电厂运行中汽轮机用矿物油维护管理导则.docx
《电厂运行中汽轮机用矿物油维护管理导则.docx》由会员分享,可在线阅读,更多相关《电厂运行中汽轮机用矿物油维护管理导则.docx(19页珍藏版)》请在冰豆网上搜索。
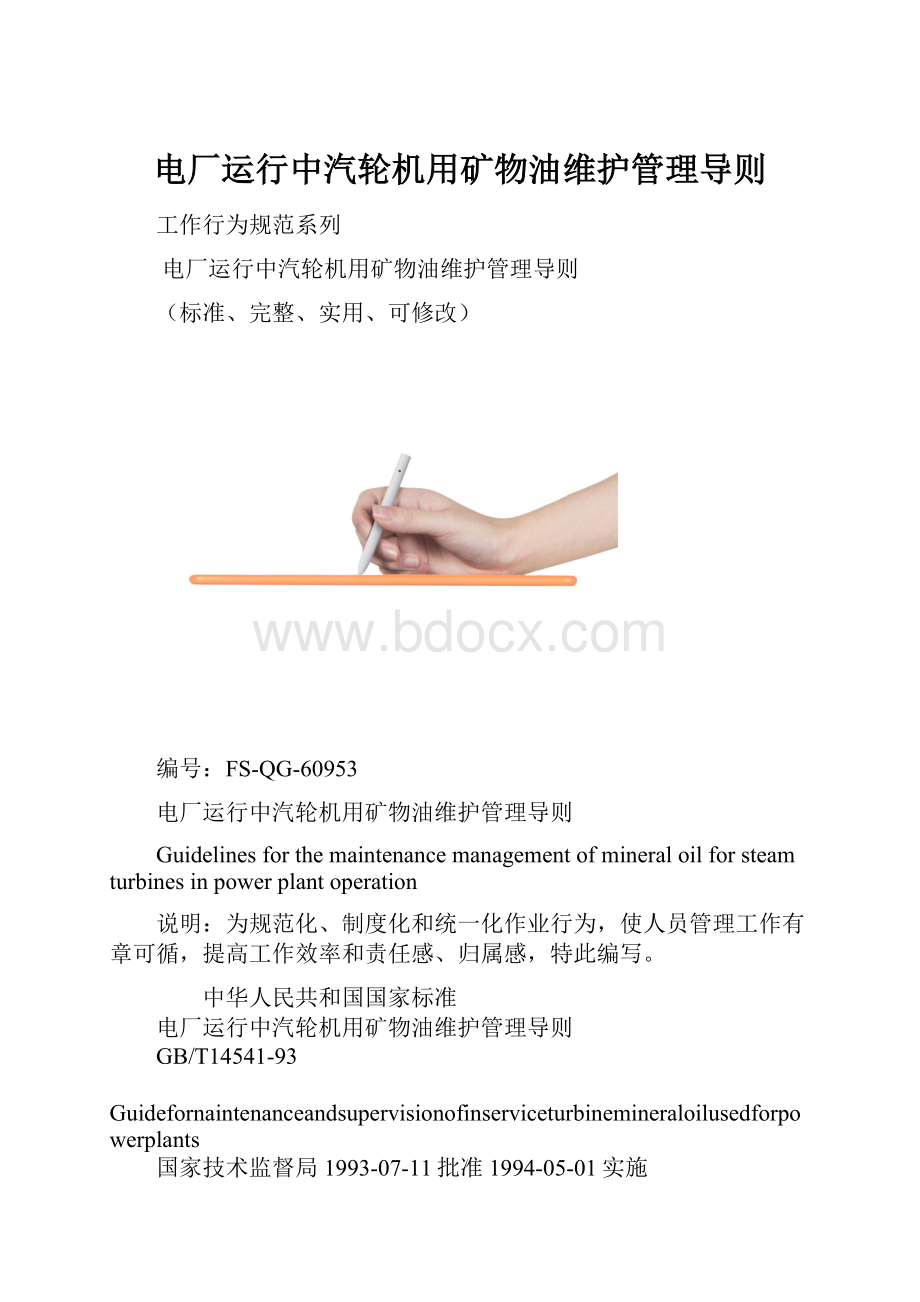
电厂运行中汽轮机用矿物油维护管理导则
工作行为规范系列
电厂运行中汽轮机用矿物油维护管理导则
(标准、完整、实用、可修改)
编号:
FS-QG-60953
电厂运行中汽轮机用矿物油维护管理导则
Guidelinesforthemaintenancemanagementofmineraloilforsteamturbinesinpowerplantoperation
说明:
为规范化、制度化和统一化作业行为,使人员管理工作有章可循,提高工作效率和责任感、归属感,特此编写。
中华人民共和国国家标准
电厂运行中汽轮机用矿物油维护管理导则
GB/T14541-93
Guidefornaintenanceandsupervisionofinserviceturbinemineraloilusedforpowerplants
国家技术监督局1993-07-11批准1994-05-01实施
本导则是参照了IECTC10236—85《汽轮机矿物润滑油使用与维护导则》和ASTMD4378—84a《运行汽轮机和燃气轮机的透平油监督》,并对国内部分电厂汽轮机油的使用维护情况作了调研与资料收集,在此基础上制定了本导则。
由于各单位情况不尽相同,在使用本导则时必须参考设备的类型和使用状况以及设备用油的特性,必要时还应参考制造厂家的说明。
1主题内容与适用范围
1.1本导则适用于电厂汽轮机系统用作润滑和调速的矿物油,也适用于水轮机调相机及给水泵等电站其他设备方面所用的矿物汽轮机油。
1.2本导则的目的是为电厂设备操作人员评价油品在设备中的使用状况,做好油质监督维护工作提供指导。
对油质评价的要求、油在使用中质量发生变化的原因及防止油质劣化的措施也作了必要的说明。
1.3本导则不适用于各种用作汽轮机润滑和调速的非矿物质的合成液体。
2引用标准
GB264石油产品酸值测定法
GB/T265石油产品运动粘度测定法和动力粘度计算法
GB/T267石油产品闪点与燃点测定法(开口杯法)
GB/T511石油产品和添加剂机械杂质测定法(重量法)
GB2537汽轮机油
GB7596电厂用运行中汽轮机油质量标准
GB7597电力用油(变压器油、汽轮机油)取样方法
GB7599运行中变压器油、汽轮机油酸值测定法(BTB法)
GB7600运行中变压器油水分含量测定法(库仑法)
GB7602运行中汽轮机油、变压器油T501抗氧化剂含量测定法(分光光度法)
GB7605运行中汽轮机油破乳化度测定法
GB11120LTSA汽轮机油(防锈汽轮机油)
GB11143加抑制剂矿物油在水存在下防锈性能试验法
GB/T12579润滑油泡沫特性测定法
SD313油中颗粒数及尺寸分布测量方法(自动颗粒计数仪法)
SH/T0124含抗氧剂的汽轮机油氧化安定性测定法
SH/T0308润滑油空气释放值测定法
DL429.2颜色测定法
DL429.6运行油开口杯老化测定法
DL429.7油泥析出测定法
