脆性材料去除机理差异性分析DOC.docx
《脆性材料去除机理差异性分析DOC.docx》由会员分享,可在线阅读,更多相关《脆性材料去除机理差异性分析DOC.docx(13页珍藏版)》请在冰豆网上搜索。
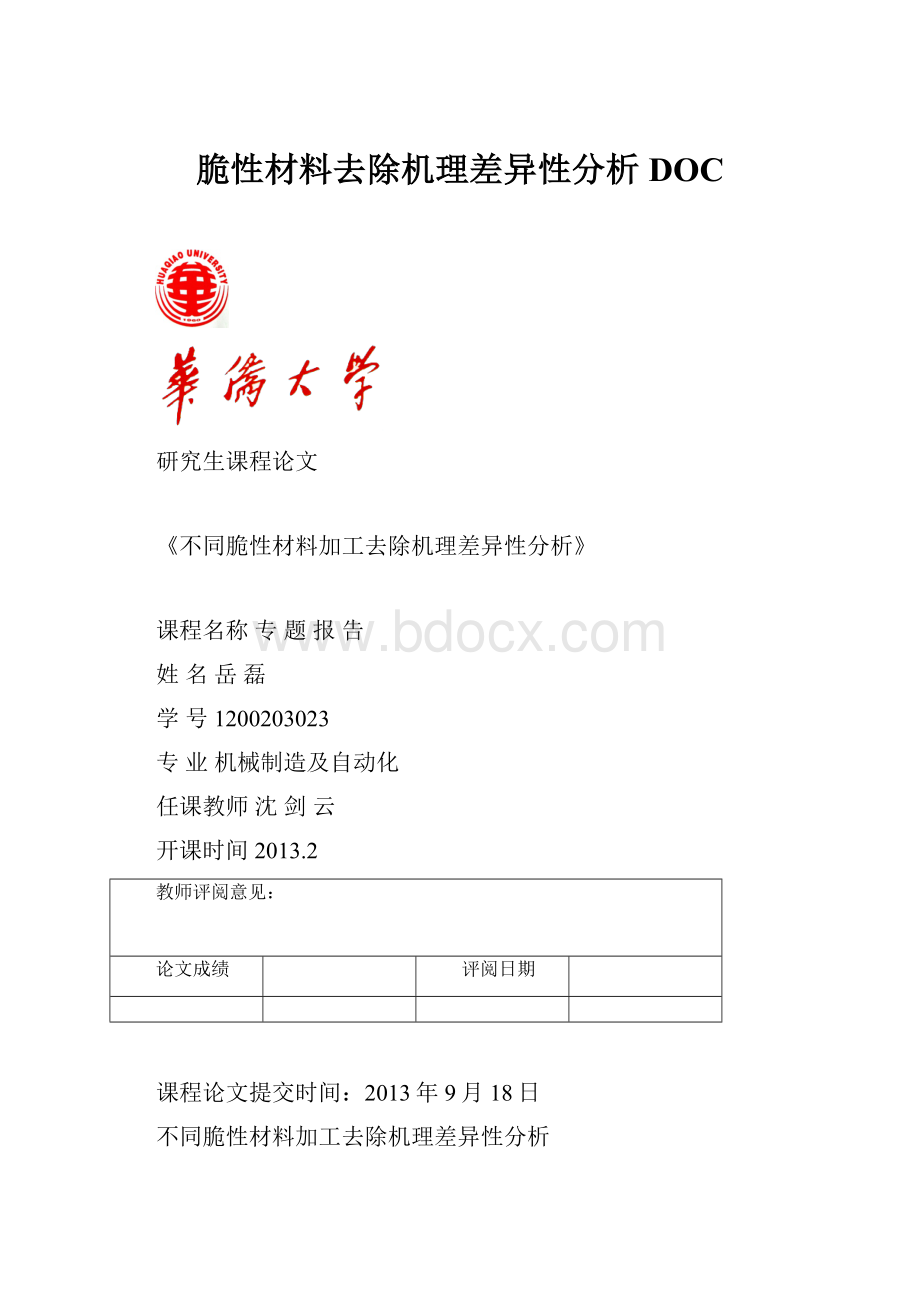
脆性材料去除机理差异性分析DOC
研究生课程论文
《不同脆性材料加工去除机理差异性分析》
课程名称专题报告
姓名岳磊
学号1200203023
专业机械制造及自动化
任课教师沈剑云
开课时间2013.2
教师评阅意见:
论文成绩
评阅日期
课程论文提交时间:
2013年9月18日
不同脆性材料加工去除机理差异性分析
摘要:
脆性材料的共性是具有高强度、高硬度、高脆性、耐磨损和腐蚀、隔热、低密度和膨胀系数及化学稳定性好等特点,是一般金属材料无法比拟的。
然而,脆性材料具有的低塑性、易脆性破坏、微裂纹以及加工方法选择不当会引起工件表面层组织的破坏的缺点,使得脆性材料的加工十分困难。
本文综述了三种脆性材料:
岩石、结构陶瓷、硅片在不同条件下的去除机理,总结了三种材料去除机理的差异性。
关键字:
去除机理岩石结构陶瓷硅片延性域去除
脆性材料由于具有独特性能,而得到迅速的应用。
特别是,近几年脆性材料正广泛地用于光学、计算机、汽车、航空航天、化工、纺织、冶金、矿山机械、能源和军事等领域。
脆性材料的共性是具有高强度、高硬度、高脆性、耐磨损和腐蚀、隔热、低密度和膨胀系数及化学稳定性好等特点,是一般金属材料无法比拟的。
但是通常脆性材料坯料必须经过机械加工才能应用。
然而,脆性材料具有的低塑性、易脆性破坏、微裂纹以及加工方法选择不当会引起工件表面层组织的破坏的缺点,使得脆性材料的加工十分困难[1]。
因此,如何实现脆性材料高质量加工表面是目前先进制造技术领域一个重要的研究主题,去除机理的研究是一个重要的方向。
到目前为止,国内外很多学者对典型脆性材料的加工去除机理进行了研究。
但是,不同脆性材料在不同的加工方式下的去除机理有很大的差异,本文综述了典型脆性材料:
岩石、结构陶瓷、硅片的去除机理,并进行了差异性分析。
1、岩石的去除机理研究
岩石的加工一般采用金刚石工具。
金刚石工具去除石材的过程,实际上可以看作是大量的具有微刃的金刚石磨粒不断地切削岩石的过程。
不同的岩石由于形成原因及条件的不同,在矿物成分、晶体粒度、晶体形状和组织结构等方面具有很大的差异,同时由于受力状态的不同对岩石的强度特性也有很大的影响,因此岩石的断裂、加工过程是一个非常复杂的力学行为[2,3]。
另外工具表面上金刚石磨粒的晶形、磨损状态、出刃高度及其在节块表面分布的不同使锯切花岗石过程的研究变得更加复杂了。
一般对岩石去除机理的研究大都采用单颗金刚石磨粒(或其它刀具)划擦和以压痕理论为基础的磨削实验研究方法。
金刚石工具表面上出露的金刚石磨粒一般都具有较大的负前角,由于磨粒晶形、磨损状态、出刃情况的不同,各磨粒具有不同的工作状态。
