机械专业模具毕业设计.docx
《机械专业模具毕业设计.docx》由会员分享,可在线阅读,更多相关《机械专业模具毕业设计.docx(19页珍藏版)》请在冰豆网上搜索。
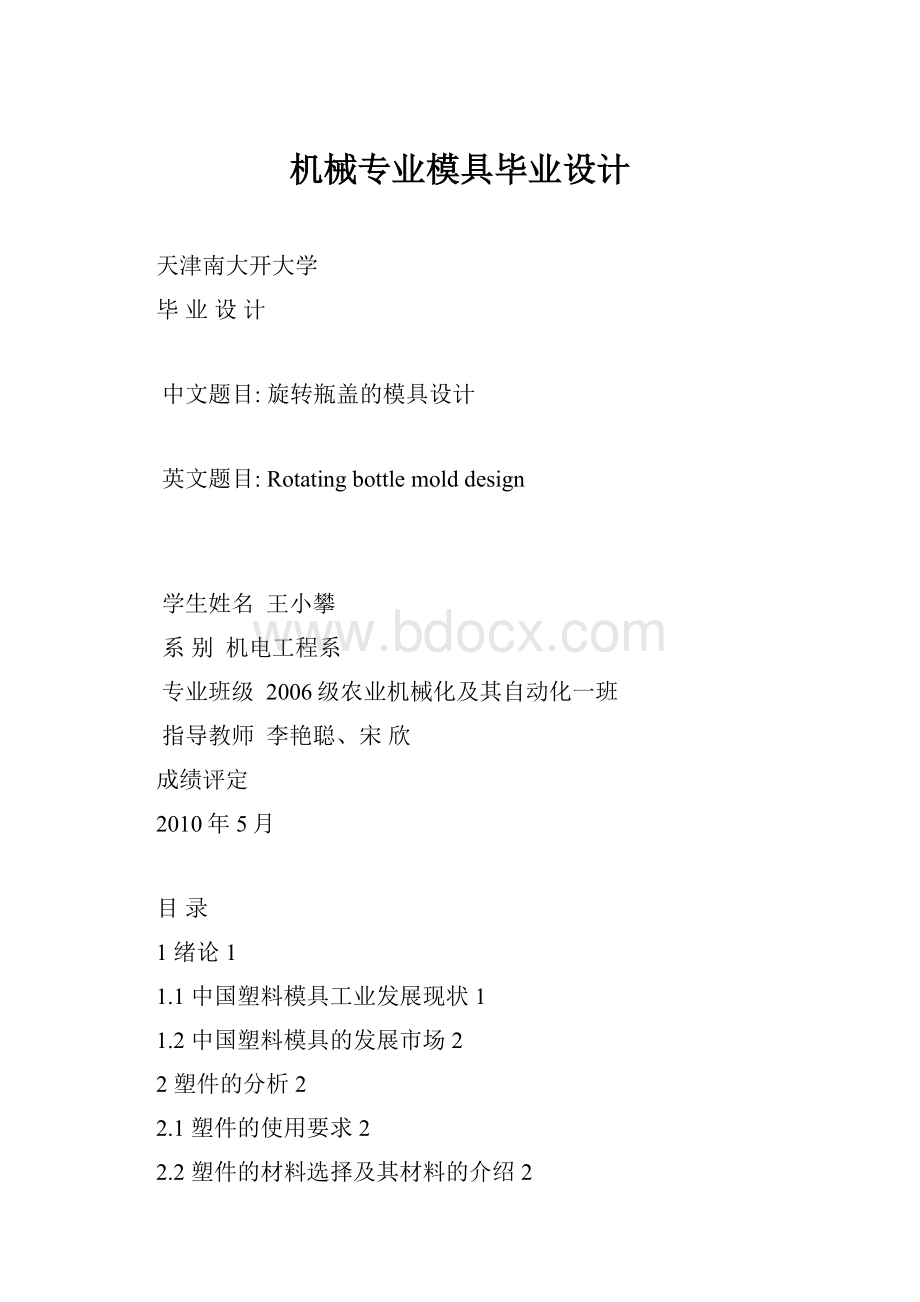
机械专业模具毕业设计
天津南大开大学
毕业设计
中文题目:
旋转瓶盖的模具设计
英文题目:
Rotatingbottlemolddesign
学生姓名王小攀
系别机电工程系
专业班级2006级农业机械化及其自动化一班
指导教师李艳聪、宋欣
成绩评定
2010年5月
目录
1绪论1
1.1中国塑料模具工业发展现状1
1.2中国塑料模具的发展市场2
2塑件的分析2
2.1塑件的使用要求2
2.2塑件的材料选择及其材料的介绍2
2.3塑件的形状及尺寸3
3行腔数目的决定及排布4
4注射机的初步选择5
4.1注射量的计算5
4.3XS-ZY-125型注射机的主要参数5
5浇注系统的设计5
5.1浇注系统设计原则5
5.2浇注系统的组成6
5.3浇注系统的设计6
6分型面与排气槽设计7
6.1分型面的选择原则7
6.2分型面的设计7
6.3排气槽的设计8
7成型零件的设计8
7.1成型零件的结构设计8
7.2成型零件工作尺寸的计算9
7.3成型零件的强度、刚度计算11
8导向机构的设计13
8.1导柱导向机构的作用13
8.2导柱导套的选择13
9推出机构的设计14
9.1推出机构的组成14
9.2推出机构设计的原则14
9.3推出机构的设计14
9.4复位零件14
10冷却系统设计15
10.1注射模冷却系统设计原则15
10.2冷却管尺寸15
11注射机的参数校核16
11.1塑件在分型面上的投影面积与锁模力校核16
11.2模具厚度校核17
11.3开模行程校核17
12总结17
摘要
塑料制品具有原料来源丰富,价格低廉,,性能优良等特点。
它在电脑、手机、汽车、电机、电器、仪器仪表、家电和通讯产品制造中具有不可替代的作用,应用极其广泛。
注射成形是成形热塑件的主要方法,因此应用范围很广。
注射成形是把塑料原料放入料筒中经过加热熔化,使之成为高黏度的流体,用柱塞或螺杆作为加压工具,使熔体通过喷嘴以较高压力注入模具的型腔中,经过冷却、凝固阶段,而后从模具中脱出,成为塑料制品。
本产品是日常应用的塑料瓶盖,且实用性强。
该产品设计为大批量生产,故设计的模具要有较高的注塑效率,浇注系统要能够自动脱模,此外为保证塑件表面质量采用侧浇口,因此选用单分型面注射模,侧浇口自动脱模结构。
