LED产品可靠性及色差控制.docx
《LED产品可靠性及色差控制.docx》由会员分享,可在线阅读,更多相关《LED产品可靠性及色差控制.docx(14页珍藏版)》请在冰豆网上搜索。
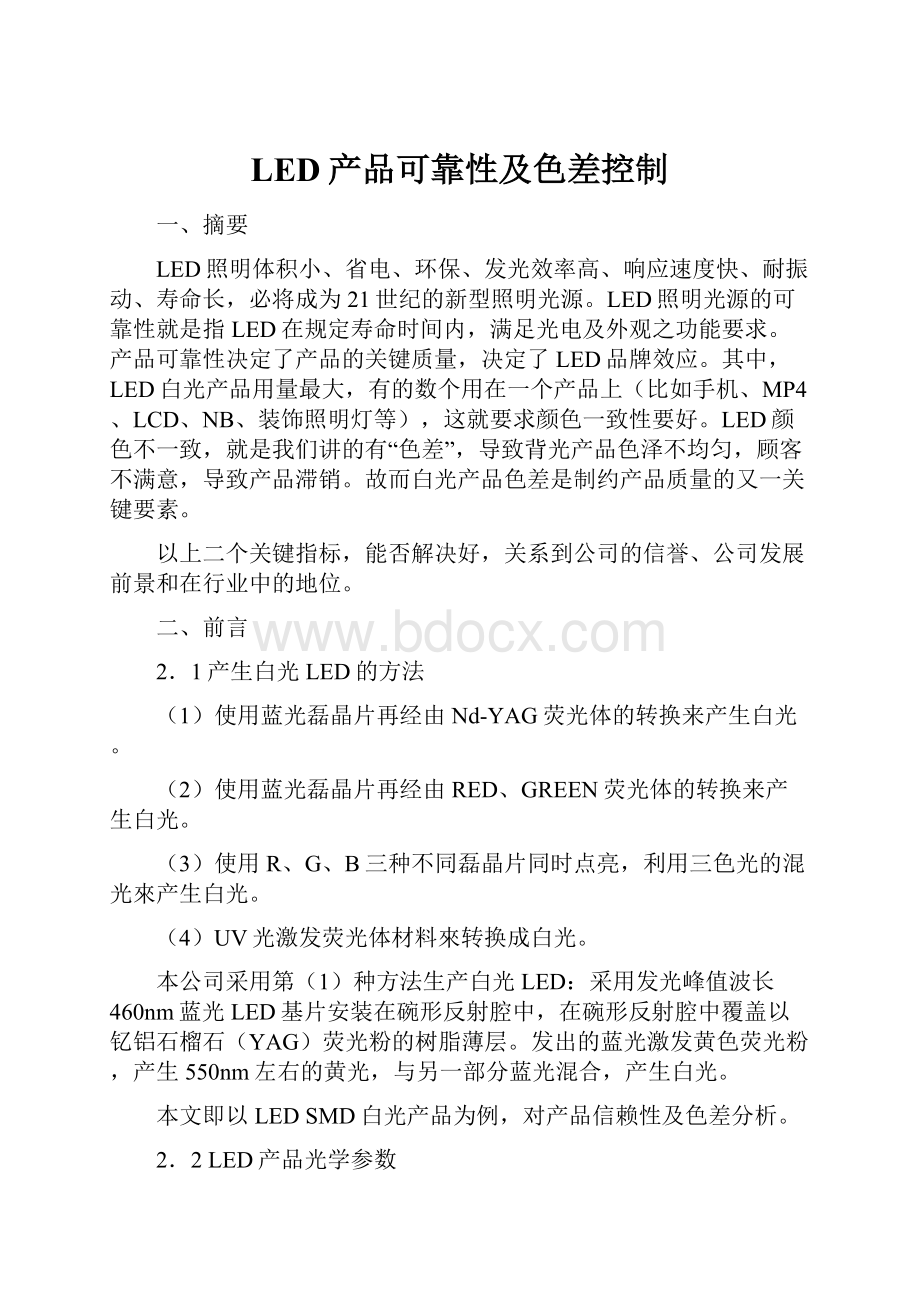
LED产品可靠性及色差控制
一、摘要
LED照明体积小、省电、环保、发光效率高、响应速度快、耐振动、寿命长,必将成为21世纪的新型照明光源。
LED照明光源的可靠性就是指LED在规定寿命时间内,满足光电及外观之功能要求。
产品可靠性决定了产品的关键质量,决定了LED品牌效应。
其中,LED白光产品用量最大,有的数个用在一个产品上(比如手机、MP4、LCD、NB、装饰照明灯等),这就要求颜色一致性要好。
LED颜色不一致,就是我们讲的有“色差”,导致背光产品色泽不均匀,顾客不满意,导致产品滞销。
故而白光产品色差是制约产品质量的又一关键要素。
以上二个关键指标,能否解决好,关系到公司的信誉、公司发展前景和在行业中的地位。
二、前言
2.1产生白光LED的方法
(1)使用蓝光磊晶片再经由Nd-YAG荧光体的转换来产生白光。
(2)使用蓝光磊晶片再经由RED、GREEN荧光体的转换来产生白光。
(3)使用R、G、B三种不同磊晶片同时点亮,利用三色光的混光來产生白光。
(4)UV光激发荧光体材料來转换成白光。
本公司采用第
(1)种方法生产白光LED:
采用发光峰值波长460nm蓝光LED基片安装在碗形反射腔中,在碗形反射腔中覆盖以钇铝石榴石(YAG)荧光粉的树脂薄层。
发出的蓝光激发黄色荧光粉,产生550nm左右的黄光,与另一部分蓝光混合,产生白光。
本文即以LEDSMD白光产品为例,对产品信赖性及色差分析。
2.2LED产品光学参数
LED的光学参数中重要的光学参数是:
发光强度、光通量、发光效率、光强分布、波长、色坐标。
(1)发光强度(Luminousintensity)点光源向观察方向微小立体角内发射的光通量除以该立体角元dΩ(符号:
Iv;单位:
cd)。
(2)光通量(Luminousflux)发光强度为Iv的光源在立体角元dΩ内的光通量为dφ=Iv·dΩ(符号:
φv;单位:
lm)。
(3)发光效率(Luminousefficiency)光通量与电功率之比。
发光效率表征了光源的节能特性,这是衡量现代光源性能的一个重要指标。
(符号:
η;单位lm/w)。
lm/w数值越高表示光源效率越佳,一般钨丝灯泡的发光效率在6~25lm/w之间,日光灯的发光效率在45~95lm/w之间。
目前LED的发光效率超过100lm/w.
(4)光强分布(Radiantdistribution)是指LED的指向特性,可以显示任意角度的光强值(光强的平面和空间分布)。
