关键工序培训教材.docx
《关键工序培训教材.docx》由会员分享,可在线阅读,更多相关《关键工序培训教材.docx(18页珍藏版)》请在冰豆网上搜索。
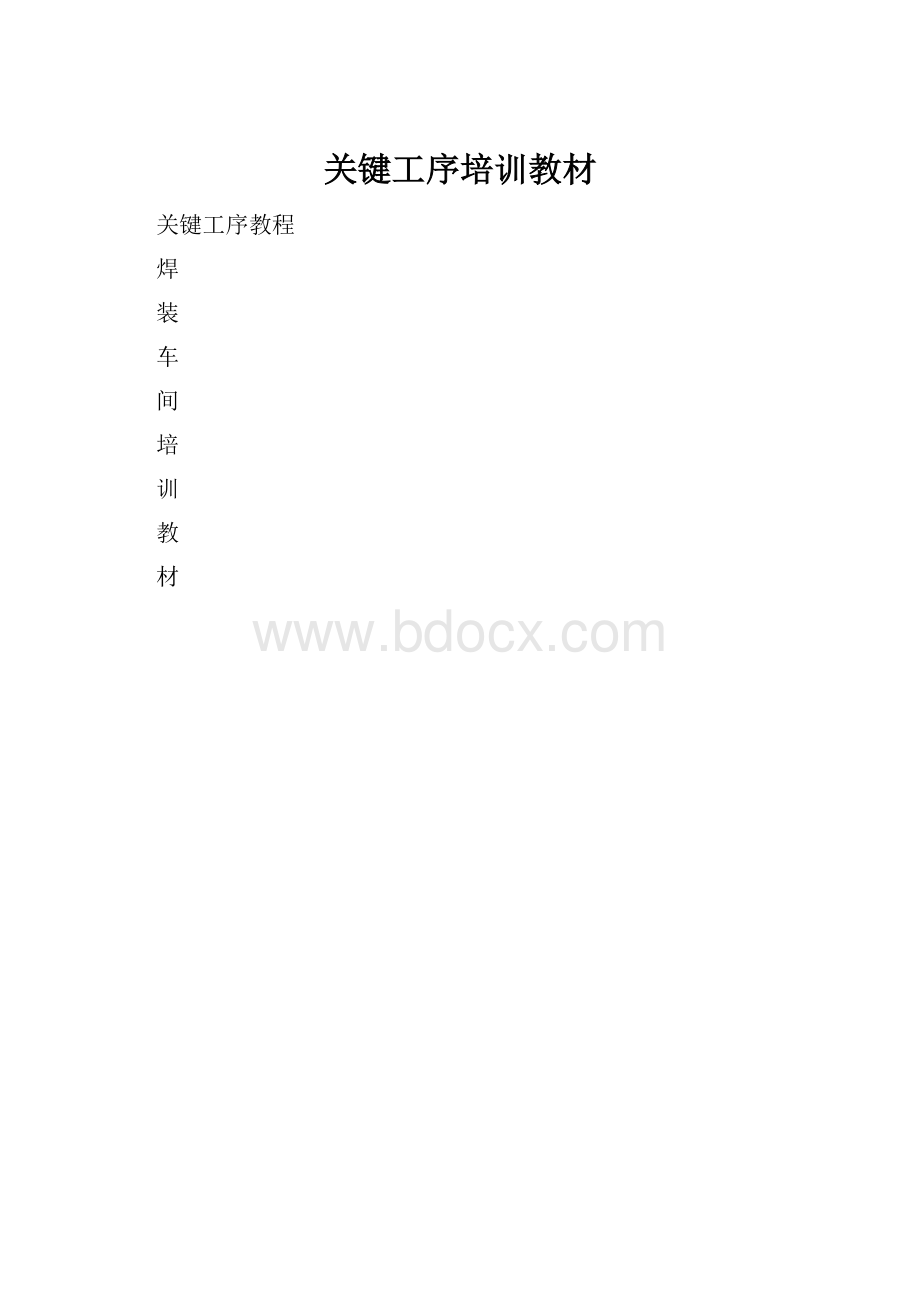
关键工序培训教材
关键工序教程
焊
装
车
间
培
训
教
材
一、关键工序的概念
关键工序是指在生产过程中需要重点进行控制的工序。
关键工序具有关键特性,也就是说,随着过程的进行,关键工序的设置不是永久不变的。
例如,某工序的质量不稳定因素得到了有效控制,处于稳定状态,这时该关键控制工序就可以撤消;而当别的环节、因素上升成为矛盾时,还需要增设新的关键工序。
二、设置关键工序
1、考虑因素
哪些部位需要设置关键工序
•
(1) 对产品的适用性(性能、精度、寿命、可靠性、安全性等)有严重影响的关键质量特性、关键部位或有重要影响因素的工位,应设置为关键工序。
•
(2) 工艺上有严格要求,对下工序的工作有严重影响的工位应该设置为关键工序。
•(3) 质量不稳定、出现不合格品的工位,应设置为关键工序。
•(4) 对用户反馈的重要不良项目的生产工序,应设置为关键工序。
•(5) 对紧缺物资或可能对生产安排有严重影响的关键工位,应设置为关键工序。
•2、设置步骤
设置关键工序的步骤
•
(1) 结合有关质量体系文件,按质量环节明确关键环节和部位,然后在程序文件和操作指导书中明确需特殊控制的质量特性和主导因素。
•
(2) 由设计,工艺和技术等部门分别确定本部门所负责的必须特殊管理的质量控制点,然后编制关键工序清单,并经批准后纳入质量体系文件之中。
•(3) 关键工序虽然单独存在,但又有很强的相关性,必须统一综合管理。
三、对关键工序操作者的要求
•1、明确职责
员工职责
•
(1) 清楚、准确的掌握本工序质量要求和关键性难点。
•
(2) 熟练掌握作业指导书的程序和规定,并严格按其要求进行操作。
•(3) 掌握必要的检验手段和方法,并按有关技术文件要求进行严格把关。
•(4) 了解本道工序的重要性,并知道对下道工序及全局的影响程度。
2、创造性的工作
•
(1) 学好全面质量管理基础知识,掌握必要的方法和手段,并做到准确灵活运用。
•
