橡胶产品成型调机技术教材资料.docx
《橡胶产品成型调机技术教材资料.docx》由会员分享,可在线阅读,更多相关《橡胶产品成型调机技术教材资料.docx(44页珍藏版)》请在冰豆网上搜索。
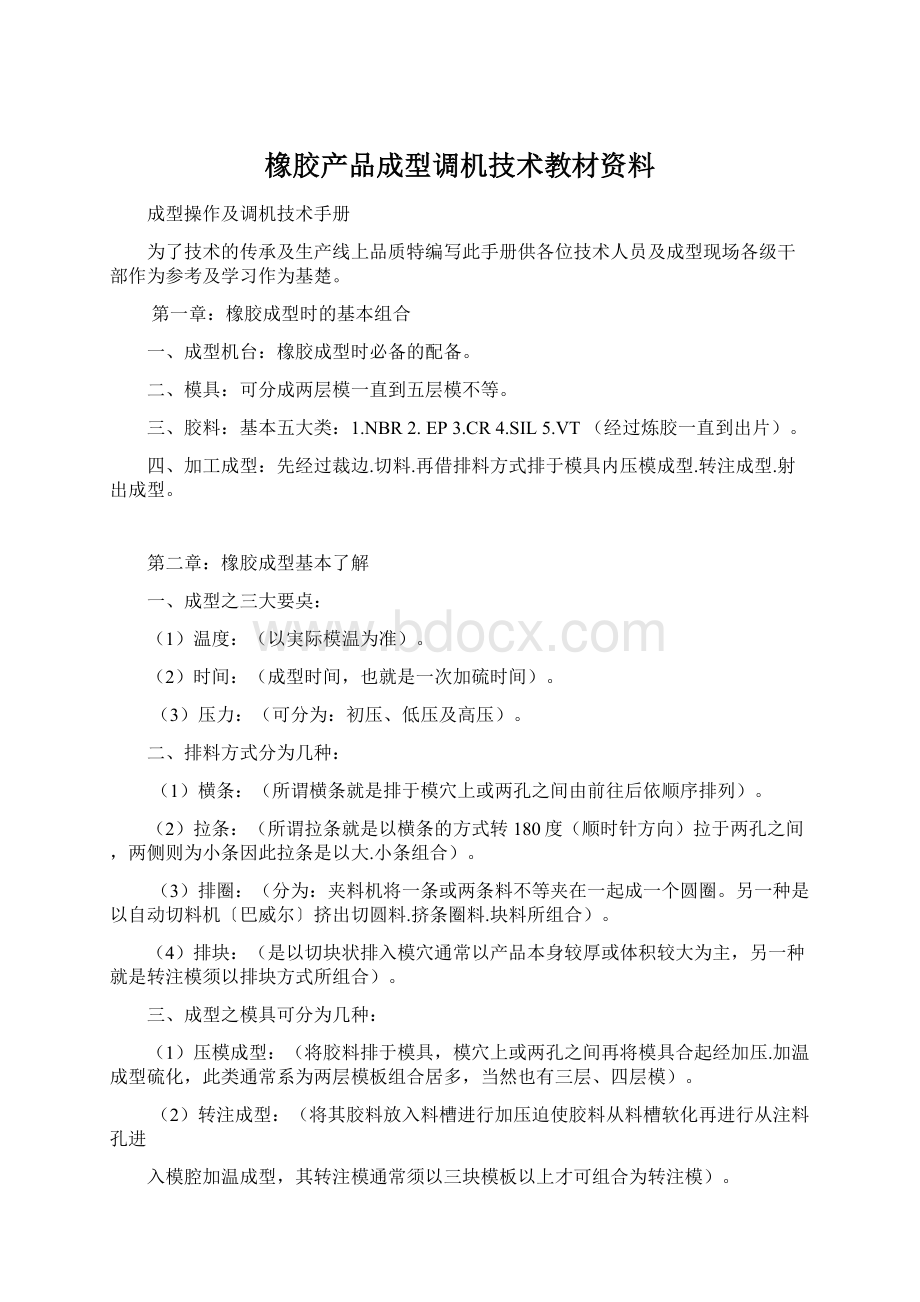
橡胶产品成型调机技术教材资料
成型操作及调机技术手册
为了技术的传承及生产线上品质特编写此手册供各位技术人员及成型现场各级干部作为参考及学习作为基楚。
第一章:
橡胶成型时的基本组合
一、成型机台:
橡胶成型时必备的配备。
二、模具:
可分成两层模一直到五层模不等。
三、胶料:
基本五大类:
1.NBR2.EP3.CR4.SIL5.VT(经过炼胶一直到出片)。
四、加工成型:
先经过裁边.切料.再借排料方式排于模具内压模成型.转注成型.射出成型。
第二章:
橡胶成型基本了解
一、成型之三大要奌:
(1)温度:
(以実际模温为准)。
(2)时间:
(成型时间,也就是一次加硫时间)。
(3)压力:
(可分为:
初压、低压及高压)。
二、排料方式分为几种:
(1)横条:
(所谓横条就是排于模穴上或两孔之间由前往后依顺序排列)。
(2)拉条:
(所谓拉条就是以横条的方式转180度(顺时针方向)拉于两孔之间,两侧则为小条因此拉条是以大.小条组合)。
(3)排圈:
(分为:
夹料机将一条或两条料不等夹在一起成一个圆圈。
另一种是以自动切料机〔巴威尔〕挤出切圆料.挤条圈料.块料所组合)。
(4)排块:
(是以切块状排入模穴通常以产品本身较厚或体积较大为主,另一种就是转注模须以排块方式所组合)。
三、成型之模具可分为几种:
(1)压模成型:
(将胶料排于模具,模穴上或两孔之间再将模具合起经加压.加温成型硫化,此类通常系为两层模板组合居多,当然也有三层、四层模)。
(2)转注成型:
(将其胶料放入料槽进行加压迫使胶料从料槽软化再进行从注料孔进
入模腔加温成型,其转注模通常须以三块模板以上才可组合为转注模)。
(3)射出成型:
(属于一种半自动成型须以射出专用机台才可加工,以人工取料将料裁成寛约6~7公分左右的长条状,料厚尽量不超过6mm以上,再将胶料放入,入料口内机台会自动将料铰入储料管内进行加温,再从射料管射入模腔称为射出成型,其模具组合两块板以上”。
*以上二.三奌如有不清楚的地方请见附图:
(1~6)
四.成型机可分为几种:
(1)油压成型机:
吨数由50吨到750吨不等依须要而定甚至1000吨。
(2)射出成型机.射出机分两种:
目前海堡公司为300吨(NBR.CR.VT.EP.HNBR等
黑色料为主依所须要而订制甚至500吨亦可。
另一种机型为SIL射出机
(3)油封专用成型机:
目前海堡没有此类机台,千慈总公司才有这类机台。
*以上油压.射出成型机依需求可装置前顶装置属于运用在三层模板以上所使用,目前前顶装置可分3RD及4RD也就是说可以顶两块中板及直接在机台上以顶具脱模的设计。
