电解锰生产工艺流程简述.docx
《电解锰生产工艺流程简述.docx》由会员分享,可在线阅读,更多相关《电解锰生产工艺流程简述.docx(16页珍藏版)》请在冰豆网上搜索。
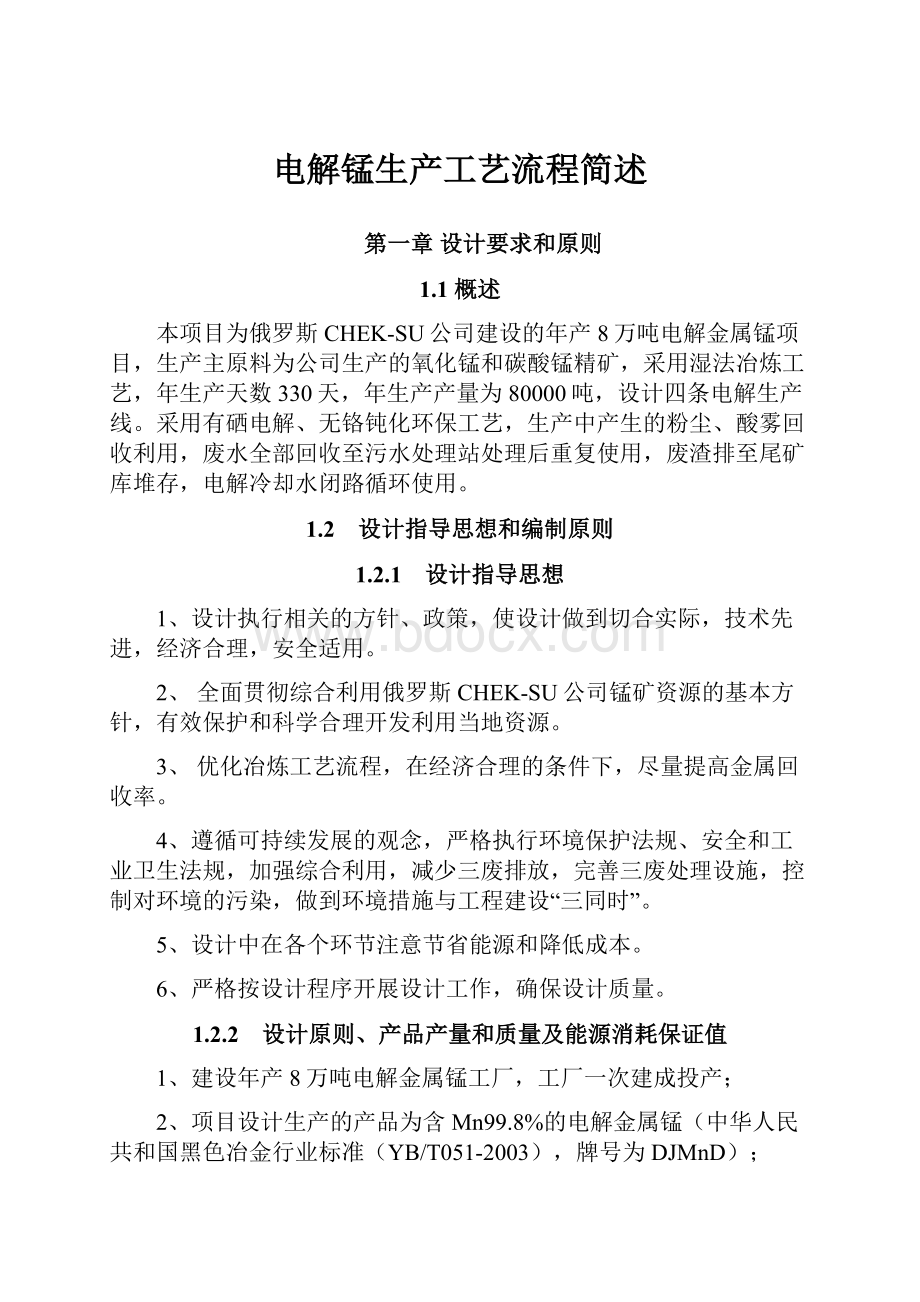
电解锰生产工艺流程简述
第一章设计要求和原则
1.1概述
本项目为俄罗斯CHEK-SU公司建设的年产8万吨电解金属锰项目,生产主原料为公司生产的氧化锰和碳酸锰精矿,采用湿法冶炼工艺,年生产天数330天,年生产产量为80000吨,设计四条电解生产线。
采用有硒电解、无铬钝化环保工艺,生产中产生的粉尘、酸雾回收利用,废水全部回收至污水处理站处理后重复使用,废渣排至尾矿库堆存,电解冷却水闭路循环使用。
1.2 设计指导思想和编制原则
1.2.1 设计指导思想
1、设计执行相关的方针、政策,使设计做到切合实际,技术先进,经济合理,安全适用。
2、全面贯彻综合利用俄罗斯CHEK-SU公司锰矿资源的基本方针,有效保护和科学合理开发利用当地资源。
3、优化冶炼工艺流程,在经济合理的条件下,尽量提高金属回收率。
4、遵循可持续发展的观念,严格执行环境保护法规、安全和工业卫生法规,加强综合利用,减少三废排放,完善三废处理设施,控制对环境的污染,做到环境措施与工程建设“三同时”。
5、设计中在各个环节注意节省能源和降低成本。
6、严格按设计程序开展设计工作,确保设计质量。
1.2.2 设计原则、产品产量和质量及能源消耗保证值
1、建设年产8万吨电解金属锰工厂,工厂一次建成投产;
2、项目设计生产的产品为含Mn99.8%的电解金属锰(中华人民共和国黑色冶金行业标准(YB/T051-2003),牌号为DJMnD);
3、主原料采用俄罗斯奇克苏福克公司生产的碳酸锰矿、氧化锰矿,湿法冶炼生产工艺;
4、本项目采用目前行业最新的设备和工艺,对生产过程中产生的废气、废水、废渣均采取了有效的治理措施,达到清洁生产及环保要求,工艺技术达到目前同行业先进水平;
5、本次项目采用的技术经济指标为:
(1)每条电解生产线330天生产量为20000吨,设计四条电解生产线,生产规模80000吨/年(产品合格率为100%);
(2)电解采用SeO2添加剂,正常生产时,电流效率68~70%,电流密度320~380A/m2,槽电压为4.2~4.6V,每吨锰直流电耗≤6500kWh;
(3)项目采用的碳酸锰精矿Mn27%,氧化锰精矿Mn35%,本批次全锰分析结果中,二价锰回收率:
85%;
(4)电解金属锰产品Mn含量达到99.8%,即产品质量符合中华人民共和国黑色冶金行业标准YB/T051-2003;
6、废弃场和排放场的再利用,应符合俄罗斯联邦的卫生和自然保护立法要求。
1.3 建设规模及产品方案
1.3.1 建设规模
本项目规模为年产8万吨电解金属锰。
1.3.2 工作制度
连续工作制,每天三班,每班8小时,年工作330天。
1.4 厂址
位于俄罗斯哈卡斯共和国西拉区图依姆村。
1.5 设计范围
原料堆场、汽修车间和加油站、焙烧车间、磨粉车间、化合车间、硫化车间、净化车间、粗滤车间、精滤车间(二者是否考虑合并在一起,节约土建投资?
