无心磨.docx
《无心磨.docx》由会员分享,可在线阅读,更多相关《无心磨.docx(12页珍藏版)》请在冰豆网上搜索。
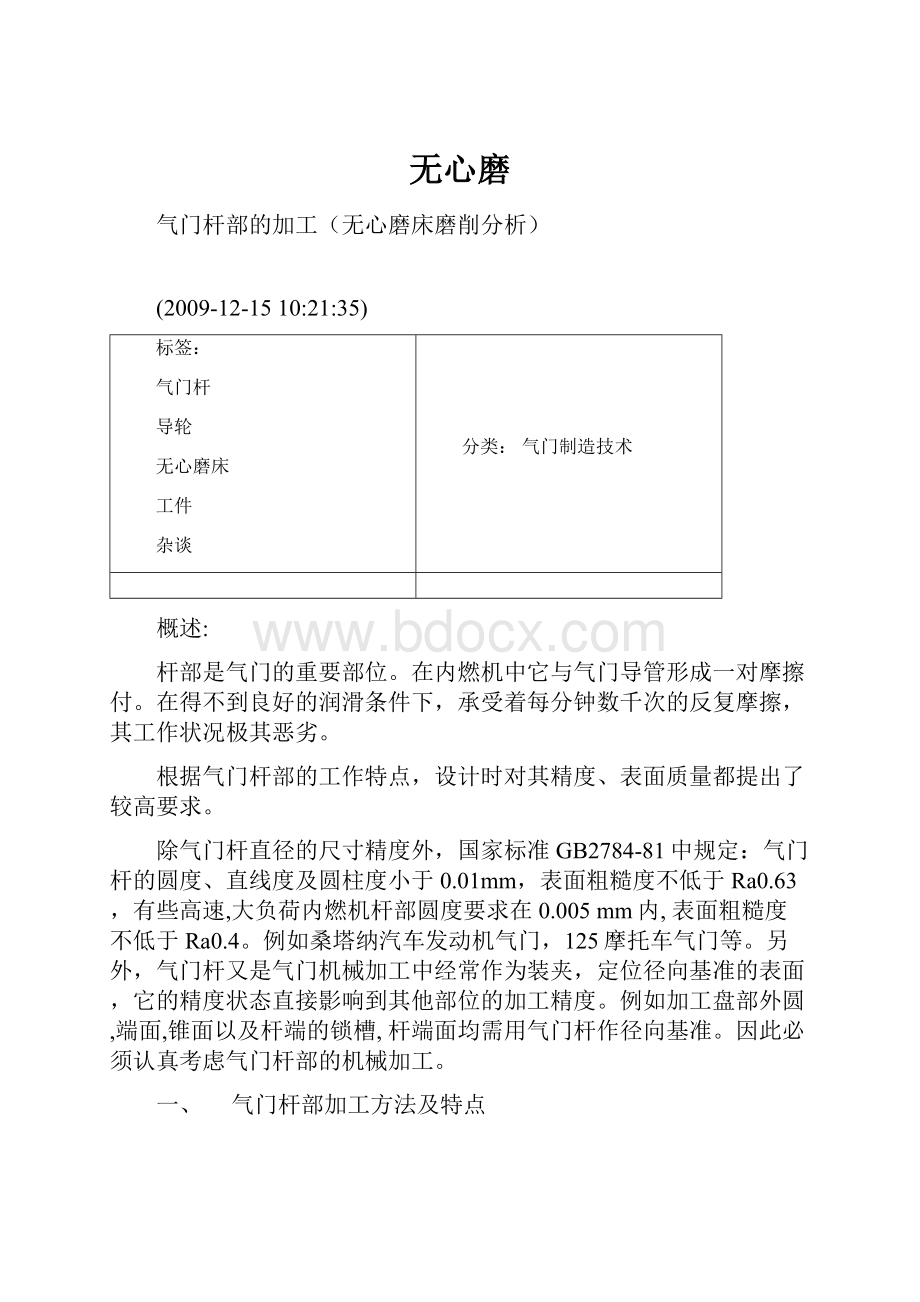
无心磨
气门杆部的加工(无心磨床磨削分析)
(2009-12-1510:
21:
35)
标签:
气门杆
导轮
无心磨床
工件
杂谈
分类:
气门制造技术
概述:
杆部是气门的重要部位。
在内燃机中它与气门导管形成一对摩擦付。
在得不到良好的润滑条件下,承受着每分钟数千次的反复摩擦,其工作状况极其恶劣。
根据气门杆部的工作特点,设计时对其精度、表面质量都提出了较高要求。
除气门杆直径的尺寸精度外,国家标准GB2784-81中规定:
气门杆的圆度、直线度及圆柱度小于0.01mm,表面粗糙度不低于Ra0.63,有些高速,大负荷内燃机杆部圆度要求在0.005mm内,表面粗糙度不低于Ra0.4。
例如桑塔纳汽车发动机气门,125摩托车气门等。
另外,气门杆又是气门机械加工中经常作为装夹,定位径向基准的表面,它的精度状态直接影响到其他部位的加工精度。
例如加工盘部外圆,端面,锥面以及杆端的锁槽,杆端面均需用气门杆作径向基准。
因此必须认真考虑气门杆部的机械加工。
一、 气门杆部加工方法及特点
对气门杆的加工,一般都是在无心磨床上通过几次磨削来完成。
无心磨床磨削与外圆磨床磨削比较有如下几个特点:
(一)无心磨床磨削
1、工件不用顶针或其它定心夹具来夹持,而是“自由”地放置在导轮与(刀板)砂轮之间,工件装卸方便,生产效率高。
(所谓顶针用在无心磨床上,只是起着轴向窜动定位作用)
2、工件的磨削表面,就是定位基面。
所以工件表面原有误差,即气门毛坯的杆部表面或前一道磨杆工序的杆部表面以及磨削过程中刚产生磨削层的误差,都会反映为定位误差,因而影响到工件表面在磨削部分的形状,尺寸,从而反映为加工误差。
毛坯杆精度要影响下一道工序,需要钢厂提供圆度质量好材料。
3、工件运动是由砂轮,导轮共同控制的。
工件运动的稳定性、均匀性不仅取决于机床传动链,还与工件、导轮及刀板的实际情况(如工件中心高h,刀板顶角F等)有关。
(二)外圆磨床磨削
1、工件必须用套筒顶住,完成定心夹持,工件装卸相对麻烦一些。
上海气门厂前期曾经使用盘部外圆用整只转动套筒,杆端用半只开口呆套筒。
(呆套筒指不转的套筒)
2、只要是定位基准准确,机床有足够的精度,工件即可磨圆(在磨削余量充足的条件下)。
其形状精度不受工件表面原有精度影响。
曾有一些气门单位因材料来自钢厂为多角形材料,圆度质量较差,只能采用这种磨削。
3、工件的运动仅取决于机床传动链。
二、 气门杆部磨削加工工艺分析
从上述分析特点可知,采用无心磨床磨削工件装卸方便,生产效率高,很适合应
用于气门大批生产,但由于无心磨削时,磨削面就是定位基准面,有许多不稳定因素存在,为保证质量,必须采取相应技术措施,结合加工工艺进行分析。
