水泥厂高温风机的变频调速设计.docx
《水泥厂高温风机的变频调速设计.docx》由会员分享,可在线阅读,更多相关《水泥厂高温风机的变频调速设计.docx(42页珍藏版)》请在冰豆网上搜索。
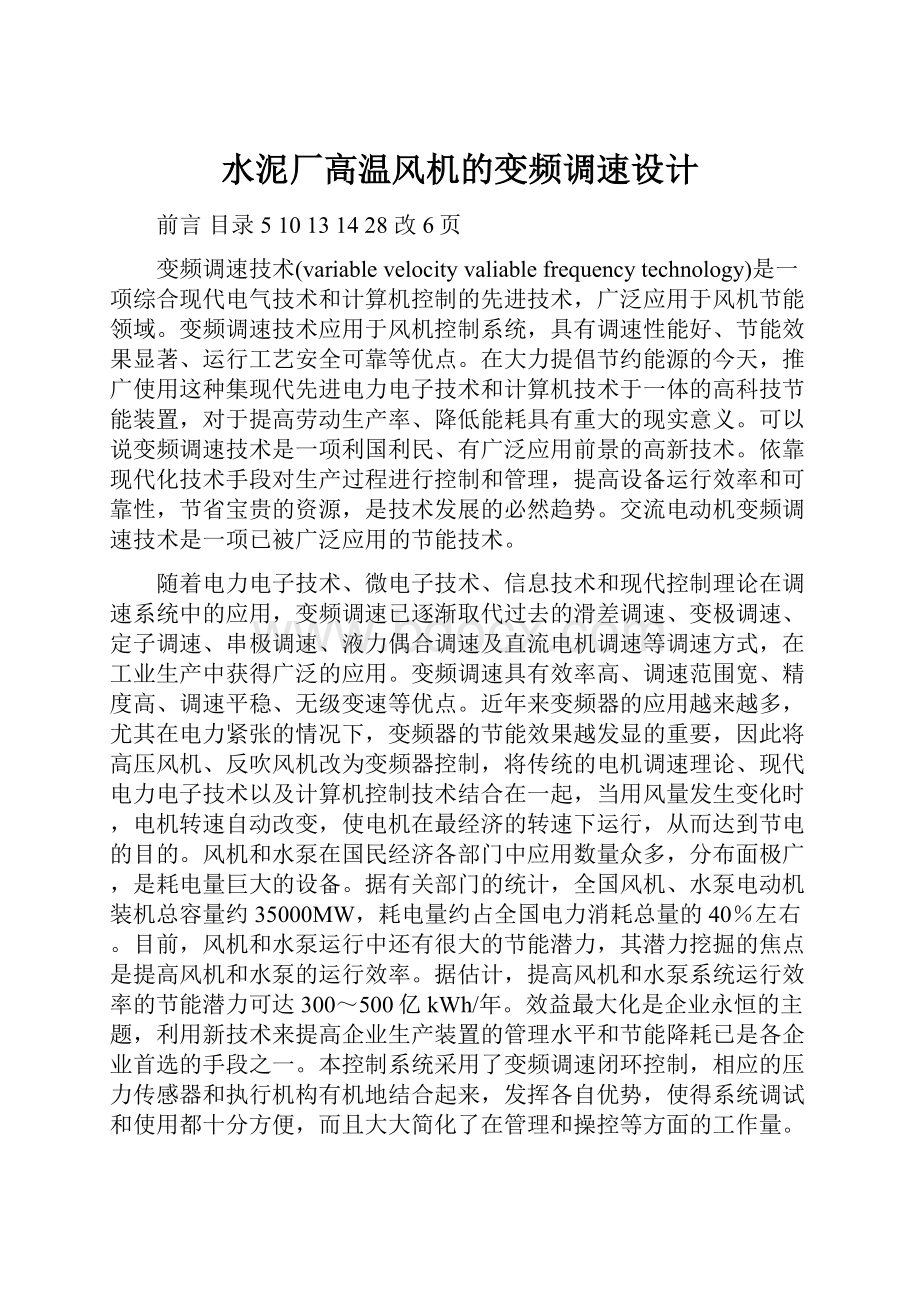
水泥厂高温风机的变频调速设计
前言目录510131428改6页
变频调速技术(variablevelocityvaliablefrequencytechnology)是一项综合现代电气技术和计算机控制的先进技术,广泛应用于风机节能领域。
变频调速技术应用于风机控制系统,具有调速性能好、节能效果显著、运行工艺安全可靠等优点。
在大力提倡节约能源的今天,推广使用这种集现代先进电力电子技术和计算机技术于一体的高科技节能装置,对于提高劳动生产率、降低能耗具有重大的现实意义。
可以说变频调速技术是一项利国利民、有广泛应用前景的高新技术。
依靠现代化技术手段对生产过程进行控制和管理,提高设备运行效率和可靠性,节省宝贵的资源,是技术发展的必然趋势。
交流电动机变频调速技术是一项已被广泛应用的节能技术。
随着电力电子技术、微电子技术、信息技术和现代控制理论在调速系统中的应用,变频调速已逐渐取代过去的滑差调速、变极调速、定子调速、串极调速、液力偶合调速及直流电机调速等调速方式,在工业生产中获得广泛的应用。
变频调速具有效率高、调速范围宽、精度高、调速平稳、无级变速等优点。
近年来变频器的应用越来越多,尤其在电力紧张的情况下,变频器的节能效果越发显的重要,因此将高压风机、反吹风机改为变频器控制,将传统的电机调速理论、现代电力电子技术以及计算机控制技术结合在一起,当用风量发生变化时,电机转速自动改变,使电机在最经济的转速下运行,从而达到节电的目的。
风机和水泵在国民经济各部门中应用数量众多,分布面极广,是耗电量巨大的设备。
