酒钢4#焦炉与3#4#焦炉相配套的干熄焦装置及备煤化产系统改造工程初步设计.docx
《酒钢4#焦炉与3#4#焦炉相配套的干熄焦装置及备煤化产系统改造工程初步设计.docx》由会员分享,可在线阅读,更多相关《酒钢4#焦炉与3#4#焦炉相配套的干熄焦装置及备煤化产系统改造工程初步设计.docx(35页珍藏版)》请在冰豆网上搜索。
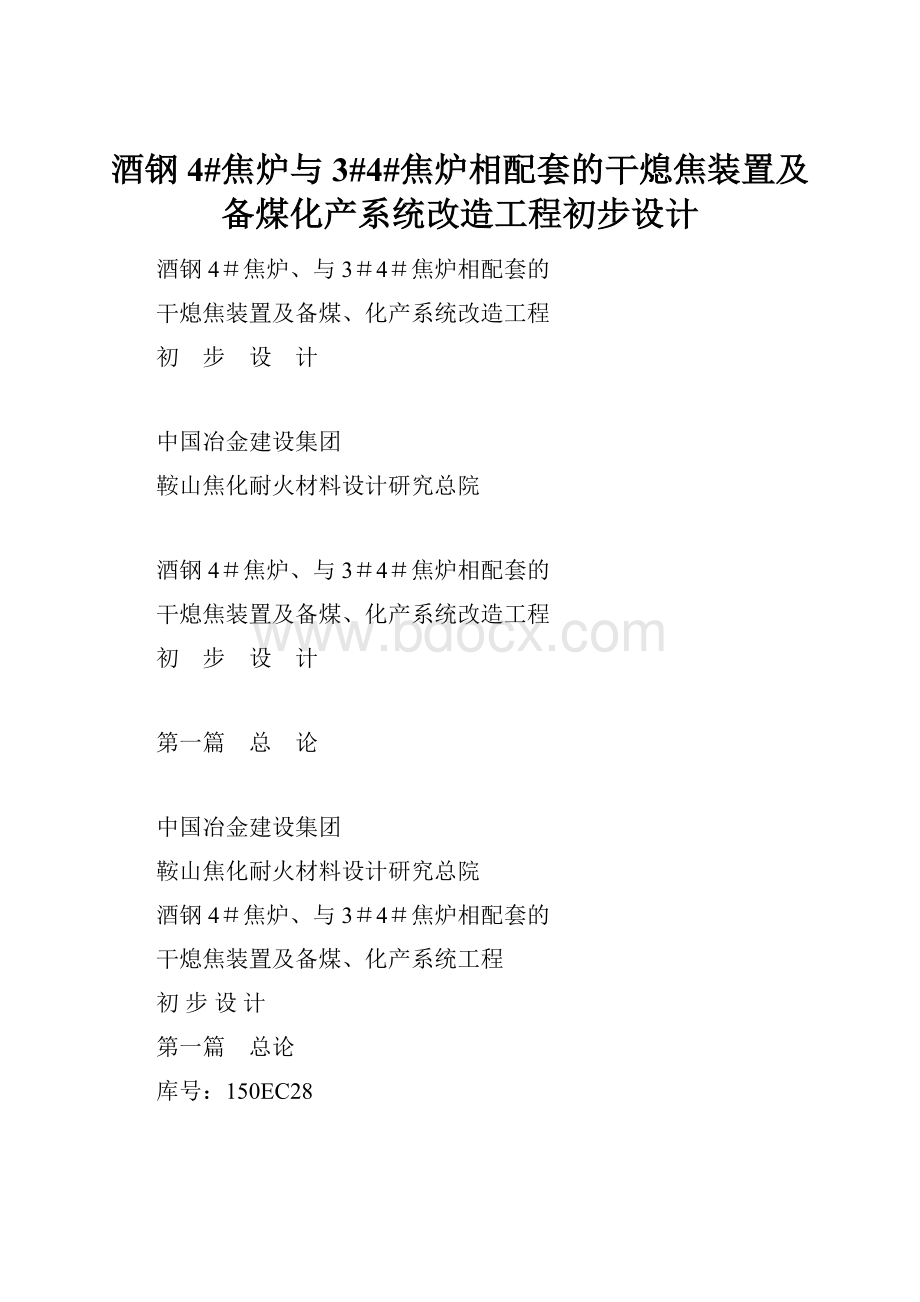
酒钢4#焦炉与3#4#焦炉相配套的干熄焦装置及备煤化产系统改造工程初步设计
酒钢4#焦炉、与3#4#焦炉相配套的
干熄焦装置及备煤、化产系统改造工程
初 步 设 计
中国冶金建设集团
鞍山焦化耐火材料设计研究总院
酒钢4#焦炉、与3#4#焦炉相配套的
干熄焦装置及备煤、化产系统改造工程
初 步 设 计
第一篇 总 论
中国冶金建设集团
鞍山焦化耐火材料设计研究总院
酒钢4#焦炉、与3#4#焦炉相配套的
干熄焦装置及备煤、化产系统工程
初步设计
第一篇 总论
库号:
150EC28
副院长
:
副总工程师
:
设计经理
:
中国冶金建设集团
鞍山焦化耐火材料设计研究总院
二OO三年十月
编制专业及人员
编制专业 室主任 专业组长 审核人 编制人
备 煤 钱理业 郑卫军 刘承智 关宏宇
炼 焦 张长青 张晓光 袁朝晖 朱 郁
化 工 张兴柱 王英丽 王家石 徐作峰
郑秀珍
精 制 叶 煌 张素利 孙 虹 朱传平
热 力 姜 宁 陈本成 任 重 罗立伦
总 图 倪荣芳 张 杰 田友富 李 芳
土 建 马文炜 郑 伟 刘业刚 刘素坤
张建奎 张庆良
电 力 王洪耀 牟卫国王冬枫 王振川
电 信 王洪耀 王柏峰 王柏峰 方丽明
仪 表 史红缨 刘福臣 刘晓东 周 浩
给水排水 尹君贤 马雁林 于泽成 林冬晓
通 风 王 满 霍延中 刘庆成 尹 华
工程经济 任少明 单晶辉 陈国红 董 静
技术经济 任少明 单晶辉 陈国红 徐丽娟
环 保 武 剑 何 平 刘 洪 李冰冰
目 录
1概述
1.1设计依据
a)酒钢的设计委托书及酒钢与焦耐院签订的设计合同;
b)酒钢与焦耐院签订的技术协议;
c)酒钢对可行性研究报告审查后形成的会议纪要;
d)酒钢、焦耐院、武汉星宇监理公司对初步设计初稿进行预 审查形成的会议纪要。
1.2设计原则和主要要求
a)酒钢焦化厂4号焦炉为60孔炭化室高6m的JN60-6型焦炉,年产焦炭约60万吨,与已建成的3号焦炉布置在同一条中心线上,组成一个炉组。
b)干熄焦装置处理能力与3号、4号焦炉(JN60-6型50+60孔焦炉)相配套,采用JNG90-4型干熄焦装置;干熄焦锅炉回收红焦的显热,所产生P=3.82MPa,t=450℃蒸汽,与公司蒸汽管网并网。
c)备煤车间新建4×Φ10m配煤槽,新增贮量2600吨,总贮量7150吨;筛焦工段现有设施可以满足新增4号焦炉要求,增设干熄焦运焦系统。
d)煤气净化车间按200万吨/年炼焦能力(原有1号、2号、3号为140万吨/年炼焦能力)进行设计。