(5)波长(Wavelength)分为主波长和峰值波长二种。
峰值波长(peakwavelength)是指发光强度最大时对应的波长;主波长(dominantwavelength)定义为:
一般情况下,在得到待测件的色度坐标(x,y)后,将其标示于CIE1931色度坐标图上,连结E光源色度点(色度坐标x,y)=(0.333,0.333))与该点并延伸该连结线,此延长线与光谱轨迹(马蹄形)相交的波长值即称之为该待测件的主波长。
(6)x,y坐标(x,ychromaticitycoordinate)常指在国际照明委员会规定的CIE1931色度坐标系统中的水平、垂直坐标。
如下图:
三、过程分析
3.1识别原材料对产品质量之影响
WHITELED贴片产品(比如215、335、3020、010等),均需要用到多种原材料,经数个工艺生产制造完成。
可见原材料是组成产品的重要因素,其质量好坏直接关系到最终产品的可靠性。
从第一个生产工艺到产品出货,需要用到支架(载体)、固晶胶(银胶或绝缘胶)、
晶粒(芯片)、荧光粉、胶水(硅胶或硅树脂)、载带。
任何一个原材料出现品质异常,均可导致产品质量问题,但影响的程度不同。
有的对产品可靠性影响较小,有的影响极大。
下面就探讨原材料的影响因素。
原材料
质量要求
质量异常引起的品质问题
支架
表面干净、电镀良好、结构精良、支架与塑料材质(PPA)结合紧密、材质纯净。
镀层剥落引脚不吃锡、晶粒(芯片)脱离、塑料断裂、色差。
固晶胶
银胶:
粘稠度合适、导电良好、剪切力强、CTE小、导热良好、可用时间长、吸水率低。
绝缘胶:
粘稠度合适、剪切力强、CTE小、导热良好、不发黄、可用时间长、吸水率低。
晶粒(芯片)脱离、压降升高、时亮时不亮。
晶粒(芯片)脱离、亮度衰减大。
晶粒(芯片)
切割整齐、焊点一致、亮度均匀、波长一致、光衰小。
静电易击穿、电性易损坏、亮度衰减大、色差。
荧光粉
颗粒一致、纯度高、吸水率小、发光效率高、受热光衰小。
色差大、激发效率低、受热光衰退。
胶水
粘稠度合适、与PPA结合力强、硬化后应力小、韧性高、不变色、吸水率低、易与荧光粉混合、常温下使用反应慢。
亮度低、易龟裂、亮度衰减大。
载带
尺寸合适、无变形、不易断、防静电
易断带、取料不易、抛料。
由以上分析可知:
支架、固晶胶、晶粒(芯片)、胶水等原材料对“产品可靠度”有重要影响,荧光粉、晶粒(芯片)、胶水对“色差”影响较大,由于支架结构不合理也可能产生“色差”问题。
3.2识别封装制程对产品质量之影响
支架型LEDSMD制造流程如下图所示:
原材料质量控制良好,并不代表出货的产品可靠性就好,还有一个关键环节,那就是制程控制,分析如下:
制造过程
关键质量要求(全工艺防静电)
异常引起的品质问题
固晶
胶量均匀适中、方向正确、位置准确、晶粒(芯片)平整。
