接箍加工工艺1.docx
《接箍加工工艺1.docx》由会员分享,可在线阅读,更多相关《接箍加工工艺1.docx(21页珍藏版)》请在冰豆网上搜索。
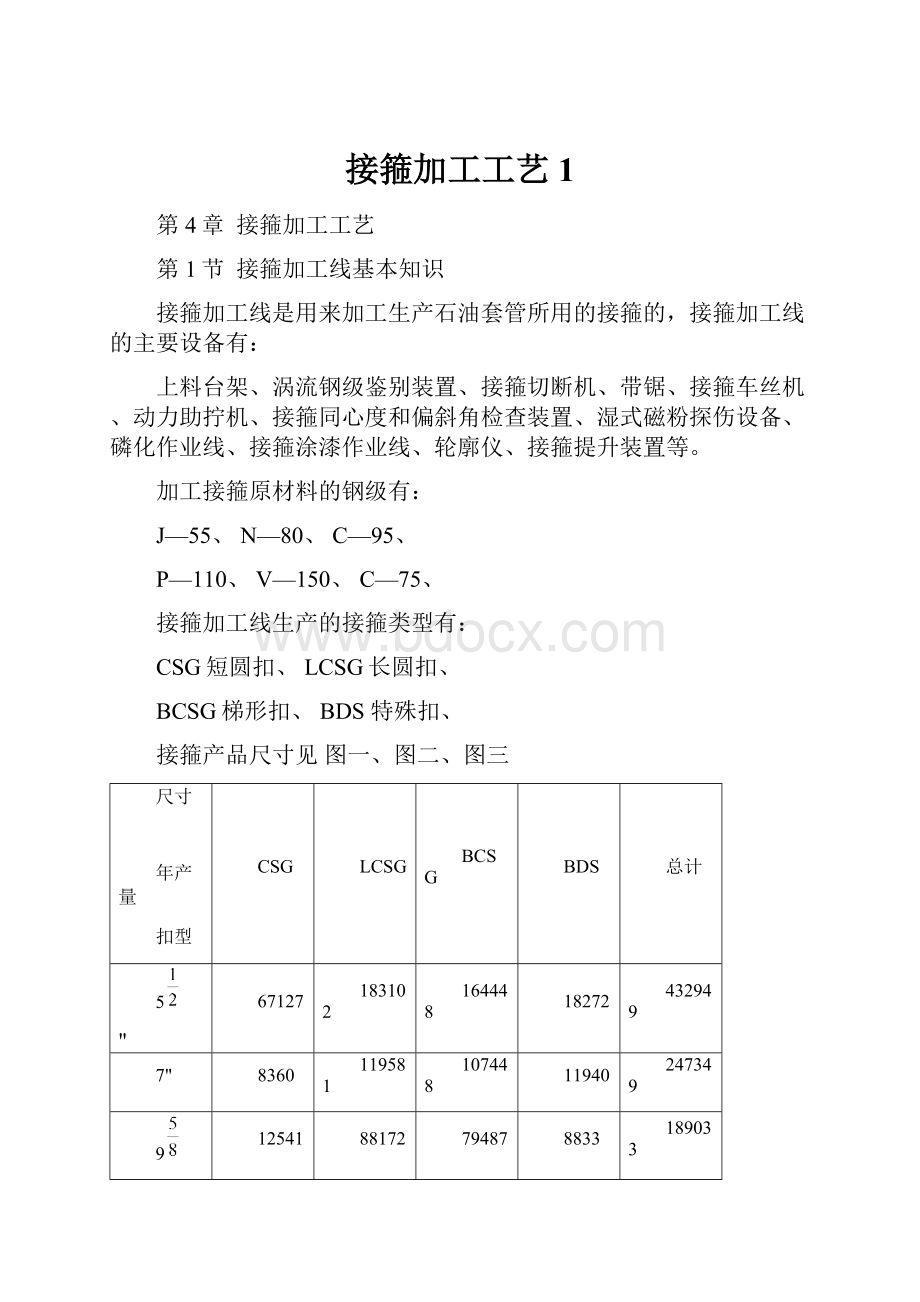
接箍加工工艺1
第4章接箍加工工艺
第1节接箍加工线基本知识
接箍加工线是用来加工生产石油套管所用的接箍的,接箍加工线的主要设备有:
上料台架、涡流钢级鉴别装置、接箍切断机、带锯、接箍车丝机、动力助拧机、接箍同心度和偏斜角检查装置、湿式磁粉探伤设备、磷化作业线、接箍涂漆作业线、轮廓仪、接箍提升装置等。
加工接箍原材料的钢级有:
J—55、N—80、C—95、
P—110、V—150、C—75、
接箍加工线生产的接箍类型有:
CSG短圆扣、LCSG长圆扣、
BCSG梯形扣、BDS特殊扣、
接箍产品尺寸见图一、图二、图三
尺寸
年产量
扣型
CSG
LCSG
BCSG
BDS
总计
5
"
67127
183102
164448
18272
432949
7"
8360
119581
107448
11940
247349
9
"
12541
88172
79487
8833
189033
接箍产量见下表:
(单位:
根/年)
(附图二)
第二节接箍生产线工艺流程及技术参数
接箍料,是按API标准生产的管子,在这条生产线上,经过切断、车丝、丝扣检查、磷化处理,及外表面喷漆等工序<详见图4-2-1和图4-2-2所示,加工成成品接箍。
下面,对接箍加工的工艺过程,做详细说明:
接箍料由中间仓库的运输小车送来,以层的形式放置在覆有人造橡胶的进料台架上。
卸下的接箍料滚动到缓冲台架的端部,由可调挡料器挡住。
挡料器一次只准许一根钢管进入缓冲台架。
接箍料由2.4m长的链式运输机运送到钢级鉴别装置的进口辊道上。
液压提升臂以2.5英尺/秒的速度纵向输送,进入1工位。
在此,进行自动钢级鉴别。
通过后,移动到出口辊道。
然后,接箍料通过一个端部传感器。
进口和出口辊道配置的是交流变速电机传动的辊子。
没有通过钢级鉴别的接箍料将离开输送辊道,进入废料槽。
这些接箍料将通过手提式测壁厚超声波装置来检查。
合格的将回线进入下道工序。
当接箍料通过检查后,被拨到覆有人造橡胶的缓冲台架上,然后移动到2工位的进料台架上,由一个可调挡料器挡住。
当接箍料被拨入输送辊道后,由一套液压夹送辊将其夹住,送入切断机,并碰上一个定位挡板。
此时喂料卡盘闭合,将接箍料向前送入切断机主轴。
当接箍料到达切割位置后,固定卡盘和弹性卡盘闭合<它们分别位于切头的两边>切断机进刀,开始切断。
固定卡盘可以将接箍料后端牢牢的夹紧,并且使它的中心线与切断机主轴的中心线相一致。
弹性卡盘可以将切下的接箍毛坯夹持住。
