输出轴加工工艺课程设计.docx
《输出轴加工工艺课程设计.docx》由会员分享,可在线阅读,更多相关《输出轴加工工艺课程设计.docx(25页珍藏版)》请在冰豆网上搜索。
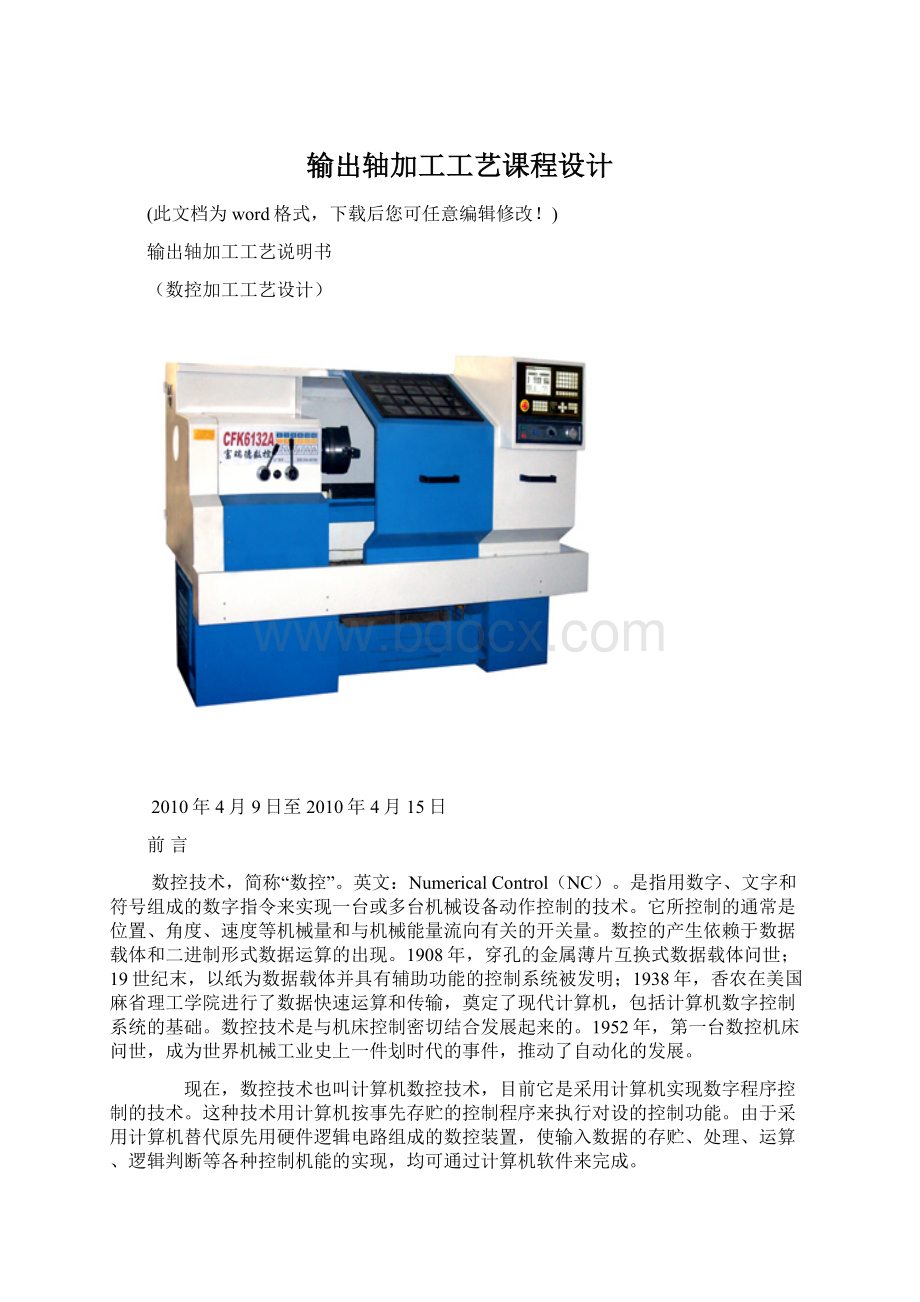
输出轴加工工艺课程设计
(此文档为word格式,下载后您可任意编辑修改!