焊线掉晶片、亮度衰减大
固晶胶烘烤
推力(剪切力)正常、支架不变色或变形。
焊线掉晶片、晶粒(芯片)或齐纳管电阻大、亮度衰减大
焊线
焊线位置准确牢固、无松晶、拉力正常、焊球剪切力正常
电性不良、时亮时不亮
配胶、点胶
无气泡、荧光胶均匀、点胶位置及胶量合适
坐标不符、色差、回流焊时龟裂
胶水长烤
胶水充分硬化、回流焊不龟裂
回流焊时龟裂、变色、亮度衰减大
冲料
无冲偏、无毛边、无断脚、无压伤
外观不良
分光
分光标准一致、分光数据分布一致
色差
包装
无侧翻、无缺料、无反包、方向一致
抛料、方向不一致、侧翻
四、可靠性分析
产品可靠性除与原材料质量有关系外,还与制造过程控制有关。
原材料的可靠性,必须使用适当的评估方法才能正确评估;而制程控制主要是控制其KPI过程。
从以上分析可知,支架、固晶胶、晶粒(芯片)、胶水等原材料对“产品可靠度”有重要影响。
4.1支架(载体)
支架中最重要的特性为:
导热性能(Thermal)、导电性能(Electrical)、机械性能(Mechanical)。
导热性能包含热阻(ThermalConductivity)和热膨胀系数(CoefficientofThermalExpansion简称CTE);导电性能包含导电阻值、镀层厚度等;机械性能包含材质耐温及挠曲强度、吸水率等。
由于LED在通电发光后,仅有20%左右的电能转换成光能,近80%的电能转换成热能,所以LED通电后,内部结温升高,即使结温在125℃以下,亮度或光通量也会随着温度的升高而降低;当结温超过200度时,将对LED将造成损害,此时LED亮度衰减很大。
特别是当外界环境温度较高时,因为散热不良,对LED寿命影响更大。
故而,在工作时,LED芯片散热好坏,直接影响到LED产品信赖性。
如何保持LED芯片工作温度较低以获得更高的可靠性和光输出就取决于支架及固晶胶的热传导性能。
常见材料的热导系数如下:
材料
热导系数(W/mk)
备注
Al2O3
14~30
陶瓷材质
AlN
150~230
CU
90~400
支架金属
AL
50~237
银胶
2~13
固晶胶
绝缘胶
0.3~1.7
空气
0.027
BT基板
0.35
PPA
0.65
材料的热胀冷缩是封装必须考虑的另一个重要问题。
LED芯片与封装材料之间的CTE不匹配,可能导致回流焊时LED芯片与封装材料(固晶胶、胶水等)开裂,进而导致发光衰减、产生色差或导热减弱。
常用材料的CTE如下:
材料
CTE(ppm/℃)
备注
铝
23
铜和铝的CTE与LED芯片材料的CTE相差大
铜
16.5
BT基板60℃~120℃
240℃~280℃
X,Y:
14~16;Z:
40~50
X,Y:
5;Z:
200~250
PPA
14.5
GaAs砷化镓
5.8
常见LED芯片材料
GaN氮化镓
5.5
