拨叉课程设计设计说明书总结.docx
《拨叉课程设计设计说明书总结.docx》由会员分享,可在线阅读,更多相关《拨叉课程设计设计说明书总结.docx(25页珍藏版)》请在冰豆网上搜索。
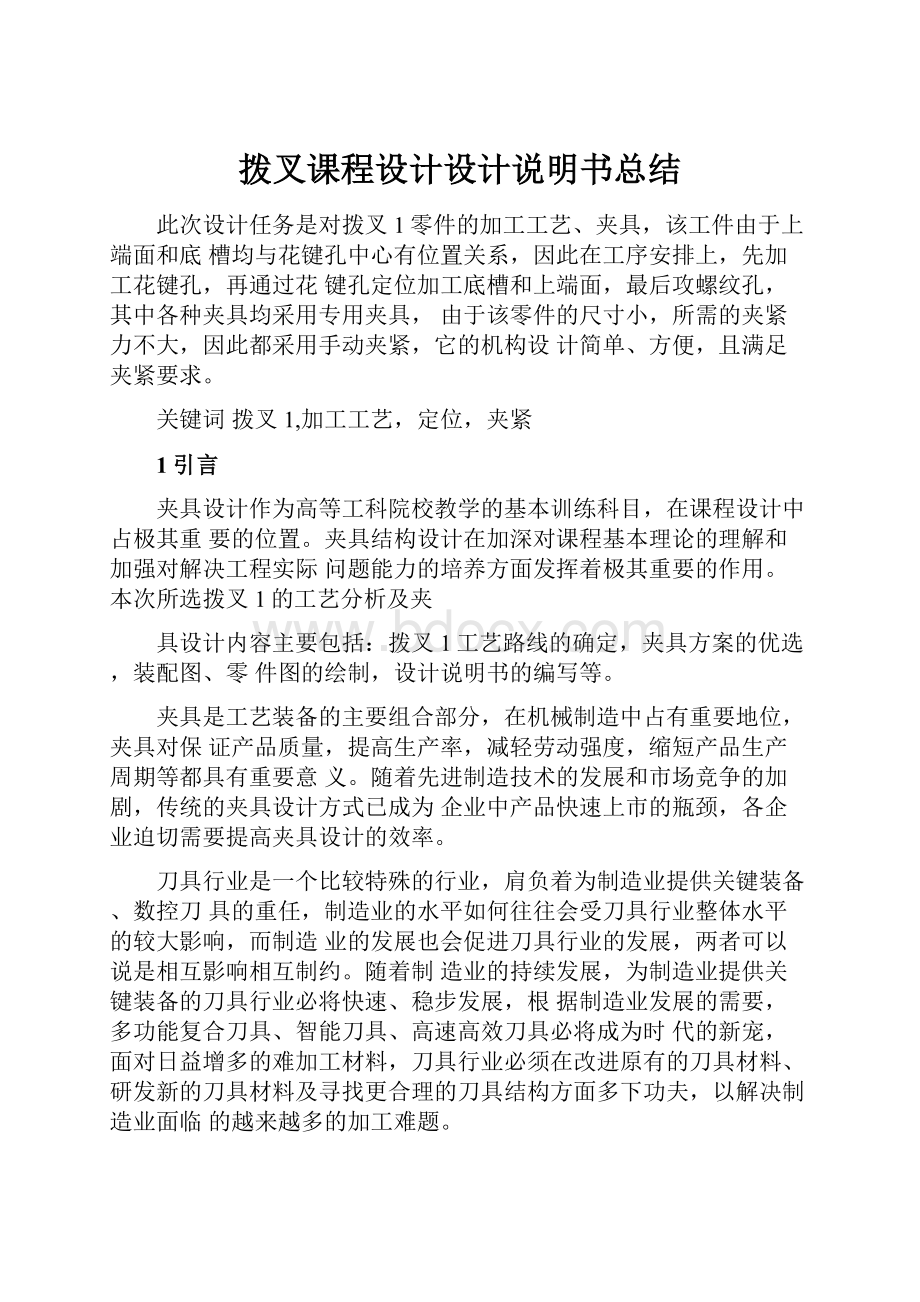
拨叉课程设计设计说明书总结
此次设计任务是对拨叉1零件的加工工艺、夹具,该工件由于上端面和底槽均与花键孔中心有位置关系,因此在工序安排上,先加工花键孔,再通过花键孔定位加工底槽和上端面,最后攻螺纹孔,其中各种夹具均采用专用夹具,由于该零件的尺寸小,所需的夹紧力不大,因此都采用手动夹紧,它的机构设计简单、方便,且满足夹紧要求。
关键词拨叉1,加工工艺,定位,夹紧
1引言
夹具设计作为高等工科院校教学的基本训练科目,在课程设计中占极其重要的位置。
夹具结构设计在加深对课程基本理论的理解和加强对解决工程实际问题能力的培养方面发挥着极其重要的作用。
本次所选拨叉1的工艺分析及夹
具设计内容主要包括:
拨叉1工艺路线的确定,夹具方案的优选,装配图、零件图的绘制,设计说明书的编写等。
夹具是工艺装备的主要组合部分,在机械制造中占有重要地位,夹具对保证产品质量,提高生产率,减轻劳动强度,缩短产品生产周期等都具有重要意义。
随着先进制造技术的发展和市场竞争的加剧,传统的夹具设计方式已成为企业中产品快速上市的瓶颈,各企业迫切需要提高夹具设计的效率。
刀具行业是一个比较特殊的行业,肩负着为制造业提供关键装备、数控刀具的重任,制造业的水平如何往往会受刀具行业整体水平的较大影响,而制造业的发展也会促进刀具行业的发展,两者可以说是相互影响相互制约。
随着制造业的持续发展,为制造业提供关键装备的刀具行业必将快速、稳步发展,根据制造业发展的需要,多功能复合刀具、智能刀具、高速高效刀具必将成为时代的新宠,面对日益增多的难加工材料,刀具行业必须在改进原有的刀具材料、研发新的刀具材料及寻找更合理的刀具结构方面多下功夫,以解决制造业面临的越来越多的加工难题。
当前,切削技术快速发展,已经进入了现代切削技术新阶段,刀具材料、刀具结构均取得了全面的进步,加工效率也在成倍提高。
同时,切削技术和刀具也成为制造业开发新产品和新工艺、应用新材料的基础工艺和建立创新体系的关键技术。
2拨叉1的分析
2.1拨叉1的作用
题目所给的零件是CA6140车床的拨叉。
它位于车床变速机构中,主要起换档,使主轴回转运动按照工作者的要求工作,获得所需的速度和扭矩的作用。
2.2拨叉1的工艺分析
拨叉1是一个很重要的零件,因为其零件尺寸比较小,结构形状较复杂,其加工内花键的精度要求较高,此外还有上端面要求加工,对精度要求也很高。
其底槽侧面与花键孔中心轴有垂直度公差要求,上端面与花键孔轴线有平行度要求。
因为其尺寸精度、几何形状精度和相互位置精度,以及各表面的表面质量均影响机器或部件的装配质量,进而影响其性能与工作寿命,因此它们的加工是非常关键和重要的。
2.3拨叉1的工艺要求
