水泥集团节能改造技术方案.docx
《水泥集团节能改造技术方案.docx》由会员分享,可在线阅读,更多相关《水泥集团节能改造技术方案.docx(7页珍藏版)》请在冰豆网上搜索。
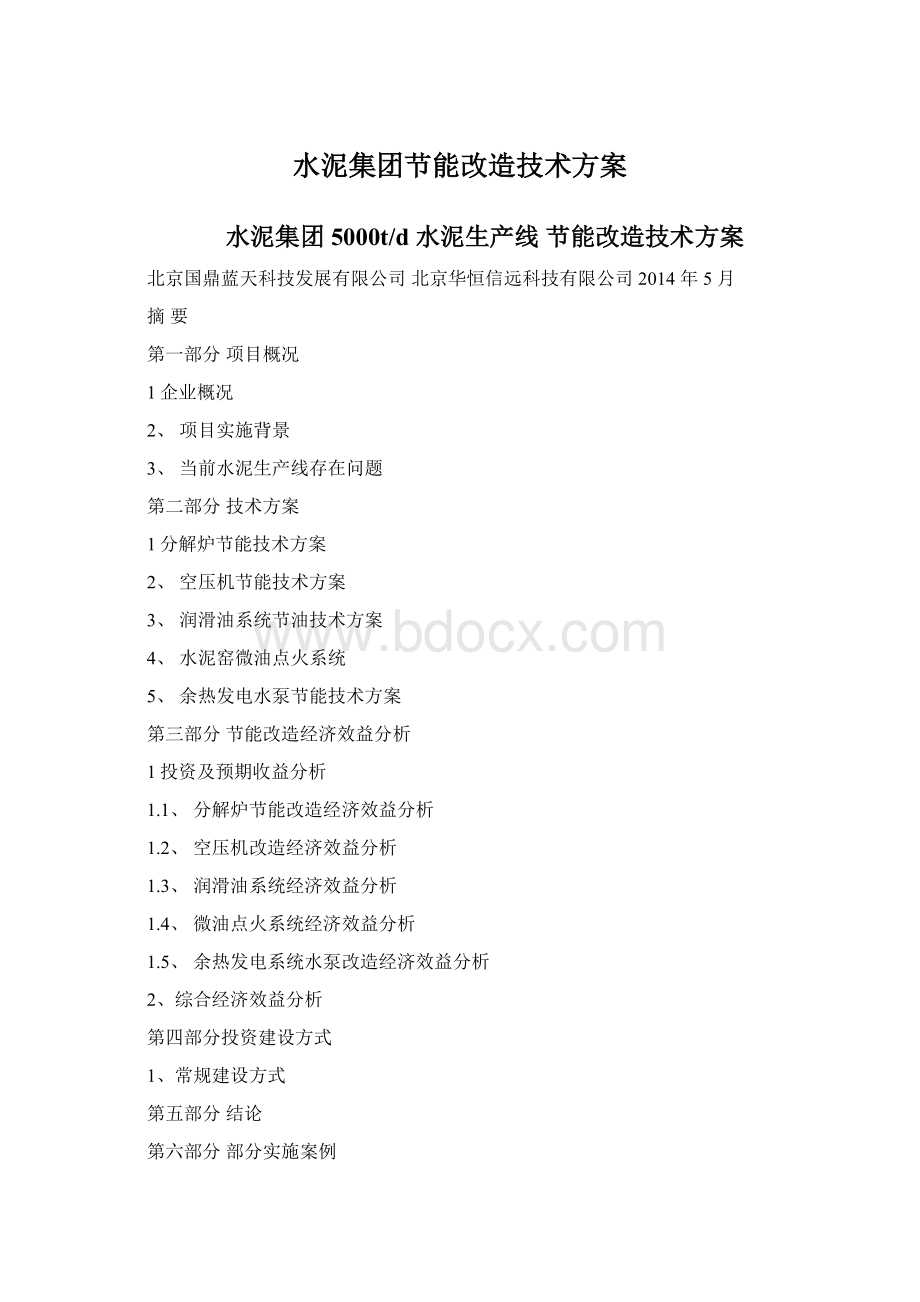
水泥集团节能改造技术方案
水泥集团5000t/d水泥生产线节能改造技术方案
北京国鼎蓝天科技发展有限公司北京华恒信远科技有限公司2014年5月
摘要
第一部分项目概况
1企业概况
2、项目实施背景
3、当前水泥生产线存在问题
第二部分技术方案
1分解炉节能技术方案
2、空压机节能技术方案
3、润滑油系统节油技术方案
4、水泥窑微油点火系统
5、余热发电水泵节能技术方案
第三部分节能改造经济效益分析
1投资及预期收益分析
1.1、分解炉节能改造经济效益分析
1.2、空压机改造经济效益分析
1.3、润滑油系统经济效益分析
1.4、微油点火系统经济效益分析
1.5、余热发电系统水泵改造经济效益分析
2、综合经济效益分析
第四部分投资建设方式
1、常规建设方式
第五部分结论
第六部分部分实施案例
摘要
当前5000t/d新型干式水泥生产线,存在明显的节能、节油的空间。
其中包括:
分解炉、空压机、余热发电系统水泵、润滑油系统、窑炉点火过程。
具体改造方案如下:
对于分解炉,可采用节煤专家系统智能控制,替代当前人工操作;对于空压机,可采用中央集控方式变频控制空压机运行,同时改造压缩空气管路减少压损,改造空压机油路系统,提高空压机能效;
对于破碎机、生料磨、熟料磨、回转窑、磨煤机等润滑油系统,采用离心净油器,减少润滑油消耗;
对于窑炉点火,采用微油点火技术,减少燃油消耗;
对于余热发电系统水泵,可采用叶轮改造或更换水泵、变频控制等方式,提高水泵实际运行能效。
各单项节能改造预期收益及经济效益分析见下表:
项目
最咼节能、节油量
年节能收益
(万兀)
投资额
(万兀)
静态投资回收期
(年)
分解炉改造
2200t标煤
154
150
0.97
空压机改造
39.6万kWh
31.68
18
0.57
润滑油过滤处理
50t润滑油
56
55
0.98
窑炉燃烧器
32t燃油
12.48
13
1.04
余热发电系统水泵
33.3万kWh
26.64
54
2.03
合计
280.8
290
综合节能改造完成后,每年可节省标煤2200t,节电72.9万kWh节省润滑油消耗50t,节省燃油消耗32t;预期获得年收益280.8万元,经济效益显著;同时,可减少碳排放约6581.3t,减少二氧化硫排放56.8t,社会效益显著。
本项目由甲方(业主方)出资建设,采用常规建设方式,乙方提供相关工程服务。
因此本项目具有良好的可实施性。
第一部分项目概况
1、企业概况
2、项目实施背景