据有关部门的统计,全国风机、水泵电动机装机总容量约35000MW,耗电量约占全国电力消耗总量的40%左右。
目前,风机和水泵运行中还有很大的节能潜力,其潜力挖掘的焦点是提高风机和水泵的运行效率。
据估计,提高风机和水泵系统运行效率的节能潜力可达300~500亿kWh/年。
效益最大化是企业永恒的主题,利用新技术来提高企业生产装置的管理水平和节能降耗已是各企业首选的手段之一。
本控制系统采用了变频调速闭环控制,相应的压力传感器和执行机构有机地结合起来,发挥各自优势,使得系统调试和使用都十分方便,而且大大简化了在管理和操控等方面的工作量。
实践证明,本系统不仅提高了水泥厂的经济效益,更是在节约能源、降低噪声美化环境表现出很好的效果。
由于编者的水平有限,设计中不免会存在一些疏漏和不妥之处,恳请指导老师批评和指正。
原始资料
我国水泥厂较多采用立窑配备155~215KW罗茨风机,罗茨风机为容积式风机,输送的风量与转数成比例,三叶型叶轮每转动一次由2个叶轮进行3次吸、排气。
与二叶型相比,气体脉动性小,振动也小,噪声低。
风机2根轴上的叶轮与椭圆形壳体内孔面,叶轮端面和风机前后端盖之间及风机叶轮之间者始终保持微小的间隙,在同步齿轮的带动下风从风机进风口沿壳体内壁输送到排出的一侧。
风机内腔不需要润滑油,结构简单,运转平稳,性能稳定,适应多种用途,已运用于广泛的领域。
又由于采用了三叶转轮及带螺旋线型的箱体,所以风机的噪声的振动很小。
叶轮和轴为整体结构,且叶轮无磨损,风机性能持久不变,可以长期连续运转。
传统的风量控制办法是依靠放风阀进行调节。
由于罗茨风机的供风量较为恒定的,煅烧时根据窑的情况需要随时调节风量,当窑内需要少风量时,通过放风阀放走多余的风量,造成严重的能源浪费。
怎样才能节省放风所浪费的能源呢?
