液压控制系统设计说明.docx
《液压控制系统设计说明.docx》由会员分享,可在线阅读,更多相关《液压控制系统设计说明.docx(48页珍藏版)》请在冰豆网上搜索。
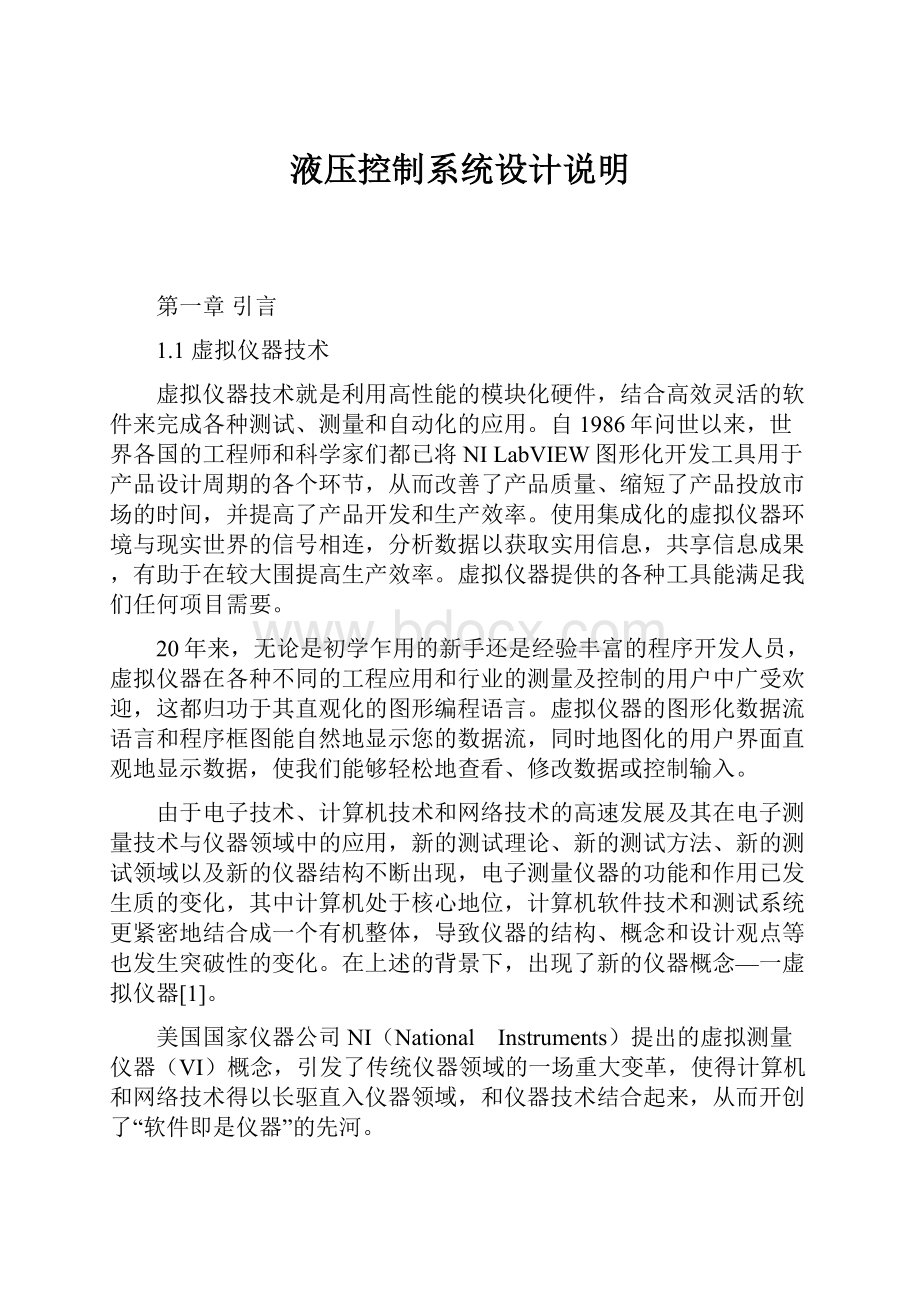
液压控制系统设计说明
第一章引言
1.1虚拟仪器技术
虚拟仪器技术就是利用高性能的模块化硬件,结合高效灵活的软件来完成各种测试、测量和自动化的应用。
自1986年问世以来,世界各国的工程师和科学家们都已将NILabVIEW图形化开发工具用于产品设计周期的各个环节,从而改善了产品质量、缩短了产品投放市场的时间,并提高了产品开发和生产效率。
使用集成化的虚拟仪器环境与现实世界的信号相连,分析数据以获取实用信息,共享信息成果,有助于在较大围提高生产效率。
虚拟仪器提供的各种工具能满足我们任何项目需要。
20年来,无论是初学乍用的新手还是经验丰富的程序开发人员,虚拟仪器在各种不同的工程应用和行业的测量及控制的用户中广受欢迎,这都归功于其直观化的图形编程语言。
虚拟仪器的图形化数据流语言和程序框图能自然地显示您的数据流,同时地图化的用户界面直观地显示数据,使我们能够轻松地查看、修改数据或控制输入。
由于电子技术、计算机技术和网络技术的高速发展及其在电子测量技术与仪器领域中的应用,新的测试理论、新的测试方法、新的测试领域以及新的仪器结构不断出现,电子测量仪器的功能和作用已发生质的变化,其中计算机处于核心地位,计算机软件技术和测试系统更紧密地结合成一个有机整体,导致仪器的结构、概念和设计观点等也发生突破性的变化。
在上述的背景下,出现了新的仪器概念—一虚拟仪器[1]。
美国国家仪器公司NI(National Instruments)提出的虚拟测量仪器(VI)概念,引发了传统仪器领域的一场重大变革,使得计算机和网络技术得以长驱直入仪器领域,和仪器技术结合起来,从而开创了“软件即是仪器”的先河。
“软件即是仪器”这是NI公司提出的虚拟仪器理念的核心思想。
从这一思想出发,基于电脑或工作站、软件和I/O部件来构建虚拟仪器。
I/O部件可以是独立仪器、模块化仪器、数据采集板(DAQ)或传感器。
NI所拥有的虚拟仪器产品包括软件产品(如LabVIEW)、GPIB产品、数据采集产品、信号处理产品、图像采集产品、DSP产品和VXI控制产品等。
虚拟仪器充分利用计算机的人机对话功能,完成仪器的各种工作参数的设置,如功能、频段、量程等参数的设置,对测量结果的表达与输出有多种方式,如屏幕显示,电、磁、光存储,绘图打印,网络传输等[2]。
由于虚拟仪器本身是以计算机为平台,具有方便、灵活的互联能力,随着通信技术、总线技术和网络技术的发展与应用,虚拟仪器向网络方向发展,网络化虚拟仪器的出现是一种必然。
它除了必要的硬件接口支持,虚拟仪器软件开发平台使用户可以借助于Windows系统的远程桌面、LabVIEW的网络通信功能、网络协议等,用户能很快在Web上发布虚拟仪器的面板,直接在本地打开并操控虚拟仪器,以实现远程测试、诊断和维修。
利用DataSocket技术,用户可以和其他有Internet功能的程序迅速建立连接并共享数据,而无需担心网络协议和数据格式等问题。
下一代的虚拟仪器工具将能够快速方便地与蓝牙、无线以太网或其他标准的网络技术相融。