采用对焦化厂现有净化系统上进行改造的方式实施,改造后车间组成为冷凝鼓风工段、硫铵工段、终冷洗苯工段、粗苯蒸馏工段、溶剂脱酚工段和蒸氨工段。
各工段均需增加相应的装置和设备,以满足新增炼焦能力的需要。
e)焦油工段,新增离心机和改质沥青反应釜,并对粗蒽离心机扩容。
f)干熄焦装置投产后,正常生产熄焦用干熄焦装置,湿熄焦系统作为干熄焦装置的备用。
1.3设计规模及进度
1.3.1设计规模
酒钢焦化厂4号焦炉(1×60孔JN60-6型)生产能力为年产焦炭60万吨,配套的备煤、煤气净化、公辅设施进行相应改造(规模按年产焦炭200万吨设计)。
根据3号、4号焦炉的生产能力,小时产焦为123.89吨,考虑干熄焦装置的强化操作系数1.1采用JNG90-4型干熄焦装置一套,原湿法熄焦系统作为备用。
1.3.2设计进度
2003年10月完成初步设计和审批工作;
2003年10月~2004年10月开展施工设计;
2003年10月~2005年10月现场施工;
2005年2月4#焦炉投产。
1.4建厂的外部条件
1.4.1气候参数:
极端最高气温38.4℃
极端最低气温-31.4℃
年平均气温6.9℃夏季平均气温23.2℃
冬季平均气温-8.9℃
年平均大气压力852.5hPa夏季平均大气压力847.0hPa
冬季平均大气压力856.0hPa
年平均降水量85.7mm
年最大降水量155.0mm
日最大降水量3.9mm
最大积雪深度14.0cm
夏季平均相对湿度43%
冬季平均相对湿度54%
全年平均风速2.4m/s
夏季平均风速2.3m/s
30年一遇的最大风速34.0m/s
全年最多风向及频率C,16%SW,11%
夏季最多风向及频率C,19%E,9%
冬季最多风向及频率C,17%SW,13%
最大冻土深度132.0cm
1.4.2工程地质及水文条件
根据西北地质勘察基础工程总公司第五工程处2003年8月13日提供的《酒钢(集团)有限责任公司4#焦炉及烟囱工程岩土工程勘察报告》(详勘),地层自上而下为:
1杂填土;不宜利用;
2卵砾石(fak=600kPa);
3卵砾石(fak=800kPa);
地下水一般埋深大于100m,因地下水埋深较大,设计可不考虑对建(构)筑物基础的影响。
1.4.3设计的主要数据:
基本风压0.60kN/m2
基本雪压0.25kN/m2冬季采暖室外计算温度-16℃
夏季通风室外计算温度26℃
冬季空调室外计算温度-19℃
夏季空调室外计算温度30.0℃
抗震设防烈度7度
1.4.4原料、产品的运输方式
本工程所需原料煤、化工原料的运入以及化工产品的运出采用铁路运输方式。
本工程备品备件、各种药剂的运入及除尘粉尘的运出采用道路运输方式。
1.5设计范围及分工
本工程界区内的生产设施由备煤车间改造;新建一座4号焦炉(60孔JN60-6型);与3号4号焦炉相配套的干熄焦装置(JNG90-4型)及配套设施;煤气净化车间及焦油工段改造组成。
公用辅助配套工程由循环水系统(包括回收和干熄焦)、余热锅炉房、除氧给水泵房、压缩空气站、制冷站、综合电气室、车间变电所、干熄焦除尘地面站、炉前焦库除尘地面站、筛焦切焦除尘地面站、预留装煤除尘地面站等组成。