我国是能源消耗大国,数据表明,目前每百万美元消耗,我国是世界平均水平的3.1倍,是OEC(经济合作发展组织)国家和地区的4.3倍,更是日本的9倍,节约能源资源和保护生态环境形势十分严峻。
出于保护环境和可持续发展的考虑,我国已经将节能减排工作列为经济发展的国策,节能市场潜力巨大。
水泥行业作为能源消耗的重点行业,节能减排工作势在必行,已经成为企业生存与发展、产业升级与经济效益的关键问题。
中央《十二五”节能减排规划刚要》中提出,坚持大幅降低能源消耗强度、显著减少主要污染物排放总量、合理控制能源消费总量相结合,形成加快转变经济发展方式的倒逼机制;坚持优化产业结构、推动技术进步、强化工程措施、加强管理引导相结合,大幅度提高能源利用效率,显著减少污染物排放;加快构建政府为主导、企业为主体、市场有效驱动、全社会共同参与的推进节能减排工作格局,确保实现十二五”节能减排约束性目标,加快建设资源节约型、环境友好型社会。
《规划》要求:
到2015年,全国万元国内生产总值能耗下降到0.869吨标准煤(按2005年价格计算),比2010年的1.034吨标准煤下降16%(比2005年的1.276吨标准煤下降32%。
到2015年,单位工业增加值(规模以上)能耗比2010年下降219左右。
其中,关于水泥行业,要求水泥熟料综合能耗从115千克标准煤/吨将至112千克标准煤/吨。
《规划》要求,促进传统产业优化升级。
运用高新技术和先进适用技术改造提升传统产业,促进信息化和工业化深度融合。
推广大型新型干法水泥生产线。
普及纯低温余热发电技术。
到2015年水泥纯低温余热发电比例提高到70%以上。
推进水泥粉磨、熟料生产等节能改造。
在国务院《“十二五”节能环保产业发展规划》中,明确指出:
节能环保产业是指为节约能源资源、发展循环经济、保护生态环境提供物质基础和技术保障的产业,是国家加快培育和发展的7个战略性新兴产业之一。
加快发展节能环保产业,是调整经济结构、转变经济发展方式的内在要求,是推动节能减排,发展绿色经济和循环经济,建设资源节约型环境友好型社会,积极应对气候变化,抢占未来竞争制高点的战略选择。
《发展规划》要求,大力发展以合同能源管理为主要模式的节能服务业,到2015年,采用合同能源管理机制的节能服务业销售额年均增速保持30%,力争节能服务业总产值突破3000亿元,累计实现节能能力6000万吨标准煤。
到2015年,节能环保产业总产值达到4.5万亿元,增加值占国内生产总值的比重为2%左右。
3、当前水泥生产线存在问题
当前,**集团水泥生产线主要是5000t/d新型干式生产线,并配有余热发电系统。
尽管生产工艺及废余热利用等相关技术已经走在国内前列,但仍存在如下问题:
1)虽然水泥生产线已实现DCS^央集控,但对于某些部位的精细控制仍由人工来实现。
例如分解炉温度控制。
