焊接质量标准0513解析.docx
《焊接质量标准0513解析.docx》由会员分享,可在线阅读,更多相关《焊接质量标准0513解析.docx(22页珍藏版)》请在冰豆网上搜索。
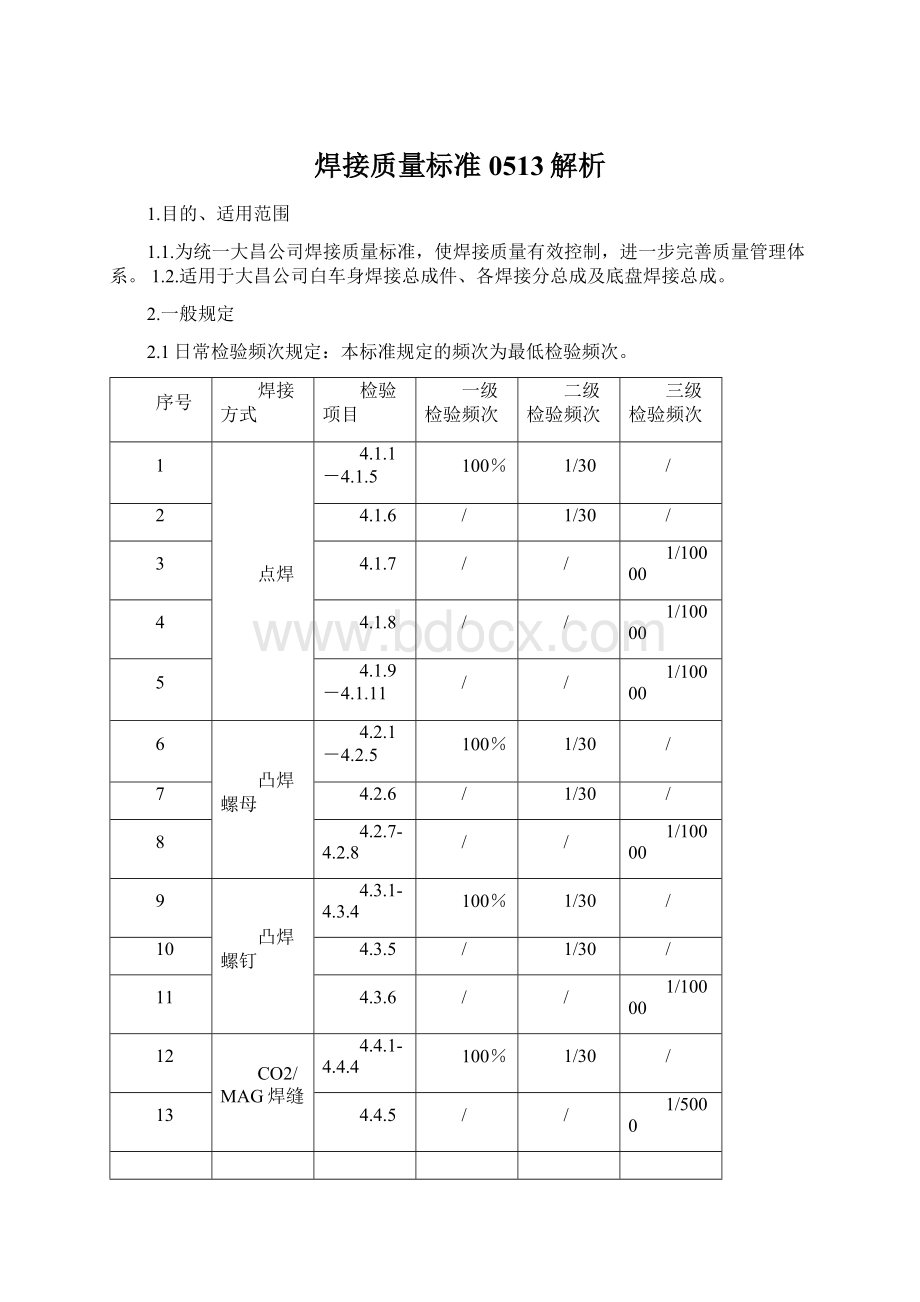
焊接质量标准0513解析
1.目的、适用范围
1.1.为统一大昌公司焊接质量标准,使焊接质量有效控制,进一步完善质量管理体系。
1.2.适用于大昌公司白车身焊接总成件、各焊接分总成及底盘焊接总成。
2.一般规定
2.1日常检验频次规定:
本标准规定的频次为最低检验频次。
序号
焊接方式
检验项目
一级检验频次
二级检验频次
三级检验频次
1
点焊
4.1.1-4.1.5
100%
1/30
/
2
4.1.6
/
1/30
/
3
4.1.7
/
/
1/10000
4
4.1.8
/
/
1/10000
5
4.1.9-4.1.11
/
/
1/10000
6
凸焊螺母
4.2.1-4.2.5
100%
1/30
/
7
4.2.6
/
1/30
/
8
4.2.7-4.2.8
/
/
1/10000
9
凸焊螺钉
4.3.1-4.3.4
100%
1/30
/
10
4.3.5
/
1/30
/
11
4.3.6
/
/
1/10000
12
CO2/MAG焊缝
4.4.1-4.4.4
100%
1/30
/
13
4.4.5
/
/
1/5000
2.2一级检验:
是指现场操作人员的日常自检和互检,由车间操作人员进行,主要有目视检查,检查外观质量;
2.3二级检验:
是指由专职检验员实施的检验,由专检员执行,主要为非破坏性检查,检查焊点、焊缝等外观和通过扁铲检查焊接(点)虚实情况;
2.4三级检验:
是指焊接实验室实施的检验工作,由剖检员及试验员执行,主要为破坏性检查,检查焊点内部质量和焊点焊接强度;
2.5以下涉及的焊点间距、焊点边距、焊点外观直径和焊点直径的计算方法均按最小料厚计算。
3.定义/术语
3.1点焊部分
一般定义
3.1.1焊点间距:
指相邻两焊点中心点之间的距离,代号:
L见附图1
3.1.2焊点边距:
指焊点中心到零件边缘的距离,焊点中心到零件R角边缘的距离也称为焊点边距,代号:
B见附图1
3.1.3接头搭接量:
指焊接位置的零件搭接量,代号:
A见附图1
3.1.4熔核直径:
电阻点焊时在工件贴合面上熔化金属凝固后形成的金属核,代号:
¢dL
3.1.5焊点直径:
指焊点压痕根部处的直径,若焊点为椭圆形则取最大值与最小值之和的平均值。
代号:
¢dP
3.1.6焊透率:
点焊时焊件的焊透程度,以熔深与板厚的百分比表示。
3.1.7压痕:
点焊后,由于通电加压,在焊件表面上所产生的与电极端头形状相似的凹痕。
压痕直径:
¢dE1,dE2压痕深度:
tE1
3.1.8一组/一列焊点:
指同一把焊钳焊接,作用相同或相近的焊点。
3.1.9安全焊点:
是指在车身中起着对关键件的连接作用承载着整车各关键部位,在整车动态和静态中承受各种方向拉应力、压应力、剪切力等,对整车安全性能影响非常严重的焊点。
3.1.10一般焊点:
除安全焊点以外的所有焊点。
缺陷定义:
3.1.11电极粘损:
点焊时电极工作表面被焊件表面的金属和氧化皮粘附污损的现象。
3.1.12缩孔:
熔化金属在凝固过程中收缩而产生的,残留在熔核中的空穴。
3.1.13喷溅:
点焊时,从焊件贴合面间或电极与焊件接触面间飞出熔化金属颗粒的现象。
3.1.14虚焊:
指焊点未形成熔核。
即熔核直径Φ=0。
3.1.15弱焊:
指焊点实际熔核直径较理论最小熔核直径小。
即Φ<Φmin。
3.1.16烧穿/焊穿/击穿:
指熔液脱离熔池,并将熔核破坏,出现一小孔的现象。
3.1.17漏焊:
指焊点实际数量少于图纸或工艺要求。
3.1.18错位:
指包括以下几种情况的缺陷。
a、实际焊点位置与产品图纸要求不一致;b、实际零件位置及零件搭接位置与要求不一致;c、焊点边距和焊点间距不符合以下标准。
一般概念见下附图1,缺陷定义见4.1.11。
附图1 焊点几何尺寸
3.2CO2/MAG焊部分
一般定义:
3.2.1热影响区:
焊接中材料受热但未熔化而发生金相组织和机械性能变化的区域。
3.2.2过热区:
焊接中,具有过热组织或晶粒显著粗大的区域。
3.2.3熔合区:
焊缝与母材交接的过渡区,即熔合线处微观显示的母材半熔化区。
3.2.4熔合线:
焊接接头横截面上宏观腐蚀所显示的焊缝轮廓线。
3.2.5熔深:
在焊接接头横截面上,母材或前道焊缝熔化的深度。
3.2.6余高:
超出母材表面连线上面的那部分焊缝金属的最大高度。
缺陷定义:
3.2.7弧坑:
弧焊时,由于断弧或收弧不当,在焊道末端形成的低洼部分。
3.2.8飞溅:
熔焊过程中,向四周飞散的金属颗粒。
3.2.9裂纹:
在焊接应力及其它致脆因素共同作用下,焊接接头中局部地区的金属原子结合力遭到破坏而形成的新界面而产生的缝隙。
3.2.10未焊透:
焊接时接头根部未完全熔透的现象。
3.2.11未熔合:
熔焊时,焊道与母材之间或焊道与焊道之间,未完全熔化结合的部分。
3.2.12夹杂物:
由于焊接冶金反映产生的,焊后残留在焊缝金属中的微观非金属夹杂(如氧化物、硫化物等)。
3.2.13气孔:
焊接时,熔池中的气泡在凝固时未能逸出而残留下来所形成的空穴。
可分为密集气孔、条虫状气孔和针状气孔等。
3.2.14咬边:
由于焊接参数选择不当,或操作方法部正确,沿焊趾的母材部位产生的沟槽或凹陷。
3.2.15焊瘤:
焊接过程中,熔化金属流淌道焊缝之外未熔化的母材上所形成的金属瘤。
