冻干粉针剂生产设备验证.docx
《冻干粉针剂生产设备验证.docx》由会员分享,可在线阅读,更多相关《冻干粉针剂生产设备验证.docx(13页珍藏版)》请在冰豆网上搜索。
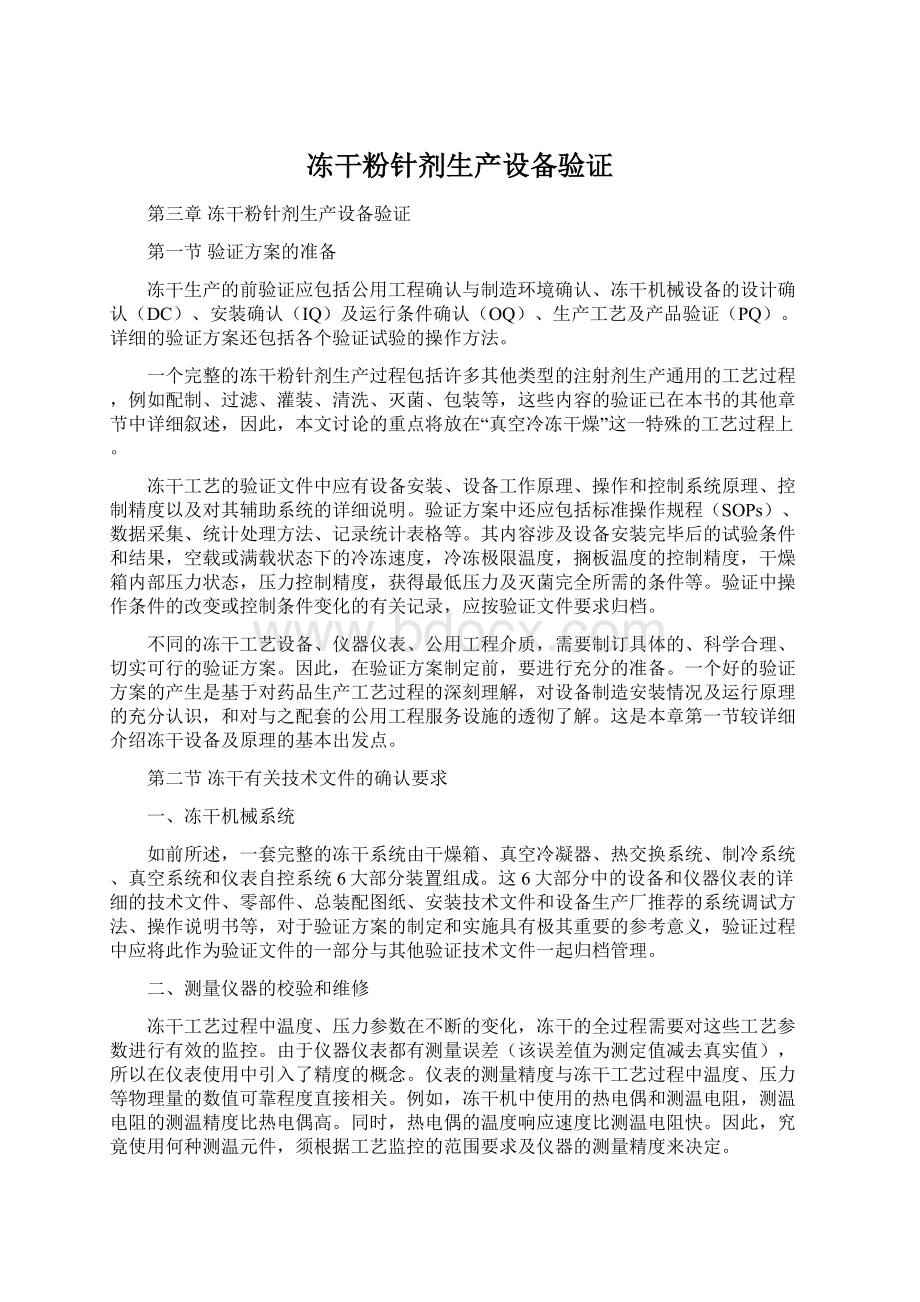
冻干粉针剂生产设备验证
第三章冻干粉针剂生产设备验证
第一节验证方案的准备
冻干生产的前验证应包括公用工程确认与制造环境确认、冻干机械设备的设计确认(DC)、安装确认(IQ)及运行条件确认(OQ)、生产工艺及产品验证(PQ)。
详细的验证方案还包括各个验证试验的操作方法。
一个完整的冻干粉针剂生产过程包括许多其他类型的注射剂生产通用的工艺过程,例如配制、过滤、灌装、清洗、灭菌、包装等,这些内容的验证已在本书的其他章节中详细叙述,因此,本文讨论的重点将放在“真空冷冻干燥”这一特殊的工艺过程上。
冻干工艺的验证文件中应有设备安装、设备工作原理、操作和控制系统原理、控制精度以及对其辅助系统的详细说明。
验证方案中还应包括标准操作规程(SOPs)、数据采集、统计处理方法、记录统计表格等。
其内容涉及设备安装完毕后的试验条件和结果,空载或满载状态下的冷冻速度,冷冻极限温度,搁板温度的控制精度,干燥箱内部压力状态,压力控制精度,获得最低压力及灭菌完全所需的条件等。
验证中操作条件的改变或控制条件变化的有关记录,应按验证文件要求归档。
不同的冻干工艺设备、仪器仪表、公用工程介质,需要制订具体的、科学合理、切实可行的验证方案。
因此,在验证方案制定前,要进行充分的准备。
一个好的验证方案的产生是基于对药品生产工艺过程的深刻理解,对设备制造安装情况及运行原理的充分认识,和对与之配套的公用工程服务设施的透彻了解。
这是本章第一节较详细介绍冻干设备及原理的基本出发点。
第二节冻干有关技术文件的确认要求
一、冻干机械系统
如前所述,一套完整的冻干系统由干燥箱、真空冷凝器、热交换系统、制冷系统、真空系统和仪表自控系统6大部分装置组成。
这6大部分中的设备和仪器仪表的详细的技术文件、零部件、总装配图纸、安装技术文件和设备生产厂推荐的系统调试方法、操作说明书等,对于验证方案的制定和实施具有极其重要的参考意义,验证过程中应将此作为验证文件的一部分与其他验证技术文件一起归档管理。
二、测量仪器的校验和维修
冻干工艺过程中温度、压力参数在不断的变化,冻干的全过程需要对这些工艺参数进行有效的监控。
由于仪器仪表都有测量误差(该误差值为测定值减去真实值),所以在仪表使用中引入了精度的概念。
仪表的测量精度与冻干工艺过程中温度、压力等物理量的数值可靠程度直接相关。
例如,冻干机中使用的热电偶和测温电阻,测温电阻的测温精度比热电偶高。
同时,热电偶的温度响应速度比测温电阻快。
因此,究竟使用何种测温元件,须根据工艺监控的范围要求及仪器的测量精度来决定。
虽然测定仪表的精度在控制系统的设计中已经予以考虑,但为了使验证过程获得的
数据准确可靠,在验证前后仍必须对仪表进行校准。
三、公用系统