一个好的结构不但要应该达到设计要求,而且要有好的机械加工工艺性,也就是要有加工的可能性,要便于加工,要能够保证加工质量,同时使加工的劳动量最小。
而设计和工艺是密切相关的,又是相辅相成的。
设计者要考虑加工工艺问题。
工艺师要考虑如何从工艺上保证设计的要求。
18H11底槽;钻、铰2-M8通孔,并攻丝。
(1)侧面的加工主要是为了后续工序中能有更好的定位面,确保后续加工所要求的精度,粗糙度在6.3即可。
(2)以*22H12为主要加工面,拉内花键槽©25H7,槽数为6个,其粗糙度要求是底边Ra=1.6,侧边Ra=3.2,*22H12内孔粗糙度Ra=6.3。
(3)
(4)
Ra=3.2,
(5)
另一组加工是粗精铣上端面,表面粗糙度要求为Ra=3.2。
第三组为粗精铣18H11底槽,该槽的表面粗糙度要求是两槽边
槽底的表面粗糙度要求是Ra=6.3。
钻并攻丝2-M8,保证两螺纹孔中心距为25mm。
2.4毛坯的选择
拨叉1毛坯选择铸件,因为生产率很高,所以可以免去每次造型。
工件尺寸较小单边余量一般在1~2mm,结构细密,能承受较大的压力,占用生产的面积较小。
生产类型为大批量生产。
2.5本章总结
通过对拨叉1的工艺分析,为以后工序的设计安排,夹具的设计打下理论基础,在对拨叉1进行工艺分析时,要充分考虑工件的材料、形状尺寸,保证工件加工时的良好工艺性,通过对拨叉1的分析,确定毛坯为铸件,在后续设计中以此分析为前提,优化夹具方案。
3工艺规程设计
3.1加工工艺过程
由以上分析可知。
该拨叉零件的主要加工表面是平面、内花键和槽系。
一般来说,保证平面的加工精度要比保证内花键的加工精度容易。
因此,对于拨叉1来说,加工过程中的主要问题是保证内花键的尺寸精度及位置精度,处理好内花键和平面之间的相互关系以及槽的各尺寸精度。
由上工艺分析知,上端面与槽边均与花键轴有位置度公差,所以,保证内花键高精度是本次设计的重点、难点。
3.2确定各表面加工方案
一个好的结构不但应该达到设计要求,而且要有好的机械加工工艺性,也就是要有加工的可能性,要便于加工,要能保证加工的质量,同时是加工的劳动量最小。
设计和工艺是密切相关的,又是相辅相成的。
对于设计拨叉1的加
工工艺来说,应选择能够满足内花键加工精度要求的加工方法及设备。
除了从加工精度和加工效率两方面考虑以外,也要适当考虑经济因素。
在满足精度要求及生产率的条件下,应选择价格较底的机床。
321选择加工方法时,需考虑的因素
(1)要考虑加工表面的精度和表面质量要求,根据各加工表面的技术要求,选择加工方法及分几次加工。
(2)根据生产类型选择,在大批量生产中可专用的高效率的设备。
在单件小批量生产中则常用通用设备和一般的加工方法。
(3)考虑被加工材料的性质。
(4)考虑工厂或车间的实际情况,同时也应考虑不断改进现有加工方法和设备,推广新技术,提高工艺水平。
(5)此外,还要考虑一些其它因素,如加工表面物理机械性能的特殊要求,工件形状和重量等。
选择加工方法一般先按这个零件主要表面的技术要求选定最终加工方法。
再选择前面各工序的加工方法。