在切断的过程中,喂料卡盘退后一个接箍毛坯长度<由操作者编程>,并重新夹紧。
当一次切断完成,固定卡盘和弹性卡盘打开,喂料卡盘向前移动一个接箍毛坯长度,以便切割下一个接箍毛坯。
这个周期自行重复,直到喂料卡盘的传感器发出信号,剩下的接箍料已不够下一次切割为止。
这时,喂料卡盘前移,夹住剩下的接箍料,退回,转到一定位置,将其放入一个溜槽,滑入料箱。
喂料卡盘不断地将下一个接箍毛坯送入,使前面的不断被从主轴箱后端顶出,进入出料槽。
切断机切剩的料头,长度足够一个接箍毛坯的,可以送至工位6进行切断,然后回线进行工序3的标记打印。
从切断机出来的接箍毛坯,通过一个链式输送机来到标记打印机的进料槽口,在此由一个拨料杆每次一个的拨入进料槽,然后滚进打印机。
接箍毛坯落到一套转动辊上,随其旋转,气动打印头落下,在接箍毛坯绕轴线的圆周上打印出标记,如厂家名,标记“SPEC、5CT”及钢级代号等。
如需要可以增加打印资料。
打印完毕,由一个液压缸将它拨入出料槽,然后进入储存箱。
叉车操作工人将打印完的接箍毛坯送到车丝机处。
通过提升装置,车丝机操作工将接箍毛坯放入自动装卸料机的进料槽内,一次一个地将接箍毛坏放入提升装置。
然后将接箍毛坯提升到自动装料机头的位置。
装料机头前移,夹住接箍毛坯,并将它与转塔的翻转卡盘对正。
翻转卡盘的卡爪将接箍毛坯夹住,然后,装料机头退出转塔。
转塔转到第一工位,这是粗镗/精镗的位置。
在此工位上按产品的尺寸和类型对接箍毛坯进行镗扎,铣端面和倒外棱。
首先加工半个接箍,然后卡盘翻转,在转塔转动之前进行另一半接箍的加工。
转塔转到第二位置,是车内螺纹/加工密封台工位。
在这个工位进行接箍内螺纹和密封台的加工く如果有密封台>。
加工过程与粗镗/精镗工位一样,先加工半个接箍,然衙再加工另外半个接箍。
接箍加工完成后,转塔转到一个空置,这个位置是为了在将来增加第三个工位而保留的。
然后,转塔再转到起始位置,在此位置上装/卸料机头前移,夹住加工好的接箍,后退并将接箍放入出料槽。
加工好的接箍从出料槽出来后到达检查位置。
在此,检验工将如下操作,以便确定接箍是否符合技术规定的要求。
检验工先用手模一遍加工的丝扣,检查是否有毛刺。
其后检查丝扣的螺距,螺纹深度,端面宽度和凹台倒棱,以便确定它们是否在公差范围内。
最后,在此位置有一个工作塞规以确定钢管和接箍间的紧密距。
然后用湿磁粉探伤装置进行检查。
这是一种湿磁粉检查方法,用来检查表面和表皮下的断续缺陷和夹杂物。
为了减少检查人员的劳动强度,接箍通过输送机的驱动辊运送到磁粉探伤装置处。
它位于二台1077车丝机之间,接箍被送进暗室检查。
检验工在此进行湿磁粉探伤检查。
湿磁粉探伤装置有以下几个基本操作:
1、把接箍放置在一个带有中心导捧的可调支架上,并把中心导棒放在接箍内。