GaP磷化镓
5.6
SiC碳化硅
3.7
AlN氮化铝
4.4
Sapphire蓝宝石
7.9
导电性能中,电镀质量和厚度直接影响打线的牢固程度,对产品信赖性也有影响(常发现第二焊点松焊等就与此有关系)。
机械性能中,材质的耐高温很关键,因为LEDSMD产品过回流焊最高时要到260℃,10s。
耐高温不良,亦致产品断裂。
所以支架载体信赖性项目中,考查热导系数及CTE,特别要做“亮度衰减”测试及“回流焊测试”。
4.2固晶胶
固晶胶一般使用银胶或绝缘胶。
使用银胶时,银胶作用是固定LED芯片并导电;使用绝缘胶时,绝缘胶的作用仅用于固定LED芯片。
但二者都有一个共同的特点:
散热。
由于胶量多少对散热有重要影响,特别是绝缘胶的厚度对散热影响更大。
对于绝缘胶而言,底部胶水厚度在45μm以下时,散热良好,厚度增加后,散热呈现明显变差趋势。
所以在固晶制程时,要保证固晶胶中不能有水汽和气泡(空气的热导系数仅为0.027w/mk),对胶量的控制必须准确、均匀。
这必要求了胶水的稠密度在室温下变化要小,使用时间要长(至少一天),这样方便控制点胶形状及点胶量。
固晶胶与支架(基板)的粘合力直接影响到散热好坏,粘合力大,散热快;粘合不紧密,散热差。
对LED亮度衰减影响较大。
所以信赖性试验时,需做“剪切力”测试。
比如,固晶烘烤后,抽测其“剪切力”并将未测的样品(可以同一片支架)放入高温高湿85℃85%RH24小时后抽测其“剪切力”,以验证固晶胶是否因吸潮而导致剪切力大幅下降到原平均值的70%以下。
经验表时,低于原平均值的70%,会导致产品信赖性不佳。
4.3晶粒(芯片)
LED产品的最重要的特性就是发光,LED芯片发光强度的衰减和电性能不稳定(比如欧姆接触阻抗高、防静电能力差、晶格错位等)、焊线不牢固,都会直接影响到LED产品的信赖性。
故而LED芯片称为LED产品的心脏。
所以在评估LED芯片时,信赖性项目必须要全面,以考查VF变化、IV变化、波长变化、反向漏电流变化、防静电能力等来评价其优劣性。
4.4胶水
高粘合、高纯度、耐湿气、高温稳定性、应力小、高折射率及高光透射比是对胶水的重要要求。
硅胶固化后成柔软的弹性体,能消除胶体热张冷缩的应力,但其折射率低,不适合用于亮度高的场合。
硅树脂其折射率高于1.50,具有高透光性98%(@405nm时)以上,所以目前行业中,贴片LED用的较多的是硅树脂。
但硅树脂的缺点是韧性不够,与LED芯片表面、LED金线等粘合力较差,较容易出现回流焊时晶粒表面或银胶周围“裂纹”。
所以在胶水信赖性试验时,须进行“断裂试验”,以验证胶水的粘合力及应力是否会导致LED胶体产生“裂纹”。
4.5KPI制程
笔者认为,固晶站工艺及点胶站工艺是LED制造过程中是最为关键的(焊线工艺也是关键制程)。
为什么这样说呢?
