催化车间安全操作规程.docx
《催化车间安全操作规程.docx》由会员分享,可在线阅读,更多相关《催化车间安全操作规程.docx(189页珍藏版)》请在冰豆网上搜索。
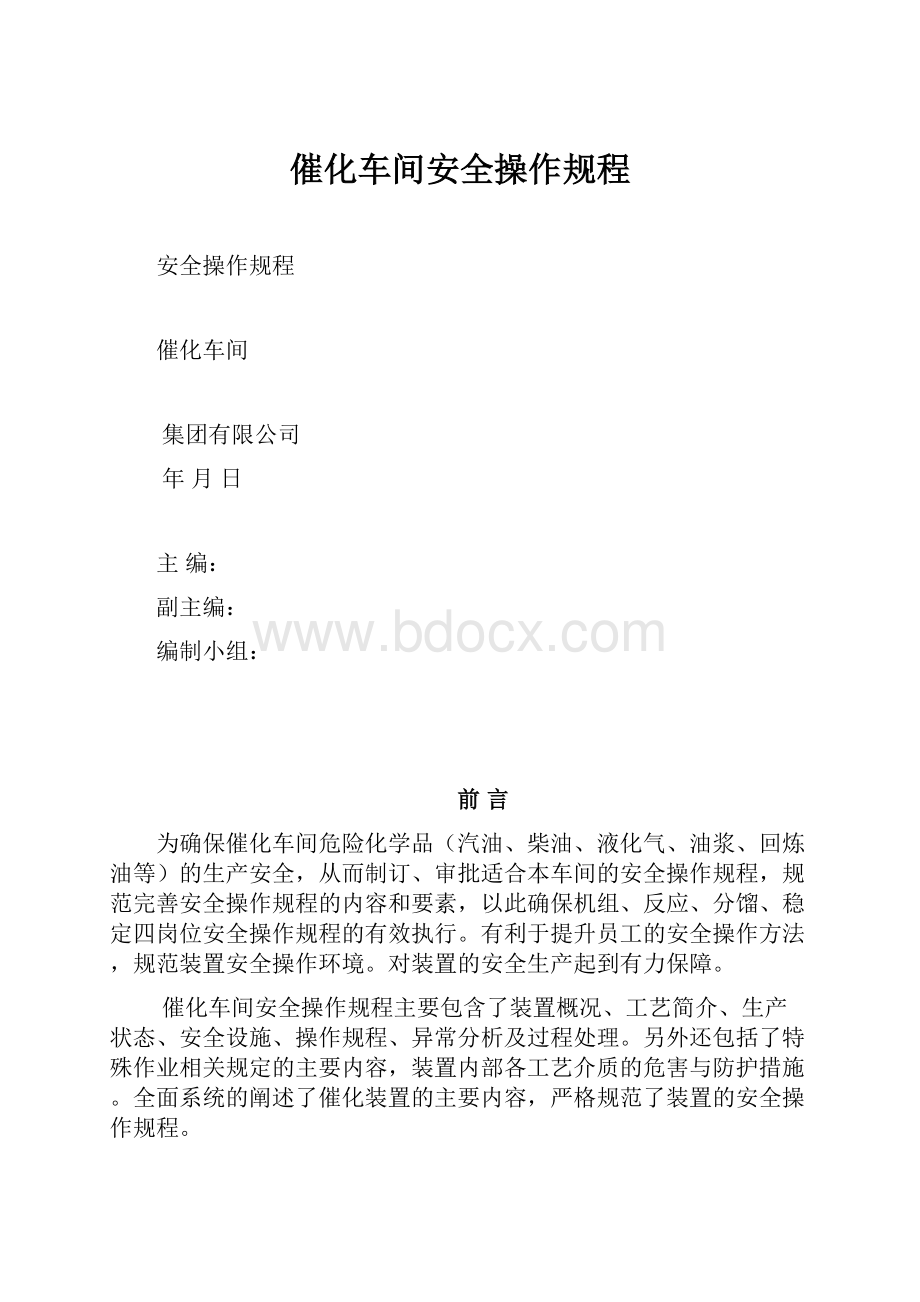
催化车间安全操作规程
安全操作规程
催化车间
集团有限公司
年月日
主编:
副主编:
编制小组:
前言
为确保催化车间危险化学品(汽油、柴油、液化气、油浆、回炼油等)的生产安全,从而制订、审批适合本车间的安全操作规程,规范完善安全操作规程的内容和要素,以此确保机组、反应、分馏、稳定四岗位安全操作规程的有效执行。
有利于提升员工的安全操作方法,规范装置安全操作环境。
对装置的安全生产起到有力保障。
催化车间安全操作规程主要包含了装置概况、工艺简介、生产状态、安全设施、操作规程、异常分析及过程处理。
另外还包括了特殊作业相关规定的主要内容,装置内部各工艺介质的危害与防护措施。
全面系统的阐述了催化装置的主要内容,严格规范了装置的安全操作规程。
催化车间安全操作规程在编制过程中分析了本岗位工艺过程,熟悉本岗位的化学品危害信息、工艺技术信息、安全信息、设备信息,了解了正确的操作步骤及控制参数。
同时编制过程中车间注重全员参与共同编制的方式,对各级员工操作知识的学习起到了很好的促进作用。
安全操作规程内容
1.催化工艺技术信息
1.1催化裂化工艺流程简图
图一.催化裂化工艺流程简图
1.2工艺化工原理资料
1.《催化裂化工艺与工程》第二版,中国石化出版社,2005,陈俊武主编;
2.《催化裂化新技术》,中国石化出版社,2004,《石油炼制与化工》编辑部变;
3.《流化催化裂化》,中国石化出版社,2005,梁凤印主编;
4.《炼油设备工程师手册》第二版,中国石化出版社,2009,中国石油和石化工程研究会主编;
5.《催化裂化工艺计算与技术分析》,石油工业出版社,2000.10,曹汉昌郝希仁张韩主编;
6.《催化车间操作规程》,山东海右石化集团内部资料。
1.3设计的物料最大存储量
催化装置相关的物料包括原料油、催柴、催汽、液化气、油浆等。
序号
危险物质
储存量(t)
生产场所
1
汽油
70
2
柴油
26
3
液化石油气
4
4
原料油
250
1.4安全操作范围
反应温度:
502±5℃
再生温度:
670~700℃
沉降器压力:
130~150kpa
两器差压:
30~60kpa
分馏塔底温度(TRCA201):
300~350℃
油气冷后温度:
40~50℃
轻柴95%点:
355~365℃(94%点365℃)
轻柴闪点:
≥57℃
油浆固含量:
≯6g∕L
粗汽油干点:
190~200℃
解析塔底重沸器返塔温度:
115~138℃
稳定塔底重沸器返塔温度:
140~155℃
稳定塔顶回流罐压力:
≤1.15MPɑ
酸性水汽提塔重沸器返塔温度:
115~130℃
干气中的丙烯含量:
≤3%
液化气中的C2:
≤0.3%
液化气中的C5:
≤3%
主风量(FI106):
32000~36000nm³/h
主风机出口压力:
≤0.25mpa
电脱盐入口温度:
≯150℃
各汽包液位:
50±20%
T201液位:
60~70%
T202液位:
40~50%
V202液位:
40~50%
V202界位:
15~20%
V301液位:
≯50%
E309液位:
50~70%
V302液位:
30~50%
V302界位:
20~30%
V303液位:
30~40%
T301、T302、T303液位:
30~50%
1.5工况异常后果评估
1)装置使用的N2若泄漏,会导致员工窒息;
2)反再系统若发生耐磨衬里脱落,器壁因催化剂磨损而导致高温催化剂泄漏,会致人重伤或死亡;
3)油气管线、分馏油浆等系统的高温介质若因设备问题泄漏,会发生火灾或爆炸事故,将致人重伤或死亡;
4)富气、干气与液化气泄漏,若遇明火会发生火灾或爆炸事故,将致人重伤或死亡。
同时以上工艺气体高浓度时也能使人员中毒或窒息;
5)主风机、气压机控制调节系统失灵,超速导致机体解体危害人员生命安全;
6)蒸汽的泄漏,烫伤操作人员
7)电脱盐电极棒绝缘被击穿短路,漏电保护系统失灵发生触电事故。
8)催化剂发生倒流事故导致高温催化剂由放空卸出,危害人员生命安全;
9)酸性水系统H2S浓度较高,若人员不注重劳保防护,会发生中毒事故;
10)再生器压力骤降,导致沉降器压力高于再生器,会导致油气互窜,发生爆炸,危及人员生命安全;
11)开工升温阶段,燃料油向再生器喷入过快,会导致再生器温度骤升,导致反再系统装置倒塌,威胁全体人员安全;
2.催化裂化装置概况
2.1催化装置周边环境
催化装置周边环境如下图:
图二.催化装置周边环境
2.2装置概况
2.2.1装置加工能力及组成:
装置设计公称能力30×104t/a,采用多产气体方案,以生产石油气及高辛烷值汽油组分为主,同时兼顾轻柴油收率。
装置由反应—再生、分馏、吸收稳定、主风机、气压机、余热锅炉、精制、酸性水汽提部分组成,产品有汽油、轻柴油、液化气、干气等。
2.2.2主要设计指标:
1、催化剂和优化工程技术,使干气产率≤5%。
2、液化石油气产率≮23%(w)。
3、再生催化剂定炭<0.1%。
4、汽油RONC≮90。
5、工程设计满足二年一大修要求。
2.2.3主要工艺技术特点
1、采用多产液化石油气(尤其是丙烯)和高辛烷值汽油工艺
1)以常压渣油为原料,在较高的反应温度、较深的反应深度、较低的油气分压、较高的剂油比,并在添加了择型分子筛的专用催化剂的作用下进行催化裂解反应,生产较多的丙烯及高辛烷值汽油。
2)目的产品产量高。
该工艺技术的高价值产品:
汽油、液化石油气、三碳烯烃、四碳烯烃产率高。
3)产品质量好。
该工艺在多产液化石油气和汽油的情况下液化气富含烯烃且汽油质量好。
汽油辛烷值RONC高达90以上,诱导期长,安定性好。
轻柴油差率较低,其十六烷值与FCC柴油十六烷值基本相当。
4)灵活的工艺条件和操作方式:
反应温度500—530℃,剂油比7.32,可以单程,重油回炼操作。
通过调整工艺操作条件,可以灵活的实现产品转化。
2、采用复合分子筛催化剂及多种助剂
为满足本装置多产液化石油气及高辛烷值汽油的要求,设计考虑采用生产高辛烷值汽油、多产液化石油气、重油裂解能力强的复合型分子筛催化剂。
从稳定操作、保证装置长周期运转及环境保护角度出发,设计中考虑添加CO助燃剂,油浆阻垢剂等助剂。
其中CO助燃剂为实现完全再生提供了可靠保证;油浆阻垢剂的应用对于避免或减轻油浆系统的结垢十分有效,为系统长期高效运转创造了有利条件。
3、采用同轴式反应—再生器
采用同轴式两器布置方案,以减少设备投资,减少占地。
