YSG南锚碇底板填芯施工方案4.docx
《YSG南锚碇底板填芯施工方案4.docx》由会员分享,可在线阅读,更多相关《YSG南锚碇底板填芯施工方案4.docx(43页珍藏版)》请在冰豆网上搜索。
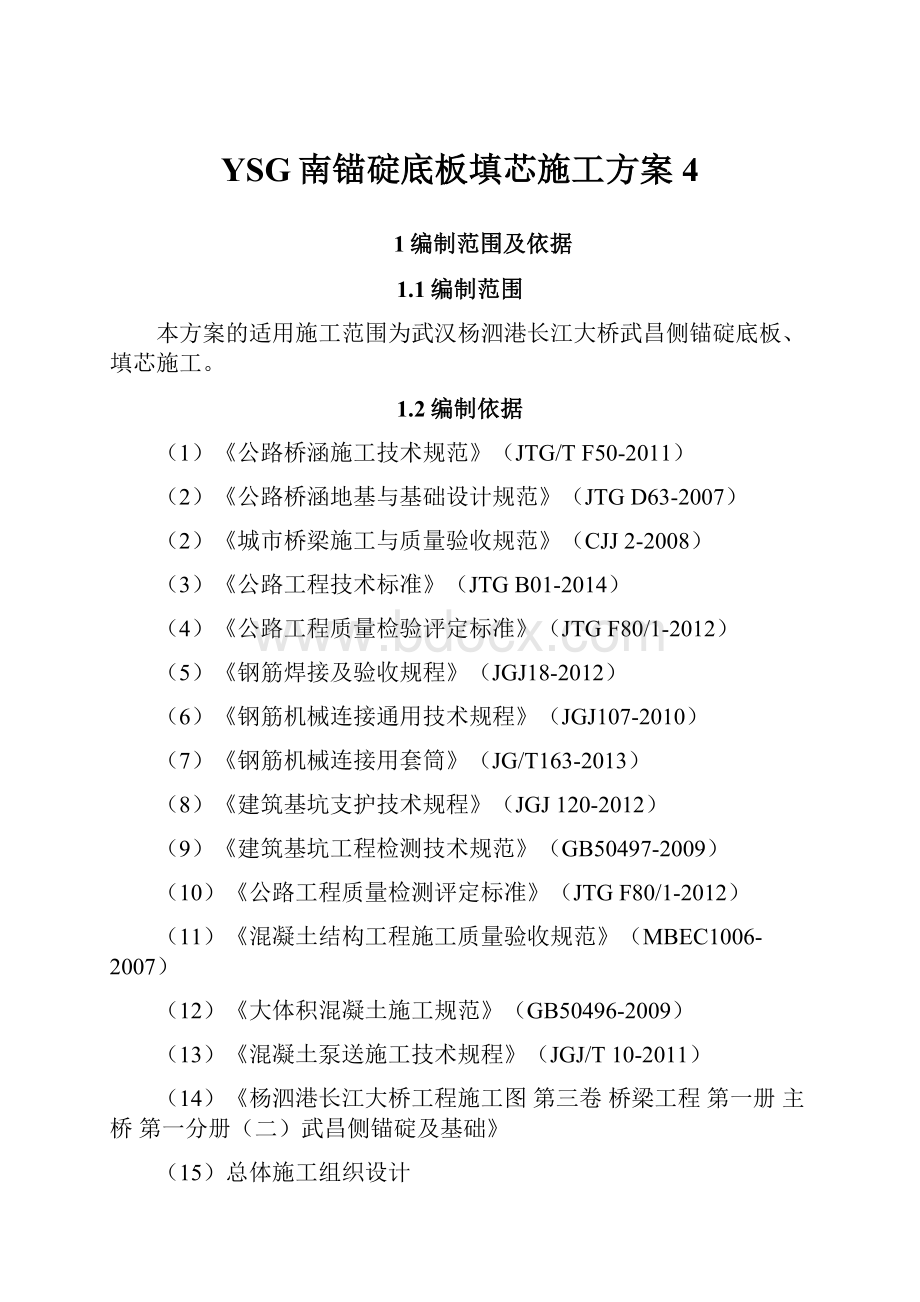
YSG南锚碇底板填芯施工方案4
1编制范围及依据
1.1编制范围
本方案的适用施工范围为武汉杨泗港长江大桥武昌侧锚碇底板、填芯施工。
1.2编制依据
(1)《公路桥涵施工技术规范》(JTG/TF50-2011)
(2)《公路桥涵地基与基础设计规范》(JTGD63-2007)
(2)《城市桥梁施工与质量验收规范》(CJJ2-2008)
(3)《公路工程技术标准》(JTGB01-2014)
(4)《公路工程质量检验评定标准》(JTGF80/1-2012)
(5)《钢筋焊接及验收规程》(JGJ18-2012)
(6)《钢筋机械连接通用技术规程》(JGJ107-2010)
(7)《钢筋机械连接用套筒》(JG/T163-2013)
(8)《建筑基坑支护技术规程》(JGJ120-2012)
(9)《建筑基坑工程检测技术规范》(GB50497-2009)
(10)《公路工程质量检测评定标准》(JTGF80/1-2012)
(11)《混凝土结构工程施工质量验收规范》(MBEC1006-2007)
(12)《大体积混凝土施工规范》(GB50496-2009)
(13)《混凝土泵送施工技术规程》(JGJ/T10-2011)
(14)《杨泗港长江大桥工程施工图第三卷桥梁工程第一册主桥第一分册
(二)武昌侧锚碇及基础》
(15)总体施工组织设计
2工程概况
2.1概述
杨泗港长江大桥位于鹦鹉洲大桥上游3.2公里、白沙洲大桥下游2.8公里处,从汉阳国博立交,沿汉新大道跨鹦鹉大道和滨江大道,在武昌侧跨八铺街堤、武金堤至八坦立交,全长约4.134公里,主桥采用主跨1700m加劲钢桁梁双层悬索桥,悬吊跨度为465m+1700m+465m。
主塔基础为沉井基础,锚碇基础采用地连墙结构型式。
图2-1主桥立面布置
2.1.1锚碇概况
锚碇为重力式锚碇,采用外径98m,墙厚1.5m的圆形地连墙加环形钢筋混凝土内衬结构。
锚碇基础由地连墙、帽梁、内衬、底板及填芯混凝土组成。
锚碇基础顶高程为24.0m(帽梁顶标高),基础底面高程为-15.0m,地连墙底面高程为-42.0m,基础深约39.0m,地连墙总深度66.0m,地连墙墙底穿过基底下圆砾土层及粉砂层,嵌入坚硬状黏土约3m。
如图2-2。
图2-2南锚碇结构示意图
2.1.2底板概况
锚碇底板为钢筋混凝土结构,截面为R=44.5m的圆形,厚7.0m,底面标高为:
-15.0m,顶面标高为:
-8.0m。
底板采用C30微膨胀混凝土浇筑,合计约43282.9m³;钢筋采用HRB400钢筋,合计约825.38t。
根据设计要求,锚碇基坑开挖完成后根据基底的情况在其上浇筑不小于0.3m厚度的C20垫层混凝土。
2.1.3填芯概况
为增大结构自重,平衡主缆竖向拉力,提高基础结构的整体性,底板到地连墙顶采用混凝土进行填充。
填芯混凝土与内衬、底板和帽梁间需设置连接钢筋。
