48FW炉型超临界机组运行方式的研究84.docx
《48FW炉型超临界机组运行方式的研究84.docx》由会员分享,可在线阅读,更多相关《48FW炉型超临界机组运行方式的研究84.docx(19页珍藏版)》请在冰豆网上搜索。
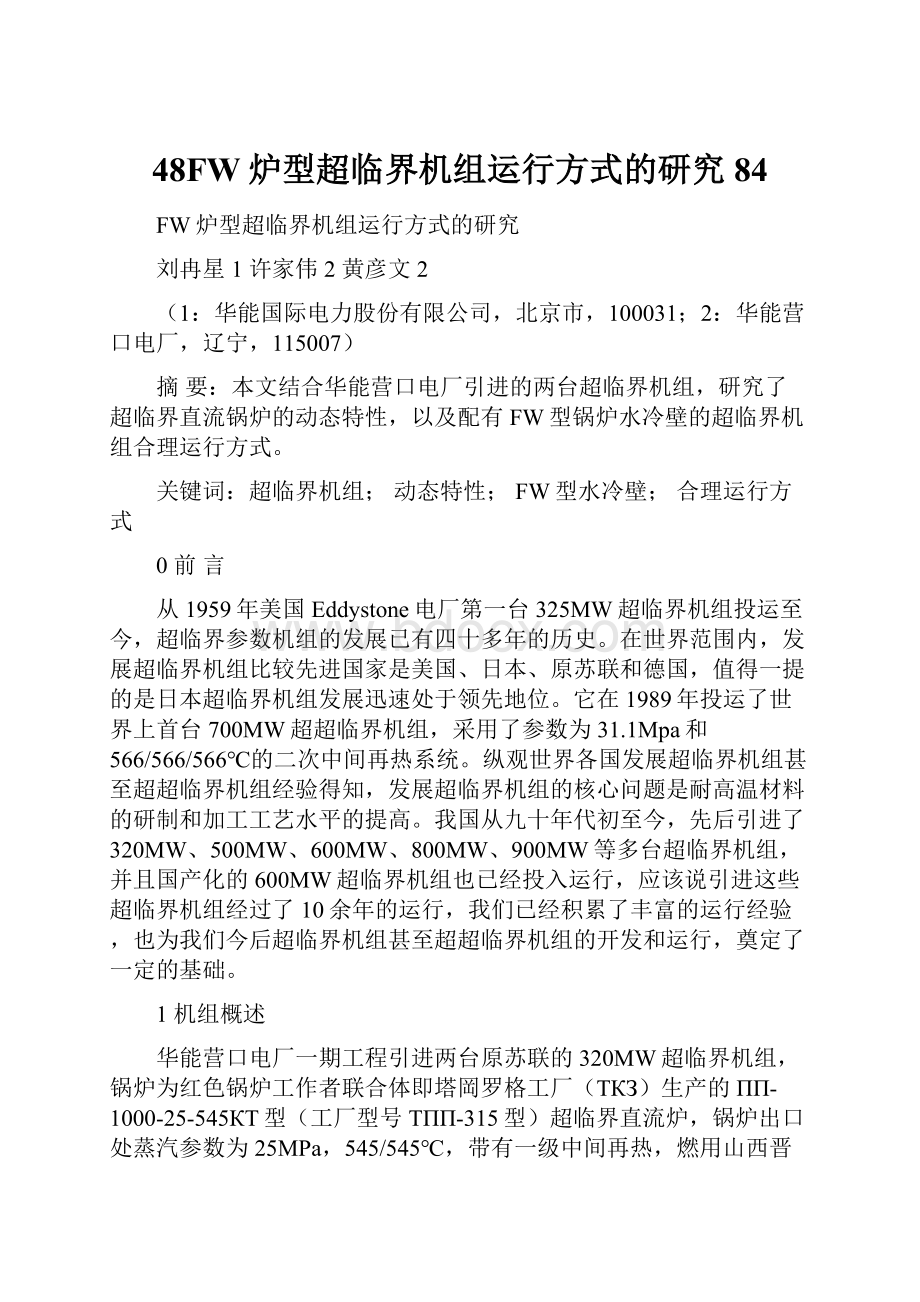
48FW炉型超临界机组运行方式的研究84
FW炉型超临界机组运行方式的研究
刘冉星1许家伟2黄彦文2
(1:
华能国际电力股份有限公司,北京市,100031;2:
华能营口电厂,辽宁,115007)
摘要:
本文结合华能营口电厂引进的两台超临界机组,研究了超临界直流锅炉的动态特性,以及配有FW型锅炉水冷壁的超临界机组合理运行方式。
关键词:
超临界机组;动态特性;FW型水冷壁;合理运行方式
0前言
从1959年美国Eddystone电厂第一台325MW超临界机组投运至今,超临界参数机组的发展已有四十多年的历史。
在世界范围内,发展超临界机组比较先进国家是美国、日本、原苏联和德国,值得一提的是日本超临界机组发展迅速处于领先地位。
它在1989年投运了世界上首台700MW超超临界机组,采用了参数为31.1Mpa和566/566/566℃的二次中间再热系统。
纵观世界各国发展超临界机组甚至超超临界机组经验得知,发展超临界机组的核心问题是耐高温材料的研制和加工工艺水平的提高。
我国从九十年代初至今,先后引进了320MW、500MW、600MW、800MW、900MW等多台超临界机组,并且国产化的600MW超临界机组也已经投入运行,应该说引进这些超临界机组经过了10余年的运行,我们已经积累了丰富的运行经验,也为我们今后超临界机组甚至超超临界机组的开发和运行,奠定了一定的基础。
1机组概述
华能营口电厂一期工程引进两台原苏联的320MW超临界机组,锅炉为红色锅炉工作者联合体即塔岡罗格工厂(ТКЗ)生产的ПП-1000-25-545КТ型(工厂型号ТПП-315型)超临界直流炉,锅炉出口处蒸汽参数为25MPa,545/545℃,带有一级中间再热,燃用山西晋北烟煤。
锅炉采用П型单炉体布置,多次垂直上升膜式水冷壁(下辐射区三次,上辐射区二次),敷管炉墙全悬吊式结构。
二十四只旋流式喷燃器,前后墙对称布置,各分三层,每层四个。
炉膛上部布置有前后屏过热器;水平烟道布置有凝渣管、对流过热器和高温再热器,尾部竖井布置有低温再热器和省煤器,省煤器后的烟气,一部分可经再循环风机送回炉膛。
空气预热器又布置在另一尾部烟道,采用三台回转式(即再生式)空气预热器,每台直径为8.8米,两台供二次风,一台供一次风。
制粉系统采用煤粉直吹式系统,配有6台中速磨煤机。
除渣方式是固态排渣,锅炉底部设有螺旋输渣机和碎渣机。
锅炉主要参数:
锅炉额定蒸发量1000t/h
过热器出口汽温545℃
过热器出口汽压25.01MPa
给水温度277℃
再热蒸汽流量830.4t/h
再热器进口汽压4.01MPa
再热器出口汽压3.76MPa
再热器进口汽温290℃
再热器出口汽温545℃
锅炉效率92%
与锅炉配套的汽轮机是由哈尔科夫汽轮机厂生产的K-320-23.5-4型超临界压力、单轴、三缸、双排汽、一次中间再热汽轮机,机组采用单旁路启动系统。
汽轮机配备有凝汽器装置和回热装置。
