底吹炉总控工培训教材.docx
《底吹炉总控工培训教材.docx》由会员分享,可在线阅读,更多相关《底吹炉总控工培训教材.docx(26页珍藏版)》请在冰豆网上搜索。
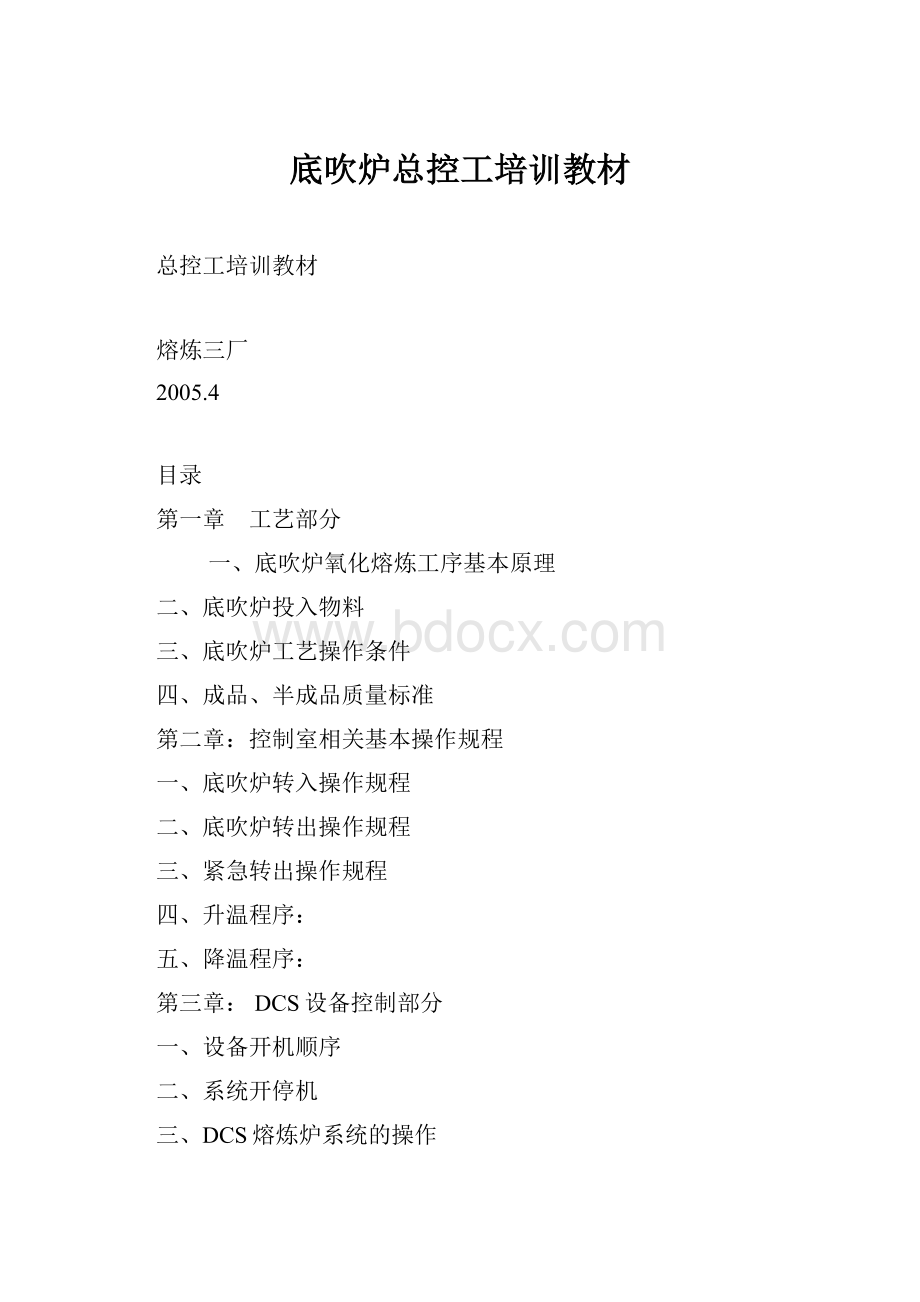
底吹炉总控工培训教材
总控工培训教材
熔炼三厂
2005.4
目录
第一章 工艺部分
一、底吹炉氧化熔炼工序基本原理
二、底吹炉投入物料
三、底吹炉工艺操作条件
四、成品、半成品质量标准
第二章:
控制室相关基本操作规程
一、底吹炉转入操作规程
二、底吹炉转出操作规程
三、紧急转出操作规程
四、升温程序:
五、降温程序:
第三章:
DCS设备控制部分
一、设备开机顺序
二、系统开停机
三、DCS熔炼炉系统的操作
四、DCS汽包部分的操作
五、控制室现场人员的操作
六、电脑故障处理
第四章:
工艺控制部分
一、渣含铅的调整
二、锅炉出口温度的控制
第五章:
事故处理
第一节:
控制室相关故障
第二节:
其它相关岗位故障回顾
第一章:
工艺部分
一、底吹炉氧化熔炼工序基本原理:
底吹炉氧化熔炼目的:
除去原料中的大部分硫,使硫化铅氧化成氧化铅,并产出符合鼓风炉还原熔炼要求的高铅渣块,同时产出含硫浓度较高的烟气,送制酸。
底吹炉氧化熔炼基本原理:
底吹炉氧化熔炼是熔池熔炼,经配料制粒的混合料从底吹炉顶部加入,氧气从底部吹入引起熔体搅拌,与混合料中的金属硫化物发生氧化反应,生成金属氧化物和二氧化硫,并释放出大量热使氧化反应继续下去,同时形成一次粗铅和高铅渣。
主要的反应方程如下:
氧化造渣反应:
2FeS+3O2+SiO2=2FeO·SiO2+2SO2
2ZnS+3O2=2ZnO+2SO2
2PbS+3O2+SiO2=2PbO·SiO2+2SO2
2PbS+3O2=2PbO+2SO2
2Pb+O2=2PbO
PbS+2O2=PbSO4(nPbO·PbSO4)
nCaO+SiO2=nCaO·SiO2
沉铅反应:
PbS+O2=Pb+SO2(综合式)
2PbS+O2=2PbO+2SO2
PbS+2PbO=3Pb+SO2
PbS+PbSO4=2Pb+2SO2
二、底吹炉投入物料:
化学成份%:
Pb50~60ZnO≤8.0FeO8-14SiO26-12CaO3-8Cu<0.5S<18As≤0.25Sb≤0.5-0.8H2O6~10
FeO/SiO2=1.2~1.7CaO/SiO2=0.4~0.8
物理规格:
粒度6~15mm占80%以上,离地面1m高落地不散为宜
三、底吹炉工艺操作条件:
项目单位参数
氧料比Nm3/t90-120
处理量t/h>20
日产渣量 t/d >220
溶池温度℃950-1150
初渣含铅 %40-55
渣面高度 mm900-1250
渣坝高度 mm 1100
铅坝高度 mm580
铅层厚度 mm250
炉外壳温度 ℃ 250-350
主烧嘴燃油量kg/h300
烟气量m3/h13000
烟气温度℃950-1150
氧气量(单支) Nm3/h<900
氮气量(单支)Nm3/h<200
氮气压力Mpa1.0-1.2
冷却水量t/h20-25
四、成品、半成品质量标准:
1、粗铅质量标准
Pb≥96%表面平整、无飞边毛刺,浮渣冰铜厚度<10mm、不夹杂杂物。
2、高铅渣质量标准
