零件的机械加工工艺规程编制和专用夹具设计.docx
《零件的机械加工工艺规程编制和专用夹具设计.docx》由会员分享,可在线阅读,更多相关《零件的机械加工工艺规程编制和专用夹具设计.docx(39页珍藏版)》请在冰豆网上搜索。
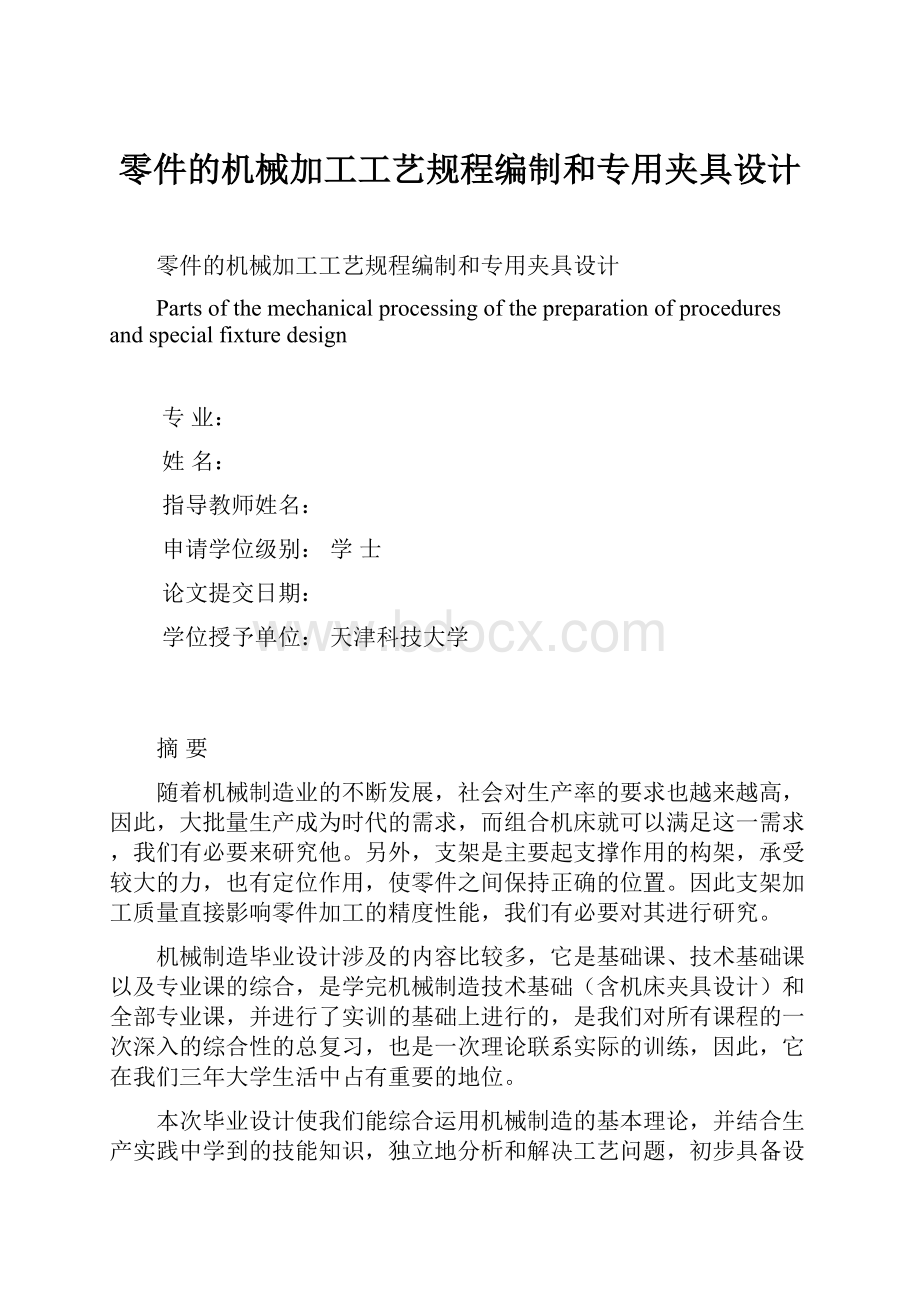
零件的机械加工工艺规程编制和专用夹具设计
零件的机械加工工艺规程编制和专用夹具设计
Partsofthemechanicalprocessingofthepreparationofproceduresandspecialfixturedesign
专业:
姓名:
指导教师姓名:
申请学位级别:
学士
论文提交日期:
学位授予单位:
天津科技大学
摘要
随着机械制造业的不断发展,社会对生产率的要求也越来越高,因此,大批量生产成为时代的需求,而组合机床就可以满足这一需求,我们有必要来研究他。
另外,支架是主要起支撑作用的构架,承受较大的力,也有定位作用,使零件之间保持正确的位置。
因此支架加工质量直接影响零件加工的精度性能,我们有必要对其进行研究。
机械制造毕业设计涉及的内容比较多,它是基础课、技术基础课以及专业课的综合,是学完机械制造技术基础(含机床夹具设计)和全部专业课,并进行了实训的基础上进行的,是我们对所有课程的一次深入的综合性的总复习,也是一次理论联系实际的训练,因此,它在我们三年大学生活中占有重要的地位。
本次毕业设计使我们能综合运用机械制造的基本理论,并结合生产实践中学到的技能知识,独立地分析和解决工艺问题,初步具备设计一个中等复杂程度零件(支架)的工艺规程的能力和运用夹具设计的基本原理和方法,拟定夹具设计方案,完成夹具结构设计的能力,也是熟悉和运用有关手册、图表等技术资料及编写技术文件等基本技能的一次实践机会。
关键词:
设计制造;自动化;机械制造;夹具设计
ABSTRACT
Withthecontinuousdevelopmentofmachinerymanufacturing,society'sdemandforproductivityisalsoincreasing,therefore,massproductionbecomestheneedsofthetimes,andthecombinationofmachinetoolscanmeetthisdemand,weneedtostudyhim.Inaddition,thebracketisthemainsupportfromtheroleoftheframework,towithstandthelargerforce,butalsopositioningrole,sothatthepartsremaininthecorrectposition.Therefore,thequalityofstentprocessingdirectlyaffecttheaccuracyofpartsprocessingperformance,weneedtostudyit.
Itisthebasisofthebasiccourse,thetechnicalbasiccourseandthespecializedcourse.Itisthebasisofthemechanicalmanufacturingtechnologyfoundation(includingthemachinetoolfixturedesign)andallthespecializedcourses,andthetrainingiscarriedoutonthebasisofthetraining.Wehaveanin-depthcomprehensivereviewofallthecourses,butalsoatheoreticalconnectionwiththeactualtraining,soitisinourthreeyearsofcollegelifeoccupiesanimportantposition.