3汽轮机油的性能和变质
3.1汽轮机油根据40℃的运动粘度划分为:
32、46、68和100四种牌号。
炼制时所选用的原油有石蜡基和混合基原油。
炼制汽轮机油的工艺为:
原油常减压蒸馏溶剂精制白土补充精制过滤加抗氧化剂或复合添加剂。
原油常减压蒸馏硫酸精制白土补充精制过滤加抗氧化剂或复合添加剂。
以上二种工艺,通常采用溶剂精制和白土补充精制较多。
酸碱精制过程,如增加电场作用,可以促使酸渣沉降速度加快。
3.2新汽轮机油的性能
新汽轮机油的质量应符合GB2537或GB11120标准,并应具备以下性能要求:
3.2.1粘温性
选择适当粘度的润滑油,对于保证机组的正常润滑是一个重要的因素。
粘度是汽轮机油的重要物理性能指标之一。
汽轮机油除了要求具有适当粘度外,还要求油的粘温特性好。
因油的粘度是随油温的升高而降低的,为保证机组在不同的温度下都能得到可靠的润滑,要求油的粘度随温度的变化愈小愈好,即油的粘温特性好,不随油温的升降而明显变化。
油的粘度选择是由制造厂根据汽轮机参数而确定的,油的粘度选择不当,粘度过大时功率损失大,粘度过小时会引起机组振动或设备磨损等问题。
使用单位需要更换油的粘度时应与制造厂商讨。
3.2.2氧化安定性
运行中汽轮机油处于强迫循环状态,不可避免地与大量空气接触而被氧化,另外温度、水分、金属催化剂和其他各种杂质都会加速油品氧化,同时也与油品的化学组成有关,不同的烃类具有不同的氧化历程(倾向),其氧化产物也不同。
但是烃类氧化初期产物大多是烃基过氧化物,而后分解为酸、醇、酮等,继续氧化则生成树脂质,沥青质等。
进一步氧化则会生成不溶于油的油泥,这些物质影响油品其他性能的降低。
3.2.3防锈性能
汽轮机油本身是无腐蚀性的,但在运行中不可避免地或多或少漏入蒸汽或水,引起油系统产生锈蚀,严重时可引起调速系统卡涩机组振动、磨损等不良后果。
解决油系统因漏水而引起锈蚀的办法,除提高设备密封性减少漏汽漏水外,还要求汽轮机油具有良好的防锈性能。
3.2.4起泡沫性
由于汽轮机润滑系统的油,是强迫循环方式,空气激烈地搅动,油面上会产生泡沫,油中也会产生气泡。
泡沫和气泡的生成,使油泵油压上不去而影响油的循环,破坏油膜,发生磨损,同时油压不稳,影响调节。
严重时泡沫由油箱顶部外溢,威胁机组运行,所以油品必须具有抗起泡沫性能。
3.2.5空气释放性
一般矿物油能溶解8%~9%(体积)空气,但是当油品通过管线、轴承、齿轮时,溶解的空气由于压力下降形成气泡,如气泡从油中释放过慢而滞留在油中,会带来以下几个问题:
a.增加了油的可压缩性,导致控制系统失灵,产生噪声和振动,严重时甚至会损害设备。
b.降低泵的有效容积。
c.降低泵的出口压力,特别是对于离心泵。
d.油中溶有空气,特别在高温情况下使用,会加速油的氧化变质。
油品放气性与油的组成有关。
油中芳烃、环烷烃及氮、硫化合物均影响其放气性。
添加剂如硅油及某些降凝剂对放气性影响较大。
通常汽轮机油中加入酸性防锈剂(T746),若被强碱物质污染,相互作用生成不溶性皂类物质,增加气泡稳定性,使油品的放气性变差。
3.2.6破乳化性能和析水能力
破乳化度是汽轮机油重要指标之一。
水分存在和激烈搅拌是产生乳化主要原因。
