压力容器安全监察规程.docx
《压力容器安全监察规程.docx》由会员分享,可在线阅读,更多相关《压力容器安全监察规程.docx(34页珍藏版)》请在冰豆网上搜索。
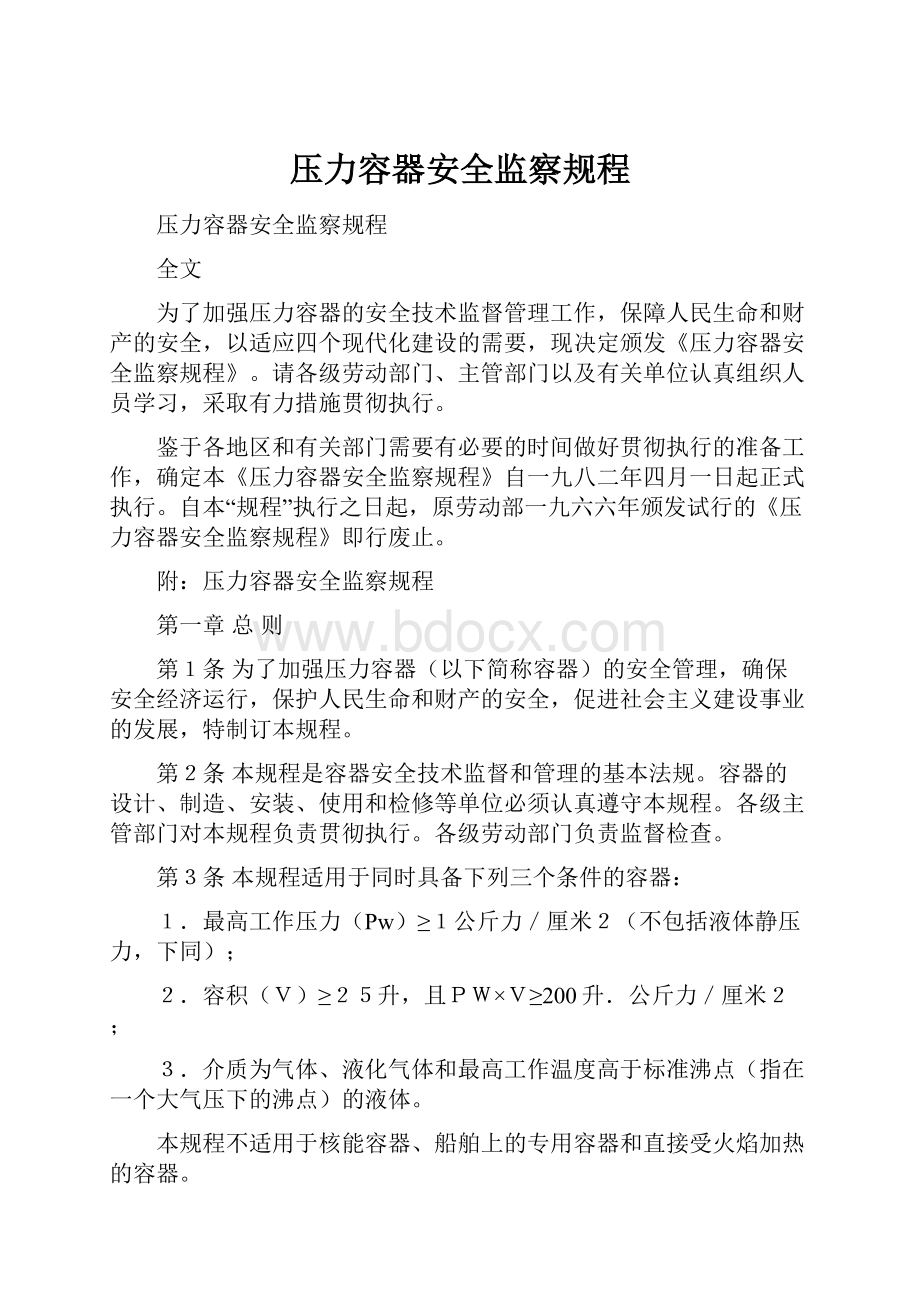
压力容器安全监察规程
压力容器安全监察规程
全文
为了加强压力容器的安全技术监督管理工作,保障人民生命和财产的安全,以适应四个现代化建设的需要,现决定颁发《压力容器安全监察规程》。
请各级劳动部门、主管部门以及有关单位认真组织人员学习,采取有力措施贯彻执行。
鉴于各地区和有关部门需要有必要的时间做好贯彻执行的准备工作,确定本《压力容器安全监察规程》自一九八二年四月一日起正式执行。
自本“规程”执行之日起,原劳动部一九六六年颁发试行的《压力容器安全监察规程》即行废止。
附:
压力容器安全监察规程
第一章总则
第1条为了加强压力容器(以下简称容器)的安全管理,确保安全经济运行,保护人民生命和财产的安全,促进社会主义建设事业的发展,特制订本规程。
第2条本规程是容器安全技术监督和管理的基本法规。
容器的设计、制造、安装、使用和检修等单位必须认真遵守本规程。
各级主管部门对本规程负责贯彻执行。
各级劳动部门负责监督检查。
第3条本规程适用于同时具备下列三个条件的容器:
1.最高工作压力(Pw)≥1公斤力/厘米2(不包括液体静压力,下同);
2.容积(V)≥25升,且PW×V≥200升.公斤力/厘米2;
3.介质为气体、液化气体和最高工作温度高于标准沸点(指在一个大气压下的沸点)的液体。
本规程不适用于核能容器、船舶上的专用容器和直接受火焰加热的容器。
第4条为有利于安全技术管理和监督检查,根据容器的压力高低、介质〔注〕的危害程度以及在生产过程中的重要作用,将本规程适用范围的容器划分为三类(压力等级和种类的划分见附件一):
1.属于下列情况之一者为一类容器:
(1)非易燃或无毒介质的低压容器;
(2)易燃或有毒介质的低压分离容器和换热容器;
2.属于下列情况之一者为二类容器:
(1)中压容器;
(2)剧毒介质的低压容器;
(3)易燃或有毒介质的低压反应容器和贮运容器;
(4)内径小于1米的低压废热锅炉。
3.属于下列情况之一者为三类容器:
(1)高压、超高压容器;
(2)剧毒介质且Pw×V≥200升。
公斤力/厘米2的低压容器或剧毒介质的中压容器;
(3)易燃或有毒介质且Pw×V≥50000升.公斤力/厘米2的中压反应容器,或PW×V≥5000升,公斤力/厘米2中压贮运容器;
(4)中压废热锅炉或内径大于1米的低压废热锅炉。
第5条各有关部门和单位编制的有关容器的设计、制造、安装、使用和检修的技术规范(标准)、技术条件和管理规程等,其安全技术要求应不低于本规程的规定。
现行的技术标准、技术条件的技术要求如高于本规程时,按高的要求执行。
对设计、制造压力大于320公斤力/厘米2的容器,还应遵循专门的技术条件规定和要求。
第6条容器的设计、制造、安装和使用需要采用新技术而又低于本规程的有关要求时,由提出单位提供可靠的科学试验报告,经省、市、自治区的主管部门审查批准,并报国家劳动总局同意。
第二章材料
第7条制造容器用的材料质量及规格应符合国标、部标和有关技术条件要求。
材料制造厂必须保证质量,并提供质量证明书。
质量证明书上至少应列出以下项目:
炉(罐)号、批号、实测的化学成份和机械性能(包括(略),对奥氏体不锈钢可不提供(略)值)、熔炼方法及供货热处理状态。
对于低温(略)容器用的材料还应提供夏比“V”形缺口试样的冲击值和脆性转变温度。
第8条选用制造容器的材料应考虑容器的操作条件(如温度、压力、介质特性等)、材料焊接性能和冷热加工性能等。
钢制容器材料应按一机部、石油部、化工部颁布的《钢制石油化工压力容器设计规定》(以下简称“设计规定”)和冶金部YB536-69《压力容器用炭素钢及普通低合金钢热轧厚钢板技术条件》选用。
第9条易燃或有毒、剧毒介质的容器受压元件不得选用沸腾钢制造。
A3钢不得用于制造盛装液化石油气体的容器。
含碳量大于0.24%的材料,不得用于焊制容器。
焊后需热处理的容器,焊条含钒量不得大于0.05%。
第10条用于制造高压容器和温度≤-40℃的低温容器的钢板,当厚度>20毫米时,应逐张进行超声波探伤。
用于制造温度>-40℃的低温容器的钢板,当厚度>20毫米时,应进行超声波抽查,抽查数量不应少于所用钢板的20%,且不少于一张。
探伤质量标准应符合有关规定。
第11条材料制造厂提供制造容器及其受压元件的新材料,必须经过技术鉴定合格。
参加鉴定的单位必须有劳动部门代表。
第12条容器的主要受压元件材料代用,必须征得原设计单位同意,并附证明文件。
第13条材料制造厂提供制造容器用的材料应有标记。
使用、保管单位应建立管理制度;当钢材割开时,必须作标记移植,保证使用者能识别。
第14条承办向国外订购容器用钢的单位在向国外订购容器用钢时,应按需方提出的钢号和技术条件订购,并应符合供货国容器用钢的标准和有关规定,如变更技术要求必须征得需方同意。
第15条焊接钢制受压元件使用的焊条,应符合GB981~984-76的规定。
焊丝应符合GB1300-77的规定。
焊条、焊丝应有制造厂的质量合格证,并按有关规定验收合格后才能使用。
对焊接第二、三类容器的焊条药皮和焊剂应选用低氢硷性型。
第16条对特殊要求的容器材料,应由供需双方协商签订合同,但不得低于本章要求。
第三章设计
第17条容器的设计压力,应略高于容器在使用过程中的最高工作压力。
装安全装置的容器,其设计压力不得小于安全装置的开启压力或爆破压力。
第18条盛装临界温度高于50℃的液化气体的容器,如有可靠的保冷措施,其最高工作压力应为所盛装气体在可能达到的最高工作温度下的饱和蒸氯压力;如无保冷措施,其最高工作压力不得低于50℃时的饱和蒸气压力。
第19条盛装临界温度低于50℃的液化气体容器,如有可靠的保冷措施并能确保低温贮存的,其最高工作压力不得低于试验实测的最高温度下的饱和蒸气压力;没有试验实测数据或没有保冷措施的容器,其最高工作压力不得低于所装介质的规定的最大充装量和50℃时的气体压力。
第20条盛装混合液化石油气的容器,其50℃时〔注〕的饱和蒸气压力低于异于烷在50℃时的饱和蒸气压时,取50℃时异丁烷的饱和蒸气压力为最高工作压力;如高于50℃时异丁烷的饱和蒸气压时,取50℃时丙烷的饱和蒸气压为最高工作压力;如高于50℃时丙烷的饱和蒸气压时,取50℃时丙烯的饱和蒸气压为最高工作压力。
第21条容器的设计温度应取容器在正常操作时相应的设计压力下壳壁的最高或最低温度。
盛装标准沸点低于或等于-20℃时的液化气容器,壁温受环境气温影响而可能低于或等于-20℃时,其设计温度还应考虑地区最低温度(见附录五)。
