烧成系统窑研讨班会议材料091010.docx
《烧成系统窑研讨班会议材料091010.docx》由会员分享,可在线阅读,更多相关《烧成系统窑研讨班会议材料091010.docx(36页珍藏版)》请在冰豆网上搜索。
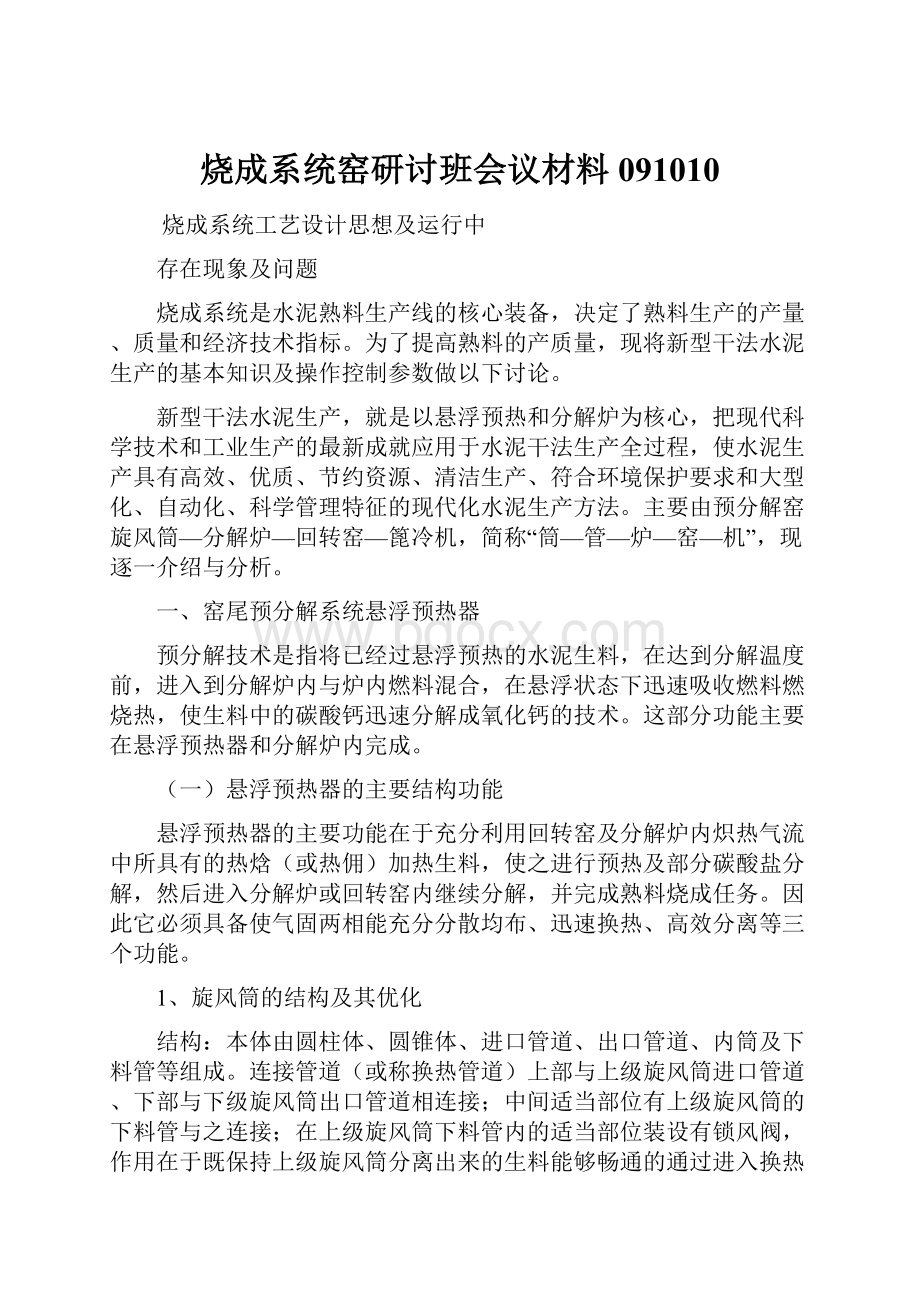
烧成系统窑研讨班会议材料091010
烧成系统工艺设计思想及运行中
存在现象及问题
烧成系统是水泥熟料生产线的核心装备,决定了熟料生产的产量、质量和经济技术指标。
为了提高熟料的产质量,现将新型干法水泥生产的基本知识及操作控制参数做以下讨论。
新型干法水泥生产,就是以悬浮预热和分解炉为核心,把现代科学技术和工业生产的最新成就应用于水泥干法生产全过程,使水泥生产具有高效、优质、节约资源、清洁生产、符合环境保护要求和大型化、自动化、科学管理特征的现代化水泥生产方法。
主要由预分解窑旋风筒—分解炉—回转窑—篦冷机,简称“筒—管—炉—窑—机”,现逐一介绍与分析。
一、窑尾预分解系统悬浮预热器
预分解技术是指将已经过悬浮预热的水泥生料,在达到分解温度前,进入到分解炉内与炉内燃料混合,在悬浮状态下迅速吸收燃料燃烧热,使生料中的碳酸钙迅速分解成氧化钙的技术。
这部分功能主要在悬浮预热器和分解炉内完成。
(一)悬浮预热器的主要结构功能
悬浮预热器的主要功能在于充分利用回转窑及分解炉内炽热气流中所具有的热焓(或热佣)加热生料,使之进行预热及部分碳酸盐分解,然后进入分解炉或回转窑内继续分解,并完成熟料烧成任务。
因此它必须具备使气固两相能充分分散均布、迅速换热、高效分离等三个功能。
1、旋风筒的结构及其优化
结构:
本体由圆柱体、圆锥体、进口管道、出口管道、内筒及下料管等组成。
连接管道(或称换热管道)上部与上级旋风筒进口管道、下部与下级旋风筒出口管道相连接;中间适当部位有上级旋风筒的下料管与之连接;在上级旋风筒下料管内的适当部位装设有锁风阀,作用在于既保持上级旋风筒分离出来的生料能够畅通的通过进入换热管道,又能最大限度地防止下级旋风筒出来的热气流经下料管短路窜入上级旋风筒,造成已被分离的生料粉二次飞扬,降低上级旋风筒的分离效率;在上级旋风筒下料管最下部与换热管道的连接部位还设有撒料装置,目的在于使上级旋风筒下来的生料粉进入换热管道时,由于重力作用冲在撒料器上飞溅起来,使生料粉能够迅速分散、均布在下级旋风筒出来的热气流中,提高换热效率。
2、旋风筒的功能与机理
在旋风预热器中,物料与气流之间的热交换主要在各级旋风筒之间的连接管道中进行,因此对旋风筒本身的设计,主要考虑了如何获得较高的分离效率和较低的压力损失。
旋风筒的主要任务在于气固分离,经过上一级预热单元加热后的生料,通过旋风筒分离后,才能进到下一级换热单元继续加热升温。
3、旋风筒内的气流和粉尘的受力情况
含尘气流在旋风筒内作旋转运动时,气流主要受离心力、器壁的摩擦力的作用;粉尘主要受离心力、器壁的摩擦力和气流的阻力作用。
此外,两者还同时受到一个由于含尘气流从旋风筒上部连续挤压而产生的向下推动力作用,这个推力则是含尘气流旋转向下运动的原因。
由此可见,含尘气流中的气流和粉尘的受力状况基本相同的。
但是由于两者物理特性不同,致使两者在受力状况基本相同的条件下,得到不同的运动效果,从而使得含尘气流最后得到分离。