填芯为顶面R=45.5m、底面为R=44.5m的变截面圆形混凝土结构,填芯采用C30混凝土浇筑,合计约200320m³;钢筋采用HRB400钢筋,合计约171.07t。
2.2主要工程数量
表2-1主要工程量数量表
序号
部位
名称
规格
单位
数量
备注
1
底板
钢筋
HRB400
t
825.38
/
2
混凝土
C30微膨胀
m3
43282.9
/
3
冷却管
Φ50×4mm
t
200
/
4
填芯
钢筋
HRB400
t
171.07
/
5
混凝土
C30
m3
200320
/
6
冷却管
Φ50×4mm
t
890
/
7
垫层
混凝土
C20
m³
1865.4
/
8
架立钢筋
HRB400
t
2314
/
3施工方案
3.1总体施工方案
3.1.1概述
底板施工:
基坑开挖完成后,进行基底清理整平,然后将坑内设备用130t履带吊吊出,并浇筑垫层混凝土。
底板共分三层进行施工,从下至上,第一层厚度为3m,第二层厚度为1.5m,第三层厚度为2.5m;每一层均分为三块进行浇筑。
上下层浇筑时应将施工缝错开至少1m,层间结合面应拉毛处理。
分块示意如下图所示:
图3-1锚碇底板、填芯浇筑分块示意图(单位:
mm)
填芯施工:
在底板施工完成后,对底板顶面进行拉毛,并根据锚固系统安装进度进行架立钢筋、冷却管、测温元件和应力计的安装。
填芯混凝土分11层进行浇筑,从下至上,第1~6层厚度为3m,第7层厚度为2.5m,第8~10层为3m,第11层厚度为2.5m。
底板和填芯分层布置见图3-2。
图3-2锚碇底板和填芯分层布置图(单位:
mm)
分层工程量表,见表3-1
表3-1锚碇底板和填芯浇筑方量表(单位:
mm)
序号
项目
分层高度
分块
分块面积
浇筑方量(m³)
备注
1
垫层
0.3m
/
6217.99
1865.4
C20
2
底板第1层
3m
下游
2141.63
6424.89
C30
中间
1937.87
5813.61
上游
2141.63
6424.89
3
底板第2层
1.5m
下游
2228.12
3342.18
C30
中间
1765
2647.5
上游
2228.12
3342.18
3
底板第3层
2.5m
下游
2141.63
5354.08
C30
中间
1937.87
4844.68
上游
2141.63
5354.08
4
填芯第1~6层
3m
下游
2141.63
6424.89
C30
中间
1937.87
5813.61
上游
2141.63
6424.89
5
填芯第7层
2.5m
下游
2200.81
5502.03
C30
中间
1960.1
4900.25
上游
2200.81
5502.03
6
填芯第8~10层
3m
下游
2260.78
6782.34
C30
中间
1982.32
5946.96
上游
2260.78
6782.34
7
填芯第11层
2.5m
下游
2260.78
5651.95
C30
中间
1982.32
4955.8
上游
2260.78
5651.95
合计
垫层
0.3m
/
/
1865.4
C20