3.2.16烧穿:
焊接过程中,熔化金属自坡口背面流出,形成穿孔的缺陷。
3.2.17凹坑:
焊后在焊缝表面或背面形成的低于母材表面的局部低洼部分。
3.2.18下塌:
单面熔化焊时,由于焊接工艺不当,造成焊缝金属过量透过背面,而使焊缝正面塌陷,背面凸起的现象。
3.2.19凸度过大:
角焊缝表面的焊缝金属过高。
4.产品特性
4.1点焊
4.1.1焊点数量
4.1.1.1检查方法:
目视检查
4.1.1.2评价依据:
产品图纸
4.1.1.3评定结果:
合格――焊点数量符合产品图纸
不合格――焊点数量不符合产品图纸
4.1.1.4缺陷类型:
漏焊、错焊
4.1.2焊点间距
4.1.2.1检查方法:
钢板尺/游标卡尺测量(可采用肉眼观察其是否符合,怀疑时则必须测量)
4.1.2.2评价依据:
附表一为焊点最小间距参考标准
最小间距Lmin(mm)
最薄板件厚度
≤1.2
>1.2
一般焊点
30
40
安全焊点
20
30
4.1.2.3评定结果:
合格——L≥Lmin
不合格——L<Lmin
4.1.2.4缺陷类型:
错位
4.1.3焊点边距
4.1.3.1检查方法:
钢板尺/游标卡尺测量(可采用肉眼观察其是否符合,怀疑时则必须测量)
4.1.3.2评价依据:
附表二为焊点最小边距参考标准
最小边距Bmin(mm)
最薄零件厚度
0.7/0.8
1.0
1.2
1.5
2.0
2.5
3.0
3.5
单排焊点
4.5
5
5.5
6
7
8
9
10
双排焊点
9
10
11
12
14
16
18
20
4.1.3.3评定结果:
合格——B≥Bmin
不合格——B<Bmin
4.1.3.4缺陷类型:
错位
4.1.4焊点外观直径
4.1.4.1检查方法:
钢板尺/游标卡尺测量(可采用肉眼观察其是否符合,怀疑时则必须测量),焊点如果呈椭圆形,焊点外观直径则取最大值与最小值的平均值。
4.1.4.2评价依据:
最小焊点外观直径标准值按以下公式计算
最小焊点外观直径=1.15×5×(安全焊点)
最小焊点外观直径=1.15×4×(一般焊点)δ—最小板厚
常用零件厚度对应的焊点外观直径标准如下表示
最小焊点外观直径(mm)
最薄零件厚度δ
0.7
0.8
1.0
1.2
1.5
2.0
2.5
3.0
安全焊点
4.0
5.0
6.0
6.5
7.0
8.0
9.0
10.0
一般焊点
3.5
4.0
4.5
5.0
5.5
6.5
7.5
8.0
4.1.4.3评价结果:
合格——最小焊点外观直径≤焊点外观直径
不合格——焊点外观直径<最小焊点外观直径
4.1.4.4缺陷类型:
焊点外观直径过小
4.1.5焊点表面质量
4.1.5.1检查方法:
肉眼观察焊点表面状况
4.1.5.2评价依据:
焊点表面不允许出现以下缺陷
a、烧穿/焊穿;