随着网络虚拟技术的发展,“网络即仪器”将成为新的概念,网络化仪器必将推动仪器界新的革命[3]。
1.2CAT技术在液压测试系统中的应用
微型计算机的出现和普及,极大的推动了液压CAT技术的应用和发展。
国外,早在二十世纪六十年代中期开始,许多液压公司就开始可液压CAT技术的研究。
MOOG公司于1976年发布了伺服阀计算机控制测试(ComputerControlledTesting)的成果,该系统能够在微机的控制下自动完成控制流量试验、压力增益试验、负载流量试验和频率响应试验,还能够保存实验数据、打印实验曲线和数据。
CAT技术的研究是跟随计算机技术、电子技术和测试仪器的发展与时俱进的。
微型计算机的操控系统已经经历过DOS,Windows9x,Windows2000,WindowsXP等升级过程。
CPU也从初级的80286到现在的PentiumN系列,计算机总线从XT总线、ISA总线、PCI总线、到最新的PXI总线。
自动测试仪器也有了数据采集卡、GPIB,VXI,PXI,等多种类型[4-5]。
特别是微型计算机操作系统的不断升级,促使CAT技术为了适应新的要求而不断改进。
近些年来由美国国家仪器公司提出的虚拟仪器的概念,为液压CAT技术提供了新的发展方向和模式。
本课题就是在虚拟仪器思想的指导下,在Windows操作系统上进行电液伺服阀的CAT的开发与研究。
1.3本课题研究目的和意义
电液伺服阀控制系统广泛应用于冶金机械、航空航天、船舶等重要领域。
电液伺服阀作为电液伺服控制系统的核心部件,既是信号转换元件,又是功率放大元件,其性能优劣直接影响到电液伺服控制系统控制精度、稳定性和可靠性。
一台合格的电液伺服阀必须经过各种仪表对其参数进行严格测试,这样才能保证伺服系统的正常运行。
在现阶段,本课题的研究具有很强的现实意义。
本课题立足国,以实用为准则,在价格实惠的情况下,对电液伺服阀进行测试,具有很高的性能,避免大而全所带来的高昂价格。
用传统的方法来测试电液伺服阀,检测准确性较差,人为因素对误差影响较大,检测速度较慢。
计算机辅助测试(ComputerAidedTest简称CAT)是建立一套计算机数据采集和数字控制系统,与试验台连接起来,由计算机对测试参数,如压力、流量、等参数进行数据采集、量化和处理并输出测试结果。
在测试过程中。
计算机还可以根据数字反馈或人工输入要求,对测试过程进行控制,达到计算切跟踪和控制试验台及试件组态的目的,从而高速、高精度地完成液压产品的性能测试[6]。
由上述分析可以看出,本课题的研究将具有很强的现实意义和实际价值。
1.4课题提出及研究方案
本文的研究对象为电液伺服阀的静态特性测试系统的设计以及虚拟仪器在其中的应用。
目的是设计出基于虚拟仪器的电液伺服阀的静态特性测试系统,研究电液伺服阀的静态特性测试的基本理论。
因此工作包括电液伺服阀的静态特性测试方法的理论分析、实验硬件的配置以及虚拟仪器测试。
首先,对电液伺服阀阀的静态特性测试方案设计分析。
主要介绍了电液伺服阀的静态特性性能指标、测试原理、数据采集和信号处理的基本理论。
然后,进行测试系统的硬件测试设计。
主要包括微型计算机、传感装置、信号调理装置、数据采集设备。
重点研究了实验过程中的压力、流量、泄漏流量的测量方法。
第三,进行测试系统的软件设计。