(二)旋风预热器的主要设计参数
1、成都院(CDC)预热器系统参数
成都院(CDC)预热器系统参数及主要位置风速如下表:
(按2006年12月白马5#标定值计算)
成都院(CDC)预热器主要部位工艺操作参数如下图:
2、南京院(NST-I)预热器系统
南京院(NST-I)预热器系统参数及主要位置风速如下表:
(按2008年5月宣城海螺1#标定值计算)
南京院(NST-I)预热器主要部位工艺操作参数如下图:
3、天津院(TDF)预热器系统
天津院(TDF)预热器系统参数及主要位置风速如下表:
(按2009年2月池州海螺2#标定值计算)
表三天津院窑尾系统参数(TDF)
位置
有效内径
(m)
截面积(m2)
风速(m/s)
产量5518t/d,热耗778.02kcal/kg.Cl,煤热值5096kcal/kg
风量Nm3/kg.Cl
风量m3/kg.Cl
风量(m3/h)
窑尾
Φ3.450
9.348
11.193
0.3078
1.6383
376675
分解炉柱体
Φ6.900
37.393
8.530
4.9942
1148258
分解炉出口
--
17.577
18.146
1.1877
4.9942
1148258
C5进口
--
17.454
18.190
1.1831
4.9712
1142958
C5柱体
Φ6.300
62.346
5.270
1.2253
5.1446
1182828
C5出口
Φ4.060
25.892
12.700
1.2272
5.1487
1183782
C5~C4管道
Φ3.740
21.972
15.030
1.2334
5.1708
1188861
C4进口
--
17.116
18.250
1.1848
4.8910
1124521
C4柱体
Φ6.140
59.218
5.440
1.2411
5.0441
1159725
C4出口
Φ4.060
25.892
12.400
1.2568
5.0271
1155819
C4~C3管道
Φ3.740
25.892
14.610
1.5049
5.9231
1361816
C3进口
--
16.450
17.480
1.1773
4.5024
1035166
C3柱体
Φ6.140
59.218
5.030
1.2563
4.6639
1072320
C3出口
Φ4.060
25.892
11.450
1.2892
4.6420
1067268
C3~C2管道
Φ3.590
20.244
14.640
1.3300
4.6405
1066940
C2进口
--
15.350
16.520
1.1902
3.9705
912895
C2柱体
Φ5.940
55.424
4.750
1.2950
4.1221
947750
C2出口
Φ3.930
24.260
10.560
1.3238
4.0113
922268
C2~C1管道
Φ3.390
18.052
14.190
1.3940
4.0109
922168
C1进口
--
7.516
15.650
0.7201
1.8418
423451
C1柱体
Φ4.268
28.614
3.650