干熄焦锅炉产生蒸汽接至焦化厂区边界与酒钢蒸气管网并网;煤气净化产生酚氰废水送现生物脱酚装置,该装置改造由酒钢设计院设计。
界区内新增系统所需的水(含除盐水)、电、蒸汽、压缩空汽、氮气(含仪表用气)等均接自酒钢及焦化厂相应系统。
1.6初步设计文件组成
本初步设计共分三部分
第一部分第一篇总论
第二篇工程设计说明
第三篇工程概算
第四篇主要设备表
第二部分环境保护专篇
劳动安全卫生专篇
消防专篇
第三部分初步设计附图
2原材料、燃料的来源及需要量
2.1原料
本装置新增炼焦能力60万t/a,年需洗精煤788400t(干基),H2SO4(93%) 年需5602吨,NaOH(40%)年需2250吨,洗油年需777吨,磷酸三钠年需0.966吨,联氨年需96.6公斤
2.2燃料
焦炉煤气35555.04×103m3/a ,高炉煤气493152.96×103m3/a。
3
主要产品品种、产量
a)焦炭(干基) 582584t/a
b)粉焦 13166.1t/a
c)焦炉煤气 252288×103m3/a
d)蒸汽 620160t/a
e)焦油 27189t/a
f)硫铵 6946t/a
g)粗苯 7768t/a
4
项目组成及工程项目内容
4.1项目组成
本项目由备煤车间改造;新建一座4号焦炉(JN60-6型);与3号4号焦炉相配套的干熄焦装置(JNG90-4型);化产车间改造;公用及辅助设施配套改造等组成。
4.2工程项目内容
4.2.1备煤车间:
新建4×Φ10m配煤槽,新增贮量2600吨,总贮量7150吨。
4.2.2炼焦车间:
4号焦炉,为60孔JN60-6型年产干全焦60万吨,与3号焦炉布置在同一条中心线上,组成一个炉组。
新建焦炉的出焦除尘仍利用3号焦炉的除尘地面站。
熄焦方式采用干法熄焦,湿法熄焦作为备用。
4.2.3干熄焦装置:
采用JNG90-4型干熄焦装置,处理能力与3号、4号焦炉(JN60-6型50+60孔焦炉)相配套;
4.2.4运焦工段:
现有设施可以满足新增4号焦炉要求,仅增设干熄焦运焦系统。
4.2.5煤气净化车间:
按200万吨/年炼焦能力(原有1号、2号、3号为140万吨/年炼焦能力)进行设计。
采用对焦化厂现有净化系统进行改造方式实施,改造后车间组成为冷凝鼓风工段、硫铵工段、终冷洗苯工段、粗苯蒸馏工段、溶剂脱酚工段和蒸氨工段。
各工段均需增加相应的装置和设备,以满足新增炼焦能力的需要。
4.2.6焦油工段:
新增焦油超级离心机和改质沥青反应釜,并对粗蒽离心机扩容。
4.2.7生产辅助设施:
新建制冷站、空压站、循环水系统改造等。
5
工艺流程及主要设备
5.1备煤
现有配煤槽贮量4550t,相当于4座焦炉13小时用煤量,所以新建4×Ф10m贮槽,新增贮量4×650t=2600t,配煤室总贮量7150t,相当于4座焦炉~20小时用煤量,满足焦炉的生产需要。
5.2炼焦
