工艺安全控制改造技术指导方案.docx
《工艺安全控制改造技术指导方案.docx》由会员分享,可在线阅读,更多相关《工艺安全控制改造技术指导方案.docx(21页珍藏版)》请在冰豆网上搜索。
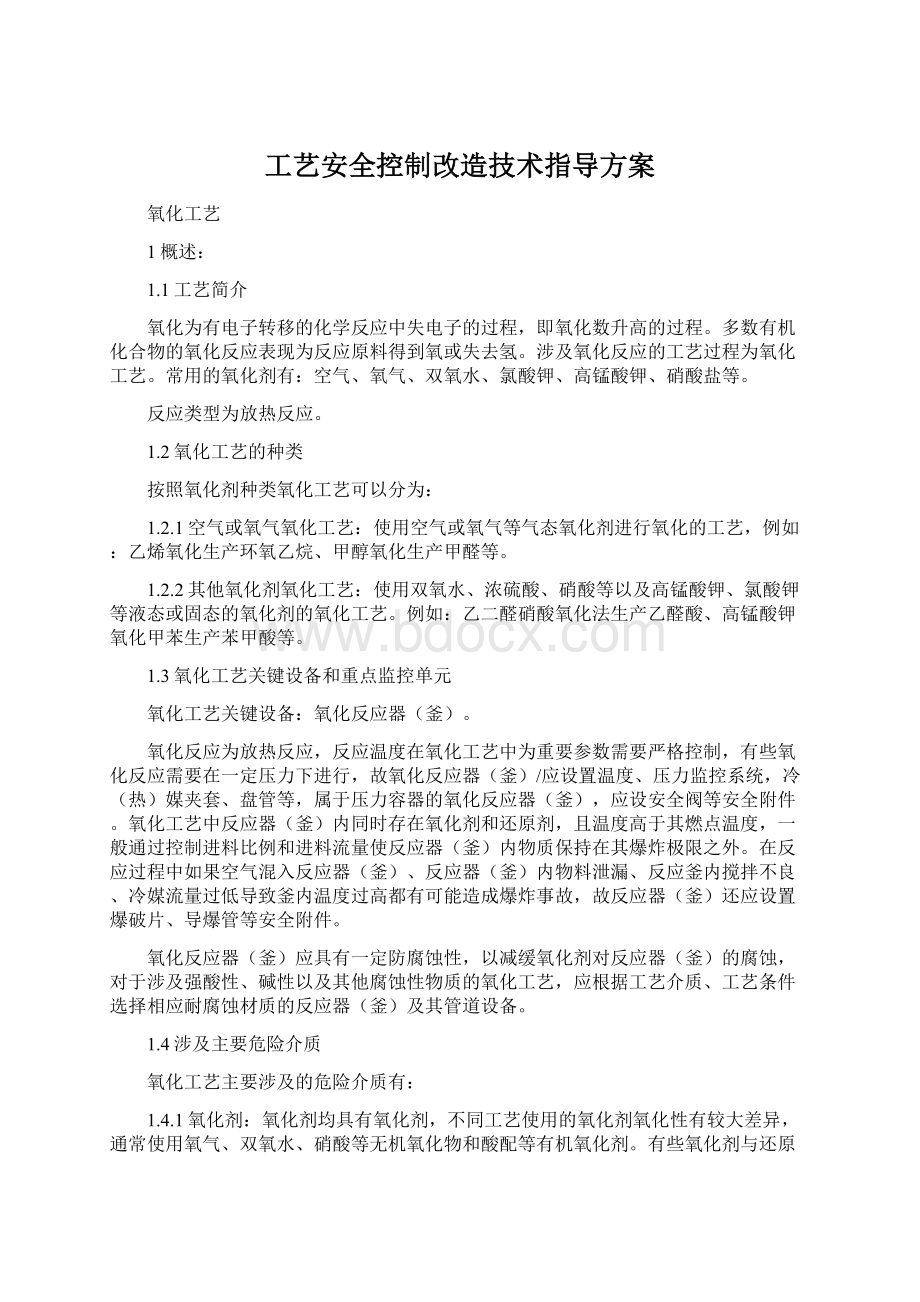
工艺安全控制改造技术指导方案
氧化工艺
1概述:
1.1工艺简介
氧化为有电子转移的化学反应中失电子的过程,即氧化数升高的过程。
多数有机化合物的氧化反应表现为反应原料得到氧或失去氢。
涉及氧化反应的工艺过程为氧化工艺。
常用的氧化剂有:
空气、氧气、双氧水、氯酸钾、高锰酸钾、硝酸盐等。
反应类型为放热反应。
1.2氧化工艺的种类
按照氧化剂种类氧化工艺可以分为:
1.2.1空气或氧气氧化工艺:
使用空气或氧气等气态氧化剂进行氧化的工艺,例如:
乙烯氧化生产环氧乙烷、甲醇氧化生产甲醛等。
1.2.2其他氧化剂氧化工艺:
使用双氧水、浓硫酸、硝酸等以及高锰酸钾、氯酸钾等液态或固态的氧化剂的氧化工艺。
例如:
乙二醛硝酸氧化法生产乙醛酸、高锰酸钾氧化甲苯生产苯甲酸等。
1.3氧化工艺关键设备和重点监控单元
氧化工艺关键设备:
氧化反应器(釜)。
氧化反应为放热反应,反应温度在氧化工艺中为重要参数需要严格控制,有些氧化反应需要在一定压力下进行,故氧化反应器(釜)/应设置温度、压力监控系统,冷(热)媒夹套、盘管等,属于压力容器的氧化反应器(釜),应设安全阀等安全附件。
氧化工艺中反应器(釜)内同时存在氧化剂和还原剂,且温度高于其燃点温度,一般通过控制进料比例和进料流量使反应器(釜)内物质保持在其爆炸极限之外。
在反应过程中如果空气混入反应器(釜)、反应器(釜)内物料泄漏、反应釜内搅拌不良、冷媒流量过低导致釜内温度过高都有可能造成爆炸事故,故反应器(釜)还应设置爆破片、导爆管等安全附件。
氧化反应器(釜)应具有一定防腐蚀性,以减缓氧化剂对反应器(釜)的腐蚀,对于涉及强酸性、碱性以及其他腐蚀性物质的氧化工艺,应根据工艺介质、工艺条件选择相应耐腐蚀材质的反应器(釜)及其管道设备。
1.4涉及主要危险介质
氧化工艺主要涉及的危险介质有:
1.4.1氧化剂:
氧化剂均具有氧化剂,不同工艺使用的氧化剂氧化性有较大差异,通常使用氧气、双氧水、硝酸等无机氧化物和酸配等有机氧化剂。
有些氧化剂与还原性物质能形成爆炸性混合物,部分氧化剂具有燃爆性,遇热、光照、摩擦或碰撞以及与有机物、金属接触时引起火灾爆炸。
有些氧化剂具有一定毒性和腐蚀性。
1.4.2氧化原料:
氧化反应原料主要为各种有机物如芳香烃类、脂肪烃类、醇类、醛类等物质。
氧化原料大多为可燃性物质,部分氧化原料与氧化性物质能形成爆炸性混合物。
不同氧化原料具有不同的中毒特性和腐蚀性,部分氧化原料对人体有一定刺激性,如有些醇类、醛类、有机酸类等。
部分原料为无毒无刺激物质,如甲烷、乙烯等烷烃类、烯烃类物质。
1.4.3产品:
氧化产品大部分为可燃液体,与氧化性物质能形成爆炸性混合物,部分氧化产品受热或光照条件下发生分解或是爆炸如部分种类的酸配。