1)含pb40-55%S<1%Zn<8%FeO/SiO21.2-1.7CaO/SiO20.4-0.8
2)粒度80mm左右
3、烟气质量标准
1)烟气温度:
电收尘进口<400℃
2)烟气含尘量:
电除尘出口<500mg/m3
4、烟灰质量标准
1)Pb≥45%
第二章:
控制室相关基本操作规程
一、底吹炉转入操作规程
1、转入前如果升温,参照升温程序;锅炉出口温度达到250℃方可转炉。
2、控制室提前半小时通知氧气厂开一台氮压机、两台氧压机将N2、O2压力升起,保证底吹炉用气。
3、提前5分钟通知各单位、各岗,并通知在警报响的同时风机岗位启高温风机,风门全开,电收尘启四个电场,机修工关排空阀。
4、手动N/O切换,现场将氧气、氮气阀门全开,控制室将氧气、氮气压力提升,使氮气支管压力高于0.8Mpa,氧气支管压力高于0.7Mpa,并达到稳定。
5、铅口岗位抬高铅坝,渣口岗位人员取下燃烧器,各岗位检查有无转炉障碍。
6、控制室发警报,炉前操作转炉。
转炉中各岗位人员要迅速巡检金属软管有无挂在其它物体上,氧枪底座是否漏铅,铅口有无冒渣现象。
7、当炉体转入正位后,若没有其它异常情况,转炉操作工方可进行其他作业,中控通知下料。
铅口岗位人员要清理铅口,并尽把渣扒出来露出铅层。
下料口岗位将主副烟道闸板放下,副烟道插板阀关死,中控通知余热锅炉人员将副烟道顶部盖板放下。
8、转入后,通知启一、二电场,电收尘出口温度200℃以上时,启3、4电场,如果转炉前温度符合要求,可直接启电场。
9、及时联系硫酸拉风并根据负压情况调整高温风机转速、风门,保证短时间内使负压达到要求,减少SO2烟气泄漏。
10、中控结合余热锅炉人员保证汽包压力、水位在正常范围,并适时调整对外供汽、汽包排空阀开度,及时调整给水及软水流量。
正常后并将N/O切换投入自动,各氧枪投入联锁。
11、根据各氧枪具体情况调整各参数,使单支枪O2流量尽量低于900Nm3/h,N2压力高于氧气压力(>1.0MP)。
二、底吹炉转出操作规程
1、提前通知炉前蓄铅放渣,如果渣线放不下,可适当降料,渣线必须<1米,越低越好,直到渣基本放不出为止;停止放铅,抬高铅坝。
(短时转炉可不蓄铅,检修提前2小时)
2、提前5分钟通知各单位、各岗。
3、通知炉前各岗人员依照转炉确认制,保证转炉无障碍。
4、中控发警报,现场转炉,各岗人员巡检炉体转动情况。
转出后,N/O切换打手动,启动N/O切换,现场将各氧气阀门调小,保持支管压力0.3Mpa左右,控制室手动将氮气总管压力下调,使各支管压力保持0.3Mpa左右。
5、炉转出后,现场人员通知停计量泵。
风机工停高温风机,风门全关,5分钟后停电场,高压风机可根据实际情况关停。
6、炉前将副烟道插板阀打开,主副烟道闸板放下,通知余热锅炉人员将副烟道顶部盖板打开。
(检修时出烟口用盖板盖住)
7、关闭对外供汽阀门,结合余热锅炉人员保证汽包水位在正常范围,调节给水及软水流量,汽包水位+100mm即可停给水泵,然后根据汽包水位间断补水;
8、炉前岗位清理铅井,并用柴禾焦炭保温,同时检查处理主燃烧口、下料口、氧油烧咀口、探料孔等。
9、降温参照降温程序。
三、紧急转出操作规程
1、平时生产勤检查,要求无任何转炉障碍,可随时转炉。
