催化裂化烘干方案分析.docx
《催化裂化烘干方案分析.docx》由会员分享,可在线阅读,更多相关《催化裂化烘干方案分析.docx(13页珍藏版)》请在冰豆网上搜索。
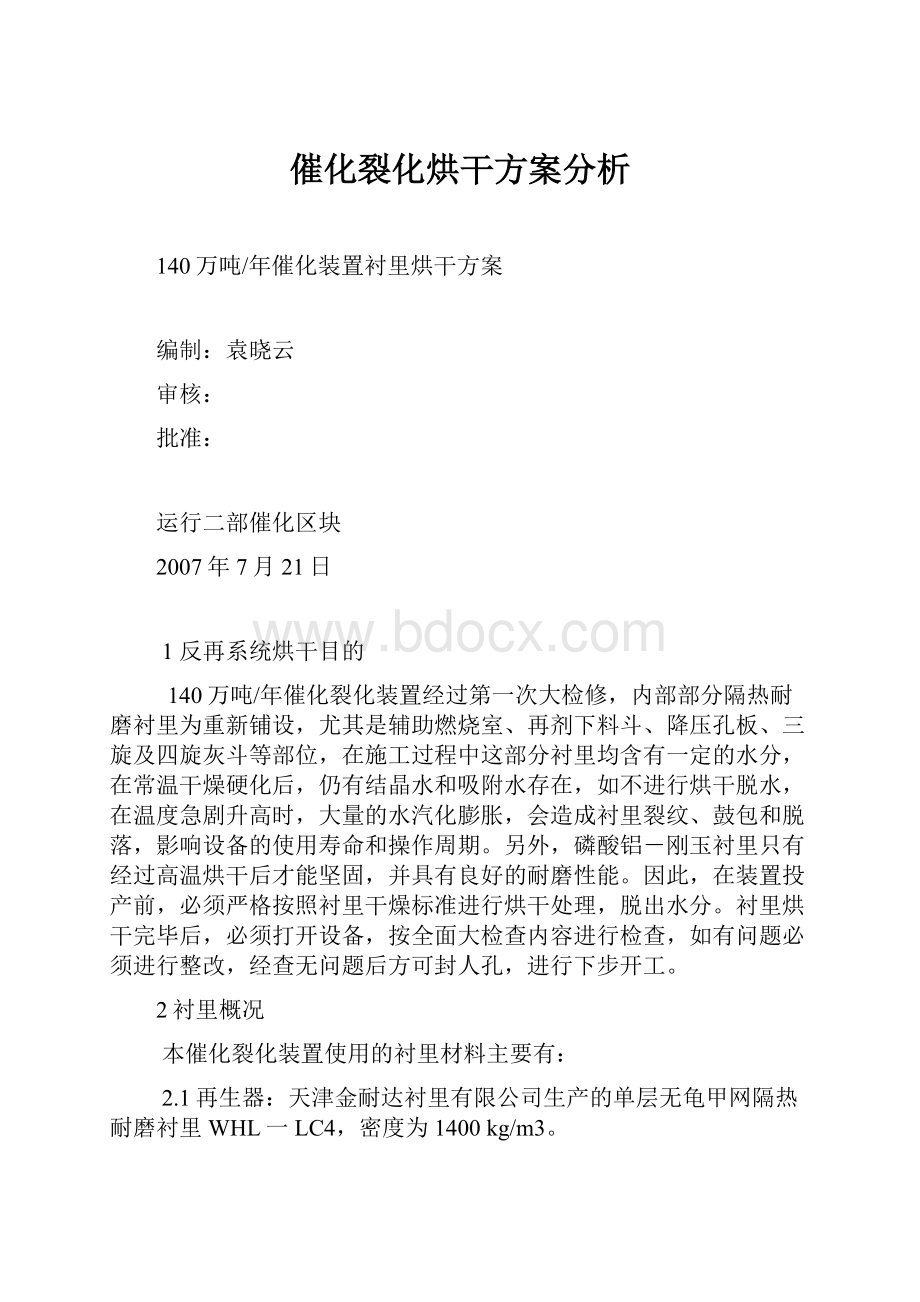
催化裂化烘干方案分析
140万吨/年催化装置衬里烘干方案
编制:
袁晓云
审核:
批准:
运行二部催化区块
2007年7月21日
1反再系统烘干目的
140万吨/年催化裂化装置经过第一次大检修,内部部分隔热耐磨衬里为重新铺设,尤其是辅助燃烧室、再剂下料斗、降压孔板、三旋及四旋灰斗等部位,在施工过程中这部分衬里均含有一定的水分,在常温干燥硬化后,仍有结晶水和吸附水存在,如不进行烘干脱水,在温度急剧升高时,大量的水汽化膨胀,会造成衬里裂纹、鼓包和脱落,影响设备的使用寿命和操作周期。
另外,磷酸铝-刚玉衬里只有经过高温烘干后才能坚固,并具有良好的耐磨性能。
因此,在装置投产前,必须严格按照衬里干燥标准进行烘干处理,脱出水分。
衬里烘干完毕后,必须打开设备,按全面大检查内容进行检查,如有问题必须进行整改,经查无问题后方可封人孔,进行下步开工。
2衬里概况
本催化裂化装置使用的衬里材料主要有:
2.1再生器:
天津金耐达衬里有限公司生产的单层无龟甲网隔热耐磨衬里WHL一LC4,密度为1400kg/m3。
2.2沉降器:
宜兴东方窑炉材料有限公司生产的单层无龟甲网隔热耐磨衬里LC3,密度为1600kg/m3。
2.3外取热器:
宜兴东方窑炉材料有限公司生产的单层无龟甲网隔热耐磨衬里LC3,密度为1550kg/m3。
2.4三旋:
宜兴东方窑炉材料有限公司生产的单层无龟甲网隔热耐磨衬里LC4,密度为1400kg/m3。
2.5烟气管道:
常州市派瑞特化工有限公司生产的双层隔热耐磨衬里:
隔热层为Fc-G-Lc4,密度为1400kg/m3。
耐磨层为Fc-G-Lc1,密度为2000kg/m3。
2.6油气线:
常州市派瑞特化工有限公司生产的双层隔热耐磨衬里:
隔热层为Fc-G-Lc4,密度为1000kg/m3。
耐磨层为Fc-G-Lc1,密度为2200kg/m3。
3准备工作
3.1两器所有设备内部和烟气、主风、催化剂管线内杂物清扫干净,保证畅通。
3.2详细检查各设备的施工质量及配件是否完好。
主要内容:
1)各处衬里的施工质量,确认衬里质量符合要求。
2)单、双动滑阀阀板与阀座接触情况。
3)燃料油喷嘴是否畅通。
4)主风分布管有无明显变形,焊接质量是否符合要求。
5)料腿出口距分布管的尺寸是否合适。
6)翼阀角度和严密性,开关是否灵活好用。
7)翼阀方向是否正确。
8)两器内外部是否有妨碍热膨胀的部件及连接方式。
9)松动点、取压点及汽提蒸汽管线是否畅通。
l0)各热电偶、取压点、松动点的位置是否正确。
3.3检查沉降器、再生器的旋分器料腿、灰斗、升气管及催化剂输送管线是否畅通。
