侧抽芯注塑模设计.docx
《侧抽芯注塑模设计.docx》由会员分享,可在线阅读,更多相关《侧抽芯注塑模设计.docx(11页珍藏版)》请在冰豆网上搜索。
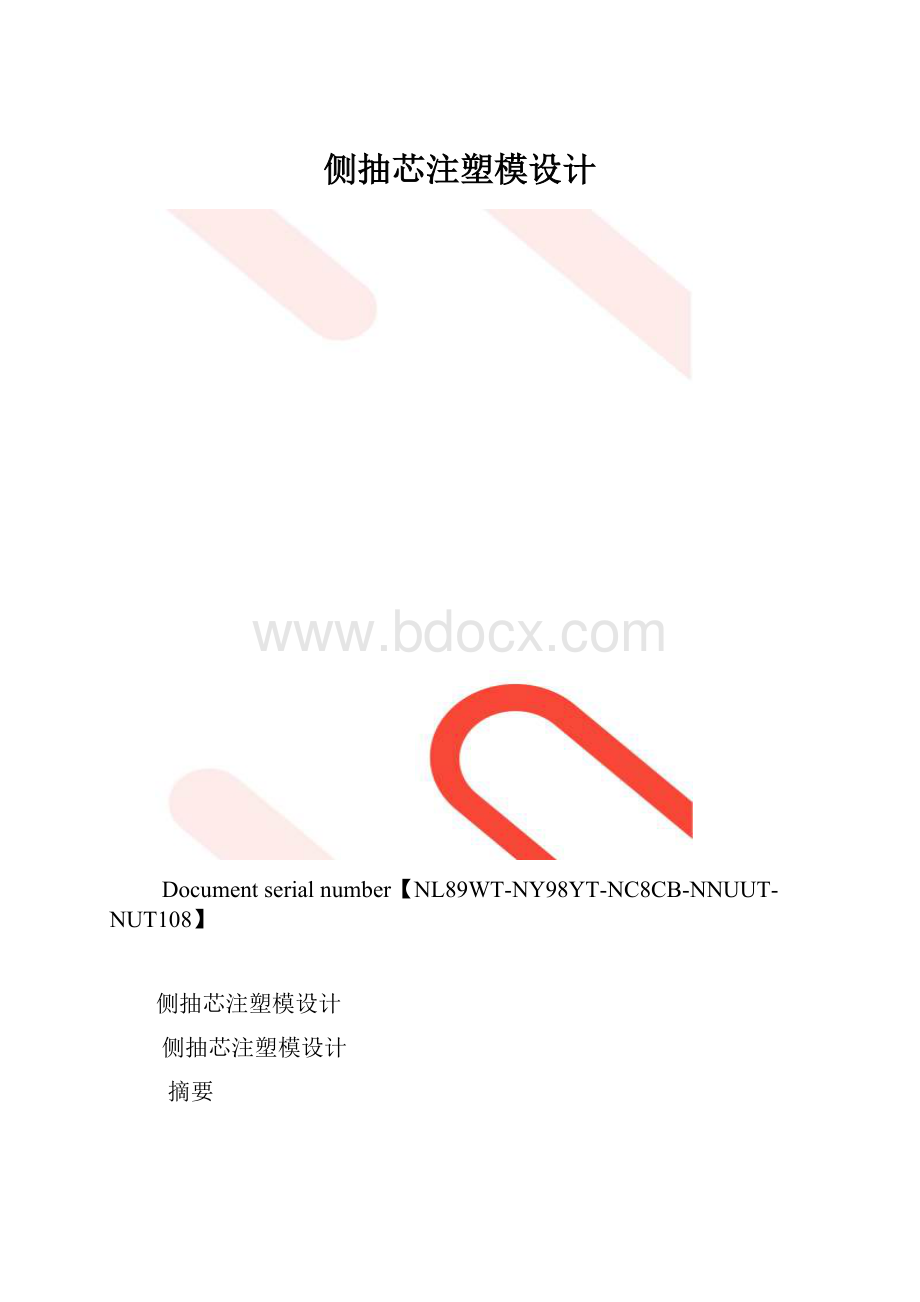
侧抽芯注塑模设计
Documentserialnumber【NL89WT-NY98YT-NC8CB-NNUUT-NUT108】
侧抽芯注塑模设计
侧抽芯注塑模设计
摘要
塑料工业是当今设计上增长最快的工业门类之一,而注塑模具是其中发展较快的种类,因此,研究注塑模具对了解塑料产品的生产过程和提高产品质量有很大意义。
塑料模具设计是模具制造中的关键工作,通过合理设计制造出来的模具不仅能顺利地成型高质量的塑件,还能简化模具的加工过程和实施塑件的高效率生产。
说明书里介绍了模具的结构组成、设计要点、模具成型生产所用的设备、模具材料和热处理要求等。
该说明书主要分为三个部分,分别介绍了塑料的性能,塑料制品的结构设计及工艺性,以及对注塑模具结构与注塑机、塑料制件在模具中的位置与浇注系统的设计、成型部件设计、结构零部件的设计、推出机构设计、侧向分型与抽芯机构设计和温度调节系统等做了介绍。
通过本设计,可以对注塑模具有一个初步的认识,了解注塑模具结构及工作原理。
关键词:
塑料模具、斜导柱、分型面、滑块
前言
塑料模具设计是模具制造中的关键工作,通过合理设计制造出来的模具不仅能顺利地成型高质量的塑件,还能简化模具的加工过程和实施塑件的高效率生产,从而达到降低生产成本和提高附加价值的目的。
近几年来塑料成型工艺迅速发展,塑料模具种类不断增加,结构也愈趋复杂,制造精度要求愈来愈高。
其中注塑成型模具应用最为广泛,而且模具的结构最为复杂。
本次模具设计采用的是一模两腔的模具结构,通过侧向分型与抽芯机构完成了塑件的成型。
说明书中介绍了模具的结构组成、结构特点、工作原理、设计要点、模具成型生产所用的设备、模具材料和热处理要求等。
该说明书主要分为三个部分,第一章主要介绍了塑料的性能,第二章介绍了塑料制品的结构设计及工艺性,第三章对注塑模具结构与注塑机、塑料制件在模具中的位置与浇注系统的设计、成型部件设计、结构零部件的设计、推出机构设计、侧向分型与抽芯机构设计和温度调节系统等做了介绍。
本说明书在编写过程中得到了师友的支持和帮助,在此我表示感谢。
同时感谢所引用文献的作者,他们辛勤研究的成果使得本次设计增色不少。
限于学生水平有限,难免出现不少的缺点和错误,恳切希望各位老师批评指正。
第1章塑料的性能
1.1设计要求
大批量生产,精度为一般精度。
图1-1塑件
1.2塑料的组成
塑料是以合成树脂为主要成分,加入适量的添加剂组成的。
1.2.1合成树脂
ABS塑料