运行中汽轮机油因氧化变质产生的环烷酸皂,胶体等物质都是乳化剂,使油更容易乳化,乳化后的油会影响润滑作用,严重时会引起轴承磨损,机组振动及锈蚀等问题。
油品如有良好的析水能力,水则会沉降到油箱的底部,及时放掉;若油品析水能力差,就会有一定量的水分留在系统中,除对添加剂起化学作用外,还会对润滑性能产生影响,故要求汽轮机油具有良好的破乳化性能和析水能力。
3.3运行中汽轮机油变质因素
3.3.1化学成分
导致运行中油品变质因素很多,其内在因素主要是油品的化学组成。
基础油的石腊烃、环烷烃和芳烃相对比例,直接影响着油品的粘度指数、倾点等理化性能,芳烃对油品氧化安定性的影响有一定规律性,这与芳烃的结构和含量有关。
一般采取提高基础油精制深度,减少油中有害物质,加入添加剂来改进油品的质量。
但如添加剂选择不当,各种添加剂相互配合性对油品氧化安定性有一定影响,反会导致油品的性能变坏。
3.3.2油系统结构和设计
a.油箱用于储存系统全部用油,还起着分离油中空气、水分和各种杂质的作用,所以油箱结构设计对油品变质起着一定的作用。
若油箱容量设计过小,增加油循环次数,油在油箱停留时间就会相应缩短,起不到水分的析出和乳化油的破乳化,加速油的劣化。
b.油流速、油压对油品变坏都有关系。
进油管中的油不但应有一定的油压,而且还应维持一定的流速(约1.5~2m/s)。
回油管中的油是没有压力的,但也应保持有一定的流速(约0.5~1.5m/s)。
若回油速度太小,回到油箱冲力也大,会使油箱中的油飞溅,容易形成泡沫,造成油中存留气体而加速油品的变质。
同时冲力造成激烈搅拌会使含水的油形成乳化。
3.3.3启动时油系统状况
新机组投运前,润滑系统管路往往会存在焊渣、碎片、砂粒等杂物,若未彻底清除干净,投运后会带来很大麻烦,严重时会造成轴承磨损和调速器卡涩等问题,这些杂质还能影响油的物理化学性能降低,导致油质变坏,所以润滑系统每个部件都应预先清洗过并加强防护措施,防止腐蚀和污染物的进入,在现场贮存期间要保持润滑油系统内表面清洁,安装部件时要使系统开口最小,减少和避免污染,保持清洁。
3.3.4油系统的运行温度
影响汽轮机油使用寿命的最重要因素之一是运行温度,特别在系统中一般是在轴承部位上有过热点出现时,会引起油的变质,此时应调节冷油器,控制油温。
3.3.5油系统检修
油系统检修质量好坏,对油品的物理化学性能有着直接关系。
尤其是漏汽漏水的机组油系统比较脏,油中会有铁锈、乳化液,沉淀物,若不能彻底清除干净,则会降低油品的性能,有时由于检修方法不当,如用洗衣粉等清洗剂,冲洗不净,就会造成油品被污染,检修时应尽量采用机械方法清除杂物,然后用油冲洗,循环过滤,并采用变温冲洗方式,变温范围在30~70℃。
冲洗过程应取样检验,油中杂质含量应达到规定要求。
3.3.6污染问题
在运行过程中,汽轮机油中污染物来自两个方面:
一是系统外污染物通过轴封和各种孔隙进入;二是内部产生的污染物,包括水、金属磨损颗粒及油品氧化产物,这些污染物都会降低汽轮机油的润滑、抗泡沫等性能。
所以汽轮机油运行中消除污染是必须进行的工作,否则不仅会加速油的变质,还会影响机组安全运行。
3.3.7汽轮机油受到辐射
核电站所用的汽轮机油会受到不同程度辐射的影响,发生变化是不可逆的。