(一)加工阶段(工序)的划分
气门杆部加工阶段(或工序)对不需镀铬的气门而言,杆部磨削分三个阶段,共计磨削五次。
(毛坯杆余量国内气门厂一般都采用0.5mm)
第一阶段称为粗加工阶段:
①第一次粗磨,磨削量0.20mm,②第二次粗磨磨削量0.15mm。
第二阶段称为半精加工阶段:
①第一次半精磨(初磨)磨削量0.08mm,②第二次半精磨(光磨)磨削量0.04mm。
第三阶段称为精加工阶段:
精磨磨削量0.03mm。
对于杆部镀铬或氮化气门往往根据具体情况而定,例如镀铬气门采用薄层镀铬工艺,则可在第二阶段的第二次半精磨后或第三阶段的精磨后进行,此后再采用拋光或精磨。
则氮化气门只能在第三阶段的精磨后进行,此后采用研磨机擦光。
上述第一个阶段到第三个阶段均采用无心磨削。
伊顿公司毛坯杆余量采用0.30mm,直接分三次磨削:
粗磨0.20mm、光磨0.07mm、精磨0.03mm。
在锥面磨削时,都采用气门杆作径向定位基准。
若采用“三辊”夹具,则夹具与气门杆作相对运动,在气门杆上必留下夹辊印,因此气门杆必须再作一次无心磨削,此时锥面对杆的跳动必然会受到影响。
若采用“定心”夹具(如弹簧夹头,薄壁夹头等),夹具与气门杆不作相对运动,锥面磨完后不可能在气门杆上留下夹具印。
因此这时的气门杆就是精磨杆,能保证锥面对杆的跳动。
先磨锥面后精磨杆的工序将逐渐淘汰,后者将逐渐推广。
上海气门厂引进美国LANDIS机床就是薄壁夹头夹具,其锥面磨削精度都取决于气门杆的精度,尤其是气门杆的圆度。
为了确保锥面对杆的跳动在0.03mm内,伊顿公司把锥面磨削放到精磨杆后面,锥面磨削夹具用高精度弹簧夹头。
(二)无心磨磨削区域对杆部加工精度的影响及正确选择与调整
图一
注解:
:
砂轮转向 :
导轮转向 :
工件转向 :
砂轮直径 :
导轮直径 :
工件直径 :
砂轮中心 :
导轮中心 :
工件中心 :
(托板)刀板角度
1:
砂轮; 2:
导轮; 3:
调整垫片 4:
托架 5:
(托板)刀板 6:
工件
A:
砂轮、导轮中心连线至机床托架底面的高度
H:
气门杆(或图一尺寸的圆柱棒)顶面至托架底面的高度
h:
工件中心高(工件中心到砂轮和导轮中心-连线垂直距离)
γ:
切削角
从图中所知,过砂轮中心,工件中心及导轮中心作剖面,此时的图形称为“磨削区域”。
砂轮、导轮的几何形状及工件所处的空间位置(工件中心高h),决定了磨削区域的形状,该形状正确与否,对气门杆部的磨削精度,生产效率有着十分密切的关系。
因此,具体分析造成磨削区域形状变化的主要原因,从而做到正确的选择与调整,进而保证杆部加工精度的目的。
从图中看出,具体影响磨削区域变化的主要因素是:
砂轮、导轮直径的大小及工件中心相对砂轮、导轮的位置;此位置除工件直径外,还取决于刀板(托板)的高度,刀板(托板)的角度F和导轮相对刀板(托板)的距离等。
从理论上讲,磨削区域是一个瞬时变化的几何形状。
因而一个绝对理想,正确的磨削区域是不存在的。