对于出刃高度较低、顶部磨钝程度较大的具有较大的刃口钝圆半径的金刚石磨粒,通常把它对岩石的切削过程看成球形压头的压痕侵入作用过程。
虽然用压头的压痕侵入过程来解释金刚石工具锯切石材过程具有很大的不足,但其基本原理仍具有一定的代表性。
1.球形压头的作用
前苏联学者奥斯特洛乌什柯[4]把球形压头在脆性或塑性岩石的破碎过程划分为如下几个阶段。
图1.球形压头加载时脆性岩石破碎发展过程
①弹性变形阶段—当作用在球形压头上的载荷P不大时(约不到0.4岩石抗压强度),岩石只产生弹性变形,在a,b接触点产生两组微细裂隙,当载荷P取消时,裂隙也随之消失。
见图1(a)。
②压皱压裂变形—当载荷增加至0.4-0.6岩石抗压强度时,a,b两组裂隙向深部发展,汇交于o点,形成aob角锥体,自a,b处又产生ac,be两组裂隙,此阶段也称疲劳破碎阶段。
载荷P取消后,裂隙已不能消失,故称压皱压裂阶段。
a为锥顶角,岩石越硬,锥顶角越小。
见图1(b)。
③体积破碎阶段—载荷P继续增加,超过岩石抗压强度,球体与岩石接触而产生压碎变形,ao,bo两组裂隙自o点,裂隙串通,Aoa,Bob剪切体崩离,ac,be两组裂隙自aob主压力被压碎,c点向自由面A,B方向扩展,即体积破碎阶段。
见图1(c)。
④过程重复—体积破碎以后,球形压头落在o点,破碎坑内留少量磨屑,在载荷P的作用下,又开始前述过程。
2.单颗金刚石磨粒切削岩石过程模型
M.Meding在细致研究了单颗粒金刚石切削石灰岩、大理岩和花岗岩后,在改进前人提出的机理模型的基础上,提出了如图1-11所示的模型[5]。
图2单颗粒金刚石切削岩石的模型
该模型指出金刚石磨粒切削岩石的过程存在三个变形区:
①第一变形区(磨粒前方及其附近区域).在磨粒前方,负前角刀刃产生的压应力使岩石产生了剪切破坏,破裂的花岗岩颗粒飞出磨粒前部,并向磨粒两旁挤压,挤压程度与负前角大小、矿物晶粒及矿物的组织解理所处的方位状态有关。
②第二变形区(在磨粒下方).对于石灰岩和大理岩而言,在磨粒与岩石的接触范围内的工件表面上,形成了一个塑性变形区域,工件表面呈光滑状。
这是由压应力形成的,在形成连续切屑时,可以从清除切屑后显示出的工件材料本体上看出这点。
强烈塑性变形层只有几微米厚,第二变形区不仅在工件表面上产生薄层变形,而且剥裂了本体层材料。
因此,切屑是通过塑性变形和受压的薄层材料强化产生的。
对于花岗岩,在磨粒和岩石接触区的高压以及高温作用下,也会产生局部塑性变形。
③第三变形区(在磨粒后方)在与磨粒紧邻的地方,产生了一些宏观细小岩石颗粒组成的尾巴,还不清楚这些颗粒是否是集中在磨粒下方的已破碎的切屑或至少部分是碎屑。
根据实验结果推断,这是由于磨粒划过后,划痕表面的应力由压应力转化为拉应力所致。
随着划伤深度增大,磨粒后方出现的颗粒切屑数量增加,其大小均在微米范围之内。