底板、填芯
39m
/
/
243602.9
C30
3.1.2总体工艺流程
图3-3工艺流程图
3.2施工组织
3.2.1人员组织
(1)项目部管理人员
表3-2管理人员责任分工表
编号
职务(分工)
人数
人员名称
职责
1
项目经理
1
李永旗
总指挥
2
总工程师
1
韩胜利
技术主管
3
分管领导
1
崔岚岭
生产、进度管理
4
架子队长
1
金伟
现场负责人、施工安排
5
现场技术负责人
1
陆占锋
技术控制,工艺落实
6
质量负责
1
吴吉祥
质量监督、管理
7
安全负责
1
王全科
全面负责施工安全
8
试验室
1
熊林森
试验检测
9
工程部
2
申世靖、周文健
技术方案、测量监控
10
物资保障
1
郭奇
保障物资及时供应
11
机械保障
1
鄂鹏
机械供应、维修保障
12
应急救援组
10
梁涛等
紧急情况处理
13
后勤组
5
方志丹等
后勤服务
(2)施工作业人员
表3-3主要施工人员及施工任务统计表
序号
作业队名称
人数
施工任务
1
钢筋加工、安装作业人员
60
底板、填芯钢筋加工安装
2
冷却水管安装作业人员
30
底板、填芯模板安装
3
模板安装作业人员
30
底板、填芯模板安装
4
混凝土浇筑作业人员
45
底板、填芯混凝土浇筑
5
场地清理人员
10
开挖场地清理、文明施工
6
基坑监控作业人员
10
基坑安全监控
3.2.2施工机械
锚碇底板、填芯施工设备主要包括塔吊、汽车吊、地泵、和布料杆等。
具体详见表3-4。
表3-4主要机械设备配置计划一览表
序号
名称
规格型号
单位
数量
备注
1
塔吊
臂长70m
台
2
2
汽车吊
25t
台
1
3
地泵
HBT80
台
4
4
布料机
臂长24m
台
4
5
插入式振动器
ZN50
台
30
6
通用钢结构
加工设备
/
套
2
7
通用钢筋
加工设备
/
套
2
8
变压器
630KW
台
2
9
发电机
250kw
台
1
10
混凝土罐车
8m3
辆
9
3.2.3施工工期
(1)工期安排
武昌侧锚碇底板、填芯施工工期为:
2017年1月1日至2017年12月13日,共计347天,具体工期安排为:
1基底清理,垫层浇筑:
2017年1月1日-1月9日,共需9天。
2底板施工:
1月10日-3月27日,共77天(含春节假期)。
分为三层,第一层施工需要21天,第二层施工需要15天,第三层施工需要21天。
③填芯施工(含锚固系统安装):
3月28日-12月13日,共261天。
填芯分为11层进行施工,每层21天,共需231天;锚固系统安装共需30天。
(2)工期分析
①基底开挖至设计标高并清基后,浇筑垫层混凝土进行基底封闭,垫层厚度为30cm。
基底清理3天,浇筑分为三块施工,单块垫层浇筑及养护2天,共需9天。
②垫层浇筑完毕后,分层分块施工底板(竖向分为3层,由下往上分别为第一层3m,第二层1.5m,第三层2.5m,水平分为3块)。
先分块进行底板钢筋绑扎,冷却水管和测温元件安装,然后进行模板安装,布料机管线及基础布置。
