材料成形工艺基础复习提纲机电专业及近机专业.docx
《材料成形工艺基础复习提纲机电专业及近机专业.docx》由会员分享,可在线阅读,更多相关《材料成形工艺基础复习提纲机电专业及近机专业.docx(12页珍藏版)》请在冰豆网上搜索。
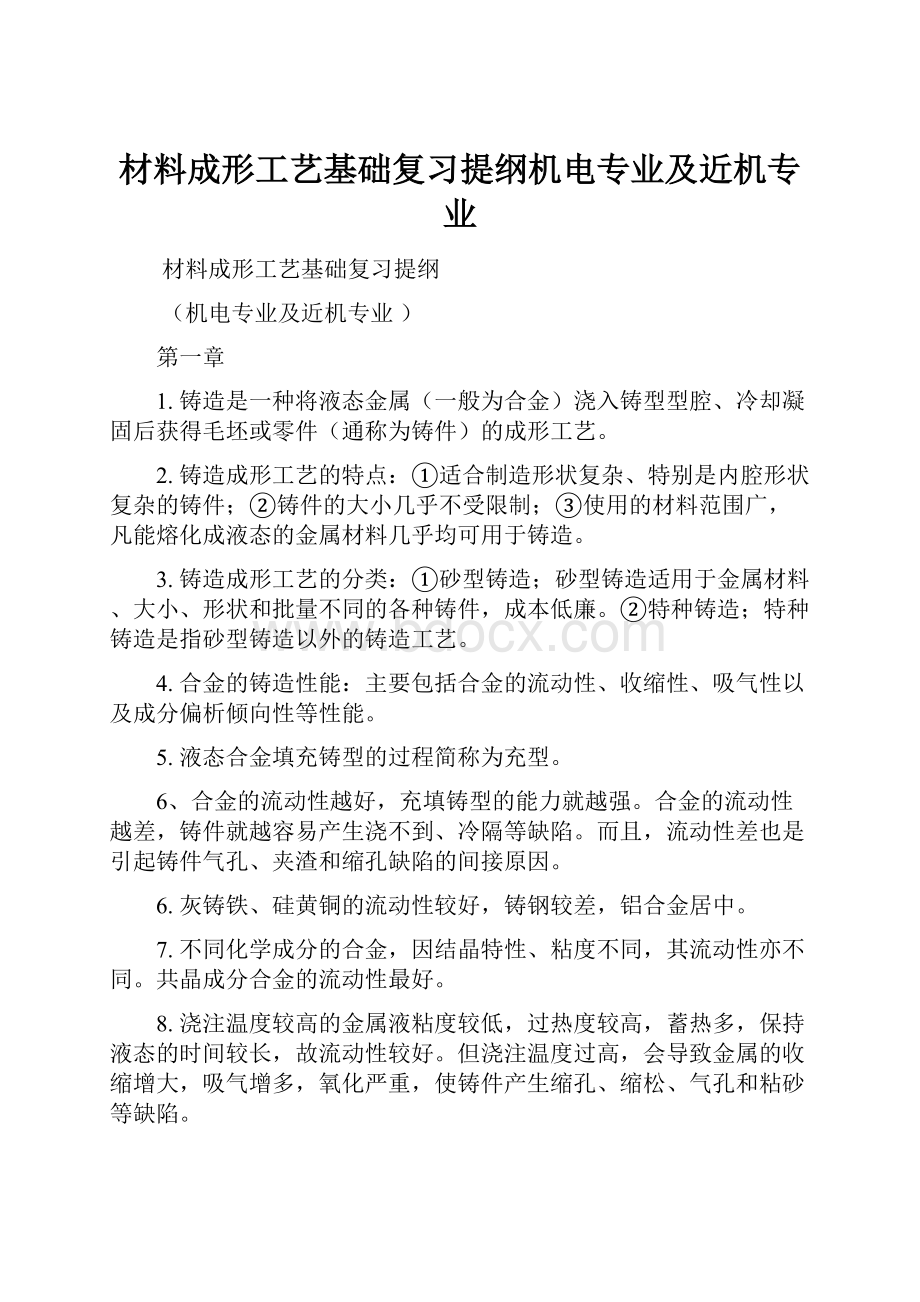
材料成形工艺基础复习提纲机电专业及近机专业
材料成形工艺基础复习提纲
(机电专业及近机专业)
第一章
1.铸造是一种将液态金属(一般为合金)浇入铸型型腔、冷却凝固后获得毛坯或零件(通称为铸件)的成形工艺。
2.铸造成形工艺的特点:
①适合制造形状复杂、特别是内腔形状复杂的铸件;②铸件的大小几乎不受限制;③使用的材料范围广,凡能熔化成液态的金属材料几乎均可用于铸造。
3.铸造成形工艺的分类:
①砂型铸造;砂型铸造适用于金属材料、大小、形状和批量不同的各种铸件,成本低廉。
②特种铸造;特种铸造是指砂型铸造以外的铸造工艺。
4.合金的铸造性能:
主要包括合金的流动性、收缩性、吸气性以及成分偏析倾向性等性能。
5.液态合金填充铸型的过程简称为充型。
6、合金的流动性越好,充填铸型的能力就越强。
合金的流动性越差,铸件就越容易产生浇不到、冷隔等缺陷。
而且,流动性差也是引起铸件气孔、夹渣和缩孔缺陷的间接原因。
6.灰铸铁、硅黄铜的流动性较好,铸钢较差,铝合金居中。
7.不同化学成分的合金,因结晶特性、粘度不同,其流动性亦不同。
共晶成分合金的流动性最好。
8.浇注温度较高的金属液粘度较低,过热度较高,蓄热多,保持液态的时间较长,故流动性较好。
但浇注温度过高,会导致金属的收缩增大,吸气增多,氧化严重,使铸件产生缩孔、缩松、气孔和粘砂等缺陷。
9.增大浇注压力显然可改善金属的流动性,常采用增加直浇道高度的方法或采用压力铸造、离心铸造工艺来增大浇注压力,提高金属的流动性。
10.合金在浇注、凝固直到冷却到室温的过程中体积或尺寸缩减的现象,称为收缩。
11.合金的收缩过程有三个阶段:
①液态收缩;②凝固收缩;③固态收缩。
合金的总收缩为上述三种收缩的和。
12.在常用铸造合金中,铸钢收缩率较大,而灰铸铁较小。
12.液态金属在铸型中的凝固过程中,由液态收缩和凝固收缩所引起的体积缩减如得不到金属液的补充,就会在铸件最后凝固的部分形成孔洞。
由此造成的集中孔洞称为缩孔,细小分散的孔洞称为缩松。
13.纯金属和共晶成分的合金易形成集中缩孔。
(倒锥形)
14.采用冒口和冷铁,使铸件定向凝固。
15.铸造应力是引起铸件产生变形和裂纹的基本原因。
16.热应力是由于铸件各部分冷却速度不同,以致在同一时间内铸件各部分收缩不一致、相互约束而引起的内应力。
17.固态金属在再结晶温度T再(钢和铸铁的T再为620~650℃)以上处于塑性状态。
18.Ρ10图1-10
19.⑴热应力的特点是,铸件缓冷部位(壁厚部位或心部)受拉伸,快冷部位(薄壁部位或表层)受压缩。
⑵铸件冷却时各部位的温差愈大,定向凝固愈明显,合金的固态收缩率和弹性模量愈大,则热应力愈大。
20.防止热应力产生的具体措施有:
尽量选用弹性模量小的合金,设计壁厚均匀的铸件,从铸造工艺方面促使铸件各部位同时凝固。