第三章:
生产前之基本条件
一、在生产前所须的各项条件均须先经过相关的单位先行试模确认至各项文件制定发行。
二、试模前的基本注意事项包括模具检查:
(1)检查模具上各个配件是否有异样。
(合页是否损坏,螺丝是否松动,导销是否变型下陷)。
(2)空模时将其模具上升查看上升到位时是否得当(上模板不可直接接触到机台上热板)。
(3)调整适合试模之胶料的温度、时间及压力。
(4)量测适当的料长。
(5)模温的量测。
三、试模过程中基本注意事项:
(1)测试每条料所须之料重(先以一条料试料重)。
(2)料重测试0K后再排整模料(适时的调整料重)。
(3)第三模排料前先再次确认温度无误后排料。
(4)第三模量测尺寸、硬度须取最少5个产品(四个角落及中间一个先以手动量测或以量具先行
量测)同时试模人员须将产品先自行试拔毛边是否ok再继续下面动作。
(5)尺寸确认无误后再行作业所须其余所须生产的模数。
(6)试模完成后进行毛边拆除、自动投影机量测、二次加硫后再送自动投影机量测二次加硫后尺寸。
(7)相关人员(工程部:
生技课)判定(尺寸.外观.硬度)是否可投产。
(8)再由相关部门(工程部)订定各项作业指导书,以利正式投产时减少问题发生及让其作业顺畅。
*以上6.7.8.点主要为新模试模所须之动作其余1-5点为可量产之型号须注意。
*试模过程中须将各项注意重奌作好记录,包括是否需脱模辅助工具,包括脱模剂种类。
排料辅助工具等等须在正式投产前予以制作完成。
第四章:
各种材质之温度设定(实际模温)
以现有海堡公司各种材质温度设定作以下序述供参考:
修改前之加硫时间.温度(无要求之加硫条件)修改后之加硫时间.温度
NBR:
一.NBR40:
最高实际模温可设定到165度+-5。
NBR:
0字头=180度/+5-0时间40秒以上
二.NBR50:
最高实际模温可设定到168度+-5。
1字头=180度/+5-0时间45秒以上
三.NBR60:
最高实际模温可设定到175度+-5。
2字头=180度/+5-0时间50秒以上
四.NBR70:
最高实际模温可设定到182度+-5。
3字头=175度/+5-0时间70秒以上
五.NBR80:
最高实际模温可设定到178度+-5。
4字头=170度/+5-0时间120秒以上
六.NBR90:
最高实际模温可设定到175度+-5。
CR:
一.CR40:
最高实际模温可设定到158度+-5。
CR:
0字头=180度/+5-0时间70秒以上
二.CR50:
最高实际模温可设定到165度+-5。
1字头=180度/+5-0时间90秒以上
三.CR60:
最高实际模温可设定到170度+-5。
2字头=180度/+5-0时间120秒以上
四.CR70:
最高实际模温可设定到178度+-5。
3字头=178度/+5-0时间150秒以上
五.CR80:
最高实际模温可设定到175度+-5。
4字头=175度/+5-0时间180秒以上
以上CR材貭之温度为自炼胶(长泓胶须再加3-5度)。
EP:
一.EP40:
最高实际模温可设定到165度+-5。
EP:
0字头=180度/+5-0时间60秒以上
二.EP50:
最高实际模温可设定到168度+-5。
1字头=180度/+5-0时间75秒以上
三.EP60:
最高实际模温可设定到175度+-5。
2字头=180度/+5-0时间90秒以上
四.EP70:
最高实际模温可设定到180度+-5。
3字头=178度/+5-0时间120秒以上
五.EP80:
最高实际模温可设定到178度+-5。
4字头=175度/+5-0时间150秒以上
六.EP90:
最高实际模温可设定到175度+-5。
EP过氧0~2字头180度;150秒,170秒,200秒
以上EP材貭之温度(过氧材质须以178度以上)。
3字头175度,220秒,4字头170度,240秒以上
SIL:
一.SIL40:
最高实际模温可设定到158度+-5。
SIL:
0字头=180度/+5-0时间60秒以上
二.SIL50:
最高实际模温可设定到163度+-5。
1字头=175度/+5-0时间70秒以上
三.SIL60:
最高实际模温可设定到165度+-5。
2字头=175度/+5-0时间90秒以上
四.SIL70:
最高实际模温可设定到168度+-5。
3字头=170度/+5-0时间130秒以上
五.SIL80:
最高实际模温可设定到168度+-5。
4字头=165度/+5-0时间160秒以上
以上为SIL材质之温度视产品结构及毛边情况作适时的调整。
VT:
一.VT50:
最高实际模温可设定到165度+-3。
VT:
0字头=175度/+5-0时间90秒以上
二.VT60:
最高实际模温可设定到175度+-3。
1字头=175度/+5-0时间120秒以上
三.VT65:
最高实际模温可设定到175度+-3。
2字头=175度/+5-0时间150秒以上
四.VT70:
最高实际模温可设定到180度+-3。
3字头=170度/+5-0时间200秒以上
五.VT75:
最高实际模温可设定到180度+-3。
4字头=170度/+5-0时间250秒以上
六.VT80:
最高实际模温可设定到180度+-3。
七.VT90:
最高实际模温可设定到175度+-3。
以上为VT材貭之温度(对于4字头以上之型号最高不可超过168度因为温度过高时
较会产生准线裂开造成产品不良,一定要特别注意)。
HNBR:
一.HNBR60:
最高实际模温可设定到165度+-3。
HNBR:
0字头=180度/+5-0时间150秒以上
二.HNBR70:
最高实际模温可设定到170度+-3。
1字头=180度/+5-0时间170秒以上
三.HNBR80:
最高实际模温可设定到170度+-3。