第22条容器的壳体和封头的厚度计算应符合《设计规定》的要求;由于物料的化学反应使其内压增高的反应容器和易燃、有毒、剧毒介质的容器,抗拉强度的安全系数(略)不应小于3,且屈服点(略)(或屈服强度(略))的安全系数(略)不应小于1.6。
对奥氏体不锈钢材料,屈服点(略)(或屈服强度(略))的安全系数(略)不应小于1.5〔注〕。
第23条每台容器的探伤检验数量应按第44条表一的规定。
选择局部探伤的容器,焊缝系数不应高于如下值:
双面焊≤0.85、单面焊≤0.8(加垫板)、单面焊≤0.7(不加垫板)。
第24条耐压试验应选用液体作为试验介质。
由于结构原因。
即不能安全地装满水的容器或不允许被试验液体沾染的容器。
可采用气体作为试验介质。
气压试验之前必须对容器主要焊缝进行100%无损探伤,且应增加试验场所的安全措施。
第25条对剧毒介质和设计要求不允许有微量介质泄漏的容器,必须做气密性试验。
试验时容器上的安全附件(安全装置、阀门、压力表、液面计等)应安装齐全。
第26条设计夹套的容器,应在图样上分别注明容器壳体和夹套的试验压力和允许的内外压差值,并应注明试验步骤和要求等。
第27条耐压试验时,容器壳体平均一次总体薄膜应力值应符合下列要求:
1.液压试验的应力不得超过所用材料在耐压试验温度下屈服点的90%;
2.气压试验的应力不得超过所用材料在耐压试验温度下屈服点的80%;
计算耐压试验应力时,所取的壁厚应扣除壁厚附加量(包括厚度偏差、腐蚀裕度、壁厚减薄量。
对壳程压力低于管程压力的列管式热交换器可不扣除腐蚀裕度),且计入液压试验时液柱静压力。
第28条内径<1000毫米的反应容器、贮运容器,如不能利用工艺接管通孔检查内部时,应开设检查孔;内径≥1000毫米的容器,如不能利用其它可拆装置进行内部检验和清洗时,应开设人孔。
检查孔、人孔的尺寸,应符合有关规定。
第29条对大型有保温层的容器,必要时,应设计为局部活套式保温结构,以便对焊缝进行检验。
第30条筒体与封头的连接结构可参照《设计规定》第一篇的附录F“焊接结构设计”的有关规定设计。
第31条盛装液化气体(液态贮存)的容器设计储存量不得超过下式计算值:
(略)
式中:
W──贮存量,公斤;
V──容器的设计容积,升;
(略)──装量系数,一般取0.9容积经过实际测定者,允许取大于0.9,但不得大于0.95;
(略)──设计温度下的饱和液体的密度,公斤/升。
第32条安全附件的设计应符合本规程第六章的有关规定。
第33条容器设计单位设计的容器,应有符合标准的总图、受压元件图和主要受压地件强度计算书。
中压以上的反应容器和贮运容器,当用户需要强度计算书时,设计单位应予提供。
总图上至少应注明下列内容:
1.容器的名称、类别(按第4条)、容积、设计温度、设计压力、介质、主要受压元件的材质、焊缝系数和腐蚀裕度等;
2.耐压试验、气密试验和检验要求;
3.除制造技术条件以外的特殊技术要求,如钢板探伤、防止容器产生应力腐蚀的焊后热处理要求和容器安装使用说明等。
第34条设计图样上应有设计、校对、审核人的签字。
对第三类容器的总图应由总工程师或容器设计技术负责人审核批准。
第35条容器设计的审批和备案。
1.容器的设计单位,须经主管部门批准,同级劳动部门审查同意,方可设计容器;