两器中沉降器在上,再生器在下的同轴式布置型式允许的两器差压大,很好的兼顾了反应和再生对操作压力的不同要求。
具有技术先进、结构简单、操作简便、控制灵活方便、抗事故能力强、能耗低、抗催化剂倒流能力强,压力平衡适用范围大等特点。
4、再生工艺方案
再生方案的选择考虑两个因素:
其一是降低再生催化剂的定炭,是催化剂能得以充分发挥;其二是避免采用过于苛刻的再生条件,恢复并保护催化剂活性。
本装置采用单段再生,催化剂定炭≯0.2%。
该技术由以下几种单体技术组成:
1)采用加CO助燃剂的完全再生方案。
采用该方案后,平均氧浓度的提高可使再生剂含炭量明显降低,对于单段再生的效果更加明显。
2)采用较低的再生温度。
较低的再生温度有利于提高剂油比并保护催化剂活性,为反应进料提供更多的催化剂活性中心。
3)采用逆流再生。
通过加高待生套筒使待生催化剂进入密相床上部,并良好分配,然后乡下流动与主风逆流接触,有利于提高总的烧焦强度并减少催化剂的水热失活。
4)采用待生催化剂分配技术,在待生套筒出口配置特殊的待生催化剂分配器,使待生剂均匀分布于再生密相床上部,为单段逆流高效再生提供基本的保证。
5)采用高床层再生。
设置较高的密相床层,不仅可提高气固单程接触时间,而且有利于CO在密相床中燃烧,还可以提高催化剂的输送推动力。
6)采用先进的主风分布管。
主风分布管的好坏直接影响再生器的流化质量,从而影响到烧焦效果。
单段再生的再生器直径较大,因此主风分布的好坏尤为重要。
为改善流化质量,采用改进的主风分布管。
主风分布管设计时还考虑了长周期操作的要求。
5、反应工艺技术方案。
吸收国内外同类生产装置积累的经验,并结合本装置具体特点,为进一步改善产品分布,提高汽油产率,降低干气及焦炭产率,在提升管反应系统设计中采用了下列措施。
1)采用MIP工艺,该工艺保留了提升管反应器高反应强度,能够促进某些二次反应多产异构烷烃,降低汽油中烯烃的含量。
2)采用了高效雾化喷嘴并采用较高的原料油预热温度(200℃),以降低原料进喷嘴的粘度,确保原料的雾化效果及油气与催化剂接触的效果。
3)设置预提升段。
使油气与催化剂接触前,以接近活塞流的形式向上运动,为催化剂和油滴均匀接触创造条件。
提升介质为自产干气,可减轻催化剂水热失活并降低蒸汽消耗。
4)提升管出口采用粗旋。
使油气与催化剂迅速分离,减少过裂化反应,避免沉降器结焦。
5)采用高效汽提技术。
设计主要从改进汽剂接触即改进挡板结构,改善蒸汽分配及增加催化剂停留时间三方面入手,在较低的蒸汽消耗量下取得理想的汽提效果。
采用上述措施使得催化剂在从进入提升管反应器至离开沉降器汽提段的整个过程中均处于优化状态。
通过预提升段尽可能地使催化剂流动均匀。
采用高效雾化喷嘴使催化剂与良好雾化并均匀分布的原料油雾滴接触,达到瞬间汽化、反应的目的。
使用快分和油气快速导出技术较少过裂化反应,使反应油气在高温区的停留时间尽可能缩短,加之完善的汽提设施,从而达到提高轻质油收率、降低、焦炭产率的目的。
6)采用合理的外取热技术
外取热器采用气控式外取热型式。
连体式汽包为立式,与外取热器紧密连接,节省了多组连接管道使外取热器管系统大为简化。
其优点:
简单可靠,投资省、设备紧凑、效率高,能够灵活调节取热负荷,满足两器热平衡需要,外取热水系统采用自然循环方式,节省动力,运行可靠。
6、采用多项新技术