Thisgraduationdesignallowsustocomprehensivelyusethebasictheoryofmechanicalmanufacturingandcombinetheskillslearnedinproductionpracticetoanalyzeandsolveprocessproblemsindependently,withtheabilitytodesignaprocessspecificationforamoderatelycomplexpart(stent)Theuseoffixturedesignofthebasicprinciplesandmethodstodevelopfixturedesignprogramtocompletethefixturestructuredesigncapabilities,butalsofamiliarwithanduseofmanuals,chartsandothertechnicalinformationandthepreparationoftechnicaldocumentsandotherbasicskillsofapractice.
Keywords:
Designandmanufacture;automation;machinerymanufacturing;fixturedesign
目录
第一章对零件进行工艺分析并画零件图1
一、支架的作用及结构特点1
二、零件的工艺分析1
三、支架的零件图,见图纸所示。
3
第二章选择毛坯的制造方式并绘制毛坯简图3
一、选择毛坯的制造方式3
二、确定毛坯的形状、大小4
第三章制订零件的机械加工工艺路线5
一、确定零件各孔、平面的加工方式5
二、定位基准的选择7
三、制订工艺路线7
四、选择各工序机床及工、夹具,刀具,加工余量及工序间尺寸与公差的确定8
五、切削用量和时间定额的确定10
六、机械加工工艺过程卡和工序卡12
第四章机床夹具设计计算和结构设计15
一、确定夹具设计方案,绘制结构原理示意图15
二、工件在夹具中加工的精度分析18
三、计算夹紧力20
四、画夹具装配图和零件图21
结论23
参考文献24
致谢25
第一章对零件进行工艺分析并画零件图
一、支架的作用及结构特点
支架是起支撑作用的构架,承受较大的力,也具有定位作用,使零件之间保持正确的位置。
在支架高20mm处两个R12mm宽12mm的凸出部位之间相隔2mm,其中一个上有螺纹孔,另一个上有通孔,则此处构造比较复杂,且在支架高36mm处有2mm宽的一个缺口,这两部分刚度比较低。
中间有Ф30mm的孔,属于套类结构,伸出部分为一平台,上有螺纹盲孔,在端部有倾斜60°的凸出部分,起定位作用,此处应力教集中,强度要好。
在平台下面有增强其硬度的肋板。
两个R12mm凸出,2mm宽36mm高处缺口及R10mm凸出部分为复杂结构,其加工存在一定的难度,要求较高,防止其损坏,需要对其进行必要的热处理。
二、零件的工艺分析
主要加工表面Ф30mm中心孔及两端倒角,上、下端面,M6↓12螺纹盲孔,右端部倾斜60°凸出部分中间孔Ф8mm,左端两个凸出部分外侧面及其中间M10螺纹孔和Ф11孔。
(1)选用灰铸铁HT150,硬度150~200HB,负荷低,磨损无关重要,变形很小,经过正火处理。