当然最根本的办法是控制罗茨风机的转速,进行风量调节,保证窑内需多少风量就供多少风,完全免除放风所造成的浪费。
水泥厂生产线为干法悬窑,其窑烧成系统流程简图如图0-1所示。
图0-1高压变频典型应用实例
悬窑是一个有一定斜度的圆筒状物,预热机来的料从窑尾进入到窑中,借助窑的转动来促进料在旋窑内搅拌,使料互相混合、接触进行反应,物料依靠窑筒体的斜度及窑的转动在窑内向前运动。
窑内燃烧产生的余热废气,在窑尾高温风机的作用下,通过预热器对进入窑尾前的生料进行预热均化,降温后的余热废气再通过高温风机抽出进入废气处理(除尘及排出)。
XXX水泥厂的1#窑,日产为2500t,到现在运行已近多年。
1#窑生产线,高温风机电机配置为6kV1600kW,窑尾EP风机配置为6kV280kW。
在高温风机的电机与风机之间,配有液力耦合器对风机进行调速,整个工艺过程主要是通过DCS的控制来调节液力耦合器的速度从而调整风机的风量,达到控制窑内负压。
窑尾EP风机依靠风门来进行调节。
由于使用年限较长,目前液力耦合器漏油严重,运行中每天需加油2~3次,以补充漏油,油面调整的控制回路失灵不能自动调节,在运行中只能靠手动调节置于固定转速比。
在运行是时仍靠风机挡板进行风量调节,当窑系统工况变化较大时,现场值班人员根据中控制室的指令对液力耦合器的勺杆进行手动调节,运行操作非常不便。
因此,决定首先对水泥厂1#窑生产线的高温风机进行了变频调速设计。
1概述
1.1变频调速系统的发展与现状
经过大约30年的发展,目前交流调速电气传动已经上升为电气调速传动的主流,在电气调速传动领域内,有直流电动机占统治地位的局面已经受到猛烈的冲击。
纵观变频技术的发展,其中主要是以电力电子器件的发展为基础的。
第一代以晶闸管为代表的电力电子器件出现于20世纪50年代,它主要使电流控制型开关器件,以小电流控制大功率的变换,但其开关频率低,只能导通而不能自关断。
第二代电力电子器件以电力晶体管(GTR)和门极关断(GTO)晶闸管为代表,在20世纪60年代发展起来,它是一种电流型自关断的电力电子器件,可方便的实现变频逆变和斩波,其开关频率只有1~5KHZ。
第三代电力电子器件以双极型绝缘栅晶体管(IGBT)和电力场效应晶体管(MOSET)为代表。
在20世纪70年代开始应用,它是电压场(场控)型自关断的电力电子器件。
第四代电力电子器件,有出现于20世纪80年代末的智能化功率集成电路(PIC)和20世纪90年代的智能功率模块(IPM)、集成门极换流晶闸管(IGCT),它们实现了开关频率的高速化、低导通电压的高性能化及功率集成电路的大规模化。
1.2变频技术的特点
电力电子器件的自关断化、模块化、交流电路开关模式的高频化和控制手段的全数字化促进了变频电源装置的小型化、高性能化,尤其是控制手段的全数字化利用了微型计算机的巨大的信息处理能力,其软件功能不断强化,使变频装置的灵活性和适应性不断增强。
交流调速装置的大容量化、开关器件的自关断化、PWM技术的应用、全数字控制技术的应用,使变频技术的应用领域不断扩大,朝着高度集成化、采用表面安装技术、转矩控制高性能化、保护功能健全、操作简便化、驱动低噪声化、高可能性、低成本和小型化的方向发展。
2变频原理
异步电动机的同步转速,即旋转磁场的转速为
n1=60f1/np
式中,n1——同步转速(r/min)
f1——定子转速(HZ)
np——磁极对数
而异步电动机的轴转速为:
n1=n1(1-s)=60f1/np(1-s)
式中,S——异步电动机的转差率,S=(n1-n)/n1
由上式可见,改变异步电动机的供电频率,可以改变其同步转速,实现调速运行。
变频技术简单地说就是把直流电逆变成不同频率的交流电,或是把交流电变成直流电,再逆变成不同频率的交流电,或者是把直流电变成交流电,再把交流电变成直流电,总之这一切都是电能不发生变化,而只有频率的变化,
