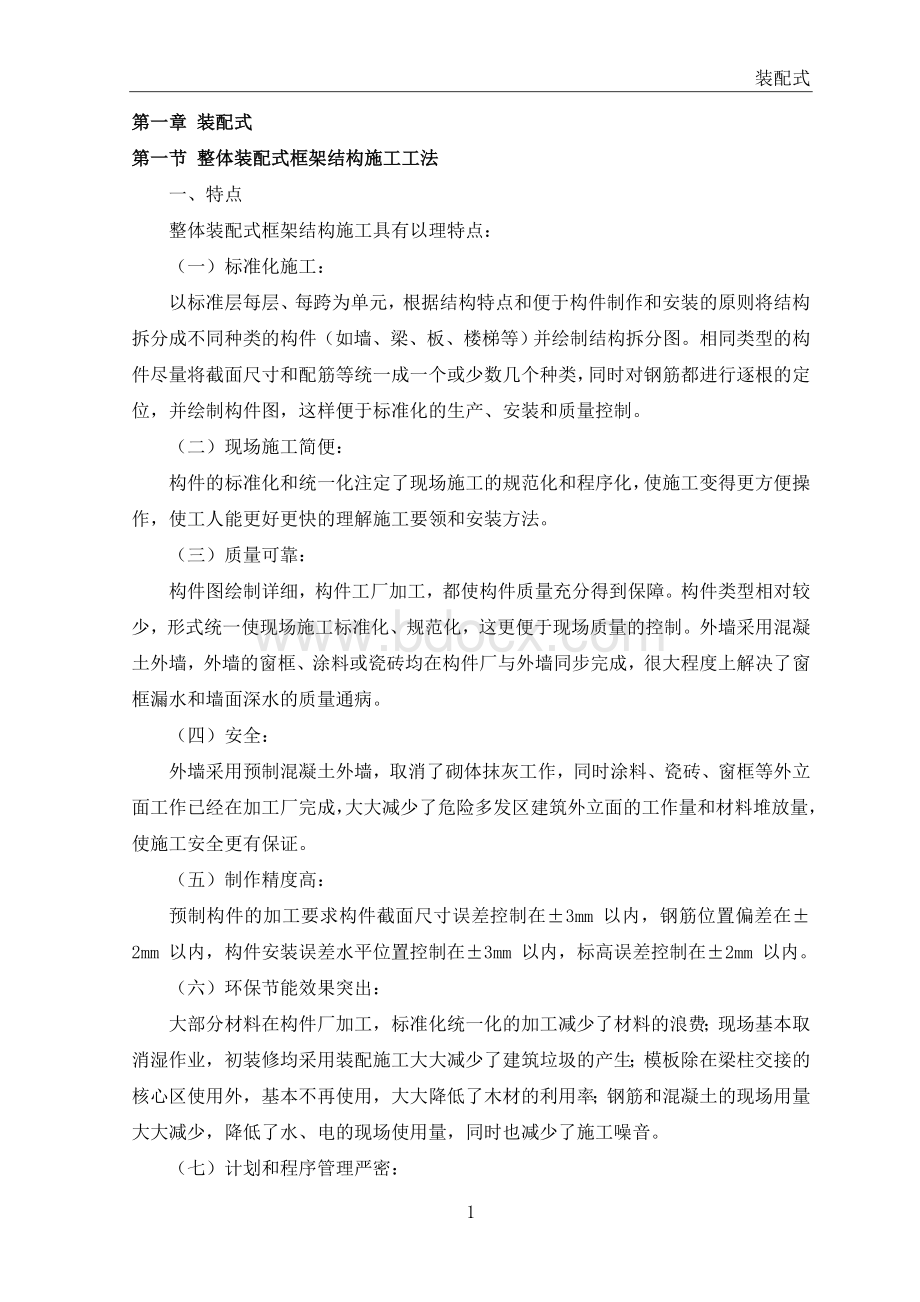
装配式
第一章装配式
第一节整体装配式框架结构施工工法
一、特点
整体装配式框架结构施工具有以理特点:
(一)标准化施工:
以标准层每层、每跨为单元,根据结构特点和便于构件制作和安装的原则将结构拆分成不同种类的构件(如墙、梁、板、楼梯等)并绘制结构拆分图。
相同类型的构件尽量将截面尺寸和配筋等统一成一个或少数几个种类,同时对钢筋都进行逐根的定位,并绘制构件图,这样便于标准化的生产、安装和质量控制。
(二)现场施工简便:
构件的标准化和统一化注定了现场施工的规范化和程序化,使施工变得更方便操作,使工人能更好更快的理解施工要领和安装方法。
(三)质量可靠:
构件图绘制详细,构件工厂加工,都使构件质量充分得到保障。
构件类型相对较少,形式统一使现场施工标准化、规范化,这更便于现场质量的控制。
外墙采用混凝土外墙,外墙的窗框、涂料或瓷砖均在构件厂与外墙同步完成,很大程度上解决了窗框漏水和墙面深水的质量通病。
(四)安全:
外墙采用预制混凝土外墙,取消了砌体抹灰工作,同时涂料、瓷砖、窗框等外立面工作已经在加工厂完成,大大减少了危险多发区建筑外立面的工作量和材料堆放量,使施工安全更有保证。
(五)制作精度高:
预制构件的加工要求构件截面尺寸误差控制在±3mm以内,钢筋位置偏差在±2mm以内,构件安装误差水平位置控制在±3mm以内,标高误差控制在±2mm以内。
(六)环保节能效果突出:
大部分材料在构件厂加工,标准化统一化的加工减少了材料的浪费;现场基本取消湿作业,初装修均采用装配施工大大减少了建筑垃圾的产生;模板除在梁柱交接的核心区使用外,基本不再使用,大大降低了木材的利用率;钢筋和混凝土的现场用量大大减少,降低了水、电的现场使用量,同时也减少了施工噪音。
(七)计划和程序管理严密:
各种施工措施埋件要反映在构件图中,这就要求方案的可执行型强,并且施工时严格按照方案和施工程序施工。
构件的加工计划、运输计划和每辆车构件的装车顺序紧密的与现场施工计划和吊装计划相结合,确保每个构件严格按实际吊装时间进场,保证了安装的连续性确保整体工期的实现。
二、工艺原理
梁、板等水平构件采用叠合形式,既构件底部(包含底筋、箍筋、底部混凝土)采用工厂预制,面层和深入支座处(包含面筋)采用现浇。
外墙、楼梯等构件除深入支座处现浇外,其它部分全部预制。
每施工段构件现场安全部安装完成后统一进行浇筑,这样有效的解决了拼装工程整体性差,抗震等级底的问题。
同时也减少现场钢筋、模板、混凝土的材料用量,简化了现场施工。
构件的加工计划、运输计划和每辆车构件的装车顺序紧密的与现场施工计划和吊装计划相结合,确保每个构件严格按实际吊装时间进场,保证了安装的连续性。
构件拆分和生产的统一性保证了安装的标准性和规范性,大大提高了工人的工作效率和机械利用率。