)、电解车间、尾矿库、成品车间、供电系统和配电系统、给排水系统、污水处理、硫磺制酸车间、冷却循环水系统、供热供暖系统、转运设施、220kV总降变电站、进厂公路和铁路。
(是否增加全厂监控、地泵房、取水泵房等小子项)
1.6设计标准
1、设计和施工标准采用俄罗斯联邦现行的强制性规定和条例。
2、在中国制造并出口的设备和材料采用中国标准,并依照俄罗斯联邦相关法律取得认证证书,以证明其符合俄罗斯强制标准要求。
第二章 技术方案
2.1 工艺技术方案
2.1.1 金属锰技术方案
2.1.1.1 生产方法
金属锰的生产方法有火法冶炼和湿法冶炼。
本项目的产品金属锰采用电解法即湿法冶炼生产。
锰矿运入厂后首先进行原料预处理:
根据原料到厂的含水分量,经过晾晒或者烘干等系统,使水分达到<5%以下,才能进入下一道工序。
氧化锰矿还原焙烧得到一氧化锰再进一步磨粉;碳酸锰矿经磨粉得到所需粒度粉料,再用埋刮板输送机将一氧化锰和碳酸锰矿粉分别送入化合槽浸出,用硫酸将碳酸锰矿和一氧化锰矿粉中的Mn2+浸出获得硫酸锰混合液矿浆,经一次压滤固液分离,硫酸锰溶液再经硫化除重金属杂质、静置24小时之后,进入二次压滤,硫酸锰溶液加入电解添加剂,进入合格液池储存,进入电解车间电解。
在电解槽内电解时,阴极析出氢,阳极析出氧气,控制各种工艺指标达到工艺要求,即可获得电解金属锰产品。
2.1.1.2 产品标准
本产品参照中华人民共和国黑色冶金行业标准(YB/T051-2003),生产Mn99.8的电解金属锰,其化学成分参见表2-1。
表2-1 电解金属锰的牌号及化学成分表
牌号
化学成分(质量分数)/%
Mn
C
S
P
Si
Se
Fe
不小于
不大于
DJMnD
99.8
0.03
0.04
0.002
0.01
0.08
0.03
注:
锰含量由减量法减去产品中表列杂质含量总和得到,
即ω(Mn)=100-[ω(C+S+P+Si+Se+Fe)](%)
2.1.1.3 工艺流程图
电解金属锰的生产工艺流程详见图2-1。
图2-1金属锰生产工艺流程图
2.1.1.4 主要生产技术指标
项目主要生产技术指标见表2-2。
表2-2项目主要技术指标表
序号
指标名称
单位
数量
一
性能保证指标
总锰回收率(碳酸锰)
%
83
总锰回收率(二氧化锰)
%
80
可溶锰(二价锰)总回收率
%
85
二
主要技术指标
1
滤渣含水
%
<25以下(取决于压滤机)
2
产品合格率
%
99.7
3
电流效率
%
65~70
4
阴极板电流密度
A/m2
320~380
5
槽电压
V
4.2~4.6
6
电解合格液Mn含量
g/L
35~40
7
阳极液Mn含量
g/L
12~15
三
工作制度
1
年工作天数
d
330
2
天工作班数
班
三
3
班工作时数
h
8
第三章工艺流程简述
3.1工艺流程系统划分
1)原料储存和制备系统;
2)浸出系统(矿浆、浸出、氧化、中和);
3)压滤系统(固与液分离、硫化、静置、合格液池);
4)电解系统(控制槽Mn+2含量,温度,pH值,电流,阴、阳极板导电)
5)产品处理系统(电解24小时后取锰板、换新板、钝化、冲洗、烘干、剥离、包装、入库);
6)电解预处理系统(处理不合格阴或阳极板,隔膜布,清槽);