(2) 记录数据准确,统计分析正确,防止伪假数据引起的偏差。
•(3) 操作中发现偏差和异常,应立即分析原因,采取措施,进行纠正。
•(4) 及时掌握必要的信息,并不断和有关人员交流沟通信息,这对较好处理质量问题是必不可少的环节。
四、焊装一车间关键工序清单:
序号
车间/生产线
工序号
工序名称
质量要求
1
焊装/前结构线
左后轮罩内板总成
保证焊接强度
2
焊装/前结构线
右后轮罩内板总成
保证焊接强度
3
焊装/前结构线
OP20
左前轮罩总成
保证焊接强度
4
焊装/前结构线
OP20
右前轮罩总成
保证焊接强度
5
焊装/下部线
OP50
车身下部总成
保证焊接强度
6
焊装/主焊线
OP20
车身骨架总成
保证焊接强度
五、焊装一车间关键工序控制方法:
焊装车间的关键工序均为点焊工位,点焊的产品特性为:
焊点数量,焊点外观质量,焊点强度和焊点位置。
我们所要控制的关键特性为焊点强度特性。
影响焊点强度的因素主要有员工操作、焊接参数(包括焊接电流和焊接时间)、气压、电极端面直径等。
我们针对这些影响因素制定了关键工序的控制方法:
(1)员工操作:
要求关键工序的操作者具有比普通焊接工更高的素质,包括焊接专业知识,标准操作的规范程度,对关键工序的认知,质量意识等,要求关键工序操作者必须通过关键工序考试并取得关键工序操作证。
(2)焊接参数:
焊接电流和焊接时间是点焊的两个最重要参数,这两个参数记录在每个工位的参数记录卡上,检验员使用电流测试仪定期检查这两个参数的实际输出值。
普通工位的检查周期为两周一次,而关键工序的检查周期为每周一次。
关键的工序所使用的设备也属于关键设备,设备维护人员也会定期进行检查维护。
(3)气体压力:
焊接时的焊接压力由压缩空气提供,气体压力的大小也直接影响到焊接强度,通常我们使用的气压为0.4到0.6Mpa,普通工位一般使用C级气压表来检测气压,而为了保证气压值更准确,我们在关键工序使用精度更高的B级气压表,并且对此类气压表进行每半年一次的检查,检查由质量保证部计量科使用专门的检测仪器进行。
六、点焊基本知识
电阻焊定义:
利用焊接区金属本身的电阻热和大量塑性变形能量,使两个分离表面的金属原子之间接近到晶格距离,形成金属链,在结合面上产生足够量的共同晶粒,而得到焊点焊缝或对接接头.