本工程在现有的3号焦炉煤塔一侧的原预留位置新建一座60孔JN60-6型年产干全焦60万吨规模的焦炉,焦炉的出焦除尘采用除尘地面站方式,与3#焦炉共用一个除尘地面站,熄焦方式采用干法熄焦,湿法熄焦做为备用。
预留3#、4#焦炉装煤除尘地面站位置。
5.2.1工艺参数
炭化室孔数1×60孔
炭化室有效容积38.5m3/孔
每孔炭化室装煤量(干)28.5t
焦炉周转时间19h
焦炉年工作日数365d
焦炉紧张操作系数1.07
装炉煤水分10%
煤气产率320m3/t干煤
成焦率75%
焦炉加热用煤气低发热值:
焦炉煤气16400kJ/m3
高炉煤气3600kJ/m3
装炉煤水分10%用时炼焦干煤相当耗热量(计算生产用量)
焦炉煤气加热时2514kJ/kg
高炉煤气加热时2836kJ/kg
5.2.2工艺流程
由备煤车间送来的配合煤装入煤塔。
装煤车按作业计划从煤塔取煤,经计量后装入炭化室内,煤料在炭化室内经过一个结焦周期的高温干馏炼制成焦炭和荒煤气。
炭化室内的焦炭成熟后,用推焦机推出,经拦焦机导入运焦车的焦罐中,运焦车由电机车牵引至干熄站进行熄焦,熄焦后的焦炭送往筛贮焦工段。
采用备用的湿法熄焦时,炭化室内的焦炭成熟后,用推焦机推出,经拦焦机导入熄焦车内,熄焦车由电机车牵引至熄焦塔内进行喷水熄焦。
出焦产生的烟尘通过带吸尘罩的拦焦机吸入集尘干管送到除尘地面站。
熄焦后的焦炭卸至晾焦台上,晾置一定时间后送往筛贮焦工段。
煤在炭化室干馏过程中产生的荒煤气汇集到炭化室顶部空间,经过上升管,桥管进入集气管,约800℃左右的荒煤气在桥管内被氨水喷洒冷却至85℃左右。
荒煤气中的焦油等同时被冷凝下来。
煤气和冷凝下来的焦油同氨水一起经吸煤气管道送入煤气净化车间。
焦炉加热用的焦炉煤气或高炉煤气,由外部管道架空引入。
焦炉煤气经预热后送到焦炉地下室。
通过下喷管把煤气送入燃烧室立火道底部与废气交换开闭器进入的空气汇合燃烧。
燃烧后的废气通过立火道顶部跨越孔进入下降气流的立火道,再经过蓄热室,由格子砖把废气的部分显热回收后,经过小烟道、废气交换开闭器、分烟道、总烟道、烟囱,排入大气。
高炉煤气由车间外部管道架空引入焦炉地下室。
通过废气交换开闭器、小烟道、蓄热室送入燃烧室与同时引入的空气汇合燃烧。
燃烧后的废气通过与燃烧焦炉煤气的废气同样途径排入大气。
上升气流的煤气和空气与下降气流的废气由交换传动装置定时进行换向。
5.2.3焦炉机械
5.2.3.1新增焦炉机械配置如下表
表2-3焦炉机械配置表
序
数量(台)
号
名 称
操作
备用
1
除尘装煤车
1
0
2
推焦机
1
0
3
液压交换机
1
0
5.2.3.2焦炉机械的主要性能及特点
焦炉机械是在总结国内焦炉机械操作经验的基础上,吸取了国外焦炉机械的先进技术,主要从提高机械效率、降低劳动强度和改善操作环境出发点并以先进、安全、实用为原则进行设计和制造的。
全套焦炉机械是按5-2推焦串序进行操作,采用单元程序控制,并带有手控装置,推焦机和拦焦机之间设有联锁装置,以及由电机车控制推焦杆的事故刹车装置,各司机室设有载波电话,提高设备运行的安全性和可靠性。