3.4检查反再系统各控制、记录仪表是否好用,并联校完毕,可随时投入运行。
压力表,温度计校验安装好,确认量程合适。
3.5各设备、特殊阀门(反再系统特阀如下表)、自保阀已调校完毕并处于良好状态,校准各阀门开度的零位、行程、灵敏度,并做好记录,各专业验收合格。
反再系统特阀
项目
特阀名称
一段提升管
二段提升管
外循环管
外取热
待生
双动滑阀
型号
DYLDⅧ800
DYLDⅣ500
DYLDⅡ1100
DYLD1000
DYLSⅧ1500
设计压力MPa
0.5
0.5
0.5
0.5
0.5
0.5
设计压差MPa
0.03
0.2
0.03
0.03
0.03
0.10
设计温度℃
750
750
750
750
750
720
全开面积cm2
1904
586
2622
2622
2622
4232
行程mm
530
320
610
610
610
460
3.6各松动点、吹扫点及特殊阀门吹扫介质改为风。
3.7检查辅助燃烧室瓦斯、燃烧油火嘴是否按要求装好,管线是否畅通,流程是否合适。
3.8准备好气密试验用的肥皂水、毛刷、吸耳球。
3.9准备好表面测温仪,以便测量壁温。
3.10抽出瓦斯点火器,在炉外试验电打火,掌握使用条件后再装进去。
3.11辅助燃烧室和烟囱安装好热电偶,接好就地温度指示,按5.4.2条(两器系统烘干基准温度)接入就地指示温度,并确保准确。
3.12加好下列盲板。
位置
盲板号
所在管号
通径
个数
油气线进分馏塔盲板
SB2201
P2107
DN800
1块
原料油至提升管喷嘴
SB2105/1-6
P2101/1-6
DN100
6块
一再燃烧油总管
SB2104
FO2101
DN80
1块
回炼油、油浆至二段提升管
SB2106/1-4
P2105/1-4
DN100
4块
粗汽油至二段提升管
SB2110/1-4
P2221/1-4
DN80
4块
粗汽油至一段提升管
SB2109/1-2
P2220/1-2
DN80
2块
3.13引净化风、非净化风至各松动点。
引风时,保持各流量稳定和风压恒定,开始进行冷态试验,用肥皂水逐一检查反再系统各部位法兰、焊缝、阀门等,如有泄漏做好记录,待关闭净化风、非净化风总阀后,联系对漏点进行处理,处理完毕,重新引净化风、非净化风至各点。
3.14管线气密试验结束后,改好烘干流程。
3.15引蒸汽至反再系统,保证蒸汽压力不低于0.7Mpa,关闭反再系统蒸汽总阀,阀后低点脱水,同时严禁蒸汽窜入或漏入沉降器和再生器,以下蒸汽阀门必须关死:
(1)沉降器顶防焦蒸汽
(2)沉降器和大油气线放空吹扫蒸汽
(3)一二段再生线路松动蒸汽
(4)待生滑阀吹扫蒸汽
(5)待生斜管松动蒸汽
(6)燃烧油雾化蒸汽
(7)双动滑阀吹扫蒸汽
(8)汽提蒸汽
(9)主风事故蒸汽
(10)一二段预提升蒸汽
(11)再生滑阀吹扫蒸汽