2、紧急转出操作与转炉程序的区别在于先紧急响警报转炉,后通知余热锅炉、电收尘、硫酸、氧气厂,其余相同。
四、升温程序:
1、余热锅炉清灰作业结束,在不影响其它设备检修的前提下,即可启主燃烧器一级火焰(使用前必须维护、试用正常;保证主燃烧器口畅通无阻、内壁无结块);
2、电收尘检修完毕启二级火焰(开二级火焰前必须用一级火焰把炉温升到800℃,以后时间以检修完毕时间算起)。
3、20分钟后余热锅炉出口闸板提1/3。
4、30分钟后架氧油烧嘴(相应通氧气),调节火焰,使火焰充满炉内(从下料口不能看到对面),杜绝冒黑烟(视升温速度而定,也可不架)。
5、45分钟后闸板全开;
6、一小时后高温风机风门开度30%;
7、80分钟后,风门全开;
8、100分钟后,风门全关,启高温风机;
9、2小时后,风门逐渐开至30%,全力升温1小时(电收尘进口250℃,炉内结壳烧开后方可转炉)。
以上操作,通过调节闸板、风门及开停高温风机使升温速度达到要求,保证升温效果。
时间控制主要根据循环水温变化速度必须控制在50℃/h以下,根据温升曲线具体调整每步动作时间。
原则上二级火焰启开3小时内具备转炉条件。
五、降温程序:
1、停高温风机、风门全关,排空阀阀门全开,膨胀节闸板放下;
2、10分钟后,高温风机风门开启20%;
3、20分钟后,高温风机风门开启50%;
4、30分钟后,高温风机风门风门全开。
5、1小时后,打开阴极振打门。
6、2小时后,打开电收尘人孔门。
7、3小时后,启高温风机,每10分钟风门开度提高10%(关闭3、4电场人孔门),及时擦拭95瓷,杜绝95瓷出现酸蚀绝缘降低现象。
8、6小时后,电收尘可进人检查清灰。
要求:
1、中控室和电收尘人员停炉前后做好记录,包括电场、变压器、95瓷的测试。
2、对应有相应操作记录一次;
3、严格按照降温要求进行操作,并做好协调指挥工作;
4、高温风机及其管道清灰可根据实际情况调整。
第三章:
DCS设备控制部分
一、设备开机顺序
烟灰输送系统→精矿输送系统→烟灰配料系统
二、系统开停机
1、转炉后的开车:
点击“准备开车”,通知各岗位人员将设备转换开关打到“自动”位,铃响60秒,点击“开车”,铃响10秒,间隔5秒后再响10秒,结束后,将系统开车打到“自动”位,点击“启程序子组”,各设备依次开启。
2、单台设备的开车:
将设备所在DCS系统中转换到“手动”位,现场打到“自动”位,由现场发信号,联系明确无误后点击“启”。
若设备带料,需首先启动后续设备。
3、停车:
若现场要求不带料停车,则点击“停程序子组”,各设备顺延停止。
停车要先停烟灰配料系统,后停精矿输送系统。
若现场要求带料停车,则点击“紧急停车”,本系统全停,由于烟灰配料系统和1#带联锁,所以停止精矿输送系统,烟灰配料系统也会全停。
若仅检修某台设备,由现场打至“0”位,DCS显示故障,上游设备全部停止。
现阶段我厂停车主要是现场停车,转炉时现场停止东西下料带和球料定量给料机,上游设备全停。
注意事项:
1、点击“启程序子组”后,注意信号反馈,待所有设备启动后,再切换到其它画面,若有某台设备显示红色故障不能启动,立即通知现场操作工检查,是否打在“自动”位,设备供电是否正常,处理完后点击“故障复位”,程序继续进行。
2、现在由现场控制的设备有东西料带,东西定量给料机,4#带。