模具的型腔选择一模四腔结构,浇注系统采用侧浇口成形,推出形式为推件板推出机构完成塑件的推出。
塑件的工艺性能要求注塑模中有冷却系统,因此在模具设计中也进行了设计。
本次的设计查阅了大量的专业资料和书籍,丰富了设计过程。
关键词:
注射成型,侧浇口,型芯
ABSTRACT
Heretoentertheneedtoturnoverasourceofplasticmaterials,lowprice,qualityandperformancecharacteristics.itisincomputersandmobilephones,carsandelectricalandelectronics,instruments,applianceandproductsmanufacturingisanalternativetotheroleofthemostwidelyused.aninjectionisathermoplastic-concreteshapeofthemainmethod,thescopeofapplicationisverylarge.
Beenshapingtheplasticmaterialsinrollsofthematerialbeingmouldofform,afteracoolingandsolidify,andthendiefromtheadjustment,asofplastic.
Theproductisofdailyuseofplasticbottle,andwithformassproduction,thedesignmoldstoautomaticallyrelease,inadditiontoensurethequalityofthesurfaceformsasidegateandthereforeusesinglecentfortheinjection,thesidegateautomaticallyreleasethestructureofthetype.themachinemoldisachoiceofamodulefourchambersstructure,thesystemusesthesidegatetopushoutofshape,formaboardwiththeagencytocompletetheformsofthelaunchoftheprocess.
Keywords:
injection;sidegate;acore.