2.部(委、局)专业设计院设计的容器,其中第三类的反应,贮运容器的图样、资料,应报主管部审批并报国家劳动总局备案;
3.省、市、自治区的专业设计院,部直属企业的设计单位,经省级主管部门审批、同级劳动部门同意的单位所设计的容器、其图样应经本单位的总技术负责人审批。
其中属于第三类容器的图样、资料,应报省、市、自治区劳动部门备案,属于本条第2款规定的容器,还应报国家劳动总局备案;
4.省、市、自治区直属或省辖市企业,一般只允许设计第一、第二类容器,其图样、资料应经企业的主管技术负责人审批;地辖市企业如有条件设计自用的容器,经批准、同意后,也可设计第一类、第二类容器;
5.备案图样、资料包括:
(1)容器设计的基本参数和技术条件;
(2)总图和主要受压元件图;
(3)强度计算书。
第四章制造与安装
第36条容器应由专业单位制造(包括现场组装),制造单位应向主管部(委、局)或省、市、自治区主管部门提出申请,由主管部门根据技术力量、检验手段、全面规划、择优定点,并报同级劳动部门审查同意发给制造许可证,制造第三类容器的单位,应有国家劳动总局发给的制造许可证。
自制自用的单位,如有制造条件条件的,须经地、市主管部门批准,同级劳动部门同意方可制造容器。
第37条容器制造、组装单位必须严格按照经审查批准的图纸和技术要求施工,如改变受压元件的材料、结构、强度时,必须征得原设计单位的同意并取得证明文件,改动的部位应作详细记载。
第38条容器新产品(指采用新材料、新结构、新工艺并经省级以上主管部门批准列入试制的产品)应按任务书进行试制,并应符合本规程的规定和有关技术标准要求。
试制产品应由主管部门组织高等院校、科研等有关单位进行技术鉴定,鉴定合格后,报省级或省级以上主管部门批准,同级劳动部门审查同意,方可投入使用或批量生产。
第三类反应容器或贮运容器,经鉴定后还应报国家劳动总局备案。
第39条属于下列情况之一,制造单位应对容器主体材料按原材料标准或设计图样及用户协议要求的项目进行复验:
1.用于制造第三类容器材料或制造第一、二类容器而材质证明书不全的材料;
2.设计图样上规定特殊要求项目的材料;
3.制造单位对资料数据有怀疑的材料。
第40条容器受压元件的焊接工作,必须由经考试合格的焊工担任。
焊工考试由制造单位按国家劳动总局颁布的《锅炉压力容器焊工考试规则》组织进行。
第41条容器组焊的要求:
1.容器的组焊不应采用十字焊缝,相邻的两筒节间的纵缝和封头与相邻筒节的纵缝应错开,错开间距应大于筒体厚度的三倍,且不小于100毫米;
2.在容器上焊接临时吊耳和拉筋板等应采用与容器相同或焊接性能相似的材料,并用相应的焊条及焊接工艺。
临时吊耳和拉筋板割除后留下的焊疤必须打磨平滑。
对低温容器和低合金钢、铬钼钢以及屈服强度大于40公斤力/毫米2的材料,应在打磨位置作磁粉或着色探伤。
第42条容器焊接工艺评定的要求:
1.属于下列情况之一的容器应在焊前做焊接工艺试板,并经评定合格:
(1)采用新材料试制的容器或施焊单位首次焊接的钢种;
(2)焊接工艺参数改变或超出原定的范围;
(3)需经过热处理改善机械性能的;
(4)改变焊接方法;
(5)改变焊接材料(焊条、焊丝、焊剂、保护焊的气体)。
2.评定焊接工艺试板之前,应先做焊接接头的抗裂性试验,并按与试验方法相应的规定进行评定。
通过抗裂试验确定焊接预热温度、层间温度以及选择焊接材料。