若有一边的下料带、给料机停止,对上游设备无影响,若两边同时停,则上游全线停车。
3、烟灰定量给料机由原料控制室控制,若烟灰配料系统其它设备故障停车,烟灰定量给料机不能自动停止,需立即通知原料控制室或现场操作工及时停止。
4、8组螺旋输送机由现场控制未参与联锁。
5、四组气动振打由现场控制,四组机械振打自动控制,但气动振打仍参与记时,机械振打除自动振打外,可另外在DCS上手动启动加强振打。
三、DCS熔炼炉系统的操作
1、调节氧气量的操作:
将氧气流量阀打至“手动”,根据氧料比计算氧气量,输入到设定值中,调节压力阀或流量阀均可,一般维持流量阀开度50~60%之间,压力阀调节时应注意不得调节过快,流量阀对流量调节变化不快,将氧气流量调节至设定值左右,将流量调节阀打至“自动”位,不得在设定值和反馈值相差较大(20Nm3)时将流量阀打至“自动”位,否则会造成氧气流量上下波动,严重时会导致氧氮切换。
2、调节氮气量的操作:
氮气主要考虑压力值,一般维持支管压力在1.0~1.2Mpa之间,将氮气流量阀基本全开,在压力阀中输入设定压力,点动“田”“日”按钮,将压力调节至设定值,然后将压力投入自动。
若想达到稳定的流量,则将压力阀投入“手动”,将流量阀开度开至“50~70%”左右,调节压力阀使流量达到设定值左右将流量调节投入“自动”
3、转炉时的气体调节
A、转出:
待炉转至水平位置后将氮氧切换转为“手动”,点击“启动”,氮氧切换完成后,下调氮气总管压力阀,可使用键盘上▽键,以达到较快效果,观察支管压力,直至支管压力0.3Mpa,氧气总管和软水由现场调节;
B、转入:
提前通知氧气厂将氮、氧气总管压力设定到1.5Mpa,将氮气支管压力提高达到0.8Mpa左右,然后点击氮氧切换“停止”按钮,将氧气切换入氧气通道,通知现场全开氧氮各支管,调节氧气总管压力和流量调节阀,使支管压力达到0.6MPa,稳定后可开始转炉。
切换前先将氧气总管压力阀开度设定为60%,流量阀开度设定为50%,调节氧气过程要缓慢,使支管压力均匀变化。
四、DCS汽包部分的操作
1、调节汽包水位:
现场水位与DCS中水位有一定差距,水位越低,相差越大,勤和现场校对水位,维持现场水位-50~+50之间,DCS中一般在-10~+80之间,打开给水量副环调节,调节开度“田”“日”按钮,或直接输入开度值,调节给水量以达到合适水位。
注意事项:
直接输入开度不得比原值差值3%以上,以防给水泵出口压力变化较大,控制给水泵出口压力5.4Mpa以下,生产正常时给水量一般维持5T/h左右,若长时间给水量较大才能维持水位,则须通知司炉工查明原因。
2、调节汽包压力:
压力汽包压力调节阀,调节“田”“日”开度,观察汽包水位,调节过程一定要缓慢,以防出现假水位,维持汽包压力在3.7~4.0Mpa之间。
如果在DCS调整后压力仍得不到控制要求,则通知司炉工调节汽包对空排汽。
3、调节除氧器水位:
打开除氧器进水阀画面,调节时可直接输入开度值,一次输入与原值差值不得超过3%,或使用键盘“田”“日”键,点击一次开度变化0.1%,控制水位在230左右。
4、除氧器的温度调节:
除氧器设定温度102-104度,调节除氧器压力调节阀开度,此阀调节对其它参数影响不大,可较大范围调节,以尽快达到设定值,观察除氧器压力和温度的关系,此值有时会产生变化,将温度调整为104度,将此时压力值输入为设定值,投入“自动”。