底板分为三层,每一层分为三块进行浇筑,底板第一层浇筑方量为18654m³,考虑交叉施工,第一块钢筋绑扎5天,第二块钢筋绑扎5天,第三块钢筋绑扎5天,第三块混凝土浇筑6天,共需21天;底板第二层浇筑方量为9327m³,考虑交叉施工,第一块钢筋绑扎4天,第二块钢筋绑扎4天,第三块钢筋绑扎3天,第三块混凝土浇筑4天,共需15天;底板第三层浇筑方量为15545m³,考虑交叉施工,第一块钢筋绑扎5天,第二块钢筋绑扎5天,第三块钢筋绑扎5天,第三块混凝土浇筑6天,共需21天;故底板施工共需77天(含春节放假20天)。
③底板施工完毕后进行填芯施工和锚固系统安装,填芯分为11层,由下往上第1~6层高3m,第7层高2.5m,第8~10层高3m,第11层高2.5m。
填芯第1~6层,每层浇筑方量为18654m³,填芯第7层,浇筑方量为15896.3m³,填芯第8~10层,每层浇筑方量为18654m³,填芯第11层浇筑方量为16251.5m³,考虑交叉施工,单层需21天,11层共需231天;考虑锚固系统安装,净增工期为30天。
故填芯施工共需261天。
3.2.4材料物资
施工中所用的主体结构材料和辅助材料均需满足技术规范要求。
进场前,用于永久结构的材料、设备均需有关材料质量保证书。
施工中所用的砂、石、水泥、水、粉煤灰、外加剂、钢筋、钢板、电焊条等。
进场后均必须按规范要求进行全面复检,不合格的材料坚决不允许用于本工程,检验结果报监理工程师审核。
材料、设备进场后,按要求分类、分批存放,堆码整齐,设防晒雨棚、支垫一定高度,做到“上盖下垫”。
特别是水泥、外加剂和电焊条等做好防潮措施并注意有效使用日期。
4施工步骤及要求
4.1底板施工
底板混凝土分为3层,第一层厚度为3m,第二层厚度为1.5m,第三层厚度为2.5m。
混凝土分块要求:
①.浇筑分块线不得在同一垂直面上;
②.上下两层浇筑分块线需间隔1.0m以上。
具体分层分块见下图。
图4-1底板分层示意图(单位:
mm)
图4-2底板第一层分块示意图(单位:
mm)
图4-3底板第二层分块示意图(单位:
mm)
图4-4底板第三层分块示意图(单位:
mm)
根据分块要求,底板每层分为上游,中间,下游三块,均以先浇筑下游侧,后浇筑上游侧,最后浇筑中间为原则。
底板第一层上下游两块进行浇筑时,布料机采用混凝土扩大基础埋设钢管桩进行设置。
混凝土基础平面尺寸为4m×4m,高度3m,钢管桩埋设在混凝土中深3m,悬伸高度为0.5m。
每浇筑一层底板(或填芯),接高一次钢管桩,布料机底座循环利用。
具体布置见下图:
图4-5底板第一层下游侧浇筑布置图(单位:
mm)
图4-6底板第一层上游侧浇筑布置图(单位:
mm)
图4-7底板第一层中间块浇筑布置图(单位:
mm)
图4-8底板第二层下游侧浇筑布置图(单位:
mm)
图4-9底板第二层上游侧浇筑布置图(单位:
mm)
图4-10底板第二层中间块浇筑布置图(单位:
mm)
每次混凝土浇筑的理论方量见表4-1。
表4-1底板混凝土浇筑数量表
序号
层数
分层高度
部位
单位
数量
备注
1
第一层
3m
下游侧
m3
6424.89
C30
2
中间
m3
5813.61
3
上游侧
m3
6424.89
4
第二层
1.5m
下游侧
m3
3342.18