0.7307
1.6353
375988
C1出口
Φ2.162
7.262
10.990
0.5648
1.2496
287314
天津院(TDF)预热器主要部位工艺操作参数如下图:
(三)窑尾预热器系统操作探讨
1、旋风筒风速合理的控制
旋风筒的收尘效率及阻力与旋风筒内的风速密切相关,旋风筒截面风速一般控制在5—6m/s,进风口风速在15-18m/s,出口风速控制在11-14m/s,若过高,引起系统阻力较大,过低不利于旋风筒收尘。
2、引起预热器系统堵塞原因分析
(1)结皮造成的堵塞
结皮是高温物料在上升烟道、下料管、旋风筒锥部内壁上粘的一层层硬皮,严重时呈圈状缩口,阻碍物料正常流动,而锥部结皮在物料、气体冲刷下,垮下造成下料管堵塞。
结皮堵塞有以下几种情况:
a、不完全燃烧造成预热器内局部温度过高产生结皮堵塞。
如煤粉在窑、炉内燃烧不完全,进入上升烟道、旋风筒内二次燃烧,形成熔融性结皮;预热器敏感部位呈还原气氛,促使有害成份富集结皮;产生低熔点煤灰,形成熔融性结皮。
b、喂煤量波动造成结皮堵塞。
如喂煤量跟不上料量的变化,料小造成系统温度过高,产生熔融性结皮;料大使气料比失调,料短路堵塞预热器;煤波动至上限,形成不完全燃烧现象。
c、翻板阀动作不灵活或卡死造成结皮堵塞。
如初投料时,因翻板阀动作不灵活或卡死,料小冲不开,造成预热器堵塞;翻板阀动作不灵活,造成下一级旋风筒高温内窜入上一级下料管,形成熔融性结皮。
d、系统操作不稳定造成结皮堵塞。
如片面强调入窑分解率,造成系统超温,形成熔融性结皮;风、煤、料调节不合理,造成气料比失调堵塞预热器和出现不完全燃烧现象。
(2)系统漏风造成堵塞
a、内漏风:
由于阀板烧漏、变形,使下一级旋风筒热气流经下料管漏入上一级旋风筒内,降低了上一级旋风筒收集物料效率,收集下来物料不能顺利排出,并在预热器内循环,一旦物料收集过多,便一大股物料冲下,极易堵下料管;另外,此高温气流进入下料管和上一级旋风筒锥部,还可形成熔融性结皮。
b、外漏风:
预热器系统从各级筒检修门、翻板阀轴、热电偶、捅料孔及管道联接法兰等处漏入冷风在筒内和下料管等与热物料接触,出现冷热凝聚现象,产生结皮或大块,造成堵塞;系统外漏冷风,相对降低旋风筒出口风速,导致物料在旋风筒内旋转速度减缓,使物料短路堆积导致堵塞。
使气体和生料短路,形成内循环,降低预热器系统换热效率,严重时造成内部塌料。
二、窑尾预分解系统分解炉
分解炉是预分解系统中的十分重要的设备,它承担预分解系统繁重的燃烧、换热和碳酸盐分解任务。
这些任务能否在高效状态下顺利完成,主要取决于生料与燃料能否在炉内很好的分散、混合和均布;燃料能否在炉内迅速的燃烧,并把燃烧热及时的传递给物料,生料中的碳酸盐组分能否迅速地吸热、分解、逸出的二氧化碳能否及时的排出。
以上要求能否达到,在很大程度上又取决于炉内气、固流动方式,即炉内流场的合理组织。
(一)分解炉的主要功能和设计依据
1、分解炉主要功能
在分解炉内,生料及燃料分别依靠“涡旋效应”、“喷腾效应”、“悬浮效应”和“流化态效应”分散于气流之中。
由于物料之间在炉内流场中产生相对运动,从而达到高度分散、均匀混合和分布、迅速换热、延长物料在炉内的滞留时间,达到提高燃烧效率、换热效率和入窑物料碳酸盐分解率的目的。
