机床设计.docx
《机床设计.docx》由会员分享,可在线阅读,更多相关《机床设计.docx(17页珍藏版)》请在冰豆网上搜索。
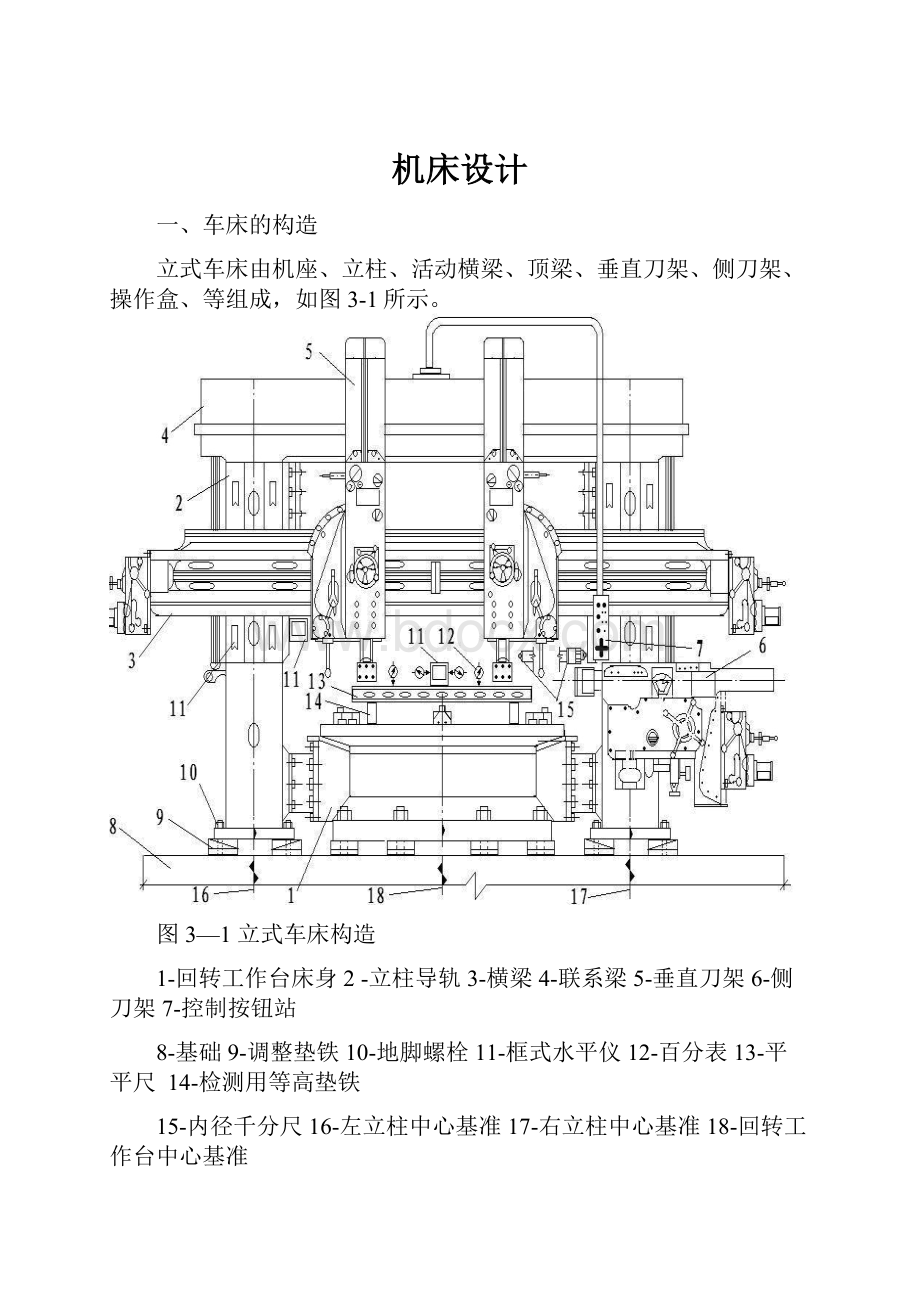
机床设计
一、车床的构造
立式车床由机座、立柱、活动横梁、顶梁、垂直刀架、侧刀架、操作盒、等组成,如图3-1所示。
图3—1立式车床构造
1-回转工作台床身2-立柱导轨3-横梁4-联系梁5-垂直刀架6-侧刀架7-控制按钮站
8-基础9-调整垫铁10-地脚螺栓11-框式水平仪12-百分表13-平平尺14-检测用等高垫铁
15-内径千分尺16-左立柱中心基准17-右立柱中心基准18-回转工作台中心基准
二、底座安装
1.地脚螺栓预埋
(1)立式车床的地脚螺栓,通常为预埋螺栓,在浇注基础混泥土时安装好,按进厂设备实物用样板划定地脚螺栓中心位置。
样板使用薄铁皮为宜。
(2)制作预埋螺栓固定架,固定架要能保证螺栓的铅垂度,在浇注混泥土时不发生变形。
(3)固定架在浇注基础前准备定位,并安装牢固,防止在浇注过程中发生位移,底座和立柱底的相互中心距离必须准确。
(4)地脚螺栓安装在固定架上,调好标高和铅垂度,将螺栓固定稳妥。
(5)浇注混泥土时要注意观察和检查,防止发生固定架和螺栓移动。
2.安置垫铁
(1)根据车床的重量、加工零件的最大重量、以及地脚螺栓的规格和个数为16个,混泥土强度等来确定垫铁的组数和排列方式,并可按下式近似计算垫铁的面积A(
):
A=
式中C——安全系数,一般取C=1.5~3;
——机床质量,单位kg;
——地脚螺栓拧紧力,单位N;
R——基础或地坪的承载强度,单位MP。
(2)基础达到可安装的强度后,划出基础纵、横中心线。
(3)垫铁处基础铲凿平整,用垫铁和平尺检查水平。
(4)某些立式车床变速箱后面处,应使用可调垫铁,以便于微动调整变速箱。
3.安装变速箱和基座
(1)当变速箱和基座底面为非加工面时,允许少量垫铁接触不平处用钢板插入垫平、垫实,待基座找平后点焊住。
将油道油腔清洗并吹扫洁净。
(2)调整找平基座。
在基座导轨上放置纵向和横向调整垫铁,将平尺通过底座导轨回转中心放在垫快上,用水平仪测量,纵向和横向偏差均不大于0.04/1000mm,调平后紧固地脚螺栓。
(3)在底座上安装工作台。
1)将工作台和底座主轴键槽的位置划出,并引出延伸到工作台和底座的侧外缘边。
2)将工作台吊升到底座上方,对正键槽划线,缓缓落入基座轴套内。
3)工作台找水平度。
在工作台上按纵向和横向放置垫铁,上放平尺,用水平仪按纵向和横向测量工作台的水平度,其偏差均不应超过设备技术文件的规定。
三、左、右立柱的安装
1.清洗检查立柱
清洗立柱各加工面上的防锈油漆,检查立柱导轨面应无锈蚀、损伤等缺陷,结合面无锈斑、销钉和销孔配合合适。
检查安装侧刀架平衡配重的右立柱内孔,铲除突出的铸造毛边。
2.吊装立柱