1绪论
1.1中国塑料模具工业发展现状
从市场情况来看,塑料模具生产企业应重点发展那些技术含量高的大型、精密、复杂、长寿命模具,并大力开发国际市场,发展出口模具。
随着中国塑料工业,特别是工程塑料的高速发展,可以预见,中国塑料模具的发展速度仍将继续高于模具工业的整体发展速度,未来几年年增长率仍将保持20%左右的水平。
整体来看,中国塑料模具无论是在数量上,还是在质量、技术和能力等方面都有很大进步,但与国民经济发展的需求、世界先进水平相比,差距仍很大。
一些大型、精密、复杂、长寿命的中高档塑料模具每年仍需大量进口。
在总量供不应求的同时,一些低档塑料模具却供过于求,市场竞争激烈,还有一些技术含量不太高的中档塑料模...整体来看,中塑料模具无论在数量上,还是在质量、技术和能力等方面都有了很大进步,但与国民经济发展的需求、世界先进水平相比,差距仍很大。
一些大型、精密、复杂、寿命的中高档塑料模具每年仍需大量进口。
在总量供不应求的同时,一些低档塑料模具却供过于求,市场竞争激烈,还有一些技术含量不太高的中档塑料模具也有供过于求的趋势。
加入WTO,给塑料模具产业带来了巨大的挑战,同时带来更多的机会。
由于中国塑料模具以中低档产品为主,产品价格优势明显,有些甚至只有国外产品价格的15~13,加入WTO后,国外同类产品对国内冲击不大,而中国中低档模具的出口量则加大;在高精模具方面,加入WTO前本来就主要依靠进口,加入WTO后,不仅为高精尖产品的进口带来了更多的便利,同时还促使更多外资来中国建厂,带来国外先进的模具技术和管理经验,对培养中国的专业模具才起到了推动作用。
2006年,中国塑料模具总产值约300多亿元人民币,其中出口额约58亿元人民币。
根据海关统计资料,2006年中国共进口塑料模具约10亿美元,约合83亿元人民币。
由此可以得出,除自产自用外,市场销售方面,2006年中国塑料模具总需求约为313亿元人民币,国产模具总供给约为230亿元人民币,市场满足率为73.5%。
进口的塑料模具中,最多的是为汽车配套的各种装饰件模具、为家电配套的各种塑壳模具、为通信及办公设备配套的各种注塑模具、为建材配套的挤塑模具以及为电子工业配套的各种塑封模具等。
出口的塑料模具以中低档产品居多。
由于中国塑料模具价格较低,在国际市场中有较强的竞争力,所以进一步扩大出口的前景很好,近几年出口年均增长50%以上就是一个很好的证明。
虽然近几年模具出口增幅大于进口增幅,但所增加的绝对量仍是进口大于出口,致使模具外贸逆差逐年增大。
一状况在2006年已得到改善,逆差略有减少。
1.2中国塑料模具的发展市场
模具外贸逆差增大主要有两方面原因:
一是国民经济持续高速发展,特别是汽车产业的高速发展带来了对模具旺盛需求,有些高档模具国内的确生产不了,只好进口;但也确实有一些模具国内可以生产,也在进口。
这与中国现行的关税政策及项目审批制度有关。
二是对模具出口鼓励不够。
现在模具与其它机电产品一样,出口退税率只有13%,而未达17%。
从市场情况来看,塑料模具生产企业应重点发展那些技术含量高的大型、精密、复杂、长寿命模具,并大力开发国际市场,发展出口模具。
随着中国塑料工业,特别是工程塑料的高速发展,可以预见,中国塑料模具的发展速度仍将继续高于模具工业的整体发展速度,未来几年年增长率仍将保持20%左右的水平。
2塑件的分析
2.1塑件的使用要求
耐用,耐磨,可以承受较大的冲击力,不易摔坏;好看,有光泽,表面较光滑;化学性质稳定,可以耐高温(一般低于100oC),耐化学腐蚀。
2.2塑件的材料选择及其材料的介绍
2.2.1根据塑件的用途及其使用要求,选用ABS塑料。
2.2.2ABS的介绍
名称中文名:
丙烯腈-丁二烯-苯乙烯共聚物
英文名:
Acrylonitrile-Butadiene-Styrenecopolymer
基本特性
无毒无味,呈微黄色,成型的塑件有较好的光泽,密度在1.02~1.05gcm3,其收缩率为0.3~0.8%。
ABS吸湿性很强,成型前需要充分干燥,要求含水量小于0.3%。
流动性一般,溢料间隙约在0.04mm。
ABS有极好的抗冲击强度,且在低温下也不迅速下降。