当DC电压加在中心导棒上时,通过汽缸的连杆移动使中心导棒通过接箍,在管端P区形成一个适宜的磁场区。
2、在将要被检查的接箍表面撒上一些磁粉液。
3、在紫外线的照射下,检查接箍表面是否有磁粉的聚集,并估计出缺陷。
<表面不连续,表皮下的不连续和夹杂物>。
当检査完后,把接箍放入卸料槽,并运出湿磁粉探伤区。
由操作工使用接箍提升装置把通过检查的接箍放入储料箱。
有缺陷的接箍被挑出来放入废料箱以便修磨。
表面陷缺可以用手提式砂轮修磨掉。
接箍的修磨工作应该在远离接箍车丝机的地方进行,以防修磨粉尘进入机床内。
修磨后的接箍再次返回磁粉探伤装置以进行进一步的检査。
叉车操作工将加工好的接箍从检查区送到磷化线上去。
操作工将加工好的接箍从检查站送到磷化线后,从储料箱中取出并放入专用工作料箱。
在上料位置每个工作料筐中可以装45个
"的接箍,28个7"的接箍或15个
”的接箍。
工作料筐往复运动在长方形的运送式磷化线作业区,装有接箍的工作料筐放在长方形的运送式磷化线作业区,装有接箍的工作料筐放在运送机上面,运送机提升着工作料筐前进的一个位置,运送机下降,将工作料筐放在浸泡槽中。
同时,一个上料工作料筐放到运送机系统,一个磷化完的工作料筐则从运送机的另一端取走。
接箍磷化的典型周期如下:
1、在第一个工位,工作料筐放入热碱洗槽内。
2、在第二个工位也是一个热碱洗槽,表面沾有冷却液和磷粉的接箍被清洗干净。
3、第三个工位同样是热碱洗槽。
4、第四个和第五个工位是温水冲洗槽,除去残碱。
5、第六个工位是活化剂槽,以提高磷化涂层的附着力。
6、第七、八、九工位是锌磷化槽,向接箍提供防锈和防腐涂层。
7、第十、十一工位是温水冲洗槽,以除去过量磷酸盐。
8、最后一个工位是热熔油槽,以提供防锈保护。
在出料位置,将专用的工作料筐从运送机上取下,以便将接箍从工作料筐中取出,放在储存料箱中。
运送机的专业工作料筐在每一个浸泡槽内停留的时间约为4分钟左右。
经过磷化处理,在接箍丝扣上镀上一层锌涂层,可以提高丝扣的质量,增强密封性和抗腐蚀性。
然后,按API标准进行外表面喷漆。
叉车操作工将装有成品接箍的储料箱运到涂漆机和烘干炉作业线。
在此由操作工用接箍提升装置将接箍从取料箱中取出并放到链式机的托盘上。
链式运输机的链长为158英尺,链节距为2英寸,有158个回转轴,12英寸的间距。
这台链式运输机采用一套具有变速装置和防爆性能的电机驱动,运输机的运送速度为3-9英尺每分钟。
当运输机接箍托盘内装上接箍后,接箍通过一个宽6英尺的喷漆室接箍旋转,从而使接箍外表面上均匀地喷上一层漆。
喷枪具备工件追踪和间隔喷射的装置,这些装置能探测到接箍以便使喷枪仅在有接箍的情况下工作。
这些功能可以节省材料的消耗,并且得到一致的表面。