化学名称:
丙烯-丁二烯——苯乙烯共聚物
比重:
克/立方厘米成型收缩率:
查表得收缩率为:
%%。
材料分析:
ABS无毒无味,呈微黄色,成型的塑件有较好的光泽,具有良好的机械强度和一定的耐磨性,耐寒性,耐油性,耐水性,化学稳定性和电器性能,密度为~cm3
ABS有一定的硬度和尺寸稳定性,易于加工,经过配色可配成任何颜色。
成型特点:
ABS在升温时粘度增高,所以成型压力较高,故塑件上的脱模斜度宜稍大,ABS易吸水,成型加压前应进行干燥处理,ABS易产节痕,模具设计时应注意尽量减少浇注系统对料流的阻力,在正常的成型条件下壁厚,熔料温度对收缩率影响极小,在要求塑件精度高时,模具温度可控制在50~60°c,而强调塑件光泽和耐热时,模具温度应控制在60~80°c。
1.2.2添加剂
填充剂——玻璃微珠;PS成型后易产生内应力,添加玻璃微珠使塑料的流动性好,残余内应力分布均匀,使光的漫反射率为80光稳定剂——氧化锌;塑料制品在日光或强荧光下,由于吸收紫外光的能量,引发氧化反应,导致聚合物降解,使制品的外观或内在性能变坏,这一过程称为光氧化或光老化。
润滑剂——硬脂酸及其盐类;对塑料的表面去润滑作用,防止塑料在成型加工时黏模。
同时提高塑料制品表面光洁度。
着色剂——青绿色;在塑料制品中,需要着色的大约占80%左右,着色的目的有:
①增加制品美感,以吸引消费者的购买欲望②提高产品的耐候性,主要是通过着色剂防紫外线功能而实现的。
图1-2制件
第2章塑料制品的结构设计及工艺性
2.1尺寸及精度
塑件的尺寸精度是决定塑件制造质量的首要标准,然而,在满足塑件使用要求的前提下,设计时总是尽量将其尺寸精度放低一些,以便降低模具的加工难度和制造成本。
对塑件的精度要求,要具体分析,根据装配情况来确定尺寸公差,该精度要求为一般精度即可,对其要有公差配合要求的部位,应选择高精度。
根据精度等级选用表,ABS的高精度为2级,一般精度为3级。
根据塑件尺寸公差表,在公称尺寸在40-50范围内,取MT2B级的公差数值为,MT3B级的公差数值为。
制品尺寸误差构成为:
Б=Бs+Бz+Бc+Бa(2-1)
式中Б——总的成型误差;
Бs——塑料收缩率波动所引起的误差;
Бz——模具成型零件制造精度所引起的误差;
Бc——模具磨损后所引起的误差;
Бa——模具安装,配合间隙引起达到误差。
2.2表面粗糙度
塑料制件的表面粗糙度是决定其表面质量的主要因素。
塑件的表面粗糙度主要与模具型腔表面的粗糙度有关。
一般来说,模具表面的粗糙度比塑件低1-2级。
塑件的表面粗糙度Ra一般为。
模具在使用过程中,由于型腔磨损而使表面粗糙度值不断加大,所以应给予抛光复原。
2.3脱模斜度