该模型还反映了岩石加工表面在金刚石磨粒挤压作用下的压实层在磨粒的前下方起着静水应力作用,传递部分切削载荷,但未能表明压实层形成规律及其对锯切表面形成过程的影响。
由前述的岩石断裂屈服理论和金刚石的破岩机理可以看出,金刚石工具在不同的切削条件下切削花岗石时,脆性断裂的崩碎行为在岩石破碎过程中占主导地位,但是同时只要受力情况符合一定的条件,仍然有塑性变形区存在。
这一些情况都可以从我们用金刚石工具切削加工后的岩石表面形貌的扫描电镜图中得到验证[6]。
文献[7,8]对锯切花岗石过程中不同矿物成分的去除形式进行了观察和分析,指出花岗石中云母的解离最完整,最易去除,其次是正长石和斜长石,而石英几乎不发生解理断裂,因此最难切割。
石英含量越高,金刚石磨损越剧烈;正长石的含量若明显偏高,则锯切过程相对较难进行;粒度粗的花岗石较之粒度细的花岗石,在相同的锯切条件下,更难以发生解理断裂。
2、结构陶瓷的去除机理研究
结构陶瓷作为一种新型的高性能陶瓷材料,是具有机械功能、热和尖端科技领域。
随着科学技术特别是材料科学的进步和现代高新技术应用领域对新型材料需求的不断提高,大大促进了工程结构陶瓷材料的研究发展,同时也掀起了加工技术领域的一场革命。
国内外很多学者对工程陶瓷的加工机理也进行了研究。
陶瓷材料磨削加工过程中的材料去除机理一般都有脆性断裂和塑性变形两种形式,即使是在大切深缓进给磨削的情况下也会发现塑性耕犁的痕迹,当脆性材料的磨削深度小于其临界磨深时,能实现脆性材料的塑性域磨削,以获得超光滑的加工表面[9,10]。
脆性断裂的材料去除方式是通过气相、晶界和裂纹的成形和扩展、剥落及碎裂[11]等方式来完成的。
而塑性变形去除方式则类似于金属材料磨削中的切屑形成过程,其中涉及了磨粒的滑擦、耕犁和切屑形成过程,材料是以剪切变形方式去除[12]。
在陶瓷材料磨削机理的研究中大多应用压痕断裂力学模型或切削加工模型为基础,结合在这些模型下的材料弹塑性变形和裂纹形成扩展的特征来解释各种形式的材料去除机理。
1.压痕断裂力学模型
尖压头对结构陶瓷的作用过程[13]如图3。
当尖压头在载荷P作用下以某一缓慢速度压入脆性材料表面,压应力的作用使压头下部的试件材料发生非弹性流动。
载荷不大时,卸载后,压痕保留,即非弹性流动结果保留。
对于韧性好的某些脆性材料,压头侧面会出现类似于切削塑性金属材料那样的隆起现象,但并不十分显著。
尽管这种压痕流动是许多原因造成的,如密度、嵌杂等,但可以将这种非弹性流动称之为显微塑性流动。
若压痕是通过材料的显微塑性流动形成,则作用于压头上的载荷P与压痕特征尺寸2a有如下关系:
P=ξ*H*a2
式中:
ξ—压头几何因子,对于维氏压头,ξ=2,H—脆性材料硬度。
图3.压头的压痕断裂力学模型
图4Vickers压痕裂纹的形成过程
裂纹产生的临界载荷值与陶瓷材料的硬度及断裂韧性是密切相关的。
对于陶瓷磨削过程,只要磨粒上所受的力超过这一临界值,工件就会产生侧向裂纹,陶瓷材料便以断裂方式去除,而当载荷低于此临界值,侧向裂纹就不会产生,金刚石磨粒与工件界面产生塑性流动[14]