将平衡配重吊入右立柱下坑内,找中心位置,避免在立柱吊装落位时发生碰阻。
立柱吊装就位时,要平正靠近底部垫铁和基座结合处,利用调整垫铁和连接螺栓使立柱于螺栓接合面贴合对正后,插入定位销,拧紧连接螺栓,下部垫铁要垫实。
3.调整立柱铅垂度
用水平仪在正导轨面和外侧导轨面上测量,同时在工作台中央放垫铁、平尺、水平仪测量,正、侧两面和工作台纵、横两方向的读数代数差值即偏差值,不应大于0.04/1000mm,如图3-2所示。
图3-2检查立柱导轨对工作台或底座导轨的垂直度
4.检验两立柱正导轨面的共面度
用平尺靠贴立柱正导轨面,用0.04mm塞尺检查,不应插入。
5.安装主变速箱
(1)在吊横梁前将主变速箱就位,于底座找正连接固定。
(2)检查并调整变速箱最末从动轴齿轮于工作台大齿圈的齿合情况,使之达到设备技术文件要求的技术条件。
四、横梁和顶梁安装
1.横梁和顶梁安装步骤
(1)清洗横梁、立柱结合面,检查结合面。
应无锈迹、损伤等缺陷,涂抹上润滑油。
(2)在横梁下边垫上方木层。
将横梁吊平吊升到安装位置,贴靠立柱找正落于垫木上。
(3)顶梁经清洗检查后吊升到立柱上,调整后有控制定距垫板时,将垫板插入顶梁和立柱间,然后拧紧连接螺栓。
(4)顶梁的栏杆和扶梯应在顶梁安装时安上,以便于在顶梁上操作。
(5)安装横梁的传动螺杆,与横梁上的螺母连接,上端与顶梁上传动机构连接。
(6)装配横梁与立柱导轨上的镶条、压板、压板弹簧,初步调整导轨间隙。
2.横梁质量检查调整。
(1)检查横梁垂直移动对工作台旋转轴线的平行度。
1)在工作台中央放检验棒或精密角尺;将百分表固定在横梁上,使其测头触到检验棒或角尺上。
2)检验横梁的垂直移动偏差:
在横梁行程的上、中、下三个位置,移动横梁测量,在1000mm的测量长度上至少应测取三个读数。
3)检验横梁垂直移动对工作台旋转轴线的平行度:
平行度偏差以百分表读数的最大差值计,在平行于横梁的平面内的平行度检测如图3-3a所示,在1000mm测量长度上,不应大于0.04mm;在垂直于横梁的平面内的平行度检测如图3-3b所示,在1000mm测量长度上,不应大于0.06mm。
图3-3检验横梁垂直移动对工作台旋转轴线的平行度
a)平行横梁平面内b)垂直横梁平面内
3.导轨间隙调整
导轨间隙调整根据机床结构,通常有平镶条导轨间隙调整、楔形镶条导轨间隙调整或压板导轨间隙调整、滚珠导轨间隙调整等类型。
(1)平镶条导轨间隙调整。
平镶条导轨间隙调整步骤见图3-4:
旋松螺母,拧紧或放松螺钉,移动平镶条1的位置,则导轨间隙变小或变大,如图3-4a,b和c所示。
调整时,宜先拧松固定螺钉2,调整完成后在拧紧螺钉2。
调整间隙时,可用塞尺在导轨的两头和中间测量,间隙应均匀,最后旋紧螺母。
平镶条只局部与螺钉接触,较易发生变形,与导轨接触状态较差。
(2)楔形镶条导轨间隙调整。
楔形镶条导轨间隙调整步骤如图3-4所示:
旋转调节螺钉2、拔杆3带动楔形板延长度方向移动,从而最大或减小间隙,拔杆还可以限制楔形镶条在工作智能中发生窜动,如图3-4d所示。
反向调整调节螺钉2(先拧松一端,在拧松对应端),拔杆3推动楔形镶条移动,使导轨间隙增大或减小,测量达到要求间隙值后,旋紧另一端的调整螺钉,将楔形镶条固定,防止在工作中出现窜动而改变了间隙值,如图3-4e所示。
当需调大导轨间隙时,先拧松螺母M,再将调节螺钉2拧松拔杆3带动镶条外移使导轨间隙增大,测量间隙值符合要求后,旋紧螺母M和N,将镶条定位。
需调小间隙时,先拧松螺母N,再将调节螺钉2拧紧其操作与调大间隙相同,如图3-4f所示。
图3-4用镶条调整轨道间隙的方法
a),b),c)平镶条d),e),f)楔形镶条
1-镶条2-调节螺钉3-调整拔杆
(3)压板导轨间隙调整。
压板导轨间隙调整步骤如图3-5所示:
将压板面m与n是平面磨准或刮准来保证需要的间隙,如图3-5a的间隙在n面。
拧开固定螺钉2,调整压板与导轨结合面间的垫片厚度来改变间隙值,测量间隙时,要拧紧固定螺钉,否则间隙值不准确,如图3-5b所示。
图3-5c所示是用调整螺钉来改变压板的位置,从而增大或减小导轨间隙。
图3-5用压板调整导轨间隙
a)用磨削或刮削压板的厚度来保证间隙b)用改变垫片厚度来调整间隙
c)用螺钉调整平镶条的位置来调整间隙
1-压板2-固定螺钉3-垫片4-平镶条5-调节螺钉
(4)滚珠导轨间隙调整。
滚珠导轨间隙调整步骤如图3-6所示:
镶钢滚珠导轨是将下部镶钢导轨固定在床身上,如图3-6a中的5和6:
上部镶钢导轨固定在工作台上,导轨中间是钢珠滚动体,用保持器将各钢珠隔开,间隙不用调整。
图3-6b为用调节螺钉7调整外侧导轨的位置来调大或调小导轨间隙测量间隙符合要求后,将螺钉、螺母拧紧螺钉7还可将导轨进行预紧,以增加导轨刚度,提高导轨的运动精度和承受较大的倾侧力矩。
图3-6滚珠导轨间隙调整
a)不需机械调整,利用油压顶浮形成间隙b)用螺钉调整镶钢导轨移动来调整间隙
1,2,5,6-镶钢导轨3-钢球4-保持器7-调节螺钉
(5)滚柱导轨间隙调整。
滚柱导轨间隙调整调整步骤与滚珠导轨间隙调整、V形和矩形截面导轨及润滑面导轨调整步骤类似,其中V形和矩形截面导轨、由于该结构只在上、下导轨间虽加装滚柱体,但其间隙会因为工作台自重而不需要调整,间隙靠润滑油压形成,如图3-7a所示。
滚柱导轨承载能力比滚珠导轨大,应用较广,但对导轨平行度要求高。
燕尾形滚柱导轨间隙调整可通过调整螺钉1来移动上燕尾导轨,改变燕尾斜面与滚柱体间的间隙,水平滚柱体的间隙不需调整,如图3-7b所示。
图3-7滚珠导轨间隙调整
a)不需机械调整,利用油压顶浮形成间隙b)用螺钉调整燕尾形导轨移动来调整间隙
1-调整螺钉2-燕尾形导轨3-滚动体
五、刀架安装
1.垂直刀架安装
(1)拆开刀架上的导轨镶条和压板,清洗导轨及加工面。