主要研究了面向仪器和测控系统的图形化开发平台LabVIEW以及本测试系统的软件结构和实现方法。
第二章电液伺服阀特性
2.1电液伺服阀的组成
伺服阀分为有机液伺服阀、气液伺服阀和电液伺服阀三大类,它们的基本组成部分相同,工程控制中绝大多数为电液伺服阀。
电液伺服阀是电液伺服控制中的关键元件,它是一种接受模拟电信号后,相应输出调制的流量和压力的液压控制阀。
电液伺服阀具有动态响应快、控制精度高、使用寿命长等优点,已广泛应用于航空、航天、舰船、冶金、化工等领域的电液伺服控制系统中。
电液伺服阀是一种自动控制阀,它既是电液转换元件,又是功率放大元件,其公用是将小功率的模拟量电信号转换为随电信号大小和极性变化、且速度响应的大功率液压能(流量或压力)输出,从而实现对液压执行器位移(或转速)、速度(或角速度)、加速度(或角加速度)的控制。
电液伺服阀的结构如图2.1所示。
图2.1电液伺服阀的结构图
电液伺服阀通常由电气—机械转换器(力矩马达)、液压放大器(先导级阀和功率级主阀)和检测反馈机构组成的。
电液伺服阀系统框图如图2.2所示。
图2.2电液伺服阀系统框图
2.1.1电气—机械转换器
电气-机械转换器是电液控制阀的直接输入器件,其功用是将来自控制放大器的电信号转换成力或力矩,去操纵液压阀阀芯的位移或转角,液压阀及整个液压系统的稳态控制精度,动态响应性能和工作可靠性,都在很大程度上取决电气-机械转换器性能的优劣。
对电气-机械转换器的一般要求如下:
具有足够的输出力和位移;稳态特性好,线性度好,灵敏度高,死区小,滞环小;动态性能好,响应速度快;尺坟紧凑,结构简单,制造方便,输入输出参数和连接尺寸标准化,规化,在某些情况下要求能在特殊环境下使用。
电气-机械转换器的种类繁多,按照作用原量与磁系统特征不同分类,主要有:
电磁式,感应式,电动力式,电磁铁式,永磁式,极化式,动圈式,动铁式,直流,交流等。
按结构形式与性能特点,主要有开关型电磁铁,动圈式马达,力矩马达,步进电动机等。
2.1.2液压放大器
液压放大器用于功率放大,通常包括先导级阀和功率级主阀。
若是单级阀,则是无先导级阀;否则为多级阀。
先导级阀又称前置级,用于接受小功率的电气—机械转换器输入的位移或转角信号,将机械量转换为液压力驱动级主阀;主阀多为滑阀,它将先导级阀的液压力转换为流量或压力输出。
2.1.3检测反馈装置
设在阀部的检测反馈机构将先导阀或主阀控制口的压力、流量或阀芯的位移反馈到先导级阀的输入端或比例放大器的输入端,实现输入输出的比较,解决功率级主阀的定位问题并获得所需的伺服阀压力—流量性能。
常用的反馈形式有机械反馈(位移反馈、力反馈)、液压反馈(压力反馈、微分压力反馈等)和电气反馈。
2.1.4伺服阀的特性及测试原理
电流和负载压力)之间的相互关系.主要包括负载流量特性、空载流量特性和压力特性,并由此可得到一系列静态指标参数,它可以用特性方程、特性曲线和阀系数等三种方法表示。
2.2伺服阀的静态特性
电液伺服阀通常包括电气一机械转换器、液压放大器、反馈机构等部分,因此阀的特性方程通常首先要电磁学、流体力学和刚体力学的基本方程列出各组成环节的特性方程,然后经过综合化简才能导出。
下面以理想零开口四边滑阀为例,介绍阀的负载流量方程.理想零开口四边滑阀的阀口对称,各阀口流量系数相等,油液是理想液体,不计泄漏和压力损失,供油压力