2、分解炉设计依据
分解炉具体尺寸设计主要取决于燃料所需的燃烬时间。
在分解炉内主要存在碳酸钙分解和燃料燃烧两种反应。
在连续稳定的状态下,二者进行的吸热和放热的速率是平衡的。
碳酸钙分解从600~700℃时开始,800℃时分解速度明显加快,900℃时分解反应迅速。
但就燃料燃烧反应而言,其在前期燃烧迅速,放热较快。
随着气体中氧含量迅速降低,其后期的燃烧速度明显下降,较难燃烬。
这就表明在分解炉内,对于碳酸钙分解进程来说,其前期主要受控于碳酸钙分解速度,而后期主要受控于燃料燃烧速度。
但在分解炉内,燃料的着火和初期燃烧均进行较快,物料在悬浮态下被迅速加热,体系快速升温,分解炉在绝大部分时间内都处于相对稳定平衡状态。
因此,基本上可以认为分解炉内的分解过程主要受控于燃料燃烧速度。
(二)分解炉的主要设计参数
1、三大院分解炉主要工艺参数
南京院分解炉
南京院(NST-I)分解炉炉容:
1470m3(本体容积+连接管道容积),气体停留时间:
3.9s。
天津院分解炉
天津院(TDF)分解炉炉容:
848m3,气体停留时间:
2.5s。
成都院分解炉
成都院(CDC)分解炉炉容:
1385m3,气体停留时间:
3.9s。
2、分解炉温度场分布
DD炉温度场分布图
(三)分解炉操作探讨
1、分解炉气流特点与控制调节
分解炉采用旋流(三次风)与喷腾流(窑)形成的复合流,兼具纯旋流与纯喷腾流的气特点,二者强度的合理配合强化了物料的分散,若三次风风阀损坏和失效,不能正常调节,使窑、炉用风比例失调,造成煤粉不完全燃烧,未燃烧的煤到C5内燃烧,引起温度倒挂现象。
2、炉温控制
分解炉内煤粉的燃烧反应速率要比CaCO3分解反应慢,分解炉内CaCO3的分解率主要取决于炉温,在850℃左右,生料在炉内若需停留3-5s,因此提高入窑分解率,必须合理控制好炉温。
3、风、煤、料合理匹配
分解炉内要保持风、煤、料的合理匹配,不能大风、大料的变化,否则,喷悬作用发挥不出来,引起燃料分布不均或物料混合不均,影响燃料燃烧、气料热交换及分解炉内温度场的均匀分布,炉容有效利用率不高,旋风筒两列温差(C5下料管)相差较大,压重时引起局部高温点,引起结皮堵塞,甚至引起塌料,使窑内热工制度不稳,窑内结大蛋。
4、分解炉用煤调节控制
预分解窑的发热能力来源于两个热源,即窑头和分解炉,对物料的预烧主要由分解炉完成,熟料的烧结主要由回转窑来决定。
因此在操作中必须做到以炉为基础,前后兼顾,炉窑协调,确保预分解窑系统的热工制度的合理与稳定。
调节分解炉的喂煤量,控制分解炉出口温度在870~900度,确保炉内料气的温度范围,保证入窑生料的分解率。
影响煤粉充分燃烧的因素有几个方面:
一是炉内的气体温度;二是炉内氧气量;三是煤粉细度。
因此,一要提高燃烧的温度;二要保证炉内的风量;三要控制煤粉的细度。
在燃烧完全的条件下,通过分解炉加减煤的操作,控制分解炉出口气体温度。
如果加煤过量,分解炉内燃烧不完全,煤粉就会带入C5燃烧,形成局部高温,使物料发粘,积在锥部,到一定成度造成下料管堵塞。
相反,如果加煤过少,分解用热不够,导致分解炉此刻气温下降,分解率低,导致窑热负荷增加,熟料质量下降。
三、回转窑
(一)回转窑的主要功能