3.16安排好操作及保运人员,包括工艺操作人员和设备、电气、仪表维护人员及施工保运人员。
3.17搞好现场卫生,清除杂物,拆除反再区内的脚手架及临时电线等。
3.18各种安全措施落实,消防器材和灭火器按规定数量、地点放置。
3.19烘干前组织专业小组检查有关管线、平台、梯子是否有膨胀余地,并作好测量工作。
3.20主风机、增压机处于良好状态,并达到开机条件。
3.21所有参加烘干的操作人员和技术人员对烘干方案已熟练掌握。
3.22外取热汽包,余热锅炉汽包产汽阀关闭,放空阀打开,水汽系统具备给水产汽及煮炉条件。
4气密试验:
4.1反应再生系统压力控制回路:
序号
位号
工位注释
用途
二次表位置
1、
PRCA-52101AB
再生器压力
记录指示
调节报警
DCS界面
2、
PRCA-52101C
再生器压力
指示调节
DCS界面
3、
HIC-52101
沉降器放空
指示手操
DCS界面
4、
大油气管线放空
手动
4.2打开沉降器顶放空蝶阀、大油气管线放空阀、大盲板前放空阀及提升管底部放空阀;打开再生、待生单动滑阀;全开双动滑阀、外循环管滑阀;打开外取热器的放空阀;关闭烟机入口闸阀;烟机出口水封罐上水;关闭水、汽、风、油等进入两器的一次阀。
4.3反应岗位检查无问题后,联系主风机岗位,将主风缓慢引向再生器、沉降器,进行吹扫。
此时辅助燃烧室的一、二次风DN800蝶阀全开,风量控制在2400Nm3/min。
4.4吹扫一小时试通所有放空后,关小所有放空阀,缓慢关小双动滑阀,逐渐将再生器压力提至0.29MPa(表压),沉降器压力0.26MPa(表压),进行气密实验(在主风机不喘振的前提下尽量提压)。
4.5用肥皂水详细检查反应--再生系统、外取热、三旋及烟道所有靠器壁一次阀前的法兰、人孔、焊口是否泄漏,如泄漏及时联系处理。
4.6气密试验检查出的问题全部处理完后,缓慢打开双动滑阀、沉降器顶及大油气线顶放空阀进行撤压。
5两器烘干
5.1烘干流程
5.2烘干排风点:
A高点排气:
沉降器顶放空
沉降器出口大油气线放空
分馏塔油气线入口大盲板前放空
三旋回收细粉储罐V2105顶放空
双动滑阀至烟囱
四旋至临界喷嘴后到烟囱
B低点排气:
烘干期间,稍开下列低点放空
a分馏塔油气线盲板前
b烟气轮机入口高温闸阀前
c三旋回收细粉罐底
d提升管底部
5.3反再升温的操作原则
5.3.1在升温过程中,尽量保持烧焦罐、再生器、外取热器、外循环管的升温、恒温速度一致,沉降器与提升管的升温速度一致。
5.3.2对沉降器、提升管的升温,一方面靠待生、再生滑阀的开度,另一方面应控制反再合理的差压,保证有足够的热风通过反应部分,从沉降器顶放空及油气线放空排出。
5.3.3对再生系统、点炉前后的升温方法有所不同,点炉前,主要靠进入各部分的风量调节升温速度,点炉后,外取热器、外循环管主要靠来自再生器热风升温,应减小外取热器流化风、提升风、外溢流管流化风,达到保护分布器的目的即可。