C30
5
中间
m3
2647.5
6
上游侧
m3
3342.18
7
第三层
2.5m
下游侧
m3
5354.08
C30
8
中间
m3
4844.68
9
上游侧
m3
5354.08
4.1.1底层土方开挖
第12层内衬施工完成且强度达到80%后,进行最后一层土方开挖,土方开挖到底时预留10~20cm采用人工开挖整平,避免扰动土体。
基坑开挖到底层时,坑内降水管井的排水效率将逐步降低并逐渐失去作用,因此只能通过设集水坑进行明排水以保证基坑相对干燥的施工条件。
根据坑内集水情况,在坑内设置若干集水坑,放置缠有滤网的过滤器,在过滤器内设大扬程污水潜水泵将水抽排出坑。
4.1.2坑底清理及垫层浇筑
土方开挖完成后,修整基底面,清理基底土渣。
用风镐对底板范围内的地连墙和内衬墙面进行清理、凿毛,并凿出内衬与底板的横向钢筋连接接器。
基底清理完成后,浇筑垫层混凝土,垫层采用地泵下料浇筑。
垫层混凝土浇筑厚度根据基底面土质情况确定。
垫层混凝土标号为C20,强度达到50%方可进行下步施工。
4.1.3底板钢筋安装
根据设计图纸,锚碇底板钢筋材质均为HRB400,钢筋规格有Φ25mm、Φ20mm、Φ16mm三种。
底板钢筋加工在钢筋加工车间加工成型,由塔吊吊入基坑内安装。
底板钢筋分两次绑扎成型,第一次绑扎底板底面钢筋、环向钢筋及架立筋,第二次绑扎顶面钢筋。
(一)钢筋原材料进场检查验收
钢筋材料进场,按照以下要求进行检查:
①.进场证明
A.每批进场的钢筋需提供轧制钢筋的轧制和处理方法,规格,牌号;
B.每批钢筋中的炉罐号,化学成分和力学性能的证明;
C.出厂质量合格证书和质量检验报告单。
②.外观质量检查
A.无有害的表面缺陷,例如无裂纹、机械损伤及剥离层等;
B.用钢丝刷刷过的截面最小尺寸符合规定允许偏差。
③.钢筋标识
在检验以前,每批钢筋应具有易识别的标签,标签上标明制造商试验号及批号,或者其他识别该批钢筋的证明。
④.取样试验
进场后的钢筋每批(同品种、同等级、同截面尺寸、同炉号、同厂家生产的每60t为一批)内按规定截取试样,进行拉力试验、冷弯试验;超过60t的部分,每增加40t(或不足40t的余数),增加1个拉伸试验试样和1个弯曲试验试样。
检验不合格的钢筋不得在工程中使用。
(二)钢筋的保护和存放
①.进场钢筋验收后,应按材料的不同种类、型号、规格、等级及生产厂家分别堆存,不得混杂,并设立识别标志。
②.钢筋统一存放在钢筋加工车间内,钢筋放置在平台或垫木上,离地面高度30cm以上,并在顶上覆盖塑料布,使其不受机械损伤或锈蚀;
③.钢筋安装时,表面应无灰尘、有害的锈蚀、松散锈皮、油漆、油脂或其他杂质。
(三)钢筋的加工
钢筋的加工成型施工要求:
①.钢筋严格按设计图纸所示的形状进行加工成型。
②.按设计图纸要求加工钢筋弯钩,直角弯曲直径不小于4d(d为钢筋直径),平直部分长度不小于10d。
③.下料前将钢筋调直并清理污锈,钢筋保证平直,无局部弯折。
钢筋笼下料后采用切割机将钢筋的两头切平,使切口端面应与钢筋轴线垂直,不得有马蹄形或挠曲,以保证钢筋连接顺利进行。
(四)钢筋的连接