其变化程度取决于油品的组分,烷烃、环烷烃所受影响比芳烃要更强,经辐射后,组分中C—C及C—H结合键发生分裂,释放出氢气,有少量甲烷及其较高的同系物。
对非饱和烃是一种聚合反应,氢气析出的量较饱和烃少。
油品受到辐射作用后,其物理化学性能和润滑性能都会发生变化,受到辐射破坏的突出表现:
有气体析出,粘度增大,氧化安定性和防腐蚀性能下降,颜色变深,出现油泥,酸值增大,同时产生难闻气味的化合物。
同时,闪点有可能降低。
这些性能的变化,与油的组成和添加剂有关。
一般辐射剂量超过106J/kg才显示出来。
4油质试验意义
4.1运行油应检查外观、沉淀物。
因为这是表明游离水或乳化物、不溶性油泥、纤维和固体颗粒等脏物存在的直观依据。
4.2颜色:
按DL429.2方法试验。
新汽轮机油一般是浅色的,在运行中颜色会逐渐变深,但这种变化趋势比较缓慢。
若油品的颜色急剧加深还不足以说明油质的变坏程度,必须进行其他的试验项目加以补充证明。
但应考虑,有些油品暴露于光线下,也会加深油品的颜色,试验时应注意这一点。
4.3水分:
按GB7600定量方法试验。
汽轮机油中水分的存在会加速油质的老化及产生乳化,同时会与油中添加剂作用,促使其分解,导致设备锈蚀。
水的存在表明冷油器泄漏、大气中湿气进入油箱或轴封部件密封不严,携带蒸气进入油中所致。
4.4运动粘度:
按GB/T265方法试验。
检验汽轮机油的粘度,主要是鉴别所补加的油是否正确或油中是否有污染物存在。
4.5闪点(开口):
按GB/T267方法试验。
汽轮机油的闪点是机组安全运行的一项控制项目。
因机组过热或混入轻质油品均可影响闪点,一经发现闪点异常,应采取适当措施以保证机组安全运行。
4.6酸值:
按GB/T264或GB7599方法试验。
油酸值是一项较重要的指标,它能反映油质的劣化情况,以便采取正确的维护措施。
4.7氧化安定性:
按SH/T0124方法试验
氧化安定性试验是用来评价汽轮机油使用寿命长短的一种手段。
国产新汽轮机油出厂时,氧化安定性是属于保证项目。
运行中油的测定可以提示应采取适当的维护措施或添加抗氧化剂,以延长油使用寿命。
4.8防锈性能:
按GB/T11143方法试验。
防锈性能是目前防锈汽轮机油较重要的使用性能之一。
系统中因某种原因而带入水分,则较易造成整个系统或某些部件的锈蚀。
因此汽轮机油中需添加防锈剂。
运行中随着水分和颗粒的排除,均会使防锈剂减少而导致防锈性能下降,所以在适当时候应考虑补加防锈剂。
4.9油泥和沉淀物:
按DL429.7方法试验。
这些物质是溶解于油中的化合物。
它是由油自身的氧化或者外部杂质溶解于油中(设备结构中采用的材料溶解于油)而产生的,它能显示油品变质的迹象。
一旦产生油泥时,需对氧化安定性进行检查。
4.10破乳化性能:
按GB7605方法试验。
若油品乳化,油水不易分离,则表明油品已经变质或被某些表面活性物质所污染,长期运行下去容易造成系统某些部件的锈蚀,应对油进行处理或加入破乳化剂,以使油、水能很好分离。
4.11起泡沫性:
按GB/T12579方法试验。
本试验表示油形成泡沫的倾向和形成泡沫后泡沫的稳定性。
汽轮机油形成泡沫,威胁机组安全运行。
因此,必须采取消除泡沫的措施,如添加消泡剂或进行其他方式的处理。
4.12空气释放值:
按SH/T0308方法试验。
本试验是表示油中存留空气(气体)的性能。