)
输出轴加工工艺说明书
(数控加工工艺设计)
2010年4月9日至2010年4月15日
前言
数控技术,简称“数控”。
英文:
NumericalControl(NC)。
是指用数字、文字和符号组成的数字指令来实现一台或多台机械设备动作控制的技术。
它所控制的通常是位置、角度、速度等机械量和与机械能量流向有关的开关量。
数控的产生依赖于数据载体和二进制形式数据运算的出现。
1908年,穿孔的金属薄片互换式数据载体问世;19世纪末,以纸为数据载体并具有辅助功能的控制系统被发明;1938年,香农在美国麻省理工学院进行了数据快速运算和传输,奠定了现代计算机,包括计算机数字控制系统的基础。
数控技术是与机床控制密切结合发展起来的。
1952年,第一台数控机床问世,成为世界机械工业史上一件划时代的事件,推动了自动化的发展。
现在,数控技术也叫计算机数控技术,目前它是采用计算机实现数字程序控制的技术。
这种技术用计算机按事先存贮的控制程序来执行对设的控制功能。
由于采用计算机替代原先用硬件逻辑电路组成的数控装置,使输入数据的存贮、处理、运算、逻辑判断等各种控制机能的实现,均可通过计算机软件来完成。
输出轴的用途很广泛,该输出应用在动力输出装置中,是动力输出的关键零件之一。
该输出轴在工作中需要承受一定冲击载荷和较大的扭矩,因此该零件应具有足够的耐磨性和抗扭强度。
所以设计中一定要注意表面热处理。
前言………………………………………………………………2
一、设计任务书……………………………………………………4
二、输出轴工艺分析
2.1输出轴的作用…………………………………………………6
2.2输出轴的结构特点、工艺,表面技术要求分析……………6
三、确定毛胚
3.1选择毛胚材料…………………………………………………7
3.2毛胚的简图……………………………………………………7
四、工艺路线的确定
4.1基准的选择……………………………………………………8
4.2各表面加工方法的确定………………………………………8
4.3工序集中和分散考虑………………………………………9
4.4加工设备于工艺设备的的选择……………………………9
五、加工顺序的安排………………………………………………10
六、走刀路线的确定………………………………………………11
七、刀具的选择………………………………………………………11
八、切削用量的选择…………………………………………………12
九、小结…………………………………………………………………13
十、参考文献……………………………………………………………13
附工艺过程卡、工序卡、加工程序…………………………………14
一、设计任务书
数控加工工艺课程设计任务书
1.设计题目:
输出轴加工工艺说明书
2.设计要求:
1.零件任选
2.零件图一张(可复印)
3.机械加工工艺规程卡片一套
4.说明书一份
5.按大批大量生产考虑
。
二、输出轴工艺分析
2.1输出轴的作用
输出轴主要应用在动力输出装置中,是输出动力的主要零件之一。
其主要作用是传递转矩,使主轴获得旋转的动力,其工作中要承受较大的冲击载荷和扭矩。
因此,该零件需具有足够的耐磨性和抗扭强度。
2.2输出轴的结构特点、工艺,表面技术要求分析
从图示零件分析,该输出轴结构简单,属于阶梯轴类零件。
主要由有φ55、φ60、φ65、φ75、φ176的外圆柱面、φ50、φ80、φ104的内圆柱表面和10个φ20的孔和一个16的键槽组成。
为了保证输出轴旋转是的速度,表面粗糙度有较高的要求,外圆的粗糙度要求都为Ra1.25um,内圆的粗糙度为Ra2.5um,其余为Ra20um。
形位精度也比较高,为了外圆和外面零件的配合后受力均匀,φ55,φ60的外圆的径向跳动量小于0.04mm,φ80的跳动量小于0.04mm,φ20孔的轴线的跳动量小于0.05mm,为了保证键槽和键的配合,键槽对φ55外圆的对称度为0.08mm。