氧化产品多数有一定中毒危险性和腐蚀性,并有一定刺激性,如有机酸类、醛类等。
有些氧化产品、过氧化物化学稳定性差、有强氧化性,遇有机物能引起燃爆。
1.4.4催化剂:
有些氧化工艺需要使用催化剂。
涉及催化剂种类较多,如金属氧化物、无机酸、以及部分种类的有机物,其火灾危险性、中毒危险性以及腐蚀性有较大差异。
大部分金属氧化物一般条件下无燃烧危险性,一般情况下无毒,但部分种类的重金属氧化物有剧毒。
部分无机酸具有一定氧化性,能与还原性物质或金属发生氧化反应,甚至起火爆炸。
2氧化工艺危险性分析
2.1固有危险性
固有危险性指氧化反应中的原料、产品、中间产品等本身具有的危险有害特性。
2.1.1火灾危险性:
在氧化工艺过程中,氧化剂与还原剂在反应器(釜)内进行受控制的氧化还原反应,一般氧化工艺的反应温度在其物料的燃点或是闪点以上,当反应器(釜)进料管线混入空气或是釜内物料进料比例出现变化,反应釜器(釜)达到燃烧条件,或是反应器(釜)内物质发生泄漏,都会出现火灾危险。
有些氧化剂及氧化产物,如双氧水、高锰酸钾、部分酸配等物质受热、光照、或摩擦碰撞等条件下发生分解反应,放出大量热量甚至发生爆炸。
部分种类的氧化剂如浓硫酸、过氧化钠、过氧化钡等还原性物质或水接触放出大量热量,或与金属接触放出可燃性气体。
当上述种类物质在工艺过程和储运过程中由于处理不当均有可能造成火灾事故。
2.1.2爆炸危险性:
氧化工艺中,氧化原料一般为还原性物质。
氧化剂具有氧化性,在工艺条件下,反应温度一般超过了氧化原料的燃点或闪点,通过控制反应器(釜)内物料浓度在其爆炸极限之外,避免反应器(釜)内发生化学爆炸。
当氧化器(釜)内进料比例出现变化、进料管线内混入空气或是设备及管道出现泄漏,就会发生火灾爆炸事故。
空气或氧气等气态氧化剂流量过大,也会导致反应器(釜)内压力过高而发生物理爆炸。
有些氧化剂及氧化产物,如双氧水、高锰酸钾、部分种类的酸配等物质受热、光照、摩擦碰撞等条件下发生分解反应,放出大量热量甚至发生爆炸。
部分种类的氧化剂如浓硫酸、过氧化钠、过氧化钡等与还原剂或水接触放出大量热量,若遇金属则放出燃烧性气体。
当上述种类物质在生产过程和储运过程中,由于处理不当均有可能造成爆炸事故。
2.1.3中毒危险危害性:
氧化工艺中,中毒危害性如下:
1)氧化剂:
部分氧化剂如空气、氧气无中毒危险性,其他种类的氧化剂如高锰酸钾、次氯酸钠、高氯酸盐等均有一定中毒危险性;浓硫酸、硝酸等物质有强酸性和强氧化性,能造成严重的化学灼伤,对皮肤有较强的刺激性。
2)氧化原料及氧化产品:
不同氧化原料及产品中毒危险性不尽相同,原料如乙醇、脂肪醇类、乙烯、乙炔等,产品如乙酸,无中毒危害或中毒危害较低;部分氧化原料如苯胺、甲苯、甲醇等,产品如甲醛、硝基苯等则有较强的毒性。
2.1.4腐蚀及其他危险性:
氧化工艺中腐蚀性危害主要是氧化剂对金属、橡胶制品等的腐蚀作用,同时部分氧化剂或是氧化原料具有一定酸碱性(特别是在较高温度下使用强氧化剂的氧化工艺),腐蚀作用会使工艺设备、管道老化,强度下降,导致设备、管道泄漏或发生爆炸,同时发生火灾和中毒事故。