只有通过计算,确定一个相对稳定的磨削几何区域,而后通过调整来达到。
目前国内的气门制造厂极大多数使用M1080无心磨床,其砂轮和导轮的标准直径是Dg=F500mm,Dr=F300mm,其直径比一般在0.6~0.8(导轮/砂轮,即Dr/Dg)。
加工制造气门的杆径大多也都是d=6mm~13mm,这样也确定了导轮与和刀板(托板)之间的距离在一个较小的范围内调整,(因考虑到刀板(托板)刚度,在保证气门杆径得到磨削的情况下,尽量厚一些,故限制了导轮相对工件的调整量)。
所以,磨气门杆部时调整磨削区域的问题,也就是调整气门中心高h的问题。
也就是说,在气门杆部直径一定时,选择刀板(托板)角度F和调整刀板(托板)高度问题。
刀板(托板)角度F的选择,一般取F=60。
。
若取F=45。
或F=30。
其刚性较差,磨削时因振动产生较大变形,因而生产上不宜采用。
由于取F=60。
,此时仍有一个较宽的磨削稳定几何区域,其使用刚性又好,这样可以减少更换不同直径气门时调整的辅助时间。
刀板(托板)高度的调整,一般是通过调整垫片3(见图一)来实现。
这里介绍一种通过计算公式来确定工件中心高度h的方法:
h=。
´
切削角r比较难测定,一般选 单位:
度。
工件中心高的实际测量方法,一般是在磨削区先放置一被加工气门或同气门杆径相同的圆柱棒,然后通过测量气门杆(或圆柱棒)顶面至托架底面高度,再通过以下公式换算而得:
H=A+h+
变换后得
h=H_(A+ 此数据可与
(1)式计算值进行比较,若相差较
大,可调整垫片3,直到差不多为止。
(2)、(3)式中A为砂轮、导轮中心连线至机床托架面的高度。
无心磨床说明书中都列出了该数值。
为了使用方便,现列出了几种常用机床面A尺寸的高度。
M1080无心磨床, A=210mm
M1083无心磨床, A=210mm
M10100无心磨床,A=255mm
M1086无心磨床, A=260mm
(三)磨削参数对杆部圆度的影响
1、砂轮线速度对杆部圆度的影响
提高砂轮线速度,采用高速磨削,可以提高无心磨削的成圆效果。
在单位时间内金属磨除量为常数的情况下,高速磨削可使平均厚度减小,降低磨削力,减少杆部原有的圆度误差。
2、工件每转进给量大小对工件圆度误差的影响
一般情况下,工件每转进给量大,则工件原有的圆度误差减少的快,但最终残留
的圆度误差大。
工件每转进给量小,则工件原有的圆度误差减少的慢,但最终残留的圆度误差小。
生产实践证明,适当增加磨光时间能改善工件圆度误差。
通常我们在不增加砂轮进给量时,继续磨削一些时间,能改善工件杆部圆度误差,上海人讲“吞”一下。
3、工件转速对圆度误差的影响
生产实践证明:
在一定磨削条件下,适当提高工件转速,工件原有圆度误差消除较快,残留圆度误差也小。
据有关部门资料介绍,工件的圆周线速度在0.37m/s最好,当增至0.67m/s时,工件的圆度误差又呈增加趋向,目前推荐的圆周速度一般为0.3~0.5m/s。