1)原料及油浆雾化采用HK-5型高效喷嘴。
该喷嘴具有压降低,雾化效果好,干气及焦炭产率低,轻质油收率高,操作平稳及油压互不干扰等优点,可以满足工艺过程的要求,且一定程度上降低能耗。
2)采用气控外循环取热器。
该型式的外取热器具有结构简单,操作方便,调节灵活,运行可靠等优点。
外取热器取热管采用翅片管,具有传热系数高,设备结构紧凑,抗事故能力强等优点。
外取热水系统采用自然循环方式,节省动力运行可靠。
3)采用高效pv型旋风分离器。
从维护反应系统平稳操作,减少催化剂自然跑损的角度出发,本装置反应系统中旋风分离器均采用分离效果好,结构简单,操作弹性大的pv型旋风分离器。
4)采用两段汽提技术。
改善汽提效果是降低焦炭产率的一个重要手段,为此本装置采用两段汽提技术。
5)有针对性的采用折流杆式冷凝器。
分馏塔顶油气冷凝系统的压降大小直接影响气压机的功率消耗以及吸收稳定系统的操作,因此分馏塔顶油气水冷系统采用低压降折流杆式冷凝器。
气压机二段出口水冷器也采用折流杆式冷凝冷却器,以减少系统压降。
6)机泵选用高效率的流程泵,部分机泵配备变频电机。
7)单、双动滑阀、塞阀均采用电液执行机构和冷壁式阀体结构。
8)采用低毒无味的BHQ-NFNV2型金属钝化剂。
7、产汽系统和余热锅炉
产汽系统是为回收装置再生器内余热及工艺物流中高温余热而设置的。
循环油浆及再生器内催化剂温度较高,组成一个低压产汽系统,产低压饱和蒸汽(180℃,1.1MPa)。
余热锅炉系统回收再生烟气的物理显热,产生低压饱和蒸汽,并过热产汽系统及余热锅炉系统所产生的饱和蒸汽至280℃,1.1MPa。
设置一台余热锅炉回收再生烟气余热,其中烟气高温段过热低压蒸汽,中温段产生低压饱和蒸汽,低温段预热装置及预热锅炉本体产汽用的除氧水。
2.2.4工艺流程简介
一、反应岗位工艺流程简述
90℃原料油自常压装置和装置外进入本装置原料油缓冲罐(V207),经原料油泵(P201AB)升压后,先经原料油—顶循环油换热器(E204AB)与顶循环油换热后,再经过原料油—轻柴油换热器(E205AB)、原料油-中段换热器(E208)、油浆—原料油换热器(E210)换热,换热后的温度至200℃左右和回炼油混合,分四路经原料油雾化喷嘴进入提升管反应器,油浆经单独的喷嘴进入提升管,与690℃的高温催化剂接触进行原料的升温、汽化及反应。
反应后的油气与待生催化剂在提升管出口经两组粗旋风分离器迅速分离后经升气管密闭进入沉降器两组单级PV型旋风分离器,再进一步除去携带的催化剂细粉离开沉降器,进入分馏塔(T201)。
积炭的待生催化剂自粗旋料腿及沉降器单级旋分器料腿进入汽提段,在此与蒸汽逆流接触以汽提催化剂所携带的油气,汽提后的催化剂沿待生立管下流,经待生立管,待生塞阀,待生催化剂分配器进入再生器(R101C),在再生器内与向上流动的主风逆流接触,完成催化剂的烧焦再生,再生催化剂经再生斜管及再生滑阀进入提升管反应器(R101A)底部,在蒸汽的提升下,完成催化剂的加速、分散过程。
然后与雾化原料接触。
为防止原料中所含有的催化剂造成污染,设置金属钝化剂加注系统。
桶装钝化剂先经钝化剂吸入泵(P101)打入钝化剂罐(V116),然后由钝化剂注入泵(P102AB)连续注入至提升管进料线上,再生器烧焦所需要的主风由主风机提供,主风自大气进入主风机(M101B),升压后经主风管道,辅助燃烧室(F101)及主风分布管进入再生器。