汽轮机还配备了汽动给水泵组,由ПH-1100-330型给水泵,ПД-1600-180-2a型前置泵及K-17-15П型的凝汽式驱动汽轮机组成,驱动汽轮机使用第四段汽轮机抽汽。
汽轮机的技术参数和主要特性:
保证条件下电功率334MW
额定功率320MW
新汽额定参数
压力23.5MPa
温度540℃
新汽额定流量1000t/h
再热蒸汽额定参数
压力3.78MPa
温度540℃
冷却水设计温度20℃
凝汽器绝对压力4.87MPa
凝汽器中冷却水流量33985t/h
除氧器中蒸汽绝对压力0.67MPa
给水温度278℃
保证条件下的毛热耗率7653.1KT/KWh
2超临界直流锅炉动态特性
超临界直流锅炉由于采用超临界压力,所以没有蒸发段,只有加热段和过热段,受热面管径变小,管壁增厚,蓄热能力小,这些对动态特性都会有影响。
锅炉动态特性是指锅炉在突然受到内、外扰动的反应,可确定各种不同扰动下下操作的极限允许值;认识锅炉变工况时该如何调节。
因此掌握动态特性对提高锅炉运行水平,分析处理异常事件,以及合理设计和运用热工调节系统都具有重要意义。
下面分析直流锅炉的动态特性:
2.1调速汽门开度扰动
给水量、燃料量、喷水量及送风量等内扰因素保持不变,当调节门开度μT突然开大时,汽轮机功率N增加,由于锅炉内热负荷及给水量G等未变,锅炉蒸发量D的暂且增大只能依靠汽压P下降所放出的附加蒸发量来补足。
也由于炉内热负荷未变,当此锅炉蒸发量瞬间增大之际,导致过热蒸汽出口温度t下降,但是由于蓄热的影响,一般有20-30秒的迟延,下降值也不大。
可见,当调节门突然开大时,锅炉参数变化是:
蒸发量D暂时增大,由于给水量未变,以后又降到原值,过热蒸汽出口压力P下降,过热蒸汽出口温度t先下降,但下降不大,后又回升一些。
如图1。
2.2给水量扰动
在直流锅炉中,给水量的扰动将引起汽压P、汽温t以及蒸汽量D的变化。
保持功率N、燃料量B、送风量V、喷水量、给水温度不变。
当给水量G突然增大时,由于需要加热的工质增加,使加热区增长,因此,过热区段缩短。
另一方面,直流锅炉的工质等一次强迫通过各个受热面区段,在达到稳定流动时,进入的给水量G等于送出的蒸发量D,因此给水量增加时蒸发量也同量地增加。
过热区段的缩短和蒸发量的增加,都促使过热汽温下降,至于蒸汽压力P的上升,则是由于汽轮机功率未变,它并不要求增加蒸汽流量,因而锅炉蒸发量随给水量增加时出口汽压升高。
在对给水量扰动的响应过程中,蒸发量D有迟延τ。
如图2所示。
2.3燃料扰动
燃料扰动将促使炉膛热负荷变化,是锅炉运行中主要和常见的扰动。
在燃煤时尤为突出,因为运行过程中给煤量不直接测定,煤的发热量变化也无及时的数量估计,即使给煤量稳定不变,煤种也可能变化,即使燃用同一煤种,煤粉细度也可能有变化。
保持功率、给水量、给水温度、送风量、喷水量等不变。
当燃料量增加时,由于直流锅炉的相变点前移,扰动后的一段短时间内蒸发量超过了给水量;又由于给水量未变,随后又回复到原来值,即蒸发量等于给水量。
燃料量的增加和过热区段的增长使过热器出口汽温升高,同样,扰动引起的蒸发量突增,使过热汽温的上升发生迟延τ。
过热区段金属的蓄热作用使过热汽温有更大的延迟。
至于汽压P在无功率扰动的情况下,它与蒸发量D一样,随蒸发量在刚开始一段短时间内亦有一短暂的压力上升,而后回复到原来值。
可见,燃料扰动主要引起汽温变化,变化程度取决于扰动量和过热区段的蓄热能力。