灰铸铁件的牌号和应用范围如表1-1所示。
(2)未标注圆角半径为R3mm。
(3)加工表面不应该有毛刺、裂缝、结疤、夹渣等缺陷,并应清理清洁。
(4)所有加工表面应光洁,不可有裂缝、压痕、毛刺、气孔、凹痕以及非金属夹杂物。
(5)上下表面应与中心孔轴线保持一定的垂直度0.06mm和平面度0.05mm,中心孔内表面表面粗糙度Ra≤1.6μm,左端两个凸出部分外表面Ra≤6.3μm,右端部倾斜60°凸出部分中间孔内表面Ra≤1.6μm,为较高精度,且Φ8
。
(6)在加工之前进行人工时效热处理,对毛坯预备性热处理,为降低零件硬度,在精加工阶段的磨削加工前进行淬火处理,淬火后工件硬度提高且易变形。
表1-1灰铸铁件的牌号和应用范围
牌号
硬度HB
应用范围
工作条件
用途举例
HT100
≤170
(1)负荷极低
(2)磨损无关重要
(3)变形很小
盖、外罩、油盘、手轮、手把、支架、坐板、重锤等形状简单、不重要的零件,这些铸件通常不经试验即被采用,一般不需要加工,或者只需经过简单的机械加工。
HT150
150~200
(1)承受中等载荷的零件
(2)摩擦面间的压力≤490KPa
(1)一般机械制造中的铸件,如支柱、坐板、齿轮箱、刀架、轴承座、轴承滑座、工作台,齿面不加工的齿轮和链轮,汽车、拖拉机的进气管,排气管、液压泵进油管等;
(2)薄壁(重量不大)零件,工作压力不大的管子配件,以及壁厚≤30mm的耐磨轴套等;
(3)圆周速度为6~12m/s的带轮以及其他符合左列工作条件的零件。
HT200
170~220
(1)承受较大负荷的零件
(2)摩擦面间的压力>490KPa(大于10t的大型铸件>1470Kpa)或需经表面淬火的零件
(3)要求保持气密性以及韧性的零件
(1)一般机械制造中较为中重要的铸件,如气缸、齿轮、链轮、棘轮、衬套、金属切削机床床身、飞轮等;
(2)汽车、拖拉机的汽缸体、汽缸盖、活塞、制动毂、联轴器盘、飞轮、离合器外壳、分离器本体、左右半轴壳等;
(3)承受7840KPa以下中等压力的液压缸、泵体、阀体等;
(4)汽油机和柴油机的活塞环;
(5)圆周速度为12~20m/s的带轮以及其他符合左列工作条件的零件。
HT250
190~240
三、支架的零件图,见图纸所示。
第二章选择毛坯的制造方式并绘制毛坯简图
一、选择毛坯的制造方式
该零件加工要求高,加工面数量多,并且种类繁多,有车、磨端面,钻孔、扩孔、攻螺纹、车倒角、钻斜孔等,位置、形状、尺寸精度都各有要求。
支架材料为灰铸铁HT150,硬度为150~200HB,承受中等载荷的零件,摩擦面间的压力≤490KPa,用于一般机械制造,薄壁(重量不大)零件,工作压力不大的管子配件以及壁厚≤30mm的耐磨轴套等和圆周速度为6~12m/s的带轮以及其他符合表1-1中条件的零件。
毛坯种类的确定是与零件的结构形状、尺寸大小、材料的力学性能和零件的生产类型直接相关的,另外还和毛坯的具体生产条件相关。
铸件:
包括铸钢、铸铁、有色金属及合金的铸件等。
铸件毛坯的形状可以相当复杂,尺寸可以相当大,且吸振性能好,但铸件的力学性能差。
生产纲领为大批量生产,采用精度和生产率高的毛坯制造方法,如金属型铸造,可以使毛坯的形状接近于零件的形状,因此可以减少切削加工用量,从而提高材料的利用率,降低了机械加工成本。
金属型铸造就是将熔融的金属浇注到金属模具中,依靠金属自重充满金属模具型腔而获得的铸件,这种铸件比砂型铸造铸件精度高,表面质量和力学性能好,生产效率也高,但需要专用的金属型腔模,适用于大批量生产中的尺寸不大的有色金属铸件,综合上述生产此支架零件选择金属型铸造铸件的方式。
二、确定毛坯的形状、大小
(1)毛坯的特点,如表2-1所示:
毛坯的特点及应用范围
制造精度
加工余量
原材料
工件尺寸
工件形状
适用生产类型
生产成本
IT11~13
大
铸铁、铸铜为主
各种尺寸
复杂
各种生产
较低
(2)铸件尺寸公差,如表2-2所示:
(/μm)
铸件基本尺寸
公差等级
大于
至
11
12
13
14
25
40
3.6
5.0
7
9
40
63
4.0
5.6
8
10
63
100
4.4
6
9
11
100
160
5.0
7
10
12
(3)铸件的机械加工余量,如表2-3所示:
(/mm)
尺寸公差等级CT
12
加工余量等级MA
F
G
H
J
基本尺寸
加工余量数值
大于
至
-
100
4.0
4.5
5.0
6.0
2.5
3.0
3.5
4.5
100
160
5.0
5.5
6.5
7.5
3.5
4.0
5.0
6.0
(4)铸造孔的最小尺寸,如表2-4所示:
(/mm)
铸造方法
合金种类
一般最小孔径
特殊最小孔径
金属及砂型铸造
全部
30
8~10
(5)机械加工余量,工序尺寸确定
由于毛坯及以后各道工序或工步的加工都有误差,因此所规定的加工余量其实只是名义上的加工余量,实际上加工余量有最大加工余量和最小加工余量之分。
铸件的机械加工余量见毛坯的制造表2-3所示,尺寸公差等级为12,加工余量等级MA为G,则可选取毛坯的加工余量有4.5mm和3.0mm两种数值,及其他分析,确定毛坯的基本尺寸,画出毛坯简图,如图2-5所示:
图2-5
第三章制订零件的机械加工工艺路线
由于零件是大批量生产,它的主要工艺特征是广泛采用专用机床、专用夹具及专用刀具、量具,机床按工艺路线排列组织流水生产。
为减轻工人的劳动强度,留有进一步提高生产率的可能,该支架在工艺设计上采用了组合机床的流水线加工方式。
一、确定零件各孔、平面的加工方式
(1)孔的加工方式,如表3-1所示:
表3-1孔的加工方案
序号
加工方案
经济加工精度等级(IT)
加工表面粗糙度Ra/μm
适用范围
1
钻
11~12
12.5
加工未淬火钢及铸铁的实心毛坯,也可用于加工非铁金属(但粗糙度稍高),孔径<20mm。
2
钻-铰
8~9
3.2~1.6
3
钻-粗铰-精铰
7~8
1.6~0.8
4
钻-扩
11
12.5~6.3
加工未淬火钢及铸铁的实心毛坯,也可用于加工非铁金属(但粗糙度稍高),孔径>20mm。
5
钻-扩-铰
8~9
3.2~1.6
6
钻-扩-粗铰-精铰
7
1.6~0.8
7
钻-扩-机铰-手铰
6~7
0.4~0.1
8
钻-(扩)-拉(或推)
7~9
1.6~0.1
大批量生产的中、小零件的通孔
由表3-1可以确定支架零件各孔的加工方案如下:
A、加工孔Φ30
,要求内表面粗糙度Ra≤6.3μm,则选择钻-扩-粗铰-精铰的加工方式;
B、加工Φ11,要求内表面Ra≤6.3μm,选择钻-铰的加工方式;
C、加工Φ8
,要求内表面Ra≤1.6μm,选择钻-粗铰-精铰的加工方式。
(2)平面的加工方式,如表3-2所示:
表3-2平面的加工方案
序号
加工方案
经济加工精度等级(IT)
加工表面粗糙度Ra/μm
适用范围
1
粗车-半精车
8~9
6.3~3.2
端面
2
粗车-半精车-精车
6~7
1.6~0.8
3
粗车-半精车-磨削
7~9
0.8~0.2
4
粗刨(或粗铣)-精刨(或精铣)
7~9
6.3~1.6
一般加工不淬硬的平面(端铣表面粗糙度可较低)
5
粗刨(或粗铣)-精刨(或精铣)-刮研
5~6
0.8~0.1
精度要求较高的不淬硬平面,批量较大时,宜采用宽刃精刨方案
6
粗刨(或粗铣)-精刨(或精铣)-宽刃精刨
6~7
0.8~0.2
由表3-2可以确定支架零件各面的加工方案如下:
分析零件的各部分技术要求,四处平面加工,精度要求都在表面粗糙度Ra≤6.3~1.6μm之间,结合零件形状尺寸,选择粗铣-精铣的加工方式。
(3)机械加工的安排原则
1.对于形状复杂、尺寸较大的毛坯,或尺寸偏差较大的毛坯,应首先安
排划线工序,为精基准加工提供找正基准;
2.按“先基面后其他”的顺序,首先加工精基准面;
3.在重要表面加工前应对精基准进行修正;
4.按“先主后次、先粗后精”的顺序,对精度要求较高的各主要表面进行
精加工、半精加工和精加工;
5.对于主要表面有位置精度要求的次要表面,应安排在主要表面加工之后
加工;
6.一般情况,主要表面的精加工和光整加工应放在最后阶段进行,对于
易出现废品的工序,精加工和光整加工可适当提前。
二、定位基准的选择
工件在机床上用夹具进行夹紧加工时,用来决定工件相对于刀具的位置的工件上的这些表面称为定位基准,定位基准分为粗基准和精基准。
1、粗基准的选择
粗基准的选择要重点考虑如何保证各个加工表面都能分配到合理的加工余量,保证加工面与非加工面的位置、尺寸精度,还同时要为后续工序提供可靠的精基准。
按照有关粗基准的选取原则(即当零件有非加工表面时,应以这些非加工表面作粗基准;若零件有若干个非加工表面时,则应以与加工表面要求相对位置精度较高的不加工表面作粗基准):
①加工D面时,选取Φ60外表面外圆为粗基准,利用V型块和一紧固螺钉以Φ60外圆定位夹紧,以限制四个自由度,再以C面为次要粗基准,限制一个自由度,共限制五个自由度,可以满足加工要求;②加工M10和Φ11以R12非加工表面外圆为粗基准;③加工Φ8
以R10非加工表面外圆为粗基准。
2、精基准的选择
选择精基准时,重点考虑的是减少工件的定位误差,保证零件的加工精度和加工表面之间的位置精度,同时也要考虑零件的装夹方便、可靠、准确。
结合零件形状尺寸大小、装夹定位,取D面为精基准,较好定位,且定位基准与设计基准重合。
三、制订工艺路线
拟定工艺路线的出发点是使零件的几何形状、尺寸精度以及位置精度等技术要求能得到保证。
工艺路线的拟定一般需要做两个方面的工作:
一是根据生产纲领确定加工工序和工艺内容,依据工序的集中和分散程度来划分工艺;二是选择工艺基准,即主要选择定位基准和检验基准。
在生产纲领已确定为批量生产的条件下,可以考虑采用万能机床,组合机床和专用夹具,并尽量采用工序集中的原则,通过减少工件安装的数量来提高生产率。
除此之外,还应尽量考虑经济精度以便使生产成本尽量下降。
根据以上原则及前文分析,拟定如下工艺路线:
工序1铸坯(铸造)
工序2热处理(人工时效,降低硬度)
工序3以所选基准,划C、D、E面加工线
工序4粗铣-精铣D面
工序5粗铣-精铣C、E面
工序6钻M6↓12螺纹底孔
工序7攻螺纹M6↓12
工序8粗铣-精铣F面
工序9钻M10螺纹底孔
工序10攻螺纹M10
工序11粗铣-精铣G面
工序12钻-铰Ф11
工序13钻-扩-粗铰-精铰Φ30
工序14倒角Φ30
孔,C端面处
工序15倒角Φ30
孔,D端面处
工序16钻-粗铰-精铰Φ8
工序17热处理淬火,提高硬度,150~200HB
工序18去毛刺
工序19终检
工序20入库
分析:
为了提高效率,尽量减少零件的装夹定位,如同一平面上孔加工在一次装夹就完成加工要求,使工序集中,节约时间,提高了生产率,按机械加工安排原则,合理的拟定工艺路线。
四、选择各工序机床及工、夹具,刀具,加工余量及工序间尺寸与公差的确定
(1)工序3,工件固定在平台上,用划线尺划线找正;
(2)工序4,选择X6130A万能升降台铣床,专用夹具,采用高速钢镶齿三面刃铣刀Ф225mm,量具卡板。