变频技术的类型主要有以下几种:
交-直变频技术(整流技术),直-直变频技术(斩波技术),直-交变频技术(振荡技术),交-交变频技术(移相技术)。
2.1交直交变频的基本电路
图2-1交-直-交电压型变频
交-直-交变频电路根据变频电源的性质可分为电压型变频和电流型变频,
2.1.1交-直-交电压型变频
交-直-交电压型变频的构成如图2-1所示,该电路的核心是三相电压型逆变器的基本电路如图2-2所示。
图中,直流电源并联一大容量的滤波电容Cd,由于Cd的存在,使直流输出电压具有电压源的特性,内阻很大,这使逆变器的交流输出电压被钳位为矩型波,与负载的性质无关,交流输出电流的波形和相位由负载功率因数来决定,在异步电动机变频调速中,这个大电容同时又是缓冲负载无功功率的储能元件。
直流电路电感Ld起限流作用,电感量很小。
图2-2三相电压型逆变器的基本电路
2.1.2交-直-交电流型变频
电压型变频,由于再生制动时必须接入附加电路,使电路复杂,电流型变频可以弥补其不足,而且主电路结构简单,安全可靠。
交-直-交电流型变频器的构成如图2-3所示。
图2-3交-直-交电流型变频
图2-4三相电流型逆变器的基本电路
三相电流型逆变器的基本电路如图2-4所示。
与电压型逆变器不同,直流电源上并联了大电感滤波。
由于大电感的限流作用,为逆变器提供的直流电流波形平直、脉动很小,具有电流源特性。
这使逆变器输出的交流电流为矩形波,与负载性质无关,而输出的交流电压波形及相位随负载的变化而变化。
对于变频调速系统而言,这个大电感同时又是缓冲负载无功能量的储能元件。
2.2脉宽调制(PWM)技术
脉宽调制(PWM)就是对逆变电路开关器件的通断进行控制,使输出端得到一系列幅值相等而宽度不等的脉冲,用这些脉冲来代替正弦波或所需要的波形,也就是在输出波形的半个周期内产生多个脉冲,使各脉冲的等值电压为正弦波状,所获得输出平滑且低次谐波少,按一定规则对脉冲的宽度进行调制,既可改变逆变电路输出电压的大小,也可以改变输出频率。
电压型交-直-交型变频电路,为了使输出电压和输出频率都得到控制,变频器通常是由一个可控整流电路和一个逆变电路组成,控制整流电路以改变输出电压,控制逆变电路来改变输出频率。
图2-5所示是电压型PWM交-直-交变频电路,这里由不可控整流电路代替可控整流电路,逆变电路采用自关断器件,这种PWM型变频电路的主要特点:
(1)可以得到相当接近正弦波的输出电压;
(2)整流电路采用二极管,可获得接近1的功率因数;
(3)电路结构简单;
(4)通过对输出脉冲宽度的控制可改变输出电压,加快了变频过程的动态响应。
图2-5PWM变频器的主电路图
其实,PWM变频器就是基本逆变变频器。
当采用PWM方法控制逆变器功率器件通断时,可获得一组等幅而不等宽的矩形脉冲,输出电压幅值的改变,可通过控制该脉冲的宽度,而输出频率的变化可通过改变此脉冲的调制周期来实现。
调压原理:
利用参考电压波Up与载频三角波Uc互相比较来决定主开关器件的导通时间来实现调压,利用脉冲宽度的改变来得到幅值不同的正弦波电压,这种参考信号为正弦波,输出电压平均值近似为正弦基波的PWM方式称为正弦SPWM方式。
脉冲的调制方法对PWM型变频调速技术的发展,作为大容量传动的高压变频技术也得到了广泛的应用。
高压电动机利用高压变频器可实现无级调速,满足生产工艺过程对电动机调速控制的要求,以提高产品的产量和质量,又可大幅度地节约能源,降低生产成本。
2.3高压变频器调速系统
近年来,各种高压变频器不断出现,可是到目前为止,高压变频器还没有像低压变频器那样近乎统一的拓扑结构。
根据高压组成方式,可分为直接高压型和高-低-高型;根据有无中间直流环节,可以分为交-交变频器和交-直-交变频器。
在交-直-交变频器中,根据中间直流滤波环节的不同,又可分为电压源型(也称电压型)和电流源型(也称电流型)。