在实际生产中,使铸件同时凝固是减小铸造内应力、防止铸件变形和裂纹的有效工艺措施。
21.Ρ11图1-14
22.热裂纹是铸件凝固末期、在接近固相线的高温下形成的。
热裂纹的特征是裂纹短,缝隙宽,形状曲折,裂纹内呈氧化色。
23.冷裂纹是较低温度下,由于热应力和收缩应力的综合作用,铸件的内应力超过合金的强度极限而产生的。
冷裂纹的特征是裂纹细小,呈连续直线状,裂纹内有金属光泽或轻微氧化色。
钢铁中磷含量愈高,铸件愈易冷裂。
24.气孔可分为侵入气孔、析出气孔和反应气孔三类。
25.Ρ17图2-1
26.按碳存在的形态(以化合物存在记为C化合,以石墨态存在记为C石墨)不同可分为白口铸铁(碳全部为C化合)、灰铸铁(碳主要为C石墨)及麻口铸铁(碳大部分为C化合);按石墨形状不同可分为灰铸铁(片状石墨)、蠕墨铸铁(蠕虫状石墨)、可锻铸铁(团絮状石墨)及球墨铸铁(球状石墨);按金属基体不同可分为铁素体铸铁、珠光体铸铁及铁素体与珠光体混合基体铸铁;另外加入合金元素、使其具有特殊性能的铸铁称为合金铸铁。
27.石墨是决定灰铸铁性能的主导因素。
第二章
28.Ρ22表2-2
29、Ρ39图3-1
29.机器造型不适合于三箱造型及活块造型。
30.砂型铸造是铸造中应用最广泛、最灵活的方法。
它既可用于单件、小批生产的手工造型,也可用于成批、大量生产的机器和自动生产线,既能浇注低熔点非铁金属及其合金液,又能浇注高熔点的铁液及钢液;铸件的尺寸可大可小,形状可简单亦可复杂。
31.覆膜砂的组成:
①原砂;②粘结剂;③固化剂;④附加剂。
32.覆膜砂的混制工艺有冷法、温法及热法三种,其中热法是一种适合大量制备覆膜砂的方法。
33.金属型可重复使用,故它又有永久铸造之称。
金属型按分型面的不同分为整体式、水平分型式、垂直分型式和复合分型式等。
金属型多采用底注式或侧注式浇注系统,以防止浇注时金属液飞溅。
34.保证铸件品质和延长金属型的使用寿命的措施:
⑴加强金属型的排气;⑵在金属型的工作表面上喷刷涂料;⑶预热金属型并控制其温度;⑷及时开型。
35.金属型铸造的特点:
1金属型铸造的优点:
①金属型可“一型多铸”,省去了砂型铸造中的配砂、造型、落砂等许多工序,节省了大量的造型材料和生产场地,提高了生产率,易于实现机械化和自动化生产。
②铸件的尺寸精度(IT12~IT14)和表面粗糙度(Ra=6.3~12.5µm)指标均优于砂型铸件,铸件的加工余量小。
因金属型冷却快而使铸件的晶粒细密,力学性能得到提高。
③劳动条件好。
2金属型铸造的缺点:
①金属型的制造成本高,周期长,不适合单件、小批生产。
②不适合制造形状复杂(尤其是内腔形状复杂)、薄壁和大型的铸件。
③用来制造铸钢等高熔点合金铸件时,金属型寿命较短,同时,还易使铸铁件产生硬、脆的白口组织。
36.金属型铸造的适用范围:
主要用于铜、铝、镁等非铁合金铸件,如内燃机活塞、缸盖、油泵壳体、轴瓦、衬套、盘盖等中小型铸件的大批生产。
37.制造蜡模是熔模铸造的重要步骤。
压型是用来压制蜡模的专用模具。
压型应尺寸精确、表面光洁。
压型的制造方法是:
①机械加工;②用易熔合金铸造。
38.熔模铸造是一种实现少无切削加工的、先进的精密成形工艺,它最适合于25㎏以下的高熔点、难以切削加工的合金钢铸件的成批、大量生产,目前主要用于航天飞行器、飞机、汽轮机、泵、汽车、拖拉机和机床上的小型精密铸件和复杂刀具的生产。
39.气化模铸造(或消失模铸造)的适用范围:
①各类合金,包括铝、镁、铜合金、灰铸铁、球墨铸铁及除低碳钢以外的铸钢(因气化模模样在浇注过程中会因熔失而对低碳钢产生增碳作用,使低碳钢的碳含量增加);②壁厚4㎜以上的铸件;③质量几公斤至几十吨的铸件;④生产批量不受限制,其中V-EPC法要求年产量为数千件以上;⑤只要利于气化模砂型的紧实,对铸件的结构形状几乎无任何特殊限制。
40.离心铸造的基本类型:
⑴立式离心铸造:
适用于高度不大的环类铸件;⑵卧式离心铸造:
适用于铸造长度较大的套筒及管类铸件,如铜衬套、铸铁缸套、水管等。
41.离心铸造的特点:
1离心铸造的优点:
①生产空心旋转体铸件时可省去型芯、浇注系统和冒口。
②在离心力作用下,密度大的金属被推往外壁,而密度小的气体、熔渣向内自由表面移动,形成自外向内的定向凝固,因此补缩条件好,铸件组织致密,力学性能好。
③便于浇注“双金属”轴套和轴瓦。
2离心铸造的缺点:
①铸件内孔自由表面粗糙,尺寸误差大,品质差。
②不适用于密度偏析大的合金(如铅青铜等)及铝、镁等轻合金。
42.离心铸造的适用范围:
主要用来大量生产管筒类铸件,如铁管、铜套、缸套、双金属钢背铜套、耐热钢辊道、无缝钢管毛坯、造纸机干燥滚筒等,还可用来生产轮盘类铸件,如泵轮、电动机转子等。
43.压力铸造的特点:
1压力铸造的优点:
①生产率高,每小时可压铸50~150次,最高可达500次,便于实现自动化、半自动化。
②铸件的尺寸精度高(IT11~IT13),表面粗糙度低(Ra=3.2~0.8µm),并可直接铸出极薄件或带有小孔、螺纹的铸件。
③铸件冷却快,又是在压力下结晶,故晶粒细小,表层紧实,铸件的强度、硬度高。
④便于采用嵌铸法(又称镶铸法)。
2压力铸造的缺点:
①压铸机费用高,压铸型制造成本极高,工艺准备时间长,不适宜单件、小批生产;②由于压铸型寿命原因,目前压铸尚不适于铸钢、铸铁等高熔点合金的铸造;③由于金属液注入和冷凝速度过快,型腔气体难以完全排出,壁厚处难以进行补缩,故压铸件内部常存在气孔、缩孔和缩松。
44.压铸是实现少无切削加工的一种重要工艺,在汽车、拖拉机、航空、仪表、纺织、国防等工业部门中以已广泛应用于低熔点非铁金属(如锌、铝、镁等合金)的小型、薄壁、形状复杂件的大批量生产。
45.低压铸造的特点:
低压铸造可弥补压力铸造某些不足,利于获得优质铸件。
1主要优点:
①浇注压力和速度便于调节,可适应不同材料的铸型(如金属型、砂型、壳型等)。
同时,充型平稳,对铸型的冲击力小,气体较易排除,尤能有效地克服铝合金的针孔缺陷。
②便于实现定向凝固,以防止缩孔和缩松,使铸件组织致密,力学性能好。
③不用冒口,金属的利用率可高达90%~98%。
④铸件的表面品质(IT12~IT14,Ra=12.5~3.2µm)高于金属型,可生产出壁厚为1.5~2㎜的薄壁铸件。