如图3所示。
2.4给水和燃料的复合扰动
由上可知,单一的给水或燃料扰动都会使过热汽温发生变化,可见直流锅炉燃料量与给水量之间平衡破坏的主要标志是过热蒸汽温度。
给水与燃料复合扰动的动态特性是给水、燃料两个单独扰动动态特性的叠加。
如图4所示,可以看出,只要给水、燃料按比例变化,便可使蒸发量D很快稳定在一个新的水平。
而过热汽温t可维持不变。
这种成比例的复合扰动的重要特性可以用来满足外界负荷扰动的要求,运行操作中严格控制“煤水比”是直流锅炉调节蒸汽参数的关键。
通过研究直流锅炉动态特性,可得出以下结论:
在燃料扰动一开始的过渡过程中,锅炉蒸发量与燃料发出的热量成比例变化,因而蒸发量可以作为运行工况发生变化的一个信号。
过热蒸汽温度,从开始过渡的截面算起,愈往出口发生变化的迟延愈大。
过热开始截面的汽温迟延约40-120秒;而出口汽温t变化迟延约200-400秒。
可见若直接以出口汽温作为信号来调节出口汽温,势必造成调节滞后和不稳定。
为了能稳定而可靠地调节过热汽温,必须使用超前信号,即选用过热区段出口之前的某一点汽温。
对应于相同程度的工况变动,压力较低的直流锅炉,其有效蓄热量的变化要比压力高的直流锅炉大,因此在受各种扰动后,蒸汽参数的变化一般也较大。
受内扰时,D与P是同向变化;受外扰时D与P呈反向变化。
3超临界机组合理运行方式
3.1超临界机组的运行方式
随着我国火电结构的优化,超临界大容量机组得到了广泛的发展,掌握超临界机组运行技术,研究超临界机组合理的运行方式,对提高临界机组运行水平,发挥超临界机组的技术优势和经济优势,提高超临界机组的可用率,使这些超临界机组安全、经济运行是非常必要的。
不合理的运行方式,错误的调整方式,无疑都会给机组带来严重影响,潜在的隐患缩短了机组零件的寿命,甚至造成设备损坏。
所谓超临界机组合理的运行方式,就是根据超临界机组结构特点,运行特性,在安全经济的前提下,寻求最优化的机组启动停机方式,运行中负荷调整和压力运行方式。
超临界机组的运行方式,取决于配套的直流锅炉的水冷壁形式,制粉系统形式,启动部件及旁路系统形式等许多因素,作为单元机组负荷运行有三种基本方式。
①机跟炉方式:
机组负荷跟随锅炉负荷的改变而改变。
②炉跟机方式:
锅炉负荷是跟汽机负荷的变化而变化;
③协调运行方式:
锅炉和汽机同时改变负荷。
因为直流锅炉的蓄热量小于汽包炉的蓄热量,所以采用直吹式制粉系统直流锅炉组成的单元制机组组,由于其负荷适应性较差,宜采用机跟炉的方式,这样有利于机组的稳定运行;而采用中间贮仓式制粉系统的直流炉组成的单元制机组,负荷适应性较好,可以采用炉跟机的运行方式。
然而,随着电网结构的变化,迫使超临界机组也要参与调峰运行,实际运行中大多数机组要采用协调运行方式,只是前一种方式以调压为主,同时兼顾到负荷;后一种方式以调负荷为主,适当兼顾到压力变化。
超临界机组的压力运行方式有三种:
一种是定压运行;一种是变压运行;还有一种是定压变压混合运行。
采用何种压力运行方式,与锅炉结构设计及水动力特性有关系。
直流锅炉当热负荷一定时,由于蒸发管中蒸汽和水的比容有差别,会出现水动力不稳定的问题,即流量具有多值性,影响锅炉受热面的安全,一般说压力越高,水动力特性越稳定,但是由于超临界压力锅炉在压力超过22.115MPa,温度超过374.15℃的相变点附近,存在一个“大比热区”。