这些都大大缩短了施工周期和减少了劳动力数量,满足了社会和行业对工期的要求以及解决了劳动力短缺的问题。
外墙采用混凝土外墙,外墙的窗框、涂料或瓷砖均在构件厂与外墙同步完成,很大程度上解决了窗框漏水和墙面深水的质量通病,并大大减少了外墙装修的工作量缩短了工期(只需进行局部修补工作)。
三、施工工艺流程及操作要点
(一)工艺流程
(二)操作要点
1、技术准备要点
(1)所有需在结构预埋措施埋件的施工方案必须在构件图绘制前将每个埋件进行定位,便于反映在构件图中。
(2)构件模具生产顺序和构件加工顺序及构件装车顺序必须与现场吊装计划相对应,避免因为构件未加工或装车顺序错误影响现场施工进度。
(3)构件图出图后,第一时间必须构件图中的预留预埋部品认真核对,确保无遗漏、无错误。
避免构件生产后无法满足施工措施和建筑功能的要求。
2、平面布置要点
(1)现场硬化采用20mm厚钢板,铺设范围包括常规材料堆场(钢管、支撑、吊具、钢模等)外架底部和构件车辆行走路。
使用钢板便于周转,利于环保节能。
(2)现场车辆行走通道必须能满足车辆可同时进出,避免因道路问题影响吊装衔接。
(3)塔吊数量需根据构件数量进行确定(结构构件数量一定,塔吊数量与工期成反比);塔吊型号和位置根据构件重量和范围进行确定,原则上距离最重构件和吊装难度最大的构件最近。
3、吊装前准备要点
(1)构件吊装前必须整理吊具,并根据构件不同形式和大小安装好吊具,这样既节省吊装时间又可保证吊装质量和安全。
(2)构件必须根据吊装顺序进行装车,避免现场转运和查找。
(3)构件进场后根据构件标号和吊装计划的吊装序号在构件上标出序号,并在图纸上标出序号位置,这样可直观表示出构件位置,便于吊装工和指挥操作,减少误吊几率。
(4)所有构件吊装前必须在相关构件上将各个截面的控制线提前放好,可节省吊装、调整时间并利于质量控制。
(5)墙体吊装前必须将调节工具埋件提前安装在墙体上,可减少吊装时间,并利于质量控制。
(6)所有构件吊装前下部支撑体系必须完成,且支撑点标高应精确调整。
(7)梁构件吊装前必须测量并修正柱顶标高,确保与梁底标高一致,便于梁就位。
4、吊装过程要点
(1)构件起吊离开地面时如顶部(表面)未达到水平,必须调整水平后再吊至构件就位处,这样便于钢筋对位和构件落位。
(2)柱拆模后立即进行钢筋位置复核和调整,确保不会与梁钢筋冲突,避免梁无法就位。
(3)突窗、阳台、楼梯、部分梁构件等同一构件上吊点高低有不同的,低处吊点采用葫芦进行拉接,起吊后调平,落位时采用葫芦紧密调整标高。
(4)梁吊装前柱核心区内先安装一道柱箍筋,梁就位后再安装两道柱箍筋,之后才可进行梁、墙吊装。
否则,柱核心区质量无法保证。
(5)梁吊装前应将所有梁底标高进行统计,有交叉部分梁吊装方案根据先低后高进行安排施工。