2.切削加工模型
压痕断裂力学模型可以成功地解释磨削加工中陶瓷材料的裂纹形成机制并为延性域磨削提供了理论基础,然而压痕断裂力学模型中压头与试件间的作用是静态的,而磨削过程中金刚石磨粒切削工件过程是动态的过程,因此人们就在压痕断裂力学模型的基础上发展了切削加工模型,也就是移动压头划擦陶瓷试件的模型。
图5.切削加工模型
切削加工模型的研究通常是采取单颗粒金刚石磨削硬脆材料工件形成划痕来解释磨削机理,在研究中常常要用到扫描电子显微镜、透射电子显微镜或其它一些显微观测方法。
在对不同切削深度的划擦过程及划痕观察中可以发现在磨削过程中,当磨粒的切深较小时,陶瓷材料在金刚石磨粒的挤压和划擦下产生塑性流动,表面只有塑性变形引起的隆起;而随着切深加大,在划擦后沟痕表面可以同时观察到鳞状裂纹和塑性流动,且材料的去除多为细小颗粒,这表明磨粒作用在陶瓷工件上的载荷超过了陶瓷材料裂纹产生的临界载荷,这时就会在加工表面产生中央裂纹、侧向裂纹,侧向裂纹也会扩展到材料表面,使部分材料以崩碎形式去除,而大部分工件材料是在磨粒的前刀面压挤作用下以裂纹扩展形成碎屑的形式去除。
而随着切深的进一步加大,裂纹的扩展随之加剧,并导致大规模的铲除和破碎。
3.脆性去除机理
陶瓷材料磨削过程中的脆性去除主要有晶粒去除、材料剥落、脆性断裂和晶界微破碎等几种方式。
在晶粒去除过程中,材料是以整个晶粒从工件表面上脱落,这种材料去除机理发生的同时伴有材料的剥落去除方式,它是磨削过程中所产生的横向和径向裂纹的扩展而形成局部剥落去除[15]。
而磨粒前下方的材料破碎则是表面圆周应力和剪切应力分布引起的各种形式脆性断裂破坏的结果[16]。
陶瓷材料加工表面的观察也表明在陶瓷磨削过程也存在着晶界微破碎和材料晶粒状位错的去除方式。
在磨削过程中,单个金刚石颗粒与陶瓷工件的接触时产生一个晶界微裂纹的损伤区,而材料去除则是通过这些晶界微破碎处的位错方式来完成的[17]。
邓朝晖教授等学者将微破碎去除解释为粉末化去除机理[18],磨削过程中磨粒引起的流体静态压应力所包围的局部剪切应力场所引起的晶界和晶间微破碎的结果,陶瓷材料晶粒因粉末化去除被碎裂成更细的晶粒,并形成粉末域。
通过磨削实验和显微观测,当磨粒切削深度在亚微米级时,磨削后陶瓷工件表面微粉碎而产生的粉末堆积而不是塑性变形,且无宏观断裂,工件表面上粉碎层材料间的结合比主体材料松散,是磨削过程接触弧区内的磨粒与工件间的静压应力使其重新被压实在工件表面。
4.塑性变形去除
从材料的宏观性能分析,结构陶瓷等脆性材料经过一定的弹性变形后即发生断裂,而在微观情况下,这些材料都会产生一定的塑性变形,这从陶瓷材料在压头载荷作用下先形成一个局部的塑性区也得到了印证[19]。
因此在一定的加工条件下,任何脆性材料能够以塑性流动的方式被去除,而压痕断裂力学模型也预测了产生横向裂纹临界载荷[20],在低于这一临界载荷加工条件时,材料去除将以塑性变形去除为主。