由于存在工况变化频繁、测控点少的问题和分解炉自身非线性、大滞后、时变的特性,使得实际生产中经常出现分解炉温度大幅度波动的现象,直接影响回转窑的正常运转;同时因优化控制涉及较少,操作工的操作水平、操作失误等因素,造成部分能源浪费,并影响影响对水泥熟料的质量。
2)水泥生产线存在压缩空气需求。
压缩空气需求负荷随生产工况的变化存在较大波动。
受空压机自身调控所限,存在用气低负荷期空压机低能效负载运行现象,造成能源浪费。
3)水泥生产的主要设备:
破碎机、生料磨、熟料磨、回转窑、磨煤机、输送机、风机、冷却机等设备的轴承、齿轮箱等部件需要润滑。
尤其破碎、研磨、输送、焙烧等粉尘教大工艺环节,润滑油极易污染。
目前这些部位润滑油处理普遍采用滤芯式滤油器净化。
因净化效果不好,需要经常换油,不仅造成润滑油的浪费,也大幅增加了维护工作量,甚至导致设备严重的故障事故。
4)水泥窑每次检修点火,需要消耗大量燃油。
不仅燃油成本远高于煤炭,因石油是我国紧缺资源,也不利于我国能源结构调整。
5)水泥窑余热发电系统,已成为当前水泥生产线必不可缺少的部分。
为了保证系统安全,发电系统的水泵,如给水泵、凝水泵、循环水泵等,在设计选型时选定扬程通常出高设计需求值10~20%。
这使得水泵的实际运行工况远远偏离水泵本身的最佳设计运行工况,造成水泵能效低下,能源浪费。
综上,当前5000t/d新型干式生产线仍存在较大工艺改进空间及节能空间。
第二部分技术方案
1、分解炉节能技术方案
1.1、目前生产线分解炉运行状况分析分解炉作为预分解窑的核心设备,其主要功能是承担熟料煅烧过程中耗热最多的碳酸盐分解任务,其耗煤量巨大,约占水泥烧成过程的60%,它既是一
个燃烧炉,同时也是一个化工反应装置,具有燃料燃烧、气固换热和碳酸盐分解等多种功能。
达到其理想的控制调节存在一定的困难,主要原因在于:
a预热部分从预热器到分解炉始终处于全密闭状态,无法检测到实际的燃烧状态,对于分解炉的控制只能通过分解炉中部温度的稳定来实现;
b系统喂煤量、生料喂料量、三次风的风温、风压对分解炉温度等参数均有一定影响,且各因素之间存在非线性耦合关系,造成分解炉出口温度调节的大滞后性和工况波动的严重性。
鉴于以上原因,目前生产线采用人工控制,而由于不同水平的中控操作员对分解炉的控制效果差别很大,存在分解炉温度波动大的现象:
温度过高容易引起预热器结皮,影响窑系统正常运行;温度过低,则造成入窑分解率过低,增加窑系统负担,不能充分发挥分解炉作用。
同时,分解炉内温度大幅波动也造成熟料产量低、质量差并且能耗大的问题,
1.2、分解炉节能专家系统技改方案
分解炉及窑系统示意图见图1。