冻干工艺相关的其他辅助系统,如氮气、冷却水、制药用水系统、压缩空气、纯蒸
汽及工业蒸汽等,由于它们对冻干工艺的影响很大,因此需要根据冻干剂生产的要求进
行确认,确认它们的对冻干工艺的保证能力。
这些系统的技术文件及确认中得到的有关
记录也应按验证的要求归档。
第三节冻干机械设备的确认
根据ISO13408—3冻干机设计的有关要求,前验证的设计确认中,应包括以下内容:
1、冻干机的设计应该有利于干燥箱和真空冷凝器的清洁和灭菌(符合用户指定的清洁和灭菌程序)。
2、冻干机装载、卸载的门,已最终灭菌内包材料暴露处,灌封作业处在百级以上的高洁净控制区域。
3、冻干作业百级以上的高洁净控制区域内环境监测及其他中间控制均不得对产品造成污染。
4、冻干机的设计和安装应能防止由于机械泄漏或暴露所致的微生物污染。
5、设备的内外表面均应光滑,门或其他附加物(如门栓等)的数目应尽可能减少,应对附加物的数目、位置和表面光洁度严格控制。
6、设备的空气过滤系统应能对进入箱体的空气进行除菌,空气过滤器的放置位置也
应方便进行过滤器的完整性测试实验。
7、冻干机的搁板及其升降系统的设计应能防止冷凝物在其间残留,要求搁板平整光
滑,有较低的表面粗糙度。
冻干工艺的验证过程中,冻干机械设备的设计确认与各个性能参数确认占有重要的地位。
工艺的技术参数要求最终都是由执行该工艺过程的机械设备来完成的,因此冻干工艺验证之前,应对冻干系统所包括机械设备的设计能力进行确认,切实证明冻干系统中各设备的运行状况、系统整体运行时的各种参数和运行的可靠性都能够达到预定的设计能力,从而能够最终满足产品的冻干工艺要求,使产品的生产过程能够始终如一地获得预期的结果。
以下所述设备确认项目、试验方法和各种物理参数指标可供验证时参考。
一、冷冻机冷却性能确认
在冻干过程中,冷冻机的作用是将制品溶液的温度降至溶液的三相点温度之下,并向制品干燥过程提供冷冻能量。
制冷,通常采用蒸气压缩的制冷循环方式,蒸气压缩制冷循环原理如图4—3—1所示。
通过冻干机干燥箱内的导热隔板或真空冷凝器,吸热后的低温制冷剂蒸气经过制冷压缩机压缩成为高压的液体,利用冷却装置冷却为高温高压的制冷剂液体,高温制冷剂液体再经过膨胀阀节流膨胀成为低温制冷剂液体,通过蒸发器放热为冻干机提供制冷量,完成一个制冷循环过程。
冷冻系统的能力,通常需在空载与模拟满载两种状态下进行确认。
由于介质间接热交换传递能量法容易保持搁板各部位温度的均一性,它在工业上广泛应用,现将此法为例展开讨论。
1、冻干机制冷方式的设计确认
由于冻干制品在整个冻干工艺过程中,对制冷状态的要求变化很大,冻干机采用的制冷方式给干燥工艺过程的影响必须加以考虑和确认。
冷冻是通过制冷剂在系统内的循环来实现的。
制冷剂在制冷机内压缩,以边冷却边压缩的方式从气态变换为液体,进入冷凝器中,液化了的制冷剂由一副冷却器继续冷却,此后,它通过膨胀阀以喷雾的形式进入蒸发器,在液体转换为气体时,吸收大量的蒸发潜热而制冷。