塑件成型时冷却过程中产生收缩,使其紧箍在凸模或型芯上为便于脱模,防止因脱模力过大而拉坏塑件或使其表面受损,与脱模方向平行的塑件内,外表面都应具有合理的斜度,以下是ABS脱模斜度推荐值:
塑件外表面塑件内表面
35′——°30′——1°
塑件内表面在造型时就有弧度,如果要有脱模斜度就是在凹槽和锁位处,这不仅对脱模有好处,而且可以更好的锁紧。
2.4壁厚
塑件应有一定的壁厚,这不仅是为了塑件在使用过程中有足够的强度和刚度,而且为了塑件成型时保持良好的流动状态。
塑件壁厚一般在1-4mm,如果壁厚过大,则易产生气泡和凹陷,同时也不易冷却。
2.5圆角
塑件上各处的轮廓过度和壁厚连接处,一般采用圆角连接,有特殊要求时才采用结构,尖角容易产生应力集中,在受力或受冲击载荷时会发生破裂。
圆角不仅有利于物料填充,同时也有利于融料在模具型腔内的流动和塑件脱模。
圆角的取值与应力集中的关系遵循R/T函数关系,当R/T=以后应力集中变的缓和,该塑件大部分的圆角取R1,较大值取R3。
2.6孔
塑件上常见的孔有通孔、盲孔、异形孔和螺纹孔等。
这些孔均应设置在不易削弱是塑件强度的地方,在孔与孔之间、孔与壁之间应留有足够的距离。
此外,孔的深度不宜太大,否则型芯会弯曲。
塑件上其他的特征还有如螺纹,嵌件,铰链,文字和花纹等,各个特征都有其设计原则和特殊功能,因为该塑件没有涉及,所以就不一一介绍了。
第3章注射成型模具设计
3.1选用注射机确定型腔数目
3.1.1根据塑件的形状估算其体积和重量
V=2X25X30X5+50X25X5X2+50X30X5-2XπX42X5
=17cm3(3-1)
m=ρv==(3-2)
式中ρ为塑料密度。
3.1.2根据塑料的计算重量或体积选择设备型号规格,确定型腔数
1.注射机的最大注射量mΡ,每次注射量不超过最大注射量的80%,
即:
n≤(KmΡ-m1)/m(3-3)
式中K——注射机最大注射量的利用系数,一般取;
mΡ——注射机最大注射量,g;
m1——浇注系统凝料量,g;
额定注射量
125cm3
螺杆直径
42mm
注射压力
120Mpa
注射行程
115mm
注射时间
1.6s
螺杆转速
69r/min
注射方式
螺杆式
合模力
900KN
最大成型面积
320cm2
最大开合模行程
300mm
模具最大厚度
300mm
模具最小厚度
200mm
动定模固定板尺寸
428x458
拉杆空间
260x290
合模方式
液压-机械
定位圈尺寸
Φ100mm
喷嘴球头半径
SR12mm
喷嘴孔直径
4mm
顶出形式
两侧顶出
顶杆中心距
230mm
机器外形尺寸
3310x750x1550
mmxmmxmm
m——单个塑件的质量,g。
估算浇注系统的体积V=15cm3,则浇注系统的塑料重量
m1==