2字头=180度/+5-0时间190秒以上
四.HNBR90:
最高实际模温可设定到165度+-3。
3字头=175度/+5-0时间220秒以上4字头=170度/+5-0时间240秒以上
以上为HNBR材质之温度(须对该材温度时间严加控制易有毛边的产生及准线裂开
的不良的产生)。
PA:
一.PA60:
最高实际模温可设定到175度+-5以上。
二.PA70:
最高实际模温可设定到180度+-5以上。
PA材质较容易产生流痕也就是说容易产生结合不好导致的痕迹应特别注意胶料的厚度须作调整
※生产到185度部分配方甚至温度可以上
PU:
一.PU70:
最高实际模温可设定到178度+-3。
二.PU90:
最高实际模温可设定到170度+-3。
该材质在生产过程中须严格控制料重因此材质在毛边去除是以毛边机作业料重不可太重。
(PU材质通常都不作二次加硫,因为二次加硫后产品容易老化)
NR:
NR材貭温度不可过高,最高不可超过175+-5(规格外)。
以0-Ring线径越细温度越低,甚至须降到150度左右
第五章:
生产过程的异常种类及分析
生产过程中经常产生的异常为下列几种:
一、包风:
(1)排气不良
(2)胶料含油量过多
(1).而排气不良又可分析为以下几种原因:
(1)-1.模具未钻排气孔,(加钻排气孔)。
(1)-2.模具设计不良,(加强修改模具)。
(1)-3.生产过程中洒水不均.要求洒水或不洒水(未做或多做)洒水动作,(加强作业督导)。
(1)-4机台参数设定不当,如:
排气距离太大或太小,排气次数太多或太少次,(改变参数)。
(2).胶料含油量过多:
胶料配方须作调整改善尤其是低硬度胶料最为常见油性包风。
二、起泡:
(1)排气不良
(2)一次加硫时间不足(3)胶料混炼不均(4)胶料静置时间不足。
(1)排气不良与包风之
(1)排气不良分析的4小点奌相同差异不大。
(2)加硫时间不足分析为以下几奌:
(2)-1.经验不足设定错误(加强教育)。
(2)-2.前次生产资料卡填写错误,(加强宣导)。
(2)-3.胶料促进剂太少(秤错),(加长加硫时间或加高温度或退回炼胶单位重新处理)。
(2)-4.排料作业人员排料速度太慢导至模温失温,(加强督导作业)。
(2)-5.机台电热管故障导至温度失控,(立即通知工务课检修)。
(3)胶料混炼不均:
须重新处理,(打薄)。
(4)胶料静置时间不足:
加长静置熟成期(己加促进剂须再重新处理)。
三、不熟:
(1)一次加硫时间不足
(2)模具失温(3)温度设定过低。
(1)一次加硫时间不足与第二大奌之
(2)加硫不足分析5小点相同,差异不大。
(2)模具失温第二大奌之
(2)-4,
(2)-5相同。
(3)温度设定过低与第二大奌之
(2)-1,
(2)-2相同。
四、破皮分析原因如下:
(1)模具生产过程中己产生大量模污,(将模具拉下清洗)。
(2)胶