(6)墙体吊装后才可进行梁面筋绑扎,否则将阻碍墙锚固钢筋深入梁内。
(7)墙体如果是水平装车,起吊时应先在墙面安装吊具,将墙水平吊至地面后将吊具移至墙顶。
在墙底铺垫轮胎或橡胶垫,进行墙体翻身使其垂直,这样可避免墙底部边角损坏。
5、梁构件吊装要点
6、板构件吊装要点
7、楼梯构件吊装要点
8、墙体构件吊装要点
四、材料与设备
(一)材料
(二)机具设备
每个安装小组机设备表
(三)劳动力
1、预制加工厂配套人员(每套模具)
2、现场吊装配备人员(每个组)
五、质量控制
(一)预制构件质量控制
1、预制构件加工精度
装配整体式混凝土结构中的梁、板和楼梯等构件采用工厂预制,预制构件精度要求高,在施工过程中如果精度无法满足要求将给后续的吊装工作带来巨大阻碍。
下表是各类构件精度要求列表:
检测项目
要求
检测方法
主控项目
混凝土强度及外观质量
符合GB50204-2002规范
检查构件查看报告
一
般
项
目
吊装标识
清晰无误
按图检查
截面尺寸
长
±6mm
卷尺
宽
±4mm
高(厚)
±3mm
梁侧、底平整度
2mm
4m靠尺
板底平整度
3mm
墙表面平整度
3mm
对角线
2mm
对角尺或高精度测距器
底部钢筋间距/长度
5mm/-3mm
箍筋间距
±5mm
焊接端钢筋翘曲
不大于2mm
预埋件定位
±2mm
埋件标高
±3mm
预留孔洞中心线
±5mm
预留孔洞标高
±5mm
2、构件加工质量控制流程
预制构件加工质量是工业化生成过程中的重要环节,直接关系到下道吊装工程的施工质量和施工进度。
装配整体式结构工程对预制构件的加工精度较高,在流程控制上对每道工序必须做到有可追溯性。
构件质量控制流程如下图:
(二)现浇部分质量控制
1、控制重点
柱网轴线偏差的控制、楼层标高的控制、柱核心区钢筋定位控制、柱垂直度的控制、柱首次浇筑后顶部与预制梁接槎处平整度和标高的控制、叠合层内后置埋件精度控制、连续梁在中间支座处底部钢筋焊接质量控制、叠合板在柱边处表面平整度控制、屋面框架梁柱处面筋节点施工质量的控制。
2、柱轴线允许偏差
柱轴线允许偏差必须满足《工程测量规范》GB50026-93要求,测量控制由高至低的级别进行布控,允许偏差不得大于3mm。
3、标高控制
标高控制在建筑物周边设置控制点,以便于相互检测。
每层标高允许误差不大于3mm,全层标高允许误差不大于15mm。
4、钢筋定位
装配整体式结构工程在设计过程中即将钢筋检讨图绘出,柱每侧竖向钢筋之间的间距必须按照钢筋检讨图进行绑扎,以利于预制梁的吊装,梁钢筋允许偏差不得大于5mm。
5、现浇柱垂直度
混凝土柱独立浇注时周边无梁板支撑架体,在加固上存在一定难度,因此在本层叠合梁板混凝土浇注时须埋设柱模加固埋件,每根柱采用三个面进行斜拉,在浇筑完成后再进行一次垂直度的监测,最终监测结果不得大于3mm。