有良好的机械强度和一定的耐磨性、耐寒性、耐油性、耐水性、化学稳定性和电气性能。
成型特点
ABS在升温时粘度增高,所以成型压力较高,塑料上的脱模斜度宜稍大;易产生熔接痕,模具设计时应注意尽量减小浇注系统对料流的阴力;在正常的成型条件下,壁厚、熔料温度及收缩率影响极小。
要求塑件精度高时,模具温度可控制在50~60oC,要求塑件光泽和耐热时,应控制在60~80。
主要技术指标
比容:
0.86~0.98cm3g。
熔点:
130~160oC
吸水性:
0.2~0.4%(24h)
热变形温度:
4.6×105Pa----90~108oC
18.0×105Pa----83~103oC
屈服强度:
50MPa
拉伸弹性模量:
1.8GPa
抗弯强度:
80MPa
ABS注射工艺参数
注射机类型:
螺杆式
螺杆转速(rmin):
30~60
喷嘴形式:
直通式
喷嘴温度(oC):
180~190
料筒温度(oC):
前200~210中210~230后180~200
模温(oC):
50~70
注射压力(MPa):
70~90
保压力(MPa):
50~70
注射时间(s):
3~5
保压时间(s):
15~30
冷却时间(s):
15~30
成型周期(s):
40~70
2.3塑件的形状及尺寸
塑件的工作条件对精度要求较低,根据ABS的性能可选择其塑件的精度等级为5级精度。
经计算得塑件的底面积为:
S塑=530.66mm2
得塑件的体积为:
V塑=2.49cm3
塑件的质量为:
W塑=V塑×r塑=2.62(g)。
见图2-1所示。
图2-1塑件图
3行腔数目的决定及排布
已知的体积V塑或质量W塑,又因为此产品属大批量生产的小型塑件,综合考虑生产率和生产成本等各种因素,初步确定采用一模四腔对称性排布。
排布图如2-2所示:
图2-2型腔数目及排布图
4注射机的初步选择
4.1注射量的计算
Q=4×2.62=10.48(g)
4.2注射机的初步选择
XS-ZY-125型注射机
4.3XS-ZY-125型注射机的主要参数
额定注射量(cm3):
125
螺杆直径(mm):
42
注射压力(MPa):
120
注射行程(mm):
115
注射时间(s):
1.5
注射方式:
螺杆式
合模力kn:
900
最大注射面积(cm2):
320
最大开(合)模行程(mm):
300
模具最大厚度(mm):
300
模具最小厚度(mm):
200
喷嘴圆弧半径(mm):
12
喷嘴孔径(mm):
4
5浇注系统的设计
浇注系统的设计是注射模设计的一个重要环节,它对注射成形周期和塑件质量(如外观,物理性能,尺寸精度等)都直接影响。
5.1浇注系统设计原则
●结合型腔布局考虑;
●热量及压力损失要小;
●确定均衡进料;
●塑料耗量要少;
●消除冷料;
●排气良好。
5.2浇注系统的组成
普通流道浇注系统一般由主流道,分流道,浇口和冷料穴等四部分组成。
5.3浇注系统的设计
5.3.1流道尺寸
根据该塑件体积,可得体积流率Q=(4×2.49)1.6≈6.55cm3s,取主流道中熔体流动rs=5×103s-1,由r-Q-Rn关系曲线图,可得Rn=4.50mm,故得主流道大端尺寸D=2Rn=9.mm,小端尺寸由注射机喷嘴尺寸,取d=4mm,SR=12+2=14mm。
如图5-1所示。
图5-1浇口套图
5.3.2分流道尺寸
为使四浇口能同时进料,各分流道按平衡式布置,故熔体在各分流道中的流速,为使分流道易于加工和顶出凝料系统容易,采用设在模具一边的梯形形分流道。
梯形大底边宽度:
B=0.2654×4.83×3.9=5
梯形高度:
H=0.67×B=3.35
为了塑件表面质量及其美观采用侧浇浇口,其尺寸d=0.15×6.7=1
5.3.3冷却穴
底部设计成带有球头形拉料杆的冷料穴,目的是捕集料流前锋的“冷料”,防止“冷料”进入型腔而影响塑件质量。
该模具浇注系统的尺寸如图5-2所示:
图5-2模具浇注系统图
6分型面与排气槽设计
分型面为定模与动模的分界面。
合理地选择分型面是使塑件能完好的成形的先决条件。
6.1分型面的选择原则
●使塑件在开模后留在有动模上;
●分型面的痕迹不影响塑件的外观;
●浇注系统,特别是浇口能合理的安排;