5.3.4烘干时原则上不控制风量,有多少用多少,各点的温度通过相关阀门来控制。
5.3.5各点温度调节方法
5.3.5.1烧焦罐、再生器:
主风升温期间,调节通过主风分布管、大孔分布板风量达到调节目的。
辅助燃烧室点火后主要用瓦斯或燃料油量调节炉膛温度达到调节目的;
5.3.5.2提升管:
通过调节再生滑阀开度及反再压差达到调节目的;
5.3.5.3沉降器:
通过调节再生滑阀和待生滑阀开度及沉降器顶放空开度及反再压差达到调节目的;
5.3.5.4外取热器:
通过调节外取热器滑阀及放空阀达到目的;
5.3.5.5外循环管:
通过调节外循环管滑阀开度达到调节目的;
5.3.5.6大油气管线:
通过调节大油气线上放空及分馏塔盲板前油气线放空达到调节的目的。
5.4两器系统烘干升温曲线
5.4.1两器系统烘干升温速度
温度升温速度所用时间
30—150℃升温6℃/h20h
150±5℃恒温0℃/h24h
150—315℃升温10℃/h18h
315±5℃恒温0℃/h36h
315—540℃升温20℃/h12h
540±5℃恒温0℃/h30h
500—100℃降温-20℃/h26h
两器烘衬里时间共计166小时,两器烘干升温曲线如下图。
5.4.2两器系统烘干基准温度
5.4.2.1烧焦罐密相:
基准温度TI52132A,参考温度TI52132B-D。
5.4.2.2烧焦罐稀相:
基准温度TI52130A,参考温度TI52130B。
5.4.2.3再生器密相:
基准温度TI52129A,参考温度TI52129B-D。
5.4.2.4再生器稀相:
基准温度TI52126A,参考温度TI52126B-D。
5.4.2.5沉降器上部:
基准温度TI52111A,参考温度TI52111B。
5.4.2.6汽提段:
TI52116。
5.4.2.7外取热中部:
基准温度TI52143A,参考温度TI52142B。
5.4.2.8大油气线出口:
基准温度TIA52109。
5.4.2.9大油气线大盲板前:
基准温度TIA52216。
5.4.2.10辅助燃烧室温度TI52153,参考温度TI52149,TI52151。
5.4.2.10辅助燃烧室出口:
基准温度TI52155。
5.5两器烘干步骤及操作法
烘干步骤
各点操作方法及注意事项
①改好主风流程,检查主风线路各阀阀位;改好烟气流程后按规程启动主风机。
关闭待生、再生单动滑阀,开大双动滑阀,按规程启动主风机,将主风缓慢引入烧焦罐和再生器。
在主风机干燥时,F2101炉膛温度和混合室温度通过进风量控制,炉内压力由双动滑阀控制。
②两器气密试验没问题后,再生器以6℃/h的速度升温,升温至150℃后恒温24小时。
在再生器升温到125±5℃时,可将大小加料线打开,让热风进入V2101、V2102、V2103进行热干燥。