在“大比热区”内水的物理性质急剧变化,导热系数、动力粘度急剧下降,焓和比容则急剧上升也同样会对水动力特性带来二种影响。
一种是管内工质平均温度尚低于临界温度,而壁面的工质已超过临界温度,发生壁温剧升现象;另一种是分配联箱进入水冷壁的入口段(L≤2m处),发生壁温剧升现象。
原因是经过大比热区后,流体平均温度与管壁温度差距逐渐增大,物性的剧烈变化导致光管壁面被一层密度比平均密度低很多的流体层覆盖,形成传热状况很差的薄膜,使传热恶化,壁温飞升。
当热负荷与质量流速之比小于0.42时,传热出现相对强化现象,在此范围内运行是安全的。
因此超临界机组的运行方式决定于直流锅炉是否能得到稳定的水动力特性,在这方面汽机是处于从属地位的,对于采用螺旋管圈式水冷壁的直流锅炉,其炉膛下部螺旋管出口工质温度在各种负荷下部相当均匀,适合采用变压运行方式;而对于采用垂直上升管屏水冷壁的直流锅炉,由于存在中间混合联箱,在压力变化时,容易出现各个管子流量分配不均,尤其是在低负荷工况变压运行时,这种现象更为明显。
另一方面,变压运行工质要经过亚临界区,工质比容变化很大,也导致流量分配不均,使工质流量减少,重量流速降低,这些不利因素,可能导致受热较强的水冷壁管中流量反而减少,导致传热恶化,宜采用定压运行方式。
华能营口电厂一期工程ПП-1000-24-545KT型直流锅炉,采用了FW型垂直上升管屏的水冷壁布置形式。
在炉膛负荷较高的下辐射区采用了三次垂直上升,和较高的质量流速。
在炉膛热负荷较低的上辐射区,采用了二次垂直上升,并适当降低了质量流速。
制粉系统采用了直吹式制粉系统,因而,为了保证锅炉具有稳定的水动力工况,采用定压运行方式是本机组最合理的运行方式。
3.2华能营口电厂两台引进320MW超临界机组运行方式的优化
营口电厂引进的原苏联320MW机组配有30%容量的单旁路启动系统,采用滑参数压力法启动。
为满足机组启动、停机和甩负荷等各种工况机炉配合要求,采用标准化的启动系统,这种启动系统在原苏联300MW、500MW、800MW及1200MW等各种型号的超临界机组上都是一致的。
优点是使启动过程的燃料消耗和电力消耗最少,启动持续时间最短;能维持单元机组正常的水质工况,而凝结水损失最小;启动程序通用化,简化操作;机组发生甩负荷时,能保证单元机组稳定运行。
启动系统除热力系统汽水通道的主要部件外,还由水冷壁出口顶出阀(ВЗ)内置式分离器(BC)分进阀(др-1)分出阀(др-3)分排阀(др-2)及点火扩容器(P-20)等组成,如图5所示。
机组启动开始时,顶出阀是关闭的。
锅炉上水至顶出阀前,锅炉满水后,用др-1保持顶出前为启动压力25MPa,并通过др-1、分离器BC、др-2、P-20点火扩容器等管线,建立启动流量约270-300t/h;锅炉点火后,分离器内达到一定压力和汽水混合物达到一定干度后,打开др-3,接通过热器,投入大旁路系统,主蒸汽管暖管,直至温度达到启动要求的温度值。
分离器出来的汽水混合物经др-2排放点火扩容器,为了余热利用,当顶出阀前温度260-270℃时,P-20向除氧器供汽,并网后当顶出阀前汽温达410℃时,关闭др-2,转为直流运行。
当机组180MW负荷时,启动部件流通能力达极限值及蒸汽压力接近于额定值23.5MPa后,打开顶出阀ВЗ,锅炉转为纯直流运行。
机组甩负荷时,大旁路也开启,且有30%的通流能力,可以维持空转或带厂用电运行。