5.3干熄焦装置
为回收红焦的显热﹑降低能耗,减少污染,提高焦炭质量,采用干法熄焦。
当干熄焦装置年修或出现故障时,原有的的湿熄焦系统作为备用。
5.3.1主要工艺参数
a)焦炉基本工艺参数
焦炉配置50+60孔JN60-6型焦炉
焦炉周转时间19h
每孔炭化室干全焦产量21.4t
小时焦炭产量123.89t
焦炉年产量1085318t
b)干熄焦装置基本工艺参数
干熄站个数1个
干熄炉型号JNG90-4
允许焦炉的检修制度3次/d,1h/次
每孔炭化室操作时间约9.07min
入干熄炉焦炭温度950~1050℃
干熄后焦炭温度低于205℃
干熄时间约1.97小时
焦炭烧损率~0.9%(设计值)
入干熄炉的吨焦气料比约1240m3/t焦
循环气体最大流量200000m3/h
循环风机全压11.5kPa
进干熄炉循环气体温度130℃
出干熄炉循环气体温度900~980℃
干熄炉操作制度24h/d连续,340d/a
干熄炉年修时间25d/a
5.3.2干熄焦工艺
装满红焦的焦罐车由电机车牵引至提升井架底部。
提升机将焦罐提升并送至干熄炉炉顶,通过带布料器的装入装置将焦炭装入干熄炉内。
在干熄炉中焦炭与惰性气体直接进行热交换,焦炭被冷却至205℃以下,经排焦装置卸到带式输送机上,然后送往焦处理系统。
循环风机将冷却焦炭的惰性气体从干熄炉底部的供气装置鼓入干熄炉内,与红热焦炭逆流换热。
自干熄炉排出的热循环气体的温度约为900~980℃,经一次除尘器除尘后进入干熄焦余热锅炉换热,温度降至160~180℃。
由锅炉出来的冷循环气体经干熄焦专用除尘器除尘后,由循环风机加压,再经热管换热器冷却至130℃后进入干熄炉循环使用。
5.3.3主要装备
为确保干熄焦装置长期﹑安全﹑稳定的运行以及技术上的先进性,干熄焦装置中部分关键设备如循环风机﹑装入装置用电动缸﹑排焦装置用振动给料器及格式密封阀等从国外引进;其它国产化设备中的关键部件如:
电机车中的制动器及变频调速系统,焦罐车用传感器,提升机中的钢丝绳﹑轴承﹑提升电机﹑电气低压元件﹑调速装置﹑PLC装置及检测系统等也拟由制造厂自国外引进。
干熄焦装置的主要装备如下;
a)电机车运行在焦炉焦侧的熄焦车轨道上,用于牵引和操纵焦罐车或湿熄焦车。
该电机车既能满足干法熄焦的作业要求,又能满足湿法熄焦的作业要求。
具有运行速度快,调速性能好,对位准确且行车安全的特性。
b)焦罐主要由焦罐体及摆动的底闸门和吊杆组成。
焦罐体由型钢构架和铸铁内衬板构成。
外框架两侧设有导向辊轮供升降导向,还设有与底闸门连动的提吊罐体的吊杆。
焦罐底部还设有柔性遮挡罩。
c)对位装置在干熄站的熄焦车轨道外侧设置了一套液压强制驱动的对位装置,主要由液压站、连接管路、液压缸及夹紧装置等组成。
d)提升机用于将装满红焦的焦罐提升并横移至干熄炉顶,将红热焦炭装入干熄炉内,装完红焦后将空焦罐放回到运站载车上。
由PLC控制并与其它设备联动。
e)干熄炉外壳用钢板制做,内衬耐磨粘土砖及断热砖等,上部为预存室,中间是斜道区,下部为冷却室。