若除氧器长时间温度较低,可适当开启对外供汽气动阀,或微关三楼对外供汽。
五、控制室现场人员的操作
1、转炉时现场人员的操作:
1)转入:
转入前现场人员应检查气体是否走在仪表管道,若走在旁通则改为仪表,将调节阀微开,缓慢关闭旁通,若流量表有较大震动,则立即打开旁通,重复上述操作,使流量显示缓慢上升,直至旁通完全关闭,转炉时由控制室内人员通知调气,调气时将氧气支管完全打开,然后通知控制室开始氧氮切换,转入到位后,通知循环泵操作工启计量泵,现场调节支管下部球阀,缓慢开启,使流量稳定在25L/h左右,若完全开启后没有流量,则检查支管其余阀门是否已全开,计量泵是否已启动。
2)转出:
炉转出后通知停计量泵,停止后关闭各氧枪软水支管下部球阀,待控制室氮氧切换后,迅速关闭各支管氧气调节阀,使其压力维持在0.3Mpa左右。
2、现场调节支管流量:
现场调节气量时调节各支管调节阀,动作一定要缓慢同时和控制室保持联系,避免调节过量,调节冷却水时要调节球阀,因调节截止阀难以稳定。
3、氮氧切换的操作
1)投入自动:
底吹炉转入运行正常后,观察所使用各枪的氧气,必须高于0.55Mpa,将所使用氧枪全部投入联锁,点击氧氮切换“自动”,按“确定”后氮氧切换投入自动。
2)投入手动:
在自动状态可将任一支枪联锁解除,使此枪不参与联锁,将所使用的氧枪全部解除联锁,不管是自动,还是手动状态都不会自动切换;若将氮氧切换投入“手动”,即使氧枪全部参与联锁,也不会自动切换。
手动切换时,点击“启动”,几秒后切换阀变为绿色(由红变成黄,再变成绿),切换完成,同时氧气总管两气动阀自动关闭。
如果把氮气切换成氧气时,点击“停止”,切断阀变为红色(由绿变成黄,再变成红),氧气总管调节阀自动打开。
3)自动切换后的恢复:
自动切换若需立即恢复,将切换阀投入“手动”,点击“故障复位”,确认后重新切换过来,此时需调节氧气总管或支管使支管压力均大于0.55Mpa,然后投入自动状态。
若自动切换后将炉转出,这些工作在转炉前完成,待炉转入平稳后再将切换阀投入“自动”。
4)当任意一支氧枪氧气压力低于0.55MPa时,氮氧切换阀会自动切换,此时应密切关注氧气总管压力变化情况,同时迅速查找原因,可分以下几种情况:
A、氧气厂停电,此时应立即转炉。
B、氧气厂到氧压机时暂时压力较低,若氧气压力缓慢回升,可重新进行氮氧切换正常生产;若氧气压力持续下降,应立即转炉。
C、人为操作失误引起氮氧切换,应立即重新切换。
六、电脑故障处理
1、在月初系统自动删除历史记录时,可能会出现几分钟的类死机状态,画面的切换迟钝,记录删除之后便会恢复正常。
2、装上键盘(直接将键盘插在原键盘引线接口),同时按下“备用”和“ESC”键,然后同时按下“CTRL”+“ALT”+“DEL”三键,选中其中多余的程序,点“结束任务”将其退出。
3、如果软启动不行,按下机箱上重启动按钮,强行启动,检查完错误后,输入登陆密码:
从机箱密码“”,主机密码“xxy”。
点“开始”→“程序”→“HollysysSmartpro”→“FacviewExplover”→“图形编码器”→“运行”,运行正常后将其他窗口关闭,并登陆,登陆密码为:
操作员:
opsops。