高-低-高型变频器采用变压器实行输入降压、输出升压的方式,其实质上还是低压变频器,只不过从电网和电动机两端来看是高压的,这是受到功率器件电压等级技术条件的限制而采取的变通办法,需要输入、输出变压器,存在中间低压环节电流大、效率低下、可靠性下降、占地面积大等;缺点:
只用于一些小容量高压电动机的简单调速。
常规的交-交变频器由于受到输出最高频率的限制,只用在一些低速、大容量的特殊场合。
顺便指出,国内习惯称作的高压变频器,实际上电压一般为2.3~10kV,国内主要为3.6kV和10kV,和电网电压相比,只能算作中压,故国外常称为中压变频器。
(1)高-低-高结构
该种结构将输入高压经降压变压器变成380V的低电压,然后用普通变频器进行变频,再由升压变压器将电压变回高压。
很明显,该种中高压变频装置的优点是可利用现有的低压变频技术来实现高压变频,易于实现,价格低;其缺点是使用了降压和升压2台变压器,
系统体积大、成本高、效率低、低频时能量传输困难等。
其拓扑结构如图2-6所示。
图2-6高-低-高变频器结构
(2)多重化技术
采用多重化技术也是用小功率器件实现大功率变换的一种方法。
所谓多重化技术就是每相由几个低压PWM功率单元在其输出端通过某种方式(如变压器)串联或并联组成。
各功率单元由一个多绕组的隔离变压器供电,由低压PWM变频单元串联叠加达到高压输出或并联达到大容量输出的目的。
其中每一个功率单元都是分别进行整流、滤波、逆变的。
目前功率单元都采用二电平方案,开关器件电压等级只要考虑功率单元内的中间直流电路电压值。
多重化技术可以大大降低谐波含量,提高功率因数。
在电压型变频器组成的多重化系统中,为防止由于不同变压器副边绕组电压差而形成环流,通常在副边采取串联方式联接。
相应地,在电流型变频器组成的多重化系统中,副边绕组一般采用并联连接。
但是多重化技术需要引入结构复杂的大容量隔离变压器;所需主管数量较多,增加了设备投入,造价昂贵,还需要占用一定安装空间;多重化技术对控制精度要求也较高。
(3)多管直接串联的两电平变换电路
将器件串、并联使用,是满足系统容量要求的一个简单直观的办法。
串、并联在一起的各个器件,被当作单个器件使用,其控制也是完全相同的。
这种结构的优点是可利用较为成熟的低压变频器的电路拓扑、控制策略和控制方法;其难点是串联开关管需要动态均压和静态均压,因此对驱动、控制电路的要求也大大提高,还需要解决dv/dt,抗共模电压技术、正弦波滤波技术等问题。
国内成都佳灵电气制造有限公司生产的高压变频器采用这种拓扑结构并申请了专利,解决了IGBT直接串联的世界难题,代表了高压变频器的一个发展方向。
其拓扑结构如图2-7所示,它完全舍弃了输入输出变压器,使得IGBT直接串联高压变频器成为目前世界上体积与占地面积最小的产品。
图2-7 二极管钳位型三电平高压变频器
(4)二极管钳位型三电平变换电路
为了解决器件直接串联时所需要的均压问题,逐渐发展出以器件串、井联为基础,各器件分别控制的变流器结构。
在这方面,日本学者A.Nabae于80年代初提出的中点箝位型PWM逆变电路结构具有开创性的意义。
二极管箝位型变流器的结构如图2-8所示,该变流器的输出相电压为三电平。
如果去掉两个箝位二极管,这种变流器就是用两个功率器件串联使用代替单个功率器件的半桥逆变电路。
由于两个箝位二极管的存在,各个器件能够分别进行控制,因而避免了器件直接串联引起的动态均压问题。
与普通的二电平变流器相比,由于输出电压的电平数有所增加,每个电平幅值相对降低,由整个直流母线电压降为一半直流母线电压,在同等开关频率的前提下,可使输出波形质量有较大的改善,输出dv/dt也相应下降,因此中点箝位型变流器显然比普通二电平变流器更具优势。
图2-8为三电平逆变一相的基本结构,V1~V4代表一相桥臂中的4个功率开关,VW1~VW4为反并联的须流二极管,VC1、VC2为钳位二极管,所有的二极管要求有与功率开关相同的耐压等级。