窑尾预分解系统基本完成了物料的干燥、预热及碳酸盐分解等功能,物料的放热反应、烧成及冷却是在回转窑中完成,因此回转窑的主要功能有以下四个方面:
1、燃料燃烧功能;
2、热交换功能;
3、化学反应功能;
4、物料输送功能;
(二)基本数据对比表
南京院
天津院
成都院
设计能力(t/d)
5000
5000
5000
规格(m)
φ4.8×74
φ4.8×72
φ4.8×74
窑内风速(m/s)
7.38
8.526
6.05
窑断面热负荷(KJ/m2.h)
1.76×107
1.59×107
1.42×107
窑单位容积产量(kg/m3.h)
193.87
193.8
195.62
窑单位容积热力强度(KJ/m3.h)
14346.0
13701.3
14082.8
筒体内容积(m3)
1339
1302.9
1339
平均有效内径(m)
4.36
4.4
4.34
有效长度(m)
74
72
72
有效内表面积(m2)
1000
986.2
982
有效内容积(m3)
1074.6
1075
1065
斜度(%)
4
3.5
3.5
(主传)转速(r/min)
0.35~4
0.396~3.96
0.35~4
(主电机)电机功率(Kw)
630
630
630
(三)回转窑操作探讨
1、熟料结圈及结蛋
在回转窑操作中,若风、煤调配不当,窑内通风不良时,就会造成煤粉不完全燃烧,煤粉跑到窑后去烧,煤灰不均匀地掺人生料,火焰过长,窑后温度过高,液相提前出现,在窑内结蛋,当窑尾温度过高时,窑后物料出现不均匀的局部熔融,成为形成结蛋的核心,然后在窑内越滚越大形成大蛋。
另外,当给煤量较大时,在1150℃条件下,Fe2O3也会部分分解为Fe3O4,与SiO2作用而生成2FeO·SiO2,形成渣相粘结。
这就使得物料在流经焙烧带时,所产生的液相、渣相极易粘附在窑衬的表面,同时粘结物料而产生结圈现象。
2、熟料游离氧化钙控制
当窑尾温度低或者有塌料、掉窑皮,喂料量的不当时,会引起熟料游离氧化钙含量增高(f-CaO是熟料中没有参加反应而以游离状态存在的CaO)。
当分解窑偶然出现较高熟料游离氧化钙含量时,正确的操作方法如下:
①一旦发现上述异常现象,立即减少喂料,减料多少根据窑内状况异常的程度而定。
比如:
塌料较大、时间较长或窑尾温度降低较多,此时减料幅度要略大些,但不宜于一次减料过大,要保持一级预热器出口温度不能升得过快过高。
②紧接着相应减少分解炉的喂煤,维持一级预热器出口温度略高于正常时的50℃以内,同时通知化验室增加入窑分解率的测定,确保85%~90%。
③略微减少窑尾排风,以使一级出口的温度能较快恢复原有状态。
但不可减得过多,否则会造成新的塌料,也影响二、三次风的入窑量,进而影响火焰。
④如果掉窑皮或塌料量不大,完全可以不减慢窑速,这批料虽以不合格的熟料出窑,但对生产总体损失是最小的。
按照这种操作方式,恢复正常运行的时间只需十分钟。
如果是打慢窑,这批料不仅无法煅烧合格,而且如上所述至少耗时半个小时以上,影响熟料的产量,以及更多熟料的质量。
当然,如果脱落较多窑皮或窜料严重,不得不大幅度降低窑速,至1r/min以内,此时更重要的是投料量要大幅度降低,为正常量的1/3左右。