b、焊接变形、焊点扭曲;
c、焊点压痕过深(凹陷程度应小于板厚的15%);
d、焊核及热影响区出现裂纹;
e、严重的毛刺,外观焊点存在毛刺。
4.1.5.3评价结果:
合格——未出现以上缺陷
不合格——出现以上任一缺陷
4.1.5.4缺陷类型:
烧穿/焊穿、焊接变形、焊点压痕过深、裂纹、毛刺
4.1.6焊点强度检查----非破坏性检查
4.1.6.1检查方法:
使用扁铲楔入两焊点之间,以厚板处建立支点向薄板一方掰动,直到薄板焊点焊核处发生变形为止。
4.1.6.2评价依据:
焊点焊核处变形时焊点未发生破坏则为合格,若发生破坏则为不合格
4.1.6.3评价结果:
合格——焊点未发生破坏
不合格——焊点发生破坏
4.1.6.4缺陷类型:
虚焊、弱焊
4.1.6.5备注:
以下情况允许通过目视检查来大致判别焊点质量。
判别的依据为:
焊点压痕深度,焊点外观直径。
若需准确判定焊点虚实则应进行破坏性试验或试板试验,现场必须使用试板试验,以判断焊接强度。
在以下情况下一般不宜使用非破坏性检查方法来判定焊点质量:
a、最薄板件厚度大于1.5mm;
b、有外观要求的焊点;
c、胶接焊点;
d、扁铲无法作用到的部位;
e、单个焊点部位。
4.1.7焊点强度检查----破坏性检查
4.1.7.1检查方法:
参照《破坏性检验指导书》.
4.1.7.2评价依据:
最小熔核直径标准值按以下公式计算
φmin=5(安全焊点)φmin=4(一般焊点)δ—最小板厚
常用零件厚度对应的焊点熔核直径标准如下表示
最小熔核直径(mm)
最薄零件厚度δ
0.5
0.8
1.0
1.2
1.5
2.0
2.5
3.0
安全焊点
3.5
4.5
5.0
5.5
6.1
7.1
7.9
8.7
一般焊点
2.8
3.6
4.0
4.4
4.9
5.7
6.3
6.9
焊点熔核除满足以上直径要求外,熔核内部不允许出现气孔。
4.1.7.3评价结果:
合格——φ≥φmin
不合格——φ<φmin
4.1.7.4缺陷类型:
虚焊、弱焊
4.1.8焊点强度检查----剪切拉伸试验
4.1.8.1检查方法:
a、试样要求:
标准试样见下图
最薄零件厚度δ(mm)
δ≤1.5
1.5<δ≤3.0
3.0<δ≤5.0
δ>5.0
搭接量a
35
46
60
80
试样宽b
45(30)
60(30)
90(55)
120(80)
试板长L
105
138
160
190
b、拉伸要求:
拉伸速度不允许超过5mm/min,如果只强调剪切拉应力,则允许拉伸速度达到Max:
10mm/min。
如下图:
4.1.8.2评价依据:
最低剪切拉伸力Fsmin标准见下表
最低单点剪切拉伸力Fsmin(N/点)
最薄零件厚度δ
0.5
0.8
1.0
1.2
1.5
2.0
2.5
3.0