Ed为一组二端,C为中间点。
图2-8三电平基本电路
对于每相桥臂通过控制功率器件V1~V4的开通、关断,在桥臂输出点可获得三种不同电平+Ed、0、-Ed,,见表2-1。
表2-1三电平变频器每相输出电压组合表
V1
V2
V3
V4
输出电压
状态代号
ON
ON
OFF
OFF
+Ed
P
OFF
ON
ON
OFF
0
C
OFF
OFF
ON
ON
-Ed
N
由表2-1看出,功率开关V1和V3状态是互反的,V2与V4也是互反的。
同时规定,输出电压只能是+Ed到0、0到-Ed,或相反地变化,不允许在+Ed和-Ed之间直接变化。
所以不存在两个器件同时开通或同时关断,也就是不存在动态均压问题。
对于由三个桥臂组成的三相逆变器,根据三相桥臂U、V、W的不同开关组合,最终可得到三电平变频器的27种开关模式,见表2-2。
表2-2三电平变频器输出状态表
PPP
PPN
PPC
PCN
PCC
PNN
PCP
PNC
PNP
CCC
CPN
CPC
CCN
CPP
CNN
CCP
CNC
CNP
NNN
NPN
NPC
NCN
NPP
NCC
NCP
NNC
NNP
采用中心点钳位方式使输出增加了一个电平,输出电压的台阶高度降低了一半,而且很重要的一点是增加了输出PWM控制的自由度,使输出波形质量在同等开关频率条件下有较大的提高。
(5)高压大功率变频器控制策略
高压大功率变频器控制技术是高压大功率变频器研究中一个相当关键的技术,它是与高压大功率变频器拓扑结构共生的。
因为它不仅决定高压大功率变频器的实现与否,而且,对高压大功率变频器的电压输出波形质量,系统损耗的减少与效率的提高都有直接的影响。
高压大功率变频器功能的实现,不仅要有适当的电路拓扑结构作为基础,还要有相应的控制方式作为保障,才能保证系统高性能和高效率的运行。
在过去的近20年里,大量的高压大功率变频器控制方法被提出,它们基本上都发源于业己成熟的两电平PWM技术,归纳起来可以分为以下几大类:
阶梯波调制、选择谐波消去法(SHEPWM)、开关频率优化法(SFOPWM)、空间矢量调制(SVPWM)、载波相移PWM调制。
一般说来,衡量一种开关调制策略的优劣从以下几个方面进行分析:
变流器输出的谐波特性、器件的开关频率、动态输出特性及传输带宽等
2.4晶闸管阀串均压技术的应用
本高压变频器为高压变频器,三相高压交流电经变频器直接控制高压控制电压电机。
这种方案的优点式显而易见的,它不需要降、升压变压器系统,故结构简单,设备少,占地面积小,效率也高。
但由于晶闸管制造技术的限制,晶闸管单管电压水平还达不到高压变频器所需要的耐压等级。
为了使变频器的每个桥臂都能承受正常工作所耐受的高电压值,就必须采用几个功率元件串联组成一个阀闸(即一个桥臂)的方法,如图2-9所示,在本装置中,采用七只4000V/200A(KP200)晶闸管串联组成晶闸管阀串,共12阀闸,84只晶闸管。
图2-9晶闸管关断时的均压结构
解决好在各种可能出现的电压下阀串中晶闸管的均压问题,各晶闸管关断和导通的一致性问题,是高压大容量变频器调速装置的关键技术问题。
同一桥臂中串联的晶闸管元件必须同时导通,否则后导通的元件将承受过高压而损坏,这就要求同一阀串中各晶闸管门极触发功率足够大,以保证各晶闸管的同时导通。
本装置中采用脉冲电压器触发,各脉冲变压器的原边通过同以触发电流,因此7只脉冲变压器的副边同时感应出幅值、波形相同的电压,由此保证触发脉冲前沿坡度的一致性和同时性。
同一桥臂中串联的各晶闸管在关断时也必须保持一致,否则先关断的元件也将承受过高压而损坏。
这要求同一桥臂中各晶闸管的参数一致,其差异越小越好。
在本装置中,采用了静态均压和动态均压措施。
2.4.1静态均压
静态均压是指晶闸管处于阻断状态下承受供频电压或直流电压时的晶闸管元件之间的均压。
在这种情况下,电压波形前沿时间较长,可采用电阻R均压。