底板内主筋和与内衬横向连接筋(直径分别为Φ25mm,Φ20mm)采用直螺纹套筒连接,其他钢筋采用焊接接头连接。
钢筋连接施工要求:
①.滚轧直螺纹接头
钢筋直螺纹套筒连接应满足《钢筋机械连接通用技术规程(JGJ107-2010)》、《滚轧直螺纹钢筋连接接头(JG163-2004)》的规定,
施工和质量检验要求如下:
A.加工要求
加工钢筋丝头时,应采用水溶性切削润滑液。
钢筋丝头的螺纹应与连接套筒的螺纹相匹配,公差带应符合《滚扎直螺纹钢筋连接接头》(JG163-2004)的要求,可选用6H。
经加工后的丝头应牙形饱满,牙顶宽超过0.6mm,秃牙部分累计长度不应超过一个螺纹周长,外形尺寸包括螺纹直径及丝头长度应满足产品设计要求。
B.丝头检验
自检合格的丝头,以一个工作班加工的丝头为一个检验批,随机抽取10%,且不少于10个。
C.套筒检验
套筒选用在厂家定制,套筒出厂应成箱包装,包装箱外应标明产品名称、型号、规格和数量,制造日期和生产批号、生产厂名等,包装箱内必须附有产品合格证及质保书。
连接套筒检验:
套筒的内螺纹尺寸检验按连续生产的套筒每500个1个检验批,每批按10%抽检,不足500个也按一个检验批计算。
套筒表面应无裂纹或其他肉眼可见的缺陷,外形尺寸包括套筒内螺纹直径及套筒长度不应超过一个螺纹长度,套筒两端应加塑料保护塞,并应进行表面防锈处理。
D.钢筋连接接头拧紧力矩检验
外观质量自检合格的钢筋连接接头应由现场质检员随机抽样进行单向拉伸检验同一施工条件下采用同一材料的同等级同型式同规格接头以连续生产的500个为一个检验批进行检验和验收不足500个的也按一个检验批计算。
每个检验批的钢筋连接接头,在现场随机抽取15%,且不少于75个接头进行外观和拧紧力矩检验。
拧紧力矩值应不小于300N·m。
E.连接接头力学性能检验
外观质量自检合格的钢筋连接接头应由现场质检员随机抽样进行检验,同一施工条件下采用同一材料的同等级同型式同规格接头以连续生产的500个为一个检验批进行检验和验收不足500个的也按一个检验批计算。
对接头的每一个验收批,必须在工程结构中随机截取3个试件作单项拉伸试验。
F.接头设置
纵向受力钢筋接头应相互错开,钢筋机械连接接头错开长度按照35d计算(d为被连接钢筋中较大钢筋直径)。
同一连接区段长度内接头百分率不得大于50%。
分块处连接钢筋布置图如下:
图4-11分块处钢筋接头布置图(单位:
mm)
②.搭接焊接头
搭接焊接头宜采用双面焊缝,如条件困难时方可采用单面焊。
搭接焊接头施工要求:
A.焊缝长度
采用搭接焊时,两钢筋搭接端部应预先折向一侧,两接合钢筋的轴线应保持一致;采用帮条焊接时,帮条采用与主筋相同的钢筋。
焊接接头的焊缝长度,双面焊不小于5d,单面焊不小于10d。
焊接接头与钢筋弯曲处的距离不应小于10d,且不宜位于构件的最大弯矩处。
B.外观检查
焊缝表面平整、不得有较大的凹陷、焊瘤,焊缝接头处不得有裂纹。
检查不合格的接头经修整补强后,再次进行检查,检查合格方可使用。
焊接接头的允许偏差应符合《钢筋焊接及验收规程》JGJ18-2012的要求。
C.机械试验
在同一台班内,由同一焊工完成的300个同牌号、同直径钢筋焊接接头应作为一批。