固晶胶、晶粒、支架是这个工艺中必须用到的关键原材料。
固晶胶的保存,至关重要。
比如银胶保存,需存储在0℃以下,一般存储在-20℃左右。
由于银胶中主要成分是银粉颗粒、环氧树脂、溶剂等。
放置一段时间后,银粉会沉淀,导致分层现象。
如果就用这种状态下的银胶直接固晶作业,将直接导致固晶胶量不均匀、烘烤后剪切力大小相差悬殊,粘合力大小不一,直接影响散热。
如果是垂直结构的晶粒,还会引起阻抗升高或回流焊后VF增大甚至银胶与支架分离。
这个问题不得不引起足够的重视。
所以,银胶在使用前搅拌均匀比不搅拌要好的多。
银胶烘烤工艺也是关键的。
一般情况下烘烤150℃2小时。
环氧树脂在烘烤过程中,必经反应收缩及冷却收缩,这二种收缩均会导致内应力增大,而支架或基板的CTE与银胶的CTE相差较大,因材料间位移,很有可能导致银胶与支架或基板脱层,从而直接影响产品信赖性,所以需要想办法降低冷脚收缩时造成的应力。
固晶胶量及厚度,对产品的散热有直接的影响。
所以对亮度衰减影响较大,也是直接关联到产品信赖性问题。
点胶站工艺除用到关键的原物料---胶水和荧光粉外,最主要的是胶水混胶后的温度、粘稠度、均匀性,同时控制点胶时间、点胶后静置的时间、烘烤条件。
其中,烘烤条件是需要多次试验优化、多次验证才能固化的。
五、产品可靠性评价方法
传统评价可靠性方法采用的方法是:
抽样检验、可靠性寿命试验、客户端收集产品的寿命数据。
抽样检验,就是从提交的一批元器件产品中抽取一定数目的元器件进行规定的项目测试检验;可靠性寿命试验,就是抽取一定的样品进行加速寿命试验,通过对试验结果进行数据处理,评价产品的可靠性等级水平;客户端收集产品的寿命数据就是从现场收集并积累使用寿命数据,评价相应产品的使用质量和可靠性。
由于抽样检验不能区分不同厂家或不同批次间必然存在的质量区别、当不良比例极低时,可靠性寿命试验所取样品数量对结论的影响极大、客户端收集产品的寿命数据有“滞后性”,所以传统评价方法虽然有些作用、但尚有些不足。
产品的可靠性是设计、制造出来的。
设计良好,生产成品率才会高;生产成品率高、产品才会具有较高的可靠性;工艺稳定并受控、工艺成品率高,产品的可靠性水平才能高;PPM(元器件平均质量水平)反映总体质量水平。
所以对设计和工艺的评价可以评价元器件产品的内在质量和可靠性。
所以,采用传统评价方法+对设计及工艺的评价,能够较好的评价元器件的可靠性。
LED产品可靠性寿命试验项目,类别不同,试验项目不同。
对于小功率TOPLED(或SIDEVIEWLED),一般取样50PCS,评价项目共8项如下:
回流焊试验:
260℃(max.)、10s,2次;
热冲击:
0℃(15s)~100℃(15s)、20个循环;
温度循环:
-40℃~25℃~100℃~25℃,100个循环;
高温贮存:
100℃,1000小时;
低温贮存:
-40℃,1000小时;
高温高湿:
85℃、85%RH,1000小时;
耐久性试验1:
25℃、35mA,500小时;
耐久性试验2:
85℃、8.5mA,1000小时;
通过并行试验,全部通过试验的产品,可靠性通过验证,可以批量生产。
以上评价方法,存在不足之处,当产品质量处于临界状态时,试验有可能通过,客户却不满意。
所以,