3.2.2面的加工
侧面的加工主要是为后续加工做准备,因此,在选择加工方法上可以选用一次性铣面,表面粗糙度为6.3。
上端面的查参考文献[5]表2.1-12可以确定,上端面的加工方案为:
粗铣一一精铣(IT7〜IT9),粗糙度为Ra=6.3~0.8,般不淬硬的平面,精铣的粗糙度可以较小。
3.2.3孔的加工
(1)加工内花键前的预制孔*22H12加工
查参考文献⑸表2.3-47,由于预制孔的精度为H12,所以确定预制孔的加工方案为:
一次钻孔,由于在拉削过程中才能保证预制孔表面精度,所以,在加工内花键前预制孔的精度可适当降低。
(2)内花键的加工
通过拉刀实现花键的加工,由于拉削的精度高,所以能满足花键表面精度,同时也能保证预制孔表面精度。
(3)2-M8螺纹孔的加工
加工方案定为:
钻,攻丝。
3.2.4槽的加工
查参考文献⑸表2.1-12可以确定,槽的加工方案为:
粗铣一一精铣(IT7〜IT9),粗糙度为Ra=6.3〜0.8,设计要求为6.3和3.2,粗铣时,精度可适当降低。
3.3确定定位基准331粗基准的选择
选择粗基准时,考虑的重点是如何保证各加工表面有足够的余量,使不加工表面与加工表面间的尺寸、位子符合图纸要求。
粗基准选择应当满足以下要求:
目的是为了保证加工面与不加
(1)粗基准的选择应以加工表面为粗基准。
工面的相互位置关系精度。
如果工件上表面上有好几个不需加工的表面,则应选择其中与加工表面的相互位置精度要求较高的表面作为粗基准。
以求壁厚均匀、外形对称、少装夹等。
(2)选择加工余量要求均匀的重要表面作为粗基准。
例如:
机床床身导轨面是其余量要求均匀的重要表面。
因而在加工时选择导轨面作为粗基准,加工床身的底面,再以底面作为精基准加工导轨面。
这样就能保证均匀地去掉较少的余量,使表层保留而细致的组织,以增加耐磨性。
(3)应选择加工余量最小的表面作为粗基准。
这样可以保证该面有足够的加工余量。
(4)应尽可能选择平整、光洁、面积足够大的表面作为粗基准,以保证定位准确夹紧可靠。
有浇口、冒口、飞边、毛刺的表面不宜选作粗基准,必要时需经初加工。
(5)粗基准应避免重复使用,因为粗基准的表面大多数是粗糙不规则的。
多次使用难以保证表面间的位置精度。
要从保证孔与孔、孔与平面、平面与平面之间的位置,能保证拨叉1在整
个加工过程中基本上都能用统一的基准定位。
从拨叉1零件图分析可知,选择
作为拨叉1加工粗基准。
3.3.2精基准选择的原则
(1)基准重合原则。
即尽可能选择设计基准作为定位基准。
这样可以避免定位基准与设计基准不重合而引起的基准不重合误差。
(2)基准统一原则,应尽可能选用统一的定位基准。
基准的统一有利于保证各表面间的位置精度,避免基准转换所带来的误差,并且各工序所采用的夹具比较统一,从而可减少夹具设计和制造工作。
例如:
轴类零件常用顶针孔作为定位基准。
车削、磨削都以顶针孔定位,这样不但在一次装夹中能加工大多书表面,而且保证了各外圆表面的同轴度及端面与轴心线的垂直度。
