车身尺寸控制方法.docx
《车身尺寸控制方法.docx》由会员分享,可在线阅读,更多相关《车身尺寸控制方法.docx(8页珍藏版)》请在冰豆网上搜索。
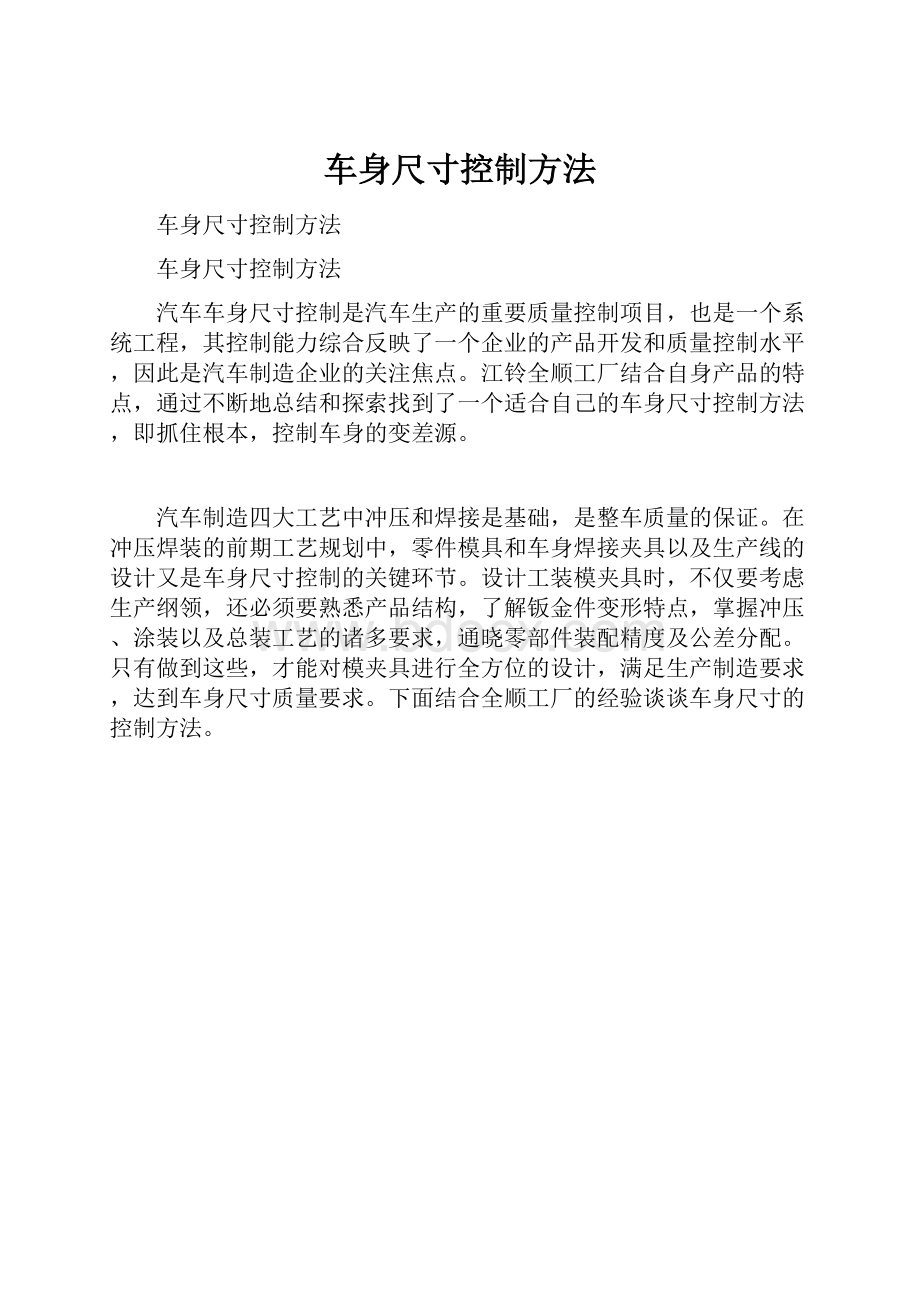
车身尺寸控制方法
车身尺寸控制方法
车身尺寸控制方法
汽车车身尺寸控制是汽车生产的重要质量控制项目,也是一个系统工程,其控制能力综合反映了一个企业的产品开发和质量控制水平,因此是汽车制造企业的关注焦点。
江铃全顺工厂结合自身产品的特点,通过不断地总结和探索找到了一个适合自己的车身尺寸控制方法,即抓住根本,控制车身的变差源。
汽车制造四大工艺中冲压和焊接是基础,是整车质量的保证。
在冲压焊装的前期工艺规划中,零件模具和车身焊接夹具以及生产线的设计又是车身尺寸控制的关键环节。
设计工装模夹具时,不仅要考虑生产纲领,还必须要熟悉产品结构,了解钣金件变形特点,掌握冲压、涂装以及总装工艺的诸多要求,通晓零部件装配精度及公差分配。
只有做到这些,才能对模夹具进行全方位的设计,满足生产制造要求,达到车身尺寸质量要求。
下面结合全顺工厂的经验谈谈车身尺寸的控制方法。
dPH汽车设计网
控制变差源
dPH汽车设计网
在车身开发阶段,有4个阶段会对车身尺寸产生较大影响,分别为产品设计、工艺开发、试生产及批量生产,各阶段产生的影响程度和侧重点不同。
要控制变差源,开发阶段控制占70%,过程控制占30%。
在开发阶段,产品设计和工艺开发尤为重要。
首先,要建立车身统一基准系统,用于统一从冲压件、零件检具、焊接总成、白车身装配,到总装装配的主定位基准原则,建立MCP(MasterControlPoint)清单,便于冲压、焊接、总装工艺在开发定位工装时协调一致,避免因工序定位选择不同而产生偏差。
其次,产品设计要避免冲压成形工艺过于复杂,减少冲压回弹和零件干涉现象,模夹具设计定位必须可靠,如夹具定位孔必须选择传递冲压的主定位孔,定位面必须选取冲压件的可靠面。
再次,工装设计时要便于员工取放料,易于操作和维护,以防生产过程中因人机工程问题造成的尺寸变差。
dPH汽车设计网
表1 车身尺寸合格率与材料状态的对照
考虑到车身钣金件回弹,形状不规则,材质及冲压工艺的影响,车身夹具都采用过定位设计以校正零件变形,而且定位夹紧单元都设计成三维或二维方向可调以适应零件变化。
一般来说,车身夹具设计遵循的原则为:
dPH汽车设计网
1.对单个工件一般用二销二型面的“定位-夹紧”稳定原则。
实质上二销确定了X,Y向,二型面则强化确定了Z向。
对特别大的工件,考虑到钣金弹性件可适当增加销与型面的“定位夹紧”,以增加局部区域的稳定性。
dPH汽车设计网
2.定位尺寸一致性传递原则,即不同工序不同夹具的定位尺寸应一致。
dPH汽车设计网
3.焊点可视原则。
dPH汽车设计网
4.以大尺寸、复杂零部件为先导,其余零件随后装上夹具,即逐次“定位-夹紧”。
dPH汽车设计网
5.定位销精度±0.05mm,定位面精度±0.2mm。
dPH汽车设计网
在试生产前,工装夹具的安装非常重要,只有合格的工装才能生产出合格的产品。
夹具安装到位后,需使用测量设备(如激光跟踪仪)对所有定位孔面进行全尺寸测量,建立完备的定位基准数据,便于生产期间的车身尺寸协调。
一般工装到位后的试生产需要维持6个月,以满足投产不同阶段的质量控制目标。