当接箍涂完漆后,则两次通过一台带摩擦轨道的立式远红外线烘干炉,摩擦轨道可以使接箍托盘旋转,以便于烘干炉对接箍均匀加热。
接箍表面的喷漆将在4.3-13.01分钟内变干<运输机的速度为3-9英尺/分,FPM>,操作工用提升装置将接箍从托盘上取下,并在接箍被送入仓库以前,用一套<外>表面喷字装置在接箍上喷印出最终的数据。
有几台鼓风机和抽风机将设置在喷漆室、烘干炉和冷却隧道中。
然后,由叉车操作工将装有喷完漆的接箍的储料箱运到接箍仓库中。
在这里储存着直到套管加工线需要为止。
接箍加工线还有DMP废水处理系统。
来自磷化作业线的废水含有各种化学成份,有的化学成份是有害的,需要控制排放。
经过DMP处理就可以将它们从废水中分离出来,并转化成不溶的固体颗粒。
来自磷化线含杂质的废水将排入一个容积为10000加仑的蓄水池中。
冲洗槽、热水沖洗槽和冷水冲洗槽的冲洗水需要不断地排放和补充,而酸洗槽、碱洗槽、磷化槽里的溶液要根据这些槽的溶液含有杂质的量定期的排放和补充。
然后将废液从蓄水池以控制的流速放入两个处理池内。
从反应剂供给装置向二个处理器<反映器>供应化学反应剂<氢氧化钠、硫酸、氯化钙和硫酸铝>。
第一个处理池是用来平衡PH值。
然后将废液排入中和槽<第二个处理池>作为进一步的化学反应。
将杂质从清水中分离出来,完全平衡了PH值。
废液从第二个处理池流入凝聚槽。
在凝聚槽内凝聚物加大,形成较大的颗粒,与分离出的不溶性泥浆一起快速沉淀。
处理后的水经过一个澄清系统,这个系统由一个Hi—F10平行板澄清器组成。
澄清器的沉淀速度大于处理后的水升速度,因此渣子运送到金属氢氧化物浓编器是通过重力作用连续进行的。
处理和澄清后的水从澄清器的顶部流入过滤器的给水槽。
金属氢氧化纳浓缩器配备有一个表面倾注洗涤器,它将形成的净水分离出来,然后流回到容积为10000加仑的蓄水池。
浓缩器产生的泥浆被打入泥浆过滤器压缩机进行脱水。
泥浆被打入高压过滤器庄缩机。
经压实和脱水后就变成了由25~40%固体颗粒组成的干泥饼。
过滤后的水从压缩机返回蓄水池。
泥浆的干泥饼被排入一个容积为55加仑的圆筒或料斗里,进行最后的处理。
将处理后的水从砂过滤给水槽放入一个连续净化的低压砂过滤器过滤器将没有随泥浆一同清除的、仍残留在清水里的悬浮固体颗粒清除掉。
澄清的溢流水进入过滤器均匀地分布在砂床底部。
过滤后的水通过砂子上升,最后从溢流口排出。
沙床以及它所积累的固体颗粒向下移动,并被泵打入一个连续的砂分离器,在这里又将砂子重新分布在砂床的顶部,分离出的废物返回到蓄水池。
第三节接箍磷化处理
一、磷化是表面化学处理的一种,钢件浸泡在磷酸盐液中,使基体金属表面获得一层不溶于水的较轫的磷酸盐薄膜的过程,叫磷化。
磷酸膜由磷酸的锌、铁、锰盐组成,颜色呈灰或暗灰色的结晶状。