(3)互为基准的原则。
选择精基准时,有时两个被加工面,可以互为基准反复加工。
例如:
对淬火后的齿轮磨齿,是以齿面为基准磨内孔,再以孔为基准磨齿面,这样能保证齿面余量均匀。
自为基准原则。
有些精加工或光整加工工序要求余量小而均匀,可以选择加工表面本身为基准。
例如:
磨削机床导轨面时,是以导轨面找正定位的。
此外,像拉孔在无心磨床上磨外圆等,都是自为基准的例子。
此外,还应选择工件上精度高。
尺寸较大的表面为精基准,以保证定位稳固可靠。
并考虑工件装夹和加工方便、夹具设计简单等。
要从保证孔与孔、孔与平面、平面与平面之间的位置,能保证拨叉1在整
个加工过程中基本上都能用统一的基准定位。
从拨叉1零件图分析可知,它的
叱5H7内花键槽,适于作精基准使用。
选择精基准的原则时,考虑的重点是有利于保证工件的加工精度并使装夹准。
3.4工艺路线的拟订
对于大批量生产的零件,一般总是首先加工出统一的基准。
拨叉1的加工
的第一个工序也就是加工统一的基准。
具体安排是:
先加工预制孔,再加工花键槽,最后以花键槽定位粗、精加工拨叉上端面和底槽及M8螺纹孔。
后续工序安排应当遵循粗精分开和先面后孔的原则。
341加工阶段的划分
零件的加工质量要求较高时,常把整个加工过程划分为几个阶段:
(1)粗加工阶段
粗加工的目的是切去绝大部分多余的金属,为以后的精加工创造较好的条件,并为半精加工,精加工提供定位基准,粗加工时能及早发现毛坯的缺陷,予以报废或修补,以免浪费工时。
Ra=80~100um。
粗加工可采用功率大,刚性好,精度低的机床,选用大的切前用量,以提高生产率、粗加工时,切削力大,切削热量多,所需夹紧力大,使得工件产生的内应力和变形大,所以加工精度低,粗糙度值大。
一般粗加工的公差等级为IT11~IT12。
粗糙度为
(2)半精加工阶段
半精加工阶段是完成一些次要面的加工并为主要表面的精加工做好准备,保证合适的加工余量。
半精加工的公差等级为IT9~IT10。
表面粗糙度为
Ra=10~1.25卩m。
(3)精加工阶段
精加工阶段切除剩余的少量加工余量,主要目的是保证零件的形状位置几精度,尺寸精度及表面粗糙度,使各主要表面达到图纸要求.另外精加工工序安排在最后,可防止或减少工件精加工表面损伤。
精加工应采用高精度的机床小的切前用量,工序变形小,有利于提高加工精度.精加工的加工精度一般为IT6~IT7,表面粗糙度为Ra10~1.25卩m。
(4)光整加工阶段
对某些要求特别高的需进行光整加工,主要用于改善表面质量,对尺度精度改善很少。
一般不能纠正各表面相互位置误差,其精度等级一般为IT5~IT6,
表面粗糙度为Ra1.25~0.32um。
此外,加工阶段划分后,还便于合理的安排热处理工序。
由于热处理性质的不同,有的需安排于粗加工之前,有的需插入粗精加工之间。
但须指出加工阶段的划分并不是绝对的。
在实际生活中,对于刚性好,精度要求不高或批量小的工件,以及运输装夹费事的重型零件往往不严格划分阶段,在满足加工质量要求的前提下,通常只分为粗、精加工两个阶段,甚至不把粗精加工分开。