为了解决再热器系统的加热及其无汽工况下工作的问题,在系统中装有再热汽排放装置(小旁路),冷温态启动中联门关闭时,打开此排放装置。
机组停机时,关闭顶出阀ВЗ及分出阀др-3,开启再热器排放装置,排净余汽避免其中存积凝结水。
营口电厂超临界机组启动状态规定,锅炉以过热系统联箱金属温度划分,温度小于80℃为冷态启动,大于等于80℃为热态启动;汽轮机则以高压缸外缸金属温度划分,当此温度小于等于150℃时,为冷态启动;大于150℃小于340℃时为温态启动,大于等于340℃时为热态启动。
因为外缸金属温度决定于夹层蒸汽的温度(对高压缸而言为七级后的温度),因此,不能精确地反映内缸最热部的真实温度,只能以此为参考点,按比例估算内缸的温度水平。
K-320-23.5-4型汽轮机,采用滑参数压力法启动,按厂家设计启动图表,在冷温态启动时,采用高压缸冲转,而中联门在冲转前用其全程试验油门强制关闭。
高压缸冲动后,锅炉再热器通汽,开启再热汽排放装置,在1000rpm,进行再热系统暖管,当暖管结束,再热蒸汽与中缸进汽部分金属温度相匹配时,再开启中联门,中缸进汽。
选择冲动参数时,除考虑调节级后蒸汽温度与金属温度相匹配外,还要考虑主蒸汽对主汽门、调速汽和导汽管的加热和各部件散热损失,调速汽门的节流温降以及蒸汽在调节级膨胀做功等因素。
因此本机组冷态启动冲动温度为270℃-280℃,压力为1.5-1.8MPa,压力的选择不但要考虑蒸汽过热度的需要,还要考虑在临界转速区快速通过的需要。
温态启动时,冲动蒸汽温度选择是高于高压缸进汽部分金属温度110℃,中缸进汽时再热温度比中缸进汽部分金属温度高90℃,热态启动时按规定是高中缸同时进汽,主再热汽温度为500℃以上。
另外,在冷温态启动时,要投入法兰、螺栓加热系统。
温态启动时,由于机组各部件冷却不均匀,使启动过程变得困难。
尤其是对超临界机组,高压缸很笨重,冷却较慢,而高压转子可能有很大的相对缩短,因此,胀差为“0”甚至为负值,对汽轮机而言是很危险。
,因为汽轮机通流部分的缸出汽侧间隙远远大于进汽侧间隙,这就使得温热态启动过程变得很困难和复杂。
如果冲动参数偏低,将可能造成更大的负胀差,汽轮机带来相当大危险,甚至造成动静磨擦。
原设计启动曲线如下表所示:
启动
状态
冲动参数
升速率
暖机
转速
暖机
时间
中缸进汽条件
启动
时间
冷态
压力1.5-1.8MPa
主汽温度270-280℃
180
r/min
1000
30
中缸金属温100-120℃
再热汽温250-270℃
5
温态1
t=200℃
高缸金属温度+110℃
主汽门金属温度与高缸进汽温度Δt<50℃
180
r/min
1000
20
中缸金属温度+90℃
中联门金属温度与中缸进汽温度Δt<50℃
2.5
温态2
t=290-
300℃
高缸金属温度+110℃
主汽门金属温度与高缸进汽温度Δt<50℃
180
r/min
1000
10
中缸金属温度+90℃
中联门金属温度与中缸进汽温度Δt<50℃
2.5
热态
压力5-7MPa
温度大于500℃
180
r/min
再热汽温大于500℃
1
从上表可以看出,各种状态下升速率均为180r/min,电调中没有考虑临界转速时升速率的问题,通过临界转速区段时需人为快速通过,除热态启动外,冷温态只选了一个暖机转速为1000rpm,暖机时间为10-30分钟。