通过调节主风量、主风放空、双动滑阀开度,由进入再生器的热风量调节再生器升温速度,外取热器升温要通过调整外取热单动滑阀和上下两个放空,外取热升温与再生器尽量同步,要保证恒温时间。
③沉降器以4℃/h的速度升温,升温至110℃后恒温24小时。
打开待生、一二段滑阀,使热风进入沉降器,沉降器顶放空阀打开,提升管底部排凝(DN100)打开,调节再生器压力稍多于沉降器,调节待生、再生滑阀开度,控制稳升温速度,使提升管、汽提段、沉降器同步升温。
④再生器150℃、沉降器110℃恒温结束后,调节再生压力为0.05Mpa,点F2101瓦斯火,按升温曲线继续升温。
1、点火后,要保持最小火焰2--4小时,炉膛温度升起后继续对混合室进行烘干,温度不能超过900℃,混合室温度不能升的过快。
2、在烘混合室时要兼顾两器衬里,当两器达到某一温度时,混合室即使未达到某一温度,也要保证两器的恒温。
3、当混合室烘炉结束后为保证两器继续升温,要对炉外进行全面检查,注意各部位没有过热点。
⑤再生器以10℃/h的速度升温,升温至315℃后恒温,沉降器以6℃/h的速度升温,升温至250℃后恒温。
在此过程中再生器、沉降器压力控制要适当。
在保证沉降器升温的同时,还要保证双动滑阀的开度,要有足够的热风去烟囱干燥,在升温时还要及时检查各点温度,并调整各阀门的开度,保证四器各点温度基本同步进行。
特别是提升管与沉降器的同步。
⑥再生器按315℃恒温36小时,沉降器250℃恒温24小时后,继续升温。
1在再生器升温和恒温过程中,要及时调节再生和待生滑阀开度,要观察一二段提升管出口温度、底部温度、汽提段下部温度,保持各点温度升幅相同,
2另外还要观察降压孔板前后温度(TI52412及TI52413),避免烟气温度忽升忽降。
3再生器在315℃恒温期间要向外取热器盘管通入保护蒸汽,并检查各部位人孔、焊口,并联系进行热紧。
⑦如两器温度升不起来,可切换油火后继续升温。
F2101切换油火步骤:
①稍开火嘴雾化蒸汽。
②缓慢打开油火嘴手阀,密切注意炉膛温度及燃烧情况,并调整雾化蒸汽量和燃烧油量,使火色亮黄。
③关小瓦斯火嘴手阀,避免炉膛温度升得过快。
④根据再生器温度和炉膛温度调节燃烧油量。
⑤及时对蒸汽、燃料油排凝脱水。
⑧切换油火后,再生器以20℃/h的速度升温,升温至540℃后恒温,沉降器以5℃/h的速度升温,升温至315℃后恒温。
在升温过程中,每半小时活动单动滑阀一次,活动范围在30%,适当活动双动滑阀,并检查各阀机械运转情况和控制情况,此时不准向四器内喷蒸汽。
⑨再生器540℃恒温30小时,对烟气管线和三旋系统的衬里进行干燥。
沉降器温度315℃恒温24小时后继续升温至450℃,可开大分馏塔大盲板前放空使油气线干燥。
在此期间,可提高主风量,提高炉出口温度,稍降两器压力,保证双动滑阀开度,增加烟道热风流量,对烟道进行干燥。
⑩四器系统烘干过程中,视需要对烟机进行热态试车。