工程师:
ensdcl。
4、屏幕闪烁
多数情况为受对讲信号、电焊影响。
5、非正常退出
按照3后半部分操作进入程序。
6、键盘上P1-P9键不能切换:
1)同时按下“ESC”和和“备用键”;(可直接登录)
2)单击“登录”输入操作员密码;
3)如果打开过任务栏,单击画面任何一处,将焦点移至画面
7、可能导致死机的常见操作
1)短时间内多次点击“放大”或“缩小”按钮;
2)打开多个“查找”、“资源管理器”、“帮助”等借以打开任务栏的窗口;
3)运行windows内的其他程序。
第四章:
工艺控制部分
一、渣含铅的调整:
渣含铅一般控制在43%—47%之间,超出此范围较多或连续两次放渣渣含铅超标都应及时调整,影响渣含铅的因素如下:
影响因素数量变化渣铅变化对烟气温度的影响
氧料比升高升高降低
红渣升高升高降低
碎煤升高降低升高
烟灰升高升高降低
渣含铅除受以上因素影响外还应注意以下几点:
1、氧料比尽量不要低于95Nm3/T,以防炉内反应不完全,渣温较低,炉况恶化。
如果因调整渣铅却需要低于95Nm3/T时,应加强关注。
2、调整渣铅时应保证烟灰仓称重曲线持平,即所产烟灰与所用烟灰相差不大。
3、渣温控制范围在950—1150℃之间,但实际生产中应尽量保持在1000—1100℃之间,以确保炉内反应正常进行,同时又不会引起其他副作用。
4、调整渣铅时,每次调整量应控制在以下范围:
氧料比2个/次
红渣0.2—0.4T/h
烟灰0.2—0.4T/h
碎煤0.02—0.03T/h
以上方法中,调整氧料比时渣铅变化最快,也易于控制,其作用时间一般在20分钟以后;其他三种方法较慢,其作用时间一般在一小时以后。
5、增加1T/h烟灰相当于增加4个氧料比
增加1T/h红渣相当于增加5个氧料比
100Kg碎煤大约要消耗140m3氧气
二、锅炉出口温度的控制
锅炉出口温度一般控制在400—430℃之间。
影响因素主要有以下几种:
1、精矿含硫量含硫越高相应出口温度越高。
2、渣含铅渣含铅较低时出口温度相应偏高。
3、锅炉清灰影响开气动振打时,出口温度会上升,若入口温度较高则出口温度上升较快且不易降;用脉冲清灰器清灰时,出口温度会先升后降;开直升烟道振打会相应降低温度。
4、渣线较高或较低时出口温度会上升。
5、辅料配料量出口温度随碎煤增加而上升,随红渣、烟灰增加而下降。
第五章:
事故处理
第一节:
控制室相关故障
一、活动门水管泄漏处蒸汽高压喷出,水汽泄漏;给水15t/h才能勉强维持水位;
处理方法:
a、应立即汇报,首先补水,通知炉前紧急转炉。
b、观察水位,当控制室显示水位到-300之后要注意观察循环泵流量,一旦发现流量下降应立即停循环泵,锅炉自然降温。
二、锅炉汽包水位计玻璃裂泄漏
原因:
1、未及时冲洗水位计;2、水位计质量问题。
处理方法:
1、加大给水维持正常水位;
2、若人无法接近时,应立即汇报停炉处理。
三、软水供应不上
1、若钠离子交换器坏,无备用软水,长时间无法修复,应转炉处理。
2、若软水箱内无水,钠离子交换器故障,可先联系动力厂供应软水尽量维持汽包正常水位,若不能转炉处理。
四、锅炉爆破吹灰器头部掉入4#刮板故障
1、通知机修电工,将4#刮板停,东西检修口打开检查。
2、降低料量,维持锅炉正常作业,关注汽包水位压力。