3.焊接工艺试板评定要求见附表录二。
第43条容器应按下列要求制作焊接试板,并作焊接接头的机械性能试验:
1.试板数量:
(1)属于下列情况之一的容器每台应制作试板:
a.设计压力≥100公斤力/厘米2的容器;
b.盛装有毒、剧毒介质的容器;
c.壳体材料为15MnVR和CrMo低合金钢的容器;
d.壳体材料的屈服强度大于40公斤力/毫米2的容器;
e.凡壳体材料需经热处理以达到设计要求的机械性能的容器;
f.设计图样上或用户协议书要求按台作试板的其他容器。
(2)除上列容器外的其他容器,若制造厂检验部门能提供50台同材料连续生产的试板数据,证明焊接质量稳定时,由厂技术部负责人或总工程师批准,报省、市、自治区劳动部门同意后,允许以批〔注〕代台,减少试板数量,具体规定如下:
产品数量(台)试板数(块)
≤51
6~102
11~203
21~503~5
51~1005~10
超过上列台数每10台产品,制作试板一块。
2.试板的要求:
(1)试板的材料、焊接及热处理工艺应与所代表的筒体一致。
试板焊缝应经100%的无损探伤检查,并作记录。
其评定标准应与所代表的容器一致。
(2)要求热处理的容器,焊接试板应与容器同炉一起进行热处理。
(3)试板焊接接头机械性能试验项目:
包括拉力、冷弯和冲击等(按标准或图样规定温度)试验。
试样尺寸、取样部位和试验要求、评定标准见附录二。
3.焊接试板试验如不合格,允许用原试板或同时焊接的另一块试板重作试验,但对不合格项目应取双倍试样复试(低温容器冲击试样的复试要求应按专门的技术规定进行),如仍不合格,则试验代表的容器焊缝为不合格。
第44条容器的焊缝探伤:
焊缝探伤包括超声波、射线、表面(磁粉、着色)等方法,制造厂应根据可能出现的缺陷性质、技术掌握情况、设备条件选择适当的方法。
1.每台容器超声波探伤和射线探伤百分数的要求和合格标准按表一、表二规定,表面探伤按本条第5款规定。
射线和超声波探伤要求表一(略)
射线和超声波探伤合格标准表二(略)
(1)**第二类容器中剧毒介质的容器;设计压力≥50公斤力/厘米2的容器;易燃介质的压缩气体、液化气体或有毒介质且容积大于1立方米的容器和第一、二类容器中采用铬钼钢焊制的容器,均应作100%探伤检查。
(2)*第一、二类容器中的其他容器可作局部探伤检查。
(3)公称直径≥250毫米的接管对接焊缝应进行探伤检查。
(4)选择超声波探伤时,还应对超探部位作射线探伤复验。
复验长度为表一百分数的20%,且不小于300毫米。
选择射线检验时,对壁厚大于38毫米的容器还应作超声波探伤复验。
复验长度为表一百分数的20%,且不小于300毫米。
采用上述二种方法进行焊缝探伤后,按各自标准均应合格,方可认为探伤合格。
当用另一种探伤方法复验后,如发现有超标缺陷时,应增加10%(相应焊缝总长)的复验长度;如仍发现超标缺陷,则应100%进行复验。
2.局部探伤以外的焊缝仍应符合表二合格标准,如经复检发现仅属于气孔的超标缺陷,可由制造单位与用户协商处理。
3.探伤检验工作应由考试合格的探伤人员进行。
4.容器局部探伤的部位,由制造单位检验部门根据实际情况选定,但对筒体与封头连接部位,筒节纵环缝交叉部位必须进行探伤。
探伤的百分数达到20%后,如发现有超标的缺陷时,应由检查员指定位置增加10%(相应焊缝总长)的探伤长度;如仍有不合格的,则要对容器所有焊缝进行100%探伤。