恒定不变.当阀芯从零位向右移时,则流入、流出阀的流量
、
为
公式(2.1)
公式(2.2)
稳态时,
,则可得供油压力
,则有
公式(2.3)
公式(2.4)
由上面四个式子可以得出
公式(2.5)
式中
——负载流量;
——流量系数;
——滑阀的面积梯度;
d——滑阀阀芯凸肩直径:
——滑阀位移;
——伺服阀供油压力;
——伺服阀负载压力;
由特性方程可以绘制出相应的特性曲线,并由此得到一系列静态指标参数。
由特性曲线和相应的静态指标可以对阀的静态特性进行评定。
2.2.1负载流量特性曲线
负载流量特性曲线是输入不同电流时对应的流量与负载压力构成的抛物线簇曲线,如图2.3所示。
负载流量特性曲线完全描述了伺服阀的静态特性.但要测得这组曲线却相当麻烦,特别是在零位附近很难测出精确的数值,而伺服阀却正好在此处工作的.所以这些曲线主要用来确定伺服阀的类型和估计伺服阀的规格,以便与所要求的负载流量和负载压力相匹配。
图2.3负载流量特性曲线
伺服阀的规格也可以由额定电流I、额定压力P、额定流量q来表示。
额定电流I为产生额定流量对线圈任一极性所规定的输入电流(不包括零偏电流),以A为单位。
规定额定电流时,必须规定线圈的连接形式。
额定电流通常指单线圈连接、并联连接或差动连结而言。
当串联连接时,其额定电流为上述额定电流之半。
额定压力P额定工作条件时的供油压力,或称额定供油压力,以Pa为单位。
额定流量q在规定的阀压降下,对应于额定电流的负载流量,以
为单位。
通常,在空载条件下规定伺服阀的额定流量,此时阀压降等于额定供油压力。
也可以在负载压降等于三分之二供油压力的条件下规定额定流量,这样规定的额定流量对应阀的最大功率输出点。
2.2.2空载流量特性曲线
空载流量特性曲线是输出流量与输入电流呈回环状的曲线,是在给定的伺服阀压降和零贸载压力下,输入电流在正负额定电流之间作一完整的循环,输出流量点形成的完整连续变化曲线(简称流量曲线).通过流量曲线,可以得出电液伺服阀的额定流量、流量增益、非线性度、滞环、不对称度、零偏等性能指标参数。
空载流量特性曲线如图2.4所示。
线性度:
流量伺服阀名义流量曲线的直线性.以名义流量曲线与名义流量增益线的最大偏差电流值与额定电流的百分比表示。
线性度通常小于7.5%。
对称度:
阀的两个极性的名义流量增益的一致程度。
用两者之差对较大者的百分比表示。
对称度通常小于10%。
滞环:
在流量曲线中,产生相同输出流量的往、返输入电流的最大差值与额定电流的百分比。
伺服阀的滞环一般小于5%。
滞环产生的原因:
一方面是力矩马达磁路的磁滞,另一方面是伺服阀中的游隙。
磁滞回环的宽度随输入信号的大小而变化,当输入信号减小时,磁滞回环的宽度将减小.游隙是由于力矩马达中机械固定处的滑动以及阀芯与阀套间的摩擦力产生的.如果油是脏的第则游隙会大大增加,有可能使伺服系统不稳定。
分辨率:
使阀的输出流量发生变化所需的输入电流的最小变化值与额定电流的百分比,称为分辨率.通常分辨率规定为从输出流量的增加状态回复到输出流量减小状态所需之电流最小变化值与额定电流之比.伺服阀的分辨率一般小于1%.分辨率主要由伺服阀中的静摩擦力引起的。
重叠:
伺服阀的零位是指空载流量为零的几何零位.伺服阀经常在零位附近工作,因此零区特性特别重要.零位区域是输出级的重叠对流量增益起主要影响的区域.伺服阀的重叠用两极名义流量曲线近似直线部分的延长线与零流量线相交的总间隔与额定电流的百分比表示.伺服阀的重叠分三种情况,即零重叠、正
重叠和负重叠。
零偏:
为使阀处于零位所需的输入电流值(不计阀的滞环的影响),以额定电流的百分比表示.零偏通常小于3。
图2.4空载流量特性曲线
2.2.3压力特性
压力特性是输出流量为零(将两个负载口堵死)时,负载压降与输入电流呈回环状的函数曲线,在压力特性曲线上某点或某段的斜率称为压力增益,它直接影响伺服系统的承载能力和系统剐度,压力增益大,则系统的承载能力强、系统刚度大、误差小。
压力特性曲线如图2.5所示。
图2.5压力特性曲线
2.2.4静耗流量特性(泄特性)
输出流量为零时,由回油口流出的部泄漏称为静耗流量.静耗流量随输入电流变化,当阀处于零位时,静耗流量最大。
对于两级伺服阀,静耗流量由先导级的泄漏流量和功率级的泄漏流量两部分组成,减小前者将影响阀的响应速度;后者与滑阀的重叠情况有关,较大重叠可以减少泄漏,但会使阀产生死区,并可能导致阀淤塞,从而使阀的滞环与分辨率增大。
泄特性曲线如图2.6所示。
图2.6泄特性曲线
伺服阀的阀系统主要用于系统的动态分析.伺服阀的负载流量方程是一个非线性方程,采用线性控制理论对系统进行动态分析时较为困难,故通常将它进行线性化处理,并以增量形式表示为:
公式(2.6)
流量增益(流量放大系数),流量特性曲线的斜率,表
示负载压力一定时,阀单位位移所引起的负载流量变化的大小。
流量增益越大,对负载流量的控制越灵敏。
流量压力系数,压力一流量特性曲线的斜率并冠以负号,使其成为正值。
流量压力系数表示阀的开度一定时,负载压降变化所引起的负载流量变化的大小,它反映了阀的抗负载变化能为,即
越小,阀的抗负载变化能力越强,亦即阀的刚性越大。
压力增益(也称压力灵敏度),压力特性曲线的斜率。
通常,压力增益表示负载流量为零时(将控制口关死)时,单位输入位移所引起的负载压降变化的大小。
此值大,阀对负载压降的控制灵敏度高[7-9]。
因此阀方程式也可以写成以下形式
公式(2.7)
2.3本章小结
本章主要介绍了电液伺服阀的组成及静态特性主要几个指标,更一步的对伺服阀的特性进行说明。
第三章测试系统硬件设计
本课题设计的基于虚拟仪器的电液伺服阀试验台的最大特点是能实现对伺服阀的静态性能的快速的自动检测,最大限度地减少人的参与。
就要求各被测量能够转换为电信号被自动地采集到控制系统程序中,以及控制程序能够实现对试验台相关元件的电信号控制。
为了实现这一目的,系统中的所有压力、流量、温度等信息都要转换为电信号,输入到控制系统中,一些执行元件也要能够被控制系统远程控制。
主要硬件大致包括计算机、传感器、输入输出接口电路、计算机外设等。
本测试系统是根据国家标准QJ2078A—1998电液伺服阀静态实验装置设计的,国家标准如图3.1所示。
V1—调压阀;V2—负载节流阀;V3—部泄漏阀;V4—回油阀;
V5—溢流阀;V6—控制阀;V7—旁通阀;T—温度计;
Ps、P1、P2、Pa—压力传感器。
图3.1国家标准QJ2078A—1998电液伺服阀静态实验装置
电液伺服阀静态实验装置分析:
计算机发出控制信号,通过放大器,使伺服阀线圈工作;液压系统开启,向伺服阀供油;压力传感器PS检测进油口压力,压力传感器Pa检测进回油口压力,压力传感器P1、P2检测控制口压力;T1温度传感器检测液压油进口油温,T2温度传感器检测液压油出口油温;直线位移传感器是测量液压缸的累积流量,线速度传感器是测量液压缸的瞬时流量;流量计是测量伺服阀回油口的流量。
系统静态特性的测试硬件组成如图3.2所示。
图3.2静态测试系统硬件结构
本次设计的原始框图如下表所示:
数
参据
数
数据
IV
最大试验流量(l/min)
63
最大试验压力(MPa)
14
试验精度级别
B
3.1传感器
传感器是能感受规定的被测量并按照一定的规律转换成可用输出信号的器件或装置。
通常,传感器由敏感元件和转换元件组成。
其中,敏感元件是指传感嚣中能直接感受或被测量的部分;转换元件是指传感器中能将敏感元件感受或响应的被测量转换成适于传输或测量的电信号部分。
传感器的静态特性是指被测量的值处于稳定状态时的输出与输入的关系,可以用灵敏度、迟滞、线性度、重复和漂移等表示;传感器动态响应特性分为瞬态响应特性和频率响应特性[10-12]。
传感嚣组成方框图如图3.3所示。
图3.3传感器组成方框图
3.1.1压力传感器的选型
3.1.1.1进油口压力传感器
供油口压力传感器的选型依据有两点:
一个是设计任务书给的最大压力即伺服阀的最大供油压力,另一个是传感器的精度满足任务书规定的精度等级。
该传感器安装在标准实验图上的PS压力表位置处,参照国家标准和设计任务书(最大供油压力14Mpa,精度等级B级—1.5%),本次设计选用一个DG1300系列普及型压力传感器如图3.4所示。
技术性能参数指标为:
测量围:
0~18Mpa
环境温度:
-20~85℃
介质温度:
-30~85℃
供电方式:
24VDC
上升时间:
≤5毫秒可达90%FS
输出形式:
两路输出
输出信号:
4-20mA
准确度:
1.0级(包括非线性、重复性及迟滞在的综合误差)
零点调节:
输出量程的±8%
量程调节:
输出量程的±20%
安装方式:
螺纹连接
M20x1.5
图3.4DG1300型森纳压力传感器
根据国家标准,本次设计选用一个DG1300型森纳压力传感器测伺服阀,采用M20x1.5密封螺纹连接,安装在电液伺服阀的进口管道,测量电液伺服阀的进口压力,测出来的压力转换成电信号,传输到数据采集卡1和2路进行信号处理。
3.1.1.2回油口压力传感器
回油口压力传感器的作用是检测伺服阀出口压力。
它的选型依据两点:
一是回油箱的被压和流量计的压力损失,另一个是设计任务书的精度指标。
该传感器安装的在标准实验图的Pa压力表处,参照国家标准和设计任务书,回的被压为0.8Mpa,流量计的压力损失在25Mpa时为5Kpa~50Kpa,取最大压力损失,任务书供油压力为14Mpa,压力损失为14/25x50kpa=28Kpa即0.028Mpa.所以回油口的最大压力为0.028Mpa+0.8Mpa=0.828Mpa本次设计选择ND-1通用压力变送器,如图3.5。
技术性能参数指标为:
压力形式:
表压/绝压/负压
量程:
0~1Mpa
介质:
气体、液体及弱腐蚀性介质
精度:
0.3级
供电:
12~36VDC(24VDC)
输出:
4mA~20mA
负载电阻:
R=(U-12.5)/0.02-RD其中:
U为电源电压,RD为电缆阻
过载能力:
200%FS
响应时间:
《1ms
接口:
M20*1.5或自定
温度:
-20~85℃
防爆等级:
本安型ExiaIICT6
图3.5ND-1通用压力变送器
根据国家标准,本次设计选用一个ND-1通用压力变送器测伺服阀回油口压力,采用M20x1.5密封螺纹连接,安装在电液伺服阀的出口管道上,测量电液伺服阀的出口压力转换成电信号,传输到数据采集卡3和4路进行信号处理。
3.1.1.3控制口压力传感器选型
控制口压力传感器的作用是检测伺服阀控制压力。
它的选型依据两点:
一控制口的最大压力,另一个是传感器的精度指标。
该传感器安装的在标准实验图的P1、P2压力传感器处,参照国家标准和设计任务书,进油口的最大压力Ps为14Mpa,回油口的压力为0.828Mpa,所以控制口的最大压力PL为14Mpa-0.828Mpa=13.172Mpa,所以传感器选择DG1300型传感器如图3.6。
技术性能参数指标为:
测量围:
0~16Mpa
环境温度:
-20~85℃
介质温度:
-30~85℃
供电方式:
24VDC
上升时间:
≤5毫秒可达90%FS
输出形式:
两路输出
输出信号:
4-20mA
准确度:
1.0级(包括非线性、重复性及迟滞在的综合误差)
零点调节:
输出量程的±8%
量程调节:
输出量程的±20%
安装方式:
螺纹连接M20x1.5
图3.6DG1300型森纳压力传感器
根据国家标准,本次设计选用两个DG1300系列压力传感器,测伺服阀控制口压力。
采用M18x1.5密封螺纹连接,安装在电液伺服阀的控制口管道,测量控制口压力,转换成电信号,传输到数据采集卡5和6路、7路和8路进行信号处理。
3.1.2温度传感器选型
3.1.2.1进口温度传感器
HYDAC贺德克ETS4000系列温度传感器是纯德国进口,质量好精度高,该温度传感器不同于普通的温度传感器,它有很强的耐压等级,非常适用与带有压力负载的测试场合,尤其是测量管道压力液体的温度。
参照QJ2078A-1998电液伺服阀国家试验标准,伺服阀进口处的油液温度为40±6℃,本次设计选用两个HYDAC贺德克ETS4144-A-000温度传感器,技术性能参数指标为:
测量围:
-25-100℃
耐压等级:
600bar(1bar=0.1Mpa)即60Mpa(本次设计最大压力为14Mpa)
精度等级:
0.5
输出形式:
单路
输出信号:
4-20mA
连接方式:
螺纹连接M20x1.5
图3.7HYDACETS4144-A-000
ETS4144-A-000温度传感器在测试系统中,用于出口油温的测量。
IETS4144-A-000温度传感器用螺纹,采用M20x15密封螺纹安装在电液伺服阀进出口管道处,测量出油温电信号,被信号采集卡3路采集,传输给控制系统。
3.1.2.2出口温度传感器
出口温度传感器用来检测伺服阀出口油温,由于伺服阀有功率消耗,出口油温相比进口油温会有一定的升高。
根据设计任务书,最大进口压力14Mpa、最大流量64l/min,查阅相关资料,温度升高值在3℃~5℃,取最大升高温度5℃,选择IC温度传感器温度传感器图3.8。
技术性能参数指标为:
耐压等级:
500bar(1bar=0.1Mpa)即50Mpa
电源电压:
5—15V
工作电流:
500uA