●使推杆痕迹不露在塑件外观表面上;
●使塑件易于脱模。
6.2分型面的设计
如图6-1所示:
图6-1分型面图
6.3排气槽的设计
当塑料熔体填充型腔时,必须顺序排出型腔及浇注系统内的空气及塑料受热或凝固产生的低分子挥发气体。
如果型腔内因各种原因而产生的气体不被排除干净,一方面将会在塑件上形成气泡、接缝、表面轮廓不清及充填缺料等成型缺陷,另一方面气体受压,体积缩小而产生高温会导致塑件局部碳化或烧焦(褐色斑纹),同时积存的气体还会产生反向压力而降低充模速度,因此设计型腔时必须考虑排气问题。
有时在注射成型过程中,为保证型腔充填量的均匀合适及增加塑料熔体汇合处的熔接强度,还需在塑料最后充填到的型腔部位开设溢流槽以容纳余料,也可容纳一定量的气体。
通常中小型模具的简单型腔,可利用推杆、活动型芯以及双支点的固定型芯端部与模板的配合间隙进行排气,其间隙为0.03~0.05mm。
7成型零件的设计
7.1成型零件的结构设计
凹模采用整体凹模
凸模由于塑件带有螺纹,为了简化模具的加工工艺,凸模设计成活动镶块的形式,活动镶块的固定方式如图7-1所示:
图7-1活动镶块的固定方式
7.2成型零件工作尺寸的计算
7.2.1成型零件尺寸产生偏差的原因
成型收缩引起制品产生尺寸偏差的原因有:
预定收缩率(设计算成型零部件工作尺寸所用的收缩率)与制品实际收缩率之间的误差;成型过程中,收缩率可能在其最大值和最小值之间发生的波动。
σs=(Smax-Smin)×制品尺寸
σs——成型收缩率波动引起的制品的尺寸偏差。
Smax、Smin——分别是制品的最大收缩率和最小收缩率。
成型零部件的制造偏差:
工作尺寸的制造偏差包括加工偏差和装配偏差。
成型零部件的磨损
7.2.2成型零件工作尺寸的计算
本产品为抗冲ABS制品,属于大批量生产的小型塑件,预定的收缩率的最大值和最小值分别取0.6%和0.3%。
此产品采用5级精度,属于低精度制品。
因此,凸凹模径向尺寸、高度尺寸及深度尺寸的制造与作用修正系数x取值可在0.5~0.75的范围之间,凸凹模各处工作尺寸的制造公差,因一般机械加工的型腔和型芯的制造公差可达到IT7~IT8级,综合参考,相关计算具体如下:
型腔径向尺寸的计算
LM1=[(1+(Smax+Smin)2)Lsl-0.5Δ]+δZ0
=[(1+0.45%)×26-0.5×0]+030
=37.4mm
LM2=[(1+(Smax+Smin)2)Ls2-0.5Δ]+δZ0
=[(1+0.45%)x10.2-0.5×0.20]+0030
=14.78+0.030mm
型腔深度尺寸的计算
图7-3:
HM1=[(1+(Smax+Smin)2)Hsl-0.5Δ]+δZ0
+δZ0=[(1+0.45%)×8.5-0.5×0]
=12.325mm
图7-2HM2=[(1+(Smax+Smin)2)Hsl-0.5Δ]+δZ0
=[(1+0.45%)×4.5-0.5×0.15]+0.050
=6.45+0.050mm
型芯径向尺寸的计算
lM1=[(1+(Smax+Smin)2)lsl+0.5Δ]0-δZ
=[(1+0.45%)×6.99+0.5×0.40]0-0.15
lM2=[(1+(Smax+Smin)2)lsl+0.5Δ]0-δZ
=[(1+0.45%)×6.05+0.5×0.40]0-0.15
型深度向尺寸的计算
)2));
C介质比热Jkg.C,水为4.187x10;
W单位时间内注入模具中塑料重量(kgmin);
Q塑料熔体的单位热量(Jkg);
冷却介质密度(kgm),水为10kgm。
表10-2
直径(mm)
流速(ms)
流量()
8
1.66
5.0x103
10
1.32
6.2x10
12
1.10
7.4x10
15
0.87
9.2x10
20
0.66
12.4x10
当冷却水平均温度在20C以上,Re=6x10时,其计算结果产生误差在2%以内:
K=2041x(1-0.015)vd
为冷却水平均温度;
由表10-2数据得:
流量V=WQ(
=2.62x10
初步确定冷却水道d=8mm;
流速为=Qπd
=1.31x10ms
管子的长度L=60WQk