3.2原料储存和制备系统
3.2.1碳酸锰(MnCO3)和二氧化锰(MnO2)
分别设计有MnCO3和MnO2矿,二个月的露天晾晒堆场,一个月封闭式库房。
温暖季节通过自然干燥,使水分降至5%以下,雨、冬季节根据气象条件、下雨、下雪时用防渗膜盖住,有晴天出现时,尽快打开晾晒,移存入库。
3.2.2硫酸(H2SO4)
硫酸(H2SO4)储罐采用钢制外加12cm的岩棉保温,钢制抗压、防腐、防火、防渗、防爆等满足危化品安全储存方式,储罐设计一个,存量2000吨,4天使用量,硫酸的含量≥98%。
3.2.3氨水
氨水储罐采用钢制外加12cm的岩棉保温,钢制抗压、防腐、防火、防渗、防爆等满足危化品安全储存方式,储罐设计两个,每个2000吨,共计4000吨,8天使用量,浓度为5%-10%。
氨水的制备利用两种换热器。
各换热器均由不锈钢材质的盘管组成,将液氨气化和氨水制备放在同一台设备中,液氨经过进入吸收器与水混合充分吸收,并放出热量,进入盘管冷却器进行降温。
通过液氨和水的流量调节氨水的浓度为5%-10%,制备好的氨水,经检测合格后,送入氨水储罐。
3.2.4化工用品
SDD、SeO2、水玻璃、磷酸、钝化剂、硫酸铵、硫化钡、硫化铵、固体硫磺等化工用品,分别按不同化学性质类别的安全规范储存要求,储存在化工用品仓库,仓库设置有通风、防火、防腐、防渗、防爆等装置和危化品标识。
3.2.5主要原料和辅助原料消耗表
表3-1主要原料和辅助原料消耗表
名称
含量
用量
时间
吨产品单耗
吨产品年耗
MnCO3(碳酸锰粉)
Mn≥27%
77625吨
90天
4.6吨
284625吨
MnO2(二氧化锰)
Mn≥35%
20250吨
90天
3.6吨
74250吨
H2SO4(硫酸)
≥98%
2000吨
4天
2吨(平均值)
160000吨
NH3·H20(氨水)
5%-10%
4000m3
8天
100kg(氨)
8000吨
SDD(福美钠)
≥95%
75吨
30天
10kg
800吨
SeO2(二氧化硒)
≥98%
15吨
30天
2kg
160吨
(水玻璃)
(工业级)
15吨
30天
2kg
160吨
(磷酸)
(工业级)
15吨
30天
2kg
160吨
无铬钝化剂
(工业级)
15吨
30天
待定
(NH3)2SO4(硫酸铵)
(工业级)
待用
待定
(硫化铵)
(工业级)
待用
待定
(硫化钡)
(工业级)
待用
待定
固体硫磺
(S≥96%)
17100吨
90天
0.32吨
62700吨
3.2.6原料制备系统(二氧化锰、碳酸锰、硫磺制酸)
二氧化锰(MnO2)制备成一氧化锰(MnO)。
首先,得把外运入库的含Mn≥35%、粒度≤10mm、水份≥5%以上的二氧化锰矿,用装载机送入料仓,再经皮带计量称,定量送至天然气加热的圆筒烘干机烘干,使水份≤5%以下,与含固定碳≥70%的还原煤(添加量15-20%)混合均匀,送进多管竖式焙烧炉进行还原,还原温度控制在750-850℃之间,还原率可达到≥95%以上,经冷却降温至50℃以下入库。
烘干、焙烧二氧化锰量为225吨/日,74250吨/a。
制备原理为:
在还原的同时:
Fe、Co、Ni、Zn、Cu等氧化物也被还原,给下道工序氧化除铁及硫化除重金属,使用的二氧化锰粉和SDD原料量相应增加,但该工艺设计比传统的反射炉、微波炉、沸腾炉、回转窑等方法,技术要先进(属自主创新),环保要清洁,还原率高,操作简单可控,投资少,运营成本低,在国内已广泛应用于大工业生产。
碳酸锰粉(MnCO3)制备
首先把外运入库的含Mn≥27%、水份>5%以上、粒度≤30mm以下的碳酸锰精矿。
根据当时当地的气象条件,采用晾晒或天然气加热的圆筒烘干机烘干方法,使水分控制在≤5%以下入仓,开始磨粉。
制粉
一氧化锰(MnO)和碳酸锰粉(MnCO3)磨粉利用装载机从料场送入至料仓,再通过电子秤喂料给单传动辊压磨机处理后(生产能力为100-120吨/a),物料经过提升机提升到V选,然后,由旋风机将细粉抽入动态选粉机。
通过旋风机收尘和袋式收尘器,把合格的产品送入料仓(100目过筛、≥95%过筛率),粗粉返回到稳流仓进入辊压机及配套系统连续进行生产,粉尘收集率≥99.8%以上,运行稳定,操作简单可控,但,在设计中要考虑碳酸锰矿和一氧化锰交叉使用该设备的相关配套装置。
采取5天加工碳酸锰粉6000吨,换一天加工一氧化锰矿1200吨。
同时,配套两个1500吨碳酸锰粉料仓系统和一个1500吨一氧化锰粉料仓系统。
为了降低噪音,最好把加工时间控制在白天的12小时,若环境允许,也可晚上加工一氧化锰。
(1)熔硫工序
硫磺库中的硫磺以装载机机送入料斗,经园盘给料机,胶带输送机送入熔硫工段快速熔硫槽。
硫磺贮存于硫磺仓库。
自原料工段来的固体硫磺在快速熔硫槽中,以蒸汽间接加热,以搅拌器连续搅拌熔融为液体硫磺并进入过滤槽,以过滤泵送入液硫过滤器,过滤分离出泥砂灰尘等杂质。
分离后的精硫入中间槽以中间槽泵送入液硫贮罐贮存,间断地溢流进入炉前精硫槽,以精硫泵送入焚硫转化工段焚硫炉。
(2)焚硫、转化工序
来自业主制备的精硫进入精硫槽,由精硫泵经机械喷咀送入焚硫炉内燃烧制取SO212%左右的炉气。
焚硫炉所需空气由空气鼓风机送入干燥塔干燥后送入炉内。
出焚硫炉SO2炉气经废热锅炉回收余热降温,以干燥空气调节SO2浓度至~10%、温度420℃左右后进入转化器进行第一次转化。
经第一段催化剂反应后的炉气以高温过热器与饱和蒸汽换热降温后进入第二段催化剂。
经第二段催化剂反应后的炉气以热热换热器与第二次转化气换热降温后进入第三段催化剂。
经第三段催化剂反应后的炉气以冷热换热器与第二次转化气换热降温,再经省煤器Ⅱ与脱盐水换热降温后进入高温吸收塔。
吸收SO3后的炉气经冷热换热器、热热换热器(E301)与SO3气换热升温至425℃进入转化器进行第二次转化。
经第四段催化剂反应后的炉气以低温过热器降温后进入省煤器Ⅰ与软水换热降温后进入干吸工段第二吸收塔进行第二次吸收。
经两次转化SO2总转化率达99.9%。
(3)干吸、成品工序
焚硫所需空气经鼓风机加压后入干燥塔,经93%硫酸吸收水分,使含水降至≤0.1g/Nm3,并经丝网除沫器除沫后进入焚硫工段焚硫炉。
干燥塔内喷淋酸出塔入干燥塔循环槽,并以一吸塔循环酸泵串来的98%硫酸调节其浓度,以干燥塔循环酸泵送入干燥塔酸冷却器冷却降温后进干燥塔喷淋。
产品93%硫酸,由干燥塔酸冷却器出口引出经成品酸冷却器进一步冷却,经电磁流量计计量后送入成品工段硫酸贮罐贮存。