当同一台台班内焊接的接头数量较少时,可在一周之内累计计算;累计仍不足300个接头时,应按一批计算。
力学性能检验时,应从每批接头中随机切取6个接头,其中3个做拉伸试验,3个做弯曲试验。
(五)钢筋加工质量验收标准
钢筋加工质量验收标准见表4-2。
表4-2钢筋加工允许偏差及检验方法
序号
名称
允许偏差(mm)
检验方法
1
受力筋全长
±10
尺量
2
弯起钢筋各部分弯起尺寸
±20
3
箍筋各部分尺寸
±5
(六)钢筋安装
钢筋安装施工要求:
根据设计图检查下层预留搭接钢筋的位置、规格、数量、长度,确保无误。
安装的钢筋品种、级别、规格和数量必须符合设计要求。
钢筋加工验收后进行安装。
安装前,先搭设架立骨架,以此为支撑,在其上绑扎钢筋骨架。
钢筋绑扎顺序:
一般情况下先长轴后短轴,由一端向另一端依次进行。
操作时按图纸要求划线、铺钢筋、绑扎、成型。
在多排钢筋之间,必要时可垫入短钢筋头或其他适当的钢垫,但短钢筋头或钢垫的端头不得伸入混凝土保护层。
钢筋接头位置应相互错开,预埋件在达到设计的要求后加以固定,以确保其预埋钢筋在浇筑混凝土后位置不变。
保护层垫块采用C30水泥砂浆垫块。
垫块与钢筋应绑扎牢固,位置和数量符合规范和设计要求,且尽量分布均匀。
钢筋保护层垫块侧面和底面的垫块数量不应少于4个/m2。
(七)钢筋安装质量验收标准见4-3。
表4-3钢筋安装及钢筋保护层厚度允许偏差及检验方法
序号
名称
允许偏差(mm)
检查方法及频率
1
受力钢筋排距
±5
尺量:
每构件检查2个断面
2
同一排中受力钢筋间距
±20
3
箍筋、横向水平钢筋间距
±10
尺量:
每构件检查5-10个间距
4
钢筋骨架尺寸
长
±10
尺量:
按骨架总数30%抽查
宽、高或直径
±5
5
弯起点位置
±20
尺量
6
钢筋保护层厚度
±10
尺量:
沿模板周边检查8处
4.1.4预埋件的安装
底板施工需要预埋的预埋件种类有:
①接地系统预埋件:
按照《杨泗港长江大桥工程施工图第三卷桥梁工程第一册主桥第一分册
(二)武昌侧锚碇及基础》的要求,由电工主导对接地系统进行安装测试。
②定位支架预埋件:
按照设计分公司《武昌侧锚碇定位支架预埋件图》的要求进行埋设。
③布料机预埋件:
按照工程部出具的工程事项通知单的要求进行预埋。
④泵管支架预埋件:
按照工程技术部出具的通知单要求进行预埋。
4.1.5冷却水管安装
为排散大体积混凝土内的水化热,在底板内安装冷却管,每层冷却管用直径Φ50mm,壁厚4mm的普通钢管,按1m的间距往返排绕,相邻两层互相垂直;冷却管每隔300~500m设一个进、出水口,通过竖直连接管接高至底板顶与水泵、排水管相接。
底板第一层布置2层冷却管,第二层布置1层冷却管,层间距1.0m~1.5m,第三层布置1层冷却管。
冷却管采用橡胶管连接,接头严密,进出口妥善防护,避免进入水泥砂浆或其它杂物,安装完毕应进行通水检试验,保证管路通畅。
进水口或出水口处要安装水表,以计量单位时间内降温水流量。
降温水管在混凝土浇筑中应防止堵塞。
且在向管内泵水时,每根管道均要用单独的水泵,以防止单根管内不畅而造成管内循环水量过小。
4.1.6