工件的圆周线速度取决于工件直径和其旋转速度。
工件直径大,则可通过导轮转速减慢,从而降低工件转速达到工件圆周线速度不变目的。
线速度计算公式v=n,n为工件转速,r为工件杆的半径。
为保持线速度为一个恒值,转速与杆径成反比。
转速可由导轮控制,一般链轮控制导轮转速,只有二档速度,一档高速,只作修整导轮用,另一档低速用作气门杆径磨削用,尽管在气门直径变化范围不太大的情况下,低速档都能用。
有的无心磨床导轮备用直流电机可控硅调压无节调速,这样就可适用不同杆径的气门磨削,无锡机床厂专门为援罗马尼亚项目设计WX-036是导轮无节调速。
但维修麻烦,像贵阳险峰机床厂出的M1080皆为链轮单速,维修方便。
(四)轴向定位对杆部精度的影响
无心磨床有窜入法和切入法两种。
窜入法适用于棒料磨削加工,气门制造工艺中也有采纳之处。
比如,杆与杆(21-4N+4Cr9Si2)摩擦焊接之后,由于夹具和机床相对位置误差存在,往往放点余量,然后在无芯磨床上,窜入式磨削,则经过窜入式磨削后的杆料取其中间值保留为其杆径,无心磨削把两部分弯曲变形部分都磨削了。
当然弯曲变形严重者不可能一次窜入式就能磨成圆柱度理想的棒材,需要多次重复,而且切削量是越少越好。
我们曾经试制过几根试棒,需要耐心,才能出精品。
限于气门的几何形状,气门杆部的磨削方法只能采用切入法,为防止气门轴向窜动,一般都将导轮倾斜一个不大的角度,»0.5。
,保证气门杆端面与顶针接触。
在气门杆部磨削之前,适当提高杆端面的精度相当重要。
尤其是杆端面对杆的垂直度,若较差,则直接影响杆的磨削质量。
因顶针不可能是点接触在杆端面中心点上,有时侯是不接触,甚至偏接触,则磨削时易产生振动,或杆偏斜等。
易造成杆圆度差(杆带锥度),因此提高杆端面质量很重要,尤其是在最后一次精磨杆时,必须有一个精度相当高的杆端面才行。
顶针设计,安装正确与否,对气门杆部磨削质量也有很大影响。
具体分析如下:
1、见图二
(1),通过调整顶针轴向定位位置,达到控制气门杆部磨光长度的目的。
一般在安装调整顶针时,将位置按气门杆部的磨光长度的上偏差调整,避免因砂轮靠近气门颈部处的脱粒较其他磨削部位脱粒快,而造成磨光长度不足,或为了顾及磨光长度,而频繁修整砂轮,造成砂轮、修整刀具(金刚笔)的损耗,影响生产效率。
2、在不划伤气门杆端面的条件下,尽量减小顶针与气门杆端面接触面积,并且尽可能把顶针尖端调在气门杆端中心位置上,避免两面接触过大或顶针尖端偏接触,在轴向力的作用下引起振动。
调整顶针尖端对准气门杆端回轴中心,其根本目的是避免磨削时造成气门跳动而影响加工精度。
3、由于气门杆径较小,砂轮、导轮间的空间所限,顶针不可能做得粗大,刚度较差,磨削时在轴向贯穿力的作用下易产生振动,从而影响加工精度。
曾记得在调试磨削XF125易初摩托车气门锁夹槽WX-036改装无心磨床时,遇到顶针细的问题,因XF125杆径只有F5.5。