试生产阶段主要是解决实际零件和工装夹具的匹配协调性,同时解决操作过程中的实际困难,直到到达设计要求的节拍以及质量目标才可转入到批量生产。
dPH汽车设计网
图2 投产各阶段车身尺寸合格率及偏差大小和分布区域
试生产阶段需要准备产品数模、模夹具数模、MCP主定位清单、零件设变清单、焊接工艺卡、产品检具、总装装车问题清单以及夹具调整记录表等相关文件,便于及时在现场排查机器和材料的状态。
dPH汽车设计网
进入批量生产阶段,主要是加强工艺和工装夹具的管理。
首先保证操作完全执行工艺文件,同时工装夹具的定位必须定期监控,及时维护模夹具定位的松动和磨损,保证定位系统完好。
dPH汽车设计网
最后要考虑环境和测量的影响,在恶劣环境下气温高低差会达到30°,定位会产生热胀冷缩现象而影响尺寸。
另外,测量系统必须做测量系统分析,同时还要保证测量定位基准与制造夹具的定位基准一致。
dPH汽车设计网
表2 车身尺寸不合格点的分类统计
数据的收集和分析方法
dPH汽车设计网
车身尺寸数据获取的方式很多,最常用的是通过三坐标测量系统,检具、PCF和UCF等工具都可以检测出实际车身及零部件相对于设计数模的符合性,再对比开发初期就制定好的各测量点公差带以及合格率的要求,从而判定车身尺寸的合格率。
dPH汽车设计网
基于三坐标测量系统的数据,我们每一台车身可以得到多则上千少则数百的整车测量点数据,但是逐个分析没有可能也不必要。
目前,我们的做法是:
先统计不合格点的状态,然后在数据稳定的情况下对生产过程进行确认并整改。
我们现有的经验是关注不合格点的超差情况和分布,同时计算一些总装和顾客关注的需要控制的点的过程能力(CP),通过部分代表的点反映整个车身的质量状态。
dPH汽车设计网
1.数据的分类整理及分析
dPH汽车设计网
在实际工作中,初步数据整理一般把车身分为5大块:
前门洞、前风窗框、后门洞、侧拉门洞以及车身前部(如表2所示)。
通过跟踪每一台车的不合格点,把其记录到表2中所列的不同区块,并记录偏离理论值的偏差,偏差小于1mm的标注绿色,大于1mm但小于2mm的标注为黄色,大于2mm的标注为红色,通过数据的不断积累,可得出各阶段不合格点数据和状态(如图2所示)。
通过表2、图2我们能了解到不合格点的变化趋势和集中的区域,方便关注重点,同时知道不合格点超差的范围,提高紧急度响应。
dPH汽车设计网
2.数据CTQ分析
dPH汽车设计网
CTQ即关键质量控制,是车身尺寸的能力指标,其分析方法是:
选取车身上与装配相关的孔的测量点,(如在开发工装夹具时,我们非常关注:
前风窗框、门洞尺寸、发动机装配孔、前后悬吊装配孔、前后灯具总成件装配孔位、顶盖装配尺寸、仪表板装配孔等),按照顾客关注的特性分别建立子系统单元,约20个左右,每个子系统包含若干个相关的车身尺寸数据点。
以仪表板装配子系统为例,把总装装配仪表板的10个安装孔的测量数据作为一个系统,分别计算这10个孔测量数据的过程能力(CP),然后按照一个科学的判定原则综合判定,得出仪表板子系统综合装配能力:
绿色为过程能力强,红色表示过程能力不足需持续改进。
子系统判定原则为:
在子系统所有点的CP>1.33的数据必须≥50%和CP>1的数据必须≥80%两种情况同时满足时呈现绿色;在CP<1的>50%时,该项目为红色;不在这两种情况中的则显示黄色。