来自转化工段的第一次转化气进入一吸塔,吸收SO3并经纤维除雾器除去酸沫后返回转化工段进行第二次转化。
一吸塔内喷淋酸出塔入一吸塔循环槽,并以干燥塔循环酸泵串来的98%硫酸调节其浓度,以一吸塔循环酸泵送入一吸塔酸冷却器冷却降温后进一吸塔喷淋。
产品98%硫酸,由一吸塔酸冷却器出口引出经成品酸冷却器冷却,经电磁流量计计量后送入成品工段硫酸贮罐贮存。
自转化工段来的第二次转化气进入第二吸收塔,吸收SO3并经纤维除雾器除去酸沫后经尾气吸收装置吸收二氧化硫后,由烟囱放空。
第二吸收塔用98%硫酸喷淋,吸收SO3浓度升高的硫酸进入二吸塔酸循环槽加水调节其浓度,以二吸塔酸循环酸泵送入二吸塔酸冷却器冷却降温后入塔内喷淋。
多出来的98%硫酸串入一吸塔循环槽。
出二吸塔的尾气经卫生塔以碱溶液吸收SO2后由烟囱放空。
(4)余热回收
从高温循环泵出口来的高温浓硫酸,经蒸汽发生器进酸口进入蒸汽发生器管束加热给水,并产生0.8MPa的饱和蒸汽;蒸汽发生器酸出口的酸温降低为~200℃。
本锅炉进行的定期排污,由锅炉排污管排入地沟。
来自脱盐水站的合格的脱盐水经脱盐水加热器加热后送入硫酸装置除氧。
经除氧器除氧后的锅炉给水,由低压锅炉给水泵送至低温热能回收系统的锅炉给水加热器加热,将温度从104℃预热到170℃左右。
加热后的锅炉给水一部分供混合器用作稀释硫酸以稳定酸浓,大部分送蒸汽发生器产生蒸汽。
送入蒸汽发生器的给水量经过给水调节阀通过汽包液位来调节,以保持汽包液位的稳定;送入混合器的给水量由进入高温吸收塔的浓度来控制。
1)高、中温余热回收
硫磺制酸中可利用的高、中温余热分为两部分:
即焚硫部分的高温余热和转化部分的中温余热。
根据制酸工艺要求,拟在焚硫炉后设置一台火管废热锅炉;在转化器一段出口设置一台高温过热器;在转化器三段(高温吸收塔进口前)设置一台省煤器II;在转化器四段出口设置一台低温过热器及一台省煤器I。
这五台设备用以回收硫磺制酸工艺生产中产生的高、中温余热,即一套硫酸高、中温余热回收系统。
其中火管废热锅炉为管壳式结构;过热器为垂直烟道式结构;省煤器为热管省煤器,结构为垂直烟道式。
余热回收设备均为露天布置。
本套硫酸高、中温余热回收系统最终将产生3.82MPa、450℃的中压过热蒸汽,根据工艺条件和装置规模,经计算本余热回收系统将产生3.82MPa、450℃的中压过热蒸汽约28t/h。
所产中压过热蒸汽大部分用于空气风机拖动,拖动空气风机的汽轮机选择采用背压式汽轮机,并背压0.8MPa饱和蒸汽。
其余少部分中压过热蒸汽经减温减压装置产出0.8MPa饱和蒸汽与汽轮机背压蒸汽合并供给用户。
2)低温余热回收
来自省煤器的含SO3的一次转化气体进入热回收系统的高温吸收塔。
三氧化硫气体向上经过填料和自上而下经过填料的浓硫酸(~99%)逆流接触接触,三氧化硫被吸收;吸收三氧化硫后的硫酸浓度约为99.6%,温度升高约20℃,流入热回收塔底,经位于循环泵槽内的高温循环酸泵将高温浓硫酸送入蒸汽发生器换热,产低压蒸汽,同时酸温降低约20℃后再经混合器稀释到~99%的浓度后进入热回收塔一级喷淋。
蒸汽发生器出口有部分硫酸经锅炉给水加热器和脱盐水加热器回收热量后串入二吸循环槽。