而在达到临界切削深度后,最初的塑性流动不断地转变为脆性断裂状态,法向力在塑性区域里随切削深度呈线性增大。
而在脆性区域里,法向力波动且并未增大多少,这表明了切削力和加工能量主要消耗于塑性流动[21]利用陶瓷等脆性材料的塑性变形去除的特点,寻找各种材料出现塑一脆性转变的临界磨粒切削深度,并在加工系统中应用高刚度高精度机床或者使用超细粒度金刚石砂轮控制磨粒切深,实现塑性域磨削(或者延性域磨削),从加工结果看,在塑性区域被磨的试件呈现出更好的表面质量及强度。
3、硅片去除机理研究
单晶硅片在加工和应用过程中都经历机械作用即接触加载,这种加载过程往往伴随着塑性变形、微观/宏观断裂、材料晶体结构的变化以及接触体之间的机械化学作用。
由于研究接触表面层的结构特性比较困难,并且试验量很大,会造成材料的浪费。
因此,很多学者通过单晶硅片的压痕、划痕及单点金刚石加工来研究单晶硅片机械加工表面层的损伤机理及材料去除机理[22]。
1.单晶硅片的压痕分析
李东升等对单晶硅片不同压痕载荷卜的压痕形貌和压痕边缘的微裂纹进行了观测[23]。
研究指出载荷较小时,由于靠近压头和单晶硅表面接触区有拉应力存在,压痕边缘向内凹入,没有明显的降起线;而当载荷较大时,在压痕回复区域内有脆性同心裂纹以及蝶翅形变形区产生。
当接触区卜的拉应力最大值超过临界值时,在压痕对角线边缘形成中位裂纹,中位裂纹的形成使接触区的应力场分布复杂化,从而导致卸载后不仅有近似理想的弹性接触应力场,还会有以拉应力分量为主的残余应力场出现。
弹性接触应力场和残余应力场的迭加使中位裂纹沿着择优取向的晶向或者沿着与主张应力分量正交的轨迹扩向自由表面并与之相切于压痕的两侧。
最终,随着载荷的进一步增大,中位裂纹的扩展呈半圆状剖面的几何形状,构成从压痕棱角扩展开来的表面径向裂纹。
当裂纹产生堆集并与试样表面交截时,会导致部分表面材料的剥落。
福州大学张琼等用TEM研究了单晶硅压痕微裂纹的形成与扩展,指出压痕应力场使高脆性单晶硅发生滑移方式的塑性变形,从而表现出形态各异的位错组态:
位错圈、堆垛层错、压杆位错、扩展不全位错及位错偶等[24]。
2.单晶硅片的划痕分析
L.C.Zhang不不同载荷下的金刚石划痕进行了TEM检测[25]。
表明载荷较小时有非晶面产生,随着载荷增大,有大量的位错和面缺陷产生,当变形超过极限或者划痕过程中产生的拉应力超过硅片的强度极限时,微裂纹产生从而释放变形产生的弹性能,材料会发生脆性断裂。
Y.Gogotsi等的研究指出[26]:
当划痕宽度超过5um时裂纹产生,材料脆性去除产生较大的碎片,如果切深进一步加大,硅片将会破碎。
不同形状的划痕器产生微裂纹的临界切削深度不同,锥形划痕器的临界切削深度比球形划痕器的临界切削深度大。
在无裂纹区域,球形划痕的深宽比比锥形划痕的深宽比小,这是由于球形划痕的尖端比较钝的原因。
锥形划痕时划痕边缘有较明显的堆积,这表明单晶硅在微米级的高塑性。