必须明确划分阶段是指整个加工过程而言的,不能以某一表面的加工或某一工序的性质区分。
例如工序的定位精基准面,在粗加工阶段就要加工的很准确,而在精加工阶段可以安排钻小空之类的粗加工。
3.4.2加工工艺路线方案的确定
3.1。
在保证零件尺寸公差、形位公差及表面粗糙度等技术条件下,成批量生产可以考虑采用专用机床,以便提高生产率。
但同时考虑到经济效果,降低生产成本,拟订一个加工工艺路线方案,加工工艺过程表。
见表
表3.1加工工艺过程表
工序号
工种
工作内容
说明
010
铸造
金属型浇铸
铸件毛坯尺寸:
长:
80mm宽:
40mm高:
75mm
预制孔、底槽不铸出
020
热处理
退火
030
铣
铣侧面
专用铣夹具装夹;卧式铣床(X52K
040
钻
钻预制孔*22H12
专用夹具装夹;轻型圆柱立
式钻床(ZQ5035)
050
拉
拉内花键©25H7
专用夹具装夹;卧式拉床(L6120)
060
铣
铣底槽18H11,深35mm
专用夹具装夹;卧式铣床(X52K)
070
铣
粗、精铣上端面
专用夹具装夹;卧式铣床(X52K)
080
钻攻丝
钻通孔©6.7mm
攻M8螺纹
专用夹具装夹;
摇臂钻床(Z3025)
090
去毛刺
清洗
100
检验
入库
3.5拨叉1的毛坯结构工艺的分析
拨叉1其材料是HT200,采用的是金属型铸造,生产类型为大批量生产。
3.5.1毛坯的结构工艺要求
铸件的壁厚应合适、均匀,不得有突然变化。
铸造圆角要适当,得有尖棱、尖角。
铸件的结构要尽量简化。
加强肋的厚度和分布要合理,以免冷却时铸件变形或产生裂纹。
(1)拨叉1为铸造件,对毛坯的结构工艺有一定要求:
①
②
③
④
5铸件的选材要合理,应有较好的可铸性。
(2)设计毛坯形状、尺寸还应考虑到:
各加工面的几何形状应尽量简单。
工艺基准以设计基准相一致。
便于装夹、加工和检查。
结构要统一,尽量使用普通设备和标准刀具进行加工。
①
②
③
④
在确定毛坯时,要考虑经济性。
虽然毛坯的形状尺寸与零件接近,可以减少加工余量,提高材料的利用率,降低加工成本,但这样可能导致毛坯制造困难,需要采用昂贵的毛坯制造设备,增加毛坯的制造成本。
因此,毛坯的种类形状及尺寸的确定一定要考虑零件成本的问题但要保证零件的使用性能。
在毛坯的种类形状及尺寸确定后,必要时可据此绘出毛坯图。
3.6确定切削用量及基本时间
工序1:
铣侧面
机床:
卧式铣床
刀具:
根据参考文献[4]表10-231,选用高速钢错齿三面刃铣刀,规格为:
D=160mm,d=40mm,L=32mm,齿数为12齿。
铣削深度ap:
ap=1mm
每齿进给量af:
查参考文献⑸表2.4-75,3^0.2~0.3mmZ,取af=0.3mmZ=3.6mm^。
铣削速度V:
查参考文献[4]表11-94,得V=15~20mm,05-03
取V=0-3mS
机床主轴转速n:
1000V1000X0.3X60
n==壬35.83r/min