低温热回收系统新建标准二级热回收塔,热回收塔的二级喷淋酸来自二吸塔上塔酸。
为确保一次转化气的吸收效率,高温吸收塔排出的烟气仍需经一吸塔吸收,然后返回转化工段。
主要技术参数如下:
A设计进塔的SO3气体温度:
180℃
B一次转化率:
95%
C进转化SO2气浓:
10~11%
D锅炉给水温度:
104℃
E设计产蒸压力:
0.8MPa
F设计产汽率:
11t/h(保证产汽量:
10t/h)
制酸物料平衡图
制酸生产物料平衡图如图3-1所示。
图3-1硫磺制酸物料平衡图
主要工艺控制指标及技术经济指标
主要工艺指标如下:
(1)转化器进口SO2浓度:
~10%
(2)催化剂:
采用进口催化剂
(3)干燥塔出口水分:
<0.1g/Nm3
(4)尾气排放:
卫生塔停运时:
SO2<400mg/Nm3,酸雾<30mg/Nm3;
卫生塔投运时:
SO2<200mg/Nm3,酸雾<30mg/Nm3。
主要技术经济指标见表3-1。
表3-1主要技术经济指标
序号
指标名称
单位
数量
备注
一
建设规模
硫酸(98%H2SO4)
t/a
200000
二
产品方案
1
硫酸(98%H2SO4)
t/a
200000
2
蒸汽(0.8MPa)
t/a
178200
3
余热发电
万kW.h/a
2376
三
总硫回收率
%
99.85
四
原料、材料消耗
1
硫磺(S≥96%)
t
66400
进口固体硫磺
2
钒触媒
t
14
3
轻质柴油
t
40
说明:
按该锰矿品位,项目年需16万吨硫酸,硫磺制酸部分按年产20万吨规模设计,为了是考虑企业将来运入的锰矿品位会有波动,杂质含量也随之变化,每吨产品耗酸量将增加;目前可通过减少设备生产天数来实现金属锰硫酸需求。
3.3浸出系统(矿浆、浸出、氧化、中和)
3.3.1锰矿粉浆化
来自细粉仓的两种矿粉,通过电子皮带秤计量送至浆化槽与阳极液(Mn+212-15g/L,H2SO435-42g/L)进行矿粉浆化,矿浆的浓度1:
3-4之间,浆化完成后通过浆化槽(V=350m3,4个)与浸出槽的设计底标高差,打开阀门,放入溜槽,自流进浸出槽。
3.3.2浸出、氧化、中和
由浆化工序送来的矿浆进入浸出桶(设计:
Φ内8000×7500,有效体积V=350m3,共计22个,其中备用2个。
(一氧化锰浸出加温,导致浸出桶使用率下降,占用的时间暂不包括。
))。
同时加入一定量的硫酸和阳极液进行反应,产生的放热反应和硫酸稀释热及高速离心压缩机送入的加热空气等使浸出槽内浸出液保持65-85℃之间正常反应,浸出反应完成后,补加阳极液至浸出槽控制液位继续反应之后,进行空气或二氧化锰氧化除铁工序,取样分析:
Mn+238-40g/L,Fe≤1mg/L以下,开始加6-8%氨水中和,pH值控制在6.5-7.2之间。
设定浸出、氧化、中和全过程为10小时完成,液固比为6-8:
1,放液进入压滤,每槽每次时间设定2小时,每槽共计:
12小时,每个槽每天2次循环使用。
由于在浸出槽中浸出过程中有水分的蒸发和损失,分别来自一压的含锰废液与废水,一并回用至浸出槽中循环利用。
同时所有浸出槽产生的硫酸酸雾经过酸雾吸收塔吸收、喷淋、中和等工艺,溶液回收至化合槽循环利用,气体达标排放。