3.硅片延性域磨削的材料去除机理
硅片延性域磨削的材料去除机理为:
在高温或高压条件下,硅也能表现出流动性质即塑性,在刀具刃圆半径很小且切削深度很小的情况下,刀具尖端作用于工件表面形成局部静水压力区域,当静水压力达到10-13Gpa,有效剪切应力达到剪切强度极限,产生塑性变形(此时拉应力值没有达到抗拉强度极限不足以产生微观裂纹),从金刚石晶体结构(Si-I相)转变为金属结构(Si-II相),体积减小22%。
当切削深度小于某一临界值,塑性区域边界处的拉应力小于断裂强度,不足以产生微细裂纹,剪切应力使磨粒前下方的材料产生塑性流动进而形成切屑,从而实现延性域加工。
加工后的表面不存在微观裂纹,仅由晶格错乱层和位错层组成,而且损伤层深度很浅,一般在几百纳米以下[27]
4、三种材料去除机理的差异性分析
(1)岩石的去除过程实际上是大量的具有微刃的金刚石磨粒不断地切削岩石的过程。
岩石的矿物成分、晶体粒度、晶体形状和组织结构的巨大差异造成了去除机理的复杂性。
总的来说,岩石的去除机理包括:
第一变形区的剪切和挤压作用使岩石产生了弹性变形;第二变形区的细粒岩石层产生塑性变形,使该层岩石逐层剥落;在第三变形区划痕表面的应力由压应力转化为拉应力,拉应力使已经变细的岩石细粒从岩石本体去除,并随着随着划伤深度增大,进一步使岩石颗粒破裂,磨粒后方出现的颗粒切屑数量增加,将切屑排除,从而完成了整个去除过程。
在整个过程中,脆性断裂的崩碎行为一直中占主导地位,但是同时只要受力情况符合一定的条件,仍然有塑性变形区存在(如第二变形区)。
由于岩石每层的不同矿物成分不同,出现了解离现象。
并且花岗石中云母的解离最完整,最易去除,其次是正长石和斜长石,而石英几乎不发生解理断裂,因此最难切割。
粒度粗的花岗石较之粒度细的花岗石,在相同的锯切条件下,更难以发生解理断裂
(2)陶瓷材料磨削加工过程中的材料去除机理一般都有脆性断裂和塑性变形两种形式,当脆性材料的磨削深度小于其临界磨深时,能实现脆性材料的塑性域磨削。
脆性去除主要有晶粒去除、材料剥落、脆性断裂和晶界微破碎等几种方式。
磨削过程中所产生的横向和径向裂纹不断扩展使材料局部剥落;磨粒和陶瓷接触产生的晶界微破碎裂纹区和材料晶粒状位错完成了材料的最终去除。
当磨粒切削深度在亚微米级时,磨削过程接触弧区内的磨粒与工件间的静压应力使陶瓷表面的粉碎层重新被压实在工件表面。
在微观情况下结构陶瓷经过一定的弹性变形后随即发生塑性变形,并且在临界切削深度以下,主要去除方式以塑性去除为主。
(3)单晶硅的精密磨削过程存在4个明显的阶段:
脆性去除阶段、摩擦裂纹阶段、延性去除阶段和弹性接触阶段。
存在两个明显的脆性—延性转变:
由第一阶段到第二阶段,表面裂纹消失;由第二阶段到第三阶段,摩擦裂纹消失,进入完全的延性域切削阶段。
参考文献
[1]魏源迁.国外硬脆材料的最新加工技术.磨床与磨削,1997(4):
24-29.