1.1点焊的基本特点:
(1)焊件间靠尺寸不大的熔核进行连接,熔核应均匀,对称的分布在两焊件的贴合面上。
(2)具有大电流、短时间压力下进行焊接。
是热——机械(力)联合作用的焊接过程。
1.2、点焊的过程分析
点焊焊接循环:
三个阶段:
a—预压阶段;b、c—通电加热阶段;d—冷却结晶。
四个程序:
1—加压程序;2—焊接程序;3—维持程序;4—休止程序。
点焊接头的形成:
预压阶段:
Fw>0,I=0,预压的作用:
在电极的压力的作用下清除一部分接触表面的油污和氧化膜,形成物理接触点。
为以后焊接电流的顺利通过及表面原子的键合作好准备
通电加热阶段:
Fw>0,I>0,其作用是在热和机械(力)的作用下形成塑性环,熔核,并随着通电加热的进行而长大,直到获得需要的熔核尺寸
熔核的冷却结晶过程:
冷却结晶阶段的机——电特点是Fw>0,I=0。
其作用是使液态熔核在压力作用下冷却结晶。
1.3、点焊的特点、分类和应用
例:
板厚1+1MM的低碳钢板,采用表中的任一组规范进行点焊均可以得到质量良好的接头:
焊接电流
(I/A)
焊接时间
(t/s)
(1s=50cyc)
电极压力
(Fw/N)
电极头端面直径(D/mm)
熔核
(d/mm)
拉伸剪切载荷
(Fτ/N)
最佳规范
8800
0.16
2250
6.4
5.8
6100
中等规范
7200
0.34
1500
6.4
5.4
5400
普通规范
5600
0.60
750
6.4
5.3
5300
分析此例,可知,点焊有如下基本特点:
a、焊件间靠尺寸不大的熔核(mugget)进行连接,熔核应该均匀,对称的分布在两焊件的贴合面上;
b、点焊具有大电流、短时间、压力状态下进行焊接的工艺特点:
c、点焊是热——机械(力)联合作用的焊接过程。
对焊件供电的方向可分为:
单面点焊,双面点焊和间接点焊;
对一次形成的焊点数可分为:
单点点焊,双点点焊,多点点焊;
按所用的焊接电流波形可分为工频点焊,电容贮能点焊,直流冲击点焊,三相低频点焊和次级整流点焊。
1.4、电阻焊的优缺点:
优点
缺点
优质:
焊接质量好
目前尚缺乏可靠的无损检测方法
高效:
生产效率高
焊接调设备及配电设备投资较大
低耗:
省材料,成本低
焊件的尺寸、形状和厚度受限制
劳动条件好
搭接接头增加构件自重,且接头抗拉、疲劳强度均较对接接头低
操作简单,易于实现机械化和自动化
1.5、点焊分流
1.5.1、点焊分流的影响因素:
(1)焊点距的分流:
A.连续点烛时,点距愈小,板厚愈厚分流愈大。
B.焊接材料导电性的影响,导电好的分流大。
(2)焊件表面状态:
焊件表面有油污、氧化膜(锈)使接触电阻增大分流增加。
(3)点焊顺序:
已焊点分布在两侧比一侧的分流大。
即:
在点焊件时补焊点要比定位点焊点分流大。
(4)电极与工件相碰引起分流。
(5)焊件装配过紧或装配不良引起的分流。
(6)单面点焊工艺造成的分路阻抗小于焊接阻抗造成的分流。
1.5.2、分流的不良影响
(1)使焊点强度降低。
(2)单面点焊产生局部接触表面过热、喷溅。
1.5.3、消除分流的措施:
A.选择合适的点距;
B.严格清理补焊工件表面;
C.注意结构设计合理性;
D.设计未用电极夹持器,避免与焊件相碰产生分流;
E.对经常有分流的焊点可适当提高电流;
单面多点焊时(现很少采用),采用调幅焊接电流波形。
2.1、影响接触电阻的主要因素有:
电极压力:
压力增加,接触电阻减小;
表面状态:
机械清理,接触电阻减小;
加热温度:
温度升高,接触电阻减小。