3.4压滤系统(固与液分离、硫化、静置、合格液池)
3.4.1固液分离
浸出矿浆,通过打开浸出槽阀门,放入溜槽,进入输送缓冲槽,矿浆边搅拌、边通过矿浆泵送至固液分离箱式压滤机进行压滤。
该设备功能有自动拉板、自动翻板、气鼓膜高压隔膜箱式压滤机(F=600m2,一次压12台,二次压3台,三次压2台,其中备用3台,共计:
17台)。
该系统布置的压滤机有规律性循环作业,尽量保持相同的时间间隔,每台压滤周期为2小时,一天循环十次左右即可。
压滤分离出固体渣含水份≤25%。
掉入渣仓,进入皮带输送机输送至堆渣场堆存,压滤分离出硫酸锰液从溜槽自流进硫化槽进行硫化除重金属:
Ni、Co、、Zn、Cu、Fe等分别≤1mg/L以下为合格。
3.4.2硫化、静置、合格液池
硫化后的硫酸锰液通过阀门放入溜槽,流入硫化缓冲搅拌槽,再用矿浆泵送入固液分离压滤机进行二次压滤、鼓膜、吹送,滤渣掉入渣仓,进入皮带输送机输送至堆场堆存,硫酸锰液通过系统布置的溜槽进入静置池静置24小时。
Fe、Co、Ni、Zn、Cu等重金属取样分样,分别达到≤1mg/L以下,然后,打开阀门放入溜槽,进入静置缓冲槽,用矿浆泵输入固液分离压滤机进行三次高压压滤、鼓膜、吹送等工序,滤渣掉入渣仓,进入皮带输送机输送至堆场堆存。
硫酸锰液通过系统布置溜槽,加入0.03-0.035g/LSeO2添加剂,混合均匀之后,一并进入合格液池,待用。
3.5电解系统(控制槽Mn+2含量,温度,pH值,电流,阴、阳极板导电)
来自合格液池中合格液经系统布置的溜槽自流至电解溜槽,通过吸管给每个电解槽连续添加硫酸锰合格液进行24小时通电电解,平均阴极电流密度320-380A/m2,单槽电压4.2-4.6V,单槽温度38-44℃,pH值控制在6.8-7.2或酸性电解(3.5-4.5),单槽锰含量为12-16g/L,阴、阳极板导电率为100%,硫酸锰合格液中的二价锰电解回收率:
≥95%以上,电解过程产生的阳极液(Mn+212-15g/L,H2SO435-42g/L)回流至低位阳极池,循环利用,用泵打入高位阳极池,自流至浸出槽再次循环使用。
3.6产品处理系统(电解24小时后取锰板、换新板、钝化、冲洗、烘干、剥离、包装、入库)
经过以上24小时电解之后,在规定的时间内,用系统布置的起重设备取出锰板,换上新板和无铬钝化1分钟。
紧接着用另外一台系统布置的起重设备放入自动超声波清洗机中清洗2-3分钟,再用起重设备吊入链条式自动电炉烘干、剥离一体化机中进行产品处理(烘干温度100-120℃),产品剥离的同时,接入吨袋中用计量秤定量为1吨/袋(±0.2㎏)包装,入库。
3.7电解预处理系统(处理不合格阴或阳极板,隔膜布,清槽)
对经过几个周期性使用的阴极板,每天按3-5%极板数选出凹凸不平、表面很粗或还有残锰的板,进行阳极液酸洗或抛光,为第二天使用做准备。
对经过几个周期性使用的电解效率低的电解槽进行清槽,每清一个槽控制时间为2-4小时,同时,对损坏的阳极板、隔膜布进行更换、酸洗、修补等工序。
阳极泥经过过滤装置,过滤出阳极液回流至阳极池,上部阳极泥送入阳极库堆存,外卖。
同时,迅速恢复该电解槽装槽、放液、调pH值等工序后,通电,使之正常电解。