探伤复验要求仍按本条第1款第(4)项规定。
5.对于材料屈服强度(略)>40公斤力/毫米2、厚度>16毫米铭钼钢,或与其相类似的钢制容器上的接管法兰、补强圈与壳体或封头相接的角焊缝和焊后调质处理的容器焊缝,还应作磁粉或着色探伤。
6.现场组装焊接的容器壳体、封头和高强钢材料的焊接容器,耐压试验后应对焊缝作20%(相,应焊缝总长)的表面探伤,若发现裂纹,则应对所有焊缝作表面探伤。
7.容器的全部原始探伤资料(底片、记录),制造单位至少保存七年。
七年后,若用户需要可转交用户保管。
第45条容器焊缝的表面质量应符合下列要求:
1.焊缝外形尺寸应符合技术标准的规定和图样的要求,焊缝与母材应圆滑过渡;
2.焊缝或热影响区表面不允许有裂纹、气孔、弧坑和肉眼可见的夹渣等缺陷;
3.焊缝的局部咬边深度不得大于0.5毫米。
低温容器焊缝不得有咬边,对于任何咬边缺陷都应进行修磨或焊补磨光,并作表面探伤,经修磨部位的厚度不应小于设计要求的厚度。
第46条焊缝的返修:
1.焊缝的返修工作应由考试合格的焊工担任,并采用经评定验证的焊接工艺,返修工艺措施应得到焊接技术人员的同意。
同一部位的返修次数一般不应超过二次。
对经过二次返修仍不合格的焊缝,如需再进行返修,需经制造单位技术总负责人批准,并作出是否对返修部位进行硬度测定与热处理等决定,应将返修的次数、部位和无损探伤等结果记入容器质量证明书中。
2.要求焊后热处理的容器,应在热处理前返修,如在热处理后还需返修时,返修后应再做热处理。
第47条筒体和封头的制造公差要求:
1.纵环焊缝对口错边量、棱角度;
2.筒体不直度;
3.同一断面上最大直径与最小直径之差;
4.封头焊缝的布置;
5.椭圆形、碟形封头主要尺寸允差;
6.球壳或球形封头分瓣冲压的瓣片尺寸允差。
上列各项均应符合本规程引用的容器制造技术条件的规定。
第48条容器制成后必须进行耐压试验。
在耐压试验压力下,任何人不得接近容嚣,待降到设计压力后,方可进行各项检查。
除设计图样规定要求,用气体代替液体进行耐压试验外,不得采用气压试验,进行气压试验前,要全面复查有关技术文件,要有可靠的安全措施,并经制造安装单位技术负责人和安全部门检查、批准后方可进行。
需要进行气密性试验的容器,要在液压试验合格后进行。
第49条容器耐压试验和气密试验的压力应符合图样要求,且不小于表三规定。
对壁温≥200℃的容器,耐压试验压力为Pγ再乘以比值(略)。
即:
(略)
式中:
P──容器的设计压力,公斤力/厘米2;(略)──耐压试验压力,公斤力/厘米2,(≥200℃);
Pr──耐压试验压力,公斤力/厘米2,(常温);(略)──耐压试验系数(按表三);(略)──试验温度下材料的许用应力,公斤力/厘米2;(略)设计温度下材料的许用应力,公斤力/厘米2;
当(略)之比值大于1.8时取1.8。
耐压试验和气密试验的压力规定表三(略)
*对不是按内压强度计算公式决定壁厚的容器,如:
考虑稳定因素等设计的容器,应适当提高耐压试验的压力。
第50条耐压试验和气密试验的升压程序及介质温度的规定:
1.液压试验:
充满液体(在容器最高点设排气口,将空气排净),待容器壁温与液体温度相同时,才能缓慢升压到规定试验压力,根据容积大小保持10~30分钟,然后将压力降到设计压力至少保持30分钟,同时进行检查。
试验应注意下列事项:
(1)一般应采用洁净水进行试验。
对不锈钢制造的容器用水进行试验时,应采取措施,防止氯离子腐蚀,否则,应限制水中氯离子含量不超过25ppm;
(2)采用石油蒸馏产品进行液压试验,试验温度应低于石油产品的闪点;
(3)试验温度应低于液体沸点温度,对新钢种的试验温度应高于材料脆性转变温度,具体温度值应按设计图样规定;
(4)炭素钢、16MnR钢制容器液压试验时,液体温度不得低于5℃。
其他低合金钢制容器(不包括低温容器)液压试验时,液体温度不得低于15℃。
如果由于板厚等因素造成材料脆性转变温度升高,还要相应的提高试验液体温度。
其他钢种的容器液压试验温度按图样规定。
2.气压试验:
缓慢升压至规定试验压力的10%,保持10分钟,然后对所有焊缝和连接部位进行初次检查;合格后继续升压到规定试验压力的50%,其后按每级为规定试验压力的10%的级差逐级升压到试验压力,保持10~30分钟,然后再降到设计压力至少保持30分钟,同时进行检查。
3.气密试验:
缓慢升压至设计压力保持30分钟;同时进行检查,气体温度应不低于5℃。
4.气压试验时所用气体应为干燥、洁净的空气、氮气或其他惰性气体,气体温度不低于15℃。
容器作定期检验时,若容器内有残留易燃气体存在,会导致爆炸时,则不得使用空气作为试验介质。
第51条对夹套容器应先进行内筒耐压试验,合格后再组焊夹套,并对夹套作耐压试验。
第52条耐压试验和气密试验时,各部位的紧固螺栓必须装配齐全。
试验时应装二块压力表,压力表应符合规程第六章的有关规定。
试验前应对安全防护措施,试验准备工作进行全面检查,液压试验升压前,容器外表面应保持干燥。
第53条耐压试验过程中,如果发现有异常响声、压力下降、油漆剥落、或加压装置发生故障等不正常现象,应立即停止试验,并查明原因。
第54条容器耐压试验,符合下列情况为合格:
1.容器和各部焊缝无渗漏;
2.容器无可见的异常变形;
3.经返修、焊补深度大于9毫米或大于壁厚一半的高强钢制容器,焊补部位按原探伤方法进行复查无超过原定标准的缺陷;
4.设计要求进行残余变形测定的容器,在耐压试验同时应作残余变形测定,其合格标准为径向残余变形率不超过0.03%或容积残余变形率不超过10%。
容积残余变形率按下式计算:
(式略)
式中:
(略)──容积残余变形率;
(略)──容积残余变形值,毫升;
(略)──容各全变形值,毫升;
用内测法测定容积全变形时,容积全变形值用下式计算:
(式略)
式中:
A──试验时总压入水量,毫升(实际测定);
B──试验管路在试验水温和试验压力下的压入水量,毫升。
(根据实际测定,不包括管路容积。
在5~40℃范围内任意水温下的实测值均可;不同试验压力使用同一管路时,应按不同试验压力分别测定;管路的几何尺寸改变时应重新测定);
V──容器实际容积,毫升;
(略)──耐压试验压力,公斤力/厘米2;
(略)──耐压试验压力及试验水温下水等温压缩系数。
第55条新制造的容器在耐压试验后,应及时将试验液体排净,并用压缩空气或其他惰性气体将容器内表面吹干。
第56条新制造的容器,必须在明显的部位装设耐腐蚀材料制作的金属铭牌。
金属铭牌上至少应载明制造单位名称、制造年月、容器名称、产品编号、设计压力(公斤力/厘米2)、设计壁温(℃)及容器总重(公斤)等。
第57条容器或部件出厂时,制造单位除按本规程第33条