机组投产后,由于在暖机转速附近有发电机转子的一阶临界转速,根据兄弟厂经验,将暖机转速改为1300rpm。
投产初期机组启动过程中,发现实际启动过程远远达不到上述图表要求,最大的问题是由高压缸冲动至1300rpm暖机的时间,由于再热汽温迟迟达不到要求,往往需要较长的暖机时间,有时甚至长达2-3小时才能勉强使中压缸进汽,分析原因是由于①采用单旁路启动系统,锅炉再热器一般布置在烟温较低的区域;②再热系统容积庞大,管径粗,而机组维持1300rpm的容积流量较小,所以对再热系统加热缓慢。
因此,在机组投产后的很长一段时间内,中压缸进汽参数很难得到保证,有时甚至在再热汽温略低于中缸进汽温度的情况下强行向中压缸进汽,造成很大的胀差负值,尤其是温态启动时更是如此,严重影响了机组的安全,损害了机组部件的使用寿命,同时,增大了启动消耗。
真对这种情况,我们进行了认真的分析,采取了各种可行的措施,如控制小旁路开度等措施,后来经过认真的研究和分析,决定各种状态下启机都增加一个2400rpm高速暖机转速,中压缸延迟进汽。
即机组启动,高压缸冲动至1300rpm,进行中速暖机,目的是为通过临界转速区1350-1850rpm做准备,中速暖机结束后继续用高压缸升至2400rpm进行高速暖机,实践证明由于高速成暖机时,工作蒸汽容积流量较之1300rpm大大增加,对加热再热系统是相当有效的,一般在2400rpm暖机15分钟内再热汽温即可满足中缸进汽条件,这样一方面加快了启动速度,缩短启动时间,降低了启动消耗,另一方面,使用合格的蒸汽进入中压缸对控制中压负胀有利。
鉴于此我们在二〇〇二年及二〇〇三年度两台机DEH系统改造中,升速程序部分采用了新的启动图表,如下表所示:
金属温度℃
升速率r/min
暖机时间min
1300r/min
2400r/min
冷态
≤150
150
45
15
温态1
150-300
200
35
15
温态2
300-340
250
25
15
热态
≥340
300
5
过临界转速区升速率为600r/min
由上表可以看出,升速过程中,在1300r/min和2400r/min处设暖机点,两次暖机时间加一起最长时间为1小时,可使本超临界机组得到最优化,最经济和最安全的启动方式。
营口电厂K-320-23.5-4型汽轮机,原设计采用电液并存的调节系统,以电调为主,液调做为备用。
电液调节系统可保证冲转、升速、并网正常运行工况下,对汽轮机进行控制及甩负荷,电网事故等,应该指出配套的电调系统功能齐全,算法周密,控制精度是很好的,但由于备品配件采购困难,软件开发困难,因此,在两台机组DCS改造中,对电调系统也进行改造,保留了部分原有控制功能,增加一些新的功能。
营口电厂的320MW超临界机组正常运行中,锅炉部分从水冷壁出口顶出阀前为定压运行,实际上从锅炉点火前就已经建立了启动压力。
并网后,在25-180MW负荷区段,汽机为滑压运行阶段,锅炉顶出阀前压力由др-1阀调节保持定压,此压力随负荷增加略有增大。
180MW负荷汽机开始升压至额定压力23.5MPa,并投入压力-1工况,锅炉开启顶出阀ВЗ,转为纯直流运行,因此在180-320MW其间本机组为定压运行,也可以采用以定压为主的协调工况。
可见,本机组由于锅炉水冷壁形式的限制,正常负荷区段基本是定压运行,这样,在负荷变化过程中,不可避免地对汽轮机各部金属温度形成较大热应力,影响汽轮机使用寿命。