3、现场将4#刮板内硬物清理干净,(若在短期无法处理应转炉处理)确认恢复后转入正常开。
五、电收尘压差500
观察电收尘锅炉压差是否上升较快,判断是否是仪表故障,同时通知锅炉人员清灰(电收尘入口),如未积灰也非仪表故障则通知振打检查电场,可能为电场积灰。
六、电脑显示汽包压力表故障
判断:
与停用的循环泵入口压力相比较相差0.2mpa为正常。
措施:
经常与现场较对水位压力,并养成习惯常与循环泵入口压力较对。
七、锅炉爆管泄漏
现象:
水汽泄漏(有声音)水位直线下降,烟灰温,给水量远远大于蒸汽量(正常供水量)难以维持正常水位。
处理:
大量补水尽量维持汽包水位,经常与现场校对水位,通知做好转炉准备,降料,立即组织放渣停炉,若不能维持正常水位,立即转炉,停止给水。
八、汽泡压力突升
升温期间使用主燃烧器曾经因油量过大而引起汽包压力爆升,给水流量7t仍无法维持正常水位。
措施:
控制室“供油系统”画面油压未点火时为0.3,着火后为0.23左右,压力过高容易熄灭,过低则油量会过大。
若不知原因,汽包压力突升,应先尽量补水,通知现场开排空泄压,尽量维持正常水位压力同时查明原因,若不能维持立即转炉。
九、风机
高压风机振动大,原因为压缩空气压力低于0.4mpa或电机电流过低。
处理:
通知空压机房(1991)赶快升压;查看电流,调整到合适值。
高温风机坏:
将风门全开联系硫酸加大拉风量保证锅炉出口负压(-50左右)。
十、停电
市电倒发电后立即通知开强制泵冷水泵、循环水泵。
后立即通知现场转炉,若发电送不上时,马上联系电工抓紧送电,若停电超过3分钟后应严禁启循环泵。
十一、铅口
(1)铅口铅流大
原因:
1、渣线高2、铅坝高(铅层厚)后放低或冲开3、转炉4、虹吸口刚烧开,吹虹吸口时。
处理:
看铅流及时换铅槽,堵铅口尽快放渣,若控制不住转炉处理,渣铅控制好。
(2)铅口出渣
原因:
1、铅层低,2、渣线过高,3、氧料比严重失调,4、压缩空气吹后a、渣线高时,b、渣铅高不易吹
处理:
及时调整渣铅,严格控制渣线保持适当铅层,出渣后铅井内渣处理干净,控制好放渣间隔时间。
十二、渣口
1、渣稀时抓紧调整炉况
渣稀的表现:
a、烟灰仓料位下降较快,b、烟气温度低(顶部、出口),c、烟灰发黄,
2、渣粘放不出来,流动性极差。
先降料或调整氧料比,若碎煤加多,烟气温度高时可降煤,渣粘住渣槽,渣线高或长时间没放出渣时,应降料量吹一边拉渣(用钢管)一边观察渣流情况,若渣线低时,先堵渣口以防粘渣充满渣槽,半小时后放渣看情况调整。
3、铸渣机头发现明铅多,
原因:
若虹吸口波动小,出铅少,可能虹吸口堵塞不通或铅层过厚。
氧料比严重失调造成渣铅不分。
使用4#枪位时也可能明铅较多。
处理:
1)用压缩空气疏通虹吸道,若长时间铅口出铅偏少,应转炉处理。
2)调整氧料比,渣铅稳定到45左右。
十三、下料口冒烟、喷渣
原因:
a、渣铅过低,b、负压小,c、渣线过高,d、两下料口间有炉结,e、配煤多,f、下料量突然大。
处理:
调整渣铅,保证负压,及时放渣降煤,若下料口间结有炉结,应停炉时烧掉。
十四、N/O切换
N/O自动切换的情况:
1、误击跟踪串级,使氧料比与原定料比相差大或断料致使切换。
2、调整流量时,未打倒手动位置且输错设定值。
3、现场阀门误操作或双击左键阀门开度为零