检查导轨面,应完好无锈蚀。
(2)左右垂直刀架分别吊装安于横梁上,在导轨面上抹上润滑油,刀架移动传动的齿轮应对正横梁装配孔,装上压板、镶条,调整导轨间隙。
(3)装好垂直刀架升降的底轴,拆除平衡锤的压紧构件,使平衡锤起配重平衡作用。
2.侧刀架安装
(1)拆下镶条、压板,清洗导轨及其他加工面,检查无缺陷后抹上润滑油。
(2)安装刀架与配重的连接件,如轴承、滑轮(或链轮)、轮轴、吊挂钢索或链子等,清洗防护油漆。
(3)在右立柱正面下部放上方木,擦净立柱导轨面,抹上润滑油,将侧刀架吊平正,缓缓靠近立柱正面导轨,安上镶条、压板,初步调好导轨间隙,连接升降机构。
(4)将配重和侧刀架连接起来,用手摇操作刀架上升,检查有无卡阻现象,拆除方木。
3.刀架质量检测
(1)检测垂直刀架水平移动对工作台面的平行度方法见图3-8所示,其步骤如下:
图3-8检验工作台固定型立式车床垂直刀架水平移动对工作台的平行度
1)在工作台距中心等距离且与横梁平行位置,放两个检验调整用等高垫块,上放平尺,使平尺与横梁水平导轨平行。
2)将横梁锁定在较下部位置,百分表固定在垂直刀架上,测头触及平尺检测表面。
3)未检验的另一垂直刀架置于该侧立柱前。
4)移动垂直刀架,在任意1000mm长度上,百分表的读数最大代数差值即不平行度偏差,不应大于0.03mm.。
5)用同样的方法检验另一台垂直刀架,均应符合要求。
6)当测得偏差值超过规定时,经分析确定无测量误差后,应调整相关部位的座底垫铁来满足刀架的几何精度。
(2)侧刀架上下移动对工作台旋转轴线的平行度检测见图3-9所示,其步骤如下:
图3-9检验侧刀架移动对工作台旋转轴线的平行度或侧刀架
移动对工作台面的垂直度
1)按垂直刀架水平移动对工作台面的平行度检测方法的相同要求,在工作台上纵向放平尺,上放检验用精密角尺,或将检验棒放在工作台中心,百分表固定在测刀架上,侧头触及检验棒或精密角尺。
2)移动侧刀架,测量并记录百分表的读数最大代数差值,在任意300mm测量长度上,不应大于0.03mm.。
六、润滑系统和液压系统安装
1.检查随机带来的所有润滑设备、附件及油管,应与设备润滑图相符,油管无破损及挤扁现象。
2.用压缩空气吹扫所有油管、油孔、油道,应畅通无污染。
必要时,可用煤油和锭子油的混合液清洗油管或按说明书的要求清洗。
3.安装油泵、油箱、操纵台,按图进行管道连接。
4.检查油箱内部,确认清洁后,按说明书要求加入润滑油到规定油位。
5.全部安装完成后,按润滑系统开车程序启动油泵,观察油泵的运转情况是否良好、润滑系统各接头处有无泄漏情况。
6.将各给油点接头拆开,排除管内的空气,至给油点连续稳定来油为止。
7.将工作台吊起,检查机座导轨的来油情况是否正常。
8.检查工作台转动及其他运动部位是否与油管相碰;特别注意检查工作台主轴的供油情况,油管是否固定牢靠、有无碰擦现象。