设n=2,则得:
mΡ=(nm+m1)/=
从计算结果,并根据塑料注射机技术规格,选用XS——ZY——125型注射机。
2.根据塑件精度,由于该塑件精度一般,故采用多型腔,即n=2。
生产批量大批量生产,取一模两腔。
3.1.3注射机型号
XS——ZY——125
表3-1注射机的规格和性能
3.1.4校核所选注射机
⑴注射量的校核
由前面计算得塑件重量为,浇注系统重量为则每次注射所需的塑料为+=
注射机的最大注射量=100>能满足要求。
⑵按注射机的锁模力与注射压力进行校核
P(nA+A1)≤FP(3-4)
式中FP——注射机额定锁模力,N;查表得900KN
A——单个塑件在模具分型面的投影面积,mm2;
A1——浇注系统在模具分型面上的投影面积,mm2;
P——塑料熔体对型腔的成型压力,其大小一般是注射压力的80%Mpa查表知Pm=70-90Mpa
其中
A=30x50=1500mm2
A1=15x50=75mm2
P取80Mpa
P(nA+A1)=80x(2x1500+75)=246000N=246KN<900KN
故满足要求。
同时XS——ZY——125的额定注射压力为120Mpa,故也满足ABS塑料成型的注射压力要求。
⑶模具厚度H与注射机闭合高度的校核
Hmax>H>Hmin(3-5)
式中Hmax——注射机允许的最大厚度,200mm;
Hmin——注射机允许的最小厚度,300mm;
H——预选模架厚度,201mm;
因为300>201>200,所以满足要求。
⑷注射机开模行程
注射机开模行程应大于模具开模时取出塑件所需的开模距,由于Hc=25≤H1+H2,对开模行程无影响
即满足下式:
S≥H1+H2+(5~10)(3-6)
式中S——注射机的最大开模行程,mm;
——推出距离,mm;
——包括浇注系统在内的塑件高度,mm;
——完成侧抽芯所需的开模行程,mm;
则H1+H2+10=26+58+10=94<300,故能满足要求。
3.2塑料制件在模具中的位置
3.2.1分型面的确定
根据分型面的设计原则:
⑴应选在塑件外形最大轮廓处;
⑵应有利于塑件的顺利脱模;
⑶应保证塑件的精度要求;
⑷应满足塑件的外观质量要求;
⑸要便于模具的加工制造;
⑹应有利于排气。
综合考虑之后,确定分型面如图3-1所示:
图3-1分型面的形状
3.2.2型腔数目的确定
注塑模的型腔数目,可以是一模一腔,也可以是一模多腔,在型腔数目的确定时主要考虑以下几个有关因数:
⑴按注射机的最大注射量确定型腔数目;
⑵按注射机的额定锁模力确定型腔数目;
⑶按塑件的精度要求确定型腔数目。
综合考虑之后,初定为一模两腔最合理。
排列形式如图3-2所示:
图3-2浇口的形式
3.3浇注系统的设计