该项节能技术主要是对熟料生产线的生料下料量、二次风温、三次风温,喂煤下料量,分解炉出口温度,C1,C2,C3,C4,C5口的温度和压力等烧成关键数据进行数据挖掘,分析预热器和回转窑内大量变量之间的关系,建立预测模型,结合水泥分解炉专家库来控制給煤量,达到生产中风、煤、料合理配比,稳定工况,从而实现生产过程的持续稳定进行,提高气固之间的热交换率,稳定生料在分解炉内的最佳分解率,使F-GaO接近最佳值,在一定程度上提高熟料的质量;减轻窑内煅烧带的热负荷,延长熟料生产窑炉的连续运行周期,提高产能,从而实现生产节能减排的目的。
图1.1分解炉及窑系统示意图
优化控制系统分为两部分进行设计,即分解炉温度优化设定系统和分解炉温度自动控制系统:
前者根据由生料三率值KHn、p和生料细度建立起的基于LS-SVM的分解炉温度预设定模型得出分解炉出口温度的预设定值,然后经其于专家系统的温度设定补偿模型和基于Fuzzy系统的温度设定校正模型对分解炉温度预设定值进行补偿校正,得出当前工况下分解炉出口温度的最优设定值;然后分解炉温度自动控制系统以此最优设定值作为系统的设定值,通过多模态控制自动识别出不同的模态,选择相应的算法对变速积分PID控制进行校正,
将分解炉温度稳定在最优设定值上。
1.3、本技术优越性分析
分解炉系统固有的时变、大滞后、非线性的特性和工况波动大的问题使得传统的控制方式无法取得理想的应用效果。
虽然国外的水泥优化控制研究与应用领先于国内,但由于国外优化控制软件价格昂贵、技术保密和国内水泥企业测控点少、工况波动大的现状,使得国外先进的水泥优化控制技术无法在国内的水泥企业取得良好的应用效果;而国内的智能控制的研究成果尚未在国内水泥企业得到广泛的推广,与真正的工业应用还有很大的距离。
与其它同类技术相比,本分解炉节能专家系统具有以下优势:
1)可达到分解炉内各参数精准的控制效果。
窑尾分解炉出口温度趋于平稳波动,80%以上的时间将温度稳定在设定值的上下5C范围之内;窑况从总体上趋于稳定,为熟料产量的上升和质量的提高创造良好的条件,使生料在分解炉内F-GaO接近最佳分解率。
2)炉窑的用煤量得到高比例控制,提高了窑炉的寿命及运转率,减少了有害废气排放。
3)稳定工况下24小时无人值守。
项目的实施彻底改变分解炉长期处于人工操作的局面,实现自动控制。
作
为窑操作员的辅助软件,能够长时间多天的连续运行。
4)快速定制过程和成熟的专家寻优系统。
5)应用案例多,节能效益显著。
本技术在山水集团临朐生产线、天瑞汝州水泥有限公司、沂州水泥一线二
线等工程中得到应用,现场实测数据证实了本技术的节能效果。
(实测结果详见第六部分)
6)投资回收期短,一年即可回收投资成本。
(经济性分析详见第三部分)
2、空压机节能技术方案
2.1、当前空压机运行状况分析
1)、5000t/d生产线一般配备4台110kW(20m3/min)。
因用气负荷波动较大,空压机单位时间内加载、卸载次数过大。
2)、空压机额定出口压力0.8MPa,当用气负荷较低时,出口压力可高达1.3MPa同一出气量条件下,系统每升高/降低0.1