9.检查油箱回油情况,油箱的油位在泵供油后是否符合规定油位要求,如低于规定油位,应补充加入同牌号油。
七、试运转
1.试车条件
(1)机床全部组装完毕,并清洗洁净。
(2)所有机床部件的安装几何精度,经检验合格。
(3)润滑、液压系统清洗合格,按技术文件要求加注润滑油、液压油,系统运转良好。
(4)机械、电气安全装置,调整正确、可靠;制动和锁紧机构应调整适当。
(5)各操作手柄转到灵活,定位应准确,并应将手柄置于“停止”位置上。
(6)电气操作控制系统接线应正确,接头牢固可靠,绝缘、接地、接零良好。
各电机旋转方向符合机床工作要求。
(7)运动部位的安全防护装置已安装好。
(8)试车场地杂物清理干净,备用工机具、应急物品准备妥当。
2.试车前的准备工作
(1)检查各导轨的间隙是否符合设备技术文件的要求,导轨和镶条的配合松紧程度是否良好。
(2)检查各刀架、横梁的锁紧调整情况是否符合要求。
(3)检查各电机的运转方向是否与机床运转方向要求相符。
(4)检查各运动部件有无有与其他部件发生碰撞和摩擦现象。
(5)润滑油的品种、规格及油量是否符合要求,各给油点供油是否正常。
(6)油盘供油的各给油点出油是否符合设备技术文件的要求。
(7)检查各手柄的操作是否灵活,位置是否正确,仪表指针有无错误。
3.试运转操作
(1)电机空负荷运转。
将电机与机械运转机构脱开,按电气启动程序运转0.5~2h;主电机的绕组温升和轴承温度应符合设备技术文件的规定;电机空负荷试运转合格后,方可与机械运转机构连接。
(2)工作台试运转
1)点动启动。
检查有无异常声响,方向是否正确。
2)以低速启动运转。
低速运转时间不少于5min。
3)正常运转。
低速运转正常后,再以各级工作速度进行运转,每级速度运转不少于5min。
4)高速运转。
正常运转试验结束后做机床的高速运转,高速运转试验应以主轴达到稳定温度为止。
试运转中,应反复变换工作台速度,变速机构应灵活可靠,指示正确。
高速运转之后,再次选定工作台中等速度,检验启动、停止、制动、正反转等动作,反复进行10次,其动作应灵活、可靠;电气、液压、润滑系统工作应良好、可靠。
(3)横梁运行试验。
慢速开动横梁的上升、下降,启动、运行应平稳,无冲击、爬行现象;横梁与立柱导轨的夹紧机构的松开、夹紧动作协调;行程开关动作准确、可靠;润滑油供油正常;启动、停止灵活、可靠;慢速试验合格后,做中速和快速试验,均应符合要求。
(4)刀架进给试验。
垂直刀架与侧刀架逐个作启动、停止试验,应动作准确、可靠;作慢速进给试验,反复动作10次,其动作应灵活正确;变速机构应灵活、可靠,指示准确;夹紧机构动作应协调、灵活可靠;行程开关动作准确、可靠;启动、停止动作准确、可靠;润滑供油良好;刀架慢速进给试验合格后,按相同操作程序做中速、高速进给试验,均应达到上述要求。
(5)刀架做水平移动(垂直刀架)和升降试验(侧刀架)。