而且也应减料操作在前,打慢窑速的操作在后,避免有大量物料在窑内堆积。
如此出来的熟料游离钙含量会合格,但付出的代价却是半个小时以上的正常产量、更多的燃料消耗、长时间的工艺制度不正常,以及类似中空窑煅烧的各种弊病,经济上损失较大。
⑤尽快找出窑内温度不正常的原因,对症治疗,防止类似情况再次发生。
比如:
找出塌料的原因、窑尾温度降低的原因等。
上述操作方法还要因具体情况而异,总的原则是:
不要纠缠一时一事的得失,要顾全系统稳定的大局。
这个大局就是用最短时间恢复窑内火焰的正常、系统温度分布的正常,各项工艺参数的正常,并继续保持它们。
3、熟料立升重控制
熟料的立升重即一立升熟料的质量,其高低是判断熟料质量和窑内温度(主要是烧成带温度)的参数之一,通过物料结粒大小及均匀程度,可以推测烧成温度是否正常。
当窑温正常时,产量高,熟料颗粒大小均齐,外观紧密结实,表面较光滑而近似小圆球状,立升重较高;物料在烧成带温度过高或在烧成带停留时间太长,过烧料多,熟料立升重过高,熟料质量反而不好。
如窑内物料化学反应不完全,熟料颗粒小的多,而且其中还带有细粉,立升重就低,说明窑内温度低,新型干法生产线的熟料立升重一般控制在1300g/L—1500g/L。
窑内熟料颗粒是在液相作用下形成的,液相在晶体外形成毛细管桥。
液相毛细管桥起到两个作用:
一是使颗粒结合在一起,另一个作用是作为中间介质,使CaO和C2S在熔融态内扩散生成C3S,颗粒的强度取决于毛细管桥的强度,桥的强度即连接颗粒的力随液相表面张力和颗粒直径的降低而增加。
毛细管桥的数量又与颗粒直径的平方根成反比。
要结好粒,必须有足够的液相,并要求颗粒在液相内分布均匀,形成较高的表面张力和适宜的结粒时间。
四、篦冷机
篦冷机是水泥熟料生产线烧成系统配套的主要设备,不仅对热熟料进行冷却和输送,而且是水泥熟料煅烧系统中热回收的重要工艺设备,也是直接影响回转窑运转率的关键设备。
熟料冷却机由单筒、多筒到篦式,以及篦式冷却机由回转式和推动式的第一、二、三、四技术的发展,无论是气固之间的逆流、同流、错流换热,都是围绕提高气固换热系数,增大气固接触面积,增加气固换热温差等提高气固换热速率和效率方向发展的。
(一)熟料冷却机的主要功能
1、作为一个工艺设备,它承担着对高温熟料的骤冷任务。
2、作为热工设备,在对熟料骤冷的同时,承担着对入窑二次风及入炉三次风的加热升温任务。
3、作为热回收设备,它承担着对出窑熟料携出的大量热焓的回收任务。
4、作为熟料输送设备,它承担着对高温熟料的输送任务。
(二)第三代篦冷机的特点
1、篦冷机入口端采用阻力篦板及充气梁结构篦床和窄宽度布置方式,增加篦板阻力在篦板加料层总阻力中的比例,力求消除预分解窑熟料颗粒变细及分布不均等因素对气流均匀分布的影响。
2、发挥脉冲高速气流对熟料料层的骤冷作用,以少量冷却风量回收炽热熟料的热焓,提高二、三次风温。
3、由于脉冲供风,使细粒熟料不被高速气流携带,同时由于细粒熟料扰动,增加气料之间换热速度。
4、高压空气通过空气梁特别是篦冷机热端前数排空气梁向篦板下部供风,增强对熟料均布、冷却和对篦板的冷却作用,消灭“红河”,保护篦板。
5、设有对一段篦床一、二室各行篦板风量、风压及脉冲供风的自控调节系统,或各块篦板的人工调节阀门,以便根据需要调节。