此外,低压铸造设备费用较压铸设备低。
2低压铸造存在的主要问题是升液管寿命短,金属液在保温过程中易产生氧化和夹渣,且生产率低于压力铸造。
46.低压铸造目前主要用于铝合金铸件(如气缸体、缸盖、活塞、曲轴箱、壳体、粗纱锭翼等)的大量生产,也可用于球墨铸铁、铜合金等较大铸件,如球铁曲轴、铜合金螺旋桨等。
47.挤压铸造的特点:
①挤压铸造的主要特征是其压力(2~10MPa)和速度(0.1~0.4m/s)较低,无涡流、无飞溅现象。
同时还因为挤压时金属液的静压力逐渐增加,较好地补缩了枝晶间的微缩孔。
不仅如此,还由于金属液不断在结晶层旁流过和冲刷,防止了树枝晶的自由长大,使铸件结晶组织细化。
因此挤压铸造可以铸出高品质的大平面薄壁铝铸件及复杂空心薄壁件。
②挤压铸造与压力铸造及低压铸造的共同点是,其增压的作用使铸件成形、“压实”并得到致密的组织;其不同点是,挤压铸造没有浇注系统,且铸件的尺寸较大、较厚一些,金属液流所受阻力较小,故铸件成形所需的压力远比压力铸造小。
挤压铸造时金属液与铸型接触较紧密,且在铸型中停留的时间较长,故应采用水冷铸型,并在型腔内壁上涂敷涂料,以延长铸型寿命;还应采用垂直分型,以利开型取出铸件和涂敷涂料。
第四章
48.铸造工艺方案的具体内容包括:
选择铸件的浇注位置及分型面,确定型芯的数量、定位方式、下芯顺序、芯头形状及尺寸,确定工艺参数(如机械加工余量、起模斜度、铸造圆角及收缩率等)以及浇注系统、冒口、冷铁的形状和尺寸及在砂型中的布置等,然后将所确定的工艺方案用文字和铸造工艺符号在零件图上表示出来,绘制铸造工艺图。
49.浇注时铸件在砂型中所处的空间位置称为铸件的浇注位置。
确定浇注位置时,应使铸件的重要面、大平面及薄壁部位朝下或侧立,厚壁部位朝上。
50.型芯用来形成铸件内腔或外形妨碍起模的部位。
51.在铸件需要进行切削加工的表面上增加的一层金属层厚度,称为机械加工余量。
52.为了顺利起模而不致损坏砂型和砂芯,应该在模样或芯盒的起模方向上带有一定的斜度,这个斜度称为起模斜度。
53.浇注系统是引导金属液流入型腔的一系列通道的总称。
它一般由浇口杯(盆)、直浇道、横浇道和内浇道等基本组元所组成。
54.在满足使用要求的前提下,铸件的形状宜尽可能用方形、圆形、圆锥等规则几何形体组成铸件形体。
55.妨碍起模的形体结构:
①凸台;②肋;③吊耳;④凹坑;⑤外圆角。
56.铸件壁厚的设计:
⑴铸件的壁厚应均匀,不应过厚或过薄;⑵壁厚不均匀的铸件的设计应有利于定向凝固。
57.熔模铸件的设计:
①为了便于浸挂涂料和撒砂,熔模铸件的孔、槽不宜过小或过深。
②因熔模型壳的高温强度低,易变形,平板型壳的变形尤甚,故熔模铸件应尽量避免有大平面。
58.Ρ96、97复习思考题
(2)、(3)、(6)
第六章
1、金属塑成形的基本工艺:
轧制、挤压、拉拔、自由锻、模锻、板料冲压。
2、加工硬化:
随着变形程度的增加,金属的强度及硬度提高,而塑性和韧性下降的现象。
具有自发回复到稳定状态的倾向。
3、回复:
回复温度温度T回=(0.25-0.3)T熔。
4、再结晶:
消除全部加工硬化,温度T再=0.4T熔。