由于输出轴在工作中要承受较大的冲击载荷和扭矩,为了增强耐磨性和抗扭强度,要对输出轴进行调质处理,硬度为250HBS。
三、确定毛胚
3.1选择毛胚材料
毛胚的种类有很多,如1、型材2、锻造3、铸造,由于该输出轴要承受较大的冲击载荷和扭矩,为了增强其刚性和韧性,所以要选择锻件做为毛胚。
如选用棒料,由于生产类型为中批,从经济上考虑,棒料要切削的余量太大,浪费材料。
3.2毛胚的的简图
四、工艺路线的确定
4.1基准的选择
基准可以分为粗基准和精基准
4.11粗基准
由于此零件为轴类零件,为了保证精度,所以选择外圆作为粗基准面。
首先选用三爪卡盘自动找正原理,夹紧。
以外圆为粗基准面,加工外圆、端面、中心孔。
然后用已加工过的外圆作为基准,加工另一端面和钻中心孔,保证两个中心孔在同一直线上。
4.12精基准的选择
精基准的选择对一个零件加工完成后的精度非常重要。
此零件选用两端的中心孔作为精基准,所以用两端中心孔来对外圆精加工。
外圆加工完成后用外圆作为精基准,加工内圆。
4.2各表面加工方法的确定
φ176外圆:
粗车
φ55外圆:
粗车—精车
φ60外圆:
粗车—精车
φ65外圆:
粗车—精车
φ75外圆:
粗车—精车
φ50内圆:
粗铣
φ80内圆:
车孔-铰孔
φ104内圆:
车孔
φ20孔:
钻孔-铰孔
左端面:
粗车
右端面:
粗车
键槽:
粗铣-精铣
4.3工序集中和分散考虑
4.31工序集中
工序集中就是将零件的加工集中在少数几道工序中完成,每道工序加工内容多,工艺路线短。
其主要特点是:
可以采用高效机床和工艺装备,生产率高;
减少了设备数量以及操作工人人数和占地面积,节省人力、物力;
减少了工件安装次数,利于保证表面间的位置精度;
采用的工装设备结构复杂,调整维修较困难,生产准备工作量大。
4.32工序分散
工序分散就是将零件的加工分散到很多道工序内完成,每道工序加工的内容少,工艺路线很长。
其主要特点是
设备和工艺装备比较简单,便于调整,容易适应产品的变换,对工人的技术要求较低;
可以采用最合理的切削用量,减少机动时间;
所需设备和工艺装备的数目多,操作工人多,占地面积大。
工序集中或分散的程度,主要取决于生产规模。
一般情况下,单件小批生产时,采用工序集中,在一台普通机床上加工出尽量多的表面;批量生产时,采用工序分散。
终上以及结合图纸要求,采用工序分散。
4.4加工设备于工艺设备的的选择
5.41普通车床CS6140
床身上最大回转直径Φ400mm,床鞍上最大回转直径Φ220mm,最大工件长度1000mm;主轴通孔直径Φ52mm,主轴头型式CS6140:
ISO702IIINO.6卡口型;其余:
ISO702IINO.8凸轮锁紧型,主轴转速范围24级9-1600rpm,主轴电机功率7.5KW;套筒直径行程Φ75150mm,顶尖锥度5MT;3、刀位数刀方尺寸425X25;X、Z向最大行程145mm、320mm,X、Z向进给范围93种0.028-6.43mmr、93种0.012-2.73mmr,公制螺纹范围48种0.5-224mm,英制螺纹范围48种72-14t.p.i,模数螺纹范围42种0.5-112πmm,径节螺纹范围42种56-14t.p.i.π
4.42数控车床CAK6136V750
CAK6136V750,床身上最大回转直径:
ф360MM,滑板上最大回转直径:
ф180MM,滑板上最大切削直径:
ф180MM,最大加工长度:
650MM,主轴通孔直径:
ф53MM,MM,Z轴最大行程:
660MM,机床重复定位精度:
X轴:
0.007,Z轴:
0.01,加工精度:
IT6,粗糙度:
RA1.6,机床净重毛重:
2030*3170KG,包装箱尺寸:
(长*宽*高):
2500*1640*2145MM.