按均压最恶劣的情况考虑。
设晶闸管SCR1的漏电流量最小,为Imin,其余晶闸管的漏电流均为Imin+△Im,△Im为最大漏电流偏差。
这样晶闸管SCR1承受的反向阻断电压最高,为Um=(I-Imin)R。
其余各晶闸管承受的反向阻断电压为U=(I-Imin-△Im)R。
阀串总电压为Up=Um+(n-1)U,n为阀串中串联的个数。
则:
Up=Um+(n-1)(I-Imin-△Im)R
=Um+(n-1)(I-Imin)R-(n-1)△Im
=Um+(n-1)Um-(n-1)△ImR
=nUm-(n-1)△ImR
均压系数定义为:
K=Uav/Um。
Uav为阀串中每个晶闸管的平均电压,因此,上式可变为:
Up=nUav/K-(n-1)△ImR
由于Uav=Up/n,Up=nUav,故
Up=Up/K-(n-1)△ImR
由此可得到静态平均电阻的阻值R
R=Up[(1/K-1)/(n-1)△Im]
通过此计算值,并与实验值结合,选取:
R=50KΩ
静态平均电压的功耗按公式Pr=Um/R计算,并留有足够的裕量,选取:
Pr=150W
2.4.2动态均压
动态均压是指同一的晶闸管开通和关断过程中的均压,即过度过程中的均压。
如图2-10所示为晶闸管关断的电流波形图。
当晶闸管关断时,电流正方向过零后,并不立即恢复其阻断特性。
由于方向恢复电荷的存在,在晶闸管中形成一个反向恢复电流Itr,反向恢复电荷Qr由下式决定:
Qr=1/2×Itr/0.64式中,Ttr为晶闸管的反向阻断恢复时间。
反向恢复电荷决定了阀串中每个晶闸管所承受的阻断电压值。
当晶闸管仅流过反向漏电流Ir时,即恢复了反向阻断特性,此时观点过程结束,由动态均压转为静态均压。
由此可见,反向恢复是晶闸管关断过程中电压非陪不均的主要原因。
为此,动态均压采用了与晶闸管并联阻容来解决。
设置晶闸管SCR1的反向恢复电荷为Qr1其余晶闸管的反向恢复电荷为Qr2,并且Qr1﹥Qr2,△Qr=Qr1=Qr2。
由于Qr1最大,在关断过程中,SCR1承受的电压最高,为Um=Qr1/C。
其余各晶闸管的电压分配值为U=Qr2/C=(Qr1-△Qr)/C。
总电压为:
Up=Qr1/C+(n-1)(Qr1-△Qr)/C
=nUm-(n-1)△Qr/C
=Up/K(n-1)△Qr/C
由此式可以推出动态均压电容的电容值:
C=(n-1)Qr/[Up(1/K-1)]
按此式计算并通过实验,本装置最终选取:
C=0.47μF
动态均压电阻主要用于限制均压电容C的放电电流,并防止电路产生寄生振荡,其值和功耗按经验选取:
R为25Ω、75W电阻。
图2-10晶闸管关断时的波形
在晶闸管的参数选取中,应十分注意在同一阀串中尽量选择漏电流、反向恢复电荷及门极触发特性一致或接近的晶闸管。
在较长时间的工业运行中,证明上述均压措施和参数选取式正确的。
均压参数K达到0.95。
3风机的基本特性及调速原理
3.1风机的发展概况与使用趋势.
风机被广泛应用在工业生产、民用生活中的各个领域。
小到民用生活的排气扇,大到工业生产中的各种类型,各种功用的通风机、高温风机。
工业生产与民用生活中使用了大量风机和水泵,它们的用电量占整个国民经济用电量的70%以上。
用恒速电动机驱动风机和水泵,需根据季节、时间或生产状态对负载进行调整时,就要同时调整阀门或风门,使之与负荷的变化相适应。
但是采用这种方法,系统从电网吸收的能量并没有减少,电动机输出功率基本没有改变。
虽然阀门或风门的输出量达到了工况要求,但是能量有效应的比例减少,而损耗增加。
在这种情况下,不会有节能、节电效果。
如果对电动机进行速度控制,因为所需动力与扭矩的3次放成比例的减少,从而能实现大幅度的节能,节电效率可达到20%~60%。
3.2风机基本特性
3.2.1风机运行特性
风机属于平方转矩类型负载,在额定转速运行的特性曲线如图3-1所示