[2]李远,黄辉,朱火明,徐西鹏.锯切不同花岗石过程中锯切力特征.金刚石与磨料磨具工程,2002,(4):
15-19
[3]李远,于怡青,徐西鹏.石制品光滑表面的形成及其光泽度与粗糙度的关系.珠宝科技.2002,
(2):
48-51
[4]徐湘涛.石材加工与金刚石工具.超硬材料.1992,
(1)
[5]M.Meding.BeschreibungdesprozeLigeschehensbeiderzerspanungvongesteinandvondessenbruch-mechanischemverhaltenunterbesondererberiicksichtigungderschallemissionsanalyse(Adescriptionoftheprocessesinthecuttingofrockandofitsfracture-mechanicsbehaviourwithparticularregardtotheanalysisofacousticemission).Doctoralthesis,TUHamburg-Harburg,1993.
[6]李远,黄辉,于怡青,徐西鹏.切磨过程中花岗石材料去除机理研究.矿物学报,2001,21(3):
401-405
[7]徐西鹏,骆灿彬.锯、磨过程中花岗石去除机理及其对锯切过程影响.金刚石与磨料磨具工程,1997,(5):
8-12
[8]李远.花岗石超大切深锯切机理与技术研究.华侨大学博士论文,2004.5
[9]陈明君,董申,李旦,张飞虎.脆性材料超精密磨削时脆转变临界条件的研究.[J]高技术通讯,2001
(2):
64-70
[10]陈明君,董申,李旦等,单晶硅脆性材料塑性域超精密磨削加工的研究,航空精密制造技术,2007,36
(2):
8一11
[11]B.Zhang,T.D.Howes,MaterialRemovalMechanismsinGrinding
Ceramics.AnnalsoftheCIRP,1994,43
(1):
30_5一308
[12]铁瑛,赵波,张波等.工程陶瓷材料精密磨削加工技术的新发展.[J]焦作工学院学报(自然科学版),2003,22(3):
217一220
[13]B.R.Lawn,M.V.Swain,MicrofracturebeneathPointIndentationin
BrittleSolids.JournalofMaterialsScience,1975,10:
113一122
[14]B.R.Lawn,A.G.Evans,D.B.Marshall,Elastic/PlasticIndentation
DamageinCeramics:
TheMedian/RadialCrackSystem,JournalofAmericanCeramicSociety,1980,63(9-10):
574一581
[15]T.M.A.Maksoud,A.A.MokbelandJ.E.Morgan,Evaluationofsurfaceandsub一surfacecracks:
ofgroundceramic.JournalofMaterialsProcessingTechnology,1999,88(1-3):
222一243
[16]H.P.Kirchner,DamagePenetrationatElongatedMachiningGrooves
inHot-PressedSi3N4.JournalofAmericanCeramicSociety,1984,67:
127一132
[17]唐修检,田欣利等.工程陶瓷边缘碎裂行为与机理研究进展.[J]中国机械工程,2010,(21):
14-120
[18]邓朝晖,张璧,孙宗禹等.陶瓷磨削材料去除机理的研究进展.[J]中国机械工程,2002,13(18):
1608一1611
[19]程军,巩亚东等.硬脆材料微磨削表面形成机理试验研究.[J]机械工程学报,2012,11(21):
190-197
[20]傅玉灿,张贝等.单颗磨粒切厚均匀化实现脆性材料延性域磨削技术.[J]南京航空航天大学学报,2012,10(5):
754-761
[21]邓朝晖,刘建等.纳米结构陶瓷涂层精密磨削的材料去除机理及磨削加工技术.[J]金刚石与磨料磨具工程,2003,12(6):
5-9
[22]张银霞.硅片加工损伤机理的压痕、划痕研究.[J]电子质量,2008,12:
44-47
[23]李东升.集成电路用直拉硅单晶力学性能.浙江大学博士论文,2001,5
[24]蔡传荣,张琼.单晶硅硬度压痕裂纹的特征.[J].电子显微学报1996,02:
562-565
[25][4]ZhangLC,ZarudiI.Towardsadeeperunderstandingofplastic
Deformationinmonocrystallinesilicon.InternationalJournalof
MechanicalSciences.[J],2001,43:
1985-1996.
[26]GogotsiY,ZhouG,KuSSetal.Ramanmicrospectroscopy
analysisofpressure-inducedmetallizationinscratchingofsilicon.[J]SemiconductorScienceTechnology.2001,16:
345-352
[27]霍凤伟.硅片延性域磨削机理研究.大连理工博士论文,2006,5