它具有较高的电绝缘性质,在空气及各种油类、苯类中具有较好的抗蚀能力,磷化膜在400-500℃下,仍能接受短期烘干烤考验。
磷化膜有松孔,可利用油或漆进行浸润,因此可做为油化喷漆的底层。
磷化膜的肌点是硬度低,机械强度低,发脆,磷化膜厚度一般控制在5-15微米范围内,由于磷化过程基体金属表面部分溶解,所以不改变零件尺寸。
二、磷化膜成膜机理:
磷化膜是磷酸盐溶液与金属铁相互作用生产的不溶性磷酸锰、磷酸锌和磷酸铁的复合防护膜,磷化液中的磷酸盐遇水后发生水解,从而使溶液中形成酸式磷酸盐,游离的磷酸和大量的金属离子(铁、锰、锌等)。
当钢铁制品件进入磷化液时,钢铁表面在“酸度的作用下,发生腐蚀。
腐蚀反应首先在钢铁本身的薄弱环节,即微电偶阳极区进行。
铁元素被溶解,并以游离态进入磷化液。
在游离酸的作用下形成磷酸氢盐和正磷酸盐。
由于工件与溶液接触面上的浓度在不断增加,当它们达到饱和时,即结晶沉积在金属表面上,并继续长大,直到形成完整的磷化膜。
溶液中的硝酸盐起催化作用,硝酸盐中的硝酸根能加速铁的溶解,增加结晶核心,加快磷化反应速度,使形成的膜更加细致牢固。
各种因素对磷化反应的影响:
(1)铁
铁含量在一定范围内,对磷化质量影响不大,但当其含量过高时,则严重影响质量,使磷化层附着性差,抗腐蚀能力降低,表面有花斑或呈暗红色等。
铁含量介于0.5-3.5克/升时质量较稳定,一般低于5克/升时,经过适当调整,还能维持反应适当进行,但大于7克/升时,将严重影响质量,若当铁含量少时,所生成的磷化膜结晶偏细,并有磷化不上的趋势,所以有时新配的药液要经过除油酸洗了铁屑处理,以增加铁离子的不断增加可加入适量30%浓度的双氧水(双氧水与水以1:
6—8比例稀释)缓缓加入搅拌均匀,澄清后再生产。
(2)锰锌:
在锰含量较低时,磷化层颜色灰白,结晶微细或无结晶。
在锌含量不足时,反映迟迟不能结束,膜的抗蚀能力亦差。
锰含量不足时,可添加玛日盐(硝酸二氢玛夫盐),锌含量则由硝酸锌调整,硝酸锌中锌含量为22%,硝酸根含量为42%,在调整锰锌含量时,游离酸度,总酸度都会发生相应变化,这一点要注意。
(3)游离酸度和总酸度:
游离酸度,总酸度的正确控制,在磷化过程中占有重要地位,当游离酸度,总酸度偏高时磷化灰白,防蚀能力差,甚至造成硝酸盐的全部沉淀,一般来说总酸度偏高能加速磷化膜的形成,并使结晶致密,但过高后,磷化膜则成粉状,灰白色甚至完全磷化不上。
4、接箍磷化作业线工艺流程<见图4—3—1,图4—3—2>。
图4-3-1
图4-3-2
第四节接箍加工过程中的在线检测
接箍加工过程中的在线检测设备有涡流钢级鉴别装置及湿磁粉探伤设备。
涡流钢级鉴别装置用于鉴别接箍料的钢级,具体的涡流钢级装置的工作原理及其操作见套管检测设备。
湿磁粉探伤用于检测接箍表面及浅层的缺陷。
下面详细说明湿磁粉探伤。