6、现浇柱顶同平整度
柱混凝土浇筑顶面与梁接槎处,表面平整度不得大于2mm,梁吊装时间尽量在柱浇筑完成的12h后进行,已避免吊装时对柱混凝土造成损坏。
7、预埋件
叠合层内后置埋件分为三种,见附表:
8、钢筋连接
预制梁底部钢筋在中间支座采用帮条熔槽焊,由于接头位置在支座中,焊接操作较困难。
验收执行标准按照JGJ18-2003要求进行严格的把关。
9、屋面框架梁钢筋锚固
屋面框架梁节点处钢筋要求下锚入柱内1.7Lae,在施工中柱混凝土浇筑后才开始梁的吊装工作,因此,施工时将梁弯锚部分在适当的部位截成两段,在柱混凝土浇筑时将套好丝的钢筋先埋入柱内,待梁吊装完成后采用直螺纹套筒进行连接。
采用这种方法施工首先必须保证预埋钢筋的定位偏差不得大于5mm,标高控制不大于±5mm。
具体施工示意图如下:
(三)吊装质量的控制
吊装质量的的控制是装配整体式结构工程的重点环节,也是核心内容,主要控制重点在施工测量的精度上。
为达到构件整体拼装的严密性,避免因累计误差超过允许偏差值而使后续构件无法正常吊装就位等问题的出现,吊装前须对所有吊装控制线进行认真的复检。
1、吊装质量控制流程
2、梁吊装控制
(1)梁吊装顺序应遵循先主梁后次梁,先低后高(梁底标高)的原则。
(2)吊装前根据吊装顺序检查构件装车顺序是否对应,梁吊装标识是否正确。
(3)梁底支撑标高调整必须高出梁底结构标高2mm,使支撑充分受力,避免预制梁底开裂。
由于装配整体式结构工程的构件不是整体预制,在吊装就位后不能承受自身荷载,因此梁底支撑不得大于2m,每根支撑之间高差不得大于1.5mm、标高不得大于3mm。
3、板吊装控制
(1)板吊装顺序尽量依次铺开,不宜间隔吊装。
(2)板底支撑与梁支撑基本相同,板底支撑不得大于2m,每根支撑之间高差不得大于2mm、标高不得大于3mm,悬挑板外端比内端支撑尽量调高2mm。
(3)每块板吊装就位后偏差不得大于2mm,累计误差不得大于5mm。
4、墙吊装控制
(1)吊装前对外墙分割线进行统筹分割,尽量将现浇结构的施工误差进行平差,防止预制构件因误差累积而无法进行。
(2)吊装顺序与板的吊装基本一致,吊装应依次铺开,不宜间隔吊装。
(3)预制墙体调整顺序:
预制墙底部有两组调节件和预制墙中部一组斜拉杆件,每组分为B类(标高调整)和C类(面外调整);埋件于叠加层梁上埋件对应使用,底部调整完后进行上部调整、最后进行统一调整。
(4)墙吊装时应事先将对应的结构标高线标于构件内侧,有利于吊装标高控制,误差不得大于2mm;预制墙吊装就位后标高允许偏差不大于4mm、全层不得大于8mm,定位不大于3mm。
5、其它构件吊装控制
其它小型构件的吊装标高控制不得大于5mm,定位控制不大于8mm。
6、吊装注意事项
(1)吊装前准备工作充分到位。
(2)吊装顺序合理,班前质量技术