零部件PPM质量管理.ppt
《零部件PPM质量管理.ppt》由会员分享,可在线阅读,更多相关《零部件PPM质量管理.ppt(54页珍藏版)》请在冰豆网上搜索。
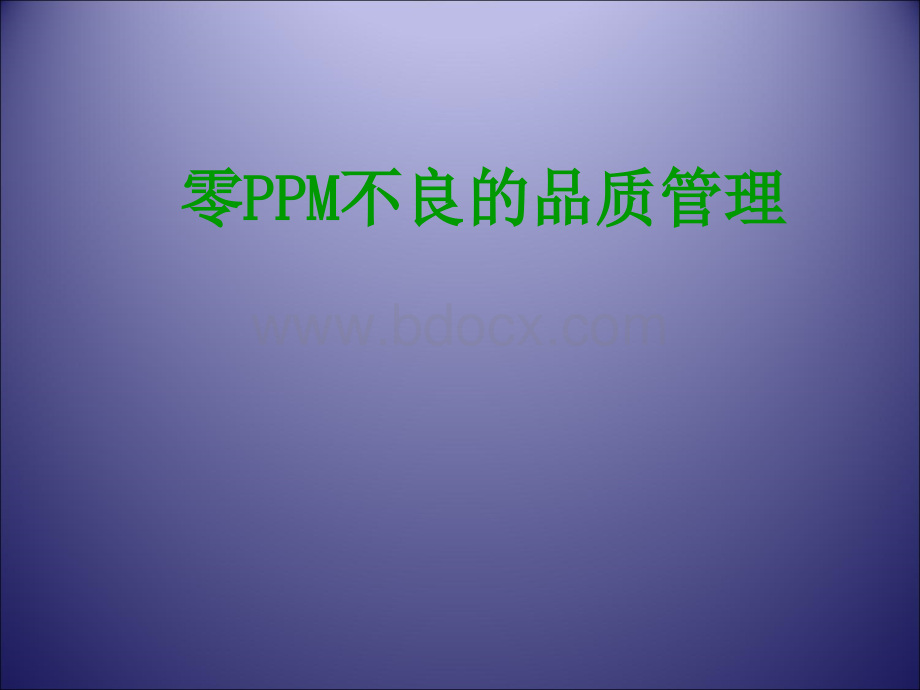
零零PPMPPM不良的品质管理不良的品质管理第一章第一章不良的总体认识不良的总体认识一、为何会产生不良一、为何会产生不良不良品的产生,主要的根源就是实际生产操作的结果,与标准规范的要求有所差异而形成的。
就影响产品品质的因素而言,主要有所谓“5M1E”的因素,如下:
1)Man(人员因素)2)Material(材料因素)3)Machine(机器因素)4)Method(方法因素)5)Measurement(量测因素)6)Environment(环境因素)换句话说,要制订上述六大因素的生产作业的标准规范,并且要能依照标准规范工作。
二、不良的二大类别二、不良的二大类别不良的意义,可以说不符合规格要求的产品,就是不良。
不良的意义,可以说不符合规格要求的产品,就是不良。
更严谨地说,不符合客户需求的产品,但是却符合自己公司生产的要更严谨地说,不符合客户需求的产品,但是却符合自己公司生产的要求产品,也是不良品,因此不良品可以概分为二大类别。
求产品,也是不良品,因此不良品可以概分为二大类别。
显在的不良显在的不良在生产中可以被在生产中可以被检测出来的不良检测出来的不良仍然会有漏网之鱼之仍然会有漏网之鱼之不良流到客户手中不良流到客户手中潜在的不良潜在的不良在生产检测时认为是良品,但是在生产检测时认为是良品,但是客户使用一段期间后成为不良品客户使用一段期间后成为不良品可靠性或信赖性不佳所致可靠性或信赖性不佳所致与制程方式及产品设计零件材与制程方式及产品设计零件材料使用有关料使用有关三、产生不良的原因三、产生不良的原因不良可以说是,只要客户不满意公司的产品,就可以称不良可以说是,只要客户不满意公司的产品,就可以称为不良。
就生产过程中,为何会产生一些显在的不良,其主要的原因,为不良。
就生产过程中,为何会产生一些显在的不良,其主要的原因,可以概分如下:
可以概分如下:
1)1)加工位置错误或尺寸错误加工位置错误或尺寸错误2)2)遗落加工工作或包装动作遗落加工工作或包装动作3)3)作业条件设定错误作业条件设定错误4)4)欠缺零件、物品欠缺零件、物品5)5)异品混入,或未清除异品混入,或未清除6)6)设备制程能力不足设备制程能力不足7)7)刀具、治具、夹具不完备刀具、治具、夹具不完备8)8)错误动作错误动作9)9)检查、测试误差检查、测试误差10)10)生产作业方式不佳生产作业方式不佳造成以上这些不良的原因,有些是在生产技术上,设计造成以上这些不良的原因,有些是在生产技术上,设计不周到所造成的。
有些,则是属于人员操作上的疏失,错误,或无心不周到所造成的。
有些,则是属于人员操作上的疏失,错误,或无心之过所造成的。
之过所造成的。
产产生生不不良良的的十十大大原原因因加工错误加工错误加工遗落加工遗落条件错误条件错误欠缺物品欠缺物品异品混装异品混装能力不足能力不足工具不备工具不备动作错误动作错误检测误差检测误差方式不佳方式不佳四、不良的原因与真因四、不良的原因与真因解决不良的首要前提,是要能先找出问题的根源所在。
解决不良的首要前提,是要能先找出问题的根源所在。
此即此即“真因真因”之意。
之意。
“真因真因”与一般所言之与一般所言之“原因原因”是不同的。
一般是不同的。
一般所言之原因,如鱼骨图所示,系指可能会造成不良的各种缘由。
而所言之原因,如鱼骨图所示,系指可能会造成不良的各种缘由。
而“真因真因”系指对某一特定之不良品,造成不良的某一个或某一些缘由。
系指对某一特定之不良品,造成不良的某一个或某一些缘由。
解决不良的重点方向,是要找出不良的解决不良的重点方向,是要找出不良的“真因真因”,而不是知道不良的,而不是知道不良的原因。
原因。