f)装入装置安装在干熄炉操作台上,主要由炉盖台车和带料钟的装入料斗台车组成,两个台车连在一起,由一台电动缸驱动。
g)排焦装置位于干熄炉的底部,将干熄炉下部冷却的焦炭连续密封地排出,它由平板闸门、电磁振动给料器、旋转密封阀和排焦溜槽等设备组成。
h)一次除尘器为重力沉降式除尘装置,用于除去循环气体中所含的粗粒焦粉。
i)二次除尘器采用了多管旋风分离式除尘器,将循环气体中的粗粒焦粉进一步分离出来。
使入循环风机的气体粉尘含量小于1g/m3,多管旋风除尘器主要由单体旋风器、旋风子固定板、导气管固定板、外壳、下部灰斗及进出口变径管等构成。
旋风器的旋风子及导向器采用高铬合金镀部分镍、钼合金元素,可提高其耐磨性以延长使用寿命。
j)循环风机是气体循环部分的核心,安装在二次除尘器和给水预热器之间,接触气体部分的材质要求耐磨,风机结构为离心风机,采用液力耦合器调速。
k)热管换热器由锅炉给水与循环气体进行换热,从而降低进入干熄炉的循环气体温度以强化干熄炉的换热效果。
型式为多排竖管式,外形为方型。
l)干熄焦余热锅炉是干熄焦装置余热回收的重要设备,额定蒸发量为74.5t/h,所产蒸汽参数为P=3.82MPa,t=450℃,采取了蒸汽超温、超压、锅炉液位过高、过低报警和联锁保护等措施,确保干熄焦锅炉安全稳定运行。
5.4运焦工段
干熄焦运焦系统是配合JNG90-4干熄焦装置而设计的。
干熄焦运焦系统将干熄焦装置处理后的焦炭运至现有的3、4号焦炉筛贮焦系统。
该系统由炉前焦库、带式输送机及相应的转运站等设施组成。
5.5煤气净化车间
煤气净化车间组成为:
冷凝鼓风工段、硫铵工段、终冷洗苯工段、粗苯蒸馏工段、溶剂脱酚工段和蒸氨工段。
5.5.1设计基础数据
5.5.1.1净化前煤气中杂质含量
NH3
7g/m3(参考)
H2S
6g/m3(参考)
HCN
1.5g/m3(参考)
B.T.X
38g/m3(参考)
5.5.1.2产品产率
焦油
3.5%(对干煤)
轻苯
0.93%(对干煤)
精重苯
0.03%(对干煤)
5.5.1.3净化后煤气中杂质含量
NH3
0.05g/m3
H2S
6g/m3
HCN
1.5g/m3
B.T.X
4g/m3
萘
0.3g/m3
焦油
0.05g/m3
5.5.2工艺及主要设备
5.5.2.1冷凝鼓风工段
a)来自焦炉集气管~82C的荒煤气,与焦油和氨水沿吸煤气管道至气液分离器,气液分离后荒煤气,进入横管初冷器。
初冷器采用高效横管冷却器,将煤气从82℃冷却到21~22℃,并分别喷洒焦油、氨水混合液,使煤气中的萘被焦油溶解,确保后序设备无堵塞之患。
采用新型高效的蜂窝式电捕焦油器,处理后煤气中焦油含量可控制在50mg/m3以下,有利于后序设备的正常操作。
a)主要设备
设备名称及规格
主要材质
台数
初冷器FN4000m2
碳钢
2
电捕焦油器DN4600
碳钢
1
机械化氨水澄清槽V=204m3
碳钢
1
循环氨水中槽DN5680V=85m3
碳钢
1
煤气鼓风机D1200-25
1