D面有3mm加工余量,粗铣2mm留1mm余量,精铣,保证平面度0.05mm;
(3)工序5,选择X6130A万能升降台铣床,专用夹具,采用高速钢镶齿三面刃铣刀Ф225mm,量具卡板。
C、E面有4.5mm加工余量,粗铣3.5mm留1mm余量,精铣,相对A基准,保证其垂直度度0.06mm;
(4)工序6,选择X6130A万能升降台铣床,专用夹具。
①Ф5麻花钻,螺旋角β=28°,顶角2Kγ=118°,后角α。
=16°,横刃斜角ψ=40~60°,钻孔深度12mmФ5盲孔,M10螺纹底孔,量具卡尺;
②攻螺纹,丝锥M6×1,螺纹量规,攻螺纹机S4012A;
(5)工序8,选择X6130A万能升降台铣床,专用夹具,采用高速钢镶齿三面刃铣刀Ф225mm,量具卡板。
F面有3mm加工余量,粗铣2mm留1mm余量,精铣,相对于B面,保证平行度0.06mm;
(6)①工序9,选择X6130A万能升降台铣床,专用夹具,Ф9扩孔钻(直柄扩孔钻),扩钻通孔Ф9,M10螺纹底孔,量具卡尺;
②攻螺纹,丝锥M10×1,螺纹量规,攻螺纹机S4012A;
(7)工序11,选择X6130A万能升降台铣床,专用夹具,采用高速钢镶齿三面刃铣刀Ф225mm,量具卡板。
G面有3mm加工余量,粗铣2mm留1mm余量,精铣,相对于B面,保证平行度0.06mm;
(8)①工序12,选择X6130A万能升降台铣床,专用夹具,Ф10.8扩孔钻(直柄扩孔钻),量具卡尺,加工此孔有4mm(双边)余量,留0.2mm精加工;
②铰刀Ф11H8,铰孔,直柄机用铰刀;
(9)①工序13,选择X6130A万能升降台铣床,专用夹具,Ф29.8扩孔钻(直柄扩孔钻),量具卡尺,加工此孔有10mm(双边)余量,留0.2mm精加工;
②粗铰到Ф29.93,直柄机用铰刀;
③精铰到Ф30H7,直柄机用铰刀;
(10)工序14、15,倒角Φ30
孔两端面内孔,选用卧式车床C620-1,专用夹具;
(11)工序16,选择X6130A万能升降台铣床,专用夹具,量具卡尺
①Ф7.8标准麻花钻,钻孔,留0.2mm余量;
②粗铰到Ф7.96mm,留0.04mm余量,直柄机用铰刀;
③精铰到Ф8H7,直柄机用铰刀;
五、切削用量和时间定额的确定
(1)工序4,粗铣-精铣D面,保证总高,fz=0.08mm/齿(参考《切削手册》),切削速度:
参考有关手册,确定V=0.45m/s。
即27m/min,采用高速钢镶齿三面刃铣刀,dw=225mm,齿数z=20,则ns=
=
=38r/min,现采用X6130万能升降台铣床,根据机床使用说明书,取nw=37.5r/min,故实际切削速度为:
V=πdwnw/1000=π×225×37.5/1000=26.5m/min
当nw=37.5r/min时,工作台的每分钟进给量fm应为:
Fm=fzznw=0.08×20×37.5=60mm/min
查机床说明书,刚好有fm=60mm/min,故直接选用该值,切削加工时,由于是粗铣-精铣,利用作图法,可得出行程刀刃口宽20mm,L=2×
×60mm=360mm,则机动加工时间为:
Tm=L/fm=360/60min=6min
(2)工序5,粗铣-精铣C、E面,切削用量同上,铣刀行程L=360mm﹢16×2mm=392mm,则机动加工时间为Tm=L/fm=392/60min=6.53min
(3)工序6,钻M6↓12螺纹底孔,即钻Ф5盲孔,确定进给量f:
根据《切削手册》,当材料δb<800MPa,d。
=Ф5mm时,f=0.2~0.6mm/r,由于本零件在加工Ф5孔时属于低刚度零件,故进给量应乘系数0.75,则
f=(0.2~0.6)×0.75=0.15~0.45mm/r
根据X61