再生器产生的烟气先经3组两级旋风分离器分离催化剂,再经双动滑阀及降压孔板进入余热锅炉,回收烟气中的热能,使烟气温度降到180℃左右,最后经烟囱排入大气。
开工用的催化剂由冷催化剂罐(V101)或热催化剂罐(V102)用非净化风送至再生器,正常补充催化剂可由催化剂小型加料线输送至再生器。
CO助燃剂由助燃剂加料斗、助燃剂罐(V106)用非净化风经小型加料管线输送至再生器。
二、分馏岗位工艺流程简介
由沉降器来的反应油汽进入分馏塔底部,与循环油浆逆流接触,洗涤反应油汽中的催化剂并脱过热,使油气呈饱和状态进行分馏。
(1)分馏塔顶油气
分馏塔顶油气经塔顶油气热水换热器(E214A,B)换热后,再经塔顶油气干式空冷器(E201A-D)及塔顶冷凝冷却器(E202A,B)冷至40℃,进入油气分离器(V202)进行气、液、水三相分离,分离出的粗汽油经粗汽油泵(P203A,B)分成两路:
一路作为吸收剂打入吸收塔(T301),另一路作为反应终止剂打入提升管上部.富气进入气压机(C301),含硫的酸性水用富气水洗泵(P209A,B,C)抽出,作为富气洗涤水送至气压机出口管线。
(2)塔顶循环
顶循环回流自分馏塔第四层塔盘抽出,用顶循泵(P204A,B)抽出,经原料油-顶循环油换热器(E204A,B)顶循环油-热水换热器(E213A,B),顶循环油空冷器(E203A,B)温度降至90℃后返塔第一层。
(3)轻柴油
轻柴油自分馏塔自流至轻柴油汽提塔(T202),汽提后的轻柴油由柴油泵(P205A,B,C)抽出后,经原料油-轻柴油换热器(E205A,B)轻柴油-富吸收油换热器(E215A,B)轻柴油空冷器(E206A,B,C)冷却至60℃分成两路:
一路出装置,另一路经轻柴油冷却器(E207)使其温度降至40℃送至再吸收塔(T303)作吸收剂。
(4)中段循环
中段回流油自塔第十八层抽出,用中段泵(P206A,B)升压,经原料油-中段换热器(E208)进入中段冷却器(E209)温度降至190℃后返塔第15层。
(5)回炼油
回炼油自T201自流至回炼油罐(V201),经回炼油泵(P207A,B)升压后,分成四路:
一路与原料混合进入提升管,一路直接返塔,一路回炼至油浆喷嘴,最后一路外甩。
(6)油浆
油浆自塔底经(P208A,B,C)抽出,经油浆-原料油(E210),油浆蒸汽发生器(E211A,B)温度降至280℃后再分为两路,大部分作为上下返塔,小部分经油浆冷却水箱(E212)冷却至90℃,作为产品油浆送出装置。
(7)原料油
原料油经原料油泵(P201A,B)抽出,经顶循-原料油换热器(E204A,B)轻柴油-原料换热器(E205A,B)去电脱盐脱盐脱水,后进入原料油-中段换热器(E208)、油浆-原料换热器(E210)温度升至200℃后与回炼油混合后去提升管反应器(R101A)。
分馏塔多余热量分别由顶循环回流,中段循环回流,及油浆循环回流取走。
三、机组岗位工艺流程简介
(一)主风机流程
空气经过主风机入口过滤器及入口消声器进入主风机,经压缩至0.35MPa(绝压),进入主风总管后分二路:
一路经辅助燃烧室进入再生器主风分布管,为再生器烧焦供压缩空气。
另一路去增压机,进一步升压后,送至外取热器、待生套筒,作为外取热器的提升风和流化风以及待生套筒的流化风。