在生产中常在结晶温度以上加热已加工硬化金属,使其发生再结晶而在次获得良好的塑性。
5、纤维组织:
纤维状的杂质不能经再结晶而消失,在塑性变形后被保留下来。
6、利用纤维组织两原则:
一,使纤维分布与零件的轮廓相符而不被切断;二,使零件所受的最大拉应力与纤维方向一致,最大切应力与纤维方向垂直。
7、影响塑性变形的因素:
1.材料性质(化学成分和金属组织);2、加工条件;3、应力状态。
8、金属的锻造性取决于材料性质(内因)和加工条件(外因)。
9、自由锻:
使用工具简单、通用,生产准备周期短,灵活性大,是大型锻件唯一的锻造方法。
10、模锻:
事加热到锻造温度的金属坯料在锻模模镗内一次或多次承受冲击力或压力的作用,而被迫流动成形以获得锻件的压力加工方法。
11、P112图7-2锤上模锻
12、预锻模膛与终端模镗的区别:
前者的模锻圆角和斜度较大,没有飞边槽。
13、P114图7-7
14、确定分模面的原则:
1、要保证模锻件能从模镗中取出;2、按选定的分模面制成模锻后,应使上下两模面的模镗轮廓一样;3、最好把分模面选在模镗深度最浅的位置处;4、使零件上所加的敷料最少;5、最好使分模面在一个平面上,上、下模镗的模镗深度基本一致。
15、冲孔连皮:
模锻件上直径小于25mm的孔一般不锻出或只压出球形凹穴,大于25mm的通孔也不能直接模锻,而必须在孔内保留一层连皮,这层连皮以后需冲除。
16、模锻件的结构工艺:
1、模锻件合理的分模面,以保证模锻件易于从锻模中取出、敷料消耗小、锻模容易制造;2、模锻件上与锤击方向平行非加工表面,应设计出模锻斜度;3、避免零件截面间差别过大或具有薄壁、高肋、凸起等结构;4、设计是避免深孔或多孔;5、形状复杂、不变模锻的锻件应采用锻-焊组合工艺,以减少敷料,简化模锻工艺。
第八章
1、板料冲压成形:
利用冲模使板料产生分离或变形的成形工艺。
2、分离工序:
使坯料的一部分相对于另一部分相互分离的工序,落料、冲孔、切断等。
3、落料及冲孔是使坯料按封闭轮廓分离的工序。
落料是被分离的为成品,留下来的是废料;冲孔是分离的为废料,留下为成品。
4、冲裁变形过程三阶段:
弹性变形、塑性变形、断裂分离。
5、冲裁件切断面上的特征:
P124图8-2
6、凹、凸模间隙:
P125图8-3
7、冲裁件的排样:
P127图8-4
8、拉深:
利用拉深模使板料变成开口空心件的冲压工序。
与冲裁模不同:
拉深凸、凹模都具有一定的圆角,不具有锋利的刃口,他们之间的单边间隙一般稍大于板料厚度。
9、拉深中常见废品:
1、拉裂:
拉深系数为0.5-0.8.塑性差的板料取上值,塑性好的取下值。
如拉深系数小,可采用多次拉深工艺(图P1308-9);2、起皱(--板料厚度)
10、弯曲时还应使弯曲线与板料纤维方向垂直。
11、回弹:
在弯曲结束后,由于弹性变形的回复,板料略有回弹,被弯曲的角度增大。
12、零件的所需的凸沿较高、一次翻边成形有困难时,可先拉深后冲孔、再翻边的工艺。
13、冲模:
有简单冲模(冲床的一次冲程只完成一个工序的冲模)、连续冲模(一次冲程中在模具不同部位上同时完成数道冲模工序)、复合冲模(一次冲程中在模具同一部位上同时完成数道冲压工序)。