电阻点焊的工艺参数:
预压时间、电极压力、焊接脉冲、焊接电流、焊接时间、
冷却时间、维持时间、休止时间、电流增加台阶、
电极端面形状及尺寸、电极修磨频次、电极使用寿命。
c、点焊工艺参数对焊点质量的影响具体分析如下:
过大-------增加工作时间
预压时间
过小-------飞溅、过烧、烧穿、损坏电极
过大-------虚焊、弱焊
电极压力
过小-------飞溅、过烧、烧穿、粘电极、电极消耗加快
过大--------飞溅、过烧、烧穿、粘电极、电极消耗加快
焊接电流
过小---------虚焊、弱焊
过大--------过烧、烧穿、粘电极、电极消耗加快、接头性能下降
焊接时间
过小---------虚焊、弱焊
过大---------虚焊、弱焊
电极直径
过小---------飞溅、过烧、烧穿、电极消耗加快
过大---------电极寿命降低
修磨频次
过小---------电极直径不符合要求,产生虚焊、弱焊
d、焊接工艺参数的确定的基本原则:
(1)、被焊材料的物理性能。
如导电、导热性能好的材料,选用焊接电流大、通电时间短的硬规范;易淬火的材料,则选择较软的规范。
选择电极压力,除考虑材料的常温、高温纺织品度及产生收缩性担缺陷倾向的大小外,应同时考虑选用规范特点。
采用硬规范时,因加热区间窄,焊接区塑变抗力大,则应采用较大的电极压力。
(2)、焊接过程中不应产生
2.2、规范参数间相互关系及选择:
(1)焊接电流和焊接时间的适当配合
硬规范——大电流、短的焊接时间
软规范——小焊接电流,适当延长焊接时间参数
硬规范适用范围:
铝合金、奥氏体不锈钢、低碳钢。
软规范适用范围:
低合金钢、可淬硬钢、耐热合金、钛合金钢。
两种规范在调节I、T使之组成不同的硬、软规范时,必须相应改变电极压力Fw。
硬规范电极压力大,软规范反之。
(2)焊接电流I和电极压力Fw的适当配合。
这种配合的特征:
A焊接过程中不产生喷溅;
B规范选择在喷溅临界曲线附近(无飞溅区内)可获得最佳焊
接质量。
2.3、金属材料的点焊焊接性
定义:
用来相对衡量金属材料在一定工艺条件下,实现优质接头的难易程度的尺度。
(1)判断金属材料点焊焊接性的主要标志:
Ø材料的导电性和导热性:
电阻率小而热导率大的金属材料其焊接性较差
Ø材料的高温塑性和塑性温度范围:
高温塑性差、塑性温度区间窄的金属材料其焊接性较差。
Ø材料对热泪盈眶掀起环的敏感性:
焊接中容易生成与热循环有关的焊接缺陷的金属材料其焊接性较多差。
熔点高、硬度高、线胀系数大的金属一般也较差。
即热敏感性大的焊接性较差。
低碳钢<耐热合金<可淬硬钢。
七、点焊机操作:
1、操作前的准备及检查
1.1电路中二次回路(变压器以下部分,如电缆、焊钳),各连接处必须连接牢固,如发现有松动时要用工具将其紧固好。
1.2水、气路不得有“跑、冒、滴、漏”现象,如有应更换橡胶管或找维修人员解决,及时消除故障,水压、气压未达标准压力时严禁焊接。
1.3焊接工件上有异物(纸张、油污等)附着时不能获得良好的焊接结果,需将上面的污物清除后方可进行焊接。
1.4有感电缆必须绑扎好,否则会降低焊接电流,影响焊接结果;无感电缆辅缆分岔处附近不得有金属物体(如平衡器下帮扎带金属扣),以防分流时损坏电缆及其他设备。
1.5检查手柄按钮有无损坏,导线是否正常;检查其他附件(如滑车、平衡器等)运行是否正常。
1.6焊接前必须穿戴好劳保鞋、巴固眼镜、手套等劳保用品,注意人身安全。
1.7检查电极是否错位;电极杆与电极臂之间螺牙是否损坏。