(二)气压机蒸汽流程
来自锅炉的新蒸汽进入蒸汽分水器经隔离阀至速关阀经蒸汽调节阀进入汽轮机,经过一个调节级和六个压力级做功进入冷凝器凝结成水,再由凝结水泵经两级射汽抽气器后进入凝结水回收管路。
四、稳定岗位工艺流程简介
(1)吸收稳定系统工艺流程
自气压机C301来的压缩富气与分馏酸性水泵P209来的富气洗涤水汇合后,先经压缩富气空冷器E301冷凝冷却,再与吸收塔底油及解析塔顶气混合后进入压缩富气冷却器E302进一步冷却至40℃后,进入气压机出口油气分离器V302进行气、液、水三相分离。
经V302分离后的气相进入吸收塔T301进行吸收,作为吸收介质的粗汽油及稳定汽油分别自第四层及第一层进入吸收塔,吸收过程放出的热量由中段回流取走,中段回流自第十七层流入吸收塔中段油泵P303,由泵升压后经吸收塔中段冷却器E303冷至38℃返回吸收塔第十八层。
经吸收后的贫气送至再吸收塔T303,用轻柴油作吸收剂吸收贫气携带的汽油组分后,干气进入干气分液罐S302进行气液分离。
分离后的干气去焦化脱硫醇后一路送至锅炉,一路返回干气缓冲罐S303,一路去常减压,一路去长明灯,一路放火炬。
凝缩油由解析塔进料泵P301从气压机出口油气分离器V302抽出分为两路:
一路作热进料经稳定汽油与凝缩油换热器E305换热后进入解析塔第九层;另一路作冷进料直接进入解析塔第一层,由解析塔底重沸器E306提供热源,解析出凝缩油中C1C2组分,解析塔底重沸器由分馏中段回流或1.0Mpa蒸汽加热。
脱乙烷汽油由解析塔T302底抽出,经稳定汽油与脱乙烷汽油换热器E307,进入稳定塔T304进行多组分分馏,稳定塔底重沸器E309由分馏中段回流或1.0Mpa蒸汽提供热源。
液化石油气从稳定塔顶馏出经稳定塔顶干式空冷器E308,稳定塔顶冷却器E304冷却至40℃后进入稳定塔顶回流罐V303,然后经稳定塔顶回流泵P305抽出,一部分作为稳定塔顶回流;其余作为液化气产品送出装置。
稳定汽油自稳定塔底先经稳定塔底重沸器E309,再经稳定塔进料换热器E307,解析塔进料换热器E305,分别与脱乙烷汽油、凝缩油换热后,再经稳定汽油除盐水换热器E310,稳定汽油冷却器E311,冷却至40℃,一部分至产品精制脱硫醇;另一部分由稳定汽油泵P306加压后进入吸收塔T301作补充吸收剂。
气压机出口油气分离器V302分离出的酸性水自压送至酸性水汽提系统。
(2)汽油精制系统工艺流程
塔T701进一步分离碱雾、水分等杂质后,即作为成品汽油送出装置。
汽油沉降罐V702顶部分离出的尾气经尾气水封罐V708送至催化烟囱,底部碱渣间断排入碱渣罐V705。
各安全阀放空的汽油进汽油放空罐V707,用碱液泵P702间断送出装置。
10%的碱液经泵P702进入催化剂碱液罐V704,然后从罐顶部加入磺化酞菁钴催化剂(含量约200ppm),用碱液泵P702混合均匀(溶液呈蓝色透明)后打入固定床反应器顶部(R701A或B,其中一台操作,一台备用),使催化剂碱液在反应器内循环浸泡,碱液由深蓝色变为淡黄色,表明吸附过程结束,此时可将碱液撤至V704,然后即可进行汽油脱硫醇。
自吸收稳定系统来的汽油经汽油--碱液混合器MI701与10%的碱液混合,进入汽油预碱洗沉降罐V701。