从许多现场实务上,所见到的许多不良改善的实例,发从许多现场实务上,所见到的许多不良改善的实例,发现许多人,大都是从原因面去下对策,寻求解决降低不良。
虽然,有现许多人,大都是从原因面去下对策,寻求解决降低不良。
虽然,有时也有一些效果,但是,具体大幅度的降低却很少见。
主要的原因在时也有一些效果,但是,具体大幅度的降低却很少见。
主要的原因在于大多数人,忽略了于大多数人,忽略了“真因真因”与与“原因原因”是不同层面的之事。
往往只是不同层面的之事。
往往只在在“原因面原因面”上下功夫,而犯了上下功夫,而犯了“事倍功半事倍功半”之果。
另一方面,是缺之果。
另一方面,是缺乏寻找乏寻找“真因真因”的方法。
当然,只能在传统的的方法。
当然,只能在传统的“原因面原因面”上去探讨问上去探讨问题。
所以说,找题。
所以说,找“真因真因”可真是一门学问。
寻找真因的经验归纳总结可真是一门学问。
寻找真因的经验归纳总结为如下的七个手法:
为如下的七个手法:
11)五现法五现法22)地图法地图法33)五问法五问法44)比较法比较法55)放大法放大法66)解剖法解剖法77)潜水法潜水法原因原因真因真因是不同的是不同的与与结果结果机器机器环境环境量测量测方法方法人员人员材料材料原因原因真因真因:
系指如鱼骨图所示,会造成不良结果的所有:
系指如鱼骨图所示,会造成不良结果的所有“各种可能的各种可能的缘由缘由”:
系指对某一:
系指对某一“特定不良品特定不良品”,造成不良结果的,造成不良结果的“特定缘由特定缘由”。
寻找真因七手法寻找真因七手法(一一)-)-五现法五现法五现法是指现场、现物、现实、现做、现查,五个名词。
代表从事不良改善,寻找真因时,第一个应用的手法。
具体而言,指寻找真因时,必须“走入现场”、“观察现物”、“了解现实”、“立即现做”、“效果现查”的五个过程。
常见一般的解决不良的第一步骤,是要收集数据,理论而言,这是正确的步骤。
可是,实际的做法不同,却影响数据收集的效果,以及后续的改善效果。
一般常见的数据收集,往往都是经由现场作业员或检查人员的检查、测试结果、登录、统计、输入电脑,汇总成各种统计报表。
管理人员,或是工程技术人员,就依据这些统计资料,来做为问题的判定,以及坐在办公室内去思考问题,寻找一些想象的可能对策。
做做实验以求证效果。
这种做法,有时也产生效果,但大多数是无功而返。
依据第三者收集的资料,做为问题判定,改善对策的订,往往会偏离事实许多,因为,提供资料人员所填写的资料,可能太过简略无法提供详细有助于判定问题缘由的资讯。
所以,减少不良的第一个动作,一定要亲临不良的发生现场。
实际观察有关人员、机器、材料作业方式及环境的实能,才能有助于找到真因。
手法一五现法要走入现场观察现物了解现实立即现做效果现查不要坐在办公室,只读不良统计报表要亲临不良发生的现场,观察5M1E的实能手法二地图法人有面相观相论性物有物相观相定品寻找真因七手法寻找真因七手法(二二)-)-地图法地图法人有面相,观其面相可以推定一个人的性向,而产品也有“物相”,观其物相也可以推定产品的“品向”,亦即“品质的趋向”。
而“地图法”就是鉴定产品的“物相”之工具。
寻找真因七手法寻找真因七手法(三三)-)-五问法五问法五问法是指对问题现象,要问五次为什么,找出问题的真正根源所在。
一般人在看到问题的现象时,往往就认定是某一个表面的原因造成,而后,据此拟订对策,以为解决问题了,但一段时间之后,同样的不良又出现了,这表示不良的真因,或源头仍然没有被发觉出来。
问五次为什么,不是要问到第五次,才能发觉出问题的根源。
而是指要打破沙锅问到底,一直问到找出问题的源头为止,实物而言,有时问到第三次为止,就能找出真因,也就可以打住了,用不着,要凑到五次为止,同理,有时问到第五次仍然找不到真因,这时,仍然要继续下去,直到真因被发觉为止,问五次为什么的方法如下:
1)首先描述问题现象,要能具体叙述何人,何时,何地,在哪一部机器,用了哪一批材料,发生了哪一类别的问题,或不良有多少等等。
2)然后,心中默问“为什么出现上述的问题现象?