兀D3.14咒160
查参考文献⑸表3.1-74取n=37.5r/min
实际切削速度v:
"盘=血迪述y31m/s
10001000X60
进给量Vf:
Vf=afZn=3.6咒12咒37.5/60=27mm/s
工作台每分进给量fm:
fm=Vf=27mm/s=1620mm/min
被切削层长度I:
由毛坯尺寸可知I=75mm
刀具切入长度li:
li=0.5D+(1~2)
=82mm
走刀次数为1
工序2:
钻预制孔
机床:
轻型圆柱立式钻床(ZQ5035)
刀具:
查参考文献[4]表10-175,选高速钢直柄麻花钻,钻预制孔到
*21.2mm,所以d=21.2mm。
进给量f:
根据参考文献⑸表2.4-38,取f=0.5mm/r
切削速度V:
参照参考文献⑸表2.4-41,取V=0.45m/s
机床主轴转速n,有:
1000V1000咒0.45咒60厂,-
n==比405.6r/min,
兀d3.14x21.2
按照参考文献⑸表3.1-36,取n=475r/min
切削工时
被切削层长度l:
l=80mm
刀具切入长度l1:
h=dctgkr+(1~2)=212ctg120°+1=5.9mm6mm
22
走刀次数为1
L80+6+3
机动时[可tj2:
tj2=—=0.37min
fn0.5x475
工序4:
粗、精铣18H11底槽
机床:
立式升降台铣床(X52K)
刀具:
根据参考文献[4]表21-5选用高速钢镶齿三面刃铣刀。
外径160mm,内径40mm,刀宽粗铣16mm,精铣18mm,齿数为24齿。
(1)粗铣16槽
铣削深度ap:
ap=33mm
每齿进给量af:
查参考文献⑸表2.4-75,得af=0.2~0.3mm/z,取af=0.2mm/z。
铣削速度V:
查参考文献[8]表30-33,得V
机床主轴转速n:
1000V1000x14crc,■
n==帝27.9r/min
兀D3.14咒160
查参考文献⑸表3.1-74取n=30r/min
实际切削速度V:
V二壘二3.14"60*307.25m/s
10001000X60
进给量Vf:
Vf=afZn=0.2x24x30/60=2.4mm/s
刀具切入长度h:
h=0.5D+(1~2)
=81mm
刀具切出长度l2:
取I2=2mm
走刀次数1次
机动时间tj1:
tj1=r^=40+81+2.o.85minj1j1£144
(2)精铣18槽
切削深度ap:
ap=35mm
根据参考文献⑸表2.4-76查得:
进给量af=0.05mm/z,查参考文献⑸表
2.4-82得切削速度V=23m/min,
机床主轴转速n:
1000V1000X23,■
n==俺45.8r/min,
兀d3.14x160
查参考文献⑸表3.1-74取n=47.5r/min
进给量Vf:
Vf=afZn=0.05咒24x47.5/60=0.95mm/s
工作台每分进给量fm:
fm=Vf=0.18mm/s=57mm/min
被切削层长度I:
由毛坯尺寸可知l=40mm.