在协调运行条件下,为了防止汽轮机压力有较大的变动,DEH系统设有压力-2工况,当主汽压力下降到22.5MPa时自动进入压力-2工况,在压力-2工况,进行单向调节,调低不调高,当主汽压力大于23.9MPa时,自动切到保压-1工况运行。
这样在一定程度上避免了,由于采用中速磨直吹式制粉系统所带来的负荷适应性差的问题,既参与了系统调峰,又在锅炉故障情况下,保证了机组的安全稳定运行。
营口电厂两台机组的停机方式,按停机目的不同主要有三种方式:
①额定参数停机,停机热备用时采用;②滑参数停机:
停机进行大修时采用,可以缩短总的检修周期;③事故停机。
对于滑参数停机,虽然可以使高中压缸温度降至很低水平,但是由于其滑停时间较长,达10小时左右,使停机耗油增加,为此我们经过认真研究,提出了在不投油的情况下,进行半滑参数停机方式,获得了较好的效果。
具体步骤是①机组转为节流直流工况,汽机由保压-1工况改为阀位工况,滑压运行,为主、再热汽滑温创造条件;②汽机投法兰螺栓加热装置,使缸体在滑温过程中均匀冷却,防止胀差负值过大;③汽泵维持3800rpm左右运行,给水流量500t/h左右;④滑停目标:
负荷13.5MW,锅炉维持550t/h蒸发量的热负荷,调速汽门全开,主汽压10MPa,主汽温400℃;⑤150MW负荷以下时,可将高低加疏水倒凝汽器,停止低加疏水泵运行。
我们认为此种方法,更适合于现场实际,既显著地降低了启动消耗,又使高、中压缸金属温度得到一定程度的降低。
用这种方法停机,我们认为是比较合理的,停机后还可用带电加热的风机将热空气打入汽缸及法兰螺栓系统,进行深度的冷却,但在使用中要控制好空气量,并严格监视各部温差,防止对汽机造成影响。
4超临界机组汽水品质控制和停机保养技术
现代大容量超临界机组,都配备直流锅炉,而直流锅炉不象汽包炉那样可以进行定期排污,锅内水处理等,如果汽水品质不好,将直接影响锅炉受热面及汽轮机通流部分的安全运行,因此直流锅炉对汽水品质指标要求十分严格。
我们知道如果汽水品质不合格,将给热力系统内设备带来腐蚀、结垢和积盐等严重后果,影响受热面管子的使用寿命,影响传热,增大了受热面管子和汽轮通流部分的流通阻力,监视段压力上升,使整个机组运行经济性大大降低,甚至造成推力瓦烧损,断叶片等严重的设备损坏事故,因此在机组启动及正常运行中,要严格控制热力系统的汽水品质指标。
华能营口电厂引进的原苏联的300MW超临界机组,采用TПП-315型直流锅炉,凝汽器循环冷却水为海水,因此,在凝结水系统设计了凝结水精处理装置,正常运行中对凝结水进行100%的处理,以保证合格的汽水品质,同时在热力系统设计上充分考虑了系统分段冲洗的功能。
分段冲洗一般在机组安装后及大修后启动时使用,因为此时系统及设备脏污、锈蚀情况比较严重,为了保证汽水指标合格需要进行分段冲洗。
分段冲洗系统如图6所示。
①凝汽器冲洗:
关闭凝结水系统截门,用化学除盐水向凝汽器补水,然后启动I级凝结水泵,将凝汽器脏物冲至循环水沟,具体流程是:
除盐水→凝汽器→I级凝泵→循环水沟。
②低加系统冲洗;关闭凝结水截门,开启除盐装置旁路门,关闭低加出口组出口截门,开启出口截门前至污凝水箱放水门。
用除盐水向凝结水管路补水至#1低加,水位正常后,启动Ⅱ级凝泵,通过低加组至污凝水箱。
具体流程是:
除盐水