尤其对于大容量机组,特别是调速系统空气释放值是愈小愈好,有利于润滑和调节作用,使用某些消泡剂(如硅油类)将不利于空气的释放。
4.13颗粒度试验:
按SD313方法试验。
油中颗粒度的测定,对于要求严格的大容量机组是十分重要的。
特别应强调的是对于新机组启动前或运行检修的汽轮机油系统,必须进行认真的清洗和冲洗。
运行中如发现油中颗粒数突然增加,需立即检查净化装置的过滤层,如发现腐蚀或磨蚀颗粒,应对油系统进行精密过滤处理,并查明颗粒来源,必要时应停机检查,以消除隐患。
5取样
当从贮油桶或运行设备内取样时,正确的取样技术和样品保存是很重要的(见GB7597)对于颗粒计数测定有专门的取样方法(见SD313)。
5.1新油到货时的取样
对新到货或准备新购置的油品,应当严格地执行取样手续,以使样品具有代表性。
5.1.1新油以桶装形式交货时,取样数目和方法应按GB7597方法进行,应从污染最严重底部取样,必要时可抽查上部油样。
如怀疑大部分桶装油有不均匀现象时,应重新取样;如怀疑有污染物存在,则应对每桶油逐一取样。
并应逐桶核对牌号、标志,在过滤时应对每桶油进行外观检查。
5.1.2对油槽车应进一步从下部阀门处进行取样。
因为留在油槽车底部的阀门导管上的粘附物可能使油品部分的污染,特别是装过不同油品的油槽车,更有可能出现上述的污染,必要时抽检上部油样。
5.2运行中从设备内取样
5.2.1正常的监督试验,一般情况下从冷油器中取样。
5.2.2检查油的杂质及水分时,应从油箱底部取样。
5.2.3在发现不正常情况时,需从不同的位置上取样,以跟踪污染物的来源和寻找其他原因。
5.2.4如果需要时,从管线中取样,则要求管线中的油应能自由流动而不是停滞不动,避免取到死角地方的油。
5.3取样瓶
取样瓶一般为500~1000mL的磨口具塞玻璃瓶,并应符合下述要求:
5.3.1取样瓶应先用洗涤剂进行充分清洗,再用自来水冲洗然后用去离子水(或蒸馏水)冲洗干净,放于105℃烘箱中干燥冷却后,盖紧瓶塞,备用。
5.3.2取样瓶应能满足存放的要求。
无盖容器或无色透明玻璃容器是不适于贮存的,应采用磨口具塞的棕色玻璃瓶。
5.3.3取样瓶应足够大,以适应试验项目的需要,一般为1000mL是足够用的。
5.3.4对于新油验收或进口油样,一般应取双份以上的样品,除试验所需的用量以外,应保留存放一份以上的样品,以备复核或仲裁用。
5.4标记
每个样品应有正确的标记,一般取样前应将印好的标签粘贴于取样容器上。
标签至少应包括下述内容:
a.单位名称;
b.机组编号;
c.汽轮机油牌号;
d.取样部位;
e.取样日期;
f.取样人签名。
取样完后,应及时按标签内容要求,逐一填写清楚。
6新油的评定
汽轮机油的取样、检验和注入机组中循环,均应按标准方法和程序进行,特别需要有经验的和技术水平较高的工作人员进行操作。
同时应对全过程的微小细节严加注意,以保证数据的真实性和可靠性。
6.1新油交货时的验收
在新油到货时,应对接受的油样进行监督,以防止出现差错,或交货时带入污染物。
所有的样品应在注入时进行外观检验。
对国产新汽轮机油应按GB2537或GB11120验收;对从国外进口的汽轮机油则应按有关国外标准或按ISO8068的标准验收或按合同规定指标验收。