5.5.2.2硫铵工段
a)由冷鼓工段来的煤气经煤气预热器进入饱和器。
煤气在饱和器的上段分两股入环形室经循环母液喷洒,其中的氨被母液中的硫酸吸收,然后煤气合并成一股进入后室经母液最后一次喷淋进饱和器内旋风式除酸器,以便分离煤气所夹带的酸雾,最后送至终冷洗苯工段。
采用喷淋式饱和器,材质为不锈钢,使用寿命长,集酸洗、除酸与结晶为一体,煤气系统阻力小,硫铵颗粒较大,流程简单,工艺先进,技术可靠。
b)主要设备的选择
设备名称及规格
主要材质
台数
饱和器DN3800/2800
SUS316L
1
结晶槽DN2000
SUS316L
1
振动流化床干燥机
1
母液循环泵
1
5.5.2.3终冷洗苯工段
a)从硫铵工段来的约55℃的煤气,进入直接式终冷塔,与循环喷洒液逆向接触,将煤气冷到~27℃后进入洗苯塔。
循环喷洒液自流至塔底贮槽,经循环喷洒液冷却器,用循环水、低温水冷却到25℃进入终冷塔循环使用。
排出的冷凝液送至生物脱酚工段或蒸氨工段。
从终冷塔出来的煤气进入洗苯塔。
由粗苯蒸馏工段送来的贫油从洗苯塔的顶部喷洒,与煤气逆向接触吸收煤气中的苯,塔底富油经富油泵送至粗苯蒸馏工段脱苯后循环使用。
出洗苯塔煤气回炉加热或外送冶金厂。
终冷采用直冷形式,一次性投资低。
洗苯塔选用新型填料,比表面积大,节省投资。
b)主要设备
设备名称及规格
主要材质
台数
洗苯塔DN3800
Q235-A
2
5.5.2.4粗苯蒸馏工段
a)粗苯洗涤及粗苯蒸馏,其工艺流程采用时分时合的综合流程。
这主要是考虑到对旧设备的充分利用,又考虑到以最经济合理的技术手段,来实现焦炉扩大生产能力之后的粗苯回收。
洗苯系统为两系洗苯塔并联工作,上塔贫油系统即分两系,洗苯所获得富油经两台富油泵将两股富油送到粗苯蒸馏部分新增设的富油槽混合。
在此再用一台大富油泵将富油送到油气换热器、贫富油换热器,出贫富油换热器的富油分两股进入两台管式炉(一台旧的,一台新的),控制两股流量均匀,分别入脱苯塔。
塔顶轻苯蒸汽进入油汽换热器、轻苯冷凝冷却器,用循环水冷凝冷却至30℃左右,经轻苯油水分离器分离出水分后流至回流槽,一部分轻苯用回流泵抽送至脱苯塔顶作回流,另一部分进入轻苯中间槽,然后用轻苯产品泵外送。
脱苯塔下的热贫油,经油油换热器与富油换热后,入贫油冷却器后,分别送入两系并联操作的洗苯塔。
采用单塔生产轻苯、精重苯的工艺,具有流程短,设备少,占地小,能耗低等优点。
脱苯塔顶设断塔盘引水,保证了全塔的操作稳定,侧线产品易于合格。
b)主要设备的选择
设备名称及规格
主要材质
台数
脱苯塔DN3000/2800H=39458
不锈钢
1
再生器DN2600H=10527
Q235-A
1
管式炉
Q235-A
1
5.5.2.5蒸氨工段
a)由冷凝鼓风工段送来的剩余氨水经浮选器,与蒸氨塔底排出的蒸氨废水换热后进入蒸氨塔,用直接蒸汽将氨蒸出,同时碱液进入蒸氨塔上部分解剩余氨水中固定铵,蒸氨塔顶部的氨汽经分缩器进入硫铵工段的饱和器。
换热后的蒸氨废水进入废水冷却器冷却后送至酚氰废水处理站。
蒸氨