一、湿磁粉探伤原理
磁粉探伤的基础是缺陷处漏磁场与磁粉的磁相互作用。
接箍磁化后,在表面和近表面的缺陷处磁力检测的漏磁场。
逸出接箍表面形成磁极并形成可检测的漏磁场。
此时,在接箍表面浇上磁悬液,磁粉粒子便会吸附在缺陷区域,显示出缺陷的位置、形状和大小。
二、湿磁粉探伤前的准备工作
<一>磁粉探伤前工件的清洗
检测工件前必须要清洗工件,以减少被带入溶液中污染物的数量,提供一个合乎要求的检测表面。
在使用荧光磁粉悬浮液时,工件上的油一定要清除干净。
因为油也可发出荧光而影响检测。
在使用水悬浮液检测时,工件应远离油和润滑脂,这些物质不溶于水,而在水中形成象涂层一样的一层外磁性层,将会降低探伤的灵敏度,而此时水悬浮液也就不能很容易地将磁粉输送到测件表面,同时润滑脂和油在工件表面自由地漂浮,并且在溶槽内形成一个浮渣层。
<二>磁悬液的准备
1、磁粉
用于湿磁粉探伤的磁粉有荧光磁粉和非荧光磁粉。
我们厂使用的是荧光磁粉。
荧光磁粉是在颗粒外覆上一层荧光染料,一般选用在紫外光激发下呈黄绿色的荧光染料。
使用这种磁粉探伤,容易观察,可见度和对比度均好,适用于任何颜色的受检表面,提高了检验速度,有效地降低了漏检率。
荧光磁粉有14A,MG412,MG410,20B,MG412是一种能发出明亮荧光的中灵敏度磁粉。
14A是一种高灵敏度的磁粉。
2、磁悬液介质
用于湿磁粉探伤的磁悬介质可以是水也可以是油。
我们厂采用的是水磁悬液。
用水做悬浮液可以降低成本,消除火灾隐患,并且无烟雾、无油味。
另外水比油稀,探伤时形成的现象快。
但用水介质容易形成气泡,腐蚀工件,因此对水介质要求具有以下性能:
<1>分散性:
用水配制好的水磁悬液能均匀地分散所用的探伤磁粉,在有效使用期中,磁粉不结团。
<2>润湿性:
配制好的水磁县液,在操作时能迅速地润湿被检工件表面,以便于磁粉的移动和吸引。
<3>防锈性:
工件在检验后,在规定的时间内存放不生锈。
<4>消泡性:
能在较短时间内有自动消除由于搅拌作用引起的大量气泡,以保证正常的检验。
<5>稳定性:
在规定的贮存期内,其使用性能不发生变化。
任何一种自来水均可用来配制水磁悬液。
3、水调节剂
有许多种水调节剂可以与荧光磁粉一同使用,促进磁粉在水悬浮。
WA-2B是一种粉沫,WA-4是液体,它们除可以使磁粉悬浮外,还能促进介质的扩散,在检测过程中提供防锈保护,但不是永久性的保护。
WA-3干粉可促进悬浮但没有防腐保护。
WA-5干粉用于溶液中有油污的钢坯探伤。
WA-2B应在每加仑水中含有1
盎司,若每加仑水中其含量低于1盎司,则其促进磁粉悬浮和防锈保护作用会大大降低,每加仑水中含量不应大于1
盎司,过高的浓度也是浪费。
WA-4是一种液态调节剂,它可以替代WA-2B使用。