6.2新油注入设备后试验程序
6.2.1当油装入设备后进行系统冲洗时,应连续循环,对系统内各部件进行充分清洗,以除去在安装、管道除锈过程中所遗留的污染物和固体杂质。
直到取样分析各项指标与新油无差异,特别是对大机组清洁度有要求的,必须经检查清洁度达到要求时,才能停止油系统的连续过滤循环(国内目前正在建立清洁度的标准,在尚未建立完善以前,一般情况下可按SAE7491中的5~6级或NAS1638中的8~9级才符合要求)。
注:
SAE为美国汽车工程师学会标准。
NAS为美国宇航标准。
6.2.2新油注入设备,经过24h循环后,从设备中采取4L油样,供检验和保存用。
试验项目:
外观——清洁、透明、无游离水。
颜色——符合新油指标。
粘度——符合新油指标。
酸值——符合新油指标。
闪点——符合新油指标。
颗粒数量:
符合规定的指标。
7运行中汽轮机油的检验
运行中汽轮机油除定期进行较全面的检测以外,平时必须注意有关项目的监督检测,以便随时了解汽轮机油的运行情况,如发现问题应采取相应措施,保证机组安全运行。
7.1运行中的日常监督
7.1.1现场检验:
现场检验包括以下性能的测定:
外观:
目测无可见的固体杂质;
水分(定性):
目测无可见游离水或乳化水;
颜色:
不是突然变得太深。
以上项目和运行油温、油箱油面高度均可由汽轮机操作人员或油化人员观察、记录。
7.1.2试验室检验:
试验室检验,250MW机组以上按表1、表2、表3进行。
250MW及以下按GB7596规定进行。
大多数试验可在电厂化验室进行,某些特殊试验项目需经过认可的试验室承担,如颗粒度试验等。
7.2检验周期
至少每星期检查一次外观、机械杂质及游离水或乳化情况,对漏水机组应坚持每天检查上述项目,其他试验项目按表2所列的正常试验周期外,所增加的试验次数,有利于观察新机组的运行情况。
表3所列为各项试验的运行中超极限值可能的原因及采取措施。
8油的相容性(混油)
8.1汽轮机、水轮机等发电设备需要补充油时,应补加与原设备用相同牌号的新油或曾经使用过的合格油。
由于新油与已老化的运行油对油泥的溶解度不同,当向运行油、特别是油质已严重老化的油中补加新油或接近新油标准的油时,就可能导致油泥在油中析出,以致破坏汽轮机油的润滑,散热或调速特性,威胁机组安全运行。
因此,补油前必须预先进行混合油样的油泥析出试验,无油泥析出方可允许补加。
表1新汽轮机组(250MW以上)投运12个月内的检验周期表
表2250MW以上汽轮机组正常运行检验周期表
表3运行中汽轮机油试验数据及措施概要
注:
1)参考国外标准控制限值为600mL。
2)参考国外标准控制限值为600min。
3)参考SAE标准5~6级或NAS1638中规定为8~9级。
4)参考国外标准控制限值为600。
8.2混合使用的油,混合前其质量均必须检验合格。
8.3不同牌号的汽轮机油原则上不宜混合使用,因为不同牌号油的粘度范围各不相同,而粘度是汽轮机油的一项重要指标。
不同类型、不同转数的机组,要求使用不同牌号的油,这是有严格规定的,一般不允许将不同牌号的油混合使用。
在特殊情况下必须混用时,应先按实际混合比做混合油样的粘度试验,如粘度符合要求时才能继续进行油泥析出试验,以决定是否可混。