在完成这一步后,被蒸发的制冷剂(气体)又按上述方式返回到制冷机内,如此循环,连续制冷。
为了避免制冷剂液体的液压缩,在制冷机的吸气口设置有贮液器。
制冷剂液体的蒸发流量,须靠膨胀阀检测蒸发器出口的过热度来控制。
负荷变动不大的设备,制冷机通过开启、停止运行(例如电冰箱,冷库等一般的冷冻系统的运行)可以没有任何问题。
而冻干机中制冷系统的特殊问题首先是其温度变化范围特别大,其次是冻结干燥工艺过程制冷负荷变化剧烈,三是长期在低效率下运行,这些都是在确认中必须加以考虑的问题。
(1)冻干工艺制冷的问题
①温度范围较宽冻干机工作的温度范围较宽,在一个冻干工艺过程中,制品干燥过程的温度通常需要在-40~50℃之间变化,起水分捕集作用的真空冷凝器内的温度需要始终维持在-70~-50℃之间,即导热搁板层的冷却可能从常温冷却直至-60~-50℃。
冷却的时间为1~1.5h,真空冷凝器系则可能需要冷却到-70~-50℃。
②冻结干燥工艺过程制冷负荷变化剧烈冻结真空干燥工艺的缺点之一,就是干燥过程的能耗高。
其中,能耗高主要体现在整个干燥工艺过程中,制冷负荷变化剧烈。
例如,导热搁板系统中,在冻干工艺的不同阶段,需要对导热媒体进行预备冻结制冷;干燥时又需要将导热媒体升温;温度超过干燥工艺的控制范围时还需要再冷却,等等。
而对真空冷凝器系统,需要连续将温度控制在-50℃以下。
因此,冻干机的制冷系统通常需要在恶劣的制冷工况条件下运行,严重地影响冷冻机的制冷效率。
③制冷机长期运行在低效率的无负荷状态下因为冻干工艺的一次、二次干燥阶段时间很长。
在干燥阶段内,只需要少量的冷源就可以满足干燥过程的低温控制要求。
但在冻干工艺过程中,制冷机需要在真空状态下低负荷或无负荷状态下长时间运转,在冻干全过程中,必须将系统控制在供货厂商规定的条件下运行。
(2)冻干机常用的制冷形式
①直接膨胀式制冷的真空冷凝器直接膨胀方式制冷的真空冷凝器(冻干机系统)(图4-3-2,)其主要的制冷原理是使制冷剂在冷却管内直接膨胀、蒸发,蒸发的制冷剂气体通过制冷压缩机压缩、冷凝。
通常,采用制冷贮液器的设置、压缩机高温排气管的旁通,无负荷时、将高温排气作为模拟负荷直接引至制冷机来调控制冷负荷,提高制冷机的效率。
冻干工艺过程中,一次干燥(升华干燥)过程中停电或其他事故发生时,直接膨胀式制冷的真空冷凝器控制系统真空下降的能力比较差。
冻干机也可以采用多套制冷系统的方式来解决真空冷凝器内的温度调控问题,冻干机的制冷机、冷凝器系统由两套以上制冷系统的多回路构成。
但它并没有从根本上解决直接膨胀方式存在的缺陷,特别是对停电等事故发生的适应能力较差问题。
②载冷剂间接冷却单一制冷方式的真空冷凝器载冷剂间接冷却方式的真空冷凝器,其主要的制冷原理是让制冷剂在冷却器内膨胀、蒸发,间接冷却载冷剂,通过导热媒体泵输送载冷剂液体,流过真空冷凝器内的热交换器,控制真空冷凝器的温度。
由于冷凝器内的温度不是通过制冷剂直接膨胀产生的制冷量直接控制,而是由已经调控均匀的载冷剂循环完成的,解决了真空冷凝器内的温度均匀问题,从而导致了制冷系统的稳定运行。