顶针选择F5,使用F5杆径刚性较差,直接影响工件磨削质量,经比较后选择图二(3)顶针结构解决问题,并且在安装时尽量减小悬臂的长度,以增强顶针刚度。
为了确保磨杆长度,延长砂轮使用寿命,TRW工艺上安排第一次磨杆之前车一次接口。
有时顶针兼用二职,既当顶针又当打料杆,这样一来在使用时易在杆端上产生印子,对精磨后的气门外观不漂亮。
TRW采用了如下结构:
①是打料杆 ②扁形顶针 ③气门
三、气门杆部表面质量的影响因素及解决办法
气门杆部磨后产生缺陷的种类很多。
主要有振纹,磨削面或近杆端側角处磨伤,表面擦伤,表面螺旋状磨痕、烧伤等。
1、振纹 明暗相同的轴向条纹痕迹即为振纹,一般情况下发生在气门杆部近顶部端。
有时振纹也有贯穿杆部全长的。
发生振纹的主要原因是工艺系统的振动。
可能引起的原因是:
①工件中心高调整过高。
②工艺系统刚性不足。
如托架太薄或顶针悬臂过长等。
③砂轮没有及时修整或修整质量达不到要求。
④金刚石修整器夹座刚性不足,金刚石修整刀具过钝。
⑤砂轮硬度过高。
⑥砂轮平衡质量不好,或砂轮使用一阶段后失去了原有的平衡状态。
⑦磨削余量过大。
⑧机床主轴(砂轮轴、导轴轴)间隙过大或导轮及砂轮传面动链精度不够。
⑨外源振动
2、磨伤或擦伤
⑴气门杆部的磨伤或擦伤比较容易发现,一般近杆部两端处为多。
产生原因分析如下:
当采用自动上下料装置出现杆部磨伤时,大多是落料顶杆的顶出方向与砂轮表面素线不平行或顶杆与杆部接触面位置不当,或顶落速度不当所致。
在杆部精磨工序或半精磨工序时,由于磨削余量较小,上道工序落料时如果产生磨伤,下道工序磨削时又不能完全消除,也是造成杆部有磨伤缺陷的原因。
此外,砂轮、导轮一旦修整后,必须在面见一端打圆,去锐角,防擦伤。
当采用手动上下工件出现杆部磨伤时,主要是由于装卸气门杆部未沿导轮面出入,造成气门杆部砂轮相碰,形成磨伤。
强调操作时产品杆必须沿着导轮面圆弧线平行进出,当然气门杆不能碰导轮。
⑵杆的磨削余量过小,中心高h过高,刀板(托板)顶角F过小,导轮表面淤塞以及导轮与杆部摩擦系数下降等原因,引起工件运动的不稳,工件与导轮间发生较大的滑动,导轮控制工件的能力下降,工件回转速度不均匀或工件短时间内停止转动而被磨伤,此时多属于贯穿杆部全长的磨伤。
⑶粗磨杆部时的擦伤,一般不被人们注意,因为擦伤痕迹较浅。
精磨杆部出现的擦伤,就要报废了。
主要是气门杆部与刀板摩擦而引起。
顾海峰工程师曾经叫我分析一只产品杆的轻微印子,我讲刀板上有凸出粒子,观察刀板固然存在,由于硬质材料刀板从制造商取来之后,未必已是合适的刀板,从以往经验告诉我们,精磨刀板最好是由粗磨和光磨已用过一个阶段再取来用,最合适。
在磨削过程中,部分脱落的磨粒,结合剂,与切削液中的油脂混合在一起,形成一种油膏状物质,附着在刀板上,磨削光洁的杆部表面与刀板摩擦而造成擦伤。
另外刀板制造精度不高也易造成杆部擦伤。
为解决杆部表面的擦伤问题,保持切削液的清洁是行之有效的方法,尤其是精磨气门杆时更为显得重要。