热传导面的平均温度与冷却水平均温度的差值,其中冷却的平均温度为冷却水在进口处和出口处温度的平均值。
11注射机的参数校核
11.1塑件在分型面上的投影面积与锁模力校核
注射成型时,塑件在模分型面的投影面积是影响锁模力的主要因素,其数值越大,需锁模力也就越大,若超过注射机的允许最大成型面积,则在成型过程中会出现涨模溢料现象。
因此有:
塑件总的投影面积nA与浇注系统的投影面积之和要小于最大成型面积A。
nA+A4x5.3+4x0.5x4=29.2<320cm2满足要求
应使塑料熔体对型腔的成型压力与塑件和浇注系统在分型面上的投影面积之和的乘积小于注射机额定锁模力:
(nA+A)PT=29.2x3.5=102.2kN<900kN满足要求
11.2模具厚度校核
模具厚度H必须满足:
Hmin式中Hmin——注射机允许的最小模厚,即动,定模板之间的最小开距;
Hmax——注射机允许的最大模厚。
H=200mm,H=60mm,M=300mm。
符合条件。
11.3开模行程校核
由于注射模最大开模行程S与模厚无关,因此有:
S≥H1+H2+(5~10)mm
式中H1——推出距离(脱模距离)(mm);
H2——包括浇注系统凝料在内的塑件高度(mm);
H1=23mm,H2=55mm,
所以s=88mm,远小于注射机的最大开模行程300mm,合适。
综上所述,所选择的注射机满足注射要求。
12总结
通过这次系统的注射模的设计,我更进一步的了解了注射模的结构及各工作零部件的设计原则和设计要点,了解了注射模具设计的一般程序。
进行塑料产品的模具设计首先要对成型制品进行分析,再考虑浇注系统、型腔的分布、导向推出机构等后续工作。
通过制品的零件图就可以了解制品的设计要求。
对形态复杂和精度要求较高的制品,有必要了解制品的使用目的、外观及装配要求,以便从塑料品种的流动性、收缩率,透明性和制品的机械强度、尺寸公差、表面粗糙度、嵌件形式等各方面考虑注射成型工艺的可行性和经济性。
模具的结构设计要求经济合理,认真掌握各种注射模具的设计的普遍的规律,可以缩短模具设计周期,提高模具设计的水平。
致谢
半年多的设计已近尾声了,一个合格毕业生要对待不仅仅在课题上重要性,还要知识的渴求,因为这也是一种责任。
自己的成就与学院领导对我们的教育与培养是分不开的,因为一个好的心态才是成功的开始。
在这最后一次考验中我要以自己最大努力作好这次毕业论文和答辩,完成四年中最好的检验也是学院赋予我们最后一个使命,给大学画上一个完美的句号。
经过这次论文不管在设计上、分析问题的能力、合作精神、严谨的工作作风等,使我对次专业知识有个开拓性的认识。
其次,我还要特别是李老师和宋老师对我的支持与悉心指导,在设计期间郭老师帮助我理清设计思路,指导设计方法,提出有效的改进方案。
导师渊博的知识、严谨的教风、诲人不倦的态度和学术上精益求精的精神使我受益终生。
同时我再次感谢机电系所有老师对我的指点与教导,感谢各位老师在学习期间对我的严格要求。
同时也要感谢身边同学的热心帮助,我也不会让他失望的我想用自己努力去创造成功与未来,
最后,我要感谢我的父母,感谢他们一直对我的关心与支持,我会用自己成功去回报他们。
相信自己未来是是美好的,将会飞的越高越远!
【参考文献】
[1]王树勋.注塑模具设计与制造实用技术[M].华南理工大学出版社,1996.78-99.
[2]王孝培.塑料成型工艺及模具简明手册[M].北京:
机械工业出版社,2000.56-67.
[3]唐志玉.塑料挤塑模与注塑模优化设计[M].北京:
机械工业出版社,2004.78-87.
[4]万林.实用塑料注射模设计与制造[M].北京:
机械工业出版社,2000.45-65.
[5]党根茂.模具设计与制造[M].西安:
西安电子科技大学出版社,1995.34-52.
[6]申树义.塑料模具设计[M].北京:
机械工业出版社,2003.67-86.
[7]马浇湘.画法几何及机械制图[M].华南理工大学出版社,1992.79-93.
[8]廖念钊.互换性与技术测量[M].北京:
中国计量出版社,1998.23-45.
[9]屈华昌.塑料成型工艺与模具设计[M].北京:
机械工业出版社,1996