逐渐关小双动滑阀,同时逐步关小沉降器顶放空,放掉烟机出口水封罐(V2106)大水封、建立小水封,并准备引进烟机对烟机进行热态试车。
具体操作见《烟机试车方案》。
⑾烟道烘干完,烟机试车完后以≯20℃/h的降温速度,降再生器、沉降器温度,到250℃后F2101熄火。
F2101熄火后,要关闭所有瓦斯,燃料油火嘴,并加盲板,停止主风进入四器,让其冷却到100℃以下。
烘干后与四器连接的所有蒸汽关严,严防蒸汽进入四器。
6烘干后的检查
当系统温度降到40℃以下时,进行系统内部全面大检查,检查内容如下:
6.1检查内部衬里有无脱落、裂纹、鼓包等现象,如发现损坏情况超过规范要求时,按《衬里施工及验收规范》要求进行修补。
6.2检查所有旋分器料腿,各立管、套管有无变形现象。
6.3检查旋分器的翼阀的密合程度,是否灵活好用;
6.4检查各分布管有无显著变形及烧坏现象。
6.5检查各立管、导向支架及料腿等有无裂纹及损坏。
6.6检查三旋内部膨胀节有无裂纹及损坏。
6.7检查外取热盘管有无异常现象。
6.8检查燃烧油喷嘴、热电偶、测压点及两器内部构件有无损坏和变形。
6.9检查烟气管线、提升管等处的膨胀节有无裂纹、变形及损坏现象。
6.10检查大油气管线热膨胀情况,立管是否垂直,横管膨胀受力情况。
7烘干注意事项
7.1烘干开始,烟气不进余热锅炉直接进烟囱,当余热锅炉烟气温度达到150℃时,烟气改进余热锅炉烘干,并按余热锅炉煮炉法对余热锅炉进行煮炉。
7.2150℃至315℃升温阶段,升温要控制平稳,严禁出现降温现象,315℃恒温阶段,要控制温度在土5℃之间波动。
7.3烘干期间,每一小时活动一次单动和双动滑阀,检查其机械和控制情况,活动速度要慢,避免造成压力波动。
7.4随时检查单双动滑阀上的吹扫风、仪表测压点的反吹风是否畅通,以防堵塞。
7.5经常检查两器有关管线、平台、梯子的膨胀情况,重点检查烟风管线上膨胀节的膨胀情况,并做好膨胀节的温升与膨胀点之间关系的测量和调整工作。
7.6烘干过程中,应严格按照曲线要求升温,控制好升温速度,密切注意F2101的燃烧情况,严禁出现超温造成设备损坏以及衬里鼓包现象,及时对瓦斯、燃料油、非净化风和蒸汽进行脱水排凝并随时检查液化气罐和燃料油罐液面,避免出现炉子熄火。
7.7烘干期间,F2101炉膛T≯850℃,主风分布管下部T≯580℃,并派专人负责炉子的点火和维护,不得熄火。
7.8烘干期间,严禁向系统喷水、喷汽,有关管线应加好盲板。
7.9烘干过程中,每小时作一次记录,绘出实际的烘干曲线。
7.10F2101烘炉与两器烘干同步进行。
7.11外取热温度达到350℃时外取热管束应通上保护蒸汽。
过热蒸汽盘管及汽提蒸汽盘管、防焦蒸汽盘管当两器温度达到350℃时通上保护蒸汽。
7.12烘干过程中,余热锅炉、三旋及烟气管道烘干与四器同步进行。
7.13烘干期间,加强提升管底部、废催化剂细粉罐、烟机入口高温闸阀前放空,分馏塔大油气管线盲板前放空。