因为是液态的,所以总处于溶解状态,每100加仑水中应有1加仑WA-4。
WA-5用于钢体的探伤,不含防锈剂,用于溶液中有油污的探伤。
WA-5在每加仑水中含
盎司
4、溶槽的准备
溶槽准备
<1>拆下搅拌器管彻底清洗管子、泵、容器和该装置的其它管道,清洗滤网。
<2>重新安装搅拌器管和滤网。
5、水磁悬液的配制
<1>将水注入溶槽至
处,记下加仑数。
<2>按要求称或测量表2中推荐的调节剂。
注:
20B荧光磁粉不需要列于表上的调节剂,已经事先处理,可直接放入水中。
<3>开动泵马达,直接加入测量好的WA-2B,WA-3或WA-4调节剂至溶槽内,马达持续开动几分钟。
<4>称重测量表2中推荐的磁粉。
<5>将称好的磁粉加入溶槽水中,最好是撒在液面上。
<6>持续开启泵马达几分钟。
<7>核查检测溶液浓度,并调至所要求的。
①加入WA-2B或WA-4水调剂的介质。
(1A)WA-3或WA-5水调节剂的介质。
6、核实溶液浓度
磁悬液的浓度是指每升液体中所含磁粉的克数。
磁悬液的浓度对显示缺陷好坏有很大的影响,浓度不同,其检验的灵敏度也不相同。
浓度太低,小缺陷会漏检;浓度太高,会使衬度变坏,而且会在工件上粘附过量的磁粉,干扰缺陷的显示。
磁悬液浓度的选用应参考磁粉的种类、粒度和受检工件表面的状态诸因素。
一般采用的荧光磁粉水磁悬液浓度为1-2克/升。
水磁悬浮液的深度应保持恒定,因此至少每天要核查一次水磁悬液的浓度。
在整个溶液充分混合搅拌以后须测定其浓度,最广泛使用的测量浓度的方法是在一个标有刻度的ASTM梨状分离器中将磁粉通过其重量沉淀出来。
用ASTM梨状分离器检测水磁悬液浓度的步骤:
1、开动泵马达几分钟,以搅拌悬浮液
2、使检测液流过软管和喷头几分钟以清洗软管
3、将检测液注入分离器至100ml刻度线
4、将分离器和支架置于一固定位置以避免振动的静止30分钟以便磁粉沉淀出来。
5、参见图表2推荐的沉淀物数值校正磁粉颗粒的沉淀量读数,若读数过高则加入悬浮液介质,若读数过低则加适量的磁粉。
注:
在分离器读数时,不能包括杂质颗粒,它们通常沉淀在磁粉颗粒的表面。
三、退磁粉探伤的过程
接箍放置在可调节的检查装置的座子上,并在接箍中心插入一个导体,在中心导体通以6000A直流电,并借助于一个气缸杆将其移动通过接箍,在接箍内形成一个周向磁场。
在磁场的作用下,将配制好的水磁悬液均匀充分地浇过接箍,在接箍裂纹处形成漏磁场而吸附磁粉。
浇水磁悬液时,喷涂应十分认真,液流要微弱,否则裂纹所表现出的现象会被冲走。
荧光磁粉痕的观察是在暗区125瓦紫外线灯的照射下进行的。
注意:
水悬浮液介质是一种很好的导体,因为操作者不可避免地要和溶液接触,所以一定要仔细检查设备是否已很好地接地,以消除任何危险隐患,这在没有特别装置用于作悬浮介质的湿磁粉探伤中是相当重要的。