1.8吊环与焊钳之间连接螺栓是否松动滑牙;焊钳上臂与下臂之间绝缘板是否损坏打火。
1.9气缸上快速接头与气管焊钳上快速接头与水管连接是否漏水,卡箍是否完好。
2、操作
2.1打开压缩空气总气阀和变压器上气阀。
2.2打开循环水总阀门和变压器上水阀,进出水压力差应在0.15Mpa以上(通常进水压力为0.15~0.25Mpa,回水压力为0~0.05MPa)。
2.3调整气动三联件中减压阀。
拉下减压阀下调节手轮可看到桔黄色标记,这时可根据操作指导卡要求调节压力(一般在0.4~0.6Mpa间),调整完毕后将调节手轮往上轻推即可锁定压力。
2.4将变压器面板上循环水阀门打开,观察回水管路上水流指示器内叶轮转动情况可大致判断水流量。
2.5以上工作完成后,确认设备无故障,将“焊接/调整”开关拨至“焊接”位置,这时即可进行焊接作业。
3.悬挂点焊机维护及保养
一级保养:
1.电极帽使用一段时间后,需用锉刀修磨保持光洁,以保证焊点质量。
2.每天工作完毕后必须清除焊钳上的飞溅。
焊钳上的飞溅会造成电极间的打火,降低焊接电流,损坏设备,因此必须及时清除。
3.定时对油雾器加油,使油面保持在要求范围内(油雾器保护罩上标有上下限位置),并要定期放出空气过滤器中的积水及灰尘。
4.每班前检查水、气管是否老化或泄露。
5.每班前检查气压表是否损坏。
6.每班前检查开关手柄与内部行程开关连接的螺栓、螺母、弹簧是否完好。
7.每班前检查电缆绑扎是否规范;电缆与平衡器之间链条是否完好;电缆与平衡器之间尼龙绳是否完好。
8.每班前检查电磁阀是否完好及元件是否完整;消音器是否齐全完好。
9.每班前检查电缆与焊钳之间连接螺母是否紧固牢靠。
二级保养:
每半月1次检查变压器是否有异常温升。
每半月1次检查电极间绝缘套是否损坏。
4.注意事项
1.作业时劳保用品穿戴整齐。
2.焊钳或电缆有不正常温升时应停止焊接,及时告知维修人员。
3.焊接时严禁将手贴近气缸活塞动作处和电极夹持区。
4..焊接时要避免焊钳与夹具相碰产生打火.
5.焊接过程中发现设备有异常情况应停止焊接,排除故障后才能继续焊接作业。
6.作业时切勿用湿手接触焊钳、焊机部分。
5.常见故障及排除方法
故障现象:
按下开关焊钳无反应
故障原因:
1)手柄开关损坏或在“单点”状态下卡死。
2)按钮接线脱落或导线断路。
3)气压为0或压力不够。
4)电磁气阀卡死或其电源线断路。
5)其他规范线路短路。
6)控制箱上故障灯亮。
解决方法:
1)将手柄开关复位或将其更换。
2)重接按钮线或换导线。
3)调节气压使其符合要求。
4)修理电磁阀。
5)排除其他规范短路故障。
故障现象:
焊接时气缸动作但无电流输出。
故障原因:
1)电缆断路。
2)焊机处于“调整”状态。
3)电极帽长期磨损后接触不上。
解决方法:
1)更换断路电缆。
2)改变焊机工作状态,使其在“焊接”状态下工作。
3)更换电极帽。
故障现象:
焊接电流偏小。
故障原因:
1)电缆老化或电缆内部短路。
2)焊接时钳臂或电极杆灯接触到非焊接区产生分流
3)电极接触处电阻过大。
4)焊钳内部短路
解决方法:
1)将故障电缆更换。
2)焊接时规范操作。
3)及时修磨电极,清理工件上污物
八、白车身电阻点焊质量要素
序号
质量要素
职责内容
职能部门
1
焊接工艺
焊点工艺设计和焊点质量标准
焊接工艺卡及质检工艺卡
焊装技术组
2
焊接零件
零件材料及表面状态控制
零件几何精度控制
外协件表面状态及几何精度控制
焊装技术组
三座标测量室
3
焊接设备
投产前设备测试
投产后设备维护、管理并定期测试