启动和停止应准确、可靠;夹紧机构动作协调、灵活、准确;运动应平稳,无卡涩和爬行现象;行程限位开关应准确、可靠;润滑供油良好;各种速度下均能达到上述要求。
(6)做机床联合动作试验。
单项动作试验合格后,做工作台、横梁、垂直刀架,侧刀架联合动作试验。
机床联合动作试验中,各项运动应协调准确、平稳;变速操作机构应灵活、可靠;启动、制动、停止、正反向运动应灵活、准确;各运动工作部位润滑良好、温升正常;电气系统、润滑系统、液压系统工作正常;整机连续空负荷运转时间,可按表3-1的要求进行;主轴承温度和温升应符合按设备技术文件或表3-2的要求。
表3-1机床连续空负荷运转时间
机床控制形式
机械控制
电液控制
数字控制
一般数控机床
加工中心
时间(h)
4
8
16
32
表3-2主轴承温度和温升℃
轴承形式
温度
温升
轴承形式
温度
温升
滑动轴承
≤60
≤30
滚动轴承
≤70
≤40
八、试运转常见故障及其消除
1.试车故障
(1)发热。
温度急剧升高,温升或最高温度超过规定值,甚至出现冒烟现象。
发热部位有轴承、滑动摩擦导轨、气缸、齿轮箱等运动部位及绕组线圈、油、水和气体介质。
(2)震动。
机身和运动部位产生超过正常允许的振幅值。
表现在转轴轴承座、机身或外壳等处。
用手触摸、检验棒测听或仪器检测,有明显异常感觉。
(3)噪声。
运动部分内部或管道内部发出异常的噪声,听觉有明显刺激。
用噪声分贝计测量,其分贝值大大超过允许值。
(4)异常响声。
内部发生撞击声、冲击声、摩擦沙沙声。
用检验棒在外部侧听油明显感觉,甚至能直接听到这些异常声响。
(5)爬行和冲击运动。
此种故障发生在滑动摩擦面的导轨上,表现为运动部连续,有时快、有时慢,甚至短暂停止和突然前进。
(6)压力异常变化。
气压、油压、水压突然急剧降低或增高,可从压力指示变化、控制仪表报警及物流量的变化中发现。
(7)油液产生大量泡沫。
从油箱中可观察到泡沫的存在,严重时大量带油液的泡沫外溢,给油点给油不稳定等。
(8)突然发生泄漏。
外部泄漏可直接观察到;内部泄漏从指示仪表或工作状态可作判断,压力表有明显压降。
(9)齿轮崩牙。
可听到突然的金属折断声,传动出现周期性的异常声响。
(10)其他故障。
如手操作或机构操纵不发生运动、抱轴、打滑、变形、拉伤、出力不足等。
2.故障产生的一般原因
机械设备试车中出现故障。
由于设备的结构不同、工作性质差异大、试车重点部位不同,出现的故障会各不相同。
但是,发生故障的原因却基本相似,一般试车中出现故障主要的原因有:
间隙调整不合理,紧固件连接不牢或松动,齿轮啮合不良,润滑不良,内部不清洁及有异物,弹簧压力调整不当,调整找中不良,试车负荷过大,结构设计不合理和零部件加工精度达不到要求等。
以上这些故障原因通常来自于三个环节:
设计方法的原因、制造装配方面的原因、安装调试和操作方面的原因。
一般情况下以最后一个环节的因素居多,也是我们分析、研究、消除的重点。