dPH汽车设计网
图3全顺工厂CTQ整改趋势
dPH汽车设计网图3是全顺工厂运用CTQ长期跟踪相关子系统的趋势,非常直观地反映了过程能力。
该分析系统的优点是,直观有效地分析出问题所在和过程能力整体趋势,与三坐标整体报告互补,三坐标尺寸报告反馈车身尺寸宏观状况和整车尺寸合格率,CTQ分析反映具体的装配效率和能力。
dPH汽车设计网
3.检具PCF/UCF/BlueBuck分析
dPH汽车设计网
以上是基于三坐标测量数据的分析,主要在欧系车型上采用,日系车型喜欢采用各类检具测量分析系统,有分总成协调检具(PCF),装配零件协调检具(UCF),甚至是标准车身检具(BlueBuck),而不喜欢研究三坐标的数据。
三坐标数据的分析和判断要求工程师对产品、夹具和工艺过程都非常了解,而检具测量系统只需对操作人员做简单的培训即可。
PCF的使用是将零件放在检具上面,通过塞尺来测量判断零部件是否合格。
UCF是将零件装配在检具上,通过测量和标准检具仿体的对比来判断每个装配件的对错。
dPH汽车设计网
在检具测量的基础上,目前新发展出来的综合检具测量系统十分有借鉴意义,其在车身上可以模拟总装的所有装配零件,且判断简单,只有通过或不通过。
如在车身上装配一个座椅,总装要装配四个螺栓,模拟检具就插三个插销,可以插入表示通过,否则不通过。
dPH汽车设计网
车身尺寸合格率=所有检具可通过的插销数量/所有检具的插销数量×100%
dPH汽车设计网
这种方法能充分反映总装的装配需求,操作判断都很简单,是一种测量系统的发展趋势,比三坐标测量系统更为实用,惟一的缺点是只能针对单一车型,不能柔性测量。
dPH汽车设计网
车身尺寸变差整改
dPH汽车设计网
数据收集和分析可以确定问题所在,并找出问题出现的根本原因。
通过工程师的简单确认,基本可以排除或纠正人员和方法两方面的影响,之后,再用检具检查冲压件。
用PCF和UCF检查对应的分总成,分别记录数据,同时根据车身数据分析的结果,首先检查问题点焊接夹具定位面、定位销的位置精度,记录偏离值并判断是否与问题的趋势一致,如果一致先调整到理论位置。
其次将零件置于夹具之上,观察零件与定位面和定位销的对应状况,调整确保零件与定位面之间无干涉部位。
再次,检查零件在夹具上定位后是否有转动或移动现象,记录定位销与零件孔的对应尺寸,结合材料检测数据和车身的尺寸数据分析结果,形成对定位销和面的整改措施。
原则上,材料有问题先整改材料,然后整改机器(焊接夹具),但实际上只要材料状态保持稳定,很多车身尺寸问题都是通过夹具整改完成的,因为夹具整改相对来说更有效率也更经济。
dPH汽车设计网
车身尺寸在开发完成进入批量生产一段时期以后,材料和机器也相对稳定,这时只要定期检测材料和机器的状态,及时维护保持稳定就可以了,同时需要把精力转到对人员和工艺方法的执行管理方面。
在批量生产阶段,通过SPC控制图可以预防一些定位销、面松动和磨损的情况。
结语
dPH汽车设计网
车身尺寸控制是一个系统工程,全顺工厂结合自身产品的特点,通过不断地总结和探索找到了一个适合自己的车身尺寸控制方法。
当然,万变不离其宗,关键是要抓住根本,控制车身的变差源。
随着汽车产业的不断发展,市场竞争日益加剧,我们会不断探索,使我们的控制手段更加高效、经济,以在市场中立于不败之地。