2.2工艺过程危险性分析
氧化反应过程为放热反应,反应器(釜)中同时存在氧化性物质和还原性物质,且反应温度一般在其燃点、闪点以上,当出现泄漏或反应器(釜)内混入空气,达到一定浓度时,会发生火灾爆炸事故。
同时,部分的氧化剂及氧化产品具有较强的腐蚀性(如浓硫酸、硝酸等),若设备、管道选材不当,容易发生泄漏,导致火灾、爆炸、中毒等事故。
对于部分以空气、氧气等氧化性气体作为氧化剂的工艺,其反应在一定压力下进行,若其压力设备设计、安装不当,可能导致设备运行中出现泄漏,导致火灾事故。
此外对于气相氧化工艺,其反应温度在原料燃点以上,当开、停车时,惰性气体置换不完全可能引发火灾事故。
部分氧化工艺涉及的原料、中间体或产品在遇热、光照、碰撞或摩擦条件下发生分解甚至爆炸,故在氧化工艺过程中,当设备、管道发生泄漏、反应器(釜)内温度过高或在物料的处理、储运过程中处理不当,都有可能造成火灾、爆炸或中毒事故。
部分工艺,特别是低温氧化工艺,生产过程中会产生过氧化物,氧化产物在进一步分离之前,应消除其中的过氧化物。
部分氧化工艺在开、停车前需要进行惰性气体置换,避免在开、停车过程中,因装置内残留空气或是工艺气体引发火灾、爆炸或中毒事故。
本指导方案在实际应用中,其工艺产品的具体危险性应根据相关风险评价方法,对整个工艺过程的危险性进行分析。
3重点控制工艺参数和控制的基本要求
3.1反应温度
氧化工艺均为放热反应,氧化反应器(釜)内存在氧化剂和还原剂,在反应器(釜)内进行控制下的氧化还原反应。
对于反应器(釜),其反应温度一般与反应速率、反应程度、反应压力均有关系,所以反应温度作为重要的工艺参数需要进行严格的监控,防止反应温度异常。
在反应器(釜)上应设置温度控制联锁系统,一般反应器(釜)内温度与反应器(釜)冷媒流量和反应进料量控制进行联锁,当反应器(釜)内温度过高时,通过加大冷媒流量、减少反应器(釜)内进料量来降低反应器(釜)内温度。
对于连续氧化工艺,反应器温度一般与反应进料和反应器冷媒流量联锁,当反应器内温度过高,通过加大冷媒流量、改变物料配比、减小进料量或降低反应压力来降低反应温度。
3.2反应压力
对于间歇氧化工艺,一般采用釜式反应器,氧化反应器内压力与釜内温度有一定关系,需要对其进行监控,防止反应釜内出现超温超压情况。
如果氧化剂为气态时,如空气、氧气等,反应一般需要在一定压力下进行,反应釜内压力与进气速率、反应速率有直接关系,需要进行严格监控,防止反应釜内氧含量过高或过低、反应温度异常造成的压力过高发生设备、管道破损泄漏引发火灾、爆炸事故。
反应釜压力一般通过控制反应温度和进料速率进行控制。
对于连续氧化工艺,反应压力与反应速率和反应温度有密切的关系,压力升高一般能提高反应速率,使反应器内温度升高。
反应器需要安装压力监控联锁,反应器内压力一般由反应进料的温度和压力、反应器出口压力以及反应器冷媒流量进行控制。