如果要更好更快的评价LEDSMD产品可靠性,可以采用“串联方法”,比如评价微芯片封装之“断裂试验”,可以高温贮存125℃24小时→高温高湿85℃、85%RH,96小时
→回流焊260℃(max.)、10s,3次,样品数量以100个为宜。
可靠性的设计和制造,指的是在产品开发阶段,就充分考虑产品的可靠性。
其涵盖产品设计评审、原材料选择及可靠性评审、工艺设计及参数评审、成品率分析及PPM评审。
产品设计时,依照简化、降额、冗余、耐温度等设计手段,并全面考量法律法规、环境、技术指标、产品性能、工艺参数、成本、开发周期,提高产品抗干扰能力,减少质量波动,缩短开发周期、降低成本。
产品的质量和可靠性才能从根本上得到保证,顾客才会满意,才能创造公司品牌价值。
六、色差分析
白光LED产品色差是指同一个LED不同部位颜色有差异,或者是同一等级的产品颜色有差异,这与人、机器、原材料、制造方法、测量、环境等多因素关联,参见下表。
因素
关联点
描述
影响分析
人
1、作业熟练程度;
2、作业员精神状态;
3、执行工艺文件力度;
4、发现“异常生产”之能力;
作业员工作时思想不集中、不熟练、工艺文件执行力不足,极易导致产品的质量水平不稳定。
同时当生产不正常时,能否及时发现并反馈,异常重要。
人,始终是最重要的因素,因为人是可以其它关联因素的。
机
1、机器设备;
2、工治具;
3、保养;
机器设备的准确度、精确度、解析度、稳定度是评估设备的四大指标;
当然工治具的质量对于设备运作效率和效果同样重要;
注重保养,全面生产维护,是保证设备正常运作的工具。
设备与设备间四大指标均有差异,、评估设备的性能,了解他们,才能制造出好产品。
公司自动化程度越高,其影响响越大。
料
1、晶片;
2、支架;
3、胶水;
4、荧光粉;
5、点胶头;
晶片的激发波长&荧光粉激发波长是对应的,只有当对应了,激发效率才会高;
荧光粉不能吸潮,否则极易导致色泽不均;
点胶头(针筒)质量对胶量控制极其重要;
胶水的稠密度对荧光粉混合搅拌能否均匀影响极大;
对于色差控制来说,原材料的选择重要性,不亚于人的影响。
法
1、固晶晶片位置;
2、固晶晶片平整度;
3、胶水与荧光粉混合均匀度;
4、点胶位置;
5、胶量多少;
6、荧光粉沉淀覆盖状况;
固晶位置及固晶平整度对色差影响存大;
胶水均匀性、胶量控制对色差影响较大;
荧光粉沉淀覆盖状态对色差及色温影响极大;
对于尺寸较大的腔体,点胶位置对色差影响也存在;
工艺控制,对于产品的质量至关重要。
在固晶工艺、点胶站工艺控制程度决定了对色差的控制好坏。
测
1、色度坐标分区方法;
2、参数设置;
同一色区在客户端使用时,不得有色差;
每台自动化设备之参数设备,须要优化然后固化,并给出微调范围(容差)。
参数设置正确否,直接影响产品质量和成品率。
环
1、温、湿度;
2、气压;
3、电压;
4、光;
5、震动、噪声;
环境不同,生产出来的产品质量会产生波动。
特别是温、湿度、电压、气压影响最大。
光、震动、噪声也会有些影响。
环境参数需要每日监控,控制在合理范围。
否则,会造成产品的质量波动。
七、提高产品可靠性和减少颜色差异
通过以上对产品可靠性分析及颜色差异(色差)分析,提出如下看法:
7.1:
提高产品可靠性
1、高可靠性产品是设计出来的