同时,一段篦速与篦下压力自动调节,保持料层设定厚度,其他段篦床与一段篦床同步调节。
(三)冷却机的性能评价指标
对于冷却机性能的评价,一般采用下列指标。
对其要求是:
1、热效率(ηc)高
即从出窑熟料中回收并用于熟料煅烧过程的热量(Q收)与出窑熟料带入冷却机的热量(Q出)之比大。
热效率通常用以下式表示:
或
式中
——冷却机热效率(%);
Q损——冷却机总热损失(KJ/kg.cl);
Qy——入窑二次风显热(kJ/kg.cl);
QF——入炉三次风显热(kJ/kg.cl)。
2、冷却效率高
即出窑熟料被回收的总热量与出窑熟料带入冷却机的热量之比值大。
冷却效率通常以下式表示:
3、空气升温效率
即鼓入各室的冷却空气与离开熟料层空气温度的升高值同该室区熟料平均温度之比值大。
空气升温效率(
I)通常以下式表示:
式中
——空气升温系数;
——鼓入某区冷却空气温度(即环境温度)(℃);
——离开该区温度层空气温度(℃);
——该区冷却机篦床上熟料平均温度(℃);
当
>2时,
当
<2时
本指标为篦冷机评价指标之一,一般
<0.9.
4、进入冷却机的熟料温度与离开冷却机的入窑二次风及去分解炉的三次风温度之间的差值小。
5、离开冷却机的熟料温度低。
6、冷却机及其附属设备电耗低。
7、投资少,电耗低,磨耗小,运转率高等。
(四)集团内5000t/d生产线所用篦冷机比较
对比的内容
成都院
天津院
南京院
型号TYPE
LBTF篦式冷却机
TC-12102篦式冷却机
NC42340篦式冷却机
设计产量t/d
5000~6000
5000~6000
5000~6000
篦床有效面积m2
133.2
119.3
133.2
冷却负荷t/(d.m2)
41.5~45.8
41.5~45.9
41.3~45.3
传动篦床段数
3
3
3段
篦床斜度
3段篦床均倾斜3°
第1、2段篦床倾斜3°,第3段篦床水平
第1、2段篦床倾斜3°,第3段篦床水平
传动形式
液压传动
液压传动
液压传动
传动功率kW
225
225
225
篦床行程mm
130
130
130
篦床运行次数次/min
4-25
4-25
4-25
入料温度℃
1400
1400
1400
出料温度℃
65+环境温度
65+环境温度
65+环境温度
热回收率%
73-76
73-76
72-75
冷却风用量Nm3/kg.cl
<2.0
<2.0
<2.0
破碎机形式
尾部锤式破碎机
尾部锤式破碎机
尾部锤式破碎机
破碎机功率kW
90
90
90
出料粒度mm
(90%)≤25
(90%)≤25
(90%)≤25
篦床的宽×长m
3.6×37.95
3.6×33.66
4.2×34
篦床的外观特征
窄而长
窄而长
宽而短
篦床的供风形式
脉冲供风
直接供风
高温段充气梁供风,中低温段为风室供风
风室熟量(个)
9
9
9
风机台数(台)
17
15
17
(五)篦冷机操作探讨
1、回转窑篦冷机堆雪人的原因及处理
(1)何谓篦冷机堆雪人
所谓篦冷机堆雪人是一种形象的称呼,实际上就是篦冷机前壁回转窑筒体下方的熟料无法运走,使其越积越高,严重时可堵到窑口致使窑内的熟料无法排出。
(2)引起堆雪人的主要原因
①