当反应器内压力过高时,通过加大反应器内冷媒流量、减小反应器进料速率来降低反应器压力。
3.3反应釜搅拌
对于釜式反应器,氧化工艺需要对反应釜搅拌状况或速率进行监控。
搅拌速率与反应釜内热量分布有关,因搅拌异常,导致反应釜内传质、传热不良,可能降低产品产率,还可能因釜内局部温度过高出现火灾和爆炸。
对反应釜搅拌速率的监控,一般反映在反应釜搅拌电机电流上,通过监控反应釜搅拌电机电流,防止因反应釜搅拌不良、停车可能造成火灾、爆炸事故。
3.4氧化剂流量
氧化工艺需要对氧化剂流量、反应物料的配比进行监控。
氧化工艺中,氧化器(釜)内同时存在氧化剂和还原剂,反应器(釜)内温度一般在物料燃点以上,通过控制反应器(釜)内物料配比量,使反应器(釜)内物料不能达到燃烧或爆炸条件,来控制氧化还原反应在安全条件下进行。
3.5气相氧含量和过氧化物含量
部分氧化工艺需要监控反应器(釜)内气相氧含量,防止反应器(釜)内气相达到爆炸极限。
反应器(釜)内温度一般在物料燃点以上,当反应器(釜)物料达到其爆炸极限范围内,会发生火灾爆炸事故。
部分氧化工艺在反应器(釜)内形成过氧化物中间体,或是氧化剂本身为过氧化物,由于过氧化物不稳定,在受热、光照等条件下可能发生分解、自燃甚至发生爆炸,所以在可能出现因反应器(釜)内过氧化物发生事故的氧化工艺,宜对反应器(釜)内过氧化物含量进行监控。
4推荐的安全控制方案
4.1各工艺参数控制方式
氧化工艺的温度、压力、进料流量及物料配比、反应釜液位及搅拌速率、冷媒运行状况、反应气体O2含量等重点监控工艺参数的控制方式见附表二。
4.2工艺系统控制方式
4.2.1基本监控要求
(1)氧化反应应实现反应器(釜)的温度和压力的自控,并设置报警和联锁系统。
其温度、压力自控方式可根据工艺过程原理采取简单控制系统或复杂控制系统。
反应器(釜)体积较大、反应热分配不均匀时,应增加温度测量点数,取其数个关键点的温度平均值作为反应釜的被控温度。
当反应器(釜)的温度和压力达到报警设定值时,发出声光报警;当反应器(釜)的温度和压力达到或超过联锁设定值时,启动联锁:
切断投料,终止反应,紧急送入惰性气体、冷媒阀门全开以带走反应热等,并同时发出声光报警。
(2)氧化反应为连续工艺过程时,参与反应的原料应有温度、压力、流量监测,应实现各原料进料的恒定控制或比值控制和联锁。
生产中若某种原料流量出现异常,要保证切断危及安全的原料投入,并发出声光报警。
(3)对于带搅拌器的反应釜,应实现搅拌器运行状况的监控和联锁。
搅拌器运行状况的监控可采取监测搅拌电机的电流、搅拌器的转速来实现。
当搅拌器出现异常时,应发出声光报警,若危及安全时,应联锁停产:
切断投料,终止反应,紧急送入惰性气体、冷媒阀门全开以带走反应热等,并同时发出声光报警。
(4)应设置原料进料紧急切断系统,使工艺操作人员可在操作室内切断原料的投入。
(5)应设置反应器(釜)的紧急冷却系统、紧急泄放系统及事故状态下的吸收中和系统等运。
且这些系统可由操作人员在控制室投运。
(6)根据工艺的实际情况,在组分测