高可靠性的LED产品开发,在不同的阶段应用QFD(质量功能展开)、DFX(面向X的设计)、PD(参数设计)、TD(容差设计)、FMEA(不良模式与影响分析)等方法。
QFD是把顾客对产品的需求转化为产品的设计要求、零部件特性、工艺要求、生产要求的质量工程工具,用来指导产品的稳健设计和质量保证。
DFX就是面向产品全寿命周期的设计,如可靠性、寿命、维护、成本、工艺、检验、环境等。
PD的基本思想是通过选择系统中所有参数(原材料、设备参数)的最佳组合,使产品质量特性波动小、稳定性好。
TD是指根据各参数的波动对产品质量特性贡献和影响的大小,从成本考虑对影响大的参数给予较小的容差,对影响小的参数给予较大的容差。
FMEA,是一种找出影响产品质量和可靠性的各种潜在的质量问题和故障模式及其危害度和原因的工具,经采取设计和工艺的纠正措施,提高产品的质量和各种抗干扰能力。
采用这些适当的方法,还要严格依照开发流程及信赖性评估认证,才能设计出高可靠性的产品。
2、高可靠性产品是最佳工艺条件生产出来的
通过确定关键工艺节点→确定关键工艺参数→实验设计、优化参数→固化参数方法,关键工艺采用工艺能力评估,比如Cpk技术,找到产品制造时最佳工艺条件,并形成标准化文件,对相关人员培训,并切实执行,监督、检查执行情况,反馈问题,持续改善。
3、高可靠性产品是稳定工艺生产出来的
要生产出高质量、高可靠性的产品,不仅要要求产线有很高的工艺能力,而且要求连续运转的工艺过程必须一直处于统计受控状态。
关键工艺,须实行SPC管制。
比如固晶工艺之剪切力、焊线工艺之拉力等。
4、高可靠性产品是全面质量管理出来的
TQM全员品质管理,是提升产品质量的又一关键途径。
总经理、经理、主管、领班、员工个个关心质量,把工作做细,养成下一工序就是您的顾客,达成以顾客为中心的理念,才能持续制造出高质量、高可靠性的产品。
7.2:
减少色差异
1、原材料选择
选择支架要只选取一种对称的、固晶位置正中、壁反射光均匀、底部腔体适当、反射率好的;注重晶片&荧光粉激发波长的相应配套性,通过DOE试验可以找出取光效率最大化和色差最小化;胶水的稠密度及特性与荧光粉搅拌的均匀性(稠密度高,可以对A胶予以适当的预热);烘烤条件的合理性,注意胶水烘烤过程中的反应收缩及冷脚收缩所造成的应力是否导致龟裂;荧光粉的贮存保管,不让其吸潮结块(如果吸潮,则需要驱除潮气)。
另外需注意的一点是,以上原材料的批量供应能力和质量控制稳定性评估。
2、点胶工艺控制
点胶胶量最需要关注,因为点胶气压、橡胶圈密封性、胶水粘稠度变化、点胶头的位置、点胶头带胶均匀性、支架平整性、点胶参数调整均可引起胶量不一,导致色差变化。
其次是每台点胶机的一致性,也是要充分评估。
因为每台点胶机有差异,作业员需要监控每台点胶机的工作状态。
3、分光设备同质性
分光机的同质性和一致性,对产品的分光结果影响甚大。
一致性不好,就有可能这台分光机分出的是Q0,另一台分光机分出来的是Q。
如果当大批量交货时,很容易出现色差困扰。
可以采用使用标准件监测,加大监测频次,当异常出现时,及时报警和维修。
4、提高员工发现“品质异常”能力
员工是控制工艺参数和操作设备的使用人,也是检验半成品或成品的主角。
在制造过程中,员工要严格执行标准工艺条件,批量生产时,能及时发现异常,可以预防批量性错误,降低品质成本,提高产品制程能力、争取交货时间、维护公司信誉。