采用载冷剂间接冷却单一制冷方式的冻干机系统(图4-3-3)制冷剂回路从预备冻结到干燥结束由单一回路构成,其优点是制品的导热搁板和真空冷凝器(冷阱)可以同时冷却,真空冷凝器(冷阱)的融冰和导热搁板的冷却也可以同时完成,干燥中的导热搁板亦可以冷却调节温度。
同时,制冷机内部的冷媒液体不会出现直接膨胀制冷方式的反流问题,可以有效地防止制冷机的超负荷运转。
载冷剂间接冷却方式的真空冷凝器主要问题是,因载冷剂间接进行制冷交换带来的换热损失,通过载冷剂循环引起的冷热损失以及载冷剂间接冷却仅仅利用了载冷剂的显热来凝结干燥过程的水蒸气。
③采用三重热交换系统制冷的冻干机三重热交换系统制冷(图4-3-4)的特点是,制冷剂回路与前述单一制冷系统相类似,从预备冻结到干燥结束由单一回路构成,制冷剂与载冷剂的热交换器配置在真空冷凝器的内部。
冷媒与热媒、冷媒与水蒸气、热媒与水蒸气之间的3种媒体能够有效地发挥其功能。
制冷机稳定性导致的事故、故障的减少,能够有效地控制导热搁板的温度、冻干箱内真空度、真空冷凝器内的温度,从而实现制品干燥的匀速恒定。
另外,三重热交换系统通过调整载冷剂的节流开度与三重热交换冷凝器相互作用,稳定地控制真空冷凝器的温度,有效地控制其水蒸气压力,具有较强的抗停电特性。
此外,通过真空冷凝器内温度的有效控制,可以正确地测定干燥箱内的空气泄漏率,并解决了冻干工艺干燥过程中,由于制冷负荷较低,制冷工作运行情况偏离设定条件的难题。
它通过载冷剂循环解决了直接膨胀系统的缺点,又解决了载冷剂循环的难点。
2、空载运转冷却能力的确认
空载状态下,干燥箱内的搁板或真空冷凝器(冷阱)降温速度的确认试验,一般安排在完成IQ后或设备经过较大检修(一般指大修或中修后的再验证)后进行。
在进行此项确认之前,首先应检查确认制冷系统管路、装置无泄漏,冷媒充注量符合设备运行要求,冷冻机试运转试验中各部分压力正确,冷却水温度正常,控制仪表盘上指示的干燥箱内导热媒体进出口温度或真空冷凝器进出口温度与标准温度计一致。
在此基础上使主冷冻机满负荷运行,对干燥箱内搁板或真空冷凝器进行冷却降温,空载状态下主冷冻机的冷却能力一般应达到下列数值。
(1)干燥箱内导热搁板建议标准:
导热媒体的温度从10℃降至-40℃所用时间不得超过70min。
导热媒体的温度从10℃降至-50℃所用时间不得超过90min,即平均降温速度应该>1.5℃/min。
(2)真空冷凝器能够达到的温度建议标准:
真空冷凝器温度应能够低于-70℃。
3、水负荷运转状态冷却能力确认
经空载运转状态确认冷却能力合格后,根据系统拟生产品种的最大负荷量,将此负荷量的注射用水均匀充注入试验用平底托盘(亦称浅盘)内,开启主冷冻机100%,对干燥箱内搁物板或真空冷凝器进行降温。
建议指标参数标准如下。
(1)干燥箱搁板降温速度导热媒体的温度从10℃降至-35℃所用时间不得超过100min。
导热媒体的温度从10℃降至-45℃所用时间不得超过120min。
(2)真空冷凝