汽油与碱液沉降分离后,碱液循环使用,新鲜碱液由碱液泵P702间断补充,碱渣间断自压送至碱渣罐V705,碱渣经泵P702间断送出装置。
脱硫化氢后的汽油经汽油—空气混合器MI702与非净化风、活化剂混合后进入固定床反应器R701。
反应器内装有经磺化酞菁钴和碱液浸泡后的活性碳,在催化剂的作用下将汽油中较难脱出的大分子硫醇氧化为二硫化物,确保汽油产品质量。
脱硫醇后的汽油进入汽油沉降罐V702,分离出的汽油经汽油成品泵P701进入汽油砂滤外来30%的碱液由P702打入碱液罐V703,以制备10%的碱液。
2.3装置主要安全措施简介
2.3.1自动控制方案简介
1、反应温度
1)原料预热温度控制(TRC103)
原料预热温度控制即提升管进料(主要混合原料油)的温度控制是通过改变原料油与油浆换热量来实现的。
2)提升管反应温度(TRCA101)
反应温度是影响催化裂解装置产率及产品分布的关键参数之一,它受许多工艺参数和制约条件的影响。
催化裂解反应是吸热反应,所需热量直接由再生器烧焦的然烧热(主要的)和进料携带的热量(次要的)提供,在其他因素相对不变的情况下,反应温度在一定范围内可以通过再生催化剂的循环量来控制。
提升管反应器出口温度是通过再生滑阀的开度控制再生催化剂的循环量实现的,为提高装置的安全可靠性和操作灵活性,在控制回路中设置再生滑阀差压保护回路。
提升管反应器出口温度调节器(反作用)与再生滑阀压降调节器(正作用)组成超驰控制系统,已实现再生滑阀的低差压软限保护,防止催化剂倒流。
正常工况时,再生滑阀压降总是大于给定值(一般为10KPa),再生滑阀由提升管反应器出口温度调节器直接控制,再生滑阀压降调节处于自动跟踪状态;在异常的工况下,即当再生滑阀压降调节的输出值去控制再生滑阀(此时提升管反应器出口温度调节器处于跟踪状态),以维持再生滑阀有一定压降,防止催化剂倒流,待再生滑阀压降正常后,提升管反应器出口温度调节器又投入控制。
2、再生器、沉降器差压与再生器压力控制
为保证催化剂循环量和主风机的安全运行,采用再生器—沉降器差压调节器(反作用)和再生器压力调节器(反作用)组成的自动选择调节系统。
当再生器与沉降器差压在正常范围时,再生器压力调节器控制双动滑阀以维持再生器压力的恒定;当反应压力异常降低使再生器与沉降器的差压正向超过安全给定值(70KPa)时,自选调节系统的两器差压调节就无扰动的自动取代再生器压力调节器进行控制,自动降低再生器压力以维持两器差压在允许的范围内。
当再生器与沉降器差压恢复到给定值范围内时,系统又无忧动地自动返回再生器压力控制双动滑阀。
当反应压力异常升高再生器与沉降器的差压反向超过安全给定值(-10KPa)时,自动选择调节系统是无能为力的,当再生器与沉降器差压继续降低可通过ESD实行装置停车。
3、反应压力控制
1)两器烘器阶段(HIC102)
通过遥控设在沉降器顶的放空阀控制沉降器压力,其目的是控制两器的升温速度。
2)建立汽封至两器流化试验阶段,用分馏塔顶压力控制分馏塔顶出口油气管道上蝶阀保证反应压力平衡。
3)反应进油后启动富气压缩机前采用分馏塔顶压力控制压缩机入口放火炬小阀(细阀),配以遥控压缩机入口放火炬大阀,保证反应压力平衡。
4)富气压缩机正常运行后
正常工况下,采用分馏塔顶压力控制富气压缩机组的转速保证反应压力平稳,此时控制气压机出口循环线上的反喘振调节阀以免富气压缩机组喘振。
5)汽轮机调速器故障
若汽