下面将各环节可能存在的影响因素分别加以说明,供分析参考。
(1)设计方面。
主要有结构设计存在不足处;设计技术参数不当;元件选配不合理,选材不尽合理,设计的精度和间隙存在问题等。
(2)制造装配方面。
加工精度存在问题;装配配合不当;材料代用欠妥;加工工序遗漏;零件发生了变形等。
(3)安装、调试、操作方面。
主要有找正对中有问题、间隙调整不合理,连接不牢固或松动,组装装配不当,拧紧力不均匀产生变形,内部有异物、系统内不清洁,油压油量调整不符合要求,操作不当或失误等。
3.机床设备安装调试中常见典型故障分析及处理举例
当出现故障时,要运用掌握的理论知识、实践经验,结合安装调整时的实况及记录、设备技术文件资料的数据,进行综合分析。
分析时要仔细、全面,对非影响因素逐步排除。
故障产生的原因确认要慎重、客观,并结合检查情况,来确定主要原因。
现列举几种故障产生的原因,供分析时参考(见表3—3)。
表3—3设备安装调试中常见典型故障原因分析及处理
故障现象
原因
处理方法
轴承发热
轴瓦与轴颈配合不良,如间隙过小或过大,接触斑点和面积不良等
重新装配,调整轴瓦和轴颈间的间隙
润滑不良,如油量过少或太多,油质不好,粘度过稠,油液中有水分或溶解有大量空气,进油温度过高等
用规定的润滑油,控制用量
如震动过大、负荷过大、操作不当(未经过从低速到高速,从低负荷到高负荷的过程),轴绕度变形过大,热膨胀造成的影响或轴瓦松动等
按规定进行操作,如轴变形过大,应从新更换轴
振动
原因有转子动、静不平衡,同轴度调整不良,配合间隙过大,连接不牢固或松动,垫铁未垫实,发生干摩擦、液压油的脉冲流动,管道连接不当,外振源引起等
垫铁未垫实应在试运行前检查清楚,如果是配合不良,应从新调整安装
噪声和异常声响
由于运动件精度未达到标准,配合件发生相对移动,运动构件与固定件发生碰撞或摩擦,连接件松动或断裂,内部有异物等。
此外,如气缸内进入油和水、活塞松动、气缸余隙太小等,介质发生紊流也能发出噪音
气缸内进入油和水用空气吹出,活塞松动、气缸余隙太小应从新调整
压力异常变化
发生了泄漏,调整装置松动、内部发生了泄漏,出现了堵塞,进油进水口位置低,吸管过高或存在空气,压缩机排气阀漏气、入口阻力大,活塞和活塞环泄漏、密封损坏或不当等
清洗设备并更换破损设备零部件
爬行和冲击
导轨间隙太小,润滑油量太少发生干摩擦,液压油压力低或有泄漏,系统中有空穴现象,操作不当出现液压冲击等
调整导轨间隙,增加润滑油量
油液产生大量泡沫
油液中如混有大量空气,则会使油液产生泡沫。
空气由系统不严密处进入,或由吸油管进入,如吸油管太高,插入液面太浅,进油和回油无隔离板且距离太近;油泵安装位离油液面太高、油的粘度大、吸油管太细、油泵转速过快、滑阀动作速度过快造成过大的真空,使油液中溶解的空气析出等
检查油管有无泄漏,如有泄漏更换油管,调整油管位置