8.4进口油或来源不明的油,需与不同牌号的油混合时,应预先对混合前后的油进行粘度试验。
如在合格范围之内,再进行老化试验,老化后混合油的质量应不低于未混合油中最差的一种油,方可混合使用。
8.5试验时,油样的混合比应与实际使用的比例相同;如果运行油的混合比是未知的,则油样采用1∶1比例混合。
8.6矿物汽轮机油与用作润滑、调速的合成液体有本质的区别,切勿将两者混合使用。
9防止油劣化措施
9.1为延长油的使用寿命和保证设备安全运行,应对运行中油采取防劣措施。
主要有:
9.1.1采用滤油器,随时清除油中的机械杂质,油泥和游离杂质,保持油系统的清洁度;
9.1.2在油中添加抗氧化剂(常用T501抗氧化剂),以提高油的氧化安定性。
对漏水、漏汽机组,还应同时添加防锈剂(常用T746防锈剂);
9.1.3安装油连续再生装置(净油器),随时清除油中的游离酸和其他老化产物。
9.2滤油器包括滤网式、缝隙式、滤芯式和铁磁式等类型,机组设计时,应根据油中污染物的种类和含量以及油系统重要部件对油清洁度的要求合理配装滤油器。
9.2.1汽轮机油系统的不同部位应配有合适的滤油器,对大型机组除在油箱设有滤网外,在润滑系统及调节系统管路上分别装设滤网或刮片式滤油器;在供给电液调节系统的油路上,除装设一般滤油器外,还须增设磁性滤油器。
必要时,旁路滤油器前,应装设冷却器,以利从油中析出老化产物并对其滤除。
9.2.2滤油器的截污能力决定于过滤介质的材质及其过滤孔径,金属质滤料包括筛网,缝隙板、金属颗粒或细丝烧结板(筒)等,其截留颗粒的最小直径约在20~1500μm,其过滤作用是对机械杂质的表面截留。
这种金属质滤元使用后可清扫再用。
非金属滤料包括滤纸、编织物、毛毡、纤维板压制品等,其截留颗粒的最小直径约为1~50μm,对清除机械杂质兼有表面和深层截留作用,还对水分与酸类有吸收或吸附作用。
但非金属质滤元的机械强度不及金属质,只能一次性使用,用后废弃换新。
9.2.3滤油器在使用中应加强检查和维修。
定期检查过滤器滤元上的附着物,可以及时发现机组、油循环系统及油中初始出现的问题。
如果发现滤油器滤元有污堵、锈蚀、破损或压降过大等异常情况,应查明原因并进行清扫或更换,精密滤元一般每年至少更换一次。
9.2.4对大型机组,特别是漏水、漏汽或油污染严重的机组,可增设大型油净化器。
这种油净化器由沉淀箱、过滤箱、贮油箱、排油烟机、自动抽水器和精密滤油器等组成。
这种油净化器由于具有较大油容积。
对油中水分、杂质的清除兼有重力分离,过滤与吸附净化作用,净化效率高且运行安全可靠(见图1)。
图1油净化器结构简图
1—抽水器;2—分式网;3—袋滤器;4—油位计;5—通风机;6—过滤筒;7—回主油箱;8—贮油箱;9—过滤箱;10—沉积箱
图2净油器在汽轮机油系统内安装方式
1—主油泵;2—调节阀;3—油箱及吸入管线来油;4—重调
系统;5—冷却水进出口;6—净油器进口油管;7—净油器;
8—净油器出口净化油管;9—辅助油泵
9.3油连续再生装置(净油器)是一种渗滤吸附装置。
它利用硅胶、活性氧化铝等吸附剂除去运行油老化过程中产生的酸类等老化产物,对防止调节系统电液、伺服零件的腐蚀有良好作用。
由于吸附剂可能同时吸附油中的某些添加剂,含有防锈剂或破乳剂的油在使用净油器后,油中应补加添加剂