在冷却装置系统中,最好使用滤清器,磁性分离器或涡旋分离器以净化切削液。
3、磨削表面螺旋状磨痕
磨削表面螺旋状磨痕,用肉眼可以观察到。
轻微的螺旋状磨痕,在灯光下也可以看到,它是一种螺旋状阴暗光亮交替的带状磨痕。
产生的主要原因是砂轮修整速度过快或修整金刚石笔破碎,修整后砂轮磨削表面带有明显的螺旋纹,在切入磨削时将此螺旋纹反映给气门杆表面。
当解决了砂轮的修整质量,可避免螺旋状痕迹的产生。
4、切削表面烧伤
表面烧伤是属于表面组织物理层的变化,严重的烧伤可用肉眼观察到被烧灼的痕迹。
轻微的烧伤经过酸洗后可以发现。
产生杆部烧伤的主要原因是磨削用量过大或磨深不均匀,或是选用的砂轮过硬,切削液不充分所致,或砂轮已无磨削力,需修整,针对性采取措施即可解决。
如适当减小磨削余量,降低进给速度。
选用较软的砂轮,增大磨削冷却液的流量并使其喷射到磨削区域等措施。
5、杆部表面粗糙度的影响因素
除了上述分析如工艺系统的振动、外源振动、切削用量的选择、砂轮的修整等因素外,砂轮粒度的选择更是影响杆部表面粗糙度的重要因素。
气门杆部精磨加工时,选用中等粒度的砂轮或较细粒度的砂轮;粗磨加工时选用较粗粒度的砂轮。
上海气门厂在精磨杆工序时,在M1080无心磨床上选用粒度的砂轮;半精磨工序时选用粒度的砂轮;粗加工阶段选用或粒度的砂轮。
表面粗糙度可分别达到,Ra0.4;Ra0.8;Ra1.6;Ra3.2;左右。
砂轮粒度选择的合适,可明显提高生产效率,但不同气门材料应选择不同砂轮材料,砂轮制造商应提供适合奥氏体气门材料的砂轮和适合马氏体气门材料砂轮给我们。
结束语:
无心磨床磨削是整个气门冷加工中关键工序项次,从气门毛坯杆径到成品杆径往往需要磨削若干次,若采用最先进的工艺和设备,无心磨床磨削次数也不会小于3次。
伊顿公司分三次磨杆(粗磨、光磨、精磨),实际上支持区有些产品还磨杆一次供金加工用。
因为通过无心磨床磨削将要完成和达到如下要求:
①气门杆必须满足几何尺寸及公差要求。
②气门杆圆度达到要求。
③气门杆圆柱度达到要求。
④气门杆表面粗糙度达到要求。
⑤气门杆外观满足要求。
生产线上的锁槽磨床也用无心磨床原理。
一般冷加工生产线上无心磨床配备数量将占据1/4~1/3。
无心磨床操作员水准也是要求最高的,在上海气门厂曾实施岗位工资时,精磨杆工种为最高级,可见其重要性。
在谈到无心磨削众多的技术要求时,一般都是指精磨工序上的要求,也就是最后一道气门杆磨削,粗磨杆和半精磨都是为精磨打好基础,尤其是圆度,从钢铁厂运来的棒材圆度较差,只能一次又一次磨削后才能纠正过来,达到要求。
我们认为凡是会操作精磨工序者,即必会操作粗磨或半精磨(半粗磨)工序。
因此培训目的,就是要培养出一批会操作精磨的操作工,这是高品位要求,也是我们公司要求,请大家努力吧!
在此也提醒操作工,当班结束后,必须清洗机床,进行日保养,爱护设备,才能使机床不失精度。