”据此探讨出此阶层的原因。
3)将上述之原因,转为下一个问为什么的源头,心中默问“为什么出现这个原因的现象”据此再探讨出下一个阶层的原因,如此反复进行,“为什么-因为”的模式,直到最底层问不下去为止,即表示真因所在。
手法三五问法要问五次为什么,打破沙锅问到底,找出问题的真正根源所在2003年4月12日下午2时14分在贴皮加工区由王建中操作之2号贴皮机器有停止生产现象问题现象1.有料夹在机器内,要停机排除夹料因为(为什么)2.夹层压皮要胶粘住薄皮因为(为什么)3.底板上层之薄皮比底板小,所以有胶外漏现象而且在“左上方”之残胶特别多因为(为什么)4.左上方之布胶伦上之扳子,在布胶后,不能自动完全转动出来因为(为什么)5.布胶机之“输出滚轴”过低,无法接触底板而转动出来因为(为什么)6.输出滚轴使用过久,被磨耗而没有更换因为(为什么)7.寻找真因七手法寻找真因七手法(四四)-)-比较法比较法比较法,指籍用比较两者之间的差异,协助我们找出问题的真因。
有时,亦可应用层别的做法,来协助进行比较的过程.例如,发生不良品,如果同一产品,生产线同时有数条生产线在生产.其中,必有一条不良率最高的生产线,和一条不良率最低的生线.我们就可以比较在这二条生产线中,机器设备方面是否有明显差异的地方.比如在压力方面,稳定性方面,速度方面等等,或者,在作业员操作的过程,手法等是否不同之处.如果,有不同之处,即是可能的真因所在.推定可能的真因之后,必须做实验以求证.如果,确实产生明显的改善成果,那就表示此为真因了.如果没有明显的改善成果,即表示真因尚未找到.必须再对其他的可能真因,继续实验求证,以迄找到真因为止.手法四比较法比较比较不良率最低的生产线不良率最低的生产线不良率最高的生产线不良率最高的生产线观察二者如下有何差异Man人员Material材料Machine机器Method方法Measurement测量Measurement环境依不同的层别比较依不同的层别比较生产线别、班别、人员别、日期别、生产批号别、材料批号别、机台别、天气别、小时别、温度别、湿度别等等。
放大法,顾名思义就是将问题的现象,或是不良的现象,如以放大来观察.有助于对问题的现象,更进一层了解.放大法除了指物体尺寸的放大之外,也可以指时间范围,及空间范围的放大和速度放慢的放大.有些不良品的现象,以肉眼目视的观察之下,无法清晰了解掌握不良的“物相”,当然也就无从明确确认不良的来源。
此时,可以把不良的“物相”放在放大境,或显微镜之下可以清晰地看出“物相”的状况。
并且同时与正常良品的“物相”互相比较,了解彼此之间的差異之处,从而找出可能的真因。
在某些情况下,甚至必须动用高倍电子显微镜才能看出“物相”的真实状况。
生产现场中,有时会有高速度的生产设备,有时会产生不良品,或者是瞬间停机状况太频繁,以肉眼目视观察,根本无法看出“物象”的状态此时,可以利用高速摄影机拍摄下来,事后再慢速播放有助于了解掌握问题的真相,从而解决问题或减少不良.空间的放大是指在探讨问题时,不要只观察某一个点的地域,可以再看看其他的区域是否也有类似的问题以及多寡的存在.时间的放大是指可以看看过去一星期,一个月或一季或半年一年以内的变化情形,找出可疑之处.寻找真因七手法寻找真因七手法(五五)-)-放大法放大法手法五放大法尺寸的放大尺寸的放大空间的放大空间的放大时间的放大时间的放大速度的放大速度的放大解剖法是指将产品拆开,观察内部的状况,才能深入了解不良的来源.解剖法由于必须拆解产品或是剖开产品之后,才能进行观察;所以,通常是破坏性的检查方式.因而解剖法也被视为最后不得已的寻找真因的手法.就是指在应用前述五个手法之后,仍然无法找出真因时,最后不得已,只好解剖来看.例如:
在制造一个金属密闭的小球体,要经过音鸣检查.在静音室内,作业者已经事先以高压空气将球体内的残留杂质清出,再经过静音检测后,确定没有异音存在.可是在运交到客户手中之后,仍然偶尔会收到客户的抱怨,有异音存在。
其真因的追查确实很困难。
最后,只有采用解刨法,将有异音的产品刨开来看,再配合放大法,观察产品内部是否有异物存在。
终于发现有一小粒的金属颗粒。
再经过高倍显微镜观察,得以判定是属于电焊后,铁水的残留物,残留在焊道下