4.43数控铣床XK713
工作台面积mm1000×320T型槽(槽数槽宽间距)mm31480X轴行程mm600Y轴行程mm320Z轴行程mm450主轴端面至工作台台面距离mm100~550工作台最大载重kg300主轴锥孔 ISO7:
24锥度No.40主轴轴径扭矩mmNmΦ60108Nm主轴电机kW5.5Kw主轴转数rpm30~4000或6000(无级)快速移动速度(X、Y、Z轴)rpm8000切削进给速度mmmin10~4000伺服电机输出扭矩N·m6齿轮润滑电机功率kW0.04刀具最大直径长度重量 Φ110mm400mm18kg电源容量KVA15机床外观尺寸mm2200×1700×2000机
五、加工顺序的安排
毛坯热处理退火(消除内应力)
普车粗车各外圆和左端面
普车粗、精车右端面、φ176外圆钻中心孔
数控车粗、精车各圆柱面(除被装夹面)
数控车精车左端各外圆
数控车钻φ45的孔,车φ50、φ80、φ104,φ80的留铰的余量
数控车铰φ80孔
数控铣钻φ20φ8孔、铰孔
数控铣铣键槽
六、走刀路线的确定
合理确定走刀路线对于保证被加工零件的加工精度和表面质量以及提高编程和加工效率起着非常重要的作用。
尤其是加工轴类零件。
应做到走刀路线短,刀具空行程少,这样才能提高工作效率。
5.7工序尺寸及公差的确定
工序尺寸及公差的确定在机械加工中起着至关重要的作用。
要按照给定的精度等级选定公差。
加工部位粗车余量及公差等级精车余量及公差等级
φ176外圆5IT12
φ55外圆15IT121IT6
φ60外圆12IT121IT6
φ65外圆5IT121IT6
φ75外圆5IT121IT6
七、刀具的选择
刀具的选择是数控加工工艺中的重要内容之一,不仅影响机床的加工效率,而且直接影响零件的加工质量。
应考虑以下方面:
(1)根据零件材料的切削性能选择刀具。
(2)根据零件的加工阶段选择刀具。
(3)根据加工区域的特点选择刀具和几何参数。
由于我们要加工的零件材料要求为45钢,根据要求,选择硬质合金刀。
(1)粗车外圆:
0190°外圆车刀
(2)精车外圆0270°外圆车刀
(3)端面:
0390°端面车刀
(4)打孔钻头:
04、05φ18、φ45高速钢钻
(5)内圆0690°内孔刀
(6)键槽073.0*13键槽铣刀3.0*13
八、切削用量的选择
所谓合理的切削用量是指充分利用刀具的切削性能和机床性能,在保证加工质量的前提下,获得高的生产率和低的加工成本的切削用量。
制订切削用量,就是要在已经选择好刀具材料和几何角度的基础上,合理地确定背吃刀量、进给量。
加工部位粗背吃刀量精车吃刀量进给量mmr
各外圆3.00.51.2
端面0.5
键槽520.1
铰孔0.1
九、小结
随着课程设计的逐渐完成,使我对《机械制造工艺学》这门课程以及对数控加工技术都有了更深入的理解和掌握。
在这段时间里,我尽着自己最大的努力学习,来学习和创新。
为了解决技术上的问题,我也不断地去翻阅所学的专业书籍和各种相关。
我认为,这种实训我受益匪浅,因为我暴露出了自己的不足。
十、参考文献
【1】赵长旭数控加工工艺西安电子科技大学2006
【2】赵长旭数控加工工艺课程设计指导书西安电子科技大学2007
【3】王健石机械加工常用刀具数据速查手册