注射模的浇注系统是指模具中从注塑机喷嘴开始到型腔入口为塑料熔体的流动通道,它由主流道,分流道,冷料穴和浇口组成。
它向型腔中的传质,传热,传压情况决定着塑件的内在和外表质量,它的布置和安排影响着成型的难易程度和模具设计及加工的复杂程度,所以浇注系统是模具设计中的主要内容之一。
3.3.1主流道的设计
主流道是连接注塑机的喷嘴与分流道的一段通道,通常和注塑机的喷嘴在同一轴线上,断面为圆形,有一定的锥度,目的是便于冷料脱模,同时也改善料流的速度,因为要和注塑机相配,所以其尺寸与注塑机有关,如图3-3所示:
图3-3主流道形状
主要参数:
锥角α=3°;内表面粗糙度Ra=μm;
小端直径D=d+(~1)mm=4mm;材料T8A;
半径R2=R1+(1~2)mm=12mm;
d——喷嘴直径;R1——喷嘴球半径
该浇口套直接嵌入模板内。
3.3.2分流道的设计
分流道是主流道与浇口之间的通道,一般开设在分型面上,起分流和转向作用,分流道的长度取决于模具型腔的总体布置和浇口位置,分流道的设计应尽可能短,以减少压力损失,热量损失和流道凝料。
分流道的断面形状有圆形,矩形,梯形,U形和六角形。
要减少流道内的压力损失,希望流道的截面积大,表面积小,以减小传热损失,因此,可以用流道的截面积与周长的比值来表示流道的效率,其中圆形和正方形的效率最高,但正方形的流道凝料脱模困难,所以一般是制成梯形流道,在该模具上取U形断面形状。
主要参数:
分流道的宽度b=15mm;半径R=;
深度h=;斜角α=5°;
长度L=50mm;粗糙度Ra=μm
3.3.3浇口的设计
图3-4侧浇口的形式
浇口是连接分流道与型腔的一段细短的通道,它是浇注系统的关键部分,浇口的形状,数量,尺寸和位置对塑件的质量影响很大,浇口的主要作用有两个,一是塑料熔体流经的通道的,二是浇口的适时凝固可控制保压时间。
浇口是类型有很多,有点浇口,侧浇口,直接浇口,潜伏式浇口等,各浇口的应用和尺寸按塑件的形状和尺寸而定,该模具采用侧浇口,浇口形式如图3-4所示。
其有以下特性:
⑴形状简单,去除浇口方便,便于加工,而且尺寸精度容易保证;
⑵试模时如发现不当,容易及时修改;
⑶能相对独立地控制填充速度及封闭时间;
⑷对于壳体形塑件,流动充填效果较佳。
主要参数:
厚度t=宽度b=5mm;
浇口长度L=。
3.3.4冷料穴和拉料杆的设计
冷料穴一般位于主流道对面的动模板上,或处于分流道末端,其作用是存放料流前端的冷料,防止冷料进入型腔而形成冷接缝,主流道末端的冷料穴除了上述作用外,还有便于在该处设置主流道拉料杆的功能,开模时能将主流道凝料从定模板中拉出。
冷料穴的尺寸宜稍大于主流道大端的直径,长度约为主流道大端直径。
由于塑件采用推件板推出机构,故采用球头拉料杆。