点焊电极材料、电缆、MAG焊丝、保护气检测及验收
焊装技术组、焊装维修
焊接实验室
4
焊接技术
工艺参数
制定及输入焊接工艺参数
管理及优化焊接工艺参数
分析及解决焊接技术质量问题
焊装技术组
5
焊接操作
焊接操作工培训及持证上岗
严格按照工艺文件进行操作
焊装技术组
焊接实验室
6
焊接质检
一级检查(非破检CND):
操作工、生产班组自检
二级检查(非破检CND):
专职质检员巡检
三级检查(破检ND):
质检室按一定频次抽检
外协件焊接质量检查:
焊接实验室
焊装技术组
焊接实验室
7
质量监控
焊接质量信息整理、分析、预防及改进
编制NQST月报,向有关职能部门通报焊接质量问题及质量信息,并督促整改
焊接实验室
焊装技术组
8
缺陷处理
不合格品返修
不合格品让步
不合格品报废
焊装技术组
下面具体分析各质量要素对点焊质量的影响。
1.焊接工艺主要包括焊点工艺设计及焊点质量标准。
正如新产品开发,产品设计相当程度上决定了产品的质量和工艺成本一样。
焊点工艺设计也在相当程度上决定了采用的工装设备,焊点质量和质量成本。
工艺设计要在充分满足产品要求和生产纲领的前提下,采用简便、合理、经济的焊接方法和焊点布置,例如:
(1)进行工艺设计时要充分考虑焊接设备的能力和本地区供电电网的品质,选择功率余量足够的焊机和控制精度合适的焊接控制器,确保焊点质量及其稳定性;
(2)进行焊点设计时应尽量考虑使用双面点焊,实践证明,双面点焊比单面点焊焊接质量更可靠,易于保证;
(3)尽量避免设计多层板(超过三层以上),特别是多层厚板的装配结构进行点焊;
(4)进行焊点设计时要充分考虑焊点的间距及边距。
选择合适的焊接顺序以减小焊接分流及焊接变形;
(5)设计焊接回路时应尽量减小二次回路阻抗;
(6)制定和采用合适焊接质量标准,该标准应与产品设计及工艺能工艺能力相适应;
(7)制定和采用合适的点焊质检工艺,使用简便、可靠、经济的质检方法和工具,制定合适的质检频次;
(8)使用合适的测试仪表及工具。
2.焊接零件
轿车白车身用材均为低碳及低合金结构钢板材,焊接性能良好。
零件表面镀层情况分以下五种;
—:
裸板:
G-:
单面热镀Zn板;
GG:
双面热镀Zn板;
E-:
单面电镀Zn板;
EE:
双面电镀Zn板。
焊接表面清理:
焊件表面氧化膜和油污等会增加焊接时的接触电阻。
由于点焊时变压器次级电压很低,所发焊件的表面质量对焊接电流的影响很大,使焊点强度不稳定。
为此必须对焊件表面的点焊区域进行前处理。
对于表面有镀层钢板的焊接,一般视镀层情况增加焊接电流(10~15)%,同进适当增加电极压力和焊接时间。
零件装配:
零件装配应保证在规定的电极压力和预压时间作用下,点焊区域能良好地贴合。
车身覆盖件装配时,易产生的缺陷是间隙过大,部分电极压力将消耗于克服钢板的弹力以消除这些间隙,故实际作用于点焊区域的焊接压力减小了。
因此飞溅的倾向增大,焊点尺寸和接头强度波动较大,易产生各种焊接缺陷如:
虚焊、弱焊、过烧、烧穿等,焊接变形也有所增加。
故一般装配间隙不应大于(0.5~0.8)㎜,当焊接尺寸较小刚度较大的冲压件时,装配间隙要求减小到(0.1~0.2)㎜。
要减小零件装配间隙,主要途径是要提高冲压件精度,其次可采用适当的夹具和样板,焊前牢固可靠地夹紧焊件,必要时还可用塞尺检验装配间隙值的大小。
焊装车间采用检具来检查控制焊件的装配精度,对白车身,还定时检其几何尺寸IQG值(即零件几何质量指数)。
发现装配质量问题,立即通知相关工序、冲压车间或外协件供应商,及时解决。