刀具切入长度li:
li=0.5D+(1~2)
=81mm
刀具切出长度L:
取J=2mm
走刀次数为1
I+L+lc40+81+2
机动时间tj1:
切=—=r-“52min
本工序机动时间tj=如+tj2=0.85+1.52=2.37min
工序5:
粗、精铣上端面
机床:
卧式铣床X52K
刀具:
根据参考文献[4]表10-231,选用高速钢错齿三面刃铣刀,规格为:
D=160mm,d=40mm,L=32mm,齿数为12齿。
(1)粗铣上端面
铣削深度ap:
ap=3mm
每齿进给量af:
查参考文献⑸表2.4-75,af=0.15~0.25mmZ,取af=1.8mmr。
mS,
铣削速度V:
查参考文献[4]表11-94,得V=15~20mm,025~0GB
取V=0-3叹
机床主轴转速n:
1000V1000X0.3X60»“/-
n==俺35.83r/min
兀D3.14咒160
查参考文献⑸表3.1-74取n=37.5r/min
进给量Vf:
Vf=afZn=1.8x12x37.5/60=13.5mm/s
工作台每分进给量fm:
fm=Vf=13.5mm/s=810mm/min
被切削层长度丨:
由毛坯尺寸可知丨=80mm
刀具切入长度li:
li=0.5D+(1~2)
=82mm
走刀次数为1
(2)精铣上端面
切削深度ap:
ap=1mm
根据参考文献[4]表11-91查得:
每齿进给量a^0.01~0.02mm/z,取af=0.24mm/r,根据参考文献[4]表11-94查得切削速度V=30m/min
机床主轴转速n:
1000V1000x30…■
n==俺59.7r/min,
兀d3.14x160
按照参考文献⑸表3.1-74取n=60r/min
实际切削速度v:
V=壘=3.14*16"60".50m/s
10001000x60
进给量Vf:
Vf=afZn=0.24X12x60/60=2.88mm/s
工作台每分进给量fm:
fm=Vf=2.88mm/s=172.8mm/min
被切削层长度I:
由毛坯尺寸可知丨=80mm
刀具切入长度li:
li=0.5D+(1~2)
=81mm
走刀次数为1
工序6:
钻M8孔并攻丝
机床:
摇臂钻床Z3025
刀具:
根据参照参考文献[5]表4.3-9硬质合金锥柄麻花钻头。
(1)钻孑L帕.7mm
钻孔前铸件为实心,根据上文所的加工余量先钻孔到*6.7mm再攻丝,所以
D=6.7mm。
钻削深度ap:
ap=9.5mm
进给量f:
根据参考文献⑸表2.4-38,取f=0.33mm/r
切削速度V:
参照参考文献⑸表2.4-41,取V=0.41m/s
机床主轴转速n,有:
按照参考文献⑸表3.1-31取n=1600r/min
被切削层长度I:
I=42mm
刀具切入长度l1:
D67
h=—ctgkr+(1-2)=^ctg120*+1=2.89mmsz3mm
22
走刀次数为1,钻孔数为
(2)攻2-M8螺纹通孔
刀具:
钒钢机动丝锥
进给量f:
查参考文献⑸表1.8-1得所加工螺纹孔螺距P=1.25mm,因此进
给量f=1.25mm/r
参照参考文献⑸表2.4-105,取V=0.133m/s=7.98m/min
实际切削速度V\
兀don
3.14^8咒350
被切削层长度
刀具切入长度
I1:
刀具切出长度
l2:
1000
=9.5mm
I1=(1~3)f
l2(2-3)
1000X60
是0.15m/s
=3x1.25=3.75mm
f=3x1.25=3.75mm,加工数为2
机动时间tj2:
tj2(^l^+2(9^32^+9.5+3.75+3.75)2Z13min
jfnfn回1.5x3501.5天350本工序机动时间tj:
tj=切+tj2=0.5