14、P137图8-20
15、拟定冲压工艺方案:
两个(P140)
16、习题P145(10)
第十章
1、压焊:
电阻焊、摩擦焊、超声波焊、爆炸焊、扩散焊,高频焊。
2、钎焊及封粘:
软钎焊、硬钎焊、封接、粘接。
3、焊接缺陷:
易产生裂纹、夹渣、气孔等。
4、熔焊三要素:
合适的热源、良好的熔池保护、焊缝填充金属
5、焊缝填充金属:
焊芯和焊丝。
6、焊接热影响区:
受焊接热循环的影响、焊缝附件的母材因焊接热循环作用而发生组织或性能变化的区域。
7、热影响区:
熔合区、过热区、正火区、部分相变区(焊接接头断裂,多发生在熔合区和过热区中)。
(P178图10-13)
8、焊接应力的防止及消除:
P178图10-16
9、焊接缺陷:
焊接裂纹、未焊透、夹渣、气孔缺陷、焊接外观缺陷。
10、热裂纹:
表面有氧化色彩;冷裂纹:
焊道下裂纹、焊趾裂纹、焊根裂纹。
无分支,通常为穿晶形,无氧化色彩。
11、焊接无损检验:
1、磁粉检验;2、着色检验;3、超声波检验;4、X射线和r射线检验。
12、手弧焊:
以有药皮的焊芯为一个电极,以焊件为另一个电极,手工短路引燃,药皮产生大量气体和熔渣,实现渣-气体联合保护。
13、手焊弧工艺:
1、直流手焊弧:
直流正接是焊件电源的正极,焊条接负极。
直流反接与正接相反,焊条接正极,焊条熔化速度快;2、交流手焊弧:
电源为交流电源。
14、埋焊弧:
用焊剂进行焊渣保护,焊丝为一电极并在焊剂层下引燃电弧。
15、气体保护焊:
1、氩弧焊;2、CO2气体保护焊。
16、等离子弧焊:
利用机械压缩效应、热压缩效应冷气流的强迫冷却下,带点粒子和电磁收缩效应将电弧压缩为一束细小等离子体的一种焊接工艺。
第十一章
1、电阻焊:
利用电阻热为热源,并在压力下通过塑性变形和在结晶而实现焊接的工艺。
2、点焊的工艺参数:
电流、压力和时间。
主要用于汽车、飞机等薄板结构的大批量生产。
3、对焊:
电阻对焊、闪光对焊。
4、超声波焊特点:
1、接头中无铸态或脆性金属间化合物,也无金属喷溅,接头的力学性能比电阻焊好,且稳定性高;2、材料范围广,适合高熔点、高导热性、难熔金属、异种材料、厚薄悬殊、多层箔片焊接;3、焊接表面清理简单,电能消耗小。
5、扩散焊特点:
1、焊接温度低;2、可焊接复杂结构、要求焊件表面十分平整和光洁及精度要求高;3、可焊接各种不同材料;4、焊缝可与母材成分性能相同,无热影响区。
第十二章
1、钎焊:
硬钎焊、软钎焊。
2、钎焊特点:
加热温度低、接头光滑平整,焊件尺寸精确;2、焊接差异性大的异种金属,对焊件厚度差无严格要求;3、可有多条接头组成的、形状复杂的构件,生产率高;4、设备简单,生产投资费用少。
第十三章
1、焊接性:
被焊金属在采用一定的焊接方法、焊接材料、工艺参数及结构形式下,获得优质焊接接头的难易程度。
包括工艺焊接性、使用焊接性。
2、P222计算经验公式。
3、P224图13-2
4、低合金钢焊接特点:
1、热影响区的淬硬倾向;2、焊接接头的裂纹倾向;3、低合金钢的焊接措施。
第十四章
本章为改错题,详细看书上P223-227图样